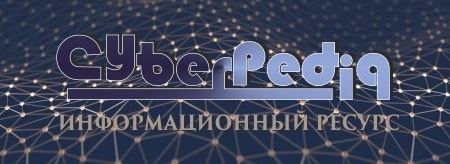
Опора деревянной одностоечной и способы укрепление угловых опор: Опоры ВЛ - конструкции, предназначенные для поддерживания проводов на необходимой высоте над землей, водой...
Типы сооружений для обработки осадков: Септиками называются сооружения, в которых одновременно происходят осветление сточной жидкости...
Топ:
Эволюция кровеносной системы позвоночных животных: Биологическая эволюция – необратимый процесс исторического развития живой природы...
Выпускная квалификационная работа: Основная часть ВКР, как правило, состоит из двух-трех глав, каждая из которых, в свою очередь...
Техника безопасности при работе на пароконвектомате: К обслуживанию пароконвектомата допускаются лица, прошедшие технический минимум по эксплуатации оборудования...
Интересное:
Уполаживание и террасирование склонов: Если глубина оврага более 5 м необходимо устройство берм. Варианты использования оврагов для градостроительных целей...
Подходы к решению темы фильма: Существует три основных типа исторического фильма, имеющих между собой много общего...
Национальное богатство страны и его составляющие: для оценки элементов национального богатства используются...
Дисциплины:
![]() |
![]() |
5.00
из
|
Заказать работу |
Содержание книги
Поиск на нашем сайте
|
|
Введение
Лабораторный практикум по дисциплине «Железнодорожный путь» является неотъемлемой частью учебного процесса при подготовке специалистов по специальности 23.05.06 Строительство железных дорог, мостов и транспортных тоннелей.
Целью выполнения лабораторных работ является формирование у обучающихся следующих компетенций:
ПК-21 способность ставить задачи исследования, выбирать методы экспериментальных работ, анализировать результаты научных исследований и делать окончательные выводы на их основе;
ПК-23 способность использовать для выполнения научных исследований современные средства измерительной и вычислительной техники.
Лабораторные работы составлены таким образом, что студент получает возможность изучить отдельные элементы верхнего строения пути: рельсы, шпалы, промежуточные и стыковые рельсовые скрепления, балластный слой, а также конструкцию стрелочных переводов, параметры рельсовой колеи и особенности работы бесстыкового пути.
Каждая работа имеет теоретическую и практическую части.
Во время выполнения работы на учебном полигоне или в лаборатории студенты производят измерение различных параметров отдельных элементов пути и конструкции в целом, разбирают и собирают отдельные элементы верхнего строения пути и производят анализ элементов. Самостоятельно студенты осуществляют теоретическую подготовку к лабораторным работам, а также применяют результаты измерений при формировании отчетов.
Правила оформления отчетов по лабораторным работам
По каждой лабораторной работе выполняется один отчет на всю бригаду по следующим правилам:
– отчет выполняется на листах формата А4;
|
– при оформлении отчета используется шрифт Times New Roman 14, межстрочный интервал – 1,15, текст выравнивается по ширине с отступом первой строки 10 мм;
– все рисунки, графики, чертежи, фотографии должны быть подписаны, при этом указывается номер рисунка и его название;
– рисунки подписываются шрифтом Times New Roman 12;
– все таблицы, приведенные в отчете, должны быть подписаны, при этом указывается номер и название таблицы;
– содержание отчета указано ниже для каждой лабораторной работы;
– графики, необходимые для отчета по лабораторной работе, могут быть выполнены на миллиметровой бумаге либо в электронном виде с использованием систем автоматизированного проектирования.
Правила техники безопасности при выполнении лабораторных работ
Лабораторные работы по дисциплине «Железнодорожный путь» выполняются на учебном полигоне СамГУПС, в ангаре учебного полигона и в лаборатории «Железнодорожный путь». При выполнении работ, необходимо строго соблюдать следующие правила техники безопасности.
1. Переходить пути следует под прямым углом, перешагивая через рельс, не наступая на рельс и на концы железобетонных шпал и масляные пятна на шпалах;
2. При нахождении на железнодорожных путях полигона запрещается:
– становиться или садиться на рельсы, концы шпал, балластную призму, электроприводы, путевые коробки и другие напольные устройства;
– наступать на концы железобетонных шпал;
– подниматься в вагон, дрезину, мотовоз, автомотрису и другие подвижные единицы, находящиеся на полигоне;
– ставить ногу между рамным рельсом и остряком стрелочных переводов;
– бегать по учебному полигону;
– поднимать и опускать шлагбаум переезда;
– находиться под поднятым шлагбаумом переезда.
