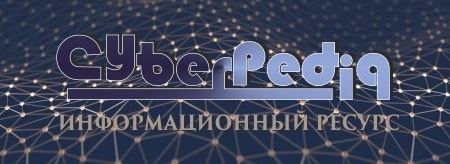
Адаптации растений и животных к жизни в горах: Большое значение для жизни организмов в горах имеют степень расчленения, крутизна и экспозиционные различия склонов...
Опора деревянной одностоечной и способы укрепление угловых опор: Опоры ВЛ - конструкции, предназначенные для поддерживания проводов на необходимой высоте над землей, водой...
Топ:
Оснащения врачебно-сестринской бригады.
Особенности труда и отдыха в условиях низких температур: К работам при низких температурах на открытом воздухе и в не отапливаемых помещениях допускаются лица не моложе 18 лет, прошедшие...
Интересное:
Распространение рака на другие отдаленные от желудка органы: Характерных симптомов рака желудка не существует. Выраженные симптомы появляются, когда опухоль...
Мероприятия для защиты от морозного пучения грунтов: Инженерная защита от морозного (криогенного) пучения грунтов необходима для легких малоэтажных зданий и других сооружений...
Аура как энергетическое поле: многослойную ауру человека можно представить себе подобным...
Дисциплины:
![]() |
![]() |
5.00
из
|
Заказать работу |
|
|
Практические занятия
По технологии приборостроения
Дисциплина «Технология приборостроения»
Специальность 200101 «Приборостроение»
Форма обучения очная
Орел 2012
Авторы: | к.т.н.профессор кафедры «Приборостроение, метрология и сертификация» ФГБОУ ВПО «Госуниверситет-УНПК» | Л.Д. Козлова |
доцент кафедры «Приборостроение, метрология и сертификация» ФГБОУ ВПО «Госуниверситет-УНПК» | В.В. Марков | |
Рецензент: | доцент кафедры «Приборостроение, метрология и сертификация» ФГБОУ ВПО «Госуниверситет-УНПК» | В.В. Мишин |
Практикум по учебной дисциплине «Технология приборостроения» предназначен для студентов, обучающихся по направлению 200101 «Приборостроение» по очной форме обучения.
Практикум может быть использован при изучении технологических дисциплин, входящих в ОПП других направлений подготовки, что будет способствовать формированию профессиональных компетенций в области производственно-технологической деятельности.
Редактор Ю.В. Касаткина
Технический редактор Н.Н. Лысых
ФГБОУ ВПО «Госуниверситет-УНПК»
Лицензия ИД №00670 от 05.01.2000 г.
Подписано к печати <дата>. Формат 60x84 1/16
Печать офсетная. Уч.-изд. л. 2. Усл. печ. л. 2,0. Тираж 15 экз.
Заказ № <число>
Отпечатано с готового оригинал-макета
на полиграфической базе ФГБОУ ВПО «Госуниверситет-УНПК»,
302020, г. Орел, ул. Московская, 65
Ó КФ Госуниверситета-УНПК, 2012
Содержание
Введение.. 5
1 Общие положения.. 6
1.1 Назначение практических занятий. 6
1.3 Требования к оформлению отчета по практическому занятию. 7
2 ПРАКТИЧЕСКОЕ ЗАНЯТИЕ №1. РАСЧЕТ РЕЖИМОВ РЕЗАНИЯ И ОСНОВНОГО ВРЕМЕНИ НА ВЫПОЛЕНИЕ ТЕХНОЛОГИЧЕСКОЙ ОПЕРАЦИИ.. 7
|
2.1 Цель занятия. 7
2.2 Содержание занятия. 8
2.3 Теоретическая часть. 8
2.3.1 Основные элементы режимов резания. 8
2.3.2 Геометрия режущей части инструмента. 10
2.3.3 Рекомендации по выбору инструментального материала. 12
2.3.4 Влияние технологических сред на процесс резания. 19
2.3.5 Методика определения режимов резания. 21
2.3.6 Определение основного времени. 24
2.4 Практическая часть. 26
2.4.1 Исходные данные. 26
2.4.2 Порядок выполнения работы.. 26
3 ПРАКТИЧЕСКОЕ ЗАНЯТИЕ №2. Определение нормы времени на технологическую операцию... 28
3.1 Цель работы.. 28
3.2 Содержание работы.. 28
3.3 Теоретическая часть. 29
3.4 Практическая часть. 51
4 Практическое занятие №4. Определение припусков и промежуточных технологических размеров.. 56
4.1 Цель занятия. 56
4.2 Содержание занятия. 56
4.3 Теоретическая часть. 56
4.4 Практическая часть. 64
4.5 Содержание отчета. 68
4.6 Контрольные вопросы.. 68
ПРИЛОЖЕНИЕ А. Форма титульного листа отчета по практическому занятию 71
ПРИЛОЖЕНИЕ Б. Экономическая точность методов обработки 72
ПРИЛОЖЕНИЕ В. Точность и качество поверхностей после механической обработки. 87
ПРИЛОЖЕНИЕ Г. Припуски на обработку. 93
Введение
Практические занятия разработаны в соответствии с ГОС ВПО по направлению подготовки дипломированного специалиста 200101 – Приборостроение.
