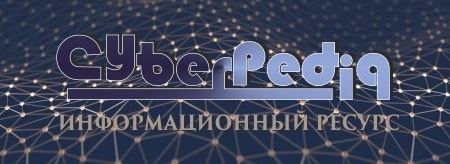
Своеобразие русской архитектуры: Основной материал – дерево – быстрота постройки, но недолговечность и необходимость деления...
Организация стока поверхностных вод: Наибольшее количество влаги на земном шаре испаряется с поверхности морей и океанов (88‰)...
Топ:
Выпускная квалификационная работа: Основная часть ВКР, как правило, состоит из двух-трех глав, каждая из которых, в свою очередь...
Отражение на счетах бухгалтерского учета процесса приобретения: Процесс заготовления представляет систему экономических событий, включающих приобретение организацией у поставщиков сырья...
Комплексной системы оценки состояния охраны труда на производственном объекте (КСОТ-П): Цели и задачи Комплексной системы оценки состояния охраны труда и определению факторов рисков по охране труда...
Интересное:
Искусственное повышение поверхности территории: Варианты искусственного повышения поверхности территории необходимо выбирать на основе анализа следующих характеристик защищаемой территории...
Аура как энергетическое поле: многослойную ауру человека можно представить себе подобным...
Подходы к решению темы фильма: Существует три основных типа исторического фильма, имеющих между собой много общего...
Дисциплины:
![]() |
![]() |
5.00
из
|
Заказать работу |
|
|
Установка предназначена для реформирования бензина и повышения октанового числа.
Установка состоит из следующих блоков:
· Блок гидроочистки
· Блок стабилизации гидрогенизата
· Блок очистки газов и регенерации моноэтаноламина (МЭА)
· Блок риформинга
· Блок стабилизации катализата (риформата)
Описание схемы каталитического риформинга.
Исходное сырье фр.95-180ºС подается насосом на смешение с циркулирующим газом гидроочистки и избыточным водородом риформинга. Полученная газо-сырьевая смесь после нагрева в теплообменнике и печи П1 поступает в реактор гидроочистки P-1. Далее смесь газа и гидроочищенного бензина отдает свою теплоту в кипятильнике, холодильнике и направляется в сепаратор высокого давления гидроочистки С-1, где газ отделяется от гидрогенизата. В водородосодержащем газе присутствует сероводород, выделяющийся при гидроочистке. Из сепаратора газ поступает в колонну К-1, где сероводород отмывается 15% - ным раствором моноэтаноламина.
Очищенный газ разделяется на две неравные части: большая – циркуляционный газ гидроочистки – поступает на прием циркуляционного компрессора 1 и вновь смешивается с сырьем, меньшая – избыточный водород – выводится с установки. Жидкая фаза в сепараторе С-1 содержит гидроочищенный бензин с растворенными в нем сероводородом, углеводородным газом и водой. Поэтому гидрогенизат поступает через теплообменник в отпарную колонну К-2, где происходит отпарка газа, воды и сероводорода от бензина за счет теплоты потока из реактора, подводимого в кипятильник. Стабильный гидрогенизат с низа колонны К-2 проходит теплообменник и направляется на смешение с циркулирующим водородом блока платформинга. Смесь бензина и газа нагревается в теплообменнике и во второй секции печи П-1, а затем последовательно проходит реактор Р-2, третью секцию печи П-1, реактор Р-3, четвертую секцию печи П-1 и реактор Р-4.
|
Продукт риформинга из реактора Р-4 направляется в теплообменник, охлаждается и поступает в сепаратор высокого давления платформинга С-3, где происходит разделение газа и бензина. Газ поступает на прием компрессора,а жидкий продукт из сепаратора С-3 попадает в сепаратор низкого давления С-4, где из платформата выделяется растворенный углеводородный газ гидроочистки и риформинга, смешивается и подается во фракционирующий абсорбер К-4.