3. При нахождении в лаборатории 8А запрещается:
– самостоятельно перемещать инструмент, находящийся в лаборатории;
– самостоятельно включать или заводить механизированный инструмент;
– самостоятельно включать станки, расположенные в лаборатории.
|
4. При производстве лабораторной работы в ангаре учебного полигона необходимо следовать следующим правилам:
– инструмент, используемый при выполнении работы, должен быть типовым и технически исправным;
– использовать инструмент следует только по прямому назначению;
– при монтаже и демонтаже скреплений запрещается располагать пальцы рук между рельсом и шпалой, а также между элементами рельсового скрепления.
Лабораторная работа №1
Рельсы новые
Рельс это основной и самый дорогой элемент железнодорожного пути, поскольку именно он воспринимает динамические нагрузки от колес подвижного состава. По этой причине к рельсам предъявляются повышенные требования.
Рельсы выполняют следующие функции:
– воспринимают нагрузку от колес подвижного состава и передают ее на подрельсовое основание;
– направляют колеса подвижного состава во время его движения;
– проводят сигнальный ток на участках с автоблокировкой и обратный тяговый ток на электрифицированных участках.
Для стабильного выполнения рельсами этих функций они должны быть прочными и твердыми, износостойкими, но в то же время упругими. Поверхность катания рельсов должна быть прямолинейной, без отклонений, поскольку их наличие приводит к возникновению дополнительных динамических сил при взаимодействии колеса с рельсом.
Цель работы
Изучение требований, предъявляемых к новым рельсам, таких как: твердость и отклонение от прямолинейности поверхности катания головки рельса, химический состав стали, класс профиля рельса.
Изучение содержания обозначения новых рельсов.
Освоение методики измерения твердости поверхности катания рельсов твердомером, освоение методики работы с рельсовым профилографом.
Место проведения работы
Лаборатория 8А «Железнодорожный путь, технология маханизация и автоматизация работ по техническому обслуживанию железнодорожного пути» СамГУПС.
Необходимый инструмент (рисунок 1.1)
1. Линейка длиной 1,5 метра, ГОСТ 474-75;
2. Набор щупов для измерения зазоров, ГОСТ 882-75;
3. Профилограф рельсовый (ПР-03);
4. Твердомер МЕТ-Д1.
Рисунок 1.1 Инструмент, используемый при выполнении лабораторной работы №1
Исходные данные
Рельсовая сталь содержит химические элементы, указанные в таблице 1.1.
|
Таблица 1.1
Содержание химических элементов в рельсовой стали по номеру группы и
номеру бригады
№ группы | № бригады | Вид стали | Массовая доля элементов, % | ||||||||
С | Mn | Si | V | Cr | N | P | S | Al | |||
К | 0,8 | 0,75 | 0,26 | 0,1 | 0,7 | 0,02 | 0,001 | 0,01 | 0,001 | ||
Э | 0,75 | 0,76 | 0,27 | 0,06 | 1,2 | 0,002 | 0,011 | 0,002 | |||
К | 0,81 | 0,77 | 0,28 | 0,07 | 0,1 | 0,015 | 0,003 | 0,012 | 0,003 | ||
Э | 0,85 | 0,78 | 0,29 | 0,08 | 0,3 | 0,016 | 0,004 | 0,013 | 0,004 | ||
К | 0,72 | 0,79 | 0,3 | 0,04 | 0,4 | 0,005 | 0,014 | 0,001 | |||
Э | 0,94 | 0,8 | 0,31 | 0,09 | 0,05 | 0,018 | 0,006 | 0,015 | 0,002 | ||
К | 0,77 | 0,81 | 0,32 | 0,05 | 0,08 | 0,007 | 0,016 | 0,003 | |||
Э | 0,79 | 0,82 | 0,33 | 0,06 | 0,5 | 0,019 | 0,008 | 0,017 | 0,004 | ||
К | 0,8 | 0,83 | 0,34 | 0,07 | 0,6 | 0,009 | 0,018 | 0,001 | |||
Э | 0,81 | 0,84 | 0,35 | 0,08 | 0,9 | 0,01 | 0,019 | 0,002 | |||
К | 0,83 | 0,85 | 0,36 | 0,09 | 0,09 | 0,02 | 0,011 | 0,02 | 0,003 | ||
Э | 0,73 | 0,86 | 0,37 | 0,07 | 0,1 | 0,011 | 0,012 | 0,019 | 0,004 | ||
К | 0,74 | 0,87 | 0,38 | 0,04 | 0,11 | 0,013 | 0,018 | 0,001 | |||
Э | 0,94 | 0,88 | 0,39 | 0,05 | 0,5 | 0,012 | 0,014 | 0,017 | 0,002 | ||
