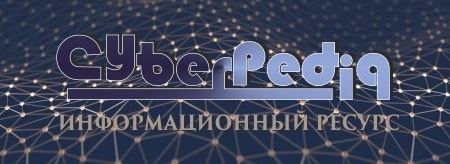
Организация стока поверхностных вод: Наибольшее количество влаги на земном шаре испаряется с поверхности морей и океанов (88‰)...
Архитектура электронного правительства: Единая архитектура – это методологический подход при создании системы управления государства, который строится...
Топ:
Процедура выполнения команд. Рабочий цикл процессора: Функционирование процессора в основном состоит из повторяющихся рабочих циклов, каждый из которых соответствует...
Комплексной системы оценки состояния охраны труда на производственном объекте (КСОТ-П): Цели и задачи Комплексной системы оценки состояния охраны труда и определению факторов рисков по охране труда...
Марксистская теория происхождения государства: По мнению Маркса и Энгельса, в основе развития общества, происходящих в нем изменений лежит...
Интересное:
Финансовый рынок и его значение в управлении денежными потоками на современном этапе: любому предприятию для расширения производства и увеличения прибыли нужны...
Инженерная защита территорий, зданий и сооружений от опасных геологических процессов: Изучение оползневых явлений, оценка устойчивости склонов и проектирование противооползневых сооружений — актуальнейшие задачи, стоящие перед отечественными...
Как мы говорим и как мы слушаем: общение можно сравнить с огромным зонтиком, под которым скрыто все...
Дисциплины:
![]() |
![]() |
5.00
из
|
Заказать работу |
|
|
Размерная стойкость инструмента имеет важное значение для анализа вопросов, связанных с работой инструмента в автоматизированном производстве. Размерную стойкость инструмента зачастую характеризуют временем его работы Т,в течение которого текущее, среднее значение размера обрабатываемых деталей располагается
в пределах части поля допуска, выделенной на переменные систематические погрешности размера, связанные с износом режущих
кромок.
Иногда размерную стойкость инструмента характеризуют количеством деталей N, изготовленных в пределах допуска без вмешательства оператора для регулирования или замены инструмента.
Размерную стойкость можно также характеризовать длиной пути резания l или площадью обработанной поверхности деталей до регулирования или замены инструмента (рис. 107). Проф. А.П. Соколовский указывал, что одной из характеристик размерной стойкости инструмента может служить линейный относительный износ,т.е. укорочение инструмента в радиальном направлении, отнесенное на 1000 м пути резания:
мкм/м,
где hi +1 – hi – линейное приращение износа по задней грани на (i + 1)-м режиме, мкм; li +1 – li – путь резания на (i + 1)-м режиме, м;
h о.з – линейный относительный износ.
Рис. 107. Графики зависимости износа h з от длины пути резания l
V 1;
V 2;
V 3
Размерную стойкость инструмента может характеризовать
и скорость размерного износа V н. Под скоростью размерного износа понимается скорость укорочения инструмента в радиальном направлении в периоде нормального износа, стойкости при принятом критерии затупления.
Все отмеченные характеристики размерной стойкости являются частными и в общем случае оказываются непригодными для проведения анализа вопросов, связанных с проблемой размерной стойкости инструмента, так как первая характеристика Т (время работы без подналадки или замены инструмента) имеет ограничения со стороны скорости резания V, подачи S, величины износа инструмента h з или hr; вторая характеристика N – количество обработанных деталей без подналадки инструмента размера обрабатываемой детали и износа (h з или hr); третья – l – ограничения со стороны подачи s, величины износа h з или hr; четвертая – П(площадь обработанной поверхности) – со стороны величины износа h з или hr; пятая – h о.л –со стороны подачи; шестая – Vh (скорость размерного износа) – со стороны скорости резания V и подачи s; наконец, последние две характеристики – поверхностный относительный износ h о.пи удельная размерная стойкость Т уд. Поверхностный относительный износ – это радиальный износ инструмента, отнесенный к 1000 см2 обработанной поверхности. Удельная размерная стойкость инструмента Т уд–площадь поверхности, которую способен обрабатывать инструмент при затуплении в радиальном направлении на 1 мкм.
|
Последние две характеристики являются универсальными, так как на них не накладываются ограничения ни со стороны скорости резания,ни со стороны подачи, критерия затупления и т.д.
Поэтому поверхностный относительный износ и удельная размерная стойкость могут быть использованы для сравнительной оценки размерной стойкости выбираемых режущих инструментов, для анализа точности и экономичности вариантов технологических процессов и режимов резания, а также для конструирования систем автоматического управления технологическими системами.
