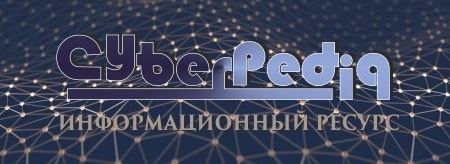
Общие условия выбора системы дренажа: Система дренажа выбирается в зависимости от характера защищаемого...
История развития хранилищ для нефти: Первые склады нефти появились в XVII веке. Они представляли собой землянные ямы-амбара глубиной 4…5 м...
Топ:
Теоретическая значимость работы: Описание теоретической значимости (ценности) результатов исследования должно присутствовать во введении...
История развития методов оптимизации: теорема Куна-Таккера, метод Лагранжа, роль выпуклости в оптимизации...
Оценка эффективности инструментов коммуникационной политики: Внешние коммуникации - обмен информацией между организацией и её внешней средой...
Интересное:
Инженерная защита территорий, зданий и сооружений от опасных геологических процессов: Изучение оползневых явлений, оценка устойчивости склонов и проектирование противооползневых сооружений — актуальнейшие задачи, стоящие перед отечественными...
Что нужно делать при лейкемии: Прежде всего, необходимо выяснить, не страдаете ли вы каким-либо душевным недугом...
Искусственное повышение поверхности территории: Варианты искусственного повышения поверхности территории необходимо выбирать на основе анализа следующих характеристик защищаемой территории...
Дисциплины:
![]() |
![]() |
5.00
из
|
Заказать работу |
|
|
С целью оптимизации процесса резания на зону резания можно оказывать воздействие с помощью различных технологических сред. К ним относятся, прежде всего, смазочно-охлаждающие технологические среды (СОТС).
Назначение СОТС:
- Смазочное воздействие для снижения интенсивности трения в зоне контакта инструмента с заготовкой и стружкой;
- Охлаждающее действие для уменьшения негативных явлений в зоне обработки, вызванных повышением температуры;
- Моющее воздействие;
- Расклинивающее действие, выламывающее действие (хрупкие материалы), т.е. предразрушающее и пластифицирующее действие по отношению к материалу заготовки.
СОТС должны обладать следующими способностями: охлаждающими, смазочными, моющими. СОТС должны обладать антикоррозионными свойствами, антипенными свойствами, нетоксичностью, бактерицидной стойкостью, недефецитностью, низкой стоимостью.
По агрегатному состоянию СОТС различают:
- Твердые;
- Жидкие (смазочно-охлаждающие жидкости – СОЖ);
- Аэрозоли;
- Газообразные.
Твердые СОТС выполняют только смазочные функции, их втирают на поверхность лезвия: графит кристаллический, дисульфит молибдена, деселенид вольфрама, твердые мыла (соли жирных кислот), воск, парафин, церезин (смесь твердых углеводородов парафинового ряда), твердые животные и синтетические мыла.
Аэрозоли. Воздушные аэрозоли СОЖ, в которых вещества находятся в дисперсном состоянии, в виде мелких капель, в струе воздуха, под давлением проникают в зазоры трущихся элементов, применяют при малом расходе.
Газы. Применяют для охлаждения и смазки. Иногда применяют обдув зоны резания воздухом, инертными газами, кислородом, парами сжиженных газов. Смазочную функцию выполняют химические пленки, образующиеся на поверхностях в зоне контакта при обдувке зоны резания.
|
СОЖ различают по химическому составу, теплопроводности, способности растекаться по металлам, проникать в зазоры и микротрещины.
По виду основы СОЖ делят на водные и масляные.
Водные СОЖ делят на:
- Электролиты (химические соединения NaCl, BaCl и другие, в которые добавляют ингибиторы коррозии, например, NaNO3);
- Синтетические и полусинтетические.
- Синтетические СОЖ – это растворы органических поверхностно-активных веществ – ПАВ – в виде органических полимеров с невысокой молекулярной массой – Аквол 10M.
