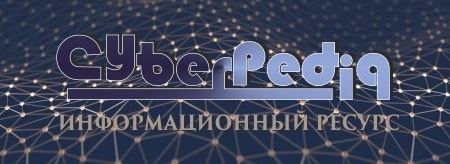
Биохимия спиртового брожения: Основу технологии получения пива составляет спиртовое брожение, - при котором сахар превращается...
Эмиссия газов от очистных сооружений канализации: В последние годы внимание мирового сообщества сосредоточено на экологических проблемах...
Топ:
Оснащения врачебно-сестринской бригады.
Техника безопасности при работе на пароконвектомате: К обслуживанию пароконвектомата допускаются лица, прошедшие технический минимум по эксплуатации оборудования...
Оценка эффективности инструментов коммуникационной политики: Внешние коммуникации - обмен информацией между организацией и её внешней средой...
Интересное:
Подходы к решению темы фильма: Существует три основных типа исторического фильма, имеющих между собой много общего...
Финансовый рынок и его значение в управлении денежными потоками на современном этапе: любому предприятию для расширения производства и увеличения прибыли нужны...
Что нужно делать при лейкемии: Прежде всего, необходимо выяснить, не страдаете ли вы каким-либо душевным недугом...
Дисциплины:
![]() |
![]() |
5.00
из
|
Заказать работу |
|
|
Остаточными напряжениями называют такие внутренние напряжения, которые сохраняются в детали при снятии внешней нагрузки. Различают напряжения I, II и III рода.
Напряжения I рода имеют макроскопический характер, уравновешиваются они в пределах всего объема детали или большей части его. По своему действию напряжения I рода приравниваются к рабочим напряжениям и оказывают благоприятное или вредное влияние на работоспособность детали.
Напряжения II рода представляют собой местные кристаллические напряжения, охватывающие объем одного или нескольких зерен металла (межкристаллические напряжения).
Напряжения III рода уравновешиваются в пределах субмикроскопических объемов данного зерна, т.е. охватывают объем нескольких кристаллических ячеек.
Наиболее интересными с точки зрения долговечности детали, т.е. с точки зрения влияния состояния поверхностного слоя детали на долговечность, являются напряжения I рода, которые и рассмотрим подробнее.
Напряжения I рода могут быть технологическими и конструкционными. Конструкционные – при клепке, сборке. Технологические – от литья, ковки, сварки, резки, механической обработки и т.д. Напряжения I рода делятся на растягивающие (+) и сжимающие (–), кроме того, могут быть тангенциальные и осевые (sт и sо).
С физической точки зрения возникновение напряжений связано с необратимыми изменениями объема металла в зоне деформации, нагрева и т.д.
При пластическом деформировании уменьшается плотность
и возрастает объем поверхностного слоя металла, а поскольку он связан с нижележащими недеформированными слоями металла, то
в процессе обработки в наружном слое будут возникать сжимающие, а в нижележащих – растягивающие остаточные напряжения.
|
Следовательно, одной из причин возникновения остаточных напряжений в поверхностном слое деталей является пластическое деформирование.
Другими причинами возникновения остаточных напряжений могут быть:
– неравномерность пластической деформации поверхностных слоев и формирования в них остаточных напряжений сжатия;
– локализованный нагрев тонких поверхностных слоев в зоне резания и формирование в них остаточных поверхностных напряжений растяжения;
– фазовые превращения различных слоев металла, приводящих
к образованию в них различных структур, обладающих различной плотностью и формирующих в этих слоях неодинаковые остаточные поверхностные напряжения различного знака.
Образование остаточных напряжений от действий силового фактора. Пластическая деформация металла поверхностного слоя приводит к изменению всех его физико-механических свойств, в том числе к уменьшению плотности удельного веса, а следовательно,
к увеличению удельного объема. Увеличение объема металла распространяется только на глубину проникновения пластической деформации и не затрагивает нижележащих слоев. В результате в слое, прилегающем к поверхности, возникают сжимающие напряжения, а в нижележащих – напряжения растяжения.
