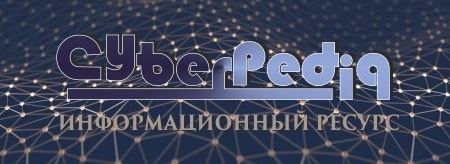
Историки об Елизавете Петровне: Елизавета попала между двумя встречными культурными течениями, воспитывалась среди новых европейских веяний и преданий...
Организация стока поверхностных вод: Наибольшее количество влаги на земном шаре испаряется с поверхности морей и океанов (88‰)...
Топ:
Оценка эффективности инструментов коммуникационной политики: Внешние коммуникации - обмен информацией между организацией и её внешней средой...
История развития методов оптимизации: теорема Куна-Таккера, метод Лагранжа, роль выпуклости в оптимизации...
Генеалогическое древо Султанов Османской империи: Османские правители, вначале, будучи еще бейлербеями Анатолии, женились на дочерях византийских императоров...
Интересное:
Принципы управления денежными потоками: одним из методов контроля за состоянием денежной наличности является...
Берегоукрепление оползневых склонов: На прибрежных склонах основной причиной развития оползневых процессов является подмыв водами рек естественных склонов...
Наиболее распространенные виды рака: Раковая опухоль — это самостоятельное новообразование, которое может возникнуть и от повышенного давления...
Дисциплины:
![]() |
![]() |
5.00
из
|
Заказать работу |
|
|
Энергетические войны: Часть 1. Вступление
Брагинский О.Б. Нефтегазовый комплекс мира - М.: Изд-во им. ИМ Губкина. 2006. - 640 с.
Америка́нский нефтяно́й ба́ррель — единица измерения объёма нефти, равная 42 галлонам или 158,988 литрам.
Развитие нефтеперерабатывающей отрасли
В России и мире
Первые попытки получить из нефти новые продукты человечество предприняло около 5 тыс. лет назад. За всю долгую историю нефтепереработки цели таких преобразований были самые разнообразные — от научного любопытства до получения нового оружия и горючих материалов. Сегодня сложно найти сферу промышленности, в которой не задействованы в том или ином виде нефтепродукты, но еще сложнее предсказать, где они окажутся востребованными завтра
ГЛУБИНА ПЕРЕРАБОТКИ НЕФТИ
В последние десятилетия в мире прослеживается четкая тенденция на укрупнение среднего размера НПЗ, на увеличение глубины переработки нефти и, соответственно, сложности предприятия. Впрочем, разброс значений довольно велик: мощность самого крупного в мире завода в Джамнагаре (Индия) составляет 70 млн тонн н. э. в год, а среднемировой размер НПЗ — всего около 7 млн тонн.
Существенно может варьироваться и коэффициент, отражающий глубину переработки нефти. В лидерах здесь США, где средняя глубина переработки порядка 95%, а на некоторых производствах показатель достигает и 98%. В России средний показатель для отечественных НПЗ — 74,2%, лучшие заводы, к которым относятся и предприятия «Газпром нефти», дают 80–85%.
Глубина переработки = (Объём переработки — Объём производства мазута — Объём потерь и топлива на собственные нужды) / Объём переработки * 100 %
|
Для оценки и сравнения отдельных нефтеперерабатывающих предприятий или отраслей разных регионов мира используются показатели «глубина переработки нефти» [3], «выход светлых нефтепродуктов», «доля вторичных процессов» [4], «коэффициент сложности» [5, 6].
3. Каминский Э. Ф., Хавкин В. А. Глубокая переработка нефти: технологический и экологический аспекты. – М.: Техника, 2001. — 384 с.
4. Сомов В. Е., Садчиков И. А., Шершун В. Г. и др. Стратегические приоритеты российских нефтеперерабатывающих предприятий. — М.: ЦНИИТЭнефтехим, 2002. — 292 с.
5. Johnson D. Complexity Index Indicates Refinery Capability, Value // Oil & Gas Journal. – 1996. – V. 18. – P. 74–80.
6. Брагинский О. Б. Сколько стоит НПЗ? // Нефть и бизнес. — 1997. — № 3. — С. 27–30.
7. Брагинский О.Б. Нефтегазовый комплекс мира - М.: Изд-во им. ИМ Губкина. 2006. - 640 с
Ни один из перечисленных показателей не лишен недостатков. Так, показатели «глубина переработки нефти» и «выход светлых нефтепродуктов» не характеризуют качество получаемых продуктов, а также качество поступающего на переработку нефтяного сырья, в частности, содержание в нем светлых фракций.
Рейтинг сложности НПЗ, вычисляемый по известным индексам Нельсона отдельных технологических процессов, представляет собой сугубо экономическую оценку стоимости сооружения предприятия и слабо отражает его технологический уровень.
