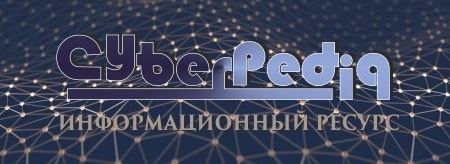
Типы оградительных сооружений в морском порту: По расположению оградительных сооружений в плане различают волноломы, обе оконечности...
Архитектура электронного правительства: Единая архитектура – это методологический подход при создании системы управления государства, который строится...
Топ:
Комплексной системы оценки состояния охраны труда на производственном объекте (КСОТ-П): Цели и задачи Комплексной системы оценки состояния охраны труда и определению факторов рисков по охране труда...
Определение места расположения распределительного центра: Фирма реализует продукцию на рынках сбыта и имеет постоянных поставщиков в разных регионах. Увеличение объема продаж...
Характеристика АТП и сварочно-жестяницкого участка: Транспорт в настоящее время является одной из важнейших отраслей народного...
Интересное:
Аура как энергетическое поле: многослойную ауру человека можно представить себе подобным...
Национальное богатство страны и его составляющие: для оценки элементов национального богатства используются...
Искусственное повышение поверхности территории: Варианты искусственного повышения поверхности территории необходимо выбирать на основе анализа следующих характеристик защищаемой территории...
Дисциплины:
![]() |
![]() |
5.00
из
|
Заказать работу |
|
|
НЕПРЕРЫВНАЯ РАЗЛИВКА СТАЛИ НА СОРТОВОЙ МНЛЗ
ВТИ ТО-04-2018
Утверждено и введено в действие__________№______от_____________
Дата введения_________________
ВПЕРВЫЕ
Начальник отдела контроля качества ___________________ П.А. Федотов " _____ " __________________ 2018 г. | Начальник технического отдела _______________ М.А. Жигарев " _____ " ______________ 2018 г. Начальник ККЦ ________________ Е.В. Киреев " _____ " _____________ 2018 г. |
Тула - 2018
Содержание
1 Введение 2 Требования к исходным ресурсам 3 Технически характеристики МНЛЗ 4 Основные требования к отливаемым заготовкам 5 Порядок выполнения технологических операций при подготовке МНЛЗ 6 Порядок выполнения технологических операций при разливке стали на МНЛЗ 7 Аварийные ситуации, неисправности на МНЛЗ и меры их устранения 8 Дефекты непрерывно-литой заготовки и причины их образования 9 Контроль и регистрация параметров процесса разливки плавки 10 Метрологическое обеспечение процесса 11 Охрана труда 12 Охрана окружающей среды 13 Нормативные ссылки Приложение А (Обязательное) Применяемые марки ШОС, ТИС и масла Приложение Б (Обязательное) Распределение марок стали по семействам Приложение В (Обязательное) Расположение опорных и направляющих роликов Приложение Г (Обязательное) Конфигурация форсунок ЗВО Приложение Д (Обязательное) Параметры качания кристаллизатора Приложение Е (Справочное) Зависимость скорости разливки от диаметров сменных стаканов-дозаторов Приложение Ж (Обязательное) Скорость разливки по семействам групп марок стали Приложение И (Обязательное) Целевой перегрев стали над температурой ликвидус в зависимости от группы и семейства марок стали Приложение К (Справочное) Виды электромагнитного перемешивателя Приложение Л (Обязательное) Дефекты непрерывно-литых заготовок Приложение М (Обязательное) Виды неисправностей в процессе работы МНЛЗ и методы устранения Приложение Н (Обязательное) Схема контроля подготовки машины, технологических процессов, качества материалов и продукции Приложение П (Обязательное) Метрологическое обеспечение контролируемых параметров Приложение Р (Обязательное) Перечень отходов, образующихся в процессе выплавки стали в ККЦ | 3 4 5 7 8 31 62 63 63 63 63 66 67 68 69 70 72 73 74 76 79 81 82 100 104 108 112 |
|
Введение
1.1 Настоящая инструкция устанавливает технологию разливки стали на сортовой машине непрерывного литья заготовок (МНЛЗ) кислородно-конвертерного цеха (ККЦ).
1.2 Инструкция составлена в соответствии с методическими рекомендациями о порядке разработки технологических инструкций МИ ОКиС-01, а также на основании опыта работы МНЛЗ на аналогичных предприятиях.
|
1.3 Ответственность за выполнение требований настоящей инструкции несут разливщики, старшие разливщики стали, операторы, старшие операторы МНЛЗ, сменные мастера участка разливки стали, мастера смен ККЦ.