Иначе это можно объяснить так: резец режет, поверхностные слои растягиваются настолько, что деформируются, а нижележащие слои упруго деформированы. После снятия нагрузки напряжения в упруго растянутой зоне будут стремиться сняться, но их снятию препятствуют пластически растянутые поверхностные слои; в результате внутренние слои частично упруго растянуты, а внешние слои упруго сжаты.
Итак, при условии, когда привалирует силовой фактор, в поверхностном слое формируется напряжение сжатия, а в нижележащих слоях – уравновешивающие их остаточные напряжения растяжения (рис. 120).
Влияние температуры резания на образование остаточных напряжений. Выделяющееся в зоне резания тепло мгновенно нагревает тонкие поверхностные слои металла до высоких температур. Металл в верхних нагретых слоях, стремясь к увеличению своего объема, встречает противодействие со стороны окружающего
металла нижележащих слоев, это приводит к образованию напряжений сжатия. При охлаждении объем верхних нагретых слоев
металла стремится уменьшиться, однако сжатию препятствуют нижележащие слои холодного металла. Вследствие этого под воздействием тепла, выделяющегося в зоне резания, в поверхностном слое образуются остаточные напряжения растяжения, а в нижнем –
сжатия. Однако следует отметить, что формирование растягивающих напряжений под действием температуры может быть только
в том случае, если внутренние напряжения, возникающие при нагреве, превзойдут по своей величине предел текучести данного материала.
|
Методы определения остаточных напряжений. Остаточные напряжения определяют в основном двумя методами: механическим и рентгеноструктурным. Оба метода имеют свои достоинства и недостатки.
Преимущества рентгеноструктрного метода – объективность, отсутствие посторонних факторов, воздействующих на образец
в процессе измерения, возможность определения напряжений без разрушения детали. Однако точность метода низкая и составляет 50 %.
Основным преимуществом механического метода является возможность быстрого получения более точного эпюра остаточных напряжений по глубине поверхностного слоя.Недостаток метода – требуется вырезка образцов из готовой детали, т.е. метод дорогой
и разрушающий.
Существует еще несколько методов определения остаточных напряжений, например метод Давиденкова и метод Закса.
Измерение величины и характера распределения остаточных напряжений по глубине поверхностного слоя проводятся на вырезанных из деталей прямоугольных образцах (рис. 121) с помощью прибора ПИОН-2 при травлении поверхностного слоя по методу Н.Н. Давиденкова. Процесс определения остаточных напряжений механическим методом состоит из следующих этапов:
– вырезка, подготовка и крепление образца;
– электрохимическое травление;
– определение глубины залегания искомых остаточных напряжений с помощью регистрации деформации в процессе травления;
– расчет и построение эпюра остаточных напряжений.
|
Образцы вырезаются таким способом, чтобы операция вырезки не внесла дополнительных остаточных напряжений (электроискровой метод, вырезка шлифовальным кругом с большим охлаждением и малой подачей). Образцы для определения величины остаточных напряжений вырезаются электроэрозионным методом, например, из ободов дисков турбин (рис. 122).
![]() |
Рис. 121. Схема установки образца в прибор ПИОН-2 для определения остаточных напряже-
ний по методу Н.Н. Давиденкова
Образец помещается в установку АПООН. Перед помещением
в установку на нижнюю поверхность образца наносят мастику для того, чтобы на этой поверхности не происходило деформаций. Затем образец зажимается по краям (см. рис. 121).
Исследуется верхняя обработанная поверхность образца. Образец помещается в электролит, а на обработанную поверхность устанавливается индикатор.
Снятие слоев материала происходит чаще путем электролитического травления. Состав электролита и режимы травления (напряжения, плотность тока, температура) подбираются из условия равномерного снятия металла, недопущения точечного разрушения поверхности и растравливания границ зерен. Напряжения изменяются от 2 до 30 В, плотность тока 10…30 амп/дм2, температура электролита 20…60 °С. При травлении образец может деформироваться – сжиматься или растягиваться.
Запись прогиба образца осуществляется через индуктивный датчик. Эта запись передается на самописец, и на нем фиксируется зависимость прогиба от времени. Затем замеряется деформация по диаграмме снятия определенного слоя металла.
Напряжения подсчитываются по формуле:
s = s1 + s2 + s3,
где s1 – напряжение, снимаемое при вырезке образца;
s2 – напряжение, существующее в слое;
s3 – напряжение, возникающее в результате удаления слоя.
