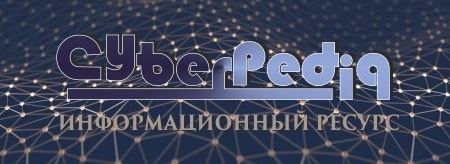
Типы сооружений для обработки осадков: Септиками называются сооружения, в которых одновременно происходят осветление сточной жидкости...
Двойное оплодотворение у цветковых растений: Оплодотворение - это процесс слияния мужской и женской половых клеток с образованием зиготы...
Топ:
Характеристика АТП и сварочно-жестяницкого участка: Транспорт в настоящее время является одной из важнейших отраслей народного хозяйства...
Методика измерений сопротивления растеканию тока анодного заземления: Анодный заземлитель (анод) – проводник, погруженный в электролитическую среду (грунт, раствор электролита) и подключенный к положительному...
Основы обеспечения единства измерений: Обеспечение единства измерений - деятельность метрологических служб, направленная на достижение...
Интересное:
Уполаживание и террасирование склонов: Если глубина оврага более 5 м необходимо устройство берм. Варианты использования оврагов для градостроительных целей...
Принципы управления денежными потоками: одним из методов контроля за состоянием денежной наличности является...
Наиболее распространенные виды рака: Раковая опухоль — это самостоятельное новообразование, которое может возникнуть и от повышенного давления...
Дисциплины:
![]() |
![]() |
5.00
из
|
Заказать работу |
|
|
Производственную программу цеха, участка — совокупность изделий установленной номенклатуры, выпускаемых в заданном объеме в течение года, — определяют исходя из производственной программы завода с учетом установленного процента запасных частей. В условиях рынка необходимо иметь резервные мощности для маневра, поэтому этот фактор также должен быть учтен при определении производственной программы.
В зависимости от типа производства и этапа проектирования производственная программа может быть точной, приведенной и условной.
Проектирование по точной программе предусматривает разработку подробных ТП обработки или сборки с техническим нормированием на все детали или сборочные единицы, входящие в производственную программу. Этот метод применяют для проектирования участков, отделений и цехов крупносерийного и массового производства. В этом случае производственная программа представляет собой ведомость, включающую полный перечень деталей или сборочных единиц, подлежащих обработке или сборке в данном цехе, с указанием их количества и массы, а для механических цехов — вида заготовок и материалов.
Проектирование по приведенной программе применяют для проектирования цехов средне- и мелкосерийного производства. Это объясняется тем, что при значительной номенклатуре объем проектных и технологических разработок становится очень большим и для его сокращения реальную многономенклатурную программу заменяют приведенной, выраженной ограниченным числом представителей и эквивалентной по трудоемкости фактической многономенклатурной программе.
С этой целью все детали или сборочные единицы разбивают на группы по конструктивным и технологическим признакам. В каждой группе выбирают деталь или сборочную единицу-пред- ставитель, по которой далее проводят расчеты. На указанные представители разрабатывают ТП обработки или сборки и путем технического нормирования или иным способом определяют трудоемкость их обработки или сборки. Рекомендуются следующие соотношения между массой и годовым объемом выпуска объекта-представителя и других объектов производства, входящих в группу:
|
0,5 m max ≤ т ≤ 2 т min
0,1 N max ≤ N ≤ 10 N min,
где m max, т min; N max, N min — соответственно наибольшие и наименьшие массы и годовые объемы выпуска объектов производства, входящих в группу.
Если указанные соотношения не выдерживаются, группу необходимо разделить на две или более групп. Вопрос формирования групп и выбора типовых представителей является очень ответственным, так как от этого зависит точность последующих технологических расчетов и проектных решений.
В практике проектирования любой объект производства, входящий в группу, может быть приведен по трудоемкости к типовому представителю с учетом различий в массе, объеме выпуска, сложности обработки или сборки и других параметрах. Общий коэффициент приведения
К пр = К 1 К 2 К 3… К n,
где К 1, К 2, К 3— коэффициенты приведения по массе, по серийности и по сложности соответственно; Кп — коэффициент приведения, учитывающий другие особенности собираемого изделия, например различие в точности изделий (в станкостроении), наличие комплектующих поставок по кооперации отдельных узлов или агрегатов и т. п.
