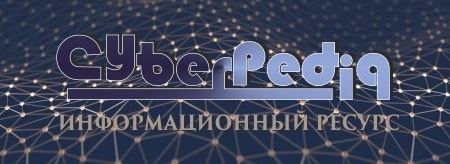
Папиллярные узоры пальцев рук - маркер спортивных способностей: дерматоглифические признаки формируются на 3-5 месяце беременности, не изменяются в течение жизни...
Наброски и зарисовки растений, плодов, цветов: Освоить конструктивное построение структуры дерева через зарисовки отдельных деревьев, группы деревьев...
Топ:
Характеристика АТП и сварочно-жестяницкого участка: Транспорт в настоящее время является одной из важнейших отраслей народного хозяйства...
Особенности труда и отдыха в условиях низких температур: К работам при низких температурах на открытом воздухе и в не отапливаемых помещениях допускаются лица не моложе 18 лет, прошедшие...
Оценка эффективности инструментов коммуникационной политики: Внешние коммуникации - обмен информацией между организацией и её внешней средой...
Интересное:
Финансовый рынок и его значение в управлении денежными потоками на современном этапе: любому предприятию для расширения производства и увеличения прибыли нужны...
Мероприятия для защиты от морозного пучения грунтов: Инженерная защита от морозного (криогенного) пучения грунтов необходима для легких малоэтажных зданий и других сооружений...
Средства для ингаляционного наркоза: Наркоз наступает в результате вдыхания (ингаляции) средств, которое осуществляют или с помощью маски...
Дисциплины:
![]() |
![]() |
5.00
из
|
Заказать работу |
|
|
При разработке проекта цеха важным этапом является синтез его структуры, т. е. обоснованный выбор состава отделений, участков и линий. Это очень сложный вопрос, требующий тщательного анализа номенклатуры и объемов выпускаемой продукции, технологии ее изготовления и организационных форм выполнения.
Относительно просто этот вопрос решается при массовом и крупносерийном производстве, где естественной является целевая предметная специализация цехов (цехи моторов, шасси и др.) и участков (участок обработки деталей и сборки коленчатого вала с маховиком, участок изготовления деталей и сборки масляного насоса и др.). Число поточных линий обработки, как правило, определяется числом изготовляемых деталей. Такая структура обеспечивает прямоточность производственного процесса, когда в конце поточных линий обработки располагаются участки узловой сборки, а дальше — сборки агрегатов или изделий.
Сложнее решить задачу структуризации для цехов среднесерийного, мелкосерийного и единичного производства, где обширная номенклатура деталей и изделий, изготовляемых последовательно на одних и тех же местах, как бы предопределяет технологическую специализацию участков с использованием однотипного оборудования (токарный, фрезерный, шлифовальный участки и т. д.). При такой структуре возникают многочисленные прямые и возвратные внешние связи между технологически специализированными участками для производства деталей множества Д (рис. 7.2, а). Это связано с тем, что рекомендации о структуре ПС преимущественно получены на основе анализа содержания операций и ТП, без рассмотрения вопросов взаимосвязи и взаимодействия операций как системы в целом.
|
При системном подходе (рис. 7.2, б) решающим является взаимосвязь, единство и эффективность работы как отдельных участков (подсистем), так и цеха (системы) в целом. Структуру ПС при этом выбирают по результатам анализа и синтеза составных частей системы как интегрированного целого объекта с качественно новыми свойствами. Причем чем ближе и полнее цель составной части соответствует цели всей ПС, тем эффективность системы выше. Поэтому при системном подходе структура производственных процессов основывается на использовании целевой подетальной или предметной специализации участков и цехов. В этом случае (см. рис. 7.2, б) цех также состоит из трех участков, но построены они по принципу подетальной специализации при пересечении внешних вертикальных и внутренних горизонтальных связей.
Рис. 7.2. Схема структуры ПС, сформированной при традиционном (а) и системном (б) подходах:
I—III— участки обработки; а, б, с — группы станков одинакового технологического назначения
Здесь конечные цели ПС складываются из целей обособленных подразделений (участков), выпускающих законченные детали-подмножества {Д1 Д2, Д3} Д, что способствует приобретению участками свойств самоорганизации и саморегулирования.