4.3.6. Влияние скорости (температуры) резания
на характеристики размерной стойкости.
Зависимость стойкость–скорость (Т – V)
При изменении скорости резания в широком диапазоне для различных процессов обработки резанием при обработке деталей из различных материалов инструментами из быстрорежущих сталей
и твердых сплавов зависимость Т = f (V)носит или экстремальный, или монотонно убывающий характер. Зависимость длины пути резания от скорости l = f (V) носит экстремальный характер (l = V · Т).
|
Положение точек максимума на кривых l = f (V)зависит от физико-механических свойств обрабатываемого материала и материала инструмента, сечения среза и других условий резания. При повышении режущих свойств инструментальных материалов наблюдается повышение оптимальных скоростей резания, соответствующих максимуму пройденного инструментом пути резания или минимуму интенсивности износа инструмента. При экстремальной зависимости размерной стойкости инструмента от скорости резания зависимость периода стойкости от скорости резания Т = f (V)может носить как экстремальный, так
и монотонно убывающий характер (рис. 108). Максимум размерной стойкости инструмента Тм и общей стойкости наблюдается при разных скоростях резания, а следовательно, и температурах в зоне резания. Для определения оптимальной скорости резания V о, соответствующей максимуму пути резания, надо первую производную пути по скорости резания приравнять к нулю:
l = ТV = f (V);
= T +
V = 0,
откуда,
V = V о = – T / .
Так как V о и Т являются положительными величинами, то равенство может наблюдаться при отрицательном значении ,что возможно лишь для ниспадающей ветви кривой. Следовательно, оптимальная скорость резания соответствует правой ниспадающей ветви кривой T = f (V). Поэтому всегда справедливо неравенство Vм <V о, где Vм –скорость резания, соответствующая максимуму периода стойкости инструмента Тм.
Даже в тех случаях, когда период стойкости Тм,наблюдаемый при Vм,выше периода стойкости Т о,–наблюдаемого при более высокой оптимальной скорости резания V о,работа на скорости VМ по сравнению со скоростью V оявляется нерациональной, так как это привело бы к снижению производительности обработки, размерной стойкости инструмента и ухудшению качества обрабатываемой поверхности.
Оптимальные скорости резания могут быть выявлены на основе обычных испытаний по кривым Т = f (V), при исследовании интенсивности размерного износа инструмента по кривым h о.л = f (V)
и h о.п = f (V), а также при исследовании интенсивности износа с помощью радиоактивных изотопов. Главным фактором, обуславливающим экстремальный характер зависимостей l = f (V)и h о.п = f (V), является рост температуры контактных поверхностей и изменение характера износа.
|
Построив зависимости Т–V в двойной логарифмической сетке координат, можно определить величину оптимальной скорости резания путем проведения касательной к кривой Т–V,проходящей под углом 45° к осям Т и V. Касательную ОК можно назвать линией постоянной размерной стойкости, так как для любой ее точки l = соnst l (l = VТ). Зависимость Т = f (V) для правой ветви может быть выражена формулой
V = Cv / Tm,
где СV –постоянная величина, зависящая от обрабатываемого
и инструментального материалов, t, s и прочих условий; Т –стойкость инструмента, в минутах; m – показатель относительной стойкости, m = a / b = tg a.
При a = 45° m = 1, т.е. V о = C / T 1, а С = V – Т 1при l max.
Для любой точки линии MN lm = Vm Tm (см. рис. 108). Если MN ближе к оси ординат, то Vm Tm меньше. Несмотря на то, что Тm >Т о,
l o > lm. Поэтому V о–это тот предел, до которого можно снижать скорость резания в целях повышения точности и производительности обработки.
Показатель относительной стойкости т характеризует степень изменения скорости резания с изменением стойкости резца. Он определяется опытным путем и зависит от материала детали и инструмента, толщины среза, вида и условий обработки. Чем ниже износостойкость режущей части инструмента и тяжелее условия резания, вызывающие повышение тепловыделения, тем меньше т.
Для быстрорежущих инструментов т << 0,125.
Для твердосплавных инструментов т << 0,2.
Для минералокерамических инструментов т >> 0,5.