После проведения всех необходимых расчетов (автоматических) строится зависимость остаточных напряжений от глубины.
5.3. Зависимость параметров качества
поверхностного слоя от условий обработки
5.3.1. Влияние условий обработки
на шероховатость поверхности
Влияние скорости резания на шероховатость. Известно, что при работе на низких скоростях резания (первая зона скоростей), при которых нарост не образуется, получается (образуется) довольно хорошая чистота поверхности, т.е. меньшая шероховатость обработанной поверхности (рис. 123). При повышении скорости резания (II зона)
|
Рис. 123. Влияние скорости резания на усадку
стружки и шероховатость поверхности
до V =20...30 м/мин создаются условия для развитого и устойчивого нароста, который, выступая впереди лезвия и ниже линии среза, ухудшает шероховатость поверхности. Дальнейшее увеличение скорости резания (III зона) приводит к уменьшению наростообразования и высоты неровностей обработанной поверхности. За пределами наростообразования высота неровностей принимает наименьшее значение. Дальнейшее увеличение скорости резания, по данным многих исследователей, не оказывает существенного влияния на шероховатость. В связи с этим А.И. Исаевым введено понятие «граничной» скорости резания V гран,а А.Н. Ереминым – понятие скорости зеркальной V зерк,после которой поверхность приобретает зеркальный блеск.
Рис. 124. Влияние скорости резания V на шероховатость протянутой поверхности Ra различных сталей и сплавов с подачей 0,02
и 0,1 мм/зуб
ВЖЛ-14
ВТ3-1
ЭИ787-ВД
ЭП517Ш
ЭП517Ш (0,1 мм/зуб )
Вместе с тем экспериментальные данные многих исследователей показывают, что кривые Rz = f (V),выражающие зависимость
высоты неровностей от скорости резания при обработке различных материалов инструментами, оснащенными различными марками твердого сплава, во многих случаях имеют характерные точки минимума. Например, при протягивании различных материалов есть две зоны скоростей резания (рис. 124) – зона неблагоприятных скоростей от 0,5 м/мин до 12 м/мин и зона благоприятных скоростей резания от 25 м/мин и выше.
Характерным является то, что точки минимума шероховатости совпадают с минимальной интенсивностью износа инструмента. Это показывает, что между интенсивностью износа инструмента, трением и шероховатостью существует тесная взаимосвязь. Установлено, что скорости V гран и V зерк совпадают с оптимальными скоростями V o как по интенсивности износа, так и по шероховатости (рис. 125).
Влияние подачи на шероховатость обработанной поверхности. Подача является важным элементом режима резания, влияющим на производительность процесса обработки. При чистовой обработке повышение подачи чаще ограничивается требуемой низкой шероховатостью обработанной поверхности.
С повышением подачи при сохранении постоянства оптимальной температуры Т о усадка стружки снижается, также снижается величина оптимального поверхностного износа h о.п.о и скорость размерного износа V.
Понижение (уменьшение) величин h о.п.о и V при увеличении подачи может уменьшить высоту неровностей. Снижение же усадки стружки повышает высоту неровностей (см. рис. 124, сталь ЭП517Ш, подачи 0,02 и 0,1 мм/зуб). Следовательно, на характер зависимости
Rz = f (S)будет влиять сумма всех факторов.
|
Влияние глубины резания на шероховатость. Глубина резания как геометрический фактор не может изменить профиль и высоту неровностей обработанной поверхности. Глубина резания влияет на высоту неровностей при изменении температуры резания, условий наростообразования, деформации срезаемого слоя и т.д. Но так как глубина резания слабо влияет на температуру резания, усадку стружки и геометрические параметры нароста, то высота неровностей изменяется незначительно. Указанное заключение справедливо при работе резцами с углом при вершине e > 90°.
При работе же резцом с e < 90° изменение глубины может существенно влиять на высоту неровностей Н,что связано с изменением отношения ширины срезаемого слоя к его толщине.
Как правило, глубина резания, оптимальная по шероховатости, оптимальна и по интенсивности износа инструмента.