К | 0,8 | 0,89 | 0,4 | 0,06 | 0,6 | 0,013 | 0,015 | 0,016 | 0,003 | ||
Э | 0,75 | 0,9 | 0,41 | 0,1 | 0,1 | 0,014 | 0,016 | 0,015 | 0,004 | ||
К | 0,8 | 0,91 | 0,42 | 0,1 | 0,7 | 0,02 | 0,017 | 0,014 | 0,001 | ||
Э | 0,75 | 0,92 | 0,43 | 0,06 | 1,2 | 0,018 | 0,013 | 0,002 | |||
К | 0,81 | 0,93 | 0,44 | 0,07 | 0,1 | 0,015 | 0,019 | 0,012 | 0,003 | ||
Э | 0,85 | 0,94 | 0,45 | 0,08 | 0,3 | 0,016 | 0,02 | 0,011 | 0,004 | ||
К | 0,72 | 0,95 | 0,46 | 0,04 | 0,4 | 0,019 | 0,01 | 0,001 | |||
Э | 0,94 | 0,96 | 0,47 | 0,09 | 0,05 | 0,018 | 0,018 | 0,009 | 0,002 | ||
К | 0,77 | 0,97 | 0,48 | 0,05 | 0,08 | 0,017 | 0,008 | 0,003 | |||
Э | 0,79 | 0,98 | 0,49 | 0,06 | 0,5 | 0,019 | 0,016 | 0,01 | 0,004 | ||
К | 0,8 | 0,99 | 0,5 | 0,07 | 0,6 | 0,015 | 0,011 | 0,001 | |||
Э | 0,81 | 0,51 | 0,08 | 0,9 | 0,014 | 0,012 | 0,002 | ||||
К | 0,83 | 1,01 | 0,52 | 0,09 | 0,09 | 0,02 | 0,013 | 0,013 | 0,003 | ||
Э | 0,73 | 1,02 | 0,53 | 0,07 | 0,1 | 0,011 | 0,012 | 0,014 | 0,004 | ||
К | 0,74 | 1,03 | 0,54 | 0,04 | 0,11 | 0,011 | 0,015 | 0,001 | |||
Э | 0,94 | 1,04 | 0,55 | 0,05 | 0,5 | 0,012 | 0,01 | 0,016 | 0,002 | ||
К | 0,8 | 1,05 | 0,56 | 0,06 | 0,6 | 0,013 | 0,009 | 0,017 | 0,003 | ||
Э | 0,75 | 1,06 | 0,57 | 0,1 | 0,1 | 0,014 | 0,008 | 0,018 | 0,004 |
Теоретическая часть
Этапы производства рельсов
В настоящее время в Российской Федерации рельсы производятся на трех металлургических комбинатах: Нижнетагильский металлургический комбинат (НТКМ), Новокузнецкий металлургический комбинат (НКМК), Челябинский металлургический комбинат (ЧМК). Металлические части стрелочных переводов производят: ООО «Муромская стрелочная кампания», ОАО «Новосибирский стрелочный завод».
|
Процесс выплавки рельсовых заготовок разделен на следующие этапы:
1. Выплавка стали производится в электропечах или в конвекторе.
На НКМК рельсовую сталь выплавляют в 100-тонных дуговых электроплавильных печах. В электропечь загружают металлолом и заливают некоторым количеством жидкого чугуна. После расплавления металлолома, окислительного периода и достижения температуры в печах 1590-1630°С проводят предварительное раскисление и металл из печи выпускают в ковш. Продолжительность плавки составляет около часа.
На НТМК и ЧМК выплавка стали производится в 160-тонных кислородных конвекторах из ванадиевого чугуна дуплекс-процессом без использования металлолома. Продолжительность плавки составляет 30-50 минут.
2. Обработка в агрегатах печь-ковш. Здесь в процессе комплексной обработки проводят продувку жидкой стали инертным газом, раскисление шлака, раскисление жидкой стали порошковой проволокой с силикокальцием, доводят химический состав стали до заданного путем введения ферросплавов.
3. Вакуумирование на циркуляционном вакууматоре. Вакуумирование снижает содержание кислорода и углерода в рельсовой стали.
4. Непрерывная разливка заготовок поперечным сечением 300·360 мм.
5. Замедленное охлаждение заготовок, которое производится для равномерного охлаждения стали как на поверхности, так и в центре сечения рельса.
После окончания производства рельсовых заготовок производится прокатка и закалка рельсов. Возможны три варианта прокатки и закалки рельсов:
1. Нетермоупрочненые рельсы (НТ).
Заготовки нагреваются в методических печах с шагающими балками в течении 3-4 часов. Прокатка осуществляется на стане линейного типа, состоящем из двухвалковых обжимных клетей. После прокатки рельсовые раскаты режут дисковыми пилами, после чего они поступают на участок замедленного охлаждения.
2. Рельсы термоупрочненные, подвергнутые объемной закалке и отпуску (ОТ).
