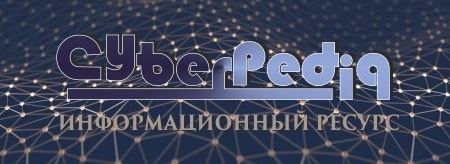
Механическое удерживание земляных масс: Механическое удерживание земляных масс на склоне обеспечивают контрфорсными сооружениями различных конструкций...
Семя – орган полового размножения и расселения растений: наружи у семян имеется плотный покров – кожура...
Топ:
Определение места расположения распределительного центра: Фирма реализует продукцию на рынках сбыта и имеет постоянных поставщиков в разных регионах. Увеличение объема продаж...
Особенности труда и отдыха в условиях низких температур: К работам при низких температурах на открытом воздухе и в не отапливаемых помещениях допускаются лица не моложе 18 лет, прошедшие...
Оценка эффективности инструментов коммуникационной политики: Внешние коммуникации - обмен информацией между организацией и её внешней средой...
Интересное:
Национальное богатство страны и его составляющие: для оценки элементов национального богатства используются...
Уполаживание и террасирование склонов: Если глубина оврага более 5 м необходимо устройство берм. Варианты использования оврагов для градостроительных целей...
Подходы к решению темы фильма: Существует три основных типа исторического фильма, имеющих между собой много общего...
Дисциплины:
![]() |
![]() |
5.00
из
|
Заказать работу |
|
|
The skilled trades together make up Bavaria's most diverse and – after industry – its second largest economic sector. In 1992, Bavaria's 140,000 craft businesses and their 1 million employees achieved an annual turnover of approx. DM 165 billion, this representing approx. 12,5 % of Bavaria's gross domestic product. These efficient and modern businesses which cover 127 different skilled trades make a major contribution to the success of the Bavarian economy. After all, one of the main reasons for Bavaria's (unprecedented leap from a primarily agricultural land to one of Germany's leaders in both economic and technological terms is the fact that Bavarian business is made up not only of large corporations operating on an international scale but also of numerous modern and highly dynamic small and medium-sized businesses.
Thanks to their diversity, the skilled trades are both active in and vital to virtually every branch of industry: In building and finishing, metalworking, woodworking, textiles and the clothing industry, the food industry, health and body care, industrial cleaning and in glass, paper and ceramics. The skilled trades perform countless important functions in both the economy and in society at large.
The skilled trades and economic progress: The skilled trades are flexible, creative and innovative. They both generate and act upon new ideas, putting these into practice fast without any bureaucratic delays. That's why so many new business developments start life in the skilled trades.
The skilled trades and new technologies: It goes without saying that craftsmen avail themselves of state-of-the-art technologies in addition to their traditional tools and methods.
The skilled trades and environmental protection: The skilled trades are helping to put into practice a professional and effective attitude to environmental protection. Take car mechanics, for example, who have an important role to play in the reduction of car exhaust fumes or the construction industry and related trades for whom energy conservation in building and heating systems has become a watchword.
The skilled trades and the division of labor: The skilled trades perform numerous important supply, service and finishing functions for other branches of industry. These range from the supply of quality precision parts to the maintenance and repair of machines and the cleaning of buildings.
The skilled trades and customer proximity: Thanks to their decentralized and demand-oriented structure, the skilled trades are able to respond particularly well to individual requirements and thus to ensure a wide range of highly differentiated, quality products and services geared to the demand.
The skilled trades and tradition: Craftsmen have always been both the creators and preservers of Bavaria's very rich and multifaceted traditions. This applies not only to the builders of Bavaria's churches and royal residences but also to gold and silversmiths, wood carvers and the brewers of Bavaria's world-famous beer.
|
The skilled trades and society: The characteristics typical of craftsmen, such as accountability for one's own actions, industriousness and a sense of one's responsibility to society, are indispensable if our social market economy and free and democratic society are to work. Bavaria's self-employed craftsmen, therefore, are a kind of compensatory force of the center, and that not only in economic and political spheres but also in society at large.
At first glance, the skilled trades in Bavaria do not appear to have profited from the export opportunities opened up by the European Single Market and the new markets in what used to be Bavaria's Eastern Bloc neighbors. This is because traditionally, they cater above all to local and regional requirements. At present, exports account for only 3 % of the skilled trades' collective turnover. As a recent survey indicated that over 50 % of Bavaria's craft businesses believe their products stand a good to fair chance on the European market, however, it looks as if this state of affairs will change very soon.
