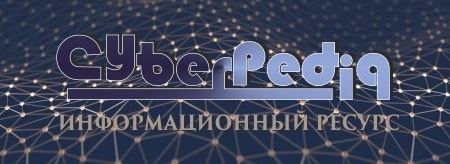
Общие условия выбора системы дренажа: Система дренажа выбирается в зависимости от характера защищаемого...
Организация стока поверхностных вод: Наибольшее количество влаги на земном шаре испаряется с поверхности морей и океанов (88‰)...
Топ:
Основы обеспечения единства измерений: Обеспечение единства измерений - деятельность метрологических служб, направленная на достижение...
Марксистская теория происхождения государства: По мнению Маркса и Энгельса, в основе развития общества, происходящих в нем изменений лежит...
Генеалогическое древо Султанов Османской империи: Османские правители, вначале, будучи еще бейлербеями Анатолии, женились на дочерях византийских императоров...
Интересное:
Что нужно делать при лейкемии: Прежде всего, необходимо выяснить, не страдаете ли вы каким-либо душевным недугом...
Инженерная защита территорий, зданий и сооружений от опасных геологических процессов: Изучение оползневых явлений, оценка устойчивости склонов и проектирование противооползневых сооружений — актуальнейшие задачи, стоящие перед отечественными...
Влияние предпринимательской среды на эффективное функционирование предприятия: Предпринимательская среда – это совокупность внешних и внутренних факторов, оказывающих влияние на функционирование фирмы...
Дисциплины:
![]() |
![]() |
5.00
из
|
Заказать работу |
|
|
Группа оборудования | К3 | КИ | |
максимальное значение | среднее по группе | ||
Универсальные станки | 0,95-1,0 | 0,8 | 0,9 |
Автоматы и полуавтоматы одношпиндельные | 0,95-1,0 | 0,85 | 0,85 |
То же многошпиндельные | 0,9 | 0,9 | 0,8 |
Агрегатные станки | 0,9 | 0,9 | 0,8 |
Станки с ЧПУ | 0,95 | 0,9 | 0,85 |
Для учета наложенных потерь применяют коэффициент использования оборудования К и, который представляет собой отношение расчетного количества единиц оборудования, необходимого для обеспечения программы выпуска изделий, к принятому. Поэтому принятое количество станков на данной операции
Сп = Срасч / К и.
При этом следует иметь в виду, что в тех случаях, когда расчетное значение коэффициента загрузки получается меньше рекомендованного, коэффициент использования в расчет не вводят (принимают К и = 1). Отметим также, что значение К 3 никогда не может быть больше единицы. В тех случаях, когда значение Срасч превышает целое число не более чем на 0,05...0,1, следует пересмотреть содержание данной операции в части изменения режима резания, структуры операции, применяемых инструментальных материалов и оснастки в целях повышения производительности обработки.
В качестве примера определим количество станков для операций токарной и зубофрезерной на поточной линии обработки зубчатого колеса на одношпиндельных полуавтоматах, если такт выпуска τ = 2 мин, а штучное время выполнения этих операций составляет соответственно t ш ток = 1,75 мин и t ш фр = 9,8 мин.
Для токарной операции С′расч ток = 1,75/2 ≈ 0,85. После округления до ближайшего большего целого числа получаем расчетное количество станков для данной операции Срасч ток = 1. Поскольку К 3 ток = 0,85, т. е. его значение меньше рекомендуемого (см. табл. 7.5), то Сп ток = Срасч ток = 1.
|
Для зубофрезерования С′расч фр = 9,8/2 = 4,9, а значит, расчетное количество зубофрезерных станков Срасч фр = 5. В этом случае коэффициент загрузки К 3 фр = 0,98, что больше рекомендуемого в табл. 7.5 значения. Следовательно, количество зубофрезеровальных станков Сп фр= Срасч фр/ К и = 5/0,85 ≈ 6.
Для переменно-поточных и групповых поточных линий количество станков на каждую операцию рассчитывают по штучно-калькуляционному времени и программе выпуска каждой закрепленной за линией детали:
Где — штучно-калькуляционное время изготовления i -й детали на данной операции (станке), мин; N i — годовая программа выпуска i -х деталей; Фоб — эффективный годовой фонд времени работы оборудования, ч; п — число различных деталей, изготовляемых на линии.
