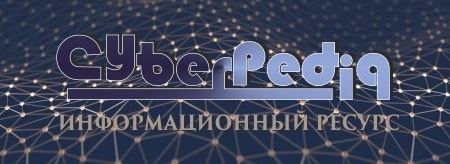
Двойное оплодотворение у цветковых растений: Оплодотворение - это процесс слияния мужской и женской половых клеток с образованием зиготы...
Организация стока поверхностных вод: Наибольшее количество влаги на земном шаре испаряется с поверхности морей и океанов (88‰)...
Топ:
Установка замедленного коксования: Чем выше температура и ниже давление, тем место разрыва углеродной цепи всё больше смещается к её концу и значительно возрастает...
Устройство и оснащение процедурного кабинета: Решающая роль в обеспечении правильного лечения пациентов отводится процедурной медсестре...
Оценка эффективности инструментов коммуникационной политики: Внешние коммуникации - обмен информацией между организацией и её внешней средой...
Интересное:
Что нужно делать при лейкемии: Прежде всего, необходимо выяснить, не страдаете ли вы каким-либо душевным недугом...
Лечение прогрессирующих форм рака: Одним из наиболее важных достижений экспериментальной химиотерапии опухолей, начатой в 60-х и реализованной в 70-х годах, является...
Финансовый рынок и его значение в управлении денежными потоками на современном этапе: любому предприятию для расширения производства и увеличения прибыли нужны...
Дисциплины:
![]() |
![]() |
5.00
из
|
Заказать работу |
Содержание книги
Поиск на нашем сайте
|
|
Семенов А.В., Гаврилов В.Н.
Технологическая практика в мастерских: Учебно-методическое пособие. - Чебоксары: ФГБОУ ВПО ЧГСХА, 2014. – 129 с.
Пособие соответствует федеральным государственным образовательным стандартам направлений подготовки и профилей подготовки (специальностей) в области техники и технологии и содержанию рабочей программы учебной практики «Технологическая в мастерских» Содержит сведения по содержанию и методике проведения технологической практики в учебных мастерских.
Изложены: основы слесарной и механической обработки деталей; основы сварки. Описаны: оборудование, инструмент, технологическая оснастка.
Предназначено для студентов высших учебных заведений, обучающихся по направлениям подготовки и специальностям в области техники и технологии.
Рецензенты: Мокеев Г.К, ст. преподаватель кафедры Ремонта машин и технологии конструкционных материалов ФГБОУ ВПО «ЧГСХА»;
Филиппов В.А., к.т.н., доцент кафедры машиноведения ФГБОУ ВПО «ЧГПУ им. И.Я. Яковлева».
Рекомендовано к изданию методической комиссией инженерного факультета ФГБОУ ВПО ЧГСХА.
Протокол №_____ от «___» __________2014 г.
© ФГБОУ ВПО ЧГСХА, 2014
© А.В. Семенов, В.Н. Гаврилов 2014
ВВЕДЕНИЕ
Технологическая учебная практика проводится в учебно-производственных мастерских кафедры ремонта машин и технологии конструкционных материалов.
Цель практики: закрепить теоретические знания студентов по обработке конструкционных материалов, подготовить студентов к производственным практикам, ознакомить с технологическим оборудованием и приемами работы на нем.
Задачи практики:
- обучить студентов навыкам обработки металлов резанием (на токарных, фрезерных, сверлильных и других станках), навыкам слесарной обработки и сварки материалов, подготовить их к изучению курса «Материаловедение. Технология конструкционных материалов».
|
- ознакомить студентов с основными свойствами обрабатываемых материалов, инструментом, приспособлениями и оборудованием, применяемыми для выполнения станочных, слесарных и сварочных работ.
Перед началом практических занятий со студентами проводятся теоретические занятия и инструктаж по охране труда.
Для практических занятий в мастерских группа делится на три звена: для выполнения станочных работ (1-е звено), слесарных работ (2-е звено), сварочных работ (3-е звено). Занятия проводят руководители из числа преподавателей кафедры и учебные мастера.
На теоретических занятиях студенты изучают основные технологические процессы изготовления деталей, применяемое оборудование, инструменты, охрану труда при выполнении работ.