Нестабильный бензин из сепаратора С-4 двумя потоками поступает в абсорбер К-4: часть холодного бензина подается на верх абсорбера, другая часть нагревается в теплообменнике и подается в низ абсорбера. С верха абсорбера К-4 уходит сухой углеводородный газ, с низа – бензин в колонну стабилизации К-5 после предварительного нагрева в теплообменнике за счет стабильного бензина. С верха колонны К-5 с установки выводится головка стабилизации, с низа колонны К-5 через теплообменники – стабильный бензин. Подвод теплоты в низ колонн К-4 и К-5 осуществляется методом горячей струи через двухкамерную печь. При полном выделении из бензина этана (режим деэтанизации) в верху колонны К-5 поддерживается 70ºС, при полном удалении пропана (режим депропанизации) – 45ºС. В обоих случаях температура низа колонны 220ºС, давление 11,5 МПа.
См. также файл «Крекинг, риформинг»
Изомеризация
Изомеризация — процесс получения изо-углеводородов, то есть углеводородов с более разветвленными цепочками атомов углерода, из углеводородов нормального строения. Например, если молекула пентана представляет собой цепочку из пяти расположенных друг за другом атомов углерода, то изопентан — это цепочка из четырех атомов углерода с ответвлением, образованным пятым атомом углерода. Изомеризация позволяет повысить октановое число смеси и используется для облагораживания бензина.
|
Стимулом к расширению объема производства бензина-изомеризата, как и других высокооктановых компонентов неароматического содержания, явилось введение жестких ограничений на экологические свойства товарных бензинов, связанные с содержанием ароматических компонентов и давлением насыщенных паров. Этим требованиям в полной мере отвечает бензин-изомеризат.
Наиболее существенным недостатком бензинов риформинга является большое содержание ароматических углеводородов, оказывающих вредное воздействие на состояние окружающей среды. Одним из наиболее рентабельных способов получения высокооктановых бензинов без ароматических компонентов является изомеризация углеводородов фракции н.к.–180оС. Получаемый прирост октанового числа изомеризата по сравнению с сырьем колеблется в пределах 13-15 пунктов в зависимости от содержания изомеров в сырье, а октановое число стабильного изомеризата составляет 84-90 по исследовательскому методу.
Эти обстоятельства приводят к значительному росту числа технологических установок изомеризации в различных странах мира.
Первые промышленные установки изомеризации парафинов появились во время Второй мировой войны и были предназначены для производства высокооктанового компонента авиационных бензинов. В связи с резким падением спроса на авиационный бензин процесс изомеризации в послевоенные годы утратил свое значение, однако интерес к нему возобновился из-за возросших требований к качеству автомобильных бензинов.
На начало ХХI века в мире производилось около 50 млн. т. бензина-изомеризата, из которых на долю России приходилось около 1 млн. т. Ведущими зарубежными фирмами-лицензиарами процесса изомеризации являются «Union Oil Products» (UOP), British Petroleum (BP), Shell, Kellog и др. (табл. 5). Большинство действующих, строящихся и проектируемых установок изомеризации основано на использовании процессов «пенекс» и «ТИП» фирмы UOP. Американская фирма UOP UOP считается мировым, а краснодарское ОАО НПП «Нефтехим» отечественным лидером по разработке установок изомеризации и производству катализаторов для них.
