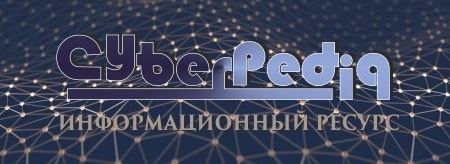
История развития хранилищ для нефти: Первые склады нефти появились в XVII веке. Они представляли собой землянные ямы-амбара глубиной 4…5 м...
Общие условия выбора системы дренажа: Система дренажа выбирается в зависимости от характера защищаемого...
Топ:
Эволюция кровеносной системы позвоночных животных: Биологическая эволюция – необратимый процесс исторического развития живой природы...
Установка замедленного коксования: Чем выше температура и ниже давление, тем место разрыва углеродной цепи всё больше смещается к её концу и значительно возрастает...
Интересное:
Уполаживание и террасирование склонов: Если глубина оврага более 5 м необходимо устройство берм. Варианты использования оврагов для градостроительных целей...
Инженерная защита территорий, зданий и сооружений от опасных геологических процессов: Изучение оползневых явлений, оценка устойчивости склонов и проектирование противооползневых сооружений — актуальнейшие задачи, стоящие перед отечественными...
Как мы говорим и как мы слушаем: общение можно сравнить с огромным зонтиком, под которым скрыто все...
Дисциплины:
![]() |
![]() |
5.00
из
|
Заказать работу |
|
|
Материальные потоки заготовок, полуфабрикатов, сборочных единиц, готовых деталей и изделий в процессе производства реализуются с помощью транспортно-складской системы. Процесс производства начинается и заканчивается на складах, где происходит преобразование параметров грузопотока. Если, например, при передаче из механического цеха М в сборочный С грузопоток по номенклатуре и интенсивности не меняется (рис. 7.18, а), то склад не требуется. Если детали из механического цеха М выходят однотипными партиями, а в сборочном цехе С требуются комплекты разных деталей для сборки изделия, то необходимо иметь склад W для преобразования параметра грузопотока (рис. 7.18, б). Динамика изменения состояния склада выражается зависимостью, приведенной на рис. 7.18, в. Масса грузов на складе характеризуется средним значением и изменяется от
до
в зависимости от массы поступающих грузов и промежутков времени между очередными поступлениями. При этом
где ,
— массы грузов на складе в моменты времени
и
соответственно;
,
— временные функции входного и выходного грузопотоков соответственно.
Рис. 7.18. Условия создания склада W (а, б) и изменение во времени массы грузов, хранимых на нем (в)
Ввиду сложности вероятностной оценки грузопотоков, возникающих в складской системе в разные моменты времени, в практике проектирования цехов пользуются нормативными данными о запасе хранения, выражаемыми числом календарных или рабочих дней, в течение которых склад может обеспечить бесперебойную работу участка или цеха, а также средним размером прибывающей или отправляемой партии грузов и периодичностью их поступления. По этим данным определяют емкость склада, тип и грузоподъемность транспортных средств, а также их количество. При детальном анализе производственных ситуаций пользуются методами имитационного моделирования.
|
Структуры складской системы и размещение ее элементов в значительной мере определяются типом производства и характером ТП. В механосборочном производстве (рис. 7.19) в начале линий механической обработки обычно предусматривают склад металла и заготовок 1. В зависимости от грузопотока и производственной мощности цеха это может быть один централизованный или несколько специализированных по видам материала или заготовок складов. При размещении нескольких цехов в одном корпусе целесообразно рассмотреть возможность создания централизованного склада заготовок.
Для хранения заготовок между операциями ТП в условиях единичного и серийного производства имеется межоперационный склад 2. Для хранения готовых деталей в структуре сборочного цеха предусматривают склад 3 с отделением или секцией для комплектования деталей в нужном количестве и ассортименте на сборку.
Рис. 7.19. Функциональная структура складской системы в механосборочном производстве
Для хранения и выдачи на сборку комплектующих изделий устраивают склад комплектующих изделий 4. Собранные и испытанные изделия поступают на склад готовых изделий 5 с экспедицией, где осуществляют окончательное комплектование изделий необходимой документацией, их упаковку и отправку потребителю.
