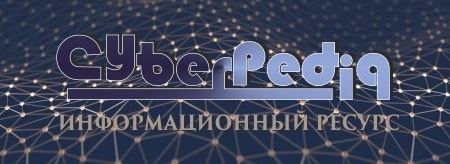
Общие условия выбора системы дренажа: Система дренажа выбирается в зависимости от характера защищаемого...
Адаптации растений и животных к жизни в горах: Большое значение для жизни организмов в горах имеют степень расчленения, крутизна и экспозиционные различия склонов...
Топ:
Устройство и оснащение процедурного кабинета: Решающая роль в обеспечении правильного лечения пациентов отводится процедурной медсестре...
Отражение на счетах бухгалтерского учета процесса приобретения: Процесс заготовления представляет систему экономических событий, включающих приобретение организацией у поставщиков сырья...
Оценка эффективности инструментов коммуникационной политики: Внешние коммуникации - обмен информацией между организацией и её внешней средой...
Интересное:
Национальное богатство страны и его составляющие: для оценки элементов национального богатства используются...
Аура как энергетическое поле: многослойную ауру человека можно представить себе подобным...
Уполаживание и террасирование склонов: Если глубина оврага более 5 м необходимо устройство берм. Варианты использования оврагов для градостроительных целей...
Дисциплины:
![]() |
![]() |
5.00
из
|
Заказать работу |
|
|
Эти системы разрабатываются производителями автомобилей, ориентированы главным образом на владельцев индивидуальных (некоммерческих) автомобилей, фирменные сервисные предприятия (дилеров) и стимулируют проведение ТО и ремонта на этих предприятиях.
Фирменные системы ТО и ремонта основаны на планово-предупредительной стратегии и информационно поддерживаются рядом документов.
1. В руководствах по эксплуатации, которыми располагают владельцы автомобилей, приводится минимум сведений:
• рекомендации проводить ТО на предприятиях технического обслуживания завода-изготовителя в соответствии с рекомендациями сервисных книжек;
• указания по выполнению минимального перечня операций между очередными обслуживаниями, которые включают проверку уровня масла и жидкостей, уход за шинами, замену ламп и плавких предохранителей, косметический уход за кузовом;
• перечень рекомендуемых топливно-смазочных материалов, эксплуатационных жидкостей и автопрепаратов;
• список ламп, применяемых на автомобилях.
Учитывая, что значительная часть владельцев автомобилей, даже в странах, имеющих традиционно развитую и доступную сервисную систему, обслуживают автомобили вне заводских сервисных предприятий, этих сведений явно недостаточно.
2. Структура системы ТО фиксируется в сервисных книгах, в которых указывается последовательность (план-график, цепочка) проведения ТО с определенной, как правило постоянной, периодичностью. Например, для семейства автомобилей ВАЗ-2110, -2111, -2112, "Вольво-400, -700, -900", "Мацда-626" такой периодичностью является 15 тыс. км, что соразмерно со среднегодовым пробегом индивидуальных легковых автомобилей в развитых странах. Такой план-график проведения ТО на автомобилях семейства "Вольво" "расписан" на 180 тыс. км, "Мацда" - на 180 тыс. км, ВАЗ – на 105тыс. км.
|
Каждый очередной вид ТО (после 15, 30, 45 тыс. км пробега автомобиля и т.д.) имеет свой перечень операций, который на 47-76% совпадает с предыдущим.
3. Ряд заводов-изготовителей для сервисных предприятий издает рекомендации по трудоемкости ТО и ремонта: трудоемкость работ (услуг) по техническому обслуживанию и ремонту ВАЗ-2110, -2111, -2112; справочник по нормативам стандартного времени для ТО и ремонта автомобилей "Вольво-300, -400, -700, -800, -900" (Volvo Standard Times Guide) и др.