При отсутствии данных о подготовительно-заключительном времени расчет количества станков на каждую операцию переменно-поточной линии можно вести по штучному времени t ш i:
где — коэффициент переналадки, принимаемый обычно равным 0,95 (для ГПЛ, не требующих переналадки,
= 1). Расчетное количество станков Срасч, как и в предыдущих случаях, получают округлением значения С’расч до ближайшего большего целого числа, а принятое количество станков Сп определяют с учетом рекомендуемых значений К3 и Ки.
Если многопредметная поточная линия работает с разным тактом при обработке каждой детали, то необходимым условием выполнения заданной программы по всей номенклатуре выпускаемых деталей является следующее соотношение:
Указанное выражение получено из условия, что фактическое время работы оборудования не может превышать эффективный фонд времени с учетом потерь на переналадку.
Качество проектирования поточной обработки в значительной степени определяется средним значением произведения коэффициентов загрузки и использования станков поточной линии, которое должно быть не менее 0,7.
|
В условиях непоточного производства количество станков определяют по каждому типоразмеру оборудования для каждого участка на основе данных о станкоемкости деталей, закрепленных для обработки за данным участком. Расчетное значение
Суммарная годовая станкоемкость обработки деталей на участке, имеющем станки данного типоразмера,
где — штучно-калькуляционное время выполнения j -й операции обработки i -й детали; п — число разных деталей, обрабатываемых на станках данного типоразмера; т — число операций обработки i -й детали на станках данного типоразмера.
ления заусенцев, контрольные стенды), доля которого составляет 5...30 % от основного. Таким образом, общее количество станков
С = (1,05... 1,3)СП.
При укрупненных расчетах можно использовать так называемый метод условной производительности. Сущность его заключается в том, что для оценки возможного уменьшения станко- емкости изготовления деталей изделия в новом варианте по сравнению с базовым рассчитывают условную производительность существующей (базовой) и проектируемой (новой) структуры оборудования (табл. 7.6). При этом выбор структуры оборудования будущего цеха в значительной степени определяется опытом и квалификацией проектантов.
Таблица 7.6
Таблица для расчета условной производительности структуры оборудования
Вид оборудования | Структура парка станков, %, для варианта | Коэффиент прогрессив- ности | Условная производительность для структуры | ||
базового | проекти- руемого | базовой | проектируемой | ||
Токарные станки: универсальные с ЧПУ Фрезерные станки: горизонтальные и вертикальные с ЧПУ Многоцелевые станки . . . Всего | A б — С б D б — 100 | A н Вн C н D н I н 100 | а b c d i — | Аб a — Сбс D б d — ∑б | Ана Вн b Снc D н d I н i ∑н |
В первую графу таблицы вносят новые виды технологического оборудования, а в третьей указывают процентное отношение числа единиц оборудования каждого вида по новому варианту к общему числу станков. Для каждого типа оборудования приводят коэффициент прогрессивности, под которым понимают число простых универсальных станков, производительность которых равна
|
производительности рассматриваемого станка, участка AЛ, ГПМ и т. д. В последние графы таблицы записывают условную производительность каждого оборудования по базовому и проектируемому вариантам, определенную как произведение доли оборудования данного вида в структуре и коэффициента прогрессивности. Суммированием по вертикали данных, приведенных в этих графах, определяют условную производительность оборудования цеха по базовому и новому вариантам соответственно.
Коэффициент характеризует увеличение условной производительности проектируемой структуры по сравнению с базовой. Обратная ему величина Ку = 1/
представляет собой коэффициент ужесточения, который выражает уменьшение станкоемкости изготовления аналогичных деталей в цехе с новой структурой оборудования, предусматривающей большую долю прогрессивного и высокопроизводительного оборудования, по сравнению с базовым вариантом. Коэффициент ужесточения используют для коррекции станкоемкости изготовления деталей по базовому варианту. Если изделия, выпускаемые в проектируемом и базовом цехах, отличаются, то в расчет вводят коэффициенты приведения по массе
и сложности
. Скорректированную таким образом станкоемкость изготовления деталей определяют по формуле
Общее количество станков в проектируемом цехе вычисляют по формуле
где — годовой выпуск i -го изделия, закрепленного за цехом.