1.4 Ответственность за подготовку МНЛЗ к работе возлагается на разливщиков, старших разливщиков, операторов, старших операторов МНЛЗ, сменных и старшего мастеров МНЛЗ, а также вспомогательные службы по принадлежности.
1.5 Контроль за выполнением требований инструкции возлагается на сменных мастеров и старшего мастера участка разливки, заместителя начальника ККЦ по оборудованию и технологии, начальника ККЦ.
1.6 Особенности технологии разливки стали приведены в технологических картах.
1.7 В настоящей ВТИ приняты следующие условные обозначения и сокращения:
ОКК – отдел контроля качества;
ПО – производственный отдел;
ТО – технический отдел;
э/л ЦЗЛ – экспресс-лаборатория центральная заводская лаборатория;
МНЛЗ – машина непрерывного литья заготовок (сортовая);
УРК – участок ремонта кристаллизаторов;
УУиВГМ – участок уборки и вырубки горячего металла (склад);
УКП – установка «ковш-печь»;
ППС – подъемно-поворотный стенд МНЛЗ;
СК – сталеразливочный ковш;
ШЗ – шиберный затвор сталеразливочного ковша;
ЗТ – защитная труба;
ПК – промежуточный ковш МНЛЗ;
СД – стакан-дозатор;
ПС – погружной стакан;
Кр – кристаллизатор;
ШОС – шлакообразующая смесь;
ТИС – теплоизолирующая смесь;
ЗВО – зона вторичного охлаждения;
ТПМ – тянуще-правильный механизм;
МГР – машина газокислородной резки заготовок;
ГПУ и ПУ МНЛЗ – главный и местный пульты управления МНЛЗ;
НЛЗ – непрерывнолитая заготовка (сортовая);
СУСД – система управления складским двором;
ММЗ – маркировочная машина заготовок;
НД и ТД – нормативная и технологическая документация;
ГОСТ – межгосударственный стандарт;
ТУ – технические условия;
ТТ – технические требования;
ТИ – технологическая инструкция;
ПТИ – производственно-техническая инструкция;
ОТ и ПБ – охрана труда и промышленная безопасность.
1.8 Примечание – за изменение, пересмотр и издание новой ТИ взамен настоящей при: обновлении действующих ГОСТ, ГОСТ Р, ГОСТ Р ИСО, ГОСТ ISO, других нормативных актов; изменении технологического процесса, или в других случаях, приведённых в п. 5.6 МИ ОКиС-01, несет ответственность подразделение-разработчик ТИ.
|
Требования к исходным ресурсам и материалам
2.1 Выплавка и подготовка стали для разливки на МНЛЗ ведется согласно требованиям
ВТИ ТО-01-2018, ВТИ ТО-02-2018, ВТИ ТО-03-2018.
2.2 Для разливки на МНЛЗ подается металл после корректировки его температуры и химического состава на установке ковш-печь (УКП) и вакууматоре (ВД), а потому возможны следующие технологические схемы контактной работы агрегатов ККЦ:
а) Конвертер – УКП – МНЛЗ;
б) Конвертер – УКП – ВД – МНЛЗ.
2.3 Требуемые температуры металла в сталеразливочном ковше (СК) после доводки и температуры стали в промковше для конкретных марок стали обозначены в соответствующих технологических картах.
2.4. Температура стали в СК при выдаче плавок с УКП на МНЛЗ (производство по схеме «а») указана в технологической карте.
2.5 В качестве технологической смазки гильз используют масло марки RUMANOL R.E.O. CAST TAOX (приложение А), рапсовое или синтетическое с аналогичными свойствами. Масло должно поступать в ККЦ только после положительного результата входной проверки качества партии. Отбор проб масла для анализа его качества с МНЛЗ производят еженедельно, место отбора проб - подвод смазки к кристаллизатору.
2.6 Используемые огнеупорные изделия, защитные трубы, стопора-моноблоки, сталепроводные изделия, погружные стаканы и др. должны соответствовать требованиям НД или контрактов.
2.7 Смесь (ШОС) допускается использовать в состоянии поставки при наличии сертификата или акта отдела внешней приемки, подтверждающих соответствие смеси ТТ или ТУ.
2.8 В случае истечения срока хранения смеси (6 месяцев с даты выпуска, указанной на упаковке) вне зависимости от назначения (промежуточный ковш, кристаллизатор), производится отбор одной пробы от пакета из верхнего слоя каждой коробки для определения влажности. Отобранная проба отправляется в ЦЗЛ. Полученные результаты анализа заносятся в журнал МНЛЗ.
2.9 Запрещается использовать:
- смеси без сертификата;
|
- смеси, не соответствующие требованиям ТТ или ТУ;
- смеси с влажностью более 1,0 % для промежуточного ковша и более 0,5 % для кристаллизатора.