Влияние свойств обрабатываемого и инструментального
материалов на шероховатость. Обрабатываемый материал, его физико-механические свойства и структура оказывают существенное влияние на характер и высоту неровностей обработанной поверхности. Влияние это осуществляется через следующие факторы процесса резания: интенсивность деформаций, трение на поверхностях контакта, наростообразование, вибрации, износ и т.д.
Более вязкие и пластичные металлы (материалы), склонные к пластическим деформациям, дают при их обработке грубые и шероховатые поверхности. С увеличением твердости обрабатываемого материала, его ударной вязкости высота шероховатости снижается (рис. 126).
Следует отметить, что для каждой твердости и структуры существует своя критическая скорость резания, при которой получается хорошая чистота обработанной поверхности.
Различные инструментальные материалы при одной и той же геометрии инструмента и тех же режимах резания могут дать обработанные поверхности с различной шероховатостью. Это объясняется различием в силах адгезионного взаимодействия и условиях трения на поверхностях контакта и разной способностью различных инструментальных материалов сохранять режущую кромку.
Исследования показывают, что инструментальные материалы, имеющие меньшую величину относительного износа, дают и меньшую высоту неровностей обработанной поверхности (рис. 127).
Влияние марки инструментального материала на Rz необходимо установить при оптимальных для каждого сплава скоростях, а не при произвольно выбранных.
5.3.2. Влияние условий обработки
на наклеп поверхности
Влияние скорости резания на характеристики наклепа. Влияние скорости резания на наклеп поверхностного слоя сложное там, где скорость резания может выступать в качестве различных факторов.
1. Скорость резания как фактор, определяющий скорость пластической деформации поверхностного слоя. С повышением скорости деформации, как известно, происходит рост предела прочности
и предела текучести конструкционных материалов. Повышение предела текучести снижает пластичность обрабатываемого материала
и действует в сторону уменьшения наклепа. Это можно видеть при анализе графиков зависимости изменений глубины и степени наклепа от скорости резания при протягивании различных жаропрочных сплавов (рис. 128).
Рис. 128. Влияние скорости протягивания V хвостовиков лопаток и пазов в кольцах направляющих аппаратов из жаропрочных никелевых сплавов на глубину h и степень наклепа h про-
тянутой поверхности
H ЭИ787-ВД;
H ВЖ102;
HВЖЛ14;
h ВЖЛ14;
h ЭИ787;
h ВЖ102
2. Скорость резания влияет на продолжительность контакта задней поверхности инструмента с обрабатываемой деталью. При большой скорости резания деталь проходит через зону контакта, не получив того наклепа, который она могла бы получить при малой скорости резания и более продолжительном контакте.
3. Скорость резания изменяет удельные контактные нагрузки
и коэффициент трения на задней поверхности инструмента. Повышение их будет способствовать увеличению наклепа.
4. Скорость резания изменяет ширину пластической зоны (зона стружкообразования) и положение ее начальной границы. При повышении скорости резания до некоторой величины происходит сужение пластической зоны и уменьшение глубины ее распространения ниже линии среза, что уменьшает наклеп.
5. Скорость резания как температурный фактор, изменяющий степень развития нароста. Нарост может увеличивать действительный радиус округления режущей кромки и тем самым способствовать повышению наклепа.
6. Скорость резания как температурный фактор влияет на интенсивность процесса разупрочнения. Повышение температуры резания способствует повышению интенсивности процесса разупрочнения и уменьшению наклепа.
7. Скорость резания способствует процессу самозакаливания поверхностного слоя и наклепу при фазовых превращениях вследствие нагрева поверхностного слоя.
8. Скорость резания изменяет температуру поверхностного слоя и характеристики пластичности материала детали при этих температурах. При обработке материалов резанием повышение температуры контакта до температуры, соответствующей максимальному охрупчиванию, будет способствовать снижению наклепа, а при дальнейшем повышении температуры наклеп увеличивается, так как пластичность в этом случае возрастает. Анализ причин, изменяющих наклеп, позволяет заключить, что зависимости h н = f (V)
и Н = f (V)должны носить экстремальный характер. Наименьшие глубина и степень наклепа наблюдаются в области оптимальных по интенсивности износа инструмента скоростей резания (рис. 129). Глубина и степень наклепа определяются средней температурой контакта, а скорость резания и подача выступают главным образом как температурные факторы. При работе на постоянной скорости резания и переменной подаче зависимости h н = f (S) и Н= f (S)могут иметь различный характер, определяемый температурой в зоне резания.