Индекс Нельсона
Индекс оценивает сложность производства и иллюстрирует уровень развития мощностей вторичной переработки по сравнению с первичной мощностью дистилляции. Для расчета индекса оборудованию по перегонке сырой нефти присваивают коэффициент 1, а все остальные установки сравнивают с ним по сложности и стоимости. Например, установка каталитического крекинга имеет коэффициент, равный 4, то есть она в четыре раза сложнее, чем установка для перегонки сырой нефти при той же производительности. Суммируя значения сложности, присвоенные каждой единице оборудования, определяют сложность НПЗ по индексу сложности Нельсона.
|
К 2015 году средний индекс Нельсона для американских НПЗ составлял порядка 12 единиц, для европейских и азиатских — около 8, а для лучших заводов, например НПЗ в индийском Джамнагаре — 14. По прогнозам экспертов, в ближайшем будущем смогут выжить только заводы, имеющие индекс Нельсона не ниже 10, а новые производства изначально будут иметь сложность около 15 единиц.
Комплексная оценка Нельсона, сопоставленная с глубиной нефтепереработки, дают более ясную характеристику НПЗ, как показано в таблице 2.
Анализируя данные таблицы, можно сделать вывод, что наибольший индекс Нельсона имеют нефтеперерабатывающие заводы нефтехимического профиля, при этом глубина нефтепереработки может быть невысокой.
Тенденция на углубление переработки характерна для НПЗ во всем мире. Это связано с перманентно уменьшающимся спросом на мазут, представляющий собой тяжелые остатки переработки нефти и нефтепродуктов, и все возрастающим спросом на высококачественный бензин и дизельное топливо. В частности, именно бурный рост в США автопарка и, как следствие, спроса на бензин привели в свое время к углублению процессов вторичной переработки на местных НПЗ. В то же время СССР с успехом использовал мазут в качестве топлива на ТЭЦ и отправлял его на экспорт, что привело к значительному отставанию во внедрении сложных вторичных процессов.
Еще одним стимулом к развитию и модернизации НПЗ служит повсеместное ужесточение экологических требований к товарным бензинам, а также совершенствование автомобильных двигателей, способствующее росту спроса на высокооктановое топливо. Все это влечет за собой необходимость внедрять в производство процессы гидроочистки и гидрокрекинга, позволяющие получать высококачественные высокооктановые бензины с минимальным содержанием серы.
По прогнозам экспертов, в ближайшие пять лет на гидроочистку и гидрокрекинг придется более 50% всех вводимых вторичных процессов в мире, при этом максимальный прирост мощностей будет касаться именно гидроочистки, — процесса, отвечающего в первую очередь за чистоту получаемого продукта.
Что же касается перспектив долгосрочного развития отрасли, то предметом спора ведущих экспертов стал вопрос, сохранят ли через 15–20 лет бензин и дизельное топливо свои доминирующие позиции на рынке или уступят место альтернативным источникам энергии. Однако, нефтехимическая промышленность, по прогнозам, сможет поддержать отрасль при любом развитии событий: в отличие от альтернативных топлив, речи об альтернативных пластиках сегодня практически не ведется, в то же время продукция нефтехимии все более совершенствуется и находит новые применения в огромном количестве областей.
|
России от бывшего СССР достались 26 морально и физически утаревших НПЗ. Из них восемь было пущено в эксплуатацию до Второй мировой войны, пять — построены до 1950 г., еще девять — до 1960 г. Таким образом, 23 из 26 НПЗ эксплуатируются более 40-70 лет. Практически все новые заводы, построенные СССР в 70-80 годы, располагались в союзных республиках. РФ на 80% досталось изношенное морально отсталое оборудование и глубина переработки нефти на российских НПЗ к началу 90-х составляла 64%. Глубина переработки нефти в 1999 году составила в среднем по России 67,4%, и только на Омском НПЗ она достигала 81,5%, приблизившись к западноевропейским стандартам.
К 2013 году в России действовало 50 заводов, включая 23 крупных НПЗ в структуре вертикально-интегрированных нефтяных компаний (ВИНК), восемь независимых НПЗ с объемом переработки более 1 млн тонн в год, а также 15 заводов с объемом переработки менее 1 млн тонн в год. Объем переработки в 2013 году достиг 275,2 млн тонн со средневзвешенным уровнем загрузки по России 92,9% и глубиной переработки — 72%.
Только в 2015 г в России было введено в эксплуатацию 11 установок вторичной переработки нефти. Общий объем переработки нефти составил 282,4 млн тонн. Глубина переработки составила 74,2%.