Коэффициент приведения по массе для геометрически подобных деталей определяют по формуле
где т i, m пред — соответственно массы рассматриваемой детали и детал и - представителя.
Физически коэффициент К 1, выражает отношение площадей поверхностей детали рассматриваемой группы и детали-представителя.
Коэффициент приведения, учитывающий различия в массе собираемых изделий, определяют по формуле
|
или
где ∑ т i, ∑ m пред — соответственно суммарная масса деталей рассматриваемого изделия группы и изделия-представителя, причем первую формулу используют при большом объеме пригоночных работ, а вторую — при малом.
Коэффициент приведения по серийности учитывает изменение трудоемкости обработки или сборки при изменении годового объема выпуска. Это обусловлено, например, большей целесообразностью применения более совершенного приспособления, сокращающего время установки детали при обработке или сборке, если объем выпуска увеличивается. В практике проектирования этот коэффициент определяют по эмпирической формуле
K 2 = (N пред / Ni)α
где N пред , Ni — соответственно годовой объем выпуска изделия- представителя и приводимого изделия; а — показатель степени, равный 0,15 — для объектов легкого и среднего машиностроения и 0,2 — для объектов тяжелого машиностроения.
Коэффициент приведения по сложности К 3 учитывает влияние конструктивных факторов на станкоемкость обработки или трудоемкость сборки. Так, повышение точности обработки и ужесточение требований по шероховатости поверхности приводят к увеличению станкоемкости обработки деталей. Трудоемкость сборки, например, существенно зависит от числа сопрягаемых элементов в конструкции изделия, точности сопряжения и многих других факторов, учесть которые очень сложно. В общем виде коэффициент приведения по сложности можно представить в виде произведения коэффициентов регрессии, учитывающих корреляционные связи между конструктивными факторами и трудоемкостью приводимых изделий:
K 3 = P 1 α 1 P 2 α2 … Pnα n
где P 1 , P 2 , …, Pn — коэффициенты, учитывающие отличие соответствующих технических параметров в рассматриваемом изделии и изделии-представителе; α 1, α 2,..., ап — показатели, указывающие на степень влияния соответствующих технических параметров на трудоемкость обработки или сборки.
Для конструктивно подобных деталей обычно бывает достаточным учесть различие в точности изготовления рассматриваемой д ет али и детали-представителя, оценив, например, средний квалитет IT обрабатываемых поверхностей. В этом случае значение коэффициента К 3 можно определить по следующим данным:
|
__
IT……………… 6 7 8 11 12 13
K 3…………….. 1,3 1,2 1,1 1 0,9 0,8
Здесь средний квалитет детали-представителя принят равным IT11. В других случаях указанные значения могут быть скорректированы делением значения К 3 для рассматриваемой детали на соответствующий коэффициент детали-представителя. Например,
если квалитет детали-представителя IT8, то все значения К 3 представленного ряда необходимо разделить на 1,1.
При наличии у детали рассматриваемой группы значительных конструктивных отличий от детали-представителя коэффициент К 3 определяют экспертным путем.
Произведение всех коэффициентов приведения дает общее значение коэффициента приведения для рассматриваемой детали, сборочной единицы или изделия. Приведенную программу выпуска для каждого изделия определяют как произведение заданной программы выпуска и общего коэффициента приведения.
В результате этого вместо заданной многономенклатурной программы получают эквивалентную по трудоемкости приведенную программу, выраженную в ограниченном числе изделий- представителей:
где п — число деталей (изделий) в группе; Ni — годовой объем выпуска i -й детали (изделия); K пр i — общий коэффициент приведения детали, изделия.
По этой программе ведут все последующие расчеты, сохраняя однако неизменной общую массу изделий для проектирования транспорта и складов.
Проектирование по условной программе применяют, когда невозможно точно определить номенклатуру и технические характеристики будущих машин (опытное, единичное производство). В этом случае также выбирают изделие-представитель — условную машину, для которой ведут технологическое проектирование на заданную (условную) годовую программу.