Например, при работе на сравнительно низкой скорости резания,когда при увеличении подачи температура резания повышается и приближается к оптимальному значению qо, глубина и степень наклепа снижаются. При работе на средней скорости резания зависимости h н = f (S) и Н = f (S)носят экстремальный характер.
Это объясняется тем, что при повышении подачи температура переходит через оптимальное значение. Для высоких скоростей резания, когда при повышении подачи температура резания все дальше отклоняется от оптимального значения, глубина и степень наклепа монотонно повышаются(см. рис. 129).
Влияние геометрии инструмента на наклеп. На условия стружкообразования в основном влияет передний угол g. При изменении g от +15 до –15° глубина наклепа h н увеличивается значительно (для ЭИ487-БУ – в 3 раза), что связано с изменением положения начальной зоны стружкообразования (пластической зоны), повышением относительного сдвига и другими факторами.
Увеличение радиуса округления режущего лезвия r повышает наклеп поверхностного слоя при всех подачах, особенно когда r больше толщины среза. Существенно оказывает влияние на наклеп
и износ резца по задней поверхности – через изменение силового фактора, повышение продолжительности пластического деформирования каждого участка обработанной поверхности и изменение температуры в зоне контакта. Фаски износа оказывают наибольшее влияние на наклеп при работе на скоростях ниже и выше оптимальных.
Главный угол в плане j и радиус резца при вершине R оказывают влияние на наклеп как фактор, изменяющий толщину среза, со всеми последствиями.
Влияние обрабатываемого и инструментального материала на наклеп. Стали и сплавы, обладая различными прочностными
и пластическими свойствами, по-разному упрочняются (наклепываются) при механической обработке. При этом более пластичные
и более упрочняемые при деформации материалы, как правило, при механической обработке имеют и больший наклеп.
Значительное влияние на характеристики наклепа оказывает
и инструментальный материал через коэффициент трения на задней поверхности. Тот инструментальный материал, который дает более высокий коэффициент трения по задней поверхности, наиболее интенсивно изнашивается, приводит к формированию большего наклепа поверхности как по глубине, так и по степени. Путем правильного выбора соответствующей марки инструментального материала можно в некоторых пределах регулировать не только стойкость инструмента, но и качество обработанной поверхности.
5.3.3. Влияние условий обработки
на остаточные напряжения
Влияние элементов режима резания. Влияние скорости резания на остаточные напряжения следует рассматривать как влияние комплексного параметра, определяющего процесс резания. С ростом V резания повышается qрезания, что должно приводить к уменьшению сжимающих напряжений и увеличению напряжений растяжения. Другие физические явления, происходящие в зоне резания, также проявляются тем или иным образом в зависимости от температуры.
Снижение силового фактора при повышении скорости резания до определенного значения происходит в результате сужения пластической зоны и уменьшения глубины ее распространения ниже линии среза. Кроме того, с увеличением скорости резания происходит снижение s b (s b выступает в данном случае как силовой фактор). Все это способствует возникновению напряжений растяжения, что и наблюдается в действительности.
Необходимо отметить, однако, что действие большинства из указанных факторов на определенной скорости резания ослабевает (или совсем прекращается); в этот момент начинают действовать другие факторы, которые могут способствовать снижению напряжений.
Таким образом, анализ причин, приводящих к образованию
и изменению остаточных поверхностных напряжений при изменении V в достаточно широких пределах, позволяет заключить (применительно к пластичным материалам), что:
– в слое, прилегающем к поверхности, должны формироваться тангенциальные напряжения растяжения;
– зависимость максимальной величины smax от скорости резания должна иметь характерную точку перегиба или носить экстремальный характер.
Экспериментальные исследования остаточных напряжений полностью подтверждают это предположение. Например, при протягивании жаропрочных сплавов ЭИ787-ВД и ВЖЛ14 величина максимальных остаточных напряжений имеет переменную характеристику с минимальными значениями в области оптимальных скоростей резания 15…20 м/мин для этих сплавов (рис. 130).