Во время слесарной практики студенты изучают такие операции, как: разметка и рубка металлов, опиливание, шабрение, обработка отверстий размерным инструментом, нарезание резьбы и др. Основным принципом организации данного раздела практики является самостоятельная работа студентов над изготовлением деталей и изделий. В качестве зачётной работы студенты изготавливают одну деталь, которая является частью работ выполняемых ими во время станочной и сварочной практик.
Во время станочной практики студенты изучают методы обработки металлов резанием на металлорежущих станках. Осваивают методы обработки гладких цилиндрических и конических поверхностей, нарезание резьбы и обработку плоскостей. Одновременно студенты знакомятся с конструкцией токарных, фрезерных и сверлильных станков, методами заточки металлорежущего инструмента. После получения основных практических навыков выполнения станочных работ студенты приступают к изготовлению детали по заданию, предварительно познакомившись с технологической картой ее изготовления. В конце станочной практики студенты сдают зачётную работу – полностью или частично изготовленную деталь.
|
Во время сварочной практики студенты знакомятся с основными видами сварки, применяемыми в машиностроении и при ремонте машин. Изучают устройство оборудования для электродуговой сварки, методы подготовки свариваемого материала и настройки сварочного оборудования, учатся правильно выбирать диаметр электрода и силу сварочного тока. Студенты осваивают основные приёмы наложения горизонтальных и вертикальных швов электродуговой сваркой.
В конце практики студенты выполняют зачётную работу, заключающуюся в сборке несложной сварной конструкции.
По итогам практики студенты представляют отчет руководителю от кафедры. Отчёт включает конспект тем теоретических занятий, технологические карты изготовления деталей (или изготовления одной детали, если её изготовление включает все необходимые виды работ), описание основного используемого оборудования и инструмента при выполнении станочных, слесарных и сварочных работ.
Защита отчёта и общий зачёт по практике проводятся после прохождения практики. Аттестация осуществляется путем защиты отчета по практике перед комиссией, в состав которой входит руководитель практики и учебные мастера. Результаты аттестации заносятся в экзаменационную ведомость.
СЛЕСАРНАЯ ПРАКТИКА
ОБРАБОТКА ОТВЕРСТИЙ
При обработке отверстий различают три основных вида операций: сверление, зенкерование и развертывание.
Сверление – это операция по образованию сквозных и глухих отверстий в сплошном материале, выполняемая при помощи режущего инструмента – сверла. Различают сверление ручное - ручными пневматическими и электрическими сверлильными устройствами (дрелями) и сверление на сверлильных станках.
Одной из разновидностей сверления является рассверливание – увеличение диаметра просверленного ранее отверстия. В качестве инструментов для рассверливания отверстий также используют сверла.
Для сверления отверстий применяют различные типы свёрл: спиральные, перовые, оснащенные пластинками из твердого сплава, для глубокого сверления, центровочные, бесперемычные и др. Наиболее широкое распространение получили спиральные свёрла.
|
Спиральные сверла (рис.16) состоят из трех частей: рабочей части, хвостовика и шейки. Рабочая часть образована двумя спиральными канавками и включает в себя режущую и цилиндрическую и включает в себя режущую и цилиндрическую (направляющую) части с двумя ленточками. Режущей частью сверла является его вершина, образующая при заточке сверла два зуба с режущими кромками. Режущие кромки сверла выполняют основную работу резания.
Рисунок 16 - Конструкция спирального сверла
Хвостовик – часть сверла, предназначенная для его закрепления (хвостовики имеют коническую и цилиндрическую форму).
Шейка – промежуточная часть между хвостовиком и телом сверла, содержащим рабочую часть.
Лапка – концевая часть конического хвостовика, служащая упором при выбивании сверла из конического отверстия шпинделя станка.
Поводок – концевая часть цилиндрического хвостовика, предназначенная для дополнительной передачи крутящего момента при резании.
Зенкерованием называется операция, связанная с обработкой предварительно просверленных, штампованных, литых отверстий с целью повышения их точности и качества поверхности. Операция выполняется при помощи специального инструмента – зенкера (рис.17). В отличие от сверла зенкер имеет большее число режущих кромок (три или четыре), что обеспечивает получение поверхностей с более высокими показателями точности и качества. По конструкции зенкеры бывают насадные и цельные.
Рисунок 17 - Зенкер
К разновидностям зенкерования относятся зенкование и цекование.