Далее в соответствии с принятой структурой оборудования находят количество станков каждого типа:
…,
и уточняют общее количество основных станков.
Условная производительность станков отдельных видов приведена ниже:
Токарные:
универсальные............................ 1,0
револьверные............................. 3,5
гидрокопировальные......................4—5
с ЧПУ....................................2-4
многоцелевые.............................5—6
Вертикально-сверлильные:
одношпиндельные......................... 1,0
с ЧПУ................................... 3-4
Многоцелевые ............................. 4—6
Протяжные.................................. 6
Шлифовальные:
однокамневые............................ 1,0
многокамневые........................... 5,0
Бесцентрово-шлифовальные ...................5,0
Следует иметь в виду, что условная производительность многих станков, особенно с ЧПУ, зависит от сложности изготовляемых деталей: чем сложнее детали, тем больше условная производительность оборудования. На условную производительность станка влияет также интенсивность режимов резания, определяемая применением высокопроизводительных материалов для режущей части инструментов.
|
Расчет числа рабочих мест
Число рабочих мест для поточной линии сборки при детальном проектировании вычисляют для каждой сборочной операции исходя из ее содержания, штучного времени t ш и такта выпуска т по формуле
где P — число рабочих на данном рабочем месте.
Полученное расчетное значение числа рабочих мест сборки округляют до ближайшего большего целого числа Мсб.
При выполнении сборки на конвейере необходимо определить скорость и тип конвейера. Расчетная скорость конвейера
Как правило, шаг конвейера
где — габаритный размер собираемого изделия в направлении перемещения;
— расстояние между собираемыми изделиями, определяемое удобством выполнения сборочных работ и применяемым сборочным оборудованием, оснасткой и другими факторами.
Скорость непрерывно движущегося конвейера обычно находится в пределах 0,5...5,5 м/мин для общей сборки крупных изделий (автомобилей, тракторов) и 0,3...1,5 м/мин — для сборки узлов средних размеров, аппаратуры и приборов. Если расчетная скорость оказывается выше этих значений, необходимо организовать работу на двух и более параллельных конвейерах, увеличив соответственно такт сборки, если ниже — то сборку целесообразно выполнять на периодически движущемся конвейере.
Содержание сборочных операций устанавливают в соответствии с выбранным тактом сборки, чтобы обеспечить равномерную загрузку рабочих мест (позиций) сборки, определяемую коэффициентом загрузки .
Число рабочих мест на операции, выполняемой на конвейере с периодическим движением, рассчитывают с учетом дополнительного времени на перемещение собираемых изделий конвейером, поскольку оно осуществляется после выполнения всех операций на каждом рабочем месте:
Время перемещения изделий зависит от скорости перемещения
которая изменяется от 5 м/мин при сборке тяжелых изделий на длинных конвейерах до 15...20 м/мин — при сборке мелких узлов и изделий.
Общее число рабочих мест сборки на конвейере
где п — число сборочных операций на конвейере, включая и контрольные операции; Мрез — число резервных постов, потребность в которых может возникнуть в процессе модернизации изделия; обычно Мрез составляет 5... 10 % от .
Для сборки небольших сборочных единиц поточные линии обычно не предусматривают. Необходимое число рабочих мест сборки в этом случае определяют по формуле
|
где — трудоемкость сборки изделия, мин;
— эффективный годовой фонд времени рабочего места, ч; Р — численность рабочих на одном рабочем месте.
Число рабочих мест (стендов) непоточной сборки при детальном проектировании определяют исходя из трудоемкости сборочных работ, а также технологических особенностей собираемых на участке сборочных единиц и изделий. Для этого анализируют содержание ТП сборки, выявляют необходимую сборочную оснастку, механизированный инструмент и оборудование. На основе этого анализа определяют типы сборочных стендов и дополнительное оборудование рабочих мест для запрессовки, шлифования в целях пригонки, сверления по месту и т. д.