For the skilled trades, increased international cooperation means above all an expansion of their sales and supply markets for both goods and services, additional demand for quality products, increased supply work as a result of the industry's continued policy of contracting out whenever possible, increased opportunities to bid for public contracts and the possibility of obtaining additional manpower and a new generation of workers. An increase in international joint ventures on the part of small and medium-sized craft businesses would also strengthen this sector of the economy, this being a positive development for all countries concerned. After all, the health and efficiency of this sector are ultimately essential to the unification of Europe in freedom and prosperity.
MAN AND MACHINE
What is the role of the employee in an increasingly automated working environment? Jean Heymans of CECIMO examines the consequences -and costs - in terms of technical development and manpower.
The Luddites had a point. In the short term mechanisation has nearly always led to unemployment. But we recognise that over a longer time scale engineering innovation is a prime mover of industrial development and therefore of economic growth. Still, in these days of global competition and obstinately high levels of unemployment in the developed economies, 'automation' is once again seen as a threat to manufacturing jobs.
This view may be too pessimistic. Jean Heymans, Secretary General of CECIMO, thinks that the replacement of shop-floor workers by machines may have reached the optimal point: 'The more electronically-driven machine tools have in the past diminished the workforce at the end-user point. I don't think this is going to continue, however.'
There might even be a slight move in the opposite direction. 'The general tendency in the early eighties was towards big, flexible machining systems. What you see now are more stand-alone machines with very quick transfer of parts from one machine to another to achieve a better product in a simpler way.'
The machine tool industry is a good barometer of the state of the manufacturing industry as a whole. 'In our sector I'd say we are now picking up and employment is increasing slightly. It's a good sign,' says Jean Heymans.
This guarded optimism was reflected in the CECIMO-sponsored 1l.EMO Fair held in Milan in May 1995. 'The fair was very successful because of the quality of the visitors. In comparison with previous fairs there were fewer people, but companies had sent decision-makers with their staff, making meetings much more efficient. This is something we have observed world wide. It's encouraging because exhibitors lose less time and in Milan we were able to shorten the fair by one day.
|
'Among the technical developments, the most important ones concerned speed - speed in tool changes and in making the pieces and the development of linear motors. In the past there was a tendency to over-engineer machinery. This has changed to having simpler machines that really answer the needs of the customer. Modularity of machine tool parts is a developing tendency.
One of the oldest mechanical enterprises is WARKA. The basic production profile of WARKA includes:
· machine tool sets, applied and special-purpose;
· technological-production lines;
· welded casings;
· untypical special-purpose equipment;
· prototypes of machinery;
· electronic equipment;
· control units for machine tools and technological equipment.
The Warka Mechanical Equipment Works has a 100 year history. The Building Fix-
tures and Metal Casting Factory – the Lubert Brothers Inc. was established in 1891. Initially, the basic production consisted of various kinds of building fixtures. New products and technology were added in time: machine tools, drills, planning, screwing and sharpening machines, and rolling bearings testing machines. The years 1962 and 1963 saw the introduction of complex machine tool sets and complete technological-production lines. They supply our products to, among others, the FSM car factory in Bielsko Biala, the URSUS tractor factory and arms industry enterprises.
TOOLS FOR EVERY TASK
The market for tool export is shifting from Europe to the US and Asia-Pacific, with CNC and full service packages occupying an increasingly important position in market sales.
Machine tools are fundamental to the manufacturing process of any company and therefore occupy a strategic position at the heart of any industrial nation. They are the 'master' or 'mother' machine, with every manufactured good being made either directly by a machine tool, or by a machine that was made by a machine tool. As such the industry has traditionally been a barometer for the health of the economy. When machine tool investment is increasing companies are looking ahead, planning to expand or cope with increased demand. Conversely, when recession occurs, investment is the first item to be cut and as a result the industry tends to suffer tremendous cycles of fortune. Yet no piece of capital equipment is more important to the development of companies and their products, and the capacity to invest in such technology should be a fundamental concern for policy makers.
The machine tool industry has faced considerable restructuring over the last fifteen years in the face of two steep recessions, technical change and the advent of increased European legislation. The strong cyclical movement in demand for machines is a reflection of the industry's heavy dependence on investment demand, particularly in the capital goods sector which is its main market.
