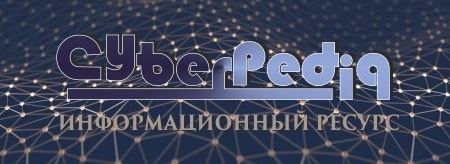
Наброски и зарисовки растений, плодов, цветов: Освоить конструктивное построение структуры дерева через зарисовки отдельных деревьев, группы деревьев...
Организация стока поверхностных вод: Наибольшее количество влаги на земном шаре испаряется с поверхности морей и океанов (88‰)...
Топ:
Эволюция кровеносной системы позвоночных животных: Биологическая эволюция – необратимый процесс исторического развития живой природы...
Установка замедленного коксования: Чем выше температура и ниже давление, тем место разрыва углеродной цепи всё больше смещается к её концу и значительно возрастает...
История развития методов оптимизации: теорема Куна-Таккера, метод Лагранжа, роль выпуклости в оптимизации...
Интересное:
Уполаживание и террасирование склонов: Если глубина оврага более 5 м необходимо устройство берм. Варианты использования оврагов для градостроительных целей...
Инженерная защита территорий, зданий и сооружений от опасных геологических процессов: Изучение оползневых явлений, оценка устойчивости склонов и проектирование противооползневых сооружений — актуальнейшие задачи, стоящие перед отечественными...
Искусственное повышение поверхности территории: Варианты искусственного повышения поверхности территории необходимо выбирать на основе анализа следующих характеристик защищаемой территории...
Дисциплины:
![]() |
![]() |
5.00
из
|
Заказать работу |
|
|
Порядок выполнения работы
Работая в лаборатории, будьте осторожны, не повредите себе руки, не роняйте детали на ноги себе и товарищам! Не засоряйте лабораторные объекты! После изучения приведите лабораторный объект в первоначальное состояние и положите его на прежнее место. Инструменты в конце занятий сдайте преподавателю.
В конструкциях редукторов в очень большой степени реализованы машиностроительные элементы, которые изучаются в дисциплине "Детали машин". По этой дисциплине вам предстоит выполнить курсовой проект (курсовую работу), где вы должны будете от начала и до конца рассчитать и сконструировать редуктор. Поэтому выполнение настоящей лабораторной работы и последующих работ позволит вам осознанно воспринять теоретическую часть курса и успешно справиться с курсовым проектом.
Настоящая работа носит ознакомительный характер и предусматривает изучение всех редукторов, имеющихся в лаборатории, в том плане, как это даётся в описании работы.
Описание довольно объёмистое, поэтому в первом чтении его следует прорабатывать вне аудитории. Начинать чтение следует с раздела "Введение" к настоящему сборнику лабораторных работ, где содержатся основополагающие положения и зависимости, без которых трудно воспринять последующий материал.
Рекомендуется читать описание по отдельным пунктам, а затем смотреть редукторы именно в связи с прочитанным. Например, вы прочитали и осмыслили пункт "Общие сведения о редукторах". Затем посмотрите, какие из упомянутых в описании редукторов имеются в лаборатории, научитесь их безошибочно узнавать и отличать друг от друга. Затем читайте следующий пункт и смотрите, как прочитанное реализовано в металле и т.д. Старайтесь запоминать названия деталей, конструктивных решений, схем и т.д., встречающихся в тексте. Всё это составляет язык изучаемой дисциплины, без которого невозможно её успешное освоение.
|
После проработки описанным способом всех материалов, должно состояться собеседование с преподавателем. При положительном исходе собеседования вы получите редуктор для углублённого изучения и написания отчёта в соответствии с разделом 7 настоящего сборника.
Работа будет считаться зачтённой, если вы защитили отчёт, подготовили ответы на контрольные вопросы и имеете достаточное представление обо всех редукторах в лаборатории.
1.2Общие сведения о редукторах
1.2.1 Редуктором называется агрегат, который содержит установленную в закрытом корпусе передачу (или передачи) зацеплением с постоянным передаточным отношением и который предназначен для понижения угловой скорости, а следовательно, повышения крутящего момента.
Такой же агрегат, но предназначенный для повышения угловой скорости, называется мультипликатором. По конструкции мультипликаторы принципиально не отличаются от редукторов. Их особенности обусловлены в основном высокими частотами вращения выходных звеньев. Мультипликаторы используются реже, чем редукторы.