Число сборочных мест (стендов) каждого типа рассчитывают по годовой трудоемкости выполняемых на этих стендах сборочных работ, фонду времени рабочего места
и плотности работы П, т. е. среднему числу рабочих, одновременно работающих на одном рабочем месте:
Под плотностью работы понимают среднее количество рабочих на одном рабочем месте. В зависимости от габаритных размеров собираемого изделия, характера выполняемых сборочных работ и других условий, обеспечивающих возможность одновременной работы сборщиков с разных сторон изделия, принимают П = 1...4. Данные о фондах времени рабочих мест сборки приведены в табл. 7.1. Годовая трудоемкость сборочных работ, выполняемых на сборочных местах (стендах),
где — трудоемкость сборки i -го изделия или сборочной единицы; п — число типов собираемых изделий.
Как и при определении количества станков, расчетное значение М'с6 округляют до ближайшего целого числа и вычисляют коэффициент загрузки сборочных мест. Подобные расчеты выполняют для всех участков сборочного цеха или отделения — участков слесарной пригонки, узловой и общей сборки. Если в состав сборочного цеха входит окрасочное отделение, то определяют необходимое число рабочих мест (стендов) для подготовки поверхности изделий под окраску, для окраски и сушки изделий.
Необходимое количество оборудования (прессов, металлорежущих станков) для выполнения сборочных работ устанавливают исходя из соответствующей годовой трудоемкости (станкоемкости) по методике, применяемой при вычислении количества станков для механического цеха. По результатам выполненных расчетов составляют заявочную ведомость в соответствии с формой, установленной эталоном рабочего проекта, в которой указывают модель, мощность, балансовую стоимость и массу каждого станка. В дальнейшем эти данные используют для разработки энергетической, строительной и других частей проекта. На специальные станки и AJI разрабатывают технические задания для их проектирования и изготовления.
7.4.5. Компоновочные схемы цехов, планировка оборудования и рабочих мест
Проектирование является итерационным процессом, когда на каждом шаге ввиду недостатка информации вначале принимают приближенное решение, которое затем по мере детальной проработки уточняют. Так, после синтеза структуры цеха, т. е. установления состава его участков и количества станков, принимают решение о взаимном размещении этих участков. Выбор варианта размещения участков определяет компоновочную схему цеха (рис. 7.3).
Размещение участков внутри цеха обусловливается взаимным размещением механических и сборочных цехов, что, в свою очередь, определяется принятой организационной формой механосборочного производства.
В поточно-массовом производстве рабочие места узловой сборки предметно-специализированных цехов располагают в кон це линии механической обработки. Механосборочный цех при этом состоит из ряда параллельно расположенных участков механической обработки (см. рис. 7.3, а, б), состоящих из непрерывно- или переменно-поточных линий, а также линий или участков узловой сборки. Перпендикулярно им размещают отделение общей сборки. При использовании сборочного конвейера участки механосборочного производства располагают в соответствии с последовательностью установки сборочных единиц и деталей в изделие на конвейере. При этом обеспечиваются наиболее благоприятные условия передачи изготовленных деталей и сборочных единиц на конвейер общей сборки в процессе прямоточной межоперационной передачи. Вариант расположения общей сборки в середине цеха используют при производстве изделий с большим числом коротких линий механической обработки и относительно небольшой трудоемкости общей сборки.
В серийном и единичном производствах применяют компоновочные схемы размещения цеха (отделения) общей сборки в отдельном пролете перпендикулярно или параллельно пролетам или участкам механических цехов (рис. 7.3, в, г).
Рис. 7.3. Компоновочные схемы механосборочного производства
При этом сборка, как правило, стационарная, непоточная, поэтому взаимное размещение участков в большей степени определяет технологическая однородность обрабатываемых деталей и применяемых видов транспорта. По этой причине, например, в одном пролете, оборудованном мостовым краном, сосредоточивают обработку наиболее крупных базовых деталей. При параллельном расположении пролетов участок базовых деталей целесообразно располагать рядом с пролетом сборочного цеха с тем, чтобы минимизировать грузопоток и облегчить передачу наиболее тяжелых деталей на сборку.
