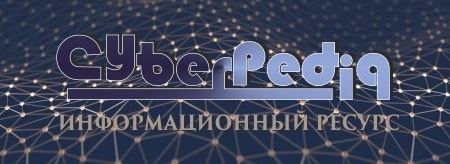
Историки об Елизавете Петровне: Елизавета попала между двумя встречными культурными течениями, воспитывалась среди новых европейских веяний и преданий...
Состав сооружений: решетки и песколовки: Решетки – это первое устройство в схеме очистных сооружений. Они представляют...
Топ:
Комплексной системы оценки состояния охраны труда на производственном объекте (КСОТ-П): Цели и задачи Комплексной системы оценки состояния охраны труда и определению факторов рисков по охране труда...
Оценка эффективности инструментов коммуникационной политики: Внешние коммуникации - обмен информацией между организацией и её внешней средой...
Устройство и оснащение процедурного кабинета: Решающая роль в обеспечении правильного лечения пациентов отводится процедурной медсестре...
Интересное:
Как мы говорим и как мы слушаем: общение можно сравнить с огромным зонтиком, под которым скрыто все...
Аура как энергетическое поле: многослойную ауру человека можно представить себе подобным...
Распространение рака на другие отдаленные от желудка органы: Характерных симптомов рака желудка не существует. Выраженные симптомы появляются, когда опухоль...
Дисциплины:
![]() |
![]() |
5.00
из
|
Заказать работу |
|
|
Термическая обработка представляет собой совокупность операций нагрева, выдержки и охлаждения металлических изделий с целью изменения структуры и свойств сплавов. Режимами процесса термической обработки являются: максимальная температура нагрева, время нагрева, время выдержки сплава при температуре нагрева и скорость охлаждения.
Те м п е р атуру нагрева для различных видов термической обработки назначают: для углеродистых сталей по диаграмме железо-цементит, для легированных сталей – по справочникам или государственным стандартам. Ориентировочно можно использовать диаграмму.
В р е м я нагрева стальных заготовок и деталей до заданной температуры зависит от ряда факторов: химического состава стали, размеров сечения, теплопроводности, площади поверхности контакта с нагревающей средой и т.д.
Ориентировочные нормы времени для нагрева стальных деталей приведены в таблице 3.
В р е м я выдержки изделий при температуре нагрева зависит от многих факторов. Ориентировочно время выдержки деталей и заготовок в пламенных и электрических печах берется в пределах 1,0 ¸ 1,5 мин на 1 мм сечения детали. Допустимо принимать время выдержки равным 1/5 от времени нагрева. Время выдержки при отпуске назначается в соответствии с таблице 4.
Время выдержки при цементации или азотировании назначается в соответствии с требованиями на толщину цементированного или азотированного слоя.
Продолжительность выдержки при цементации в твердом карбюризаторе (с момента достижения температуры цементации 950°С) ориентировочно определяется из расчета 0,1 ¸ 0,15 мм/ч. При газовой цементации (при 950°С) продолжительность выдержки берется исходя из опытных данных:
|
Толщина слоя, мм ……………0,75 | 1,5 | 2 | 2,5 | 3 | 3,5 |
Время выдержки, ч…………….1,0 | 4 | 7 | 12 | 16 | 22 |
Таблица 3. Время нагрева изделий из углеродистой и легированной сталей
Наименование агрегата | Температура нагрева, оС | Время нагрева на 1 мм условного диаметра изделия из, с | |
Углеродистой стали | Легированной стали | ||
Пламенная печь | 800-900 | 60-70 | 65-80 |
Электропечь | 750-820 | 60-65 | 70-75 |
820-880 | 50-55 | 60-65 | |
Соляная ванна | 770-820 | 12-14 | 18-20 |
820-880 | 10-12 | 8-10 | |
1240-1280 | 6-8 | 8-10 | |
Свинцовая ванна | 770-820 | 6-8 | 8-10 |
820-880 | 5-7 | 7-8 |
Таблица 4. Время выдержки при отпуске деталей
Температура отпуска, °С | Время отпуска в электропечах | Время отпуска в соляных ваннах, мин |
200 | 120 мин +1 мин на 1 мм условной толщины | 120 |
300-400 | 20 мин + 1 мин на 1 мм условной толщины | 15-20 |
400-680 | 10 мин + 1 мин на 1 мм условной толщины | 3 мин + 0,4 мин на 1мм условной толщины |
При проведении поверхностной закалки токами высокой частоты определяется необходимая частота тока, от которой зависит глубина закаливаемого слоя, подбирается тип установки с необходимыми параметрами.
Величина тока может быть ориентировочно принята по таблице 5.
Для поверхностного нагрева стали под закалку необходимо применять сравнительно большую удельную мощность (до 2 кВт/см2) и сравнительно малое время нагрева (2 – 10 с). При этом скорость нагрева лежит в пределах 15-300°С/с. Снижение удельной мощности и увеличение времени нагрева обусловливает получение более глубокого нагрева.
