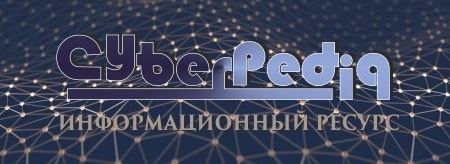
Папиллярные узоры пальцев рук - маркер спортивных способностей: дерматоглифические признаки формируются на 3-5 месяце беременности, не изменяются в течение жизни...
Историки об Елизавете Петровне: Елизавета попала между двумя встречными культурными течениями, воспитывалась среди новых европейских веяний и преданий...
Топ:
Оценка эффективности инструментов коммуникационной политики: Внешние коммуникации - обмен информацией между организацией и её внешней средой...
Характеристика АТП и сварочно-жестяницкого участка: Транспорт в настоящее время является одной из важнейших отраслей народного...
Марксистская теория происхождения государства: По мнению Маркса и Энгельса, в основе развития общества, происходящих в нем изменений лежит...
Интересное:
Подходы к решению темы фильма: Существует три основных типа исторического фильма, имеющих между собой много общего...
Инженерная защита территорий, зданий и сооружений от опасных геологических процессов: Изучение оползневых явлений, оценка устойчивости склонов и проектирование противооползневых сооружений — актуальнейшие задачи, стоящие перед отечественными...
Искусственное повышение поверхности территории: Варианты искусственного повышения поверхности территории необходимо выбирать на основе анализа следующих характеристик защищаемой территории...
Дисциплины:
![]() |
![]() |
5.00
из
|
Заказать работу |
Содержание книги
Поиск на нашем сайте
|
|
ТЕРМИЧЕСКИЙ РЕЖИМ
При нагреве металла с повышением температуры уменьшается его временное сопротивление, а относительное удлинение увеличивается. Таким образом, при деформировании стали, нагретой, например, до температуры 1200 °С, можно достичь большего формоизменения при меньшем приложенном усилии, чем при деформировании ненагретой стали. Все металлы и сплавы имеют тенденций к увеличению пластичности и уменьшению сопротивления деформированию при повышении температуры в случае выполнения ряда требований, предъявляемых к процессу нагрева. Так, каждый металл должен быть нагрет до вполне определенной максимальной температуры. Если нагреть, например, сталь до температуры, близкой к температуре плавления, наступает пережог, выражающийся в появлении хрупкой пленки между зернами металла вследствие окисления их границ. При этом происходит полная потеря пластичности. Пережог исправить нельзя, пережженный металл может быть отправлен только на переплавку.
Ниже температуры пережога находится зона перегрева. Явление перегрева заключается в резком росте размеров зерен. Вследствие того, что крупнозернистой первичной кристаллизации (аустенит), как правило, соответствует крупнозернистая вторичная кристаллизация (феррит + перлит или перлит + цементит), механические свойства изделия, полученного обработкой давлением из перегретой заготовки, оказываются низкими. Брак по перегреву в большинстве случаев можно исправить отжигом. Однако для некоторых сталей (например, хромоникелевых) исправление перегретого металла сопряжено со значительными трудностями, и простой отжиг оказывается недостаточным.
Максимальную температуру нагрева, т. е. температуру начала горячей обработки давлением, следует назначать такой, чтобы не было пережога и перегрева. В процессе обработки нагретый металл обычно остывает, соприкасаясь с более холодным инструментом и окружающей средой. Заканчивать горячую обработку давлением следует также при вполне определенной температуре, ниже которой пластичность вследствие упрочнения (рекристаллизация не успевает произойти) падает и в изделии возможно образование трещин. Но при высоких температурах заканчивать деформирование нецелесообразно (особенно для сплавов, не имеющих фазовых превращений). В этом случае после деформирования зерна успевают вырасти и получается крупнозернистая структура, характеризующаяся низкими механическими свойствами.
|
Каждый металл и сплав имеет свой строго определенный температурный интервал горячей обработки давлением. Например, алюминиевый сплав АЛ4 470—350 °С; медный сплав БрАЖМц 900—750 °С; титановый сплав ВТ8 1100—900 °С. Для углеродистых сталей температурный интервал нагрева можно определить по диаграмме состояния в зависимости от содержания углерода. Например, для стали 45 температурный интервал 1200—750 0С, а для стали У10 1100—850 °С.
Заготовка должна быть равномерно нагрета по всему объему до требуемой температуры. Разность температур по сечению заготовки приводит к тому, что вследствие теплового расширения между более нагретыми поверхностными слоями металла и менее нагретыми внутренними слоями возникают напряжения. Последние тем больше, чем больше разность температур по сечению заготовки, и могут врасти настолько, что в центральной зоне с растягивающими напряжениями при низкой пластичности металла образуются трещины. Разность температур по сечению увеличивается с повышением скорости нагрева, поэтому существует допустимая скорость нагрева. Наибольшее время требуется для нагрева крупных заготовок из высоколегированных сталей из-за их низкой теплопроводности, например, время нагрева слитка массой ~40 т из легированной стали составляет более 24 ч.
|
Однако с увеличением времени нагрева увеличивается окисление поверхности металла, так как при высоких температурах металл активнее химически взаимодействует с кислородом воздуха. В результате на поверхности, например, стальной заготовки образуется окалина – слой, состоящий из оксидов железа: Fе2О3, Fе3О4, FеО. Это приводит к потерям металла с окалиной. Последняя, вдавливаясь в поверхность заготовки при деформировании, вызывает необходимость увеличения припусков на механическую обработку. Окалина увеличивает износ деформирующего инструмента, так как ее твердость значительно больше твердости горячего металла. При высоких температурах на поверхности стальной заготовки интенсивно окисляется не только железо, но и углерод: происходит так называемое обезуглероживание. Толщина обезуглероженного слоя в отдельных случаях достигает 1,5—2 мм. Для уменьшения окисления заготовки нагревают в нейтральной восстановительной атмосфере.