Зенкование – это обработка на просверленных отверстиях конических углублений под головки винтов и заклепок, а также фасок. Операция выполняется при помощи специального инструмента – зенковки (рис.18).
Рисунок 18 - Зенковка
Цекование – это операция по обработке опорных поверхностей под крепежные детали (шайбы, гайки, стопорные кольца ит.п.). Операция выполняется с помощью специального инструмента – цековки (рис.19). В отличие от зенкеров имеют режущие зубья на торце и направляющие цапфы, которые обеспечивают нужное направление в процессе обработки. Цапфа вводится в предварительно просверленное отверстие.
|
Рисунок 19 - Цековка
Развертывание – это операция по обработке ранее просверленных отверстий с высокой степенью точности и малой шероховатостью. Обработка развертыванием выполняется после предварительного сверления, рассверливания и зенкерования отверстия развертками (рис.20). Которые подразделяются на черновые и чистовые, ручные и машинные. Осуществляется развертывание как вручную, так и на станках.
Рисунок 20 - Развертка
НАРЕЗАНИЕ РЕЗЬБЫ
Нарезанием резьбы называется образование резьбы снятием стружки (а также пластическим деформированием) на наружных или внутренних поверхностях заготовок деталей.
В зависимости от конфигурации профиля резьба бывает треугольной, трапецеидальной, прямоугольной и круглой. Каждая резьба характеризуется определенными числовыми параметрами – элементами (рис.21), которыми являются шаг, угол профиля, наружный, внутренний и средний диаметры.
Шаг резьбы S – это расстояние в миллиметрах между вершинами двух соседних витков резьбы, измеренное в направлении ее оси.
Высота профиля t – это расстояние от вершины резьбы до основания профиля, измеренное в направлении, перпендикулярном оси резьбы.
Основание резьбы – это участок профиля резьбы, находящийся на наименьшем расстоянии от ее оси.
Угол профиля α – это угол между прямолинейными участками сторон профиля резьбы.
Наружный диаметр резьбы d – это наибольший диаметр, измеряемый по вершинам резьбы перпендикулярно ее оси.
Внутренний диаметр резьбы d1 – это наименьшее расстояние между противоположными основаниями резьбы измеренное перпендикулярно ее оси.
Средний диаметр резьбы d2 – это диаметр условной окружности, проведенный посредине профиля резьбы между дном впадины (основанием резьбы) и вершиной выступа перпендикулярно оси резьбы.
Рисунок 21 - Элементы резьб: а – треугольной; б – прямоугольной; в –трапецеидальной упорной; д – круглой; α – угол профиля; S – шаг резьбы; d – наружный диаметр резьбы; d1 – внутренний диаметр резьбы; d2 – средний диаметр резьбы.
По направлению движения винтовой линии резьба бывает правой и левой. Кроме того, резьбы бывают одно и многозаходными. Однозаходные имеют малые углы подъема винтовой линии и применяются для надежного крепления деталей. Резьбу на деталях получают нарезанием на резьбонарезных, сверлильных и токарных станках, накатыванием или вручную при помощи метчиков (рис.22), служащих для нарезания внутренней резьбы, и плашек (см. рис.23), используемых для нарезания наружной резьбы.
Метчики делятся на ручные и машинные, изготавливаемые из инструментальной стали марок У8, У12, 9ХС. Для нарезания внутренней резьбы вручную требуется большое усилие. Для облегчения работы и для получения более чистой резьбы ручные метчики выпускаются комплектно: черновой, средний и чистовой, причем на метчиках соответственно наносят 1, 2 и 3 кольца для их различия.
|
Для уменьшения нагревания метчика и для получения более чистой резьбы необходимо применять смазочно-охлаждающие жидкости, выбираемые в зависимости от материала детали.
Рисунок 22 - Метчик для нарезания внутренней резьбы
До нарезания резьбы в деталях сверлят отверстия диаметром несколько меньше, чем диаметр будущей резьбы.
Диаметр сверла выбирают по табличным данным (табл. 1) или вычисляют по формулам:
Dсв = dр − S, или d = D − 1,5 t, (13)
где Dсв − диаметр сверла, мм; dр − диаметр резьбы, мм; S − шаг резьбы, мм; d − диаметр отверстия под резьбу, мм; D − наружный диаметр резьбы, мм; t − глубина резьбы, мм.
