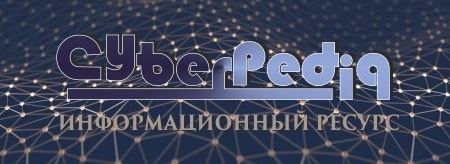
Опора деревянной одностоечной и способы укрепление угловых опор: Опоры ВЛ - конструкции, предназначенные для поддерживания проводов на необходимой высоте над землей, водой...
Наброски и зарисовки растений, плодов, цветов: Освоить конструктивное построение структуры дерева через зарисовки отдельных деревьев, группы деревьев...
Топ:
Когда производится ограждение поезда, остановившегося на перегоне: Во всех случаях немедленно должно быть ограждено место препятствия для движения поездов на смежном пути двухпутного...
Генеалогическое древо Султанов Османской империи: Османские правители, вначале, будучи еще бейлербеями Анатолии, женились на дочерях византийских императоров...
Организация стока поверхностных вод: Наибольшее количество влаги на земном шаре испаряется с поверхности морей и океанов...
Интересное:
Берегоукрепление оползневых склонов: На прибрежных склонах основной причиной развития оползневых процессов является подмыв водами рек естественных склонов...
Лечение прогрессирующих форм рака: Одним из наиболее важных достижений экспериментальной химиотерапии опухолей, начатой в 60-х и реализованной в 70-х годах, является...
Уполаживание и террасирование склонов: Если глубина оврага более 5 м необходимо устройство берм. Варианты использования оврагов для градостроительных целей...
Дисциплины:
![]() |
![]() |
5.00
из
|
Заказать работу |
|
|
Реальная поверхность детали после механической обработки
в отличие от идеальной поверхности, изображенной на чертежах, всегда имеет неровности различной формы и высоты.
Под шероховатостью поверхности понимается совокупность микронеровностей с относительно малыми шагами, образующих рельеф поверхности. В соответствии с ГОСТ 2789–83, шероховатость поверхности характеризуется высотой неровностей Rz или средним арифметическим отклонением Rа, или R max, в мкм.
Значения Rа и Rz шероховатости по ГОСТ 2789–83 приведены
в табл. 16.
Высота и форма неровностей поверхности, расположение
и направление обработочных рисок зависят от принятого метода и режима обработки, геометрии режущего инструмента, свойств обрабатываемого материала, состояния используемого оборудования и т.д.
Для оценки и измерения шероховатости существует целый ряд приборов. Наиболее широкое применение в промышленности и исследовательских организациях получили оптический прибор – двойной микроскоп МИС-11 (МИС-12) конструкции академика ВЛ. Линника – и щуповые – различные модели профилографов-профилометров. Для визуального сравнения существуют эталоны шероховатости для каждого вида обработки резанием.
Таблица 16
Классы и величина шероховатости поверхностей
Класс шероховатости (старый ГОСТ) | Ra, мкм | Rz, мкм | Базовая длина, мм |
– – – | 8,0 | ||
– – | 2,5 | ||
2,5; 2,0; 1,6 | – | – «– | |
1,25; 1,00; 0,80 | – | 0,8 | |
0,63; 0,50; 0,40 | – | – «– | |
0,32; 0,25; 0,20 | – | – «– | |
0,160; 0,125; 0,100 | – | – «– | |
0,080; 0,063; 0,050 | – | 0,25 | |
0,040; 0,032; 0,025 | – | – «– | |
– | 0,100 | – «– | |
– | 0,50 | – «– |
Волнистость поверхности, в отличие от шероховатости, представляет собой совокупность периодически чередующихся выступов и впадин синусоидальной формы, имеющих значительно больший шаг.
|
В общем виде высота неровностей Rz (Rа)при точении может быть определена из следующей зависимости:
Rz = Н р + D Н, мкм,
где Н р – расчетная или теоретическая величина неровностей;
D Н –отклонение фактической высоты неровностей от расчетной.
При этом расчетная величина неровностей при радиусе резца при вершине, равной нулю, может быть определена по формуле
Н р = (S tg j tg j1)/(tg j+ tg j1),
при R, не равном нулю, по формуле
Н р = S 2/8 R.
Суммарная величина отклонений D Н может быть представлена выражением
D Н = D Н пл.деф + D Н упр.деф + D Н тр.зад + D Н нар + D Н вибр + D Нh,
т.е. учитывает влияние пластической D Н пл.деф и упругой D Н упр.деф деформаций, трения задней поверхности инструмента о деталь D Н тр.зад, наростообразование D Н нар, вибрации D Н вибр, износ инструмента D Нh
и т.д.