- Полусинтетические СОЖ – жидкости с растворимыми в воде маловязкими минеральными и синтетическими маслами, водорастворимыми полимерами, их изготавливают в виде концентратов, которые растворяют в воде с концентрацией 2…15%;
- Эмульсии – грубодисперсные смеси взаимонерастворимых компонентов воды и капелек масла, поставляются в виде концентрата (эмульсола), который растворяется воде с концентрацией 3-10% ив основе своей содержат масла, эмульгаторы, противозадирные и антифрикционные присадки, ингибиторы коррозии и другие присадки (укрикол, Э2, ЭГ2 и др.);
- Масляные СОЖ – минеральные индустриальные масла с различными присадками (МР8, Л3 и др.).
Вид СОЖ выбирают по справочным таблицам в зависимости от вида обработки, марки материалов заготовок и инструмента, скорости резания, условий обработки, подачи и глубины резания.
2.3.5 Методика определения режимов резания
Определение оптимальных значений элементов режимы резания является актуальной задачей при технологическом проектировании.
Цель установления оптимальных технологических режимов – обеспечение требуемого качества обработки при минимизации времени и средств на обработку изделия.
Режимы резания могут устанавливаться различными методами.
Расчетно-аналитический метод базируется на использовании эмпирических зависимостей режимов резания от значения первичных технологических факторов, полученных на основе обработки результатов многочисленных экспериментальных исследований. Аналитические зависимости и числовые значения величин, приведенных в этих формулах, даются в нормативных таблицах, при этом учитываются условия выполнения рабочего перехода.
|
Табличный метод базируется на определении элементов режимов резания по нормативным таблицам. Причем табличные значения элементов режимов резания обязательно корректируются с учетом отклонений реальных условий обработки от тех, для которых разработаны нормативные таблицы.
Алгоритм определения режимов резания следующий:
- Определяется глубина резания. Глубина резания принимается равной максимальному значению припуска (на сторону) для данного рабочего перехода. Величина глубины резания не должна превышать значения, допустимые для данного станка и инструмента (по прочности). Если толщина припуска больше рекомендуемой глубины резания, этот припуск следует удалять за несколько рабочих ходов, при этом за первый рабочий ход удаляется 60-70% припуска.
Пример: обтачивается цапфа оси диаметром 5h11 из заготовки в виде круглого проката диаметром 15мм за один рабочий переход. Припуск для обточки заготовки до диаметра 5h11 с заданной шероховатостью определен расчетным путём: Zmax =0,5 мм. Общий фактический максимальный припуск на рабочий переход составляет:
Z 0=0,5(dзаг-dдет)
Z 0=0,5(15-5)=5мм.
Обработку проводим за три рабочих хода (в рамках одного рабочего перехода):
- за первый рабочий ход удаляем припуск
Z 1 =0,7* Z 0=0,7*5=3,5мм;
- за второй рабочий ход удаляем Z 2= Z 0- Z 1- Z 3
Z 2=5-3,5-0,5=1мм
- За третий рабочий ход удаляем припуск Z 3= Zmax =0,5мм.
Глубина резания при выполнении рабочего перехода за три рабочих хода: t 11=3,5мм, t 12=1,0мм, t 13=0,5мм.
Расчет усилия резания и мощности на данный рабочий переход необходимо выполнять учетом глубины резания t 11=3,5мм, соответствующей наиболее нагруженному рабочему ходу.
При выборе глубины резания можно воспользоваться рекомендациями таблицы 2.2.
Таблица 2.2 – Рекомендации по назначению глубины резания при точении
Вид точения | Точность обработки, квалитет | Требуемая шероховатость Rz, мм | Рекомендуемая макс.глубина резания t, мм |
Черновое | 12-14 | >40 | 7-9 |
Получистовое | 9-11 | 20-40 | 2-5 |
Чистовое | 7-8 | 6-20 | <0,5 |
Тонкое | 5-6 | 1,6-3,2 | 0,05-0,2 |
|
- Назначение подачи. Подачу назначают по рекомендациям нормативов и справочников[1÷7].
