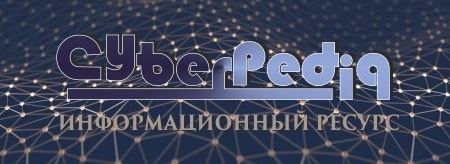
Своеобразие русской архитектуры: Основной материал – дерево – быстрота постройки, но недолговечность и необходимость деления...
Двойное оплодотворение у цветковых растений: Оплодотворение - это процесс слияния мужской и женской половых клеток с образованием зиготы...
Топ:
Оснащения врачебно-сестринской бригады.
Марксистская теория происхождения государства: По мнению Маркса и Энгельса, в основе развития общества, происходящих в нем изменений лежит...
Организация стока поверхностных вод: Наибольшее количество влаги на земном шаре испаряется с поверхности морей и океанов...
Интересное:
Лечение прогрессирующих форм рака: Одним из наиболее важных достижений экспериментальной химиотерапии опухолей, начатой в 60-х и реализованной в 70-х годах, является...
Национальное богатство страны и его составляющие: для оценки элементов национального богатства используются...
Финансовый рынок и его значение в управлении денежными потоками на современном этапе: любому предприятию для расширения производства и увеличения прибыли нужны...
Дисциплины:
![]() |
![]() |
5.00
из
|
Заказать работу |
|
|
В приводах главного движения станков с ЧПУ преимущественно применяют регулируемые приводы с двигателем постоянного тока и тиристорным преобразователем напряжений. Необходимая мощность привода главного движения станка изменяется в функции частоты вращения. Так как основную нагрузку по снятию припуска в процессе обработки несет привод главного движения, то его считают работающим в режиме постоянной мощности. Поэтому по мере уменьшения скорости исполнительного органа момент нагрузки на валу возрастает и соблюдается соотношение
Р г = М гwг = const,
где Р г – мощность привода главного движения; М г и wг – момент и частота вращения на валу привода главного движения.
Для регулирования частоты вращения в режиме автоматического управления технологическим процессом требуется непрерывное управление скоростью в диапазоне
D p = const = 1:2.
Для двигателей постоянного тока серии 2П этот диапазон
D p = const = 1:4.
Однако при обработке заготовок различного размера с помощью многих различных инструментов (многоцелевые станки) значение частоты вращения необходимо иметь в диапазоне
D p = const = 1:50.
В этом диапазоне частота вращения может изменяться ступенчато с применением дополнительной коробки скоростей.
Автоматизация переключения частот вращения в передачах осуществляется с помощью электромагнитных фрикционных муфт. Этот принцип использован в автоматических коробках скоростей типа АКС. Унифицированные коробки типа АКС позволяют реализовать все операции управления главным приводом: пуск, торможение, реверсирование, регулирование частоты вращения. Они обеспечивают высокую скорость переходных процессов, защиту от перегрузок, удобство в работе и т.д.
|
К вспомогательным операциям на станках с ЧПУ относятся: реверсирование направления вращения шпинделя и его останов; установка исполнительных органов в исходное положение; обеспечение транспортирования, зажима и разжима деталей; поиск, смена, фиксация инструмента и т.д.
Приводы вспомогательных движений должны удовлетворять следующим требованиям: высокая удельная мощность, большой крутящий момент на выходе, высокая надежность, удобство в эксплуатации. В большой степени этим требованиям соответствуют гидроприводы. Гидропривод содержит следующие основные элементы: источник гидравлического потенциала; аппаратуру, регулирующую давление и расход жидкости, а также направление ее движения; гидродвигатель, осуществляющий движение исполнительного органа станка; соединительные магистрали. Основным элементом является гидродвигатель, в качестве которого применяются гидромоторы, силовые цилиндры возвратно- поступательного и возвратно-поворотного действия. Они обладают небольшими моментом инерции и моментом трогания, высоким быстродействием, широким диапазоном регулирования.
В механизмах, где не требуется высокая выходная мощность, стабильность скорости перемещения вспомогательных органов и точное позиционирование, применяют пневматические и пневмоэлектрические приводы. Эти приводы обладают простой системой управления, высокой надежностью и малой стоимостью.
Привод подач является одним из основных узлов, который определяет производительность, точность и надежность работы станка с ЧПУ.