4. Учитывая международный обмен автомобильной техникой (экспорт, импорт, лизинг, международные перевозки, туризм), большое значение и распространение приобретают обобщающие нормативные и технологические материалы, которые при их составлении автотранспортными и информационнымикомпаниями приобретают функции рекомендуемых нормативов ТЭА.
Лекция № 11
Основы рациональной организации ТО и ремонта
Транспортных средств
На автомобильном транспорте в течение длительного времени основное внимание уделялось поиску более совершенных методов организации производства и труда ремонтных рабочих. Вопросам управления производством не уделялось необходимого внимания. Это во многом обусловливалось небольшими размерами предприятий и слабым развитием их производственной базы. К основным методам организации производства относятся: организация специализированных и комплексных бригад, агрегатно-участковый и агрегатно-зональный методы.
Метод специализированных бригад применяется в сравнительно небольших АТП и предусматривает создание бригад, специализирующихся по видам технических воздействий. На каждую бригаду в зависимости от объема работ планируются определенное количество рабочих и фонд заработной платы.
|
При организации производства методом специализированных бригад одна группа (бригада) рабочих производит ТО-1, вторая ТО-2, третья — текущий ремонт автомобилей, четвертая ремонтирует агрегаты, снятые с автомобилей. Специализированные бригады состоят из рабочих различных профессий и квалификаций, необходимых для выполнения установленного комплекса работ по данному виду воздействия. При этом специализированная бригада выполняет работу по закрепленному за ней виду воздействия, как правило, но всем автомобилям АТП.
Специализация бригад по видам воздействий способствует повышению производительности труда рабочих и создает предпосылки для применения поточного метода организации технологического процесса ТО, позволяющего максимально механизировать процесс.
Однако при такой организации производства в случае преждевременного выхода агрегата или узла из строя практически сложно установить виновника, так как один рабочий смазывает агрегат, другой производит по нему крепежные работы, третий регулирует, четвертый ремонтирует его на автомобиле и пятый ремонтирует агрегат, снятый с автомобиля.
Метод комплексных бригад характеризуется тем, что за определенной группой автомобилей (например, за автоколонной, дизельными или карбюраторными автомобилями, прицепами и полуприцепами) автотранспортного предприятия закрепляется комплексная бригада, выполняющая ТО-1, ТО-2 и текущий ремонт.
В состав комплексной бригады входят слесари-регулировщики, слесари, электрики, смазчики, слесари-сборщики и рабочие других профессий, необходимые для выполнения закрепленных за бригадой работ.
При организации производства методом комплексных бригад обезличка ответственности за качество ТО и ремонта сохраняется. Следовательно, сохраняются и все недостатки, присущие методу специализированных бригад. Кроме того, при организации труда методом комплексных бригад каждая бригада, как правило, имеет свои рабочие места, посты для обслуживания и ремонта, свое оборудование и инструменты, запас оборотных агрегатов и запасных частей, что приводит к распылению материальных средств АТП и осложняет руководство производством обслуживания и ремонта автомобилей.
При этом методе организации производства возникают трудности в регулировании загрузки отдельных исполнителей по различным комплексным бригадам, так как комплексные бригады закреплены за группами автомобилей (колоннами). Зачастую возникают ситуации, когда рабочие одной комплексной бригады перегружены, а другой недогружены, рядом простаивают автомобили, но рабочие не заинтересованы в их выпуске на линию, так как они 'закреплены за другой комплексной бригадой.
|
Сущность агрегатно-участкового метода заключается в том, чтовеж работы по ТО и ремонту подвижного состава АТП распределяются между производственными участками, ответственными за выполнение всех работ ТО и ТР одного или нескольких агрегатов (узлов, механизмов и систем) по всем автомобилям АТП [3]. Моральная и материальная ответственность за качество ТО и ремонта закрепленных за участком агрегатов, узлов и систем при данной форме организации производства становится конкретной.
Результаты работы производственного участка оцениваются по средней периодичности ТР соответствующих агрегатов и по величине простоев автомобилей по техническим неисправностям агрегатов, закрепленных за участком.
