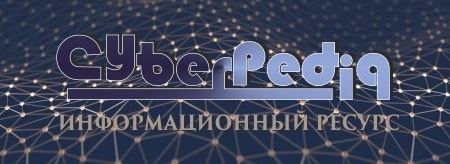
Папиллярные узоры пальцев рук - маркер спортивных способностей: дерматоглифические признаки формируются на 3-5 месяце беременности, не изменяются в течение жизни...
Семя – орган полового размножения и расселения растений: наружи у семян имеется плотный покров – кожура...
Топ:
Устройство и оснащение процедурного кабинета: Решающая роль в обеспечении правильного лечения пациентов отводится процедурной медсестре...
Оценка эффективности инструментов коммуникационной политики: Внешние коммуникации - обмен информацией между организацией и её внешней средой...
Марксистская теория происхождения государства: По мнению Маркса и Энгельса, в основе развития общества, происходящих в нем изменений лежит...
Интересное:
Распространение рака на другие отдаленные от желудка органы: Характерных симптомов рака желудка не существует. Выраженные симптомы появляются, когда опухоль...
Лечение прогрессирующих форм рака: Одним из наиболее важных достижений экспериментальной химиотерапии опухолей, начатой в 60-х и реализованной в 70-х годах, является...
Аура как энергетическое поле: многослойную ауру человека можно представить себе подобным...
Дисциплины:
![]() |
![]() |
5.00
из
|
Заказать работу |
Содержание книги
Поиск на нашем сайте
|
|
Almost all metals and alloys subject to the action of atmospheric air or other surrounding media (for example, sea water, soil, acid and alkali solutions, organic liquids, etc.) are gradually destroyed, beginning from the surface, and lose their initial appearance. This progressive destruction of a metallic surface exposed to an external aggressive (active) medium is called corrosion.
Experience shows that corrosive destruction depends mainly upon the following three factors: (1) the chemical nature "of the metal or composition of the alloy and their structures; (2) the chemical nature of the surrounding medium and the percentage of aggressive matter in metals (oxygen, moisture, acids, alkalis, etc.) and (3) the temperature of the surrounding medium.
As to its character, metal corrosion may be classified as: (1) uniform corrosion, in which the whole surface of the metal or alloy is corroded with equal intensiveness; (2) localized corrosion, in which only certain areas of the surface are attacked; (3) selective corrosion, where.-only separate structural components of an alloy are affected and (4) intercrystalline corrosion, which involves destruction of the metal or alloy along its grain boundaries.
According to the mechanism of the corrosion process, it is necessary to distinguish between chemical and electrochemical corrosion.
Chemical corrosion conforms to the laws of chemical kinetics. A typical example of chemical corrosion is the oxidation and erosion of the valves of internal combustion engines by the incandescent products of combustion. A film of corrosion products, usually oxides, is formed on the surface of metal in the course of chemical destruction. In some cases this film may protect the underlying metal against further corrosion, i. e. make it more passive in.respect to the surrounding medium.
Electrochemical corrosion occurs in the presence of liquids which are electrolytes containing free ions. The 4 scene of electrochemical corrosion is that the atoms, on the surface of the metal, ire contact with the electrolytic solution, pass into the solution as ions and leave an equivalent quantity of electrons in the metal.
1.What process is called corrosion?
2.What factors does corrosive destruction depend upon?
3. How may metal corrosion be classified
4. What is a typical example of chemical corrosion?
5. What is the essence of electrochemical corrosion?
6. What are the principal corrosion protection methods?
Вариант 4.
1. Переведите текст. Ответьте на вопросы. Задайте все возможные вопросы к выделенному предложению.
2. Выпишите и переведите все встречающиеся в тексте термины.
3. Поставьте первый абзац текста в прошедшее время.
MAGNESIUM AND ITS ALLOYS
Magnesium has a specific gravity of approximately 1.7; its alloys are the lightest of all engineering metals employed. The melting point of magnesium is 650° C; its boiling point is 1007° C. Magnesium is very inflammable and burns with a dazzling flame, developing a great deal of heat
|
The mechanical properties of magnesium, especially the tensile strength, are very low and therefore pure magnesium is not employed in engineering. The alloys of magnesium possess much better mechanical properties which ensure their wide application.