4.3.7. Положение о постоянстве
оптимальной температуры резания
Большинство факторов, влияющих на интенсивность износа
инструмента, являются функцией температуры. Это позволило проф. А.Д. Макарову в 1961 году сформулировать следующее положение: оптимальным скоростям резания (для заданного материала режущей части инструмента при различных комбинациях скорости резания, подачи, глубины резания и геометрии инструмента) соответствует постоянная температура в зоне резания – оптимальная температура резания, например 700 °С при протягивании сплава ЭИ787-ВД (рис. 109).
|
Из положения о постоянстве оптимальной температуры резания вытекает ряд важных для науки и практики следствий.
Например, для инструментов с любой комбинацией геометрических параметров режущей части (r, a, j, j1, gи др.) точкам минимума кривых, выражающих зависимость интенсивности износа от скорости резания, соответствует одна и та же оптимальная температура резания, хотя уровень оптимальных скоростей резания при этом может колебаться весьма существенно (рис. 110). Большое значение указанного следствия состоит в том, что на его основе путем поддержания постоянства оптимальной температуры резания Т о можно осуществить процесс резания в оптимальном режиме при использовании инструментов с любой комбинацией геометрических параметров
режущей части без проведения весьма трудоемких и дорогостоящих стойкостных исследований. С физической точки зрения объяснение природы появления минимумов интенсивности износа связано
с появлением так называемых зон провала пластичности обрабатываемого материала с увеличением температуры (скорости) резания.
С целью определения влияния температуры на основные механические свойства исследуемых обрабатываемых материалов проводились испытания при одноосном растяжении круглых стандартных
а
б
Рис. 109. Влияние скорости резания V на изменение температуры резания Т (а) и интенсивности износа протяжек h о.з.л (б) при протягивании жаропрочного сплава ЭИ787-ВД с различными подачами на зуб: 0,02 мм/зуб;
0,06 мм/зуб;
0,1 мм/зуб
образцов на прессе Амслера с записью кривой деформации в диапазоне температур 293…1273 К. На рис. 111 приведены графики изменения механических свойств жаропрочного сплава ЭИ787-ВД в зависимости от температуры испытаний.
а б
в
Рис. 110. Влияниe l(а),a(б)и r (в) на температуру резания и поверхностный относительный износ резцов с различными геометрическими параметрами. Сталь ЭИ654; резцы ВК8
Анализ данных, приведенных на рис. 111, показывает, что изменение прочностных и пластических свойств этого сплава носит сложный характер: происходит снижение прочностных свойств с увеличением температуры испытаний (порядка 873…973 К). При этих температурах предел прочности снижается с 1100…1200 до 800…900 МПа, т.е. на 20…30 %. Аналогичную картину можно наблюдать и для других сплавов ЭИ437БУ-ВД, ЭП109-ВД.
Рис. 111. Влияние температуры механических испытаний Т на прочностные (s b) и пластические (d, y) свойства жаропрочного деформируемого сплава
ЭИ787-ВД
s b; ¨ y; · d
Несколько иную картину дает изменение показателей пластичности (относительное удлинение d и относительное сужение y). С повышением температуры наблюдается общая тенденция к первоначальному росту этих показателей в диапазоне температур
473…573 К, затем происходит снижение параметров пластичности до минимальных значений при определенных температурах, характерных для каждого исследуемого материала. После этого наблюдается резкий рост пластичности у всех материалов. Анализ графиков показывает, что для всех исследуемых жаропрочных сталей и сплавов есть определенная температурная зона низкой пластичности или повышенной хрупкости. Часто такую зону называют зоной провала пластичности металлов.
|
Сравнивая графики на рис. 109 и 111, можно видеть, что оптимальная температура Т о = 700 °С, при которой наблюдается минимум интенсивности износа инструмента, совпадает с температурной зоной минимума пластичности – с температурой провала пластичности обрабатываемого материала Т п.п. Таким образом, можно с физической точки зрения объяснить необходимость обработки резанием данного сплава при заданных условиях с такой оптимальной скоростью резания V o, при которой в зоне контакта инструмента и заготовки обеспечивается постоянная оптимальная температура Т о, совпадающая по величине с температурой провала пластичности Т п.п.
4.3.8. Экономическая скорость резания
и скорость резания, соответствующая максимальной
производительности на данном рабочем месте
В общем случае работа должна вестись на экономических скоростях резания, т.е. скоростях, когда себестоимость обработки минимальна. Скорость V эрасположена на правой ветви зависимости
Т = f (V) и всегда соблюдается неравенство V э> Vm (см. рис. 108).