Агрегатно-участковый метод, обладая определенными преимуществами по сравнению с ранее рассмотренными бригадными формами организации труда рабочих, вместе с тем не лишен недостатков.
Децентрализация производства при агрегатно-участковом методе затрудняет оперативное управление производством. Отсутствие информации о ходе выполнения ремонтов в целом по автомобилю не позволяет рационально использовать производственные площади (посты обслуживания и ремонта), материальные и трудовые ресурсы. Так, например, при обслуживании автомобиля, у которого обнаружены одновременно неисправности по нескольким агрегатам, узлам и системам, неизбежно его маневрирование по специализированным постам различных производственных участков, что ведет к увеличению времени нахождения автомобилей в ТО и ремонте. Имеют место скопление рабочих на одних автомобилях и излишние простои других автомобилей, требующих обслуживания.
Распределение автомобилей, поступающих на ТО и ремонт по производственным участкам, не позволяет планировать время окончания ремонта по всему автомобилю.
|
При агрегатно-зоналъном методе техническая служба строится в соответствии с принципами агрегатно-участковой организации. Но при этом число основных бригад рабочих соответствует числу специализированных зон ТО-2 и ремонта.
В наиболее крупных АТП в дополнение к специализированным по агрегатам бригадам организуется небольшая бригада рабочих общепаркового назначения.
ТО-1 производится, как правило, на потоке и силами специализированных по группам агрегатов бригад рабочих. В относительно небольших АТП может организовываться отдельная специализированная бригада рабочих по производству ТО-1.
Работы по ТО-2 производятся только в межсменное время суток, а по ремонтам — в несколько смен при переводе основной массы ремонтов, связанных с простоем автомобилей на межсменное время. Производство ТО-2 и сопутствующих ему ремонтов осуществляется за несколько приемов-заездов. Эти заезды строго соответствуют дням планового производства ТО.
В соответствии с числом плановых заездов на ТО-2 в АТП организуется несколько специализированных по агрегатам и системам автомобиля зон ТО-2 и ремонта.
Все цехи, склады и прочие подсобные помещения, обслуживающие определенную зону, располагаются на территории последней или по возможности ближе к ней.
Основным преимуществом агрегатно-зонального метода является то, что в этом случае облегчается возможность выполнения значительной части ремонтов и ТО-2 за межсменное время, сокращается время нахождения автомобилей в ТО и ремонте.
Однако агрегатно-зональный метод обладает практически всеми недостатками, присущими агрегатно-участковому методу. Кроме того, выполнение ТО-2 в несколько приемов-заездов приводит к тому, что в обороте планирование — производство постоянно находится большое количество автомобилей, и эти процессы на крупных АТП становятся неуправляемыми.
Анализ показывает, что на автомобильном транспорте первые попытки комплексно решить вопросы совершенствования организации и управления технической службой АТП нашли свое отражение в разработанной НИИАТом агрегатно-участковой системе организации ТО и ремонта автомобилей. В ней кроме рекомендаций по организации производства даны также рекомендации по другим элементам: учету и анализу, диспетчеризации производственных процессов, материальному стимулированию, должностным обязанностям, которые были разработаны в соответствии с основными принципами построения системы. Внедрение агрегатно-участковой системы дало определенные положительные результаты. Однако, как указано выше, наряду с положительными результатами в ходе внедрения и работы автохозяйств по агрегатно-участковой системе, выявился ряд значительных ее недостатков, вызванных; отсутствием лица, ответственного в целом за автомобиль при проведении его обслуживания или ремонта; наличием фактически двойственного оперативного подчинения рабочих, выделенных от участков для выполнения ТО и ремонта; возникающими трудностями при перераспределении работ, обеспечении очередности их выполнения, оказании взаимопомощи и т. д.; наличием у руководителей и рабочих производственных участков больших непроизводительных затрат времени на хождение, что препятствует эффективному управлению производством.
|
В связи с этим появилась необходимость разработки и внедрения более совершенных методов управления процессами ТО и ремонта подвижного состава на АТП.