The principal alloying elements in magnesium alloys are aluminum, zinc and manganese. Aluminum, added in amounts up to 11 per cent, increases the hardness, tensile strength and fluidity of the alloy. Up to 2 per cent zinc is added to improve the ductility (relative elongation) and cast ability. The addition of 0.1-0.5 per cent manganese raises the corrosion resistance of magnesium alloys. Small additions of cerium, zirconium and beryllium enable a fine-grained structure to be obtained, they also increase the ductility and oxidation resistance of the alloys at elevated temperatures.
Magnesium alloys are classified into two groups; (1) wrought alloys, grades MAI, MA2, (2) casting alloys, grades MJI4, MJI5. Wrought magnesium alloys MAI and MA2 are chiefly used for hot smith and closed-die forged machine parts. They are less frequently used as sheets, tubing or bar stock. Magnesium casting alloys MJI4 and MJI5 are widely used as foundry material though their cast ability is Inferior to that of aluminum-base alloys.
1 What specific gravity has magnesium?
2. What is the melting point of magnesium?
3. Why is pure magnesium not employed in engineering?
4. What are the principal alloying elements in magnesium alloys?
5. How much aluminum is added to magnesium?
6. How much zinc is added to magnesium?
7. How much manganese is added to magnesium?
8. For what purpose are small additions of cerium, zirconium and beryllium added to magnesium?
Вариант 5.
1. Переведите текст. Ответьте на вопросы. Задайте все возможные вопросы к выделенному предложению.
2. Выпишите и переведите все встречающиеся в тексте термины.
3. Поставьте третий абзац текста в прошедшее время.
TITANIUM AND ITS ALLOYS
As engineering material titanium has been widely applied only in the last years.
Titanium is a silvery-white metal which melts at approximately 1668° C and has a specific gravity of 4.505. Commercially pure titanium possesses high strength properties. The tensile strength of most titanium alloys ranges from 100 to 140 kg/mm2, in conjunction with high elongation.
The hardness, tensile strength and yield point of titanium are increased with the degree of cold deformation. The elongation value drops rapidly when the degree of cold deformation (reduction) exceeds 50 per cent and becomes equal to 10 per cent. Impurities found in commercial titanium can be.divided into two groups: elements which form interstitial solid solutions with titanium (62, N, C and Hb) and elements which form substitution solid solutions (Fe and other metallic elements). The first have a much greater effect on the mechanical properties than those in the second group.
Even very small amounts of oxygen and nitrogen in titanium alloys sharply reduce the ductility. A carbon content of more than 0.2 per cent reduces both the ductility and impact strength of a titanium alloy. It is supposed that the brittleness of titanium is a result of strain ageing and is connected with the presence of dissolved hydrogen in the beta-phase.
|
Titanium and its alloys are hardened either by a surface heat treatment followed by ageing at 400°—500° C or by producing a case which contains nitrogen, carbon and boron Industrial titanium alloys contain vanadium, molybdenum, chromium, manganese, aluminum, tin, iron or other elements, singly or in various combinations.
A combination of high mechanical properties with a low specific weight and excellent corrosion resistance enables titanium to be used in building supersonic aircraft.
1.What is titanium?
2. What does the hardness, tensile strength and yield point of titanium depend upon?
3. Do very small amounts of oxygen and nitrogen in titanium alloys reduce the ductility?
4. How are titanium and its alloys hardened?
5. What constituents do industrial titanium alloys
contain?
Вариант 6.
1. Переведите текст. Ответьте на вопросы. Задайте все возможные вопросы к выделенному предложению.
2. Выпишите и переведите все встречающиеся в тексте термины.
3. Поставьте второй абзац текста в прошедшее время.
FUELS.
All fuels are of organic origin; their combustible constituents are carbon, hydrogen and various compounds of these elements (hydrocarbons). Fuels also contain a certain amount of oxygen and sulphur. Sulphur is the most harmful constituent of fuel since in the process of smelting some of it may dissolve in the metal and impair its properties.
Fuels used in metallurgy must contain the least possible amount of inert mineral admixtures which are incombustible and reduce the calorific poweri Solid, liquid and gaseous fuels are employed in process metallurgy. Solid fuels include charcoal, coke and coal.
Charcoal is used in small-volume blast furnaces for making high grades of cast iron with a low sulphur content. Charcoal is an expensive fuel; its production is limited because of the shortage of timber. Coke is a solid carbonized residue formed in the process of heating (dry distillation) of certain grades of coal in retort (coke) ovens. Coke is the chief type of metallurgical fuel for blast furnaces and cupolas; very high temperatures may be developed in its combustion. Of the numerous kinds of coal, the best qualities are found in anthracite. It has a denser structure and contains little volatile matter.
