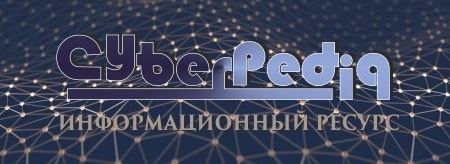
Двойное оплодотворение у цветковых растений: Оплодотворение - это процесс слияния мужской и женской половых клеток с образованием зиготы...
Опора деревянной одностоечной и способы укрепление угловых опор: Опоры ВЛ - конструкции, предназначенные для поддерживания проводов на необходимой высоте над землей, водой...
Топ:
Отражение на счетах бухгалтерского учета процесса приобретения: Процесс заготовления представляет систему экономических событий, включающих приобретение организацией у поставщиков сырья...
Характеристика АТП и сварочно-жестяницкого участка: Транспорт в настоящее время является одной из важнейших отраслей народного...
Методика измерений сопротивления растеканию тока анодного заземления: Анодный заземлитель (анод) – проводник, погруженный в электролитическую среду (грунт, раствор электролита) и подключенный к положительному...
Интересное:
Отражение на счетах бухгалтерского учета процесса приобретения: Процесс заготовления представляет систему экономических событий, включающих приобретение организацией у поставщиков сырья...
Аура как энергетическое поле: многослойную ауру человека можно представить себе подобным...
Инженерная защита территорий, зданий и сооружений от опасных геологических процессов: Изучение оползневых явлений, оценка устойчивости склонов и проектирование противооползневых сооружений — актуальнейшие задачи, стоящие перед отечественными...
Дисциплины:
![]() |
![]() |
5.00
из
|
Заказать работу |
Содержание книги
Поиск на нашем сайте
|
|
Принципиальная структура сортовых хлебопекарных помолов пшеницы с ее дальнейшей витаминизацией состоит из следующих этапов:
· драной процесс (первичное измельчение зерна в вальцовых станках) и сортирование продуктов измельчения в рассевах;
· ситовеечный процесс (процесс обогащения крупок и дунстов в ситовеечных машинах);
· шлифовочный процесс (шлифование крупок и дунстов на вальцовых станках);
· размольный процесс (измельчение обогащенных промежуточных продуктов);
· формирование сортов муки из отдельных компонентов (по специальному заданию) и их витаминизация;
Драной процесс
Для измельчения зерна используют вальцевые станки (рис.7), рабочими органами которых служат два чугунных вальца, вращающихся навстречу друг другу с разной скоростью. Поверхность вальцов делают рифленой, шероховатой, а иногда гладкой. Расстояние между рифлями, их форма и глубина зависят от места и роли вальцевого станка в технологическом процессе. Зерно, попадая в зазор между вальцами, дробится на частицы разной крупности.
Зерно, подготовленное к помолу, направляют в вальцовые станки I др. с. после взвешивания на автоматических весах. Электронная аппаратура позволяет устанавливать необходимую частоту взвешивания с точностью до ±1,0 с, что в сочетании с высокой технологической дисциплиной, соблюдением регламента подготовки зерна, надежной работой оборудования предопределяет стабильную величину нагрузки на отдельные системы всего технологического процесса в размольном отделении (рис. ХХVI-2).
Драной процесс включает четыре системы, при этом III и IV разделены на крупные и мелкие. На II др. с. поступает верхний сход первых шести сит рассева I др. с. II драную систему на крупную и мелкую не делят, что можно объяснить необходимостью стабилизации нагрузки на системы. В противном случае изменение влажности зерна, режима отволаживания, состояния рифлей существенно меняет фракционный состав верхнего схода I др. с. и, как следствие, массовое соотношение фракций, направляемых на II драную крупную и мелкую системы. Это вызывает необходимость изменения настройки станков, нагрузки на материалопроводыпневмоустановок.
На всех драных системах, за исключением IV др. с. м., рифли расположены «спинка по спинке», окружная скорость быстровращающегося вальца 6,0 м/с, соотношение окружных скоростей 2,5.Режимы измельчения и нагрузка на системы драного процесса приведены в таблицах ХХVI-3 и ХХVI-4.
|
Особенность построения драного процесса состоит в отборе муки со всех рассевов драных систем, за исключением II др. с., из-за большого количества образующихся крупок и дунстов, необходимости повышения четкости их сепарирования перед направлением на ситовеечные системы. Для более эффективного сортирования продуктов размола с учетом количества и качества фракций применяют большое число вариантов схем рассева, в каждой секции которого установлено 22 ситорамы. Окончательно выделяют муку с драных систем на сортировочных системах.