Установка передачи в жестком закрытом корпусе обеспечивает высокую точность и стабильность расположения элементов передачи, лучшую смазку, меньший износ, защиту от попадания загрязнений. Поэтому в большинстве случаев применяют закрытые передачи – редукторы и мультипликаторы – вместо открытых передач. Открытые передачи используют при ручном приводе, а также при механическом приводе в тихоходных и громоздких машинах (подъемные краны, экскаваторы и т.п.).
В редукторах применяют, как правило, зубчатые или червячные передачи и их комбинации, изредка применяются и цепные передачи.
1.2.2 Схемы исполнения редукторов весьма разнообразны /3, с.129/. Для удобства изучения разделим редукторы на следующие группы:
|
– редукторы с цилиндрическими зубчатыми колесами – цилиндрические (одно-, двух- и трехступенчатые);
– редукторы с коническими зубчатыми колесами – конические;
– редукторы с червячной передачей – червячные;
– редукторы комбинированные (коническо-цилиндрические, цилиндро-червячные и т.п.);
– редукторы планетарные;
– мотор-редукторы с редукторами, перечисленными выше.
Промышленность выпускает ряд семейств стандартных редукторов общего назначения (цилиндрические одноступенчатые, цилиндрические двухступенчатые, коническо-цилиндрические, червячные и др.).
Весьма многочисленны также редукторы специального назначения, которые проектируются как составная часть вполне определенной машины (автомобиля, судна и т.п.).
1.2.3 Цилиндрические редукторы с прямозубыми и косозубыми цилиндрическими колесами получили наибольшее распространение.
Одноступенчатые цилиндрические редукторы (см. рисунок 1.1а) проектируют на передаточные числа до 10, но чаще – до 6,3.
Примечание – На рисунках редукторы представлены в виде их кинематических схем. Научиться читать эти схемы вам поможет приложение Б.
В одноступенчатых редукторах преобладают колеса косозубые. Для передачи больших мощностей (сотни киловатт) их выполняют иногда шевронными.
Основное распространение получили двухступенчатые цилиндрические редукторы с передаточными отношениями от 3 до 50. Их выполняют чаще всего по развернутой схеме (рисунок 1.1б). Она обеспечивает простоту конструкции, но свойственное ей несимметричное расположение колес на валах приводит из-за деформации валов к перекосу этих колес и, как следствие, к неравномерному распределению нагрузки по длине зубьев (к концентрации нагрузки). Это обстоятельство вынуждает ограничивать ширину колес и повышать жесткость валов.
Схема с раздвоенной быстроходной ступенью (рисунок 1.1в) позволяет улучшить условия работы наиболее нагруженной тихоходной ступени за счет симметричного расположения ее колес на валах. Для обеспечения равномерной нагрузки обеих зубчатых пар быстроходной ступени их, во-первых, делают косозубыми с одинаковым по величине, но противоположно направленным наклоном зубьев, то есть придают им свойства шевронной пары, а, во-вторых, один из валов устанавливают на подшипниках, не препятствующих его осевому перемещению под воздействием осевых сил (вал с такой установкой на подшипниках называют "плавающим" в осевом направлении).
|
Соосная схема по рисунку 1.1г позволяет расположить быстроходный и тихоходный валы на одной оси. Недостатки редукторов этого типа – увеличенный габарит вдоль осей и несимметричное расположение колес на промежуточном валу.
Трехступенчатые цилиндрические редукторы выполняют на передаточные числа от 40 до 160 и более. Их проектируют по простейшей развернутой схеме или по более совершенной схеме с раздвоенной промежуточной ступенью (рисунки 1.1д,е). Эта схема обеспечивает весьма благоприятные условия для работы быстроходной и тихоходной ступеней, так как их зубчатые колеса располагаются симметрично относительно подшипников и зубья колес нагружаются по длине равномерно.
Схемы редукторов:
а – одноступенчатого;
б – двухступенчатого, выполненного по развернутой схеме;
в – двухступенчатого с раздвоенной быстроходной ступенью;
г – двухступенчатого соосного;
д – трехступенчатого, выполненного по развернутой схеме;
е – трехступенчатого с раздвоенной промежуточной ступенью;
Буквами Б и Т на схемах обозначены соответственно быстроходный и тихоходный валы.
1 – опора (подшипник); 2 – колесо зубчатое цилиндрическое; 3 – вал; 4 – корпус.