The UK machine tool industry which comprises the cutting, forming and processing of metals spans a wide spectrum of users, covering aerospace, automotive, defence and general engineering as well as any industry directly or indirectly involved in the manufacturing process. The aerospace and automotive sectors account for around 45 per cent of machine tool purchases in the UK.
The world machine tool market is now dominated by Germany and Japan who between them account for around 50 per cent of world production. Japan in particular has seen sharp growth from 5 per cent of the world market in 1970 to 25 per cent in 1995. The UK remains a significant supplier of machine tools, however, being the world's eighth largest producer and seventh largest exporter.
Technical developments have dramatically changed the structure of the machine tool industry as many manual operations have now been replaced by an electronics-based solution, undertaken by CNC machines which are capable of performing several different operations with tools automatically changed in a pre set sequence. Indeed the life cycle of machines is becoming ever shorter as the power of computers continues to increase. Machines are now likely to become obsolete within three to five years if they are not upgraded or replaced.
|
The development of technology within the machine tool industry continues to be increasingly sophisticated with machines capable of working to an accuracy of thousandths of a millimetre up to panels the size of aircraft wings. The major areas of development at present affect lasers, high speed machining up to 50,000 rpm and new materials which may in time supplant metal as a core material. Ceramics and plastics for example are being developed for use by the aerospace and automotive industries.
In some areas British machine tool technology leads the world, such as in probes and sensors, coordinate measuring devices and grinding and laser technology.
The outlook for the machine tool industry is dependent on a recovery in investment, not only in the UK but in the major industrial countries throughout the world, following the slump during the period 1990-1993. Although the climate has undoubtedly improved recently, continuing weak demand in Europe, particularly in the aerospace and defence sectors, will delay the growth in demand for capital goods and machine tools in the short term. However the combination of a competitive exchange rate, low interest rates coupled with sustained productivity growth ahead of most competitors should underpin the competitive position of most UK producers lifting their long term prospects.
In the UK manufacturing investment remains by common consent significantly below the levels of our major competitors and at present there appears to be little acceptance among policy makers that such a problem exists despite its acceptance amongst most commentators. With such investment, particularly in high technology goods, the UK would be able to take advantage of its other competitive leads. Without it we face the dual problems of increased inflation due to capacity pressures and, inevitably, a loss of quality.
SMART SOLDERING
Mike Judd and Keith Brindley of SMART give an insight into all that is new and exciting in the world of soldering.
In SC soldering processes, the component is placed on the printed circuit board at a later stage than solder and flux. At a later stage still, heat is applied. In a nutshell, then, SC soldering processes involve three distinct stages:
· applying solder and flux as a solder plastic;
· placing components;
· applying heat.
This separation of solder application from the application of heat (both go together in CS soldering process - and cannot be split because molten solder in a CS process itself supplies the required heat) effectively means that application of solder, in practice, becomes an assembly process rather than a soldering process. Readers are referred to Chapter 2 for a discussion on methods of solder paste application.
Heat application
There are only three basic ways of transferring heat; conduction - hot liquid, hot belt, heated collet; convection - hot air, hot gas, hot vapour; radiation -infra-red, laser, light beam.
Processes may be a combination of two or all three heat transfer methods but only two of these (infra-red and hot vapour) are used to any great extent.
Both infra-red and hot vapour soldering machines have been developed to such an extent there is really very little to choose between them. Both processes (at least their state-of-the-art variants) are capable of soldering densely-populated printed circuit assemblies to a high level of performance, and with few defects.
|
Laser soldering is currently in late developmental stages, and shows great promise for specialised SC soldering of surface mounted components. At present it is more costly than infra-red and hot vapour soldering processes, but it may find a niche market for soldering individual components which cannot easily be soldered by other mass means.
Infra-red soldering
Infra-red (IR) soldering processes have developed rapidly in recent years since their first introduction. Main developments of infra-red soldering machine processes with time are:
· focused lamps – near infra-red – fusing tin/lead electroplate;
· diffuse lamps;
· diffuse infra-red lamps and secondary reflector/emitters;
· diffuse vitreous flat panels – far infra-red (black);
· metal-faced flat black panels – far infra-red - natural convection;
· metal-faced panels and interstage recirculated convection;
· metal panels with holes for uniform forced convection;
· metal panels with holes and zoned forced convection;
· metal panels and higher volume zoned forced convection;
· metal panels and higher volume zoned forced convection of nitrogen.