11.2.. СТЕПЕНЬ ОСНАЩЕННОСТИ АТП ПРОИЗВОДСТВЕННО-ТЕХНИЧЕСКОЙ БАЗОЙ
Одним из решающих условий в достижении высокого уровня технической готовности автомобилей и снижении затрат на их обслуживание и ремонт является удовлетворение потребности ни в производственно-технической базе.
![]() |
По данным Гипроавтотранса, для нормального функционирования АТП удельный вес стоимости производственно-техническойбазы в основных производственных фондах предприятия (включающих, кроме базы, стоимость подвижного состава) должен в общем случае составлять 50%.
Специальными исследованиями, проведенными в Саратовском политехническом институте, эти рекомендации подтверждены. Так, полученная на основании корреляционного анализа статистических данных по большому ряду АТП Поволжья, Прибалтики и других районов страны зависимость коэффициента технической готовности αт
автомобилей от относительной стоимости производственно-технической базы
Sп-т.б в основных производственных фондах АТП имеет следующий вид (рис. 8).
Сначала повышение оснащенности АТП ведет к заметному росту коэффициента технической готовности αт, а когда стоимость базы достигает 45—50% стоимости основных фондов, его рост становится неощутимым.
Это позволяет считать, что на каждый рубль стоимости подвижного состава должно приходиться около 0,9—1,0 руб. стоимости производственно-технической базы.
Однако этими же исследованиями установлено, что на большинстве анализируемых АТП относительная стоимость базы ниже 50% при средних значениях на грузовых АТП — 34%, а на. АТП смешанного типа — 33%.
Более частным аспектом проблемы оснащенности АТП производственно-технической базой является степень обеспеченности их производственными площадями, и, в частности, постами ТО и ТР. При типовом проектировании за основу расчетов числа постов принимаются так называемые эталонные условия (определенный типаж подвижного состава, его среднесуточные пробеги и другие исходные данные), тогда как на практике, даже при одном и том же списочном числе автомобилей, потребности в постах для различных АТП могут как угодно отличаться друг от друга. Поэтому для каждого конкретного предприятия становится важным определение действительно необходимого числа рабочих постов. Общепринятая методика расчета постов для зон технического обслуживания не вызывает возражений.
Следует лишь учитывать, что в среднем на одном рабочем посту зоны ТО-1 и, в особенности, зоны ТО-2 может согласно технологии назначаться довольно большое число рабочих (от 3 до 5), что способствует сокращению общего числа постов, а следовательно, и площади зоны.
Существенным резервом повышения пропускной способности этих зон и сокращения потребной площади является во многих случаях организация двухсменной и трехсменной работы, а также использование одной и той же поточной линии для ТО-2 и для ТО-1 в различные смены суток.
В типовых проектах АТП поточный метод обслуживания зачастую распространен на все три вида профилактических воздействий; в связи с чем и количество поточных линий в производственных зданиях предусматривается вполне достаточное (а иногда даже более чем достаточное).
По-иному складывается проблема обеспечения АТП постами для текущего ремонта. Обычная методика расчета этих постов [108 и др.], подразумевая выполнение на автомобилях лишь разборочно-сборочных, контрольно-крепежных и регулировочных работ при высокой степени использования рабочего времени поста (0,85—0,90), приводит к заведомо меньшему расчетному числу постов ремонта, чем их требуется в обычных, наиболее распространенных условиях.