На выбор варианта расположения участков также оказывают влияние условия работы и технологические особенности используемого оборудования. Поэтому нецелесообразно размещать рядом участки и линии изготовления высокоточных и относительно грубых деталей ввиду неизбежного влияния вибрации оборудования для черновой обработки на точность обработки ответственных деталей. В обоснованных случаях для финишных операций изготовления деталей и сборки прецизионных изделий предусматривают термоконстантные помещения. Недопустимо смежное размещение участков абразивной обработки и сборки. В каждом конкретном случае необходимо учитывать совместимость ТП смежных участков и цехов, степень пожарной опасности оборудования и процесса, а также концентрацию вредных для здоровья окружающих аэрозолей, выделяемых при работе оборудования. Пожароопасные или опасные для здоровья окружающих участки или производства должны быть изолированы от других помещений соответствующими перегородками и оборудованы системами очистки воздуха. Это в первую очередь касается окрасочных участков и цехов.
При предварительной проработке компоновочной схемы общую площадь участка и цеха определяют по показателю удельной общей площади
на один станок или S ' ya общ на одно рабочее место:
или
Значение показателя зависит от габаритных размеров применяемого оборудования и транспортных средств. Последние определяют ширину проездов между рядами станков. Так,
= 18...22 м2 для средних станков и 14...18 м2 для мелких. Поскольку в составе участка (цеха) имеется оборудование разных габаритных размеров, то для предварительной оценки требуемой площади удобнее пользоваться удельными показателями для аналогичных цехов, обобщенных по ряду действующих заводов или ранее выполненных проектов. Такие показатели для механических и сборочных цехов приведены в справочной литературе.
Важным при проектировании является выбор строительных параметров здания — сетки колонн и высоты пролета (рис. 7.4). Сетку колонн (ширину пролета L и шаг колонн t в метрах) и высоту пролета Н (расстояние от пола до нижней части несущей конструкции здания) выбирают из унифицированного ряда их значений. При этом ширину пролета назначают такой, чтобы можно было рационально разместить кратное число рядов оборудования — обычно от двух до четырех рядов в зависимости от габаритных размеров станков и варианта их размещения. Для определения высоты пролета сначала, исходя из максимального габаритного размера оборудования по высоте, минимального расстояния
между оборудованием и перемещаемым грузом, а также размеров
и
транспортируемых грузов и подъемно-транспортного средства (крана) соответственно, находят высоту
до головки подкранового рельса:
=
+
+
+
(см. рис. 7.4).
При этом высоту устанавливают с учетом крайних положений подвижных частей станка, причем значение ее должно быть не менее 2,3 м, а расстояние
принимают не менее 400 мм. По высоте
устанавливают минимальную высоту пролета Hmin.
При проектировании участков и цехов ГАП целесообразно использовать пролеты с мостовыми кранами, причем одна из причин применения мостовых кранов состоит в обеспечении высокой мобильности при перестановке и замене оборудования. В цехах автотракторной промышленности в основном используют здания, оборудованные подвесными конвейерами, монорельсами и кран-балками.
Рис. 7.4. Схема поперечного разреза пролета и его план:
1 — кабина крана; 2 — ось подкрановых путей; 3 — продольная разби- вочная ось; 4 — станок; 5 — поперечная разбивочная ось;(1),(2),... — поперечные разбивочные оси; (Б), (В),... — продольные разбивочные оси
Наиболее часто в одноэтажных производственных зданиях пролеты имеют ширину 18 или 24 м при шаге колонн t = 12 м. При отсутствии мостовых кранов высоту пролетов принимают равной 6; 7,2 или 8,4 м; для крановых зданий она несколько больше: 8,4; 9,6; 10,8; 12,6 м и более.
Длину станочных участков и линий из соображений пожарной безопасности принимают в пределах 35...50 м, а между ними предусматривают магистральные (пожарные) проезды шириной 4,5...5,5 м. По известной производственной площади участков определяют их ширину.
Имея габаритные размеры участков с учетом наличия продольного и поперечных магистральных проездов, определяют габаритные размеры и ориентировочную площадь цеха.
Для многоэтажных производственных зданий принята сетка колонн 9x6 м при допускаемой нагрузке на перекрытия до 15 кПа и 6x6 м при допускаемой нагрузке до 25 кПа. Высота этажей составляет 3,6; 4,8 или 6 м, причем последний этаж может быть с большей шириной пролета.