Рисунок 1.1 – Схемы наиболее распространенных цилиндрических редукторов
1.2.4 Конические редукторы применяют тогда, когда оси входного и выходного валов должны быть расположены под углом друг кдругу. Этот угол составляет чаще всего 90°.
Редукторы с одной только конической парой по рисунку 1.2а выполняют на передаточные отношения до 6.
Для увеличения передаточных отношений применяют комбинированные коническо-цилиндрические редукторы (рисунки 1.2б,в). Они выполняются обычно двух- и трехступенчатыми на передаточные отношения соответственно от 6 до 30 и от 30 до 180. Конической в этих редукторах делают всегда наименее нагруженную быстроходную пару, поскольку изготовление конических колес больших размеров затруднительно.
|
1.2.5 Червячные редукторы при передаточных отношениях от 8 до 80 выполняют одноступенчатыми (рисунок 1.2г). При больших передаточных отношениях – двухступенчатыми (рисунок 1.2д). Одноступенчатые редукторы выполняются с нижним, верхним и боковым расположением червяка.
КПД червячной передачи обычно уменьшается с увеличением передаточного отношения. Поэтому для получения достаточно больших передаточных отношений и повышения КПД используют комбинированные редукторы, содержащие червячную и зубчатую цилиндрическую передачи (рисунок 1.2е). Червячные передачи применяются чаще в качестве быстроходной ступени, так как с повышением скорости улучшается режим смазки и повышается КПД червячной передачи.
1.2.6 Планетарные редукторы отличаются тем, что оси некоторых их колес (сателлитов) подвижны. По сравнению с обычными зубчатыми планетарные редукторы имеют, как правило, меньшие габариты и вес при одинаковых передаточных отношениях и передаваемых моментах. Это преимущество достигается за счет:
– использования внутреннего зацепления;
– передачи нагрузки параллельно несколькими сателлитами;
– меньшего влияния деформаций деталей на распределение нагрузки по ширине колес;
– широкого применения высококачественных материалов и их термохимического упрочнения, что более доступно для зубчатых колес относительно малых размеров.
Схемы планетарных редукторов довольно многочисленны. Простейший редуктор по схеме рисунка 1.3а позволяет получить передаточное отношение до 8 при КПД 0,97...0,98.
При том же значении КПД редуктор по схеме рисунка 1.3б может иметь передаточное отношение до 16. Для получения больших передаточных отношений проектируют редукторы, составленные
Схемы редукторов:
а – конического одноступенчатого;
б – коническо- цилиндрического двухступенчатого;
в – коническо- цилиндрического трехступенчатого;
г – червячного одноступенчатого;
д – червячного двухступенчатого;
е – червячно-цилиндрического двухступенчатого.
Буквами Б и Т на схемах обозначены соответственно быстроходный и тихоходный валы.
1 – колесо коническое; 2 – опора (подшипник); 3 – вал; 4 – корпус; 5 – колесо червячное; 6 – вал червяка.
Рисунок 1.2 – Иллюстрация схем различных редукторов
Схемы простейших планетарных редукторов:
а – одноступенчатого; б – с двухрядным сателлитом.
1 – солнечное колесо; 2 – сателлиты, оси которых подвижны; 3 – корончатое колесо (неподвижное); 4 – корпус; 5 – водило.
Буквами Б и Т на схемах обозначены соответственно быстроходный и тихоходный валы.
Рисунок 1.3 – Иллюстрации планетарных редукторов
|
Схемы мотор-редукторов:
а – с двухступенчатой соосной зубчатой передачей;
б – с одноступенчатой планетарной передачей.
Буквами Т и ЭД на схемах обозначены соответственно тихоходный вал и электродвигатель.
Рисунок 1.4 – Иллюстрации мотор-редукторов
из двух последовательно расположенных передач, показанных на упомянутых рисунках, а также и по другим схемам. Планетарные редукторы широко применяют на транспортных и грузоподъемных машинах, в авиации, на судах и т.д. В редукторах используют как прямозубые, так и косозубые цилиндрические колеса.
1.2.7 Мотор-редуктором называют агрегат, состоящий из зубчатого редуктора и электродвигателя, корпуса которых жестко соединяются между собой (рисунок 1.4). В мотор-редукторах применяются обычно цилиндрические одно- и двухступенчатые, а также планетарные редукторы или их комбинации. Электродвигатели используют асинхронные специального исполнения или же серийные фланцевые.