Прокатка рельсов производится способом, приведенным выше, далее производится термическая обработка рельсов, которая заключается в их нагреве в закалочной печи. Температура рельсов в момент закаливания составляет 815-830°С, продолжительность – 48-52 минуты. После нагрева рельсов, они подаются в закалочную машину, в которой охлаждаются при помощи подачи масла. Закаленные рельсы подаются в отпускную печь, в которой производится отпуск при температуре 435-465°С в течении 2-х часов. После отпуска рельсы охлаждаются на холодильнике.
3. Рельсы термоупрочненные, подвергнутые дифференцированному упрочнению по сечению рельса (ДТ).
Термическое упрочнение производится дифференцированно, то есть охлаждение рельса производится в различных режимах для головки, шейки и подошвы. Охлаждение производится посредством обдува охлажденным воздухом, интенсивность подачи которого и его температура различны в разных частях сечения рельса.
|
Прямолинейность рельсов.
Отклонения от прямолинейности на заданной базовой длине для рельсов соответствующих классов не должны превышать значений, указанных в таблице 1.5.
Таблица 1.5
Допускаемые отклонения рельсов от прямолинейности
Элемент рельса* | Направление отклонения | Класс А | Класс В | Класс С | |||
d, мм | L, м | d, мм | L, м | d, мм | L, м | ||
Основная часть рельса | В вертикальной плоскости | 0,30 | 0,40 | 0,60 | 1,5 | ||
и | и | ||||||
0,20 | 0,30 | ||||||
В горизонтальной плоскости | 0,45 | 1,5 | 0,60 | 1,5 | 0,80 | ||
Концевая зона рельса | Длина зоны | 2 м | 1,5 м | ||||
В вертикальной плоскости вверх | 0,40 | 0,50 | 1,5 | 0,70 | 1,5 | ||
и | |||||||
0,30 | |||||||
В вертикальной плоскости вниз | 0,2 мм при 0,6 м | ||||||
В горизонтальной плоскости | 0,60 | 0,50 | 1,5 | 0,50 | 1,5 | ||
и | |||||||
0,40 | |||||||
Переходная зона | Длина зоны | 2 м | 1,5 м | ||||
В вертикальной плоскости | 0,30 | 0,40 | 1,5 | - | - | ||
В горизонтальной плоскости | 0,60 | 0,40 | 1,5 | - | - | ||
Рельс в целом | В вертикальной плоскости | Для рельсов длиной 25 м и более - кривизна рельса, лежащего на подошве или головке, не более 10 мм | |||||
Для рельсов длиной менее 25 м: | |||||||
Прогиб не более 1/2500 длины рельса | Прогиб не более 1/2200 длины рельса |
Нормы прямолинейности класса А применяют для рельсов категорий ВС и СС, классов В и С - для рельсов остальных категорий.
Химический состав рельсов.
Химический состав стали, определяемый по ковшовой пробе, должен соответствовать, указанному в таблице 1.6.
Таблица 1.6
Химический состав стали
Марка стали | Массовая доля элементов, % | ||||||||
Углерод | Марганец | Кремний | Ванадий | Хром | Азот | Фосфор | Сера | Алюминий | |
Не более | |||||||||
90ХАФ | 0,83-0,95 | 0,75-1,25 | 0,25-0,60 | 0,08-0,15 | 0,20-0,60 | 0,010-0,020 | 0,020 | 0,020 | 0,004 |
76ХАФ | 0,71-0,82 | 0,75-1,25 | 0,25-0,60 | 0,05-0,15 | 0,20-0,80 | 0,010-0,020 | 0,020 | 0,020 | 0,004 |
76ХФ | 0,71-0,82 | 0,75-1,25 | 0,25-0,60 | 0,03-0,15 | 0,20-0,80 | - | 0,020 | 0,020 | 0,004 |
76ХСФ | 0,71-0,82 | 0,75-1,25 | 0,25-0,60 | 0,05-0,15 | 0,50-1,25 | - | 0,020 | 0,020 | 0,004 |
90АФ | 0,83-0,95 | 0,75-1,25 | 0,25-0,60 | 0,08-0,15 | Не более 0,20 | 0,010-0,020 | 0,020 | 0,020 | 0,004 |
76АФ | 0,71-0,82 | 0,75-1,25 | 0,25-0,60 | 0,05-0,15 | Не более 0,20 | 0,010-0,020 | 0,020 | 0,020 | 0,004 |
76Ф | 0,71-0,82 | 0,75-1,25 | 0,25-0,60 | 0,03-0,15 | Не более 0,20 | - | 0,020 | 0,020 | 0,004 |
Категории рельсов устанавливаются с учетом марки стали и термической обработки рельсов по таблице 1.7.