Цель практических занятий – закрепление и углубление теоретических знаний в области технологии производства изделий приборостроения, а также приобретение практических навыков по технологическому проектированию в процессе их выполнения.
Каждая практическое занятие ПЗ состоит из трех частей. В первой части приводятся теоретические сведения, помогающие грамотно и осмысленно выполнять работу.
Во второй части приводятся исходные данные и методические указания по последовательности выполнения практического занятия.
В третьей части ПЗ излагаются требования к оформлению отчета и приводятся контрольные вопросы.
Для подготовки к практическим занятиям дан список использованных источников и приложения, в которых приводятся справочные таблицы, необходимые для выполнения задания.
|
Общие положения
Подготовка к практическим занятиям.
Подготовка кпрактическим занятиям заключается в:
-изучении теоретического материала по разделам дисциплины «Технология приборостроения», к которым относится практическое занятие;
-повторении теоретического материала из смежного курса «Технология материалов в приборостроении» по теме практического занятия №1;
-подборе нормативных материалов и справочной литературы, необходимой при выполнении работы.
Для подготовки к выполнению практических занятий в практикуме приводится теоретическая часть, а также список рекомендуемой литературы. Контрольные вопросы к практическим занятиям обеспечивают возможность самоконтроля при теоретической подготовке.
При подготовке к практическому занятию студент должен оформить титульный лист, описать исходные данные, подготовить бланки с таблицами для записи результатов расчетов.
Подготовку к практическому занятию студент выполняет самостоятельно, во внеаудиторное время. Консультации проводятся по утвержденному на кафедре графику.
1.3 Требования к оформлению отчета по практическому занятию.
В общем случае отчет должен содержать:
-титульный лист;
-тему занятия;
-описание исходных данных;
-результаты расчетов;
-выводы по полученным результатам;
-список использованных источников.
Титульный лист отчета оформляется в соответствии с приложением A.
Описание исходных данных и результатов расчётов можно представить в виде таблиц.
Формулы для расчетов приводят в символическом виде с пояснением и размерностью входящих в них величин, а затем в численном виде.
Отчет выполняется на листах формата А4 (210×297), графики и таблицы оформляются в соответствии с требованиями ГОСТ 2.105-95 с помощью чертежных инструментов.
Графики и таблицы должны быть пронумерованы и иметь соответствующие названия. Страницы отчета также нумеруются.
2 ПРАКТИЧЕСКОЕ ЗАНЯТИЕ №1. РАСЧЕТ РЕЖИМОВ РЕЗАНИЯ И ОСНОВНОГО ВРЕМЕНИ НА ВЫПОЛЕНИЕ ТЕХНОЛОГИЧЕСКОЙ ОПЕРАЦИИ
Цель занятия
Цель занятия–закрепление и углубление теоретических знаний, а также приобретение практических навыков выбора режимов резания при проектировании технологического процесса изготовления изделия.
|
Важной задачей является приобретение студентами навыков поиска и последующего использования справочной, руководящей нормативной и методической документации по выбору типа и материала режущих инструментов, смазывающе-охлаждающих жидкостей, технологических режимов времени и др.