«Газпромнефть–Омский НПЗ», дочернее предприятие компании «Газпром нефть», является одним из самых современных нефтеперерабатывающих заводов России и одним из крупнейших в мире. В 2015 году Омский НПЗ переработал 20,9 млн тонн нефти. Предприятие на 3,6% — до 4 млн тонн — увеличило объем производства бензина экологического стандарта «Евро-5» по сравнению с предыдущим годом. Выпуск дизельного топлива 5-го экологического класса составил 6,3 млн тонн, что соответствует уровню 2014 года.
|
Среди крупнейших текущих и перспективных отечественных проектов НПЗ, ГПЗ и нефтехимических предприятий выделяются следующие: http://www.oilandgasrefining.ru/refinery-report/
гидроочистка дизельного топлива – «Газпромнефть – МНПЗ», «Киришинефтеоргсинтез», «Газпромнефть – Ярославнефтеоргсинтез», ЛУКОЙЛ-Волгограднефтепереработка, ЛУКОЙЛ-Ухтанефтепереработка, Хабаровский НПЗ;
изомеризация - «Газпромнефть – МНПЗ», Саратовский НПЗ;
гидроочистка бензина каталитического крекинга – «Газпромнефть – МНПЗ», «Газпромнефть – ОНПЗ», Уфимский НПЗ, «Газпромнефть – Ярославнефтеоргсинтез»;
риформинг - Новокуйбышевский НПЗ, Хабаровский НПЗ;
алкилирование - Новоуфимский НПЗ, «Славнефть – ЯНОС»;
гидродепарафинизация масел - ТАНЕКО.
ПОДГОТОВКА НЕФТИ
Прежде чем попасть на производство, нефть еще на промысле проходит первоначальную подготовку. При помощи газонефтяных сепараторов из нее удаляют наиболее легкие, газообразные составляющие. Это попутный нефтяной газ (ПНГ), состоящий преимущественно из метана, этана, пропана, бутана и изобутана, то есть из углеводородов, в молекулах которых содержится от одного до четырех атомов углерода (от CH4 до C4H10). Этот процесс называется стабилизацией нефти — подразумевается, что после него нефть будет сохранять свой состав и основные физико-химические свойства при транспортировке и хранении.
Объективно говоря, разгазирование пластовой нефти начинается еще в скважине по мере продвижения ее наверх: из-за падения давления в жидкости газ из нее постепенно выделяется. Таким образом, наверху приходится иметь дело уже с двухфазным потоком — нефть / попутный газ. Их совместное хранение и транспортировка оказываются экономически невыгодными и затруднительными с технологической точки зрения. Чтобы переместить двухфазный поток по трубопроводу, необходимо создать в нем условия постоянного перемешивания, чтобы газ не отделялся от нефти и не создавал в трубе газовые пробки. Все это требует дополнительных затрат. Намного проще оказывается пропустить газонефтяной поток через сепаратор и максимально отделить от нефти ПНГ. Получить абсолютно стабильную нефть, составляющие которой совсем не будут испаряться в атмосферу, практически невозможно. Некоторое количество газа все равно останется и будет извлечено в процессе нефтепереработки.
Для подготовки нефти на промыслах применяют Дожимные насосные станции с установкой предварительного сброса воды (ДНС с УПСВ), где идет многоступенчатый процесс сепарации газа. При этом решается проблема достижения нормативного уровня использования ПНГ в 95%, которая, наиболее остро стояла перед небольшими месторождениями, расположенными в районах со слабо развитой инфраструктурой. Погасить факела на промыслах - важнейшая проблема экономики и экологии нефтедобычи. Кстати, сам попутный нефтяной газ — это ценное сырье, которое может использоваться для получения электроэнергии и тепла, а также в качестве сырья для нефтехимических производств. На газоперерабатывающих заводах из ПНГ получают технически чистые отдельные углеводороды и их смеси, сжиженные газы, серу.
|
На промыслах проводят только первичную подготовку нефти – ее отстаивание и термохимическое обезвоживание, а в ряде случаев и обессоливание. Свежие водно-нефтяные эмульсии сразу после выхода из скважины разрушаются значительно легче, поэтому первичное обезвоживание и обессоливание следует проводить на промыслах. В отстойники установок подготовки нефти добавляют деэмульгаторы – специальные вещества, способствующие разрушению эмульсий и ускоряющие процесс расслаивания нефти и воды. При выборе деэмульгатора учитывают тип нефти (смолистая, парафинистая), содержание в ней воды, интенсивность перемешивания, температуру и другие. Деэмульгатор, кроме того, не должен вызывать коррозию трубопроводов и аппаратуры, иметь неприятный запах, вызывать загрязнения окружающей среды. Также на месторождении от нефти отделяют воду и механические примеси. После этого она поступает в магистральный нефтепровод и отправляется на нефтеперерабатывающий завод (НПЗ).