Особенность построения драного процесса заключается также в том, что все фракции крупки и дунстов, за исключением мелких дунстов, направляют в ситовеечные машины. Они обслуживают только драной процесс. В шлифовочном и размольном процессах их не используют.
Вымол сходовых продуктов драного процесса начинают с III др. с.
Для вымола применяют горизонтальные бичевые машины А1-БВГ (рис.8), обечайка которых изготовлена из металлического сита с перфорированными отверстиями Ø 1,25; 1,00 и 0,75 мм, в зависимости от вида обрабатываемого продукта.
Ситовеечный процесс
Ситовеечный процесс включает десять систем. Схема построения ситовеечного процесса имеет ряд отличий от применяемой на мукомольных заводах, оснащенных серийным отечественным оборудованием. Ситовеечные машины А1-БСО (рис.9), двухприемные, с трехъярусным расположением сит, схема обогащения крупки и дунстов последовательная, т. е. с каждой секции ситовеечной машины получают три сходовые и одну-две проходовые фракции с нижнего яруса сит.
|
На ситовеечные машины направляют только крупки и дунсты I, II и III др. с., за исключением мелких дунстов с сортировок этих драных систем. На каждую ситовеечную систему поступает, как правило, одна фракция продуктов какой-либо системы, что дает возможность оперативно контролировать ее работу. Продукты с ситовеечных машин (проходовые фракции) идут на первые размольные, проходы последних сит нижнего яруса — на шлифовочные системы, а сходовые фракции в зависимости от крупности и качества — на шлифовочные системы, III др. с. м. и 4-ю, 5, 7-ю р. с., выполняющие роль сходовых соответствующих групп размольных систем.
При расстановке сит в ситовеечных машинах соблюдают следующие принципы: каждое последующее сито должно быть на один номер реже предыдущего сита этого же яруса. При этом каждое сито нижерасположенного яруса должно быть на один номер гуще расположенного над ним сита. Рекомендуемые нормы нагрузок на ситовеечные машины приведены в таблице ХХVI-7.
Шлифовочный процесс
Построение, назначение и параметры шлифовочного процесса существенно отличаются от аналогичного этапа обогащения промежуточных продуктов размола, применяемого на мукомольных заводах, работающих по традиционной технологии. Это обусловлено тем, что вследствие высокой эффективности драного иситовеечного процессов образуется сравнительно небольшое количество промежуточных продуктов, требующих обогащения. Поэтому применяют сокращенный по протяженности шлифовочный процесс, включающий две системы с интенсивными режимами измельчения на второй системе.
На шлифовочные системы направляют продукты после обработки в ситовеечных машинах, в основном вторые (последние) проходы и схода нижнего яруса сит. Крупки и дунсты шлифовочных систем направляют на 3-ю и 4-ю р. с. Отличительная особенность заключается в том, что продукты измельчают на вальцах с шероховатой поверхностью, окружная скорость быстровращающегося вальца 5,4 м/с, соотношение окружных скоростей 1,25, уровень шероховатости Rа=2,2...2,4 мкм.
После вальцового станка А1-БЗН продукт поступает в машину ударно-истирающего действия — деташер А1-БДГ (рис.10), в котором происходит дополнительное измельчение частиц продукта, предразрушенных в вальцовом станке, а также разрушение агрегатированных частиц (табл. XXVI-8).
|
На 1-ю шл. с. направляют смесь из шести компонентов в количестве (по данным баланса помола) 6,81% от массы продукта, поступающем на I др. с. средневзвешенной зольностью 1,39%. Общее извлечение на 1-й шл. с. составляет 18...25%. При таком режиме зольность верхнегс схода 1-й шл. с., в котором сосредоточиваются оболочечные частицы и зародыш, в два раза выше, чем исходного продукта, и его направляет на сходовую систему, роль которой выполняет 4-я р. с.
В верхнем сходе рассева 1-й шл. с., а также в потоках продуктов, направляемых на вальцовый станок 4-й р. с., содержится большое количество зародыша, который в виде верхнего схода 4-й р. с. может быть выделен как отдельный вид продукта и использован в фармацевтической, пищевой, комбикормовой и других отраслях.