Таблица 5
Процессы изомеризации углеводородных фракций
Показатели | Фирма/процесс | |||
UOP/пенекс | Shell/ хайзомер | UOP/ТИП | ВР/Lsom | |
Температура, оС | 120 – 200 | 260 – 370 | 260 – 370 | 90 – 100 |
Давление, МПа | 2,1 – 7 | 1,4 – 3,5 | 1,4 – 3,5 | 2 – 3 |
Объемная скорость подачи сырья, ч–1 | 1 – 3 | 1 – 3 | 1 – 3 | 1 – 3 |
Катализатор | Pt/Al2O3 | Pt/цеолит | Pt/цеолит | Pt/Al2O3 |
Соотношение Н2/ сырье | 1: (1 – 4) | 1: 4 | 1: 4 | 1: 3 |
Октановое число (ИМ) | ||||
Удельные кап. вложения долл./т | 14,3 | 10,7 | 7,5 | |
Удельные энергозатраты на 1 м3 сырья: электроэнергии, кВт∙ч | 10,6 | 11,9 | 19,5 | 8,17 |
топливо, тыс. ккал | 15,2 | |||
водорода, м3 | - | 13,1 | 17,8 | - |
|
Технология изомеризации пентан-гексановых фракций Изомалк-2 является уникальной российской разработкой НПП «Нефтехим» в области изомеризации легких бензиновых фракций. Особенностью технологии является использование катализатора СИ-2, обеспечивающего протекание процесса в термодинамически выгодной для изомеризации парафиновых углеводородов низкотемпературной области 120-180°C, обладающего повышенной устойчивостью к действию каталитических ядов — воды, серы, азота. В состав катализатора входит платина, нанесенная в количестве 0,25 % масс. на оксид алюминия. Срок службы катализатора 10-12 лет.
Установка Изомалк-2 Омского НПЗ, спроектированная по лицензии «НПП Нефтехим», позволяет получать изопентановую фракцию с октановым числом 92-93 пункта и легкую изогексановую фракцию с октановым числом до 92,5 пунктов по исследовательскому методу. Пуск установки производительностью 800 тыс. т/год состоялся в ноябре 2010 года.
Основной особенностью технологии является выделение С7–фракции и осуществление ее изомеризации на отдельной установке по разработанной ОАО "НПП Нефтехим" технологии.
Гидропроцессы
В гидропроцессах все реакции происходят под действием водорода. Простейший гидропроцесс — гидроочистка. Она применяется для того, чтобы удалить из нефтепродуктов компоненты, содержащие серу, и некоторые другие соединения. Гидроочистке подвергаются бензиновые и керосиновые фракции, дизельное топливо, вакуумный газойль и фракции масел.
Гидрокрекинг — один из видов крекинга, используемый для получения бензина, дизельного и реактивного топлива, смазочных масел, и др. из мазута или гудрона. Одновременно с реакциями крекинга происходит гидроочистка продуктов от соединений серы и насыщение водородом непредельных углеводородов, то есть получение устойчивых соединений.
|
Давления, используемые в современных процессах гидрокрекинга, составляют от примерно 70 атм для превращения сырой нефти в сжиженный нефтяной газ (LP-газ) до более чем 175 атм, когда происходят полное коксование и с высоким выходом превращение парообразной нефти в бензин и реактивное топливо. Процессы проводят с неподвижными слоями (реже в кипящем слое) катализатора. Процесс в кипящем слое применяется исключительно для нефтяных остатков – мазута, гудрона. В других процессах также использовались остаточное топливо, но в основном – высококипящие нефтяные фракции, а кроме того, легкокипящие и среднедистиллятные прямогонные фракции. Катализаторами в этих процессах служат сульфидированные никель-алюминиевые, кобальт-молибден-алюминиевые, вольфрамовые материалы и благородные металлы, такие, как платина и палладий, на алюмосиликатной основе.
В апреле 2015 года «Газпромнефть–ОНПЗ» и новосибирский Институт катализа имени Г.К. Борескова заключили генеральное соглашение о сотрудничестве в области развития технологий производства и применения катализаторов гидроочистки и гидрокрекинга. Министерство энергетики РФ присвоило проекту компании «Газпром нефть» «Катализаторы глубокой переработки нефтяного сырья на основе оксида алюминия» статус национального проекта. Он рассчитан до 2020 года и предполагает создание на Омском НПЗ производства не выпускаемых пока в России катализаторов гидрогенизационных процессов мощностью 6 тыс. тонн в год и катализаторов каткрекинга годовой мощностью 15 тыс. тонн.
Алкилирование
Алкилирование — это процесс, который позволяет получить высокооктановые бензиновые компоненты (алкилат) из непредельных углеводородных газов. В основе процесса лежит реакция соединения алкена и алкана с получением алкана с числом атомов углерода, равным сумме атомов углерода в исходных соединениях. По сути это реакция, обратная крекингу, так как в результате получаются вещества с более длинными цепочками молекул и большей молекулярной массой. Впоследствии алкилат смешивают с низкооктановыми бензиновыми фракциями, получая на выходе облагороженный бензин.