Переработку нефти на НПЗ начинают с очистки от содержащихся в ней солей (хлоридов и сульфатов натрия, кальция и магния), которые вызывают коррозию оборудования, оседают на стенках труб, загрязняют насосы и клапаны. Для этого используются электрообессоливающие установки (ЭЛОУ), где нефть смешивают с водой, в результате чего возникает эмульсия — микроскопические капли воды в нефти, в которых растворяется соль. Эмульсию подвергают воздействию электрического поля, из-за чего капли соленой воды сливаются друг с другом и затем отделяются от нефти. В переработку допускается нефть, содержащая £ 0,1% воды и £ 3–4 мг/л солей. Таким образом, подготовку нефти к переработке осуществляют дважды: на нефтепромыслах и на НПЗ.
Электродегидраторы блока ЭЛОУ
Наука - Технология добычи газа и нефти
Обезвоживание и обессоливание нефти это процессы очистки нефти от воды и минеральных солей. Глубокое обессоливание нефти обеспечивает снижение коррозии и уменьшение отложений в аппаратуре, улучшение качества нефтяных фракций, в том числе и по содержанию металлов. Нефть, поступающая в колонну атмосферной ректификации, должна содержать воды не более 0,2 мае. % и солей не более 5 мг/л, в то время как в добываемой из скважины нефти содержание воды может быть от 5 до 90 % и минеральных солей до 10-15 кг/т. После промысловой подготовки нефти к транспорту содержание солей в ней снижается до 40-1800 мг/л и воды до 0,2-1,0 мае. %.
Уменьшение содержания солей в нефти с 8-14 до 3 мг/л снижает потери от коррозии и позволяет не только увеличить межремонтный период работы установок ректификации нефти и мазута от 1-2 до 3-5 лет, но и продлить межремонтный период работы установок вторичной переработки нефтяных фракций, а также уменьшить расход технологического топлива, реагентов и катализаторов.
Вода и нефть взаимно нерастворимы, но при интенсивном перемешивании они образуют водонефтяную дисперсную смесь - эмульсию «вода в нефти», разделение которой в отстойниках не происходит из-за малого диаметра частиц диспергированной воды (от 0,1 до 1000 мкм). Минеральные соли присутствуют растворенными в воде, поэтому при обезвоживании нефти происходит и ее обессоливание. Разрушают водонефтяные эмульсии гидромеханическим, термохимическим и электротермохимическим методами, для чего создана и соответствующая аппаратура.
Гидромеханический метод отстаивания нефти с целью расслоения пластовой воды и нефти, а также для осаждения мелких частиц диспергированной воды в слое нефти осуществляется в гравитационных отстойниках различной конструкции. Отстойники - это обычно горизонтальные цилиндрические аппараты объемом 100-150 м3 с большой поверхностью раздела фаз, в которых отстаивание нефти происходит в течение 1-2 ч при температуре 120-140 °С и давлении до 1,5 МПа. Простое отстаивание нефти малоэффективно, но оно входит обязательным элементом во все другие методы обезвоживания.
Термохимический метод использует добавление в нефть деэмульгаторов, которые химически разрушают оболочку мельчайших глобул диспергированной воды. Мелкие глобулы воды объединяются друг с другом, и образовавшиеся глобулы крупного диаметра осаждаются с гораздо большей скоростью. Деэмульгаторы (5-50 г/т нефти) в смесителе добавляют к нефти, которая при температуре 60-100 °С направляется в горизонтальный отстойник. Деэмульгаторы чрезвычайно разнообразны, их состав и добавляемое количество подбирают экспериментально для каждой нефти разных месторождений. Наибольшее применение получили поверхностно-активные вещества (ПАВ): сульфанол, сульфоэфиры, оксиэтилированные жидкие органические кислоты (ОЖК), алкилфенолы (ОП-Ю и ОП-ЗО), нефтенолы, органические спирты (неонол, синтанол и др.), сополимеры этилен- и пропиленоксидов (диссольван, проксанолы, проксамин, кемеликс, сепарол и др.), дипроксамин, оксафоры, прохинор и др.
Глубокая очистка нефти от воды (до 0,1 мае. %) и солей (до 1-5 мг/л) достигается только электротермохимическим методом с интенсивным осаждением мелких частиц воды в сильном электрическом поле в присутствии больших количеств свежей промывочной пресной воды (5-7 мае. %). Сферические глобулы (капли) воды под действием переменного электрического поля деформируются, вытягиваются, «дрожат», соударяются и, наконец, сливаются в более крупные глобулы. Этому способствуют также и деэмульгаторы, разрывающие оболочки капель воды, и повышенная температура (120-130 °С), понижающая вязкость нефти. Все эти факторы вместе увеличивают скорость осаждения капель диспергированной воды, в которой растворены минеральные соли.