2.10 Возможно использование материалов, которые соответствуют другим нормативным документам. Решения об использовании таких материалов, после заключения ЦЗЛ об их качестве и пригодности, принимается ТО.
Подготовка оборудования МНЛЗ к разливке серии плавок
5.3.1 Перед каждой серий разливки плавок дежурные механики, гидравлики, энергетики, электрики проверяют состояние оборудования МНЛЗ (тянуще-правильных машин (ТПМ), рольгангов, машины газовой резки (МГР), упоров, маркировочных машин заготовки (ММЗ) и др).
5.3.2 Аварийные желоба очищают от шлака, скрапа, при необходимости проводят их ремонт и сушку.
5.3.3 Подготавливают аварийные желоба к новой серии плавок. Контроль выполнения работ осуществляет старший разливщик.
5.3.4 Футеровка аварийного желоба стальковша, желоба за кристаллизатором и рядом с кристаллизатором производится штучными шамотными огнеупорами (Al2O3 40 – 45%). Сушку осуществляют с помощью специальных горелок не менее 2-х часов.
Подготовка кристаллизаторов к разливке
5.4.1 При подготовке к разливке с плит кристаллизаторов удаляют скрап, остатки шлака, ШОС, при этом запрещается сброс мусора в полость кристаллизаторов.
5.4.2 Разливщики обдувает сжатым воздухом рабочие поверхности гильз кристаллизаторов.
5.4.3 Дефекты поверхности гильз и несмывающийся нагар от смазки в районе мениска зачищают мелкой наждачной бумагой.
5.4.4 Старший оператор осматривает поверхность гильз.
5.4.5 Разливщики очищают каналы для подачи технологической смазки в кристаллизаторы, для ее равномерного истечения по граням гильз. Инструментами для очистки масленок служат специальные полоски из пружинной стали толщиной около 0,8 мм.
5.4.6 В планово-предупредительные ремонты (ППР) и профилактики осуществляют вскрытие чистку (при необходимости - замену) масленок кристаллизаторов, установленных на МНЛЗ.
5.4.7 Кристаллизатор подлежит замене в следующих случаях.
5.4.7.1 При обнаружении и невозможности устранения на месте следующих отклонений:
- застревания слитка или скрапа в кристаллизаторе после прорыва металла или прекращения вытягивания;
- двух прорывов по трещине подряд;
- угловых продольных трещин и других дефектов заготовок, на которые оказывает влияние состояние гильзы, на двух плавках подряд;
- искажений формы (ромбичности, выпуклости, вогнутости) заготовок предыдущих плавок свыше допустимых значений;
- разность между диагоналями превышает 1,5 %;
- на внутренней поверхности гильзы явные грубые дефекты или пористость (контроль визуальный);
- явно выраженная боковая деформация гильзы (контроль визуальный);
|
- износ по углам гильзы (контроль визуальный);
- течь воды по стыку верхнего или нижнего фланцев;
- прогаров и наплывов на внутреннем торце верхнего фланца;
- внутренних трещин в макроструктуре (по сечению) заготовки на глубине до 30 мм;
- люфт или заклинивание роликов нижнего фланца;
- после разливки на МНЛЗ от 150 до 200 плавок со времени последней ревизии;
- износ нижней части кристаллизатора более 1мм на расстоянии 25 мм нижней части кристаллизатора;
- задиров, трещин, царапин на рабочей поверхности гильзы глубиной:
· 1 мм и более на расстоянии до 300 мм от верхнего края гильзы;
· 2 мм и более, шириной 3 мм на расстоянии от 300 до 1000 мм от верхнего края.
- течи воды в рабочую полость кристаллизатора;
- утечки смазки через уплотнения или засорение каналов для подачи смазки, которые не удается прочистить без снятия кристаллизатора;
- снижения расхода воды на охлаждение кристаллизатора ниже 10% аварийного расхода (1300 л/мин);
- перепада температуры охлаждающей воды в процессе разливки на входе и выходе из кристаллизатора (∆Т) более 10 °С при рабочем давлении.
5.4.8 Решение о замене кристаллизатора принимает сменный мастер МНЛЗ. Причина замены регистрируется в журнале разливки и паспорте кристаллизатора.
5.4.9 Не допускается использование кристаллизатора без технического паспорта и с гильзами, не прошедшими контроль состояния рабочей полости.
5.4.10 При снижении расхода воды первичного охлаждения ниже минимального проводят полную разборку кристаллизатора и проверяют состояние внешней поверхности гильзы, чистоту каналов.