Таблица 1 - Диаметры свёрл, применяемых для получения резьбовых отверстий
Диаметр резьбы, мм | Диаметр сверла, мм | Диаметр резьбы, мм | Диаметр сверла, мм | ||
Чугун, бронза | Сталь, латунь | Чугун, бронза | Сталь, латунь | ||
М 2 | 1,5 | 1,5 | М 14 | 11,7 | 11,8 |
М 4 | 3,4 | 3,5 | М 16 | 13,8 | 13,9 |
М 5 | 4,1 | 4,2 | М 18 | 15,1 | 15,3 |
М 6 | 4,9 | 5,0 | М 20 | 17,1 | 17,3 |
М 8 | 6,6 | 6,7 | М 22 | 19,1 | 19,3 |
М 10 | 8,3 | 8,4 | М 24 | 20,5 | 20,7 |
М 12 | 10,0 | 10,1 |
Наружную резьбу нарезают с помощью плашек (рис.23). Плашки бывают круглые (цельные и разрезные) и призматические (раздвижные). Цельными плашками можно нарезать резьбу только одного диаметра, а разрезными можно регулировать диаметр резьбы, нарезаемой в небольших пределах.
Рисунок 23 - Плашка для нарезания наружной резьбы
Диаметр нарезанной резьбы измеряют штангенциркулем. Для определения шага резьбы применяют резьбомер. Для комплексной проверки резьбы применяют комплект резьбовых калибров, состоящий из проходного и непроходного калибров.
Диаметр стержня для нарезания резьбы определяют по табл.4.
Таблица 2 - Диаметр стержня для нарезания резьбы
Диаметр резьбы, мм | Шаг резьбы, мм | Диаметр стержня, мм | |
наименьший | наибольший | ||
М 6 | 1,0 | 5,8 | 5,8 |
М 8 | 1,25 | 7,8 | 7,9 |
М 10 | 1,50 | 9,75 | 9,85 |
М 12 | 1,75 | 11,76 | 11,88 |
М 14 | 2,0 | 13,7 | 13,82 |
М 16 | 2,0 | 15,7 | 15,82 |
М 18 | 2,5 | 17,7 | 17,82 |
М 20 | 2,5 | 19,72 | 19,86 |
Содержание отчета
1. Наименование работы.
2. Формулировка и исходные данные индивидуального задания.
Задание: «Описать технологию изготовления детали (изделия), перечни и характеристики используемого оборудования и оснастки, представить результаты контроля размеров».
3. Чертеж детали «Ушко».
4. Перечень технологических методов слесарной обработки, используемых при изготовлении детали.
5. Наименование и характеристика технологического оборудования: наименование, модель, технологические возможности, части и узлы станка.
6. Эскиз технологического перехода с указанием получаемого размера и шероховатости обработанной поверхности (дается по заданию преподавателя).
7. Перечень применяемых при выполнении технологического перехода приспособлений, режущих, вспомогательных и измерительных инструментов.
8. Результаты контроля размеров изготовленного изделия, представленные в форме табл. 4.
Таблица 4 - Результаты измерения детали «Ушко»
Размер по чертежу | 60-0,8 | 30-0,6 | Ø13 | 16±0,2 | R15 |
Размер действительный |
9. Выводы.