Очистка нефти от воды и солей начинается на нефтяном промысле (подготовка нефти к транспорту) и заканчивается на НПЗ, при этом возможны три-пять стадий очистки с использованием разных методов обезвоживания. Конечной стадией является электрообезвоживание нефти на НПЗ. Современная технологическая установка обезвоживания и обессоливания нефти с применением электродегидраторов может быть автономной (например, ЭЛОУ-6, индекс 10/6) или быть блоком в составе комбинированной установки атмосферной ректификации нефти и вакуумной ректификации мазута (например, ЭЛОУ-АТ-8, индекс 13/1 или ЭЛОУ-АВТ-6, индекс 11/4). В последнем варианте нефть насосом прокачивается через теплообменную группу, где за счет тепла полученных нефтяных фракций нагревается до температуры 130-140 °С и под давлением 1,4-1,5 МПа через смеситель (для смешивания нефти с деэмульгатором и промывочной пресной водой) поступает в электродегидраторы первой ступени. Далее обезвоженная нефть вновь смешивается с деэмульгатором и промывочной пресной водой и поступает в электродегидраторы второй ступени, из которых обезвоженная и обессоленная нефть проходит теплообменную группу для нагрева до температуры 200-230 °С перед первой ректификационной колонной. Из электродегидраторов отводится дренажная соленая вода (с большей частью деэмульгатора и солями) для дальнейшей утилизации. Конструкции промысловых и заводских электродегидраторов несколько различаются. Типовой горизонтальный электродегидратор (рис. 2.10) имеет диаметр 3,4 м и длину 18-24 м, объем 160-200 м3 и расчетное давление 1,8 МПа. Внутри него располагаются два-три решетчатых электрода (несколько выше оси аппарата), которые подвешиваются на изоляторах к корпусу аппарата. Для работы используется высокое напряжение переменного электрического тока (22-44 кВ), расход электроэнергии составляет 2,5-5,0 Вт /м3 нефти.
ФРАКЦИОННЫЙ СОСТАВ НЕФТИ
Нефть состоит из множества компонентов — фракций, — свойства, область применения и технологии переработки которых различны.
Нефть состоит из большого количества разных углеводородов. Их молекулы различаются массой, которая, в свою очередь, определяется количеством составляющих их атомов углерода и водорода. Чтобы получить тот или иной нефтепродукт, нужны вещества с совершенно определенными характеристиками, поэтому переработка нефти на НПЗ начинается с ее разделения на фракции.
В одной фракции могут содержаться молекулы разных углеводородов, но свойства большей части из них близки, а молекулярная масса варьируется в определенных пределах. Разделение фракций происходит путем перегонки и основано на том, что у разных углеводородов температура кипения различается: у более легких она ниже, у более тяжелых — выше. Этот процесс называется перегонкой (дистилляцией).
Основные фракции нефти определяют по интервалам температур, при которой кипят входящие в них углеводороды:
бензиновая фракция — 28–150°C,
керосиновая фракция — 150–250°C,
дизельная фракция, или газойль — 250–360°C,
мазут — выше 360°C.
Например, при температуре 120°C большая часть бензина уже испарилась, но керосин и дизельное топливо находятся в жидком состоянии. Когда температура поднимается до 150°C, начинает кипеть и испаряться керосин, после 250°C — дизель.
Существует ряд специфических названий фракций, используемых в нефтепереработке. Так, например, головной пар — это наиболее легкие фракции, полученные при первичной переработке. Их разделяют на газообразную составляющую и широкую бензиновую фракцию. Боковые погоны — это керосиновая фракция, легкий и тяжелый газойль.
Фракции, кипящие при температуре свыше 360°C, при атмосферной перегонке (перегонке при атмосферном давлении) не отделяются, так как при более высокой температуре начинается их термическое разложение (крекинг): крупные молекулы распадаются на более мелкие и состав сырья меняется. Чтобы этого избежать, остаток атмосферной дистилляции (мазут) подвергают перегонке в вакуумной колонне. Так как в вакууме любая жидкость кипит при более низкой температуре, это позволяет разделить и более тяжелые составляющие. На этом этапе выделяются фракции смазочных масел, сырье для термического или каталитического крекинга, гудрон.
Многие процессы на НПЗ требуют подогрева нефти или нефтепродуктов. Для этого используются трубчатые печи. Нагрев сырья до требуемой температуры происходит в змеевиках из труб диаметром 100–200 мм.