Таблица 1.7
Категории рельсов в зависимости от марки стали и термической
обработки рельсов
Марка стали | Категории рельсов по термическому упрочнению | ||
ДТ | ОТ | НТ | |
90ХАФ | ДТ370ИК | - | - |
90АФ | ДТ370ИК | ОТ370ИК | - |
76ХАФ | ДТ350НН | - | - |
76АФ | ДТ350НН | ДТ350НН | - |
76ХФ | ДТ350ВС ДТ350СС ДТ350 | НТ300 | |
76ХСФ | - | - | НТ320ВС НТ320 |
76Ф | ДТ350ВС ДТ350СС ДТ350 | ДТ350СС ОТ350 | НТ260 |
Механические свойства.
Механические свойства при испытаниях на растяжение и ударный изгиб должны соответствовать требованиям, указанным в таблице 1.8.
Таблица 1.8
Механические свойства
Категория рельсов | Временное сопротивление σВ, Н/мм | Предел текучести, σ0.2, Н/мм | Относительное удлинение, δ, % | Относительное сужение, ψ, % | Ударная вязкость, KSU, Дж/см |
не менее | |||||
ОТ370ИК | 8,0 | 20,0 | |||
ДТ370ИК | 9,0 | 14,0 | |||
ОТ350 ОТ350НН ОТ350СС | 8,0 | 25,0 | |||
ДТ350 ДТ350НН ДТ350СС ДТ350ВС | 9,0 | 25,0 | |||
НТ320 НТ320ВС | 9,0 | - | - | ||
НТ300 | 8,0 | - | - | ||
НТ260 | 8,0 | - | - | ||
Примечания: 1 Ударную вязкость для рельсов категорий ОТ350НН и ДТ350НН определяют при температуре образцов минус 60 °С, а для рельсов остальных категорий - при комнатной температуре. 2 Ударная вязкость для рельсов категории ДТ350НН из стали марки 76АФ, дифференцированно термоупрочненных с повторного нагрева, должна быть не менее 25 Дж/см |
Качество поверхности рельса
Поверхность нового рельса должна быть без раскатанных загрязнений, трещин, рванин, раскатанных корочек, плен, закатов, раковин от окалины, подрезов, вмятин, продиров, поперечных рисок и поперечных царапин. Выявление данных дефектов производится средствами неразрушающего контроля.
Вид и максимальные значения параметров допускаемых дефектов поверхности в зависимости от места их расположения приведены в таблице 1.10.
Таблица 1.10
Допускаемые дефекты поверхности рельса.
Вид дефекта | Параметр дефекта | Место расположения и параметры дефекта для классов качества поверхности рельсов Е и Р, мм | |||||
Поверхность катания | Средняя треть основания подошвы | Остальные элементы профиля | |||||
Е | Р | Е | Р | Е | Р | ||
Раскатанные пузыри и волосевины | Глубина | 0,35 | 1,00 | 0,30 | 0,30 | 0,50 | 1,00 |
Длина | |||||||
Продольные риски, царапины, морщины | Глубина | 0,30 | 0,50 | 0,30 | 0,30 | 0,50 | 0,50 |
Ход работы
1. Группа делится на 4 бригады для выполнения лабораторной работы.
2. Каждая бригада получает для выполнения работы образцы нового рельса типа Р-65, протяженностью 1,5 метра и 1 см. Длина рельса, от которого был взят образец – 25 метров.
3. На поверхности катания рельса протяженностью 1,5 метра производится измерение отклонений от прямолинейности согласно методике, приведенной в Приложении 1.
4. На поверхности катания рельса протяженностью 1,5 метра производится измерение твердости в контрольной точке 1 (рисунок 1.3) при помощи твердомера согласно методике, приведенной в Приложении 2.
5. На образце рельса толщиной 1 см производится измерение твердости на контрольных точках 2-8 (рисунок 1.3) при помощи твердомера согласно методике, приведенной в Приложении 2.
6. На образце рельса производится съемка профиля головки рельса при помощи профилографа согласно методике, приведенной в Приложении 3.
7. Путем наложения снятого профиля на эталонный определяются максимальные отклонения параметров профиля головки рельсов.
8. По таблице 1.9 определяется категория рельса.
9. По таблице 1.1 определяется марка стали рельса.
10. По таблице 1.4 определяется класс точности профиля.
11. По таблице 1.5 определяется класс прямолинейности.
12. Составляется схема обозначения рельса, как показано на рисунке 1.4. Класс качества поверхности принимается - Р.
Содержание отчета по лабораторной работе.
Отчет должен содержать результаты всех произведенных измерений, распечатанные профили, снятые при помощи профилографа. В качестве вывода указывается схема обозначения рельса с расшифровкой.
Контрольные вопросы.
1. Что обозначают позиции в схеме обозначения рельсов?
2. Что показывает цифра в типе рельсов (Р-65, Р50 и т.д.)?
3. Что такое твердость?
4. По какому принципу работает твердомер?
5. По какому принципу работает профилограф?
6. Что такое объемная закалка рельсов?
7. Что такое дифференцированная закалка рельсов?
8. Как определяется категория рельсов?
9. Как определяется класс точности профиля?