Второй сход 1-й шл. с. поступает на 2-ю шл. с., на которую идут схода третьего яруса ситовеечных машин. На них обогащают мелкую крупку и дунсты. Средневзвешенная зольность смеси продуктов, обрабатываемых на 2-й шл. с., в 1,5 раза ниже зольности продуктов на 1-й шл. с.
На вальцовом станке 2-й шл. с. принят интенсивный режим измельчения, т. е. извлечение муки составляет 45...55%, что в сочетании с деташером обеспечивает общее извлечение 60...70%. Вследствие высокой влажности продуктов (15,2...15,5%), направляемых в вальцовый станок, применения шероховатых вальцов идеташера получают муку с хорошими хлебопекарными достоинствами, которую используют для формирования первого компонента (мука высшего сорта).
Размольный процесс
Крупки и дунсты размалывают на 11...12 размольных системах. Рабочая поверхность вальцов шероховатая, за исключением вальцов на последней системе (установлены вальцы с рифленой поверхностью). Главная отличительная особенность размольного процесса состоит в применении двухстадийного измельчения крупки и дунстов почти на всех системах размольного процесса. После вальцового станка А1-БЗН продукт направляют для дополнительного измельчения в машину ударно-истирающего действия (энтолейтор РЗ-БЭР или деташер А1-БДГ), где происходит дополнительное измельчение с последующим сепарированием в рассеве. При двухстадийном измельчении снижаются удельная энергоемкость, повреждение крахмала, повышается срок службы рабочей поверхности вальцов, наблюдается явление стабилизации измельчения на каждой системе.
Высокая эффективность подготовки крупки и дунстов, обрабатываемых на размольных системах, и возможность интенсификации размола путем двухстадийного измельчения позволяет формировать потоки продуктов, направляемых в вальцовые станки, в основном с учетом зольности, а не крупности. Однако для более эффективного измельчения на 1-й р. с. продукты разделяют на две фракции по крупности и измельчают их на 1-й р. с. кр. и 1-й р. с. м.
Например, на 1-ю р. с. кр. направляют первые проходы нижнего яруса ситовеечных машин, на которых обогащают крупную и среднюю крупу, а на 1-ю р. с. м. поступают первые проходы этих машин. В них обогащают среднюю и мелкую крупу, а также дунсты. Рекомендуемые нагрузки и извлечение муки на отдельных системах приведены в таблице ХХVI-9.
|
Интенсивно измельчают крупки и дунсты на головных размольных системах. На них направляют продукты, содержащие незначительное количество оболочечных частиц. Поэтому после вальцовых станков 1-й, 2 и 3-й р. с. устанавливают энтолейторы РЗ-БЭР, которые более интенсивно воздействуют на продукт, чем деташеры А1-БДГ.
В результате применения энтолейтора муки извлекают в 1,3...1,5 раза больше. При этом зольность муки и другие показатели ее качества изменяются незначительно. Применение энтолейторов на других системах, на которые поступают потоки промежуточных продуктов размола, содержащие значительное количество оболочечных частиц, приводит к ухудшению качества муки по сравнению с использованием деташера. Поэтому на всех размольных системах после третьей применяют в качестве дополнительных измельчителейдеташеры А1-БДГ. Однако на последних размольных системах после обработки продукта в деташерах наблюдается существенное повышение зольности и величины удельной поверхности муки.
|
|
Состав сооружений: решетки и песколовки: Решетки – это первое устройство в схеме очистных сооружений. Они представляют...
Папиллярные узоры пальцев рук - маркер спортивных способностей: дерматоглифические признаки формируются на 3-5 месяце беременности, не изменяются в течение жизни...
Опора деревянной одностоечной и способы укрепление угловых опор: Опоры ВЛ - конструкции, предназначенные для поддерживания проводов на необходимой высоте над землей, водой...
Кормораздатчик мобильный электрифицированный: схема и процесс работы устройства...
© cyberpedia.su 2017-2024 - Не является автором материалов. Исключительное право сохранено за автором текста.
Если вы не хотите, чтобы данный материал был у нас на сайте, перейдите по ссылке: Нарушение авторских прав. Мы поможем в написании вашей работы!