Таблица 3 -Технологическая карта изготовления детали «Ушко» методами слесарной обработки
Чертеж детали
![]() | |||||
№ пп | Содержание перехода | Эскиз перехода | Режущий инструмент и оснастка | Режим обработки | Измерительный инструмент |
1 | 2 | 3 | 4 | 5 | 6 |
Править заготовку | ![]() | Правильная плита, молоток | Лекальная линейка | ||
Установить и закрепить заготовку | ![]() | Верстак, тиски слесарные | Линейка 0–150 мм |
Продолжение табл.3
1 | 2 | 3 | 4 | 5 | 6 |
Опилить грани 1 и 2 под углом 900 последовательно | ![]() | Напильник плоский, № 2, длиной 250 мм | Угольник 900 | ||
Разметить заготовку в соответствии с эскизом | ![]() | Линейка, чертилка, кернер, молоток, циркуль разметочный | Штангенциркуль 0–150 мм | ||
Отрезать углы и стороны заготовки по контуру | ![]() | Ножовка по металлу | Штангенциркуль 0–150 мм | ||
Установить и закрепить заготовку | ![]() | Верстак, тиски слесарные | Линейка 0–150 мм | ||
Опилить заготовку по контуру с переустановкой в тисках | ![]() | Напильник плоский, № 2 | Штангенциркуль 0–150 мм, шаблон R 15 |
продолжение табл.3
1 | 2 | 3 | 4 | 5 | 6 |
Установить и закрепить заготовку | ![]() | Настольно-сверлильный станок, машинные тиски | |||
Установить и закрепить спиральное сверло Ø 4мм | Сверло спиральное Ø4 мм, патрон сверлильный | ||||
Сверлить по разметке 4 отверстия Ø 4 мм | ![]() | Настольно-сверлильный станок, сверло спиральное Ø 4мм, патрон сверлильный | n= 710 мин-1, подача – ручная | Штангенциркуль 0–150 мм | |
Снять сверло и установить коническую зенковку | Зенковка коническая с углом конуса 900, патрон сверлильный | ||||
Зенковать 3 отверстия | ![]() | Зенковка коническая с углом конуса 900, патрон сверлильный | n= 710 мин-1, подача – ручная | Шаблон 900×1 мм |
продолжение табл.3
1 | 2 | 3 | 4 | 5 | 6 |
Снять зенковку и установить сверло, переустановить заготовку | Спиральное сверло Ø 13 мм, переходная втулка, машинные тиски | ||||
Рассверлить отверстие Ø 13 мм | ![]() | Спиральное сверло Ø 13 мм, переходная втулка, машинные тиски | n = 280 мин-1, подача – ручная | Штангенциркуль 0–150 мм | |
Раскрепить и снять заготовку со станка, закрепить заготовку в слесарных тисках | ![]() | Верстак, тиски слесарные | Штангенциркуль 0–150 мм | ||
Опилить плоскости А и Б заготовки, обеспе чивая заданную шероховатость | ![]() ![]() | Верстак, тиски слесарные, напильник плоский № 3, L= 250 мм. | Обработка перекрестным движе- нием | Эталоны шероховатости | |
Раскрепить, снять заготовку, контролировать размеры | Штангенциркуль 0-150мм, шаблон R15 мм |
СТАНОЧНАЯ ПРАКТИКА
ОБЩИЕ ПОЛОЖЕНИЯ
Обработка металлов резанием – это удаление режущим инструментом с поверхностей заготовки слоя металла (стружки) для получения необходимой геометрической формы, точности размеров, взаиморасположения и шероховатости поверхностей детали. Удаленный слой металла называют припуском. Для осуществления резания инструмент и заготовку закрепляют в рабочих органах станка, которые обеспечивают относительные движения заготовки и инструмента.
Движения рабочих органов станка делят на движения резания и вспомогательные. Движения, которые обеспечивают срезание с заготовки слоя металла, называют движениями резания. К ним относятся главное движение D Ги движение подачи DS. За главное принимают движение, которое определяет скорость деформирования и отделения стружки, за движение подачи − движение, которое обеспечивает непрерывность врезания режущей кромки инструмента в материал заготовки. К вспомогательным движениям относятся закрепление заготовки и инструмента, быстрое перемещение рабочих органов станка, переключение скоростей движения резания и подачи и т. д.
Токарные приспособления
Для установки и закрепления заготовок на токарных станках используют различные приспособления (рис. 37).
К основным типам приспособлений относят: трехкулачковые самоцентрирующие и четырехкулачковые патроны, цанговые и поводковые патроны, центры.
а б в
г
д е
Рисунок 37 - Приспособления к токарным станкам:
а – трехкулачковый самоцентрирующий патрон; б – четырехкулачковый патрон;
в – планшайба; г – центр обыкновенный; д – центр вращающийся; е – люнет
Патрон закрепляют на шпинделе станка, а центр устанавливают в пиноли задней бабки или в отверстии шпинделя станка.