При такой форме организации ПС реализуются три структурообразующих принципа:
1) целевая подетальная или предметная специализация цехов и их участков, а следовательно, пространственная концентрация производства однородных деталей или сборочных единиц;
2) унификация ТП с использованием групповых методов изготовления деталей или сборочных единиц и, как результат, определенная концентрация, специализация и комплектность необходимого для этого оборудования или технологического оснащения;
3) централизация выдачи цехам и участкам целевых программ на изготовление комплектного состава деталей изделия со стороны органов оперативного управления, а значит, определенная концентрация во времени изготовления комплекта деталей, что важно для сокращения цикла производства законченных изделий.
|
Методика формирования подетально групповых участков, групповых поточных линий и высших их форм гибких автоматических участков и линий включает три этапа:
1) анализ номенклатуры деталей изделий по конструктивнотехнологическим признакам;
2) анализ планово-организационных характеристик деталей (их трудоемкости, программы выпуска);
3) синтез первых двух этапов и определение структуры производственных подразделений.
Рассмотрим их более подробно.
Задача анализа конструктивно-технологической общности деталей состоит в том, что все многообразие обрабатываемых в цехе деталей необходимо разделить на группы по конструктивным и технологическим признакам. С этой целью любую деталь из всей номенклатуры, выражаемой множеством Д, описывают набором признаков Р {Р i, i = 1,2,..., n }, по которым ее классифицируют. Эти признаки могут описывать: P1 — вид заготовки; Р2 — габаритные размеры деталей, определяющие возможную габаритную группу оборудования; Р3 — основной технологический маршрут, характеризуемый преобладающими видами обработки (например, токарной (Т), токарной и фрезерной (Т—Ф), токарной, фрезерной, сверлильной (Т—Ф—С), сверлильной, фрезерной, расточной (С—Ф—Р) и др.) и указывающий на комплект необходимого оборудования для основной обработки деталей группы; Р4 — конструктивный тип деталей (корпусные детали, рычаги, валы и др.), определяющий характер технологических операций и СТО и
т. д.
Анализ действующих участков с подетальной специализацией показывает, что не всегда удается обеспечить необходимую загрузку оборудования участка и линии обработкой деталей только одной конструктивно-технологической группы. При использовании групповой обработки за участками закрепляют детали, входящие в разные группы, если их можно обработать на одних и тех же станках (например, корпусные детали, рычаги, кронштейны, планки). Поэтому необходимо дополнительно группировать детали по признаку Р5 станкоемкости и объему выпуска.
В качестве показателя, синтезирующего этот признак, можно использовать относительную станкоемкость i -й детали:
где Ni — годовая программа выпуска i -й детали; k oп i — число операций обработки i -й детали; t ш ij — штучное время j -й операции обработки i -й детали; Фоб - эффективный годовой фонд времени работы оборудования; — средний коэффициент выполнения норм в цехе (учитывается при анализе действующих цехов).
|
Нетрудно заметить, что величина К дет i представляет собой расчетное количество «обезличенных» станков, необходимых для изготовления заданного объема Ni выпуска деталей при рассматриваемой технологии и режиме работы.
Относительная станкоемкость обработки К дет m по т -й группе
где f — число наименований деталей в группе.
Следует иметь в виду, что в группу могут быть включены и детали других конструктивных типов. Наиболее удобно результаты анализа представлять в виде матрицы (табл. 7.3).
Таблица 7.3
|
|
Двойное оплодотворение у цветковых растений: Оплодотворение - это процесс слияния мужской и женской половых клеток с образованием зиготы...
Опора деревянной одностоечной и способы укрепление угловых опор: Опоры ВЛ - конструкции, предназначенные для поддерживания проводов на необходимой высоте над землей, водой...
Таксономические единицы (категории) растений: Каждая система классификации состоит из определённых соподчиненных друг другу...
Индивидуальные и групповые автопоилки: для животных. Схемы и конструкции...
© cyberpedia.su 2017-2024 - Не является автором материалов. Исключительное право сохранено за автором текста.
Если вы не хотите, чтобы данный материал был у нас на сайте, перейдите по ссылке: Нарушение авторских прав. Мы поможем в написании вашей работы!