10. Как определяется класс прямолинейности рельса?
11. Что такое электросталь?
12. Что такое конверторная сталь?
Лабораторная работа №2
Цель работы
Изучить учетную форму ПУ-2 «Рельсовая книга», научиться правильно заполнять все разделы книги.
Научиться производить измерение износа головки рельсов, смятия стыков. Научиться получать информацию о рельсах по итогам визуального осмотра.
Инструмент
1. Дорожный курвиметр Nedo 703;
2. Штангенциркуль путевой ПШВ Путеец;
3. Линейка длиной 1 метр, ГОСТ 427-75.
Рисунок 2.1 Инструмент, необходимый для выполнения лабораторной работы №2
Место проведения работы
Железнодорожные пути учебного полигона СамГУПС.
Исходные данные
Таблица 2.1
Стрелочные переводы
Номер группы | Стрелочный перевод №1 | Стрелочный перевод №2 | Стрелочный перевод №3 |
Уложен 12.05.2003, Новый, при производстве твердость поверхности катания составляла 365 Бр, отклонение от прямолинейности 0,5 мм. | Уложен 18.09.1998, Новый, при производстве твердость поверхности катания составляла 355 Бр, отклонение от прямолинейности 0,6 мм. | Уложен 12.04.1986, Новый, при производстве твердость поверхности катания составляла 331 Бр, отклонение от прямолинейности 0,5 мм. | |
Уложен 21.08.2004, Новый, при производстве твердость поверхности катания составляла 345 Бр, отклонение от прямолинейности 0,8 мм. | Уложен 11.06.19.1976, Новый, при производстве твердость поверхности катания составляла 372 Бр, отклонение от прямолинейности 0,8 мм. | Уложен 12.05.1979, Новый, при производстве твердость поверхности катания составляла 356 Бр, отклонение от прямолинейности 0,2 мм. | |
Уложен 01.07.2005, Новый, при производстве твердость поверхности катания составляла 340 Бр, отклонение от прямолинейности 0,6 мм. | Уложен 08.08.1999, Новый, при производстве твердость поверхности катания составляла 399 Бр, отклонение от прямолинейности 0,7 мм. | Уложен 22.05.1980, Новый, при производстве твердость поверхности катания составляла 350 Бр, отклонение от прямолинейности 0,8 мм. | |
Уложен 03.05.2006, Новый, при производстве твердость поверхности катания составляла 336 Бр, отклонение от прямолинейности 0,4 мм. | Уложен 06.10.1982, Новый, при производстве твердость поверхности катания составляла 329 Бр, отклонение от прямолинейности 0,5 мм. | Уложен 11.07.1999, Новый, при производстве твердость поверхности катания составляла 338 Бр, отклонение от прямолинейности 0,6 мм. | |
Уложен 12.09.2007, Новый, при производстве твердость поверхности катания составляла 342 Бр, отклонение от прямолинейности 0,7 мм. | Уложен 29.07.1997, Новый, при производстве твердость поверхности катания составляла 359 Бр, отклонение от прямолинейности 0,8 мм. | Уложен 02.06.1994, Новый, при производстве твердость поверхности катания составляла 368 Бр, отклонение от прямолинейности 0,4 мм. | |
Уложен 25.08.2008, Новый, при производстве твердость поверхности катания составляла 374 Бр, отклонение от прямолинейности 0,5 мм. | Уложен 12.07.1995, Новый, при производстве твердость поверхности катания составляла 393 Бр, отклонение от прямолинейности 0,6 мм. | Уложен 11.04.1998, Новый, при производстве твердость поверхности катания составляла 366 Бр, отклонение от прямолинейности 0,7 мм. |
Таблица 2.2
Пути полигона
№ группы | 1 путь | 2 путь | 3 путь | 4 путь |
Уложен 01.06.1975, новый, при производстве твердость 325, отклонение от прямолинейности 0,4, первая пара рельсов старогодняя пропущенный тоннаж до переукладки 300 | Уложен 01.06.1976, новый, при производстве твердость 335, отклонение от прямолинейности 0,5, первая пара рельсов старогодняя пропущенный тоннаж до переукладки 200 | Уложен 01.06.1977, новый, при производстве твердость 345, отклонение от прямолинейности 0,6, первая пара рельсов старогодняя пропущенный тоннаж до переукладки 250 | Уложен 01.06.1978, новый, при производстве твердость 355, отклонение от прямолинейности 0,7, первая пара рельсов старогодняя пропущенный тоннаж до переукладки 350 | |
Уложен 01.06.1979, новый, при производстве твердость 365, отклонение от прямолинейности 0,8, первая пара рельсов старогодняя пропущенный тоннаж до переукладки 300 | Уложен 01.06.1980, новый, при производстве твердость 375, отклонение от прямолинейности 0,4, первая пара рельсов старогодняя пропущенный тоннаж до переукладки 300 | Уложен 01.06.1981, новый, при производстве твердость 385, отклонение от прямолинейности 0,5, первая пара рельсов старогодняя пропущенный тоннаж до переукладки 350 | Уложен 01.06.1982, новый, при производстве твердость 324, отклонение от прямолинейности 0,6, первая пара рельсов старогодняя пропущенный тоннаж до переукладки 300 | |