5.4.11 Проверку, ремонт и настройку кристаллизаторов с 1-й секцией роликов проводят механики в объеме, предусмотренном специальной инструкцией.
5.4.12 Результаты замеров и осмотра регистрируют в паспорте Кр.
5.4.13 Кристаллизаторы передают в ремонт очищенными от нагара, масла, остатков стали и шлака, сопровождают паспортом кристаллизатора с заполненной дефектной ведомостью, указанием причин снятия с МНЛЗ.
5.4.14 В случае потери ручья в результате отрыва слитка или прорыва после окончания разливки допускается извлекать чулок из гильзы, для чего при рабочем расходе воды на охлаждение кристаллизатора кислородной трубкой подрезают «чулок» по углам, включают подачу смазки и извлекают из гильзы.
5.4.15 Решение об извлечении «чулка» из гильзы принимает сменный мастер МНЛЗ.
5.4.16 При невозможности извлечения «чулка» кристаллизатор передается на участок ремонта кристаллизаторов МНЛЗ.
5.4.17 Ответственность за сдачу кристаллизаторов в ремонт и приемку из ремонта несет старший мастер МНЛЗ.
Подготовка системы технологической смазки гильз кристаллизаторов для разливки стали «открытым» способом
5.6.1 После установки кристаллизаторов и подсоединения маслопровода проверяют работу системы подачи технологической смазки, настраивают равномерность ее подачи по сторонам гильз.
5.6.2 При переходе с «закрытого» способа разливки на «открытый» дежурные механики снимают верхние фланцы кристаллизаторов для проверки и очистки каналов подачи масла в кристаллизатор.
5.6.3 При разливке «открытой» струей каждый межсерийный простой разливщики очищают щелевые каналы для подачи масла в кристаллизаторы для равномерного истечения смазки по сторонам гильз. Если канал прочистить невозможно дежурные механики снимают фланец для прочистки каналов.
5.6.4 Не разрешается смешивание разных масел, использование другого типа (марки) масла без предварительной очистки и продувки емкостей и трубопроводов подачи в Кр.
5.6.5 В ППР проводят проверку соответствия фактических расходов масла в Кр с показаниями расхода на дисплее компьютера ГПУ МНЛЗ.
5.6.6 Контроль качества смазки гильз Кр и расхода масла (указано в приложении к техкарте) осуществляют старший и сменный мастера МНЛЗ.
5.6.7 При подготовке системы смазки гильз маслом контролируют работу маслостанций, подкачку и систему подачи масла в автоматическом режиме, отсутствие течи масла, равномерность подачи смазки по сторонам гильзы кристаллизатора, работу КИПиА.
Подготовка системы вторичного охлаждения
5.9.1 Проверяется исправность и надежность крепления рукавов для подвода воды к коллекторам, расположение коллекторов относительно оси зоны вторичного охлаждения, форсунок относительно заготовок. Выставка коллекторов охлаждения II-ой зоны ЗВО осуществляется по шаблону.
5.9.2 Выставка коллектора I зоны вторичного охлаждения осуществляется по шаблону и жестко крепится к корпусу стола качания.
5.9.3 I зона вторичного охлаждения подлежат замене при:
- ее деформации;
- повреждении резьбы на отводах;
- деформации отвода;
- наличии потерь воды в результате нарушения целостности трубы.
5.9.4 Отводы стояка с форсунками должны размещаться соосно к грани, на расстоянии, указанном на соответствующем общем чертеже. Контроль осуществляется по заведенной затравке или по шаблону, установленному сверху в гильзу кристаллизатора.
5.9.5 Выставка коллекторов II и III зоны вторичного охлаждения осуществляется по шаблону и имеют регулировку.
5.9.6 Отводы коллекторов с форсунками должны быть соосны слитку, направлены на середины граней и стоять на одинаковом расстоянии от оси заготовки.
5.9.7 Расход и давление воды по зонам контролируется по приборам, расположенным на ГПУ МНЛЗ. Повышенное давление на приборе (при заданном расходе) указывает на забитость форсунок или фильтров, а пониженное – на недопустимую утечку воды через отсутствующую форсунку или порыв подводящих рукавов.
5.9.8 Проверяется исправность, ориентация и работа форсунок при максимальном расходе воды, особенно работа форсунок I зоны.
5.9.9 Факел распыления воды должен быть направлен перпендикулярно поверхности слитка; угол раскрытия должен соответствовать типу форсунки; расстояние от форсунки до поверхности заготовки для форсунок одной зоны должно быть одинаковым (погрешность допускается до 5 мм).
5.9.10 Засоренные или с искаженным углом раскрытия форсунки чистятся путем их выкручивания и продувки сжатым воздухом.