Переменная доля себестоимости операции, зависящая от скорости резания, определяется формулой
A = t м(a раб + a ст) + t см/ Q (a раб + a ст) + e / Q,
где t м – машинное время на операцию, мин;
a раб – минутная зарплата рабочего с начислениями, коп;
a ст–затраты связанные с эксплуатацией станка в течение 1 минуты, коп;
a раб + a ст= Е –стоимость станко-минуты, коп;
t см – время на смену затупившегося инструмента и его подналадку за период стойкости, мин;
e – стоимость эксплуатации инструмента за период стойкости, коп.;
Q – количество обрабатываемых деталей за период стойкости, шт.
Выразим Q и t м через период стойкости инструмента:
t м = p DLh /1000 v · s · t,
где D –диаметр обрабатываемой детали, мм;
L –путь инструмента, мм;
h –припуск на сторону, мм.
С учетом формулы V = Cv / Tm
t м = p DLh /1000 v · s · t = p DLh Tm /1000 v · s · t Cv = C o Tm.
Переменная доля себестоимости операции зависит от скорости резания. Для обеспечения максимальной производительности труда на данном рабочем месте обработку необходимо вести на V м.п. При определении периода стойкости Т м.п,соответствующего скорости V м.п,пренебрегают затратами на эксплуатацию инструмента за период его стойкости.
Так как Т м.п <Т э,то скорость резания V м.п, при которой достигается максимальная производительность труда на данном рабочем месте, выше экономической скорости резания, т.е. V м.п >V э.
4.3.9. Возможные потери при выборе
высоких периодов стойкости
Как было показано выше, зависимость Т–V в двойной логарифмической сетке имеет вид прямой линии лишь в узком диапазоне скоростей резания. Этот участок кривой Т – V (рис. 112),содержащий наиболее употребительные периоды стойкости для данного инструмента, является основой для получения формул вида V = Cv / Tm, котoрые впоследствии служат для расчета и назначения режимов резания (нормативы по режимам резания НИАТ, 1965 г.). Вместе с тем указанные формулы используются для значительно более широкого диапазона периода стойкости.
Рассмотрим это на примере обработки жаропрочного сплава ЭП220 резцом ВК6М (t = 0,5 мм; s = = 0,09 мм/об.).
Повышение технологической стойкости при работе на V o для разных периодов стойкости приведено в табл. 15. Как видно из нее, при обработке на оптимальных режимах технологическая производительность может быть повышена в 2…3 раза, а размерная стойкость инструмента – более чем в 2 раза по сравнению с работой на режимах, рекомендуемых нормативами.
Таблица 15
Параметры технологической стойкости
при работе на оптимальной скорости V o
Т, мин | V т | V о | V о/ V т | h опт | h о.п | h опт/ h о.п |
2,06 | 2,32 | |||||
2,7 | 2,43 | |||||
11,5 | 3,04 | 2,45 |
Это объясняется тем, что нормативы рекомендуют работу на более низких скоростях резания (но высоких Т),соответствующих левым ветвям кривых h о.п = f (V), которые приводят к более интенсивному износу и повышенному расходу инструмента (рис. 113). Подобная картина роста интенсивности износа инструмента наблюдается и при назначении скоростей резания, превышающих V о. В этом случае скорости резания расположены на правой ветви кривой h о.п = f (V), что также приводит к значительному повышению интенсивности износа инструмента и снижению ее размерной стойкости.
4.3.10. Влияние различных факторов
на скорость резания и стойкость инструмента
На скорость резания и стойкость инструмента оказывают существенное влияние следующие факторы:
– глубина резания и подача (сечение среза);
– геометрия инструмента;
– вид обработки и сечение резца;
– величина износа инструмента;
– обрабатываемый и инструментальный материалы;
– состояние поверхностного слоя обрабатываемой детали;
– СОТС и т.д.
С увеличением t и s возрастают силы резания и повышается количество выделяющегося тепла, а следовательно, при сохранении постоянной стойкости инструмента скорость резания должна быть уменьшена. Зависимость V = f (T, t, s) выражается формулой
V = Cv / T m txv s yvKV, м/мин.
Многочисленные экспериментальные данные показывают, что при t > s показатели степени xv <уV;это объясняется тем, что с увеличением t и s повышается температура резания, но увеличение t
в большей мере оказывает влияние на улучшение теплоотвода, чем увеличение подачи. Если же t < s, то показатели степени хV и уV нужно поменять местами.
Стойкость инструмента при всех прочих равных условиях резания определяется износостойкостью материала режущей части.
Поэтому влияние геометрических параметров на его износ в равной степени относится к периоду стойкости, а значит и к скорости
резания. Так, уменьшение угла jприводит к уменьшению величины износа (за счет изменения соотношения между шириной и толщиной среза), стойкость при этом повышается.