Уложен 01.06.1983, новый, при производстве твердость 334, отклонение от прямолинейности 0,7, первая пара рельсов старогодняя пропущенный тоннаж до переукладки 400 | Уложен 01.06.1984, новый, при производстве твердость 344, отклонение от прямолинейности 0,8, первая пара рельсов старогодняя пропущенный тоннаж до переукладки 400 | Уложен 01.06.1985, новый, при производстве твердость 354, отклонение от прямолинейности 0,4, первая пара рельсов старогодняя пропущенный тоннаж до переукладки 450 | Уложен 01.06.1986, новый, при производстве твердость 364, отклонение от прямолинейности 0,5, первая пара рельсов старогодняя пропущенный тоннаж до переукладки 450 | |
Уложен 01.06.1987, новый, при производстве твердость 374, отклонение от прямолинейности 0,6, первая пара рельсов старогодняя пропущенный тоннаж до переукладки 500 | Уложен 01.06.1988, новый, при производстве твердость 384, отклонение от прямолинейности 0,7, первая пара рельсов старогодняя пропущенный тоннаж до переукладки 270 | Уложен 01.06.1989, новый, при производстве твердость 328, отклонение от прямолинейности 0,8, первая пара рельсов старогодняя пропущенный тоннаж до переукладки 320 | Уложен 01.06.1990, новый, при производстве твердость 338, отклонение от прямолинейности 0,4, первая пара рельсов старогодняя пропущенный тоннаж до переукладки 550 | |
Уложен 01.06.1991, новый, при производстве твердость 348, отклонение от прямолинейности 0,5, первая пара рельсов старогодняя пропущенный тоннаж до переукладки 600 | Уложен 01.06.1992, новый, при производстве твердость 358, отклонение от прямолинейности 0,6, первая пара рельсов старогодняя пропущенный тоннаж до переукладки 370 | Уложен 01.06.1993, новый, при производстве твердость 368, отклонение от прямолинейности 0,7, первая пара рельсов старогодняя пропущенный тоннаж до переукладки 420 | Уложен 01.06.1994, новый, при производстве твердость 378, отклонение от прямолинейности 0,8, первая пара рельсов старогодняя пропущенный тоннаж до переукладки 650 | |
Уложен 01.06.1995, новый, при производстве твердость 388, отклонение от прямолинейности 0,4, первая пара рельсов старогодняя пропущенный тоннаж до переукладки 700 | Уложен 01.06.1996, новый, при производстве твердость 326, отклонение от прямолинейности 0,5, первая пара рельсов старогодняя пропущенный тоннаж до переукладки 300 | Уложен 01.06.1997, новый, при производстве твердость 336, отклонение от прямолинейности 0,6, первая пара рельсов старогодняя пропущенный тоннаж до переукладки 350 | Уложен 01.06.1998, новый, при производстве твердость 346, отклонение от прямолинейности 0,7, первая пара рельсов старогодняя пропущенный тоннаж до переукладки 750 |
Теоретическая часть
Ведомость рельсов, лежащих в главных путях, состоит из следующих разделов:
1. «КМ»
Указывается номер километра, на котором уложен рельс.
2. «ПК»
Указывается номер пикета, на котором уложен рельс. Если рельс расположен на границе двух пикетов, то его относят к тому пикету, где звено начинается (по счету километров).
3. «Метр начала звена»
Указывается метр начала звена, измеренный от пикетного столбика.
4. «Звено»
Указывается номер звена. Количество звеньев учитывается в пределах пикета.
5. «Нить»
Указывается сторонность нити. Сторона нити определяется по ходу километров.
6. «№ стрелочного перевода, № плети»
В случае если рассматриваемый рельс является частью рельсовой плети, указывается номер плети по проекту. Данный номер также указывается в маркировке рельсовой плети, которая наносится белой краской на шейке рельса с внутренней стороны на расстоянии 1 метра от начала плети.
В случае, если рельс является частью стрелочного перевода, указывается номер стрелочного перевода, согласно схеме станции.
7. «Год прокатки»
Указывается год прокатки (производства) рельса. Год и месяц прокатки указывается на самом рельсе в виде выпуклых цифр. Месяц указывается римскими цифрами, а год – арабскими.
8. «Дата укладки»
Указывается дата укладки рельса в данный участок пути.
9. «Тип рельса»
Указывается тип рельса. Тип рельса обозначается буквой «Р» и цифрой, обозначающей примерную массу одного погонного метра рельса. Типы рельсов, уложенные на отечественных железных дорогах, указаны в таблице 2.3. Тип рельса указывается на шейке рельса выпуклыми символами.