![]() |
Рис. 130. Влияние скорости протягивания V хвостовиков лопаток и пазов
в кольцах направляющих аппаратов из жаропрочных никелевых сплавов на
глубину h и степень наклепа Hпротянутой поверхности
ЭИ787-ВД, острые протяжки;
ЭИ787-ВД, затупленные протяжки;
ВЖЛ14, острые протяжки;
ВЖЛ14, затупленные протяжки
Когда главным образом действует силовой фактор, то возникают сжимающие напряжения, и чем больше подача, тем при меньших V онаблюдается перегиб (рис. 131). Характер зависимости smax = = f (S)определяется уровнем скорости (температуры) резания (рис. 132). При резании на низкой скорости V о1повышение подачи приводит к увеличению объема и интенсивности пластической деформации и повышению температуры; причем последняя приближается к своему оптимальному значению.
![]() ![]() | |
Рис. 131. Влияние скорости резания на шероховатость Rz, коэффициент трения m¢ и остаточные поверхност- ные напряжения smax | Рис. 132. Влияние скорости резания на smax при обработке на разных подачах S |
В этом случае повышение подачи приводит к росту остаточных тангенциальных напряжений растяжения. Снижение коэффициента трения на задней поверхности инструмента m¢ уменьшает действие силового фактора и также способствует росту напряжений растяжения.
При работе на средней скорости резания V о2зависимость
smax= f (S)носит экстремальный характер. Экстремальный характер функции smax= f (S)может быть объяснен переходом температуры резания через оптимальное значение. Снижению максимальной величины остаточных напряжений после некоторого значения подачи может способствовать повышение коэффициента трения по задней поверхности m', т.е. повышение действия силового фактора.
Для высокой скорости резания V о3с увеличением подачи происходит монотонное снижение тангенциальных растягивающих напряжений (рис. 133). Это может быть вызвано возрастающим действием силового фактора вследствие повышения m'.Кроме того, при высоких скоростях резания ослабевает действие температурного фактора.
В заключение следует отметить, что между высотой микронеровностей обработанной поверхности, глубиной
и степенью наклепа, остаточными напряжениями, контактными явлениями в зоне резания и интенсивностью износа инструмента при резании наблюдается тесная взаимосвязь. Все перечисленные характеристики имеют характерную точку перегиба или носят экстремальный характер. Экстремальные (или критические) точки кривых находятся в области оптимальных скоростей резания.
Главным фактором, определяющим коэффициент трения по задней поверхности резца, параметры наклепанного слоя остаточного напряжения и интенсивность износа инструмента, является средняя температура контакта, а скорость резания выступает в основном как температурный фактор.
5.4. Влияние качества поверхностного слоя
на эксплуатационные свойства деталей
Установлено, что в результате приработки на трущихся поверхностях образуется оптимальная шероховатость, характерная для данных конкретных условий работы соединения. Поэтому если в процессе обработки деталей на поверхности обеспечить шероховатость, близкую к оптимальной, то время приработки на износ будет наименьшим. Оптимальная по износостойкости шероховатость поверхности зависит от вида соединений и конкретных условий эксплуатации.
На износ деталей оказывают влияние не только высота, но и направление неровностей исходной шероховатости трущихся поверхностей. Шероховатость поверхности оказывает существенное влияние на усталостную прочность деталей и коррозионную стойкость.
С уменьшением шероховатости поверхности коррозионная стойкость деталей повышается.
Установлено, что наклеп поверхностного металла, созданный специальными технологическими приемами или полученный в результате механической обработки, приводит к увеличению контактной жесткости и контактной выносливости. Кроме того, наклепанный поверхностный слой деталей уменьшает интенсивность проявления всевозможных геометрических и структурных концентраторов напряжений в поверхностных слоях, повышая тем самым усталостную прочность деталей. Вместе с тем наклеп поверхностного слоя деталей после механической обработки понижает в большинстве случаев коррозионную стойкость деталей.