Патроны подразделяют на простые и самоцентрирующие. Самоцентрирующие патроны (рис.37, а) в большинстве случаев изготавливают трехкулачковыми и реже – двухкулачковыми. Трехкулачковые самоцентрирующие патроны очень удобны в работе, так как все кулачки, закрепляющие заготовку, перемещаются по радиальным пазам одновременно и синхронно друг с другом к центру или от центра. Поэтому заготовка, имеющая цилиндрическую поверхность (наружную или внутреннюю), устанавливается и закрепляется в патроне так, что ее ось совмещается с осью шпинделя. Кроме того, в этом случае значительно сокращается время на установку и закрепление заготовки.
Простые (несамоцентрирующие) патроны (рис.37, б) изготовляют обычно четырехкулачковыми. Каждый кулачок в них перемещается своим винтом независимо от остальных. Это позволяет устанавливать и закреплять в патронах заготовки цилиндрической и нецилиндрической форм.
При обработке на токарных станках длинных и нежестких заготовок применяют люнеты (рис.37, е) (подвижные и неподвижные); при o6pаботке заготовок больших диаметров и несимметричной формы используют планшайбы (рис 37, в), Кроме приведенных приспособлений на рис. 37 применяют различные специальные приспособления и оправки.
Фрезерные приспособления
В процессе фрезерования заготовка должна быть закреплена в необходимом по отношению к фрезе положении, а само крепление должно быть достаточно прочным и жестким, чтобы противостоять силам резания, возникающим при обработке. Чаще всего с этой целью применяют планки, машинные тиски, упоры и универсальную делительную головку, которые и называют приспособлениями.
К простейшему виду крепёжных приспособлений относят прижимные планки, которые при помощи болтов прижимают заготовку либо к поверхности стола, либо к особым планкам, которые подкладывают под заготовку (рис.45). Квадратные головки болтов при этом вводят в Т-образные пазы стола станка.
Рисунок 45 - Крепление заготовки прижимными планками
Для закрепления заготовок широко применяют машинные тиски, у которых одна из губок неподвижна. В зависимости от того, как должна быть установлена заготовка по отношению к фрезе, используют простые (рис.46, а), поворотные (рис.46, б) и универсальные (рис.46, в) машинные тиски.
а б
в
Рисунок 46 - Типы машинных тисков: а – простые, б – поворотные, в – универсальные
Поворотные тиски обеспечивают возможность поворота заготовки без ее раскрепления вокруг вертикальной оси, а универсальные – вокруг вертикальной и горизонтальной осей. Углы поворота устанавливают по значениям, указанным на круговых шкалах основания тисков.
Тиски закрепляют на столе станка при помощи болтов, головки которых вводят в Т-образные пазы стола.
Универсальная делительная головка (УДГ).Одним из сложных видов работ, выполняемых на фрезерных станках, является последовательное фрезерование на заготовке нескольких фасонных канавок, расположенных под заданными углами друг к другу. Примером детали с такими канавками является зубчатое колесо. Последовательное фрезерование очередной канавки после фрезерования предыдущей без раскрепления и снятия заготовки со станка требует поворота ее на заданный между канавками угол. С этой целью используют приспособление, называемое универсальной делительной головкой (рис. 47).
Универсальные делительные головки значительно расширяют технологические возможности фрезерных станков, способствуют повышению, как производительности, так и точности обработки. Применение делительных головок позволяет устанавливать обрабатываемую заготовку под заданным углом к плоскости стола станка, выполнять ее поворот на требуемый угол, обеспечивать непрерывное вращение заготовки при фрезеровании винтовых канавок.
Рисунок 47 - Универсальная делительная головка
Универсальные делительные головки используют при выполнении таких видов работ, как нарезание зубьев зубчатых колес, фрезерование стружечных канавок у сверл, разверток, зенкеров, метчиков и фрез; фрезерование боковых граней специальных болтов, гаек и т. п.
Делительная головка имеет чугунное основание 1 со стяжными дугами 2, на котором установлен корпус 3. Ослабив гайки 4 (рис.48), можно поворачивать корпус на определенный угол. Отсчет углов поворота производится по шкале и нониусу 5 (рис.47), имеющемуся на корпусе.
На опорной плоскости основания делительной головки имеются два точно пригнанных параллельно шпинделю сухаря, которые служат для установки головки и задней бабки в пазы стола фрезерного станка.