Ахметов ОСНОВЫ ФИЗИКОХИМИИ НЕФТИ... 1.2.1. Элементный и фракционный состав нефти
С позиций химии нефть – сложная исключительно многокомпонентная взаиморастворимая смесь газообразных, жидких и твердых углеводородов различного химического строения с числом углеродных атомов до 100 и более с примесью гетероорганических соединений серы, азота, кислорода и некоторых металлов. По химическому составу нефти различных месторождений весьма разнообразны и обсуждение можно вести лишь о составе, молекулярном строении и свойствах «среднестатистической» нефти. Менее всего колеблется элементный состав нефтей: 82,5…87 % углерода; 12,5…14,5 % водорода; 0,05…0,35, редко до 0,7 % кислорода; до 1,8 % азота и до 5,3, редко до 10 % серы. Кроме названных, в нефтях обнаружены в незначительных количествах другие элементы, в т. ч. металлы (Са, Mg, Fe, Al, Si, V, Ni, Na и др.).
Поскольку нефть и нефтепродукты представляют собой многокомпонентную смесь углеводородов и гетероатомных соединений, то обычными методами перегонки не удается разделить их на индивидуальные соединения со строго определенными физическими константами, в частности температурой кипения при данном давлении. Принято разделять нефти и нефтепродукты путем перегонки на отдельные компоненты, каждый из которых является менее сложной смесью и называется фракцией или дистиллятом. В условиях лабораторной или промышленной перегонки отдельные фракции отгоняются при постепенно повышающейся температуре кипения, поэтому нефть и ее фракции характеризуются не температурой кипения, а температурами начала кипения (н. к.) и конца кипения (к. к.).
При исследовании качества новых нефтей (т. е. составлении технического паспорта нефти) их фракционный состав определяют на стандартных перегонных аппаратах, снабженных ректификационными колонками (например, на АРН-2 по ГОСТ 11011–85). Это позволяет значительно улучшить четкость погоноразделения и построить по результатам фракционирования так называемую кривую истинных температур кипения (ИТК) в координатах температура – выход фракций в % мас., (или % об.).
Отбор фракций до 200 °С проводится при атмосферном давлении, а более высококипящих – под вакуумом во избежание термического разложения. По принятой методике от начала кипения до 300 °С отбирают 10-градусные, а затем 50-градусные фракции до температуры к. к. 475…550 °С. Таким образом, фракционный состав нефтей (кривая ИТК) показывает потенциальное содержание в них отдельных нефтяных фракций, являющихся основой для получения товарных нефтепродуктов (автобензинов, реактивных и дизельных топлив, смазочных масел и др.).
Нефти различных месторождений значительно различаются по фракционному составу, а следовательно, по потенциальному содержанию дистиллятов моторных топлив и смазочных масел. Большинство нефтей содержит 15…25 % бензиновых фракций, выкипающих до 180 °С, 45…55 % фракций, перегоняющихся до 300…350 °С.
Известны месторождения легких нефтей с высоким содержанием светлых (до 350 °С). Так, самотлорская нефть содержит 58 % светлых, а в нефти месторождения Серия (Индонезия) их содержание достигает 77 %. Газовые конденсаты Оренбургского и Карачаганакского месторождений почти полностью (85…90 %) состоят из светлых.
Добываются также очень тяжелые нефти, в основном состоящие из высококипящих фракций. Например, в нефти Ярегского месторождения (Республика Коми), добываемой шахтным способом, отсутствуют фракции, выкипающие до 180 °С, а выход светлых составляет всего 18,8 %.
Подробные данные о фракционном составе нефтей бывшего СССР имеются в четырехтомном справочнике «Нефти СССР».
Светлые нефтепродукты,
Бензины
Бензины — легковоспламеняющиеся бесцветные или слегка желтоватые жидкости, представляют собой смесь нефтепродуктов с интервалом кипения от 40 до 200°С. Интересно, что слово «бензин» происходит от арабского словосочетания, означающего «яванское благовоние». Так называли смолу дерева стиракс, известную также как «росный ладан». Позднее из нее стали производить кислоту, названную бензойной. В 1833 году немецкий химик Эйльхард Мичерлих получил из этой кислоты простейшее ароматическое соединение бензол и назвал его benzin. В некоторых языках это название закрепилось за классом легких нефтепродуктов, в состав которых входят ароматические соединения, в том числе бензол.
Составляющие бензина — продукты многих процессов на НПЗ (см. врезы о различных процессах): первичной перегонки (прямогонные бензиновые фракции) и вторичных процессов переработки — крекинга, риформинга, алкилирования, изомеризации, полимеризации, пиролиза и висбрекинга. Также в состав бензина могут входить кислородсодержащие органические соединения (оксигенаты) — спирты, эфиры и другие компоненты.