Необходимо отметить, что пластическая деформация и другие факторы воздействуют на Rz таким же образом, как они действуют на интенсивность износа инструмента при резании. Так, чем выше трение, тем больше интенсивность износа, тем хуже обработанная поверхность и т.д.
Поскольку расчетная высота неровностей Нр находится из чисто геометрических соображений и от других параметров процесса резания не зависит, то изменение шероховатости обработанной поверхности связано с изменением D Н.
На величину D Н (или на Rz)оказывают влияние следующие основные факторы: скорость резания, свойства обрабатываемого материала, свойства инструментального материала, жесткость системы станок–приспособление–инструмент–деталь и др.
5.2.2. Наклеп поверхностного слоя
при резании металлов
Под наклепом металла следует понимать повышение его прочностных свойств и твердости при его пластическом деформировании. Первоначальная пластическая деформация металла, образующего поверхностный слой, протекает в зоне стружкообразования, так как начальная граница этой зоны (линия СЕ), как правило, лежит ниже линии среза (рис. 118). Другой причиной деформации поверхностного слоя (а следовательно, и упрочнения) является то, что резание металлов осуществляется инструментом, лезвие которого всегда имеет некоторый радиус округления r. Для заточенных алмазным кругом резцов радиус r может быть в пределах от 3 до 10 мкм. Для резцов, имеющих износ h з от 0,1 до 0,3 мм, радиус округления составляет 20...60 мкм.
|
Рис. 118. Схема процесса резания с образованием наклепа
глубиной упрочнения H у
При наличии r часть металла выше линии АВ уходит в стружку, а слой металла толщиной Н сжне срезается, а подминается округленной частью резца, подвергаясь упругой и пластической деформации.
Третьей причиной деформации поверхностного слоя является частичное упругое восстановление несрезанного деформированного металла на величину H y. Это приводит к появлению на задней поверхности инструмента нормальных и касательных сил, а следовательно, и к дополнительной пластической деформации поверхностного слоя.
Таким образом, металл, образующий поверхностный слой,
в процессе резания претерпевает неоднократное пластическое деформирование. Это приводит к изменению всех физико-механических свойств и структуры металла. Основными характеристиками наклепа являются: степень наклепа Hи глубина наклепанного слоя h с. Степень наклепа определяется по формуле
H= (H 1 – H)100%/ H,
где H 1 – микротвердость детали непосредственно с поверхности;
Н –микротвердость исходного металла.
Методы определения наклепа. В соответствии с изменениями, происходящими в поверхностном слое, глубина наклепанного слоя определяется или по изменению микротвердости по сечению детали, или рентгеноструктурным методом по изменению характера интерференционных линий на рентгенограммах при послойном стравливании исследуемой поверхности.
Наиболее распространенным методом исследования глубины
и степени наклепа в настоящее время является метод измерения микротвердости. Метод заключается в исследовании микротвердости материала (металла) на участке наклонного микрошлифа (рис. 119),
![]() |
![]() |
б
Рис. 119. Измерение микротвердости образца по глубине поверхностного слоя:
а – схема нагружения; б – следы алмаза;
|
1 – образец
изготовленного на специальном приспособлении. Для измерения глубины и степени наклепа обработанных поверхностей используется микроскоп ПМТ-3 и метод косых шлифов. Для проведения исследований изготовлены специальные косые образцы. Измеряя
на косом срезе отпечатки алмазного наконечника, по формулам
или по таблицам определяют микротвердость образца на разной
глубине.
Между hс и Нсуществует тесная взаимосвязь hс = k ·Н, где K – коэффициент пропорциональности.
Наклеп поверхностного слоя в значительной степени зависит от многих технологических факторов – элементов режима резания, геометрических параметров инструмента и состояния его режущего лезвия, свойств инструментального и обрабатываемого материалов, вида СОЖ и т.д.
|
|
История развития хранилищ для нефти: Первые склады нефти появились в XVII веке. Они представляли собой землянные ямы-амбара глубиной 4…5 м...
Историки об Елизавете Петровне: Елизавета попала между двумя встречными культурными течениями, воспитывалась среди новых европейских веяний и преданий...
Типы сооружений для обработки осадков: Септиками называются сооружения, в которых одновременно происходят осветление сточной жидкости...
Типы оградительных сооружений в морском порту: По расположению оградительных сооружений в плане различают волноломы, обе оконечности...
© cyberpedia.su 2017-2024 - Не является автором материалов. Исключительное право сохранено за автором текста.
Если вы не хотите, чтобы данный материал был у нас на сайте, перейдите по ссылке: Нарушение авторских прав. Мы поможем в написании вашей работы!