В корпусе расположен шпиндель со сквозным отверстием. Концы шпинделя расточены под конус Морзе. На одном конце устанавливается центр 6, на другом – оправка для дифференциального деления. Передний конец шпинделя имеет резьбу 7 и центрующий поясок для установки и крепления планшайбы с поводком или самоцентрующегося патрона. На буртике шпинделя установлен лимб 8 непосредственного деления.
Рисунок 48 - Делительная головка (вид сзади).
На шпинделе, в средней его части, установлено червячное колесо с круговой выточкой на торце, в которую входит конец зажима 9, смонтированного в корпусе 3. Червячное колесо, имеющее 40 зубьев, получает вращение от однозаходного червяка, расположенного в эксцентрической втулке. Червяк может быть введен в зацепление или выведен из него поворотом эксцентрической втулки с помощью рукоятки 10 (рис.48) с сектором 11. Передаточное отношение червячной пары составляет 1:40.Делительный диск 12 посажен на вал, смонтированный в подшипниках скольжения, один конец которого расположен в корпусе 2 (см.рис.47), другой – в крышке 13. Крышка фиксируется на корпусе центрирующей расточкой и крепится неподвижно к основанию. Количество отверстий на делительных кругах, расположенных с одной стороны делительного диска, равно 24, 25, 28, 30, 34, 37, 38,39, 41, 42 и 43, и с другой стороны – 45, 46, 49, 51, 53, 54, 57, 58, 59, 62, 66.
На валу делительного диска установлены коническая и цилиндрическая шестерни, а также приводная рамка, имеющая рукоятку с фиксатором, перемещающуюся по требуемому ряду отверстий на делительном диске. К делительному диску с помощью пружины прижат раздвижной сектор 14, состоящий из двух линеек и зажимного винта, с помощью которого линейки устанавливаются под требуемым углом. Пружинная шайба предотвращает самопроизвольный поворот сектора.
Вал 15 механического привода от станка смонтирован в подшипниках скольжения и расположен во втулке 16 с фланцем. Втулка крепится в крышке 11. На его конце расположена коническая шестерня, которая находится в постоянном зацеплении с конической шестерней, сидящей на валу делительного диска. Делительный диск фиксируется в требуемом положении стопором 17.
Задняя бабка служит для крепления обрабатываемой детали. Центр бабки можно перемещать в горизонтальном и вертикальном направлениях. В основании 18 расположен корпус 19, который штифтом соединен с рейкой. Вращением головки зубчатого вала корпус можно перемещать вверх и поворачивать относительно оси штифта. В требуемом положении задняя бабка крепится на столе станка с помощью болтов и гаек.
Перемещение пиноли 20 с полуцентром 21 осуществляется вращением маховика 22, укрепленного на винте.
На опорной плоскости основания имеются два направляющих сухаря, выверенных относительно оси пиноли, сухари обеспечивают совпадение центров делительной головки и задней бабки при установке их на стол станка.
Люнет является дополнительной опорой при обработке длинных и тонких деталей. Он состоит из корпуса 23, в котором расположен винт, перемещающийся с помощью гайки 24. Винт имеет призматическую головку 25. С помощью стопорного винта 26 головку можно закреплять на требуемой высоте.
Периодический поворот обрабатываемой детали на определенный угол выполняют способами непосредственного, простого и сложного (дифференциального) деления. При этом обычно кроме заданного числа, на которое необходимо разделить окружность, учитывается также и характеристика N делительной головки, которая представляет собой величину, обратную передаточному отношению червячной передачи. Все делительные головки отечественного производства имеют характеристику N = 40.
Непосредственное деление осуществляют поворотом шпинделя универсальной делительной головки с закрепленной на нем заготовкой рукояткой, при этом отсчет угла поворота ведут по лимбу 8. Данный метод не обеспечивает высокую точность угла поворота. Его применяют при повороте заготовок на углы типовых значений: 10, 20, 30, 40, 60, 90, 120, 180 градусов.
Простое деление реализуют в тех случаях, когда требуется обеспечить высокую точность углового расположения обрабатываемых поверхностей заготовки друг относительно друга.
Заготовку при использовании данного метода поворачивают на заданный угол α (заданную часть окружности) вращением рукоятки. Требуемая точность углового расположения обработанных поверхностей достигается применением в процессе «деления» делительного диска 12 и проведением до обработки некоторых расчетов с последующей несложной наладкой универсальной делительной головки. Основная задача при расчетах состоит в определении числа оборотов nр рукоятки, которое следует сделать для поворота заготовки на заданный угол α. Это число определяют по формуле:
nр = N / z, (6)
где z – часть полного оборота заготовки, соответствующая повороту ее на заданный угол α; z = 360/ α. При фрезеровании многогранника значение z соответствует числу его граней.