Содержание занятия
Изучение основных элементов режимов резания, геометрии режущей части инструмента, рекомендаций по выбору инструментального материала, влияния технологических сред на процесс резания.
Знакомство с методикой определения режимов резания и основного времени, выполнение практического задания.
Теоретическая часть
Рекомендации по выбору инструментального материала
К инструментальным материалам в зависимости от метода обработки, вида обрабатывающего инструмента и условий обработки предъявляется целый ряд требований.
Требования к прочностным характеристикам. Для обеспечения необходимой стойкости инструмента соотношение между твердостью инструментального материала Hu и материала заготовки H з должно составлять: Hu / H з >2,0¸2,5.
Если обработка ведется при наличии высоких контактных циклических нагрузках, инструментальный материал должен иметь высокие значения пределов прочности на сжатие – s сж, изгиб - s u и циклические нагрузки s -1.
Инструменты, работающие в условиях ударных нагрузок должны обладать высокой ударной вязкостью.
Для снижения интенсивности трения по поверхностям лезвия необходимо, чтобы инструментальный материал в паре с обрабатываемым обладал как можно меньшим коэффициентом трения и высокой износостойкостью.
Требования к тепловым свойствам. Чтобы противостоять высоким температурам, действующим на контактных площадках лезвия, инструментальный материал должен обладать:
- высокой теплостойкостью – температурой, при которой материал теряет свои первоначальные прочностные свойства;
- высокой теплопроводностью для эффективного отвода тепла в «тело» инструмента от наиболее нагретых контактных площадок лезвия.
|
Требования к технологическим свойствам. Стоимость инструмента снижается, если инструментальный материал обладает хорошей обрабатываемостью при обработке его лезвийным и абразивным инструментами, а также при термической обработке. Хорошая обрабатываемость инструментальных сталей характеризуется:
- при термической обработке – высокой прокаливаемостью и отсутствием трещин при закалке;
- при обработке лезвийным инструментом – малой вязкостью, высокой теплопроводностью, низкой склонностью к взаимодействию с материалом инструмента и др.;
- при абразивной обработке – отсутствием «закаливания» абразивного круга обрабатываемым материалом, а также отсутствием прожогов и трещин при шлифовании (из-за высокой температуры резания в зоне резания).
Экономические требования. С целью снижения стоимости инструментов, которая переносится в себестоимость обработанного изделия, инструментальный материал не должен содержать дефицитных компонентов в исходном сырье; стоимость получения сырья и изготовления инструмента должна быть низкой.
Краткая характеристика инструментальных материалов. Обеспечить все перечисленные выше требования в одном инструментальном материале не представляется возможным, поэтому в промышленности разработан и продолжает разрабатываться широкий ассортимент инструментальных материалов, который в общем случае можно разбить на несколько групп:
- углеродистые инструментальные стали;
- низколегированные инструментальные стали;
- высоколегированные инструментальные стали (быстрорежущие стали);
- инструментальные твердые сплавы;
- минералокерамика;
- металлокерамика;
- сверхтвёрдые материалы.
Углеродистые стали появились в середине CIC века и более пятидесяти лет были единственным материалом для изготовления режущих инструментов. Содержание углерода, от которого зависят во многом свойства стали, составляет от 0,6%¸1,4%.
Для получения высокой твердости эти стали подвергаются закалке (нагревают до температуры 750-850°С с последующей закалкой в воде и дополнительном отпуске для снятия внутренних напряжений, повышения прочности и вязкости) HRC 60-62.
Материалы являются самыми дешевыми и обладают высокой технологичностью.
Выпускают 2 группы углеродистых инструментальных сталей: качественные стали (У7, У13) и высококачественные (У7А, У13А). Недостатки:
- низкая прокаливаемость и, как следствие, закалка в воде с возможным появлением трещин;
- низкая теплостойкость 200-250°С и, как следствие - низкие скорости резания 9¸15 м/мин.