Все процессы алкилирования для производства моторных топлив производятся с использованием в качестве катализаторов либо серной, либо фтороводородной кислоты при температуре сначала 0–15о C, а затем 20–40о С.
Термические процессы
Термические процессы нефтепереработки позволяют получать различные нефтепродукты под воздействием тепла и высокого давления. Первым из таких процессов стал термический крекинг. В настоящее время различные варианты термических процессов (коксование, пиролиз, флексикокинг, висбрекинг) используются в первую очередь для переработки тяжелых фракций нефти и нефтяных остатков.
|
К примеру, коксование позволяет получать из них твердый нефтяной кокс (состоящий преимущественно из углерода), а также низкокипящие углеводороды, которые можно использовать в качестве сырья для других процессов с последующим получением ценных моторных топлив.
Висбрекинг применяют для получения главным образом котельных топлив (топочных мазутов) из гудронов. Флексикокинг предназначен для переработки остатков различных процессов, которые смешиваются с нагретым коксовым порошком и дают на выходе разнообразные компоненты жидких топлив и газ.
Пиролиз
Пиролиз используется для получения углеводородного газа, содержащего такие вещества, как этилен, пропилен и дивинил — сырье для нефтехимической промышленности. Самые важные с точки зрения дальнейшей переработки олефины — этилен (с формулой С2Н4) и пропилен (с формулой С3Н6), а пиролиз — главный процесс для их получения. При этом пропилен может производиться еще и в процессе дегидрирования пропана и на НПЗ в процессе каталитического крекинга. Этилен же — достижение исключительно пиролиза. В нефтянке пиролиз — самый горячий процесс. Он протекает при температурах 700–900°C и давлениях, близких к атмосферному. В результате такой сильной термической обработки молекулы исходного вещества расщепляются на менее длинные — углеводородные цепочки алканов становятся короче, а заодно и теряют в процессе часть молекул водорода. Например, из бутана (С4Н10) получается пропилен (С3Н6) и метан (СН4). Помимо пропилена и этилена, пиролиз позволяет получить ароматические углеводороды.
Дегидрирование
В отличие от пиролиза, где на выходе получаются смеси важнейших олефинов, а сам процесс сложен и очень энергоемок, в ходе дегидрирования алканы* превращаются в индивидуальные олефины. В этом случае в качестве сырья выступают отдельные компоненты сжиженных углеводородных газов, а сам процесс заключается в «отъеме» у них молекулы водорода (Н2).Так, например, из молекулы пропана (С3Н8) получается пропилен (С3Н6), а из бутана (С4Н10) — бутилен (С4Н8). Многокомпонентные продукты пиролиза должны проходить дальнейшее дорогое и сложное фракционирование, в то же время при дегидрировании достаточно отделить целевой олефин от исходного, не вступившего в реакцию алкана и незначительного количества побочных продуктов. Среди недостатков процесса можно отметить высокую стоимость его катализаторов и ограниченный состав сырья, требующего предварительного фракционирования.
Химия и нефть
|
|
Организация стока поверхностных вод: Наибольшее количество влаги на земном шаре испаряется с поверхности морей и океанов (88‰)...
Двойное оплодотворение у цветковых растений: Оплодотворение - это процесс слияния мужской и женской половых клеток с образованием зиготы...
Наброски и зарисовки растений, плодов, цветов: Освоить конструктивное построение структуры дерева через зарисовки отдельных деревьев, группы деревьев...
Автоматическое растормаживание колес: Тормозные устройства колес предназначены для уменьшения длины пробега и улучшения маневрирования ВС при...
© cyberpedia.su 2017-2024 - Не является автором материалов. Исключительное право сохранено за автором текста.
Если вы не хотите, чтобы данный материал был у нас на сайте, перейдите по ссылке: Нарушение авторских прав. Мы поможем в написании вашей работы!