Планировка оборудования на участках и линиях механической обработки определяется организационной формой производственного процесса, длиной станочных участков, количеством станков, видом межоперационного транспорта, способом удаления стружки и другими факторами. При оформлении планировки используют условные обозначения, приведенные в табл. 7.7.
Последовательность размещения станков непрерывно- и переменно-поточных линий практически однозначно определяется последовательностью выполнения операций ТП. Задача рационального размещения оборудования сводится к выбору варианта размещения станков относительно транспортного средства, числа рядов станков и общей конфигурации поточной (автоматической) линии.
Таблица 7.7
Условные обозначения элементов на планировка
Элемент | Обозначение | |
Стены и перегородки вновь проектируемые Вновь проектируемые наружные стены с остеклением Перегородки щитовые остекленные Границы участков Цеховые проезды и проходы
Категория (числитель) и класс (знаменатель) помещения по взрыво- и пожароопасности Проемы ворот и дверей Запасной выход Кран подвесной электрический, управление с пола Оборудование, обслуживаемое одним рабочим (33 — номер оборудования в спецификации, 616 — номер цеха) Оборудование при многостаночном обслуживании Стеллаж Электрический щит Потребитель сжатого воздуха низкого давления (до 0,7 МПа) для обдува, пневмоиспытаний и пневмоци-линдров Отсос воздуха Потребитель холодной воды Отвод холодной воды Потребитель эмульсии Потребитель пара
Отвод конденсата
Потребитель масла Потребитель керосина Потребитель бензина Потребитель электроэнергии Пульт управления Электрический шкаф Точка замера концентрации паров взрывоопасных веществ Розетка штепсельная напряжением 220, 380 или 36 В | ![]() ![]() ![]() ![]() ![]() ![]() ![]() | |
Относительно транспортного средства возможны варианты продольного, поперечного, углового и кольцевого размещения станков (рис. 7.5). Продольное размещение станков фронтом к транспортному средству или проезду обеспечивает наиболее благоприятные условия для механизации и автоматизации межопе- рационного транспортирования и обслуживания рабочих мест. При поперечном расположении условия обслуживания станка оператором ухудшаются в связи с его удалением от рольганга или конвейера. Однако при использовании для автоматической загрузки станков-манипуляторов или промышленных роботов портального типа это противоречие решается, и при этом варианте обеспечивается компактность планировки, т. е. лучшее использование производственной площади. Расположение станков под углом к проезду применяют для расточных, продольно-фрезерных станков, прутковых автоматов, револьверных и других станков, длина которых значительно превышает их ширину. Прутковые автоматы при этом размещают обычно загрузочным устройством к проезду для облегчения установки прутков. Кольцевое
расположение станков создает благоприятные условия для многостаночного обслуживания, но при этом возникают трудности для использования межоперационного транспорта и инженерных коммуникаций.
Рис. 7.5. Варианты размещения станков относительно транспортного средства: а — продольное; б — поперечное; в — угловое; г — кольцевое
Выбор того или иного варианта определяется также способом удаления от станков стружки. При использовании автоматизированных систем уборки стружки необходимо учитывать взаимное расположение станочных и цеховых стружкоуборочных транспортеров.
В зависимости от длин технологического потока и станочного участка применяют однорядное или многорядное размещение станков. При этом для обеспечения прямоточности начало линий (зону заготовок) располагают со стороны проезда, а конец — с противоположной стороны в направлении дальнейшего перемещения деталей на сборку. Основные варианты размещения оборудования в непрерывно- и переменно-поточных линиях показаны на рис. 7.6.
Для линии, оборудование которой размещено в пределах длины участка, применяют однорядный вариант размещения (см. рис. 7.6, а). В приведенном примере на второй операции предусмотрены два станка, поскольку штучное время на этой операции превышает такт выпуска. Короткие линии обработки располагают последовательно, как это показано на рис. 7.6, б. Поточные линии с большим числом станков размещают в два или несколько рядов (см. рис. 7.6, в, г), но с обязательным условием, чтобы начало линии располагалось со стороны проезда и зоны заготовки, а конец — с противоположной стороны.