Стали У7-У9 имеют высокую ударную вязкость и используются для слесарных инструментов (керны, зубила и т.д.) и деталей вырубных штампов.
|
Стали У10-У12 – более хрупкие, используются для изготовления металлорежущих инструментов, работающих на низких скоростях (мелкие сверла, метчики, прошивки, развертки).
Низколегированные инструментальные стали. Появились в конце CIC века. Это углеродистые стали, легированные хромом, вольфрамом, ванадием, кремнием (до 1% каждого компонента) и содержанием углерода 0,7¸1,3%.
Хром способствует глубокой прокаливаемости и повышению твердости, ванадий способствует образованию твердых и стойких карбидов и мелкозернистой структуры. Примером являются стали марок 7ХФ, 9Хс, ХВГ, ХВ5. После термической обработки имеют твердость HRC 62¸65, теплостойкость 250¸350°С., скорость резания 15¸25м/мин имеют улучшенную прокаливаемость, можно калить в масле, что резко снижает вероятность появления закалочных трещин. Однако у этих сталей хуже обрабатываемость: при шлифовании и заточке может появляться прижог.
Применяют для изготовления слесарных ударных инструментов, металлорежущих инструментов, работающих на невысоких скоростях, имеющих более высокую стойкость, чем углеродистые стали.
Практическая часть
Исходные данные
Исходные данные выдаются преподавателем: вид обработки, наименование операции, содержание рабочих переходов в структуре операции, модель станка, паспортные данные станка.
Исходные данные по заготовке необходимо взять из ранее выполненной самостоятельной работы.
Исходные данные необходимо представить в виде таблицы 2.3.
Таблица 2.3 – Исходные данные для практического занятия
Наименование операции | Содержание рабочих переходов | Тип станка | Тип обрабатываю-щего инструмента, размеры | |
|
| Тип приспособления |
| |
Марка СОЖ | ||||
Модель станка
Паспортные данные станка
Данные по заготовке
(инструмент показать в начале обработки и после ее завершения, дать схему базирования и закрепления, указать размеры обрабатываемой поверхности)
Марка материала
Предел прочности sв
Твердость HB
Вид исходной заготовки
Припуск (на сторону) на обработку
Порядок выполнения работы
1. Выбрать материал режущей части инструмента с указанием марки материала и его основных характеристик; [1,3,5]
2. Выбрать углы заточки режущей части инструмента (с обоснованием): g, a, j, j ¢, l, r; [1,2,3,5,6]
3. Выбрать смазочно-охлаждающую жидкость (марку, ТУ или ГОСТ). Необходимые данные занести в таблицу; [1,3,6]
4. Обосновать глубину резания t на каждом рабочем переходе;
5. Выбрать подачу S табл, S расч скорректировать по паспортным данным S пасп; [1,2,3,4,5,6,7]
6. Назначить период стойкости инструмента T (с обоснованием);
7. Выбрать табличное значение скорости резания v табл, рассчитать значение скорости с учетом корректирующих коэффициентов v расч. Рассчитать v рез по эмпирическим зависимостям, сравнить с табличным значением; [1,2,3,4,5,6,7]
8. Рассчитать число оборотов шпинделя n расч и выбрать ближайшее n пасп;
9. Рассчитать фактическую скорость резания, проверить правильность корректировки n расч;
10. Рассчитать силы резания Px, Py, Pz; [1,2,3,5,6,7,8]
11. Рассчитать момент резания; [1,2,3,5,6,7,8]
12. Рассчитать мощность, необходимую на резание, сравнить полученное значение с табличным;
13. Сделать выводы, подтверждающие обоснованность выбора инструмента и станка; [10]
14. Рассчитать основное время на выполнение операции;
15. Дать рекомендации по сокращению Т0.
2.5 Контрольные вопросы
1. Дайте определение технологического метода обработки, обработки резанием.
2. Что понимают под кинематической схемой обработки?
3. Дайте определение главного движения и скорости резания.