При проектировании цеха или участка наряду с характеристикой и номенклатурой выпускаемых изделий необходимо иметь достоверные данные о трудоемкости изделия. Трудоемкостью Т изделия называют время, затраченное на его изготовление, выражаемое в человеко-часах. Определяют трудоемкость по нормативам, отражающим применение в производстве современных методов и средств. Расчетная трудоемкость включает в себя все нормируемое по ТП время, как станочное, так и ручное, причем при многостаночном обслуживании суммарное время обработки на станках, обслуживаемых одним рабочим, делят на число обслуживаемых станков.
|
При расчете количества оборудования необходимо иметь данные о станкоемкости Тст изделия, т. е. о затраченном на изготовление изделия времени, выражаемом в станко-часах работы оборудования. Связь между трудоемкостью и станкоемкостью определяется выражением:
Т = Тст / К м + Труч,
где К м — коэффициент многостаночного обслуживания, или среднее число станков, обслуживаемых одним рабочим; Труч — трудоемкость ручных операций, Труч = (0,03...0,08)Т.
В зависимости от этапа проектирования, типа производства и других факторов трудоемкость (станкоемкость) механической обработки детали или сборки изделия определяют различными способами.
Проектирование цехов и участков массового и крупносерийного производства ведут по точной программе, что предполагает наличие детально разработанных ТП обработки и сборки с техническим нормированием. При этом трудоемкость обработки комплекта деталей или сборки узлов на одно изделие для массового производства будет
а для серийного производства —
где п — число деталей в изделии при определении трудоемкости обработки или узлов — при определении трудоемкости сборки;
m — число операций обработки детали или сборки узла; t ш ij, t ш-к ij — соответственно штучное и штучно-калькуляционное время выполнения j -й операции обработки i -й детали или сборки i -го узла.
Суммарная трудоемкость сборки изделия Тсб.и дополнительно включает трудоемкость общей сборки Тобщ изделия из предварительно собранных узлов, т. е. Тсб.и = Туз + Тобщ, где Туз — трудоемкость узловой сборки.
При отсутствии детально разработанных ТП изготовления всех деталей их трудоемкость (станкоемкость) может быть определе на аналоговым методом по трудоемкости (станкоемкости) деталей-представителей с помощью коэффициента приведения:
Ти = Тпред K пр,
где Ти, Тпред — соответственно трудоемкости обработки или сборки рассматриваемой детали или изделия данной группы и детали или изделия-представителя.
При разработке проектов технического перевооружения или реконструкции цехов, а также в тех случаях, когда объектом проектирования является освоенное изделие, трудоемкость (станко- емкость) обработки деталей этого изделия или трудоемкость его сборки можно определить по заводским данным, полученным в ходе предпроектного обследования, с учетом внедрения новой технологии, средств автоматизации и механизации производственных процессов в проектируемом производстве.
|
В ходе предпроектного обследования выявляют как суммарную станкоемкость обработки деталей, так и станкоемкость обработки на основных группах оборудования, а для сборки — трудоемкости узловой сборки, слесарно-пригоночных работ, общей сборки изделия, испытания изделия в целом и его отдельных сборочных единиц.
Одновременно при этом определяют наиболее «узкие» места производства, т. е. те операции и процессы, которые в наибольшей степени сдерживают расширение производства и улучшение качества продукции. При этом устанавливают объемы работ, переводимые на станки с ЧПУ, ГПМ, многоцелевые станки и другое прогрессивное оборудование, и корректируют их с помощью коэффициента прогрессивности К пг, учитывающего более высокую производительность этого оборудования:
Тст н i = Тст i / К пг
где Тст н i, Тст i — соответственно станкоемкость i -го вида работ по проектному (новому) и базовому вариантам.