5.9.11 Запрещается чистка забитых форсунок на месте при помощи тонкой проволоки, так как окалина или грязь, попадая в коллектор при подаче воды, вновь заносится в форсунку, забивая ее. Проверяется у прочищенных форсунок угол раскрытия. Вышедшие из строя форсунки заменяются исправными.
5.9.12 Форсунки считаются вышедшими из строя, если нельзя организовать нормальный угол раскрытия (факел распыления).
5.9.13 Особенно тщательно проверяют исправность системы вторичного охлаждения после обнаружения неравномерности температуры поверхности по граням слитка при выходе его из камеры вторичного охлаждения по предыдущей разливке. Фильтры (сетчатые) чистятся путем их снятия для последующей промывки водой и продувки сжатым воздухом.
5.9.14 Производится выставка давления и расхода воды по форсуночным секциям для рабочих скоростей разливки.
5.9.15 При правильном расположении форсунок:
- 1-я зона: факел полностью перекрывает грань заготовки;
- 2-й, 3-й секций ЗВО факел не должен полностью перекрывать грань заготовки.
5.9.16 Замену форсунок, коллекторов выполняет технологический персонал по решению сменного мастера МНЛЗ.
5.9.17 Конфигурация (типы, число, расположение) форсунок ЗВО указана в приложении Г.
5.9.18 При засорении коллекторов и форсунок технологический персонал выполняет их замену и промывку.
5.9.19 Промывку осуществляют при максимальных расходах воды путем открытия соответствующего клапана с ГПУ МНЛЗ.
5.9.20 После замены коллекторов и форсунок включают соответствующий контур охлаждения и проверяют параметры расхода и давления воды при ее максимальных расходах.
Подготовка головок затравок типа «Conseal»
5.10.1 Подготовку головки затравок типа «Conseal» производить в следующей последовательности:
- на участке парковки затравок очистить головку от остатков металла, при необходимости удалить заусеницы и обдуть сжатым воздухом;
- на пульте разливщика установить переключатель в позицию «подготовка», а на главном пульте нажать кнопку «автоматический ввод затравки», при этом затравка электрическим приводом вводится в тянущий модуль (ТПМ), зажимается тянущими роликами;
- после автоматического включения двигателя тянущих роликов затравка вводится в камеру охлаждения и автоматически останавливается под кристаллизатором в зоне расположения поддерживающих роликов;
- если остановка затравки в автоматическом режиме не произошла, нажать кнопку «Стоп мотор ТПM» на подвесном пульте разливщика;
- перед заведением затравки в кристаллизатор включить пароотсос;
- обдуть сжатым воздухом или высушить резаком головку затравки.
5.10.2 Устройство «Conseal» быстрого уплотняющего затвора служит для обеспечения:
- надежного соединения между разливаемой сталью и затравкой;
- надежного уплотнения между затравкой и гильзой кристаллизатора, не зависящего от вибраций в начале пуска ручья и ошибок разливщиков;
- безопасного выполнения операции подготовки головки затравки при переналадке ручьев во время работы МНЛЗ под кристаллизатором внутри камеры охлаждения, исключающего выполнение операций между промковшом и кристаллизатором;
- быстрого выполнения операции, в результате которого экономится время при проведении работ по переналадке ручья;
- для надежного автоматического отсоединения затравки.
5.10.3 Узел «Conseal» состоит из металлических и пластмассовых деталей, которые соединяются друг с другом в форме пирамиды (рисунок 5.2), которая надежно устанавливается на головку затравки, и таким образом происходит ее самостоятельное уплотнение при ее вводе в кристаллизатор.
Рисунок 5.2 – Узел «Conseal» в сборе
5.10.4 Металлическая часть состоит из собранных между собой деталей (рисунок 5.3):
Рисунок 5.3 – Составные части узла «Conseal»
- основная пластина для защиты головки затравки от воздействия жидкой стали;
- размеры пластины соответствуют размерам сечения отливаемых заготовок;
- в центре пластины расположен паз, в который вставляется вторая охлаждающая пластина;
- в ее нижней части имеется крючок, с помощью которого «Conseal закрепляется на головке затравки»;
- вторая пластина охлаждения, вставляется в главную пластину через имеющийся паз;
- на задней стороне обеих деталей имеются два паза, которые прочно удерживаются на отливаемой заготовке и предотвращают преждевременное отделение затравки от заготовки;
- пластиковые вставки изготовлены экструзивно-выдувным способом и могут быть использованы только один раз;
- пластиковые вставки надежно фиксируются на ударной плите, обеспечивая идеальное соединение и хорошую герметизацию гильзы. Кроме того, они защищают стенки и углы гильзы от повреждения во время ввода затравки.