Скорость резания при сохранении прежнего Т увеличивается.
С повышением заднего угла aснижается трение, но ухудшается теплоотвод и ослабляется режущий клин. Значение оптимального заднего угла aоптможет быть определено по формуле
sin aопт = С / aq,
гдеa = s sin j, С и q зависят от обрабатываемого материала.
Передний угол g для разных обрабатываемых материалов различный, т.е. зависит от свойств обрабатываемого материала детали
и может быть определен по следующим формулам:
– для стали:
gопт = 18 – 0,7 НRс;
– для чугуна:
gопт = 17,8 – 0,066 НВ.
Обычно R изменяется в небольшом диапазоне от 0,5 мм до 2 мм. R < 0,5 мм обеспечивает, как правило, низкую Т,а при R > 2 мм возникают вибрации. При этом не следует забывать, что изменение R приводит к изменению соотношения между толщиной и шириной среза. Значение оптимального радиуса R оптможет быть определено по формуле
R опт = (8 – 10) s.
Влияние вида обработки сводится к следующему:
– при расточке скорость резания несколько ниже, чем при обычном точении и K g = 0,9, так как расточной резец работает в более тяжелых условиях, чем проходной;
– при подрезке торца подрезные резцы работают в несколько лучших условиях, чем проходные, так как скорость при обработке
к центру снижается. Поправочный коэффициент при этом K g= 1,04;
– при отрезке в особо тяжелых условиях работают отрезные резцы, поэтому K gпринимают равным 0,5…0,6.
С увеличением поперечного сечения стержня резца улучшается теплоотвод, что положительно сказывается на стойкости.
Самое сильное влияние на скорость резания оказывает обрабатываемый материал, что проявляется через:
– твердость (выше твердость – ниже скорость резания);
– жаропрочность;
– склонность к адгезии;
– химическое сродство или инертность обрабатываемого материала к материалу инструмента;
– истирающую способность, или абразивность;
– теплопроводность и т.д.
Если скорость резания может изменяться в зависимости от геометрии резца и ширины среза до 3 раз, от толщины среза до 5 раз, от материала режущей части инструмента до 75 раз, то в зависимости от обрабатываемого материала – до 200 раз. Это значит, что при обработке, например, закаленной стали или твердого чугуна скорость резания в 200 раз меньше, чем при обработке алюминия.
Поправочный коэффициент на материал инструмента – Kv и,а на обрабатываемый материал – Kv м .
Поверхностный слой детали также оказывает большое влияние на выбор скорости резания V. Например, кованные и литые детали имеют более твердый поверхностный слой, в связи с чем скорость резанияпо корке ниже, чем по детали без корки.
При определении допустимой скорости резания учитывается
и износ инструмента. Если работа будет производиться до износа выше нормального, V должна быть уменьшена. Если же будет возможность работать до h з = 1,5…2 мм(нормативный h з = 0,8…1,5), то KVh = 1,33.
При применении СОТС скорость резания может быть повышена (в зависимости от вида и характера подвода СОТС в зону резания) – Kv СОТС = 1…1,15.
Итак, обобщенная формула для выбора скорости резания V имеет следующий вид:
V = Cv / T mt xvs yvKv м Kv и Kv j KvhK сотс.
Значения СV, хV, уV и поправочных коэффициентов приведены
в соответствующей справочной литературе.
В каком же соотношении находятся V э и V o?
Почти всегда (в большинстве случаев) экономическая скорость резания выше V о.
Эти скорости могут быть приняты одинаковыми при обработке:
– жаропрочных сплавов в любых условиях производства;
– закаленных сталей при любых условиях производства;
– некоторых марок жаропрочных сталей и титановых сплавов;
– любых материалов в условиях автоматизированного производства.
|
|
Состав сооружений: решетки и песколовки: Решетки – это первое устройство в схеме очистных сооружений. Они представляют...
Археология об основании Рима: Новые раскопки проясняют и такой острый дискуссионный вопрос, как дата самого возникновения Рима...
Эмиссия газов от очистных сооружений канализации: В последние годы внимание мирового сообщества сосредоточено на экологических проблемах...
История развития хранилищ для нефти: Первые склады нефти появились в XVII веке. Они представляли собой землянные ямы-амбара глубиной 4…5 м...
© cyberpedia.su 2017-2024 - Не является автором материалов. Исключительное право сохранено за автором текста.
Если вы не хотите, чтобы данный материал был у нас на сайте, перейдите по ссылке: Нарушение авторских прав. Мы поможем в написании вашей работы!