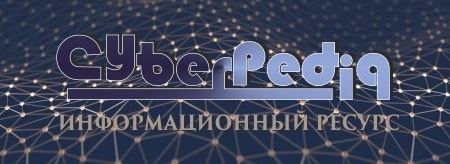
Историки об Елизавете Петровне: Елизавета попала между двумя встречными культурными течениями, воспитывалась среди новых европейских веяний и преданий...
Семя – орган полового размножения и расселения растений: наружи у семян имеется плотный покров – кожура...
Топ:
Техника безопасности при работе на пароконвектомате: К обслуживанию пароконвектомата допускаются лица, прошедшие технический минимум по эксплуатации оборудования...
Организация стока поверхностных вод: Наибольшее количество влаги на земном шаре испаряется с поверхности морей и океанов...
Выпускная квалификационная работа: Основная часть ВКР, как правило, состоит из двух-трех глав, каждая из которых, в свою очередь...
Интересное:
Как мы говорим и как мы слушаем: общение можно сравнить с огромным зонтиком, под которым скрыто все...
Искусственное повышение поверхности территории: Варианты искусственного повышения поверхности территории необходимо выбирать на основе анализа следующих характеристик защищаемой территории...
Лечение прогрессирующих форм рака: Одним из наиболее важных достижений экспериментальной химиотерапии опухолей, начатой в 60-х и реализованной в 70-х годах, является...
Дисциплины:
![]() |
![]() |
5.00
из
|
Заказать работу |
|
|
Offset printing is an indirect lithographic printing technology. Offset printing has spread markedly since approximately 1970 and has, to a great extent, ousted the letterpress printing technology which prevailed until that time. The offset printing technology is now the major printing technology.
In the offset printing process the printing and nonprinting areas of the plate are practically on one level. The printing areas of the printing plate are oleophilic - ink-accepting and water-repellent, that is, hydrophobic. The non-printing areas of the printing plate are hydrophilic, consequently oleophobic in behavior. This effect is created by physical phenomena at the contact surfaces. The dampening system covers the non-printing areas of the printing plate with a thin film of dampening solution. This dampening solution (water plus additives) spreads over the non-printing areas. To achieve good wetting, surface tension has to be reduced by means of dampening solution additives.
The plates used in offset printing are thin (up to about 0.3 mm), and easy to mount on the plate cylinder, and they mostly have a monometal (aluminum) or, less often, multimetal, plastic or paper construction. Aluminum has been gaining ground for a long time among the metal-based plates over zinc and steel. The necessary graining of the aluminum surface is done mechanically
either by sand-blasting, ball graining, or by wet or dry brushing. Nowadays, practically all printing plates are grained in an electrolytic process (anodizing), that is, electrochemical graining with subsequent oxidation.
The ink used in offset printing is usually a highly viscous mixture having the basic components of ink pigment, vehicle (binder), additives, and carrier substance.
Ink pigmentscan have either an organic or inorganic nature. The pigments determine the hue of the printing ink. They consist of solid, irregularly-shaped particles that are about 0.1–2 μm in size.
Vehicles(binders) are needed to bind the pigment, which is supplied in powder form, to the substrate. Vehicles also form a protective film around the pigments so that they are protected from mechanical abrasion.
Additives can be mixed into the ink to achieve specific properties and to overcome specific printing problems.
Mineral oils are used as carrier substancesfor offset inks. They fulfill the function of transporting the ink and are removed again in the drying process (evaporation, absorption).
Inking Units
During the printing process, a thin film of ink is transferred from the image areas of the plate to the substrate. The inking unit’s function is to provide a constant supply of fresh ink to the image areas on the plate to maintain a constant inking process. The amount of ink “used up” must be fed back to the system. There must be an equal balance between ink fed and ink dispensed in order to avoid variations in the ink density on the printed image. Another important factor for the print quality is the uniformity of the ink film thickness on the image areas of the plate or the image areas of the substrate. (It is a postulate of offset printing that the film of ink should be of the same thickness across the entire printed sheet. Reproduction technology for the creation of color separations is based on this principle). Consequently, the criteria determining quality are:
|
• temporary fluctuations of the average ink film thickness (quantity balances) and
• uniformity of the ink film thickness on the image areas of the plate or the printed areas of the substrate.
Dampening Units
Conventional offset printing requires a dampening system to supply a very thin film of dampening solution to the non-printing elements of the printing plate. Since part of the dampening solution is printed via the ink, plate, and blanket and another part evaporates, it is necessary to have a constant supply of dampening solution.
Printing Unit
Printing unit consists of inking and dampening units, the plate cylinder with the printing plate, the blanket cylinder with the blanket fixed to it, and the impression cylinder. The plate cylinder with the inked printing plate rolls over the circumference of the blanket cylinder. The blanket cylinder, in turn, rolls over the circumference of the impression cylinder, on which the sheet of paper is held by grippers. The contact line between the blanket cylinder and the impression cylinder is called the printing nip.