Достоинство мотор-редуктора состоит в том, что его масса и габариты значительно меньше, чем у аналогичной по техническим данным установки, составленной из двигателя, редуктора и соединяющей их муфты. Для уменьшения габаритов основные детали редуктора изготавливают из высококачественных материалов и подвергают их упрочняющей термохимической обработке.
Промышленность серийно выпускает несколько семейств мотор-редукторов общего назначения /4, т.3, с. 506...516/.
Основные детали редукторов
1.3.1 На рисунке 1.5. изображены детали классического одно-ступенчатого цилиндрического редуктора. С ними сходны по конструкции детали других редукторов, с которыми вам предстоит ознакомиться.
1.3.2 Корпус – наиболее массивная и дорогая часть редуктора. Он служит для размещения деталей передачи, их точной взаимной координации, защиты от загрязнения и организации смазки трущихся поверхностей.
Корпус воспринимает усилия, возникающие в зацеплении, и др. Он должен быть не только прочным, но и жестким, чтобы его собственные деформации были минимальны и не влияли ощутимо на правильность зацепления зубьев передач. Жесткость – основной критерий работоспособности корпуса. При достаточной жесткости прочность обеспечивается обычно с многократным запасом.
Корпус представляет собой коробку, стенки которой ограничиваются как плоскими, так и изогнутыми поверхностями. Ввиду сложности формы, корпус чаще выполняют литым, реже его сваривают из
малоуглеродистой стали. Преобладающим материалом отливок служит серый чугун. Стальное литье применяют редко – лишь в случаях воздействия больших нагрузок ударного характера. Для облегчения конструкций используют литье из алюминиевых и магниевых сплавов.
1 – крышка подшипника глухая; 2 – подшипник качения; 3 – основание корпуса; 4 – колесо зубчатое; 5 – вал тихоходный; 6,7,8 – крепеж (болт, шайба пружинная, гайка), соединяющий части корпуса; 9 – крышка корпуса; 10 – прокладка; 11 – крышка смотрового отверстия; 12 – рым-болт; 13 – штифт; 14 – крышка подшипника проходная; 15 – вал-шестерня; 16 – маслоуказатель жезловый; 17 – пробка сливная; 18 – шайба маслоотражательная; 19 – прокладка крышки подшипника.
Рисунок 1.5 – Детали одноступенчатого цилиндрического редуктора
Корпус редуктора может выполняться неразъёмным в виде одной детали и разъёмным, состоящим из нескольких деталей (рисунок 1.6).
Неразъёмный корпус обычно проще конструктивно и легче. Но его использование затрудняет сборку редуктора и для обеспечения сборки порой приводит к усложнению конструкции других элементов редуктора. Неразъёмные корпуса характерны для редукторов специального назначения, от которых требуется компактность и малая масса (транспортные машины, авиация и т.п.). Иногда их используют для конических и червячных редукторов общего назначения.
Разъёмный корпус позволяет облегчить сборку и упростить конструкцию некоторых деталей. К его недостаткам (по сравнению с неразъемным корпусом) относятся: большая масса, большие габариты, повышенная трудоёмкость обработки. Он состоит, как минимум, из двух частей – основания и крышки (см. рисунок 1.6) иногда этих частей бывает и больше.
Плоскость разъема частей корпуса проходит, как правило, через оси валов. Она обычно параллельна опорной поверхности основания корпуса. Косой разъём менее технологичен, его выполняют иногда (см. рисунок 1.6) при большой разнице диаметров колёс у разных ступеней для более оптимального погружения колес в масло.
В плоскости разъема части корпуса стыкуются элементами, называемыми фланцами. Фланцы соединяются между собой резьбовыми крепежными деталями.
С плоскостью разъема корпуса совпадают оси отверстий (гнезд) под подшипники. Отверстия эти обрабатываются в специальных приливах корпусных деталей (приливы, особенно мелкие, называют еще бобышками).
Очень важно уяснить, что отверстия под подшипники и наружные поверхности приливов, в которых располагаются эти отверстия, обрабатываются у обеих частей корпуса одновременно после их предварительной сборки. Для выполнения этой сборки сначала начисто обрабатывают следующие элементы корпуса (см. рисунок 1.6):
– опорную поверхность основания;
– плоскости разъема основания и крышки;
– отверстия под крепеж, соединяющий основание и крышку.