4. Дайте определение подачи в процессе резания. Назовите виды подач?
5. Что называют глубиной резания?
6. Назовите углы заточки режущей части резца. Каково их влияние на процесс резания?
7. Назовите основные требования к инструментальным материалам.
8. Назовите основные группы инструментальных материалов, дайте их краткую характеристику.
9. Каково назначение СОТС?
10. Перечислите виды СОТС, их назначение.
11. Назовите основные группы СОТС.
12. В какой последовательности нормируются режимы резания, какие методы используются для нормирования?
13. Как определяется основное время на выполнение рабочего перехода, технологической операции?
3 ПРАКТИЧЕСКОЕ ЗАНЯТИЕ №2. Определение нормы времени на технологическую операцию
Цель работы
Цель лабораторной работы закрепление и углубление теоретических знаний, а также приобретение практических навыков в области технического нормирования труда.
Содержание работы
Лабораторная работа включает:
– изучение теоретических сведений о нормировании времени технологических операций (значение нормирования для повышения производительности труда, нормативные материалы для нормирования, структура нормы времени, методы установления норм времени, организация оплаты труда);
– анализ исходных данных, необходимых для нормирования времени технологической операции операций;
– расчет нормы времени выполнения технологической операции;
– обоснование рекомендаций по сокращению штучного времени на выполнение технической операции.
Теоретическая часть
Организация оплаты труда
Заработная плата представляет собой часть общественного продукта, идущая на личное потребление рабочих и служащих и распределяемая в соответствии с количеством и качеством их труда.
Заработная плата регулируется следующим образом:
– планирование фондов заработной платы;
– установления дифференцированных норм оплаты труда для работников различных квалификаций и разных видов труда;
– определения конкретных форм и порядка оплаты труда разных групп работников в зависимости от организационно-технических и других условий работы.
В основе организации заработной платы лежит тарифная система, системы заработной платы рабочих, инженерно-технических работников и служащих; премиальные системы для различных категорий работников предприятия.
Тарифная система представляет собой совокупность нормативов, определяющих дифференциацию труда в зависимости от сложности труда и условий, форм заработной платы, отрасли производства и района страны. Основными элементами тарифной системы оплаты труда рабочих являются тарифные сетки, часовые ставки, тарифно-квалификационные справочники и районные коэффициенты к заработной плате. Тарифная система лежит в основе организации оплаты труда рабочих на предприятии. Рабочему присваивается определенный разряд в зависимости от уровня профессиональных знаний и трудовых навыков. Для установления разряда рабочим в цехах создаются специальные квалификационные комиссии.
Тарифная сетка – это шкала, с помощью которой дифференцируются все работы на группы (разряды) в зависимости от сложности труда, затрачиваемого на их выполнение. Для каждого разряда устанавливается коэффициент, определяющий соотношение в оплате труда данного разряда и первого (коэффициент квалификации).
Часовая тарифная ставка определяет размер оплаты труда рабочего соответствующего разряда за один час. Тарифная ставка первого разряда является основной, она задает уровень ставок в других разрядах.
Отношение часовой тарифной ставки соответствующего разряда к часовой ставке первого разряда называется тарифным коэффициентом. Разрыв в тарифных коэффициентах первого и шестого разрядов (диапазон тарифной сетки) в машиностроении составлял 1,71.
Часовые тарифные ставки дифференцированы по специальностям, а также по условиям выполнения работы (нормальные, тяжелые и вредные, особо тяжелые и особо вредные условия труда) и по системе оплаты труда (сдельная или повременная).
Месячная тарифная ставка рассчитывается путем умножения часовой ставки соответствующего разряда на число рабочих часов в месяц; дневная ставка на число рабочих часов в смену.
Система сдельной оплаты труда. Мерой количества труда выступает либо отработанное рабочим время, либо количество выработанной им продукции. Соответственно формы заработной платы могут быть повременными и сдельными. Сдельная форма оплаты может быть индивидуальной и коллективной (бригадной) и включать системы: прямую сдельную, сдельно-премиальную, прогрессивно-сдельную, косвенную сдельную и аккордную. Повременная форма применяется в виде простой повременной и повременно-премиальной систем.