НАГРЕВАТЕЛЬНЫЕ УСТРОЙСТВА
Устройства, в которых нагревают металл перед обработкой давлением, можно подразделить на нагревательные печи и электронагревательные устройства. В печах теплота к заготовке передается конвекцией и излучением из окружающего пространства нагревательной камеры, выложенной огнеупорной облицовкой. Теплоту получают в основном сжиганием газообразного или жидкого топлива (мазута).
По конструктивным признакам печи разделяют на ряд разновидностей. Например, одним из наиболее распространенных типов являются камерные печи (рис. 5), в которых заготовки 2 укладывают на под 1 печи через окно 4 и после прогрева до заданной темпер извлекают через то же окно. Рабочее пространство печи нагревают сжиганием газа с помощью горелок 5, служащих для смешения с воздухом и подачи смеси в печь. Продукты сгорания отводят через дымоход 5 в рекуператор – теплообменник, в котором постующий к горелкам воздух нагревается теплотой горячих уходящих газов. Подогрев воздуха до температуры 350 – 500 °С позволяет экомить до 25 % топлива. Камерные печи периодического действия применяют на производстве, где часто меняется типоразмер нагреваемых заготовок. Для нагрева очень крупных заготовок используют камерные печи с выдвижным подом.
|
![]() | |
Рис. 5. Камерная нагревательная печь | Рис. 6. Схема индуктивного электронагревательного устройства |
В крупносерийном производстве применяют механизированные проходные печи методического действия, в которых заготовки загружают с одной стороны печи, перемещают по поду и выгружают с другой стороны печи нагретыми.
В электронагревательных устройствах теплота выделяется в самой заготовке либо при пропускании через нее тока большой силы – в контактных устройствах, либо при возбуждении в ней вихревых токов – в индукционных устройствах. При индукционном нагреве (рис. 6) заготовку 1 помещают внутрь многовиткового индуктора 2, выполненного из медной трубки прямоугольного сечения. По индуктору пропускают переменный ток, и в заготовке, оказывающейся в переменном электромагнитном поле, возникают вихревые токи. Теплота в нагреваемом металле выделяется в основном вследствие действия вихревых токов в поверхностном слое, толщина которого достигает 30—35 % ее радиуса. Толщина этого слоя уменьшается с ростом частоты тока в индукторе, поэтому для достижения более равномерного нагрева по сечению заготовки с увеличением ее диаметра частоту тока уменьшают (от 8000 Гц для заготовок малых диаметров до 50 Гц для заготовок диаметром до 180 мм). Преимущества электронагрева: высокая скорость, значительно превышающая скорость нагрева в печах; почти полное отсутствие окалины; удобство автоматизации, улучшение условий труда. Однако применяют электронагревательные устройства только при необходимости нагрева достаточно большого количества одинаковых заготовок диаметром до 75 мм в контактных и до 200 мм в индукционных устройствах.
ПРОКАТНОЕ ПРОИЗВОДСТВО
I. СУЩНОСТЬ ПРОЦЕССА
Прокатке подвергают до 90 % всей выплавляемой стали и большую часть цветных металлов. При прокатке металл пластически деформируется вращающимися валками. Взаимное расположение валков и заготовки, форма и число валков могут быть различными. Выделяют три основных вида прокатки: продольную, поперечную и поперечно-винтовую.
При продольной прокатке (рис. 7, а) заготовка 2 деформируется двумя валками 1, вращающимися в разные стороны, и перемещается перпендикулярно к осям валков.
|
При поперечной прокатке (рис. 7, б) валки 1, вращаясь в одном направлении, придают вращение заготовке 2 и деформируют ее. При поперечно-винтовой прокатке (рис. 7, в) валки 1 располагают под углом и сообщают заготовке 2 при деформировании вращательное и поступательное движения.
![]() | ![]() |
Рис. 7. Основные виды прокатки: 1 – валки; 2 — заготовка; 3 — оправка | Рис. 8. Схема действия сил в момент захвата металла валками |
В процессе прокатки металл непрерывно втягивается в зазор валками под действием сил трения между металлом и валками. Для осуществления процесса прокатки необходима определенная величина этих сил трения. Так, при наиболее распространенной продольной прокатке на заготовку со стороны валков действуют нормальные силы N и сила трения Т (рис. 8). Спроектировав эти силы на горизонтальную ось, можно записать условие захвата металла валками (по отношению к одному валку, так как система симметрична):
N sina < Т cosa.
a называется углом захвата.
Вытяжка при прокатке обычно составляет 1,1—1,6 за проход, но может быть и больше.
|
|
Архитектура электронного правительства: Единая архитектура – это методологический подход при создании системы управления государства, который строится...
Адаптации растений и животных к жизни в горах: Большое значение для жизни организмов в горах имеют степень расчленения, крутизна и экспозиционные различия склонов...
Историки об Елизавете Петровне: Елизавета попала между двумя встречными культурными течениями, воспитывалась среди новых европейских веяний и преданий...
Папиллярные узоры пальцев рук - маркер спортивных способностей: дерматоглифические признаки формируются на 3-5 месяце беременности, не изменяются в течение жизни...
© cyberpedia.su 2017-2024 - Не является автором материалов. Исключительное право сохранено за автором текста.
Если вы не хотите, чтобы данный материал был у нас на сайте, перейдите по ссылке: Нарушение авторских прав. Мы поможем в написании вашей работы!