Затем части корпуса соединяют резьбовым крепежом и во фланцах (сразу в обоих) сверлят и развертывают два (иногда более) отверстия под штифты (см. рисунок 1.5 поз.13). После установки штифтов предварительная сборка считается законченной, и корпус направляется на обработку отверстий под подшипники. Роль штифтов весьма важна: они, в отличие от резьбовых деталей, ставятся в отверстия
1 – основание; 2 – крышка; 3 – фланцы для соединения частей корпуса; 4 – приливы для отверстий под подшипники; 5 – отверстие под крепеж; 6- отверстия для винтов крепления крышек подшипников; 7 – прилив (лапа) с отверстиями для установки и крепления к фундаменту; 8 – прилив с отверстием для сливной пробки; 9 – прилив с отверстием для маслоуказателя; 10 – приливы для рым-болтов; 11 – прилив для смотрового отверстия; 12 – ребра жесткости.
Рисунок 1.6 – Разъёмный корпус цилиндрического редуктора (вверху справа вариант корпуса с косым разъёмом)
без зазора и за счет этого точно фиксируют взаимное положение частей корпуса (основания и крышки) как при их совместной обработке, так и при всех последующих сборках редуктора.
Стык по плоскости разъема корпуса герметизируют уплотнительной пастой, которая наносится на поверхности разъема при окончательной сборке редуктора. После затяжки крепежа лишняя паста выдавливается, а оставшаяся образует герметизирующий слой, практически не имеющий толщины и не искажающий поэтому круглую форму отверстий под подшипники.
Примечания
1 Уплотнительные пасты именуют еще "Герметиками". Они имеют разный состав и представляют собой вязкие жидкости. После нанесения одни пасты полностью высыхают и затвердевают, другие сохраняют эластичность. Широко применяется паста марки УН-25 по ТУ 6-10-1284-77.
2 Указание о герметизации стыка между частями корпуса дается пунктом технических требований на чертеже редуктора. Пункт имеет такое, примерно, содержание: "Поверхности разъема основания поз.2 и крышки поз.3 смазать перед окончательной сборкой пастой уплотнительной УН-25, ТУ 6-10-1284-77".
В нижней части (основании) корпуса (см. рисунок 1.6) предусматриваются лапы с отверстиями для установки и крепления корпуса к раме; отверстие для сливной пробки и отверстие для устройства, которым контролируется уровень масла.
В верхней части (крышке) корпус имеет обычно смотровое отверстие, приливы с отверстиями для рым-болтов или же приливы для непосредственной застропки при подъёме краном.
1.3.3 Зубчатые колёса, образующие пару, называются: большее – колесом, меньшее – шестерней. Термин "зубчатое колесо" является общим.
Колесо может быть выполнено как самостоятельная деталь, так и за одно целое с валом (вал-шестерня). Последний вариант используют тогда, когда диаметр колеса, примерно, не более чем вдвое превышает диаметр вала.
Основным материалом цилиндрических и конических зубчатых колёс является сталь различных марок. Реже применяют серый чугун или пластмассы.
Конструкция зубчатого колеса зависит от его размера и технологии изготовления (рисунок 1.7). У колеса различают три основных элемента: зубчатый венец (обод), ступицу и диск. Из рисунка 1.7 видно, что эти элементы разграничиваются не всегда четко.
В редукторах преобладают колёса с диаметрами до 600 мм. Их изготавливают из круглого проката (при малых диаметрах), а чаще из кованых и штампованных заготовок. Колёса больших размеров выполняют литыми, сварными или же собранными из отдельных частей.
Червячные колёса в целях экономии выполняют составными: венец из бронзы, ступица и диск (центр) из чугуна или стали (рисунок 1.8). Мелкие червячные колёса (с диаметром до 100...120 мм) выполняют целиком из бронзы, цельными выполняют также и чугунные колёса всех размеров.
Червяки выполняют, как правило, за одно целое с валом (рисунок 1.9). Рабочие поверхности червяков подвергаются термоупрочнению (поверхностная закалка, цементация) и шлифуются.
Зубчатые колеса в большинстве случаев неподвижно устанавливаются на валах с небольшим зазором или натягом. Для передачи крутящего момента используется шпоночное или реже – шлицевое соединение. В отдельных случаях натяг увеличивают, и тогда крутящий момент может передаваться за счет трения между ступицей колеса и валом. Подвижные в осевом направлении колеса (в коробках передач) устанавливаются на валах с зазором. Крутящий момент в этом случае передается чаще всего шлицевым соединением, реже – шпоночным.