Подача выбирается с учетом вида обработки, глубины резания, шероховатости и размеров обрабатываемой поверхности. В общем случае выбранную подачу необходимо проверить по нескольким прочностным критериям механизма станка и обрабатывающего инструмента.
Табличные значения подачи S табл мм/об (S табл мм/зуб) корректируется с использованием поправочных коэффициентов, учитывающих реальные условия обработки:
, мм/об. (2.1)
Расчетные значения подачи следует корректировать по паспорту, принимая для дальнейших расчетов:
S пасп ≤ S расч.
- Назначение периода стойкости. Назначение периода стойкости Т, мин, производят по нормативным таблицам с учетом условий обработки, материала режущей части инструмента и обрабатываемой заготовки [1÷7].
- Определение скорости резания. Табличное значение скорости резания v табл выбирают по нормативным таблицам [1÷8] с учетом условий обработки, затем корректируют v табл c учетом реальных условий обработки, отличающихся от приведенных в таблице для выбора скоростей:
, м/мин. (2.2)
где Kvi –корректирующий коэффициент;
m – количество учитываемых факторов.
Рекомендуется выполнить расчет скорости резания по аналитической зависимости, приведенной.
- Определение частоты вращения шпинделя. Расчетное число оборотов шпинделя (главного движения) определяют по известной зависимости:
, об/мин (2.3)
где d – диаметр заготовки (сверла, фрезы) в мм.
Расчетное значение числа оборотов корректируют по паспорту станка, принимают
n пасп ≈ n расч , об/мин, (2.4)
затем рассчитывают фактическую скорость резания:
, м/мин (2.5)
Фактическое значение скорости резания не должно превышать расчетное более чем на 20%, т.е.:
|
v факт ≤1,2* v расч (2.6)
Следует сравнить значения скорости, полученные расчетным и табличным методами.
- Расчет сил резания. Выполняется по аналитическим зависимостям с учетом вида обработки (точение, сверление, зенкерование, фрезерование и др.) Pz, Py, Px [1,3,6,7,8].
- Расчет крутящего момента – Мрез, выполняется по нормативным таблицам и аналитическим зависимостям с учетом условий и вида обработки [1,3,7,8].
- Расчет необходимой мощности станка N расч. Выполняется по аналитическим зависимостям или нормативным таблицам, приведенным в справочной литературе [1,2,3,6,7,8].
Полученное значение N расч должно находиться с следующем соотношении с мощностью двигателя станка с учетом коэффициента потерь в механических передачах от двигателя к шпинделям станка – η:
1,3* N гл расч ≤ N дв *η. (2.7)
В общем случае расчетная мощность привода станка определяется с учетом мощности, затрачиваемой на главное движение N гл.дв . и на подачу Nп, т.е.:
N расч = N гл.дв + N п. (2.8)
Если необходимо использовать станок заданной модели, а его мощности недостаточно, необходимо сделать перерасчёт скорости резания, а затем и корректировку n пасп:
v рез = N дв * η / Pz, (2.9)
где N дв, b т; PZ, h.
Примеры определения режимов резания даны в [9].
|
|
Биохимия спиртового брожения: Основу технологии получения пива составляет спиртовое брожение, - при котором сахар превращается...
Своеобразие русской архитектуры: Основной материал – дерево – быстрота постройки, но недолговечность и необходимость деления...
Типы сооружений для обработки осадков: Септиками называются сооружения, в которых одновременно происходят осветление сточной жидкости...
Индивидуальные и групповые автопоилки: для животных. Схемы и конструкции...
© cyberpedia.su 2017-2024 - Не является автором материалов. Исключительное право сохранено за автором текста.
Если вы не хотите, чтобы данный материал был у нас на сайте, перейдите по ссылке: Нарушение авторских прав. Мы поможем в написании вашей работы!