ОСНОВНЫЕ ХАРАКТЕРИСТИКИ
Важнейшая характеристика бензина — октановое число, которое определяет его детонационную стойкость, то есть способность противостоять самовоспламенению при сжатии. Детонация — нежелательное явление в бензиновом двигателе. Оно возникает, когда часть топлива в цилиндре загорается еще до того, как его достигнет пламя от свечи зажигания, и сгорает быстрее, чем требуется. В результате мощность двигателя снижается, он перегревается и быстрее изнашивается. О детонации свидетельствует характерный стук в моторе. В современных двигателях степень сжатия поршня в цилиндре высока — это дает и большую мощность, и увеличение КПД, а значит, бензины с высокой детонационной стойкостью всё востребованнее.
Октановое число — условный показатель. Его оценивают, сравнивая детонационную стойкость бензина с модельной смесью двух веществ — изооктана и н-гептана. Сам показатель соответствует процентному содержанию в этой смеси изооктана (один из изомеров октана – 2,2,4,-триметилпентан), который с трудом самовоспламеняется даже при высоких степенях сжатия. Его октановое число принято за 100. Н-гептан, напротив, детонирует даже при небольшом сжатии. Его октановое число — 0. Если октановое число бензина равно 95, это означает, что он детонирует, как смесь 95% изооктана и 5% гептана.
Углеводороды, которые содержатся в топливах, значительно различаются по детонационной стойкости: наибольшее октановое число имеют ароматические углеводороды и парафиновые углеводороды разветвленного строения (изоалканы), наименьшее октановое число у парафиновых углеводородов нормального строения. Последние в подавляющем большинстве содержатся в прямогонных бензинах, и их октановое число, как правило, не превышает 70.
Ароматические углеводороды образуются в процессе каталитического риформинга, а разветвленные парафины — при каталитическом крекинге. Именно эти два процесса в XX веке стали основными процессами вторичной переработки нефти, позволяющими получать бензины с повышенным октановым числом.
Сегодня высокооктановые бензиновые фракции также получают в результате процессов алкилирования, изомеризации и гидрокрекинга, или используя в низкооктановых бензинах разнообразные присадки.
БЕНЗИНОВЫЙ КУПАЖ (КОМПАУНДИРОВАНИЕ)
Вообще, производство бензина, как и любого другого современного высококачественного топлива — это целое искусство. Судите сами: каждый из процессов переработки нефти на НПЗ дает бензины в разном количестве, разного состава (соотношение основных компонентов) и с разным октановым числом. Все эти параметры обусловлены не только характеристиками процессов, но также особенностями технологической схемы каждого конкретного производства и составом исходного сырья. Далее необходимо смешать компоненты так, чтобы на выходе получился продукт с требуемыми параметрами.
Со временем помимо таких характеристик, как октановое число, фракционный состав, химическая стабильность, давление насыщенных паров, все большую роль стали играть экологические показатели. Когда-то, чтобы повысить октановое число бензина, в него добавляли тетраэтилсвинец — такой бензин назывался этилированным. Сегодня использование этой присадки полностью запрещено из-за ее токсичности.
Постепенно росли и требования, ограничивающие содержание в топливе серы. Если в бензине содержатся активные сернистые соединения (сероводород, низшие меркаптаны), они могут вызвать коррозию топливной системы. Неактивные сернистые соединения (тиофены, сульфиды, высшие меркаптаны и др.) не вызывают коррозии, однако при их сгорании образуются оксиды серы (SO2, SO3), которые, в свою очередь, и коррозионный износ двигателя повышают, и на окружающую среду влияют не лучшим образом: кислотные дожди, представляющие собой раствор серной кислоты, — прямое следствие попадания в атмосферу значительного количества серного ангидрида.
Большую опасность для людей представляют и некоторые ароматические соединения, в частности ряд полициклических ароматических углеводородов, а также бензол, который признан сильным канцерогеном. Ограничение содержания ароматики — требование, которое позволяет снизить негативный экологический эффект от использования бензина. Для примера, в бензинах класса «Евро-3» содержание ароматики было ограничено 42%, а последний европейский стандарт «Евро-6» подразумевает уже не более 24% ароматических углеводородов.
Чтобы добиться соответствия бензина экологическим стандартам, сегодня высокооктановый (с октановым числом 100–104) бензин каталитического риформинга (риформат), содержащий много ароматических углеводородов, смешивают с другими фракциями с меньшим октановым числом, полученными в результате изомеризации, каткрекинга или алкилирования. В результате удается получить и высокое октановое число, и приемлемое содержание ароматики.
В настоящее время в России производят автобензины:
— по ГОСТ 2084–77: А-72, А-76, АИ-91, АИ-93 и АИ-95;
— по ГОСТ Р 51105–97: Нормаль-80, Регуляр-91, Премиум-95 и Супер-98 (табл. 1.5);
— по ГОСТ Р 51866 (EN–228): бензин-регуляр и премиальный бензин.