1.3.4 Валы несут на себе зубчатые колёса и другие детали передач, обеспечивают их правильное взаимное положение, воспринимают и передают усилия в передачах.
Диаметральные размеры валов определяются в конечном итоге не столько их прочностью при изгибе и кручении, сколько конструктивными соображениями и жесткостью.
Для валов, подчиненных критерию жесткости, применяют, как правило, углеродистые и малолегированные стали с содержанием углерода 0,35…0,50%. Валы из этих сталей обычно нормализуют или улучшают, шлицевые участки, а также поверхности, взаимодействующие с уплотнениями и подшипниками скольжения, подвергают поверхностной закалке. Валы, на которых нарезаны зубья зубчатых колес (вал-шестерня) выполняют из тех сталей, которые назначены для зубчатых колес. Термообработка при этом зачастую определяется требованиями к зубчатому колесу (цементация, азотирование).
Для передачи моментов от деталей, насаженных на валы, к самим валам в редукторах чаще применяют шпоночные соединения, реже - шлицевые и соединения с натягом.
Концы валов, выходящие наружу из редуктора, проектируются в расчете на установку на них шкивов, звездочек, муфт и т.п. Эти концы выполняются цилиндрическими или реже коническими со шпоночным пазом, а иногда - шлицевыми.
Они снабжаются зачастую резьбовым хвостовиком или осевыми резьбовыми отверстиями. То и другое предназначено для осевой фиксации деталей, насаживаемых на конец вала. В более редких случаях вал (обычно тихоходный) может заканчиваться зубчатым венцом, служащим частью зубчатой муфты, или фланцем с осевыми отверстиями, расположенными по окружности.
Представление о назначении отдельных элементов валов дают рисунки 1.13 - 1.16.
а, б, в, г – колёса малого диаметра (до 200 мм); д, е, ж, з – колёса среднего диаметра (200…600 мм), изготовленные из поковок и штамповок;
1 – зубчатый венец (обод); 2 – диск; 3 – ступица.
Рисунок 1.7 – Характерные конструкции зубчатых колёс
Продолжение рисунка на следующей странице.
и – передвижная шестерня; к – блок шестерён коробки скоростей;
л – вал-шестерня цилиндрическая; м – вал-шестерня относительно малого диаметра; н – вал-шестерня коническая; R – радиус перехода, соответствующий радиусу фрезы, которой нарезались зубья.
Рисунок 1.7 – Характерные конструкции зубчатых колёс (продолжение рисунка)
1 – венец посажен на центр с натягом и дополнительно зафиксирован стопорными винтами;
2 – венец соединён с центром болтами;
3 – венец отлит в форме, куда предварительно установлен центр, имеющий впадины для более надёжного соединения с венцом.
Рисунок 1.8 – Характерные конструкции червячных колёс, состоящих из бронзового венца и чугунного или стального центра
Конструкции червяков:
1 – цилиндрического;
2 – цилиндрического с относительно малым диаметром;
3 – глобоидного.
Рисунок 1.9 – Характерные конструкции червяков
1.3.5 Подшипники поддерживают вращающиеся валы и другие детали, воспринимают от них нагрузки и передают эти нагрузки корпусу.
В редукторах преобладают подшипники качения. Подшипники скольжения применяют иногда в крупных редукторах, а также при особо высоких частотах вращения. Они весьма требовательны к непрерывной подаче смазки, поэтому для смазывания подшипников скольжения требуется, как правило, циркуляционная система смазки со специальным насосом, фильтром и др. устройствами.
Подшипники качения менее требовательны к организации смазки и отличаются зачастую меньшими потерями на трение. Эти и некоторые другие достоинства обеспечили им широкое распространение в машиностроении.
Подшипник качения в общем случае состоит из следующих частей (рисунок 1.10):
– наружного и внутреннего колец, на которых имеются полированные дорожки качения;
– тел качения (шариков или роликов);
– сепаратора, разделяющего и направляющего тела качения.
В подшипниках некоторых типов могут отсутствовать сепаратор, а также одно или оба кольца. Функции отсутствующих колец выполняют при этом другие детали (вал, корпус и т.д.).
По форме тел качения подшипники делятся на шариковые и роликовые (с роликами цилиндрическими, коническими, бочкообразными, игольчатыми и витыми).