В позиционных и контурных СЧПУ чаще всего встречаются два типа приводов. Первым и наиболее простейшим вариантом исполнительного позиционного привода подач является электрический шаговой привод. Шаговые приводы используют несиловые и силовые шаговые двигатели. При применении несилового шагового двигателя в состав привода входит гидравлический усилитель крутящего момента. Выходной вал силового шагового двигателя непосредственно соединяется с ходовым винтом или редуктором механизма подачи.
|
Структура шагового привода с несиловым шаговым двигателем представлена на рис.69. От программо-задающего устройства импульсы в унитарном коде поступают на вход электронного коммутатора. Под действием очередного входного импульса электронный коммутатор изменяет свое состояние через усилитель мощности, переключает фазы шагового двигателя, поворачивая его ротор на угловой шаг.
Рис.69. Структурная схема с шаговым приводом
Основные характеристики шаговых двигателей: частота приемистости (мгновенный перепад частот управления, обрабатываемый шаговым двигателем без потери шага), максимальная частота управления в режиме плавного разгона и максимальный крутящий момент. Для несиловых шаговых двигателей частота приемистости не более 1000 Гц, максимальная частота равна 16...18 кГц, максимальный крутящий момент достигает 0,3 Н×м. В последнее время наблюдается устойчивая тенденция к отказу от применения несиловых и применению силовых шаговых двигателей. Большое преимущество силового шагового двигателя – отсутствие динамических погрешностей, вносимых системой усиления крутящего момента.
Преимущества шагового привода: простота конструкции и экономичность, отсутствие устройств обратной связи для измерения положения и скорости исполнительного органа, задание программы в унитарном коде. Недостатки шагового привода: ограничение по скорости, связанное с пропуском импульсов; необходимость плавного разгона и торможения; ошибки в отработке программы в случае потери импульсов. Система управления, в случае применения шагового привода, получается разомкнутой со всеми присущими ей недостатками.
В контурных СЧПУ, как правило, применяют следящий электропривод (рис.70). Управляющие импульсы от интерполятора УЧПУ поступают в цифроаналоговый преобразователь, в котором импульсный сигнал преобразуется в аналоговый. Число управляющих импульсов, поступающих от интерполятора, определяет перемещение, а их частота – скорость перемещения исполнительного органа. Заданный сигнал j3 поступает на элемент сравнения, который сравнивает j3 с сигналом j, характеризующим фактическое положение исполнительного органа. На основе сравнения сигналов j3 и j вырабатывается сигнал рассогласования e, поступающий в контур формирователя ошибки перемещения. Регулируемый привод отрабатывает сигнал рассогласования в сторону его уменьшения. Сигнал рассогласования поступает в предварительный усилитель системы импульсно-фазового управления.
|
Для увеличения диапазона регулирования привод охватывается обратной связью по частоте вращения w. Для этого на входном валу двигателя устанавливается тахогенератор, напряжение которого пропорционально угловой скорости выходного вала. Разность между заданным напряжением и напряжением от тахогенератора усиливается и подается в тиристорный преобразователь. Система импульсно-фазового управления преобразует выходное усиленное напряжение в прямоугольные импульсы, фаза которых изменяется пропорционально входному воздействию. Эти импульсы управляют тиристорами. Напряжение на входе тиристорного преобразователя пропорционально рассогласованию e и производной от рассогласования . Тиристорный преобразователь управляет двигателем, который обеспечивает через механизм подачи движение исполнительного органа с заданной скоростью и на заданное расстояние. Основной характеристикой следящего электропривода является погрешность положения e = j3 – j.
Рис.70. Структурная схема следящего электропривода в контурных СЧПУ
В приводах станков с ЧПУ нашли применение малоинерционные двигатели с гладким якорем. В этих двигателях уменьшение момента инерции достигнуто за счет резкого увеличения активной длины якоря и уменьшения его диаметра. В качестве общего недостатка, который характерен для всех типов малоинерционных двигателей, следует отметить необходимость специального динамического согласования двигателя с механической системой станка.