Наиболее заметно влияние остаточных напряжений в поверхностном слое на усталостную прочность деталей. При этом сжимающие напряжения повышают предел выносливости, а растягивающие –уменьшают его. Имеются данные о том, что сжимающие остаточные напряжения в поверхностных слоях детали повышают прочность
и надежность соединений с натягом, поэтому необходимо стремиться, чтобы в поверхностном слое формировались сжимающие напряжения возможно большей величины.
При обработке деталей в результате действия высоких температур в поверхностном слое могут происходить структурные изменения, которые приводят к вторичной закалке и образованию
поверхностного слоя повышенной твердости по сравнению с основной структурой металла. При обработке закаленных металлов
в поверхностном слое может происходить отпуск различной
степени.
5.5. Особенности образования поверхности
при чистовой лезвийной и абразивной обработке
Чистовая лезвийная обработка деталей машин проводится на таких операциях окончательной обработки, как чистовое точение, чистовое фрезерование, зенкерование и развертывание отверстий, протягивание наружных и внутренних поверхностей. Основная задача чистовой обработки – обеспечить заданное качество поверхностного слоя и заданную точность поверхности. В качестве режущих инструментов применяются лезвийные инструменты с доведенными режущими гранями и кромками. Припуски на обработку обычно составляют 0,2…0,5 мм. Требуется обеспечить шероховатость обработанной поверхности по Ra не более 2 мкм, а точность в пределах 0,02…0,1 мм.
Для этого применяют специальные прецизионные станки, приспособления и инструменты. Обработку ведут на повышенных скоростях резания, минимальных подачах с оптимальной геометрией инструмента.
Чистовая абразивная обработка проводится с помощью различных видов абразивного инструмента методами шлифования, полирования, доводки, притирки, обдувки и т.п. Припуски на обработку составляют 0,05…0,2 мм. При этом шероховатость поверхности может достигать величины по Ra в пределах 0,05…1,25 мкм
Особенности процессов отделения срезаемого слоя металла при чистовой лезвийной обработке рассмотрены нами в предыдущих главах, поэтому далее рассмотрим процессы абразивной обработки.
5.5.1. Понятие об абразивном инструменте.
Характеристики абразивного инструмента
Шлифование представляет собой операцию обработки поверхности заготовки абразивным инструментом.
Под абразивными понимаются материалы естественного или искусственного происхождения, зерна которых обладают высокой твердостью и способностью резания. Абразивные инструменты могут быть изготовлены со связанными зернами (шлифовальные круги, головки, сегменты, бруски, шкурки) и в виде несвязанных, свободных зерен (пасты, суспензии, порошки). Абразивные инструменты характеризуются материалом зерен и их величиной, видом связки, твердостью, структурой, формой и размерами.
Алмазные круги и бруски дополнительно характеризуются конструкцией и маркой алмазов.
Абразивные материалы и инструменты. Абразивные материалы делятся на искусственные (синтетические) и естественные (природные). Более широкое применение в промышленности в настоящее время имеют искусственные абразивные материалы: электрокорунд, карбид кремния (карборунд), карбид бора, синтетические алмазы, кубический нитрид бора (эльбор).
Связующие вещества (связки): неорганические (керамическая, магнезиальная и силикатная); органические (бакелитовая, глифталиевая, вулканитовая); металлические (порошки меди, алюминия, олова и др.).
Электрокорунд (А12О3). Большая часть (~ 80 %) абразивного инструмента изготавливается из электрокорунда, который получают путем плавки глинозема в электрических печах. Существует несколько разновидностей электрокорунда:
– Э – электрокорунд нормальный (91…99 % А12О3) (марки: 16А, 15А, 14А, 13А, 12А);
– ЭБ – электрокорунд белый (97…99 % А12О3) (марки: 25А, 24А, 23А, 22А);
– ЭХ – электрокорунд хромистый (марки: 34А, 33А, 32А);
– ЭТ – электрокорунд титанистый – 37А (содержит» 97 % А12О3 и 2 % ТiO2);
– М – монокорунд, зерна которого представляют отдельные кристаллы и имеют большое число режущих граней (марки: 45А, 44А).
Титанистый электрокорунд представляет собой соединения А12О3 + 1,5 % ТiO2, отличается от нормального электрокорунда большей вязкостью и стабильностью свойств, что хорошо для доводочно-притирочных работ.