Coals, including anthracite, are practically not used for smelting iron in a blast furnace because they melt down at high temperatures. Mascot is a valuable raw material of the chemical industry, and therefore it must be replaced by gaseous fuels in process metallurgy. The gaseous fuels are coke-oven, producer, blast-furnace and natural gases. Coke-oven gas, obtained as a by-product in the manufacture of coke, burns with a colorless flame and develops very high temperatures in the furnace.
Producer gas is obtained in a producer furnace upon incomplete combustion of solid fuels. Blast-furnace gas is a by-product of the blast-furnace process in pig-iron production. Natural gas is obtained from gas fields. Natural gas is very cheap fuel with a high calorific power and is rich in hydrocarbons, especially methane. In recent years metallurgical plants have begun to use natural gas to a great extent.
1., What are the combustible constituents of fuels?
2. Where are solid, 'liquid and gaseous fuels employed?
3. What purpose is charcoal used for?
4. What purpose is coke used for?
5. In what kind of coal are the best qualities found?
6. Why must mascot be replaced by gaseous fuels in process metallurgy?
7. How is coke-oven gas obtained?
8. How is producer gas obtained?
9. How is blast-furnace gas obtained?
Вариант 7.
1. Переведите текст. Ответьте на вопросы. Задайте все возможные вопросы к выделенному предложению.
|
2. Выпишите и переведите все встречающиеся в тексте термины.
3. Поставьте второй абзац текста в прошедшее время.
IRON AND MANGANESE ORES
Iron ore comprises the ore body and the dead rock or gangue. The ore body is the name given to the natural chemical compounds of iron, most frequently its oxides, which are found in the ore. Practically all of the iron (98 to 99 per cent) is reduced from its chemical compounds in the blast furnace and goes over in'to the pig iron. The gangue of iron ore may be of various chemical composition. Most frequently it consists of quartzite (SiO2) or sandstone with an admixture of clayey matter. In the blast furnace the gangue is converted into slag thereby separating from the pig iron. Iron ores are classified a rich or lean according to the amount of gangue which they contain. After crushing and sizing, rich ores are charged directly into the furnace while lean ores are subjected to concentration in which the proportion of the ore body (iron oxides) in the ore is increased. As more effective concentration techniques are developed, it becomes possible to use lean ores which were previously dumped or not worked at all.
A certain amount of harmful impurities are always present in iron ores; they include sulphur, arsenic and phosphorus. Deposits mined first on an industrial scale are those in which the iron ore contains a negligible amount of harmful impurities and the optimum amount of gangue for the given conditions.
Since most iron ores contain very little manganese it is necessary to add manganese ore to the charge of the blast furnace in the manufacture of pig iron. The ore body of a manganese ore may comprise one of several oxides of manganese and compounds of manganese oxides and oxides of other elements.
Manganese ores used in the blast furnace contain from 25 to 40% Mn.
1.What constituents does iron ore comprise?
2. What is the ore body?
3. How much iron is practically reduced from its chemical compounds in the blast furnace?
4. Into what matter is the gangue converted in the blast furnace?
5. How are iron ores classified?
6. Are rich ores charged directly into the furnace?
7. Are lean ores subjected to concentration?
8. What deposits are mined first on an industrial scale?
9. What ore is added to the charge of the blast furnace in the manufacture of pig iron?
10.What constituents may the ore body of a manganese ore comprise?
Вариант 8.
1. Переведите текст. Ответьте на вопросы. Задайте все возможные вопросы к выделенному предложению.
2. Выпишите и переведите все встречающиеся в тексте термины.
3. Поставьте первый абзац текста в будущее время.
|
|
Своеобразие русской архитектуры: Основной материал – дерево – быстрота постройки, но недолговечность и необходимость деления...
История создания датчика движения: Первый прибор для обнаружения движения был изобретен немецким физиком Генрихом Герцем...
Поперечные профили набережных и береговой полосы: На городских территориях берегоукрепление проектируют с учетом технических и экономических требований, но особое значение придают эстетическим...
История развития хранилищ для нефти: Первые склады нефти появились в XVII веке. Они представляли собой землянные ямы-амбара глубиной 4…5 м...
© cyberpedia.su 2017-2024 - Не является автором материалов. Исключительное право сохранено за автором текста.
Если вы не хотите, чтобы данный материал был у нас на сайте, перейдите по ссылке: Нарушение авторских прав. Мы поможем в написании вашей работы!