По техническим условиям выпускаются:
– бензины для экспорта А-80, А-92, АИ-96, АИ-98;
– бензины с марганцевыми антидетонаторами Нормаль-80 и Регуляр-91;
– бензины для зарубежных автомобилей Премиум-95 и Супер-98;
– неэтилированные бензины с улучшенными экологическими показателями (с содержанием бензола не более 3 %) АИ-80 эк, АИ-93 эк, АИ-98 и др.
Дизельное топливо
Основная область применения легких газойлей, полученных при атмосферной перегонке нефти, а также с помощью гидрокрекинга, термического или каталитического крекинга и коксования нефтяных остатков, — изготовление дизельного топлива. В его состав входят углеводороды с интервалом кипения 200–350°C. Дизель состоит из более тяжелых углеводородов, чем бензин и керосин, он более вязкий и темный (прозрачен, но имеет желтоватый или коричневатый оттенок). Традиционно дизель использовался в первую очередь как топливо для железнодорожного и водного транспорта, грузового автотранспорта, сельскохозяйственной техники, а также в качестве котельного топлива. Однако позднее приобрел популярность и как топливо для легковых автомобилей благодаря экономичности и надежности дизельных моторов.
В дизельном двигателе горючая смесь воспламеняется не от искрового зажигания, а в результате сжатия. Это значит, что, в отличие от бензинов, для дизельного топлива высокая детонационная стойкость как раз нежелательна. Главный критерий его качества — воспламеняемость, которая выражается цетановым числом. Подобно определению октанового числа бензина его получают, сравнивая исследуемое топливо со смесью цетана (C16H34) и a-метилнафталина (C11H10). Процентное содержание цетана в смеси с аналогичной воспламеняемостью и даст цетановое число. Высокое цетановое число и хорошая воспламеняемость дизельного топлива снижают время запуска двигателя, уровень выбросов и шум. Еще одна важная качественная характеристика дизеля — низкотемпературные свойства, то есть способность не замерзать при низких температурах.
Углеводородный состав дизельной фракции более сложен, чем у более легких дистиллятов: в зависимости от процесса получения здесь можно найти и парафиновые углеводороды (алканы), и ароматику, и олефины, и изопарафины. Каждое из этих веществ обладает своими преимуществами и недостатками с точки зрения применения дизеля.
Например, у алканов отличная воспламеняемость, но плохая устойчивость к низким температурам. Зато олефины прекрасно переносят морозы, но значительно снижают цетановое число. Это обстоятельство в том числе способствует тому, чтобы производить разные сорта дизельного топлива из различных смесей углеводородов с учетом дальнейшего применения. За основу принимают средние дистилляты прямой перегонки — в советские времена их использовали без лишних примесей — это всем известная солярка.
Ценный компонент дизеля — газойль гидрокрекинга, у него высокое цетановое число и малое содержание посторонних примесей. Вообще гидроочистка — обязательный процесс при получении качественного дизеля — в средних и тяжелых дистиллятах скапливается максимальное количество серы и других примесей, бывших в исходном сырье.
В зависимости от условий применения в соответствии с ГОСТ 305–82 установлены следующие марки дизельных топлив (табл. 1.8) для быстроходных дизелей:
Л – (летнее), З – (зимнее) А – (арктическое)
В стандарт введена следующая форма условного обозначения топлив: к марке Л добавляют цифры, соответствующие содержанию серы и температуре вспышки, например, Л-0,2-40; к марке З – содержание серы и температуры застывания, например, З-0,2 минус 35. В условное обозначение марки топлива А входит только содержание серы, например, А-0,4.
По техническим условиям выпускаются дизельные топлива:
– экспортные ДЛЭ, ДЗЭ;
– с депрессорными присадками ДЗП, ДАП;
– экологически чистые и с улучшенными экологическими свойствами (с содержани
|
|
Общие условия выбора системы дренажа: Система дренажа выбирается в зависимости от характера защищаемого...
Опора деревянной одностоечной и способы укрепление угловых опор: Опоры ВЛ - конструкции, предназначенные для поддерживания проводов на необходимой высоте над землей, водой...
Двойное оплодотворение у цветковых растений: Оплодотворение - это процесс слияния мужской и женской половых клеток с образованием зиготы...
Археология об основании Рима: Новые раскопки проясняют и такой острый дискуссионный вопрос, как дата самого возникновения Рима...
© cyberpedia.su 2017-2024 - Не является автором материалов. Исключительное право сохранено за автором текста.
Если вы не хотите, чтобы данный материал был у нас на сайте, перейдите по ссылке: Нарушение авторских прав. Мы поможем в написании вашей работы!