Рассмотренная структура может видоизменяться как по составу складов, так и по их месту в производственном процессе. Так, для поточно-массового производства межоперационный склад не предусматривают. Единство целей и функций складов определяет возможность их централизации. При этом возрастает эффективность использования складского транспорта и объема складов, но удлиняются маршруты цехового транспорта. Поэтому основной критерий выбора структуры складской системы — наименьшие приведенные затраты на создание и эксплуатацию общей транспортно-складской системы.
|
Склады металла и заготовок предусматривают при механических цехах единичного и мелкосерийного производства. В состав этого склада часто входит заготовительное отделение для резки проката на штучные заготовки и зацентровки. В массовом производстве склады заготовок обычно размещают при заготовительных цехах, а в начале линий механической обработки предусматривают зону шириной 2...3 м для размещения тары с заготовками, как это показано на рис. 7.12. Исключение составляют автоматные цехи, где предусматривают склад прутковых материалов.
Штучные заготовки, а также резаный прокат хранят в таре. Применение унифицированной тары очень важно для того, чтобы исключить перекладывание заготовок при транспортировании их с других заводов в порядке кооперации, а также при межкорпусном перемещении. Заготовки в ящичной таре удобно складировать штабелем в несколько ярусов, а применение ящичных поддонов с открывающейся верхней частью одной из стенок позволяет отбирать детали из нижних поддонов штабеля, не снимая верхние поддоны. Штабельное хранение применяют также для крупных и тяжелых отливок, сварных конструкций, а также для небольших складов с однородными по номенклатуре заготовками. Укладку поддонов в штабель осуществляют напольными электропогрузчиками, высокая маневренность и высота подъема вильчатого захвата которых обеспечивает укладку пяти ярусов поддонов с заготовками. Это очень экономичный вид складирования для небольших цехов.
Склады стеллажной конструкции, более емкие по сравнению со штабельной формой хранения, занимают меньшую площадь благодаря лучшему использованию здания по высоте, а также обеспечивают возможность автоматизации складских работ. К тому же высокая устойчивость конструкции обеспечивает безопасность работы. Особенно эффективны склады стеллажной конструкции при большой номенклатуре заготовок или полуфабрикатов. При этом для груза каждого наименования отводят свою зону хранения, что обеспечивает порядок и четкую организацию складских работ.
Недостатком складов стеллажной конструкции является их малая гибкость к изменению планировки, так как для создания подобного склада требуются специальные фундаменты с закладными элементами. Поэтому создание и размещение подобных складов следует увязывать с перспективой развития цехов и завода в целом.
|
В машиностроительных цехах в основном применяют два варианта компоновки склада (рис. 7.20). В большинстве случаев используют тупиковую схему, при которой участки приема 1 и выдачи 3 заготовок размещены с одного торца склада. В этом варианте склад получается более компактным, удобна передача освобождающейся тары с одного участка на другой, оба участка могут обслуживать одни и те же рабочие. Передачу поддонов с заготовками на участки обработки осуществляют напольным или подвесным транспортом. Продольно-поперечная схема имеет преимущества в лучшей увязке с расположением производственных участков, так как участки выдачи при этом совмещены с началом линий обработки соответствующих деталей. В каждом случае выбор компоновочной схемы склада должен быть увязан с общей компоновкой цеха и принятой транспортной системой.
На рис. 7.21 показана схема планировки централизованного автоматизированного склада тупикового типа. Заготовки 1 поступают на участок временного хранения 5, оборудованный кран- балкой 3, или непосредственно на транспортер приема поддонов 4 и далее на один из участков 12—14 распределительного конвейера. После поворота поддон с заготовками попадает на одно из передаточных устройств 15, расположенных в зоне обслуживания каждого штабелера, а затем штабелером 16 помещается в соответствующую ячейку склада. Для комплектования партии запуска поддон с заготовками доставляется штабелером к передаточному устройству 15, а затем с помощью конвейеров 9 и 11 на участок комплектования 10. Здесь операторы склада отбирают необходимое количество заготовок в поддон, находящийся на столе 6.