Имеющаяся тенденция в привлечении математического аппарата (например, теории массового обслуживания) для получения оптимального числа постов ремонта в практическом смысле не совсем правомерна, так как оптимальное число постов не в состоянии удовлетворить потребности АТП в такие пиковые периоды, как подготовка парка к очередному годовому техосмотру, подготовка автомобилей к работе на уборке урожая и т. д. В этом плане значительно целесообразнее можно считать начатый Гипроавтотрансом опыт проектирования зон ТР с постами подпора, которые при необходимости могут использоваться в качестве ремонтных постов. С такими планировочными решениями выполнены многие типовые проекты станций технического обслуживания автомобилей, проект гаража на 275 легковых автомобилей-такси для южных районов, проект главного корпуса предприятия на 250 автопоездов КамАЗ (рис. 10). Из приведенного рисунка видно, что на 22 собственно технологических поста ТО и ТР приходится 16 постов подпора, из которых большинство расположено непосредственно в зоне ТР. Очевидно, такой принцип оснащения АТП постами ремонта следует распространить и на случаи реконструкции действующих предприятий.
Вопросы оснащения АТП технологическим оборудованием, также являющиеся аспектом развития производственно-технической базы, рассматриваются в следующем параграфе.
11.3.. УРОВЕНЬ МЕХАНИЗАЦИИ И АВТОМАТИЗАЦИИ ТЕХНОЛОГИЧЕСКИХ ПРОЦЕССОВ
Одним из важнейших путей повышения производительности труда ремонтно-обслуживающих рабочих на автотранспортных предприятиях, а вместе с тем и сокращения простоев подвижного состава в ТО и ТР является дальнейший рост технического уровня производства, который, в первую очередь, характеризуется уровнем механизации и автоматизации.
В общем случае под уровнем механизации принято считать удельный вес механизированного труда в общем объеме работ [44]:
(60)
где Км — уровень механизации, %;
Тм — объем работ, выполняемых механизированным способом, чел-ч;
То— общий объем работ, чел-ч.
Рис. 10. План главного корпуса по типовому проекту АТП на 250 автопоездов КамАЗ:
1 — линия ТО-1; 2 — посты подпора: 3 — посты ТО-2 и ТР; 4 — пост углубленной диагностики; 5—помещения цехов и складов
Уровень автоматизации Кавтопределяется аналогично:
(61)
где Тавт — автоматизированный объем работ, чел-ч.
По существующей методике Гипроавтотранса [122] способы выполнения производственных операций или процессов, кроме ручного, подразделяются по степени внедрения механизации на четыре вида:
механизированно-ручные — при помощи простейших механизмов и ручного механизированного инструмента;
механизированные — с помощью машин, и механизмов, получающих энергию от специального источника;
комплексно-механизированные — при выполнении всего цикла механизмами и машинами;
автоматизированные — когда участие человека сводится лишь к наблюдению за работой машин и механизмов.
При этом уровень механизации на АТП оценивается тремя показателями: степенью охвата рабочих механизированным трудом С, уровнем механизированного труда в общих трудовых затратах
Yм и уровнем механизации и автоматизации производственного процесса (производства в целом) Yп по уравнениям, в которых для упрощения расчетов показатели трудозатрат Т заменены на количество рабочих Р, выполняющих работы различными способами:
(62)
(63)
(64)
где Р м — число рабочих, выполняющих работу механизированным способом;
Р м-р — число рабочих, выполняющих работу механизированно-ручным способом;
Рр — число рабочих, выполняющих работу вручную;
Р — общее число рабочих на участке (на производстве);
Yм.т — уровень механизированного труда в общих трудовых затратах, %;
Y м-р — уровень механизированно-ручного труда в общих трудовых затратах, %;
К — коэффициент механизации (отношение времени механизированного труда рабочего к общим затратам времени на данном оборудовании или рабочем месте);
И — коэффициент простейшей механизации (доля затрат времени механизированно-ручного труда в общих затратах времени рабочего за смену);
Yп. м. — уровень механизации и автоматизации производственных процессов при механизированном труде, %;
Yп. м-р — уровень механизации и автоматизации производственных процессов при механизированно-ручном труде, %;
П — коэффициент производительности оборудования (отношение затрат времени на выполнение операции или процесса вручную к затратам времени при использовании действующего оборудования).
Значения коэффициентов К, И, П приводятся в специальных таблицах [122].