Основной системой на машиностроительных предприятиях является прямая сдельная оплата. Заработная плата рабочего находится в прямой зависимости от количества выработанной им продукции (количества работы).
Применение сдельной оплаты труда экономически целесообразно при наличии количественных показателей выработки или работы в натуральных измерителях; при наличии возможностей для рабочего перевыполнить задание без изменения (и нарушения) технологического процесса; при рациональном обслуживании рабочих мест и полноценном использовании рабочего времени.
Сдельная расценка представляет собой оплату труда за единицу продукции, выплачиваемую рабочему независимо от фактически затраченного им на выполнение данной работы времени. Расценки пересматриваются одновременно с нормами времени выработки.
В зависимости от принятой на данном участке системы учета результатов работы (по отдельным рабочим, бригадам) применяют две разновидности прямой сдельной оплаты труда: индивидуальную и бригадную.
При прямой индивидуальной сдельной оплате рабочий получает оплату за все работы (количество продукции), выполненные им в течение отчетного периода по соответствующим расценкам без ограничений. Сдельная заработная плата рабочего за расчетный период может быть определена по формуле:
(3.11)
где m – число видов работ (деталеопераций), выполненных рабочим за расчётный период;
–фактическая выборка по каждому виду работ;
–расценка каждого вида работ.
При бригадной сдельной оплате труда устанавливают коллективные сдельные расценки на все виды работ.
(3.12)
где n – число членов бригады, чел;
li – тарифные ставки членов бригады, коп.;
tшк – норма времени, устанавливаемая на единицу выполняемой работы, ч.
Заработная плата всей бригады:
(3.13)
где – фактическая выработка продукции бригадой за расчётный период.
Тарифная заработная плата бригады за расчётный период:
, (3.14)
где Fi – время, отработанное каждым членом бригады за расчётный период.
Заработная плата La распределяется между членами бригады в соответствии с присвоенными им разрядами и отработанным временем.
Прогрессивно-сдельная система оплаты труда отличается от прямой сдельной. При ее применении устанавливаются дифференцированные расценки за работы, выполненные в пределах установленной нормы, или повышенные (например, полуторные и двойные расценки) за работы, выполненные сверх установленной месячной нормы выработки:
, (3.15)
где – повышенная расценка за продукцию, выполненную сверх нормы;
Nф i – фактическая выработка продукции одного рабочего за расчётный период;
Nвыр i – нормативная выработка продукции одного рабочего за расчётный период.
Эта система устанавливается в виде исключения в качестве временной оплаты труда на «узких» участках основного производства.
Косвенная сдельная система оплаты труда применяется для стимулирования производительности труда вспомогательных и обслуживающих рабочих. Для этого применяют косвенные расценки, устанавливаемые за единицу продукции, произведенной за расчетный период рабочими цеха или участка, которых обслуживают вспомогательные рабочие. По такой системе оплачиваются наладчики станков, транспортные рабочие, рабочие по дежурному обслуживанию в основных цехах и др.
Сдельная форма оплаты труда в сочетании с премированием образует сдельно-премиальную систему или аккордную.
Системы повременной оплаты труда. При повременной оплате труда мерой количества труда рабочего является только отработанное им время. Они применяются при аппаратурных процессах, при работе на конвейерных линиях, при выполнении работ, требующих большой тщательности (некоторые контрольные операции, экспериментальные работы).
Различают две системы повременной оплаты труда: простую повременную и повременно-премиальную. При простой повременной оплате труда заработная плата рабочего LП зависит от его квалификации (часовой тарифной ставки l ) и отработанного времени Тф т.е.:
. (3.16)
Материально она не побуждает рабочего к увеличению выработки, к повышению качества продукции, экономии материальных ресурсов. Чаще ее сочетают с дополнительными условиями и показателями премирования и применяют в виде повременно-премиальной системы.
Заработная плата при повременно-премиальной системе складывается из тарифной и премии, как правило, начисляемой в зависимости от тарифной заработной платы или от размера достигнутой экономии.