Рис. 7.20. Тупиковая (а) и продольно-поперечная (б) компоновки склада с участками приема (1), хранения (2) и выдачи (3) грузов
Поддон с оставшимися заготовками вновь возвращается в ячейку склада, а скомплектованные для обработки заготовки передают на площадку временного хранения 7 или для отправки на участок обработки. Отсюда заготовки цеховым транспортом 8 передаются для обработки. Управление складом осуществляют с пульта 2.
|
Для ГПС и участков механосборочного производства разработан перечень автоматизированных складов для межопераци- онного хранения на базе штабелеров грузоподъемностью 0,1; 0,25; 0,5 и 1 т. На рис. 7.22 приведена конструкция и основные параметры автоматизированного склада на базе штабелера грузоподъемностью 0,25 т.
Рис. 7.21. Схема планировки автоматизированного склада тупикового типа
Рис. 7.22. Автоматизированный склад СА-0,25: электрошкафы; 2 — пульт управления; 3 — ограждение; 4 — позиции загрузки;
5 — штабелер
Высота стеллажей Нх = 4,4...10,4 м. Максимальное число ячеек по горизонтали п = 60, по вертикали — 30. Габаритные размеры тары 800x600x300 мм. Предусмотрена возможность стыковки склада с транспортной системой ГПС с обеих сторон, что позволяет обслуживать два участка. Максимальное число ячеек на складе
2 530 при его длине 41,8 м.
При укрупненном проектировании цехов площадь склада определяют на основании нормативных данных о запасах хранения заготовок, полуфабрикатов и готовых деталей, а также техникоэкономических показателей аналогичных складов по формуле
где — масса заготовок, полуфабрикатов, деталей, проходящих через цех в течение года, т; t — нормативный запас хранения грузов на складе, календарные дни; i — число поступлений на склад (для склада заготовок и деталей i = 1, для межоперацион- ного склада i = k — 1, k — среднее число операций обработки деталей на участках, обслуживаемых складом); Д — число календарных дней в году; q — средняя грузонапряженность площади склада, т/м2;
— коэффициент использования площади.
Типовые нормы для проектирования цеховых складов даны в табл. 7.11. Данные о грузонапряженности на 1 м2 полезной площади склада в таблице приведены для среднесерийного производства. Для других производств необходимо принимать следующие поправочные коэффициенты: 0,8 — для единичного и мелкосерийного; 1,1 — для крупносерийного и 1,2 — для массового. Как следует из приведенных данных, средняя грузонапряженность площади склада зависит от вида груза и способа его хранения. Наибольшие значения соответствуют многоярусному хранению грузов в стеллажных складах.
Коэффициент учитывает наличие проездов для транспортных средств и площадок приема, комплектации и выдачи грузов. Его значение принимают равным 0,25...0,3 при обслуживании склада напольным транспортом и 0,35...0,4 — при обслуживании стеллажными и мостовыми кранами-штабелерами.
Численность кладовщиков, обслуживающих склады механического и сборочного цехов, определяют при укрупненном проектировании в зависимости от количества производственных станков и численности производственных рабочих соответственно.
|
Таблица 7.11
|
|
Состав сооружений: решетки и песколовки: Решетки – это первое устройство в схеме очистных сооружений. Они представляют...
История развития хранилищ для нефти: Первые склады нефти появились в XVII веке. Они представляли собой землянные ямы-амбара глубиной 4…5 м...
Двойное оплодотворение у цветковых растений: Оплодотворение - это процесс слияния мужской и женской половых клеток с образованием зиготы...
Типы сооружений для обработки осадков: Септиками называются сооружения, в которых одновременно происходят осветление сточной жидкости...
© cyberpedia.su 2017-2024 - Не является автором материалов. Исключительное право сохранено за автором текста.
Если вы не хотите, чтобы данный материал был у нас на сайте, перейдите по ссылке: Нарушение авторских прав. Мы поможем в написании вашей работы!