5.10.5 Установка «Conseal» на головке затравки производится под кристаллизатором внутри камеры охлаждения в соответствии с рисунком 5.4 и рисунком 5.5
Рисунок 5.4 - Схема установки «Conseal» на головку затравки
Рисунок 5.5 - Выполнение операции подсоединения «Conseal» к затравке
5.10.6 Крепление «Conseal» на головке затравки обеспечивается алюминиевым штифтом (рисунок 5.6).
4 |
° |
90 |
R1 |
3 |
Ø |
8 |
Ø |
6 |
150 |
- |
180 |
Рисунок 5.6 – Штифт для крепления затвора «Conseal» к головке затравки
5.10.7 Допускается для крепления «Conseal» использовать алюминиевую проволоку диаметром не менее 8 мм.
5.10.8 Штифт должен свободно входить в отверстия в корпусе головки и приводиться в требуемое положение легким постукиванием.
5.10.9 При необходимости более жесткой фиксации штифта, для предотвращения блокирования заготовки или её преждевременного отсоединения, использовать деревянные клинышки.
5.10.10Ввод головки затравки с «Conseal» в гильзу кристаллизатора производить под визуальным контролем, без повреждения пластмассовых элементов «Conseal» (рисунок 5.7)
Рисунок 5.7 – Ввод затравки с узлом Conseal в кристаллизатор
5.10.11 Необходимо всегда проверять состояние системы уплотнения «Conseal» расположенной в кристаллизаторе с помощью фонарика.
5.10.12 Если она имеет разрывы или вмятины, то ее необходимо заменить.
5.10.13 Затравка вводиться в кристаллизатор на расстояние 50-80 мм от нижнего среза гильзы кристаллизатора (рисунок 5.8).
Рисунок 5.8 – Схема ввода затравки в кристаллизатор
5.10.14 Для охлаждения первых порций жидкого металла в кристаллизаторах укладывать дополнительные «холодильники».
5.10.15 Для снижения вероятности накапливания испарений конденсатной влаги, образующейся при сгорании избыточного количества, подаваемого для предварительной смазки гильзы масла, необходимо:
- не подавать для предварительной смазки гильзы кристаллизатора избыточное количество масла;
- включить пароотсос.
5.10.16 Подготовку затравок в кристаллизаторах проводят не ранее чем за 40 мин до начала разливки.
5.10.17 Отсоединение затравки от заготовки происходит под воздействием правильного ролика при поступлении заготовки в отделяющий модуль ТПМ. Ролик деформирует заготовку, происходит смещение заготовки относительно головки затравки и обламывание штифта (рисунок 5.9).
Рисунок 5.9 - Отсоединение заготовки от устройства быстрого уплотняющего затвора
Подготовка промежуточных ковшей для разливки стали открытой струей
5.11.1 Для разливки стали на МНЛЗ используются промежуточные ковши с рабочим слоем футеровки, выполненным из торкрет-массы.
Сборку промежуточных ковшей, подготовку их к разливке, разогрев футеровки ведут под контролем старшего разливщика.
5.11.2 Промежуточные ковши с установленными крышками и системой разливки MNC подаваемые на участок разливки, должны иметь исправный кожух, прочищенные выпарные отверстия и узлы для крепления огнеупорных защитных изделий. В ковшах не должно быть посторонних предметов, отходов огнеупоров на дне и в каналах дозаторов, а также скрапин на кожухе около дозирующих узлов и на фланцах.
5.11.3 Каждый ковш должен иметь заполненный паспорт.
5.11.4 Приемку промковша переданного на МНЛЗ, в присутствии бригадира ковшевого участка, осуществляет старший разливщик или сменный мастер МНЛЗ.
5.11.5 Перед установкой промковша на разливочную тележку механизмы центровки тележки с помощью гидроцилиндра переводят в среднее положение штока. Ковш прижимают к базовым упорам консолей таким образом, чтобы обеспечивались одинаковые зазоры между торцами ковша и боковыми стенками консолей.
5.11.6 В направляющие кассеты системы MNC устанавливаются сменные дозаторы требуемого диаметра.
5.11.7 Затем устанавливается гидроцилиндр для перемещения стакан-дозаторов.
5.11.8 Перемещение дозаторов в положении разливки осуществляется с пульта управления мобильной маслостанции для каждого ручья поочередно.
5.11.9 Кассеты устройств быстрой смены дозаторов закрываются защитными экранами.
5.11.10 С главного пульта управления включается гидростанция MNC.
5.11.11 Затем проверяют центровку дозаторов относительно ковшевого стакана.