Увеличение динамического момента при неизменном моменте инерции достигается в высокомоментных двигателях. Высокомоментные двигатели постоянного тока выполняют с возбуждением от постоянных магнитов. Применение постоянных магнитов позволяет увеличить КПД на 10...15% и уменьшить размеры двигателя по сравнению с электромагнитным возбуждением. Постоянные магниты выполняются на основе ферритов, имеющих высокие значения напряженности магнитного поля и удельного сопротивления.
|
Отечественные тиристорные приводы с высокомоментными двигателями постоянного тока ПВБ-100, ПВБ-112 и ПВБ-132 выпускают с мощностью 0,75...5,5 кВт. Они обеспечивают диапазон регулирования 1:10000 при номинальном значении частоты вращения n = 1000 мин-1. Этот двигатель устанавливается непосредственно на ходовой винт механизма подачи станка. Привод подач с высокомоментным двигателем позволяет выполнить разгон перемещаемого исполнительного органа до максимальной скорости за весьма малое время (например, разгон до скорости 10 м/мин осуществляется примерно за 0,25 с).
В станках с ЧПУ в качестве привода подач находит применение гидропривод. Гидроприводы имеют довольно высокий КПД, равный 0,85...0,95, что выше КПД электрических приводов. Существуют две основные схемы питания гидродвигателей в гидропередачах станков с ЧПУ: от гидронасоса с регулируемой производительностью – объемное управление и от дроссельного устройства – дроссельное управление. В настоящее время в приводах подач станков с ЧПУ применяются гидроприводы объемного регулирования, которые в сравнении с гидроприводом дроссельного управления имеют более высокий КПД, меньший нагрев рабочей жидкости, обеспечивают более плавный реверс и торможение гидродвигателя.
3.9.4. Многооперационные станки с ЧПУ
В последнее время выпускают металлорежущие станки с автоматической сменой инструментов с программным управлением – так называемые многооперационные станки (обрабатывающие центры). Они предназначены для обработки корпусных деталей с отверстиями, а также деталей типа рычагов, плит, кронштейнов и т.п.
Фрезерно-сверлильно-расточные станки с автоматической сменой инструментов изготовляются как с небольшим числом инструментов, помещенных в гнездах револьверных головок, так и с очень большим числом инструментов (свыше 100), находящихся в специальных магазинах различной конструкции. Появились станки токарной группы («Торнинг-центры»), у которых вместо обычных револьверных головок применяются магазины с большим числом инструментов.
Предпосылками появления станков с автоматической сменой инструментов послужили общее повышение требований к мобильности, перенала-живаемости производственного оборудования в машиностроении и настоятельная необходимость автоматизации мелкосерийного производства.
Рассмотрим конструктивные особенности многооперационных станков. Это в основном одношпиндельные станки или станки с револьверными головками, шпиндели которых работают поочередно. Шпиндель может реверсироваться и автоматически фиксироваться в определенном угловом положении. Реверс используется при резьбонарезании метчиками, а угловая фиксация – при некоторых расточных операциях и при автоматической смене инструментов.
|
Автоматическая смена инструментов осуществляется посредством индексирования револьверной шпиндельной головки или автоматической разгрузки и загрузки шпинделя оправками с инструментами из магазина с помощью автооператоров.
Станки оборудуются приводами, допускающими автоматическое изменение режимов обработки при смене инструментов. Для обработки деталей с разных сторон станки снабжают прецизионными поворотными столами, индексирующимися через угол 90° или способными поворачиваться на разные углы, заданные программным управлением. Для совмещения времени установки новых заготовок с основным временем работы станки оснащают дополнительными устройствами, в результате чего время смены заготовок снижается до нескольких секунд. Механизмы подачи узлов станка имеют привод с безлюфтовыми зубчатыми передачами и шариковыми ходовыми винтами, чаще всего – от гидродвигателей.
Станки оборудуют позиционными или контурными системами программного управления перемещениями узлов станка, сменой инструментов и заготовок, поворотами стола с обрабатываемой деталью, автоматическим изменением частоты вращения шпинделя и скоростью подачи.
Схемы построения фрезерно-сверлильно-расточных станков разнообразны. Многооперационные станки выполняют с компоновками типа вертикально-сверлильных, горизонтально- и вертикально-фрезерных консольных и бесконсольных, координатно-расточных, продольно-фрезерных и портальных станков.
На рис.71представлена компоновка бесконсольного вертикально-фрезерного станка с револьверной головкой 1, которая установлена на шпиндельной бабке 4, перемещающейся по стойке 2 в направлении оси Z. Стол 3 с обрабатываемой деталью совершает движение подачи по направлениям X и Y. Наиболее разнообразны компоновки станков с револьверными шпиндельными головками, поскольку в них проще менять инструменты.