The printing plate (an up to 0.3 mm thick sheet of metal or a foil) carries the image elements of the respective color separation. The blanket is an approximately 2 mm-thick, exchangeable cylinder cover made from flexible material and layers of fabric. The plate cylinder’s circumference is interrupted by an axial recess, the cylinder gap. This recess holds the plate clamping mechanism. The blanket cylinder, likewise, has a gap to hold the blanket clamping mechanism, and the impression cylinder has a gap to accommodate the gripper system for paper transportation.
To ensure perfect transfer of the print image from plate to paper, all three cylinders must have the same circumferential speed at the contact line/printing nip. Due to the recesses in the cylinder’s circumferences, the relative rolling motion necessary for continuous production cannot be achieved simply by friction between the cylinder surfaces. Along with the frictional connection via the cylinder surfaces, the cylinders are also connected via a gear train for this reason.
The printing unit is driven by the impression cylinder via a gear train. The printing unit in turn transmits the necessary drive power for the inking unit. Printing problems arising from the gear train (the unwelcome “gear marks” in particular) are avoided by the narrow tolerances specified for the design of gearwheels and thanks to tried and tested production technology and quality control.
For the proper transfer of ink between plate and blanket and between blanket and paper, a sufficiently high contact pressure between the cylinders as well as the same circumferential speed of the cylinders are necessary.
Рис. 1
Advantages of offset printing are:
• materials with different sheet size and grammages can be processed;
• nearly all finishing operations are possible
• the quality is rather high.
Disadvantages are:
• complicated method – causes misprints
• sheet size just as big as machine size
• expensive printing machines.
|
ESSENTIAL VOCABULARY
Words and Word Combinations
ACTIVITIES
13. What units does the offset printing press consist of?
16. Why is offset printing considered to be the major technology now?
1 | non-printing | a | tension |
2 | physical | b | speed |
3 | dampening | c | areas |
4 | printing | d | phenomena |
5 | ink | e | units |
6 | plate | f | cylinder |
7 | blanket | g | solution |
8 | gear | h | pigments |
9 | surface | i | train |
10 | circumferential | j | cylinder |
5. Fill in the gaps with an appropriate word or phrase from the box:
Dampening solution, hydrophilic, oleophilic, ousted, graining, circumferential speed, hue, plate, a highly viscous mixture, non-printing areas, blanket, impression. |
1. Offset printing has spread since 1970 and ……….. the letterpress printing technology.
2.The printing areas of the printing plate are ………...
3. The non-printing areas of the printing plate are ……….
4. The dampening system covers the non-printing areas of the printing plate with a thin film of ……… ………...
5. The ………. of the surface can be done mechanically.
6. The ink used in offset printing is usually…………..
7. The pigments determine the ….. of the ink.
8. The dampening solution spreads over ………. ………...
9. Printing unit consists of inking and dampening units, the ……. cylinder, the …….. cylinder and the …… cylinder.
10. High contact pressure between the cylinders and the same ……….. ……… of the cylinders are necessary for the proper transfer of ink between the plate, blanket and the paper.
6. Put the verbs in brackets in appropriate form, translate the sentences into Russian:
1. Offset printing (to spread) markedly since approximately 1970.
2. The dampening solution (to spread) over the non-printing areas.
3. Aluminum (to be gaining) ground for a long time among the metal-based plates over zinc and steel.
4. The cylinders (to be connected) via a gear train.
5. Mineral oils (to be used) as carrier substances for offset inks.
6. The dampening solution (to consist) mainly of water.
7. Letterpress printing technology (to prevail) until the spreading of the offset printing.
|
7. Find the sentences with the following prepositions in the text. Give some examples of your own using the prepositions under study:
Due to, along with, for, via, as well as, since, in turn.
8. Translate the following expressions from Russian into English. Use these expressions in the sentences of your own:
Печатная технология, пробельная зона, печатная зона, олеофильный, гидрофильный, красковпитывающий, водоотталкивающий, физический феномен, увлажняющий раствор, хорошее смачивание (увлажнение), поверхностное натяжение, легко установить, широко использоваться долгое время, основной компонент, частицы неправильной формы, порошкообразный, толщина красочного слоя, формный цилиндр, офсетный цилиндр, печатный цилиндр, печатная форма.
9. Transfer the sentences from passive voice into active:
e .g.: Physical phenomena create this effect at the contact surfaces.
|
|
История создания датчика движения: Первый прибор для обнаружения движения был изобретен немецким физиком Генрихом Герцем...
Семя – орган полового размножения и расселения растений: наружи у семян имеется плотный покров – кожура...
Опора деревянной одностоечной и способы укрепление угловых опор: Опоры ВЛ - конструкции, предназначенные для поддерживания проводов на необходимой высоте над землей, водой...
Организация стока поверхностных вод: Наибольшее количество влаги на земном шаре испаряется с поверхности морей и океанов (88‰)...
© cyberpedia.su 2017-2024 - Не является автором материалов. Исключительное право сохранено за автором текста.
Если вы не хотите, чтобы данный материал был у нас на сайте, перейдите по ссылке: Нарушение авторских прав. Мы поможем в написании вашей работы!