5.11.12 Производят подсоединение воздушных шлангов к системе MNC.
5.11.13 Готовность системы замены дозаторов промковша оценивают по сигнальным лампам на главном пульте управления:
- питание включено, насос включен (горят зеленые лампы на панели пульта);
- рабочее давление в системе от 140 до 160 бар (горят зеленые лампы на панели пульта);
- при отсутствии давления в системе загорается красная лампа;
- при недостаточном уровне масла в баке маслостанции загорается красная лампа;
- переключатель выбора ручьев МНЛЗ должен быть установлен в положение «0».
5.11.14 Основной вариант управления, с индивидуальных пультов управления системой MNC для каждого ручья МНЛЗ. При необходимости, управление цилиндрами на каждом ручье можно производить с главного пульта управления, используя переключатель выбора ручья и переключатели запуска или закрытия предварительно выбранного ручья МНЛЗ.
5.11.15 Во время подготовки промковша к разливке стали проверяют качество запасовки и состояния гидравлических шлангов MNC.
5.11.16 При установке гидроцилиндров в направляющие системы, случаи их перекоса должны быть исключены.
5.11.17 Начало разливки стали без охлаждения пружин и гидроцилиндров MNC сжатым воздухом не допускается.
5.11.18 В резервной позиции в кассете MNC должна быть установлена глухая плита для закрытия ручья в любой момент.
Подготовка промежуточных ковшей для разливки закрытой струей
5.12.1 Для разливки стали на МНЛЗ используются промежуточные ковши с рабочим слоем футеровки, выполненным из торкрет-массы.
5.12.2 Сборку промежуточных ковшей, подготовку их к разливке, разогрев футеровки ведут под контролем старшего разливщика.
5.12.3 Промежуточные ковши с установленными крышками, стопорными механизмами и аварийными шиберными устройствами, подаваемые на участок разливки, должны иметь исправный кожух, прочищенные выпарные отверстия и узлы для крепления огнеупорных защитных изделий. В ковшах не должно быть посторонних предметов, отходов огнеупоров на дне и в каналах дозаторов, а также скрапин на кожухе около дозирующих узлов и на фланцах.
5.12.4 Каждый ковш должен иметь заполненный паспорт.
5.12.5 Приемку промковша переданного на МНЛЗ, в присутствии бригадира ковшевого участка, осуществляет старший разливщик или сменный мастер МНЛЗ.
5.12.6 Перед установкой промковша на разливочную тележку механизмы центровки тележки с помощью гидроцилиндра переводят в среднее положение штока. Ковш прижимают к базовым упорам консолей таким образом, чтобы обеспечивались одинаковые зазоры между торцами ковша и боковыми стенками консолей.
5.12.7 Затем производят установку стопоров.
5.12.7.1 Последовательность установки приведена на рис. 5.10:
Рисунок 5.10 - Установка стопора
- перед установкой стопора поворотом маховика установите поперечный кронштейн стопорного механизма в промежуточное положение (1);
- положение поперечного кронштейна обозначено стрелкой в смотровом окошке стопорной коробки;
- промежуточное положение необходимо для правильной установки стопора;
- выньте болт поперечного кронштейна: этот болт не дает поперечному кронштейну перемещаться в горизонтальном направлении вокруг рычага стопора (вертикально);
- сдвиньте поперечный кронштейн так, чтобы можно было установить стержень стопора (рисунок 5.11);
Рисунок 5.11 Установка стержня стопора
- вставьте стопор в стакан-дозатор и поперечный кронштейн (2);
- вручную затяните верхнюю и нижнюю гайки на стержне стопора (3);
- выполните центровку стопора так, чтобы он находился вертикально над погружным стаканом SES/SEN (4), рисунок 5.12;
Рисунок 5.12 – Вид стопора
- поднимите стопор с помощью маховика и затяните верхнюю гайку гаечным ключом (5);
- вручную затяните нижнюю гайку (6) и проверьте правильность расположения стопора;
- проверьте при помощи маховика как выполняется открытие и закрытие стопора (7);
- закройте стопор и, удерживая его в закрытом положении, затяните верхнюю гайку гаечным ключом (8);
- проведите окончательную проверку правильности установки стопора, открыв и закрыв его с помощью маховика и удостоверьтесь, что:
- наконечник стопора входит и закрывает отверстие погружного стакана SEN/SES, при этом стопор не отклоняется в сторону при входе или выходе из отверстия в закрытом положении;
- при движении стопора не должно возникать никаких препятствий в виде посторонних предметов. Это ключевой момент при запуске ручьев в начале разливки;
- присоедините трубопроводы охлаждающего воздуха и азота к стопорной коробке.