Монокорунд –разновидность электрокорунда. Он получается из боксита оксисульфидным способом в виде зерен, состоящих из изометрических кристаллов корунда различной величины. Сущность способа получения монокорунда состоит в сплавлении боксита с сернистым железом и восстановителем – антрацитом или коксом –
в электропечах.
Зерна электрокорунда ЭХ, ЭТ и М имеют более высокие режущие свойства, чем Э и ЭБ.
Карбид кремния (SiС) – химическое соединение кремния с углеродом, получается при плавке кварцевого песка и кокса. Зерна SiС имеют более высокую твердость, чем электрокорунд. Применяются две разновидности карбида кремния: черный КЧ (95…97 % SiС) марок 55С, 54С, 53С, 52С и зеленый КЗ (98…99 % SiС) марок 64С, 63С, 62С. Недостаток карбида кремния – высокая хрупкость и малая прочность. Поэтому при обработке сталей он почти не применяется. Карбид кремния применяется при абразивной обработке хрупких материалов: чугунов, бронзы; тугоплавких сплавов, металло- и минералокерамики.
Карбид бора (В4С) – химическое соединение бора с углеро-
дом – получают плавлением борной кислоты В2О2 с нефтяным коксом при температуре 2000...2350 °С. Карбид бора имеет высокую твердость, большую хрупкость и применяется в виде порошков для доводочных процессов и при ультразвуковой обработке хрупких материалов.
Борсиликарбид в отличие от карбида бора не содержит вредной примеси графита, отличается большей стабильностью свойств, более прочен и дешевле. На операциях доводки показал на 30…40 % более высокую производительность, чем карбид бора.
Окись хрома –порошок темно-зеленого цвета для доводки. Получается из бихромата калия с примесью серы.
Окись железа (крокус) – тонкий полировальный порошок, состоящий в основном из кристаллической окиси железа. Получается переработкой железного купороса и щавелевой кислоты.
Синтетические алмазы (АС) получают в виде мелких кристаллов, размеры обычно не более 1 мм. Синтез алмазов происходит в результате воздействия на графит высоких давлений (до 1,7·10 кгс/см2) и высоких температур (до 2500 °С). В присутствии металлического катализатора происходит перекристаллизация углерода из гексагональной структуры графита в кубическую структуру алмаза. Синтетические алмазы в зависимости от прочности делятся на пять марок: низкой прочности (АСО), повышенной прочности (АСР), высокой прочности (АСВ), монокристальные (АСК и АСС).
Кубический нитридбора (КНБ, боразон или эльбор) состоит из 44 % бора и 56 % азота; твердость его уступает лишь алмазу, а теплостойкость в 2 раза выше алмаза. Круги из эльбора наиболее эффективны при чистовом шлифовании, заточке и доводке инструментов из быстрорежущих сталей повышенной производительности (кобальтовых и высокованадиевых).
К естественным материалам относятся кварц (кремнезем SiО2), наждак, корунд и алмаз. Природные абразивные материалы, за исключением алмаза, имеют низкие режущие свойства и для абразивной обработки металлов почти не применяются.
Природный алмаз А – минерал, состоящий из кристаллического углерода. Природные технические алмазы содержат небольшие примеси окислов алюминия, железа, кальция, кремния, марганца, которые придают им различный цвет. Атомы углерода в кристаллической решетке алмаза очень прочно связаны, что обеспе
|
|
Семя – орган полового размножения и расселения растений: наружи у семян имеется плотный покров – кожура...
Адаптации растений и животных к жизни в горах: Большое значение для жизни организмов в горах имеют степень расчленения, крутизна и экспозиционные различия склонов...
Эмиссия газов от очистных сооружений канализации: В последние годы внимание мирового сообщества сосредоточено на экологических проблемах...
Своеобразие русской архитектуры: Основной материал – дерево – быстрота постройки, но недолговечность и необходимость деления...
© cyberpedia.su 2017-2024 - Не является автором материалов. Исключительное право сохранено за автором текста.
Если вы не хотите, чтобы данный материал был у нас на сайте, перейдите по ссылке: Нарушение авторских прав. Мы поможем в написании вашей работы!