3.3.6 Общие рекомендации по использованию нормативов
Определение штучно-калькуляционного времени осуществляют с использованием сборника нормативных материалов для расчёта технически обоснованных норм времени на работы, выполняемые на металлообрабатывающем оборудовании в серийном производстве [11,12,13].
По указанным нормативам определяются все составляющие вспомогательного времени, время на обслуживание рабочего места (техническое и организационное, время перерывом на отдых и личные надобности) и подготовительно-заключительное время.
Основное время на выполнение всех не совмещённых рабочих переходов – То при выполнении всей операции определяется по формуле:
, (3.17)
где Toi – время выполнения i-го рабочего перехода;
m – количество несовмещенных рабочих переходов.
Основное время – То определяется при расчёте режимов резания, который выполнен на предшествующей лабораторной работе.
В нормативах предусмотрены два метода определения вспомогательного времени на операцию с различной степенью укрупнения норм в зависимости от вида применяемого оборудования и содержания выполняемой работы на технологической операции.
Первый метод. Для операций, выполняемых на универсальном оборудовании, предназначенном для выполнения нескольких рабочих переходов без замены инструмента (токарно-револьверные станки, вертикально-сверлильные станки с револьверной головкой), а также на станках за несколько рабочих переходов, требующих замену инструмента (токарно-винторезные, фрезерные), вспомогательное время определяется как сумма затрат на:
– установку и снятие детали;
– переустановку заготовки, (если это предусмотрено в операционной карте);
– времени на рабочий переход, определяемого для каждого рабочего перехода отдельно с учётом количества рабочих ходов;
– времени на изменение режимов обработки, смену инструмента и перемещения частей станка, на совмещение осей при растачивании, на выводы сверла при сверлении глубоких отверстий (для удаления стружки);
– времени на вспомогательные переходы, не вошедшее в укрупнённые комплексы (замену кондукторных втулок и др.);
– времени на контрольные измерения всех параметров, которые обеспечиваются на каждом рабочем переходе, (с учётом процента контролируемых деталей от обработанной партии деталей).
Второй метод. Для однопереходных операций, когда обработка производится без изменения технологических режимов обработки и смены инструмента, вспомогательное время дано на укрупнённый комплекс приёмов на операцию.
При выполнении лабораторной работы необходимо установить какие приёмы вошлив комплексы. Если для конкретной операции необходимы дополнительные действия рабочего, не учтённые в комплексах, то вспомогательное время на их выполнение устанавливается по нормативным таблицам и добавляется к комплексному вспомогательному времени.
Необходимо помнить о том, что в норму штучного времени включают только те составляющие вспомогательного времени, которые не перекрываются основным временем.
Пример. Обработка производится на горизонтально-фрезерном станке с использованием многоместного приспособления со сменной кассетой для установки заготовок. Время установки заготовок в сменную кассету перекрывается основным временем, в течении которого фрезеруется пакет деталей, ранее установленных и закреплённых в сменной кассете.
При определении вспомогательного времени на установку и закрепление одной заготовки необходимо время на установку и закрепление кассеты с деталями в приспособлении поделить на количество одновременно обрабатываемых деталей.
Время на установку заготовок в сменную кассету не учитывается, т.к. оно перекрывается основным временем.
Вспомогательное времени установку и снятие детали. Нормативное время на установку заготовки и снятие детали предусматривает следующие работы:
– установить и закрепить заготовку;
– включить станок (главное движение, движение подачи);
– выключить станок;
– очистить приспособление от стружки.
Если по технике безопасности допускается перемещение заготовки для последовательной обработки поверхностей детали без выключения вращения шпинделя, (последовательное сверление нескольких отверстий одного диаметра), то вспомогательное время необходимо уменьшать с указаниями, приведёнными в нормативах.
Вспомогательное время, связанное с переходом или обрабатываемой поверхностью. В нормативах эта составляющая вспомогательного времени дана по типам станков на укрупнённый комплекс приёмов, составленный по технологическим признакам и видам работ. В комплекс включены:
– подвод инструмента к заготовке;
– включение и выключение подачи;
– измерение детали при взятки пробных стружек (обработка по методу пробных проходов);
– отвод инструмента в исходное положение.