Наблюдается также разнообразие устройств автоматической смены инструментов и заготовок. Эти устройства оказывают существенное влияние на развитие компоновок станков, выдвигая ряд требований. Например, для обеспечения рациональной автоматической смены инструментов желательно, чтобы в компоновках выполнялись следующие условия: минимум координатных перемещений при смене инструментов, сохранение постоянства координат оси шпинделя при смене инструментов, расположение неработающих инструментов вне рабочей зоны станка и др.
Рис.71. Компоновка вертикально-фрезерного станка с револьверной головкой
На рис.72 представлена схема компоновки горизонтально-расточного станка с подвижной колонной 1. Инструменты, расположенные в магазине 2, по мере необходимости подводятся к шпинделю 3 станка и специальными устройствами устанавливаются и закрепляются в нем. Перед этим отработавший инструмент автоматически переводится из шпинделя 3 в свободное гнездо магазина 2.
Рис.72. Компоновка горизонтально-расточного станка
Решающее влияние на компоновку станка в ряде случаев может оказать способ смены заготовки, например применение двух поворотных столов или сменных поворотных столов. Индексация поворотных столов выполняется прецизионной, чтобы обеспечить соосность отверстий, растачиваемых с двух противоположных сторон обрабатываемой детали, а также перпендикулярность и параллельность обработанных плоскостей. Обычно индексирующиеся поворотные столы имеют четыре или восемь позиций, но иногда это число достигает 72. На рис.73 представлены способы кантования и смены обрабатываемых деталей на многооперационных станках. На рис.73, а обрабатываемая деталь устанавливается на поворотную плиту или приспособление 1 и подается на станок. На станке имеется устройство 2, принимающее плиту или приспособление. Устройство подводит деталь с плитой в рабочую зону к шпинделю 3 станка. Разгрузка и загрузка происходит в то время, когда приспособление 1 находится на автооператоре 4. На рис.73, б показана схема кантования детали с двумя сдвигающимися рабочими столами. Стол 5, находящийся на поворотных салазках 6, после завершения обработки детали с четырех сторон автоматически сдвигается на направляющие второй установочной позиции 7 для разгрузки-загрузки, а на его место из позиции 8 поступает второй стол с новой заготовкой.
На рис.73, в показаны два поворотных стола 5, смонтированных на неподвижном основании 9. Все координатные перемещения совершает шпиндель 3. В позиции 10 деталь обрабатывается, в позиции 11 происходит разгрузка-загрузка. Процесс смены и кантования обрабатываемых деталей на этих станках сокращен до минимума благодаря автоматизации и управлению по сигналу от системы программного управления.
На рис.74, а приведена схема многооперационного станка со сдвоенными поворотными столами 1, загружаемыми поочередно. Инструменты из магазина 2 подаются в зону резания и специальными устройствами устанавливаются в шпинделе 3 станка. На рис.74, б показана схема многооперационного станка с двумя сдвигающимися столами 1.
Рис.73. Способы кантования и смены обрабатываемых деталей
Рис.74. Схемы многооперационных станков
На рис.75, а показаны способы автоматической замены инструмента с автооператором, расположенным между магазином и шпинделем. Автооператор имеет два захвата – для отработавшего и для нового инструментов. Автоматическая смена инструмента совершается в определенной последовательности. Во время работы станка магазин 1 индексируется в положение, в котором последующий инструмент поступает в позицию разгрузки-загрузки. По окончании работы предыдущего инструмента шпиндель 2 возвращается в положение разгрузки-загрузки. Автооператор 3 поворачивается из своего исходного положения и одновременно захватывает предыдущий и последующий инструменты. Механизм зажима освобождает оправку шпинделя. Автооператор перемещается в осевом направлении, извлекая предыдущий инструмент из шпинделя, а последующий – из магазина, затем поворачивается на 180°, меняя местами предыдущий и последующий инструменты, и перемещается в осевом направлении, посылая последующий инструмент в шпиндель, а предыдущий – в гнездо магазина. Механизм зажима закрепляет новую оправку в шпинделе. Автооператор, поворачиваясь, приходит в исходное положение. Весь цикл смены инструмента занимает пять-шесть секунд.