Таблица 2.3
Типы рельсов
№ | Тип рельса | Масса погонного метра рельса | Область применения |
Р-75 | 74,60 | Все пути | |
Р-65 | 64,88 | Все пути | |
Р-65К | 64.67 | Наружные рельсы в кривых участках | |
Р-50 | 51,80 | Приемо-отправочные и прочие станционные пути | |
Р-43 | 44,65 | Прочие станционные и подъездные пути | |
Р-38 | 38,42 | Прочие станционные и подъездные пути | |
Р-33 | 33,48 | Прочие станционные и подъездные пути |
10. «Признак укладки»
В данном разделе указывается буква:
«Н» – если укладывается новый рельс;
«П» – если рельс ранее был уложен на другом участке пути и был переложен в данный участок пути.
При производстве капитального ремонта пути (и других видов ремонта) производится сплошная замена рельсошпальной решетки. После снятия решетки ее перевозят в ПМС (путевая машинная станция), где производится ее демонтаж. После демонтажа рельсы подлежат сортировке, в результате которой отбираются рельсы, пригодные к повторной укладке в путь.
11. «Характеристики переложенных рельсов. Вид ремонта»
Данный раздел заполняется только для переложенных рельсов. Указывается вид ремонта рельса после изъятия его из пути.
«П» – при производстве шлифовки головки рельса в РСП.
При сварке старогодных рельсов в плеть или повторном использовании рельсовых плетей, рельсы из ПМС отправляются в РСП (рельсосварочный поезд). Старогодные рельсы, относящиеся по пропущенному тоннажу к группам годности I, II, III, но по другим показателям не соответствующие требованиям таблицы 4, предварительно ремонтируют в РСП с целью повышения группы годности рельсов, а затем направляют для профильной обработки их головки строжкой или фрезеровкой.
При наличии в рельсах дефектов 10, 11, 14, 17, 18 глубиной более 2 мм, а также 20, 21, 24, 25, 26.3, 27, 30В, 30Г, 46.3, 50, 52, 55, 56.3, 60, 62, 65 производят их вырезку на расстоянии 10 см от краев дефекта. При распространении вышеуказанных дефектов и дефектов 40, 41, 43 по всей длине рельса старогодные рельсы переводят в IV группу годности.
Рельсы с дефектами 85, 86.3 подвергают правке, а при невозможности их выправки производят вырезку дефектов.
Старогодные рельсы с дефектами 59, 69, 74 на репрофилирование не направляются.
Перед вырезкой дефектных мест, обнаруженных при дефектоскопировании, необходимо светлой краской повторить маркировку на всех кусках рельса, которые будут направлены на фрезеровку, строжку или сварку.
Куски рельсов длиной менее 3 м, оставшиеся после резки, отбраковывают в металлолом, длиной от 3 до 6 м - используют в качестве концевых при формировании мерных рельсов длиной 25 м, а от 6 м и более - отправляют на фрезерование, строжку или сварку для формирования 25-метровых рельсов с последующей их строжкой или сварку рельсов в бесстыковые рельсовые плети.
Старогодные рельсы после удаления вышеперечисленных дефектов и проведения ремонта должны быть отнесены к соответствующей группе годности в зависимости от их состояния по другим показателям.
У рельсов отрезают концевые участки на расстоянии не менее 10 см от края последнего бокового отверстия, включая отверстия под штепсельные соединители и дроссельные перемычки.
Старогодные рельсы, имеющие по всей длине рельса дефект 11, а также дефект 10 с глубиной отслоений и выкрашиваний более 2 мм длиной до 10 мм, репрофилированию не подлежат, а переводятся в группу годности III-5 с укладкой в пути 5 класса.
Технология фрезерования предусматривает за один проход рельса длиной от 6 м и более формирование ремонтного профиля обработкой поверхности катания и боковой выкружки комплектом специальных фрез, оснащенных неперетачиваемыми твердосплавными пластинами.
Допуск<
|
|
Эмиссия газов от очистных сооружений канализации: В последние годы внимание мирового сообщества сосредоточено на экологических проблемах...
Типы оградительных сооружений в морском порту: По расположению оградительных сооружений в плане различают волноломы, обе оконечности...
Адаптации растений и животных к жизни в горах: Большое значение для жизни организмов в горах имеют степень расчленения, крутизна и экспозиционные различия склонов...
Таксономические единицы (категории) растений: Каждая система классификации состоит из определённых соподчиненных друг другу...
© cyberpedia.su 2017-2024 - Не является автором материалов. Исключительное право сохранено за автором текста.
Если вы не хотите, чтобы данный материал был у нас на сайте, перейдите по ссылке: Нарушение авторских прав. Мы поможем в написании вашей работы!