Показатель общего уровня механизации Yп является не только количественным, но и качественным показателем, отражающим производительность применяемого оборудования.
О степени механизации и автоматизации производства свидетельствуют также такие показатели, как уровень оснащенности АТП оборудованием, определяемый удельным весом стоимости оборудования в общей стоимости пассивной части (здания, сооружения, оборудование) основных производственных фондов, а также стоимость оборудования, приходящаяся на один списочный автомобиль и др.
В последние годы процессы механизации и автоматизации охватывают все больше и больше объектов производства технического обслуживания и ремонта автомобилей.
Большинством АТП решен вопрос механизации таких трудоемких процессов, как снятие, установка и транспортировка агрегатов и крупногабаритных узлов автомобилей при их ремонте за счет внедрения различного типа подъемно-транспортного оборудования (электротельферов, кран-балок, мостовых кранов, авто- и электропогрузчиков и т. д.).
Решаются вопросы механизации работ по снятию и установке колес, демонтажу и монтажу автошин, вывешиванию и транспортировке автомобилей и т. д. На многих АТП продолжительное время работают механизированные посты для замены масел и выполнения смазочных работ, эксплуатируются автоматические и полуавтоматические установки для мойки автомобилей и другое технологическое оборудование.
Тем не менее, средние по предприятиям и ведомствам показатели говорят о далеко еще не достаточном уровне внедрения механизированного труда в производство ТО и ТР автомобилей.
Для целенаправленного, экономически обоснованного внедрения средств механизации и автоматизации, кроме укрупнения АТП, внедрения передовых методов технического обслуживания и ремонта, позволяющих развивать специализацию работ и рабочих мест и т. д., необходимо сам уровень механизации рассматривать по составляющим элементам.
Рекомендуемые показатели степени механизации по подразделениям [44] и по видам воздействий [87] целесообразно дополнить показателями и для отдельных видов работ (тяжелых работ со снятием и установкой агрегатов и узлов, их транспортировки; разборочно-сборочных работ и т.д.).
Возможно достижимый уровень механизации по подразделениям, по видам воздействий и по видам работ будет различный, но достигнутый уровень механизации па предприятии как обобщающий показатель позволит объективно оценить и сопоставить усилия различных предприятий в развитии механизации.
11.4.. ПОДГОТОВКА ПРОИЗВОДСТВА И СНАБЖЕНИЕ РАБОЧИХ МЕСТ
Повышение эффективности любого производства требует тщательной его подготовки.
Для своевременного и качественного выполнения работ по ТО и ремонту автомобилей необходимо осуществлять подготовку производства по двум направлениям:
1. Создание и совершенствование производственных мощностей, т.е. строительство необходимых производственных помещений; приобретение технологического оборудования, приспособлений и инструмента, подъемно-транспортного оборудования, механизмов и обеспечение их работоспособности; обеспечение производства всеми видами энергии; проведение мероприятий по охране труда.
2. Обеспечение производства ТО и ТР автомобилей необходимыми запасными частями, материалами; своевременная их доставка к рабочим местам; своевременное предоставление рабочим объемов работ; регулирование очередности выполнения заявок на ремонт и подачи автомобилей на посты ТО и ТР и т. д.
|
|
Биохимия спиртового брожения: Основу технологии получения пива составляет спиртовое брожение, - при котором сахар превращается...
Организация стока поверхностных вод: Наибольшее количество влаги на земном шаре испаряется с поверхности морей и океанов (88‰)...
Особенности сооружения опор в сложных условиях: Сооружение ВЛ в районах с суровыми климатическими и тяжелыми геологическими условиями...
Общие условия выбора системы дренажа: Система дренажа выбирается в зависимости от характера защищаемого...
© cyberpedia.su 2017-2024 - Не является автором материалов. Исключительное право сохранено за автором текста.
Если вы не хотите, чтобы данный материал был у нас на сайте, перейдите по ссылке: Нарушение авторских прав. Мы поможем в написании вашей работы!