Во вспомогательное время связанное с переходом кроме затрат на комплекс приёмов включают дополнительные составляющие на приёмы, которые не вошли в комплекс (смена инструмента, смена кондукторных втулок, время на перемещение частей станка, если длина обработки превышает указанную в нормативах и др.).
Вспомогательное время на контрольные измерения обработанной детали. Устанавливается по нормативам на контрольные измерения после окончания обработки поверхности с учётом периодичности измерения, которая определяется при проектировании технологической операции.
При выполнении лабораторной работы следует принять, что 10÷15% деталей от всех обработанных на операции подлежит контролю оператором (станочником).
Время на контроль каждого из параметров, которые обеспечиваются на данной операции, устанавливается в зависимости от формы, размеров, точности и шероховатости обрабатываемой поверхности, а также вида средства измерения, а затем суммируется. В норму штучного времени (в общее вспомогательное время) включается, 10÷15% вспомогательного времени на контроль всех параметров (диаметра, длины, межосевого расстояния, шероховатости и т.п.).
Время на обслуживание рабочего места. Принимается в процентах от оперативного, процент выбирается по нормативам в зависимости от вида обработки и оборудования.
В укрупненных нормативах даётся процент для определения времени на обслуживания рабочего места, которое включает две составляющие:
– время технического обслуживания рабочего места, (смена затупившегося инструмента, правка шлифовального круга регулировки и подналадка станка в процессе работы, сметание и уборка стружки в процессе работы);
– время организационного обслуживания рабочего места (осмотри опробование в начале смены, уборка рабочего места в конце смены; получение инструктажа, раскладка инструмента в начале и уборка его в конце смены).
Время на отдых и личные надобности принимают в процентах от оперативного времени, которые устанавливаются по нормативам в зависимости от интенсивности и условий труда.
Подготовительно-заключительное время на обработку деталей партии запуска объёмом – n принимается для выполнения следующей работы:
– получение на рабочем месте наряда, технической документации, инструктажа;
– ознакомление с технической документацией;
– подготовка рабочего места, наладка оборудования, установка приспособлений и инструмента;
– пробная обработка деталей (пробной партии);
– демонтаж наладки после обработки партии запуска и сдача её в инструментальную кладовую.
При выборе подготовительно-заключительного времени необходимо учитывать условия организации труда, производится ли доставка приспособлений, инструмента на рабочее место вспомогательным рабочим или самим наладчиком. В последнем случае необходимо включить дополнительную составляющую в нормируемое подготовительно-заключительное время.
В норму полного штучного времени (штучно-калькуляционного) включается часть подготовительно-заключительного времени, приходящаяся на одну деталь партии запуска. Объём партии запуска можно определить по формуле:
, шт. (3.18)
где Nгод – годовой объём выпуска деталей данного наименования в штуках, можно принять Nгод = 2000 шт, если объём не был задан;
а – количество дней, на которые необходимо обеспечить запас деталей на сборки, можно принять дней;
Fр.в – действительный годовой фонд рабочего времени, рабочих дней.
Практическая часть
Исходные данные для выполнения практического занятия
Для выполнени
|
|
Своеобразие русской архитектуры: Основной материал – дерево – быстрота постройки, но недолговечность и необходимость деления...
Поперечные профили набережных и береговой полосы: На городских территориях берегоукрепление проектируют с учетом технических и экономических требований, но особое значение придают эстетическим...
Индивидуальные очистные сооружения: К классу индивидуальных очистных сооружений относят сооружения, пропускная способность которых...
Автоматическое растормаживание колес: Тормозные устройства колес предназначены для уменьшения длины пробега и улучшения маневрирования ВС при...
© cyberpedia.su 2017-2024 - Не является автором материалов. Исключительное право сохранено за автором текста.
Если вы не хотите, чтобы данный материал был у нас на сайте, перейдите по ссылке: Нарушение авторских прав. Мы поможем в написании вашей работы!