Рис.75. Схемы автоматической смены инструмента
Оправки с инструментами от магазина 1, расположенного вне бабки (рис.75, б), к шпинделю 2 и обратно переносятся автооператорами 3. Увеличение числа передающих механизмов и их усложнение не приводят к увеличению времени на смену инструментов, так как она совершается во время работы станка. Для дальнейшего сокращения времени смены инструмента применяют шпиндельные головки с двумя шпинделями – рабочим и предзагрузочным (рис.75, в, г). Пока один шпиндель находится в работе, другой разгружается от отработавшего инструмента и загружается новым с помощью автооператора, скорость работы которого в этом случае может быть небольшой. По окончании работы инструмента шпиндельная головка поворачивается на 180° индексирующим механизмом и вводит в действие второй шпиндель с новым инструментом. Смена инструмента может совершаться в течение одной-двух секунд.
В многооперационных станках число используемых в работе инструментов достигает нескольких десятков. В связи с этим решается задача такого кодирования инструмента в магазине, которое допускало бы автоматическое распознавание номеров и выбор каждого последующего инструмента по сигналам программного управления. Если, применяя магазин инструментов, их располагают по порядку использования, то кодирования не требуется. При обмене инструментами между шпинделем и гнездом магазина порядковая нумерация не нарушается, однако инструменты в магазине постепенно смещаются на один шаг. Повторное использование инструментов возможно путем их ручной перестановки в свободные гнезда, что усложняет обслуживание и увеличивает возможность ошибок при перестановке инструментов. Поэтому располагать инструменты в магазине в порядке их очередности можно только для операции, где общее число их невелико.
Кодирование инструментов позволяет избежать этих ограничений. Автоматический поиск инструмента допускает любое расположение инструментов в магазине независимо от их очередности. Существует несколько способов кодирования инструментов: кодирование места под инструмент, применение специальных ключей, несущих код инструмента, и непосредственное кодирование оправок с инструментами. Рассмотрим сущность последнего способа. В этом случае между конусным хвостовиком оправки и инструментом помещают кодовые кольца. Кодирование оправок заключается в определенном расположении колец, отличающихся диаметрами. Закодированная оправка с инструментом помещается в гнездо магазина и при его повороте воздействует кольцами на конечные выключатели, число которых должно быть равно общему числу колец. Релейная схема определяет совпадение заданного кода с сочетаниями включенных и невыключенных конечных выключателей и, таким образом, выбирает нужный инструмент.
Метод непосредственного кодирования оправок с инструментами имеет следующие достоинства: допускается любая последовательность загрузки магазина инструментами; нет необходимости в поиске соответствующего места для предыдущего инструмента при возврате его в магазин.
Многооперационные станки позволяют эффективно осуществлять программу большого объема. Если на отдельных простых операциях фрезерования, сверления, резьбонарезания и т.д. возможности станков с программным управлением не используются и применение их часто является нерациональным, то интеграция простых операций в одну общую совокупную программу обработки делает применение таких станков целесообразным и экономически эффективным. Возможность быстрой переналадки станка на новую деталь особенно ценна в условиях мелкосерийного производства.
СПИСОК ЛИТЕРАТУРЫ
1. Металлорежущие станки / под ред. В.К. Типинкичиева. – М.: Машиностроение, 1973.
2. Металлорежущие станки и автоматы / под ред. А.С. Проникова. – М.: Машиностроение, 1981.
3. Колев, Н.С. Металлорежущие станки: учеб. пособие для втузов / Н.С. Колев [и др.]. – М.: Машиностроение, 1980.
4. Металлорежущие станки / под ред. В.Э.Пуша. – М.: Машиностроение, 1985.
5. Таратынов, О.В. Металлорежущие системы машиностроительных производств / О.В. Таратынов [и др.]. – М.: Высшая школа, 1988.
6. Васильев, В.С. Современная классификация металлорежущих станков и станочных систем. Основные термины и определения / В.С. Васильев [и др.] // Станки и инструмент. № 2. 1984. С.35.
|
|
Историки об Елизавете Петровне: Елизавета попала между двумя встречными культурными течениями, воспитывалась среди новых европейских веяний и преданий...
Архитектура электронного правительства: Единая архитектура – это методологический подход при создании системы управления государства, который строится...
Кормораздатчик мобильный электрифицированный: схема и процесс работы устройства...
Наброски и зарисовки растений, плодов, цветов: Освоить конструктивное построение структуры дерева через зарисовки отдельных деревьев, группы деревьев...
© cyberpedia.su 2017-2024 - Не является автором материалов. Исключительное право сохранено за автором текста.
Если вы не хотите, чтобы данный материал был у нас на сайте, перейдите по ссылке: Нарушение авторских прав. Мы поможем в написании вашей работы!