Абсолютные значения коэффициентов прогрессивности зависят от сложности обрабатываемых деталей, технического уровня действующего производства, партии запуска. Чем сложнее обрабатываемые детали, ниже технический уровень действующего производства и меньше партия запуска, тем выше значение коэффициента К пг и наоборот. Так, при переводе деталей типа тел вращения на станки с ЧПУ и ГПМ рекомендуется принимать К пг = 1,5...3, а при переводе на токарные многоцелевые станки — К пг = 4...5. При переводе корпусных деталей на многоцелевые станки и ГМП в зависимости от указанных выше факторов коэффициент К пг = 2...6.
При дипломном проектировании расчетную станкоемкость при выполнении годовой программы участка или цеха можно ориентировочно определить по формуле
Тст ∑ = Т * ст ∑ K из K у
где Т*ст ∑ — суммарная станкоемкость годового выпуска деталей по заводским данным; K из — коэффициент изменения станко- емкости для годового объема выпуска, K из = N Н / N б (NH, N б — соответственно годовой объем выпуска деталей в проектном (новом) и базовом вариантах); Ку — коэффициент ужесточения, представляющий собой отношение станкоемкости обработки деталей на участке или в цехе после внедрения новой технологии к станкоемкости обработки аналогичных деталей по действующей на заводе технологии.
Значение коэффициента ужесточения при дипломном проектировании можно определить на основе сопоставления станкоемкости обработки деталей-представителей по сравниваемым вариантам, т. е. по тем деталям, на которые разрабатывали новые ТП:
K у = Тст н / Тст б
где Тст н, Тст б — соответственно станкоемкость обработки деталей-представителей по проектному (новому) и базовому вариантам.
При механообработке трудоемкость разметочных, моечных, слесарных и других дополнительных работ зависит от типа производства (в процентах от станкоемкости): 8... 15 % — для единичного и мелкосерийного, 5... 10 % — для среднесерийного, 3...6 % — для крупносерийного и массового производства.
При укрупненном проектировании, применяемом на этапе технико-экономического обоснования проекта, станкоемкость механической обработки годового выпуска деталей изделия определяют по показателям станкоемкости механической обработки комплекта деталей одного изделия или одной тонны массы изделия.
Трудоемкость сборки изделия можно найти по станкоемкости механической обработки при изготовлении деталей данного изделия. Для этого необходимы данные о соотношении между трудоемкостью сборки и станкоемкостью механической обработки в аналогичных производствах.
Таблица 7.2
Структура трудоемкости сборочных работ в различных производствах, %
Вид сборочных работ | Тип производства | ||||
единичное | мелкосерийное | серийное | крупносерийное | массовое | |
Слесарно-сборочные работы | 25-30 | 20-25 | 15-20 | 10-15 | — |
Узловая сборка | 5-10 | 10-15 | 20-30 | 30-40 | 45-60 |
Общая сборка | 60-70 | 60-70 | 50-60 | 45-60 | 40-55 |
Трудоемкость сборки изделия подразделяют на трудоемкость слесарно-пригоночных работ, узловой и общей сборки (табл. 7.2).
Из приведенных в таблице данных следует, что в условиях единичного и мелкосерийного производства увеличивается доля слесарно-пригоночных работ и общей сборки. Это объясняется тем, что сборку в основном ведут на одном рабочем месте (стенде), а требуемая точность ответственных сопряжений обеспечивается пригонкой. В условиях массового производства в целях сокращения цикла сборки и увеличения производительности изделие разбивают на отдельные узлы, сборку которых ведут параллельно.
|
|
Историки об Елизавете Петровне: Елизавета попала между двумя встречными культурными течениями, воспитывалась среди новых европейских веяний и преданий...
Кормораздатчик мобильный электрифицированный: схема и процесс работы устройства...
Механическое удерживание земляных масс: Механическое удерживание земляных масс на склоне обеспечивают контрфорсными сооружениями различных конструкций...
Общие условия выбора системы дренажа: Система дренажа выбирается в зависимости от характера защищаемого...
© cyberpedia.su 2017-2024 - Не является автором материалов. Исключительное право сохранено за автором текста.
Если вы не хотите, чтобы данный материал был у нас на сайте, перейдите по ссылке: Нарушение авторских прав. Мы поможем в написании вашей работы!