Ориентировочные значения скорости нагрева и удельной мощности даны в таблице 6. Ориентировочные данные режимов закалки деталей токами высокой частоты приведены в таблице 7.
Таблица 5. Зависимость глубины поверхностной закалки от частоты тока
Частота тока, Гц | Рациональные пределы глубины нагрева, мм | Минимальный диаметр заготовки при нагреве под закалку,мм |
50 | 15-80 | 200 |
1000 | 3-17 | 44 |
2500 | 2-11 | 28 |
4000 | 1,5-9 | 22 |
8000 | 1-6 | 16 |
10000 | 0,9-5,5 | 14 |
70000 | 0,3-2,5 | 5 |
400000 | 0,2-1 | 2,2 |
Таблица 6. Зависимость глубины нагрева от удельной мощности и скорости нагрева
|
Глубина нагрева, мм | Скорость нагрева в области фазовых превращений, °С/с | Удельная мощность, кВт/см2 |
1-2 | 100-300 | 0,8-1,5 |
3-5 | 20-80 | 0,5-1,8 |
6-10 | 2-15 | 0,05-0,2 |
Таблица 7. Режимы закалки ТВЧ машиностроительных деталей
Детали | Марка стали | Глубина закалки, мм | Твердость поверхности, HRC | Закалочная среда | Рекомендуемые частоты, кГц | |
1 | 2 | 3 | 4 | 5 | 6 | |
Валы | 40 | 2,5 | 56 | Вода | 10 | |
Шлицевые валы малого диаметра | - | 1 – 2 | 60 | Вода | 10 | |
Валы раздаточных коробок отбора мощности | - | 0,8 – 1,7 | 52 – 55 | Масло | 10 | |
Тонкие оси (штоки) | - | 4 | 56 – 58 | Масло | 10 | |
Венец маховика | - | 2,5 – 3 | 50 – 55 | Масло | 10 – 7 | |
Пальцы | 55 | - | 60 – 62 | Масло | 10 – 7 | |
Зубчатые муфты и венец | 50ХМ | 1,5 | 58 – 62 | Эмульсия | 10 – 7 | |
Оси блока шестерен | - | 1 – 3 | 60 – 65 | Вода | 8 | |
Шестерни ведомые | - | 1 – 2,5 | 58 – 63 | Вода | 2,4 | |
Шлицевые втулки | 40Х | Сквозная | НВ255 - 302 | - | - | |
Вилки | 20 | 0,3 – 0,5 | 56 – 62 | Вода | 8 | |
Валы (промежуточные) | 25ХГМ | - | 25 – 40 | Воздух | 8 | |
Шестерни ведущие нагруженные | 30ХГТ | - | 35 | Воздух | 8 | |
Скорость охлаждения изделия напрямую зависит от выбранной охлаждающей среды. Охлаждающая среда должна обеспечивать скорость охлаждения в верхнем диапазоне температур выше критической скорости закалки, а в нижнем (в области мартенситных превращений) – по возможности меньшую скорость охлаждения, чтобы предотвратить коробление изделий и образование трещин.
В качестве закалочных сред для углеродистых сталей, имеющих высокую критическую скорость охлаждения, применяют воду и различные водные растворы, а для легированных сталей, имеющих небольшую критическую скорость охлаждения, используют масло и воздух (таблица 8).
Таблица 8. Скорости охлаждения (град/с) в различных охлаждающих средах
Закаливающая среда | Интервал температур | |
650 – 550 0С | 300 – 200 0С | |
Вода при температуре, 0С: |
600 |
270 |
20 | ||
30 | 500 | 270 |
50 | 100 | 250 |
75 | 30 | 200 |
10%-ный раствор поваренной соли при 180С | 1100 | 300 |
10%-ный раствор соды при 180С | 800 | 270 |
Мыльная вода | 30 | 200 |
Машинное масло | 150 | 30 |
Трансформаторное масло | 120 | 25 |
Спокойный воздух | 3 | 1 |
Сжатый воздух | 30 | 10 |
|
|
Состав сооружений: решетки и песколовки: Решетки – это первое устройство в схеме очистных сооружений. Они представляют...
Типы сооружений для обработки осадков: Септиками называются сооружения, в которых одновременно происходят осветление сточной жидкости...
Поперечные профили набережных и береговой полосы: На городских территориях берегоукрепление проектируют с учетом технических и экономических требований, но особое значение придают эстетическим...
Особенности сооружения опор в сложных условиях: Сооружение ВЛ в районах с суровыми климатическими и тяжелыми геологическими условиями...
© cyberpedia.su 2017-2024 - Не является автором материалов. Исключительное право сохранено за автором текста.
Если вы не хотите, чтобы данный материал был у нас на сайте, перейдите по ссылке: Нарушение авторских прав. Мы поможем в написании вашей работы!