Рис. 7.6. Варианты размещения оборудования в поточных линиях
Для обеспечения лучшего использования отдельных станков возможно параллельное размещение линий с использованием «общего» оборудования (см. рис. 7.6, д), однако в этом случае перед «общим» оборудованием необходимо предусматривать заделы для компенсации определенной несинхронности работы двух линий. На рис. 7.6, д «общее» оборудование двух линий заштриховано.
Значительно сложнее выбрать оптимальный вариант размещения станков для подетально-специализированных участков серийного производства. На этих линиях можно одновременно обрабатывать партии разных деталей, поэтому вариант размещения будет влиять на транспортные расходы, себестоимость продукции и капитальные вложения, на непрерывность и ритмичность производства.
Возможны три различных варианта расположения станков на предметно-замкнутых (подетально-специализированных) участках: точечный, при котором отсутствуют кооперативные связи между станками;
рядный, когда оборудование размещено в линейной последовательности, соответствующей ходу ТП характерной детали;
гнездовой, при котором станки располагают группами в зависимости от кооперативных связей между ними.
Точечный вариант расположения станков возможен при полной обработке деталей на одном станке. Применяют его в тяжелом машиностроении при обработке крупных деталей, а в легком и среднем машиностроении — при использовании станков типа обрабатывающий центр, а также на автоматных участках обработки несложных деталей.
Рядный и гнездовой варианты расположения станков характерны для групповых поточных линий, где в зависимости от степени синхронизации работа возможна на переменно-поточной линии с определенным тактом или на несинхронной (прямоточной) линии. Применяют также комбинации указанных вариантов расположения станков внутри одного участка.
При выборе того или иного варианта в качестве основного параметра, влияющего в наибольшей степени на эффективность работы участка и линии, обычно используют грузооборот участка, характеризуемый грузопотоком между рабочими местами
и
:
где р — число деталемаршрутов между рабочими местами и
;
— годовой объем выпуска и масса k -й детали соответственно.
При точечном варианте расположения оборудования, когда перемещение деталей осуществляют со склада к рабочему месту и обратно, рабочие места с наибольшей интенсивностью грузопотока размещают ближе к складу и наоборот.
Сложнее решить задачу для линейного и гнездового вариантов расположения оборудования. Задача оптимального размещения рабочих мест на участке в общем виде может быть сформулирована так. Известна матрица грузопотоков между станками (рабочими местами) размерностью (где
— число рабочих мест на участке), места расположения площадок для рабочих мест и расстояния между ними. Матрица расстояний также имеет размерность
. В качестве допустимого множества площадок обычно берут узлы прямоугольной или треугольной решетки либо фиксированные точки на плоскости. Надо расположить рабочие места по узлам решетки или в точках плоскости таким образом, чтобы мощность грузопотока, определяемая суммой произведений грузопотоков на соответствующие расстояния, была минимальной:
при условии
где — булева переменная, показывающая размещено ли
-е рабочее место на
- й площадке;
— булева переменная, показывающая размещено ли
-е рабочее место на
-й площадке; —
грузопоток с
- го рабочего места на
-е;
—расстояние между
-й и
-й площадками.
Сформулированная задача в математической постановке сводится к «задаче о назначениях» и может быть решена с помощью точного алгоритма. На практике такой метод решения возможен при небольшом числе рабочих мест (обычно не более 7), так как резко возрастает размерность матриц, что затрудняет расчеты даже с и
|
|
Двойное оплодотворение у цветковых растений: Оплодотворение - это процесс слияния мужской и женской половых клеток с образованием зиготы...
Своеобразие русской архитектуры: Основной материал – дерево – быстрота постройки, но недолговечность и необходимость деления...
Опора деревянной одностоечной и способы укрепление угловых опор: Опоры ВЛ - конструкции, предназначенные для поддерживания проводов на необходимой высоте над землей, водой...
Таксономические единицы (категории) растений: Каждая система классификации состоит из определённых соподчиненных друг другу...
© cyberpedia.su 2017-2024 - Не является автором материалов. Исключительное право сохранено за автором текста.
Если вы не хотите, чтобы данный материал был у нас на сайте, перейдите по ссылке: Нарушение авторских прав. Мы поможем в написании вашей работы!