Generally, infra-red soldering machines direct infra-red heat onto the board from above and below. Radiating elements have built-in thermocouples to allow temperature control. Heat transferred onto the assembly and so temperature of the joints to be soldered, however, depends on the materials and shapes of the board and components as well as wavelength of the infra-red radiation. For this reason, in such a basic infra-red machine it is difficult to be sure that all joints reach the same temperature at the same time. The effect of different joint temperatures is known as the shadow effect.
In operating terms, the shorter the wavelength of the infra-red element the more likely are boards and small components to suffer from overheating. On the other hand, more uniform heating of solder paste is obtained with short wavelengths.
Longer wavelength elements have an advantage in their air around them is heated. This hot air provides heat to assemblies by convection means. If hot air is allowed to aid heating of assemblies naturally the process is known as infrared radiation with natural convection heating. The addition of convection heating to infra-red radiant heat soldering machiners tends to give more uniform heating and reduce temperature differences between joints on assemblies.
This principle of using convection heating to reduce air temperature differentials is extended by forcefully circulating warmed air to provide forced convection heating. It can be extended further by forcing air through perforations in each infra-red panel emitter, such that it is distributed evenly over the assembly surface. In this way, high volumes of airflow can be generated at quite low velocities. In general, the higher the volume of forced airflow the smaller the difference between joint temperatures across an assembly. A further advantage of forced convection is the lower infrared emitter temperatures required.
By dividing the infra-red soldering machine into distinct and isolated zones, each of which use forced convection, greater control over assembly joint temperatures is available. Typically, air is taken into a zone from the assembly area, recirculated then diffused through heater elements back to the air intake. This effectively segregates each zone from its neighbour and gives a high degree of temperature isolation and controllability. Control of assembly temperature within such a soldering machine is achieved simply by standard computer and electronic closed-loop control principles, allowing high degrees of accuracy and adjustment.
Air is not the only gas which can be used in convection infra-red SC processes. An inert gas, say, nitrogen, can easily be incorporated into the system instead.
The ability of infra-red soldering machines to produce perfectly soldered assemblies depends on temperature uniformity over all the joints to be soldered. As an assembly passes through a soldering machine, the ideal is to maintain a constant temperature at all joints across the assembly; in other words there should be no difference in temperature between any two points on the printed circuit board. This elimination of temperature differential is often known as a zero.
Temperature differentials between joints can be caused by a number of factors, including:
· assembly variations - board size, component densities, component masses and so
on;
· heating elements - some infra-red heaters do not dissipate heat uniformly onto the
assembly surface;
· conveyor systems - which extract heat from an assembly local to the conveyor
|
supporting arms.
Hot vapour soldering
Hot vapour soldering processes saturated vapour, condensation, or vapour phase (VPS) soldering processes.
Although classed here as a convection form of heating, heat transfer in a hot vapour soldering process takes place when a saturated vapour condenses on the board, and is thus a product of the liquid's latest heat of evaporation. If a liquid is selected with a boiling point of that required to convert the solder paste into molten solder (around 215°C to 230°C), then once that temperature has been reached, no further condensation can take place so no further temperature rise can occur. Upper temperature control in the process is therefore simply not required - a significant advantage over other SC soldering processes, particularly those using infra-red heating elements.
In turn the equipment, in principle at least, is extremely simple. All element heats the liquid to boiling point, while the assembly is positioned in the resultant vapour above the liquid. Liquid used is a perfluorocarbon (this is no environmental threat). Times to reach soldering temperature range from as little as just 5 or 6 for small joints, to around 50 for large joints. The vapour also removes flux and flux residues in a washing action after soldering has taken place, reducing the requirement for post-assembly cleaning.
|
|
Опора деревянной одностоечной и способы укрепление угловых опор: Опоры ВЛ - конструкции, предназначенные для поддерживания проводов на необходимой высоте над землей, водой...
Археология об основании Рима: Новые раскопки проясняют и такой острый дискуссионный вопрос, как дата самого возникновения Рима...
История развития хранилищ для нефти: Первые склады нефти появились в XVII веке. Они представляли собой землянные ямы-амбара глубиной 4…5 м...
Особенности сооружения опор в сложных условиях: Сооружение ВЛ в районах с суровыми климатическими и тяжелыми геологическими условиями...
© cyberpedia.su 2017-2024 - Не является автором материалов. Исключительное право сохранено за автором текста.
Если вы не хотите, чтобы данный материал был у нас на сайте, перейдите по ссылке: Нарушение авторских прав. Мы поможем в написании вашей работы!