Дифференциальное деление. Дифференциальное деление применяют при необходимости поворота заготовки на заданный угол в том случае, когда метод непосредственного деления не обеспечивает заданную точность углового расположения обработанных поверхностей, а возможность такого поворота простым методом не предусмотрена. Методика выполнения деления заготовки в данной работе не рассматривается.
Установка режима резания.
Элементами режима резания при фрезеровании являются: скорость главного движения резания υ, м/мин, подача заготовки s и глубина резания t, мм. Скорость резания представляет собой окружную скорость точек режущих кромок лезвия фрезы, наиболее удаленных от её оси. Скорость резания определяют по формуле:
υ = π Dфр n / 1000, (7)
где Dфр – диаметр фрезы, мм; n – частота вращения фрезы, мин-1.
Подача s – поступательное перемещение заготовки относительно фрезы в единицу времени. Подачу выбирают, исходя из прочности обрабатываемого материала и режущего инструмента, глубины резания и требований к шероховатости обработанной поверхности.
При фрезеровании различают три вида подач:
– минутную подачу Sм, мм/мин, которая соответствует величине перемещения стола с заготовкой за минуту;
– подачу на оборот Sо, мм/об, равную значению перемещения стола с заготовкой за один оборот фрезы;
– подачу на зуб Sz, мм/зуб, которая равна перемещению стола с заготовкой за время поворота фрезы на угловой шаг ее зубьев. Подачу на зуб выбирают из справочника. Она является исходной для расчета S о и Sм:
So = Sz·z; (8)
Sм = S o∙ n = Sz·z·n. (9)
Глубиной резания называют расстояние между обрабатываемой и обра-ботанной поверхностями заготовки по нормали к обработанной поверхности. На основе заданной или выбранной по справочнику скорости главного движения резания рассчитывают частоту вращения шпинделя nрасч на основе формулы (7), а затем по табличным данным станка выбирают частоту вращения шпинделя, выполнив условие nст ≤ nрасч. Вслед за этим рукоятки коробки скоростей устанавливают в положения, обеспечивающие выбранное значение nст.
Исходя из принятой частоты вращения шпинделя nст, числа зубьев фрезы и подачи на зуб Sz по формуле (9) рассчитывают минутную подачу. На станке устанавливают ближайшее меньшее значение минутной подачи, которое указано на таблице коробки подач станка.
Установку фрезы на необходимую глубину резания t при фрезеровании осуществляют следующим образом:
– сообщают фрезе вращательное движение;
– подводят фрезу до касания с обрабатываемой поверхностью заготовки вращением рукояток продольной, поперечной и вертикальной подач;
– отводят заготовку от фрезы;
– вращением рукоятки вертикальной подачи перемещают стол с заготовкой на глубину резания немного меньшую, чем требуемая глубина резания t;
– фрезеруют поверхность заготовки ручным движением подачи на длину 3…5 мм;
– отводят заготовку, останавливают вращение фрезы и измеряют полученный размер;
– корректируют положение заготовки относительно фрезы перемещением стола в направлении установленной глубины резания на расстояние, равное разности между получившимся и требуемым размерами;
– включают механическую подачу стола и фрезеруют поверхность заготовки.
– отводят заготовку, останавливают вращение фрезы и измеряют полученный размер;
– корректируют п
|
|
Общие условия выбора системы дренажа: Система дренажа выбирается в зависимости от характера защищаемого...
Типы сооружений для обработки осадков: Септиками называются сооружения, в которых одновременно происходят осветление сточной жидкости...
Типы оградительных сооружений в морском порту: По расположению оградительных сооружений в плане различают волноломы, обе оконечности...
Кормораздатчик мобильный электрифицированный: схема и процесс работы устройства...
© cyberpedia.su 2017-2024 - Не является автором материалов. Исключительное право сохранено за автором текста.
Если вы не хотите, чтобы данный материал был у нас на сайте, перейдите по ссылке: Нарушение авторских прав. Мы поможем в написании вашей работы!