По способности воспринимать нагрузки осевого и радиального направлений подшипники делят на четыре следующие группы;
– подшипники радиальные (воспринимают в основном или только радиальную нагрузку);
– подшипники радиально-упорные (воспринимают радиальную и осевую нагрузки приблизительно в равной степени);
– подшипники упорно-радиальные (по сравнению с предыдущими в большей степени воспринимают осевую нагрузку за счет радиальной). Упорно-радиальные подшипники не всегда выделяют в отдельную группу и зачастую рассматривают их как радиально-упорные;
– упорные подшипники (воспринимают в основном или только осевую нагрузку).
Наиболее распространенные типы подшипников качения охарактеризованы в приведенной ниже таблице 1.1.
Большинство подшипников качения относится к изделиям стандартным. Годовой выпуск подшипников в России близок к миллиарду, а количество типоразмеров значительно превышает тысячу.
Предусмотрено пять классов точности подшипников (в порядке повышения точности): 0, 6, 5, 4, 2. Подшипники повышенной точности более дороги, но они отличаются повышенной долговечностью и меньшим шумом при работе.
На каждом подшипнике качения ставится клеймо – его условное обозначение. Расшифровка смысла этого обозначения приводится в специальной литературе, например /8/.
Для понимания последующего материала важно уяснить свойства зазоров у разных типов подшипников.
У радиальных шарикоподшипников (рисунок 1.10) радиальный и осевой зазоры для данного подшипника постоянны. Поэтому эти и подобные им по свойствам радиальные роликоподшипники с цилиндрическими роликами и радиальные сферические двухрядные шарико - и роликоподшипники называют нерегулируемыми. Заметим, что осевой зазор называют еще осевой игрой подшипника.
У радиально-упорных роликовых и шариковых подшипников (рисунок 1.11) радиальный и осевой зазоры зависят от взаимного положения наружного и внутреннего колец и могут регулироваться сразу оба за счет перемещения одного кольца относительно другого. Подшипники эти называются регулируемыми. Операция регулировки выполняется после монтажа подшипников на свое место в подшипниковом узле.
Кольца подшипника в подшипниковом узле могут монтироваться неподвижно, т.е. с некоторым натягом, или подвижно - с зазором. С натягом обычно монтируется вращающееся кольцо (чаще оно внутреннее), а с зазором - неподвижное (чаще оно наружное). Бывают, однако, и отступления от этого правила.
Итак, еще раз обращаем ваше внимание, что из числа подшипников, охарактеризованных в таблице 1.1, к регулируемым относятся радиально-упорные шариковые и роликовые с коническими роликами. Остальные – нерегулируемые.
Рисунок 1.10 – Иллюстрация зазоров в нерегулируемых подшипниках
Таблица 1.1 – Наиболее распространенные типы подшипников качания
№ п/п | Эскиз | Краткая характеристика |
![]() | Радиальные шарикоподшипники способны воспринимать радиальные и значительно меньшие двухсторонние осевые нагрузки. Для этих подшипников перекос наружных колец относительно внутренних, вызванный несоосностью гнёзд в корпусе и прогибом вала, не должен превышать 10…15 угловых минут. Подшипники принадлежат к наиболее распространённому, дешевому и быстроходному типу. | |
![]() | Радиальные роликоподшипники с короткими цилиндрическими роликами способны воспринимать значительно большие радиальные нагрузки, чем равногабаритные радиальные шарикоподшипники, но уступают им по быстроходности и стоят несколько дороже. Подшипники без буртов на одном из колец (эскиз а) осевые нагрузки не воспринимают совсем; подшипники с буртами на обоих кольцах (эскиз б) могут воспринимать весьма незначительные осевые нагрузки. Подшипники эти очень чувствительны к взаимному перекосу колец. | |
![]() | Двухрядные радиальные сферические шарико- и роликоподшипники (соответственно эскизы в, г) воспринимают радиальные и небольшие двухсторонние осевые нагрузки. Они способны нормально работать при весьма больших взаимных перекосах колес, достигающих 1…2° (эскиз Д). Это свойство обеспечивается тем, что дорожка качения наружного кольца обработана по сфере, центр которой лежит на оси подшипника. Сферические подшипники применяют при невозможности достаточно соосно обработать гнёзда в корпусе или при расположении гнезд в разных корпусах, а также при установке подшипников на недостаточно жестких валах. Роликовые сферические подшипники (ролики бочкообразные) при одинаковых габаритах имеют большую грузоподъемность и меньшую допускаемую частоту вращения, чем шариковые. Сферические подшипники называют также самоустанавливающимися. |