- дежурным электрикам вставить вилку питания и сигнальные кабели для управления стопором в разъем на коробке стопора (рисунок 5.13).
Рисунок 5.13 – Кабели управления стопором.
- проверить работоспособность стопорного механизма;
- поднимите стопор в полностью открытое положение и зафиксируйте маховик.
5.12.8 Стопора должны всегда быть зафиксированы в закрытом положении во время перемещения промковша краном или на тележке промковша во избежание их повреждения.
5.12.9 Проверьте состояние направляющих аварийных шиберных затворов.
5.12.10 Присоедините гидравлические цилиндры на аварийные шиберные затворы, при этом не допуская их перекоса.
Отделение затравки
6.11.1 Режимы работы ТПМ при запуске и разливке ручья приведены в таблице 6.3
Таблица 6.3 Режим работы ТПМ
Режим работы | Кв.150 мм | КВ.180 мм |
Давление ролика вытягивания затравки (бар) | 50 | 50 |
Давление тянущей клети при вытягивании горячей заготовки (бар) | 28 | 33 |
Давление правильной клети (бар) | 17 | 21 |
Давление прижимного ролика при отделении затравки (бар) | 180 | 180 |
6.11.2 Отсоединение затравки от заготовки происходит под воздействием прижимного ролика при поступлении заготовки в отделяющий модуль ТПМ. Ролик деформирует заготовку, происходит смещение заготовки относительно головки затравки и обламывание штифта (рисунок 6.4).
Рисунок 6.4 - Отсоединение заготовки от затравки
6.11.3 Если отделения затравки не произошло, то необходимо отрезать головную часть заготовки с помощью ручного газокислородного резака и переместить затравку в позицию парковки.
6.11.4 После ТПМ через промежуточный рольганг заготовки поступают на МГР.
6.11.5 Передний конец заготовки отрезается на МГР в автоматическом режиме, при этом длина «головной» обрези для сечения 150х150 мм и 180х180 мм не менее 500 мм на ручей.
6.11.6 Мерная длина заготовок и общая длина отлитого слитка на ручьях от начала разливки измеряется автоматически с помощью кодового датчика ТПА1 и ТПА3.
6.11.7 Порезка заготовок на машинах газовой резки (МГР) производится в автоматическом режиме в соответствии с заданием ПО.
6.11.8 Допускается порезка заготовок ручным аварийным резаком при условии, если МГР вышла из строя в процессе разливки.
6.11.9 Длина отрезаемых заготовок рассчитывается Уровнем 2 по заранее заданной заказной длине с учетом коэффициента термической усадки непрерывнолитой заготовки.
6.11.10 При недорезах, отказах в работе МГР порезку заготовок на мерные длины ведут вручную газокислородными резаками с переходной площадки.
6.11.11 Все порезанные заготовки на мерные длины на разгрузочном рольганге 1 ускоряются и перемещаются на разгрузочный рольганг 2 для взвешивания.
6.11.12 После взвешивания заготовки перемещаются на разгрузочный рольганг 3 для подъема гидравлическим передаточным устройством на опорную раму верхнего уровня. Отсюда заготовки перемещаются поперечным шлеппером к толкателю заготовок в зону напротив передаточного рольганга 1.
6.11.13 Заготовки взвешиваются отдельно на каждом ручье.
6.11.14 На разгрузочном рольганге предусмотрен убирающийся упор, позволяющий осуществлять параллельное складирование заготовок (длиной 6 м) перед их подъемом на 2-й уровень.
6.11.15 В случае «горячего посада» передаточные рольганги (TRT 1 и 2) транспортируют пакет заготовок до конечного упора, собранный поперечным шлеппером и перемещенный толкателем заготовок, к конвейеру-столу для укладки заготовок.
6.11.16 После обнаружения датчиками конвейерного-ст
|
|
История развития пистолетов-пулеметов: Предпосылкой для возникновения пистолетов-пулеметов послужила давняя тенденция тяготения винтовок...
Эмиссия газов от очистных сооружений канализации: В последние годы внимание мирового сообщества сосредоточено на экологических проблемах...
Механическое удерживание земляных масс: Механическое удерживание земляных масс на склоне обеспечивают контрфорсными сооружениями различных конструкций...
Наброски и зарисовки растений, плодов, цветов: Освоить конструктивное построение структуры дерева через зарисовки отдельных деревьев, группы деревьев...
© cyberpedia.su 2017-2024 - Не является автором материалов. Исключительное право сохранено за автором текста.
Если вы не хотите, чтобы данный материал был у нас на сайте, перейдите по ссылке: Нарушение авторских прав. Мы поможем в написании вашей работы!