Таблица 1.1 – Продолжение
№ п/п | Эскиз | Краткая характеристика |
![]() | Радиально-упорные конические роликоподшипники способны воспринимать совместно действующие радиальные и односторонние осевые нагрузки. С увеличением угла контакта ![]() | |
![]() | Радиально-упорные шарикоподшип-ники способны воспринимать совместно действующие радиальные и только односторонние осевые нагрузки. С увеличением угла контакта ![]() | |
![]() | Упорно-радиальные роликоподшипники сферические способны воспринимать одностороннюю осевую нагрузку и значительно меньшую радиальную. Дорожка качения наружного кольца обрабатывается по сфере. Такая форма допускает значительный перекос осей колец без нарушения работоспособности подшипника. Ролики бочкообразные. |
Таблица 1.1 – Окончание
№ п/п | Эскиз | Краткая характеристика |
![]() | Упорные шарикоподшипники предназначены для восприятия осевых нагрузок. Они очень чувствительны к перекосу осей колец и применяются обычно совместно с подшипниками других типов, которые воспринимают радиальные нагрузки и центрируют ось вала. |
r – радиальный зазор; a – осевой зазор (осевая игра); – угол контакта.
Обратите внимание на то, что зазоры, связанные зависимостью r =2·atg , могут меняться только оба одновременно.
Рисунок 1.11 – Иллюстрация зависимости зазоров в регулируемых подшипниках от взаимного положения колец
1.3.6 Подшипниковый узел содержит (см. рисунки 1.5 и 1.6):
– подшипник (или подшипники) качения;
– сопряжённые с кольцами подшипника вал и отверстие в подшипниковом гнезде корпуса передачи;
– крышку, уплотнения, регулировочные детали и пр.
Среди валов преобладают двухопорные, опирающиеся на два подшипника, реже встречаются валы трёхопорные и многоопорные. Вал, опирающийся на подшипники, имеет две степени свободы, т.е. он может вращаться и перемещаться вдоль своей оси.
Для правильного взаимодействия деталей, закреплённых на валах, например зубчатых колёс, осевое перемещение валов в большинстве конструкций должно быть ограничено. Иными словами, валы должны быть зафиксированы в осевом направлении с большей или меньшей возможностью (или даже с невозможностью) осевого перемещения. Это перемещение называют осевой игрой или реже – осевым люфтом вала.
Валы по типу осевой фиксации делятся на следующие три группы, иллюстрированные рисунком 1.12:
– группа первая – валы, фиксированные в двух опорах;
– группа вторая – валы, фиксированные в одной опоре. Другая опора плавающая;
– группа третья – валы, нефиксированные в осевом направлении или плавающие.
1.3.6.1 Валы первой группы, зафиксированные в двух опорах, иллюстрированы рисунками 1.13 и 1.14. На рисунке 1.13 а представлена весьма простая и распространённая конструкция, выполненная на радиальных шарикоподшипниках. Она применяется главным образом в цилиндрических передачах с прямозубыми и косозубыми колёсами при небольших (до 150) углах наклона зубьев β, где осевые нагрузки невелики по сравнению с радиальными.
Наружные кольца подшипников монтируются в корпусе с некоторым радиальным зазором, поэтому вал вместе с подшипниками может сдвигаться осевой силой до упора внешнего кольца того или другого подшипника в соответствующую крышку. При этом через крышку подшипников в корпус упираются и ограничивают перемещение вала внешние торцы наружных колец подшипников. Обратите внимание на эту особенность. Именно она является признаком установки подшипников враспор. Научитесь отличать уст
|
|
Кормораздатчик мобильный электрифицированный: схема и процесс работы устройства...
Поперечные профили набережных и береговой полосы: На городских территориях берегоукрепление проектируют с учетом технических и экономических требований, но особое значение придают эстетическим...
Типы сооружений для обработки осадков: Септиками называются сооружения, в которых одновременно происходят осветление сточной жидкости...
Индивидуальные и групповые автопоилки: для животных. Схемы и конструкции...
© cyberpedia.su 2017-2024 - Не является автором материалов. Исключительное право сохранено за автором текста.
Если вы не хотите, чтобы данный материал был у нас на сайте, перейдите по ссылке: Нарушение авторских прав. Мы поможем в написании вашей работы!