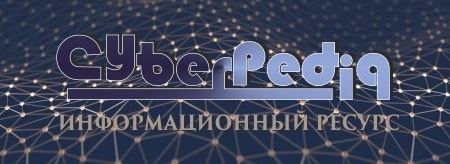
Состав сооружений: решетки и песколовки: Решетки – это первое устройство в схеме очистных сооружений. Они представляют...
Таксономические единицы (категории) растений: Каждая система классификации состоит из определённых соподчиненных друг другу...
Топ:
Комплексной системы оценки состояния охраны труда на производственном объекте (КСОТ-П): Цели и задачи Комплексной системы оценки состояния охраны труда и определению факторов рисков по охране труда...
Характеристика АТП и сварочно-жестяницкого участка: Транспорт в настоящее время является одной из важнейших отраслей народного хозяйства...
Техника безопасности при работе на пароконвектомате: К обслуживанию пароконвектомата допускаются лица, прошедшие технический минимум по эксплуатации оборудования...
Интересное:
Мероприятия для защиты от морозного пучения грунтов: Инженерная защита от морозного (криогенного) пучения грунтов необходима для легких малоэтажных зданий и других сооружений...
Национальное богатство страны и его составляющие: для оценки элементов национального богатства используются...
Влияние предпринимательской среды на эффективное функционирование предприятия: Предпринимательская среда – это совокупность внешних и внутренних факторов, оказывающих влияние на функционирование фирмы...
Дисциплины:
![]() |
![]() |
5.00
из
|
Заказать работу |
|
|
Vibration analysis is the cornerstone of all PPM programs. Perhaps the question asked most often is What is the vibration level that indicates the pump is in distress?". The answer is that there is no absolute vibration amplitude level that is indicative of a pump in distress. However, there are several guidelines that have been developed as target values that enable the analyst to set alarm levels. Also many users have developed their own site criteria that is used as a guideline. Institutions such as the Hydraulic Institute and API have developed independent vibration criteria. Caution should be exercised when applying the published values...each installation is unique and should be handled accordingly. When a machine is initially started, a baseline vibration reading should be taken and trended over time.
IMPELLER CLEARANCE
Open impeller centrifugal pumps offer several advantages. They're particularly suited but not restricted to liquids which contain abrasive solids. Abrasive wear on an open impeller is distributed over the diametrical area swept by the vanes. The resulting total wear has less effect on performance than the same total wear concentrated on the radial ring clearance of a closed impeller.
The open impeller permits restoration of "new pump" running clearance after wear has occurred without parts replacement. Many of Goulds open impeller pumps feature a simple positive means for axial adjustment without necessity of disassembling the unit to add shims or gaskets.
SETTING IMPELLER CLEARANCE (DIAL INDICATOR METHOD)
1. After locking out power, remove coupling guard and coupling.
2. Set dial indicator so that button contacts shaft end.
3. Loosen jam nuts (423B) on jack bolts (371 A) and back bolts out about two turns.
4. Tighten each locking bolt (370C) evenly, drawing the bearing housing toward the bearing frame until impeller contacts casing.
5. Set indicator to zero and back locking bolt about one turn.
6. Thread jack bolts in until they evenly contact the bearing frame. Tighten evenly backing the bearing housing away from the frame until indicator shows the proper clearance established in instruction manual.*
7. Evenly tighten locking bolts, the jack bolts keeping indicator at proper setting.
8. Check shaft for free turning.
*Established clearance may vary due to service temperature.
CENTRIFUGAL PUMP
The operating manual of any centrifugal pump often starts with a general statement, "Your centrifugal pump will give you completely trouble free and satisfactory service only on the condition that it is installed and operated with due care and is properly maintained."
Despite all the care in operation and maintenance, engineers often face the statement "the pump has failed i.e. it can no longer be kept in service". Inability to deliver the desired flow and head is just one of the most common conditions for taking a pump out of service. There are other many conditions in which a pump, despite suffering no loss in flow or head, is considered to have failed and has to be pulled out of service as soon as possible. These include seal related problems (leakages, loss of flushing, cooling, quenching systems, etc), pump and motor bearings related problems (loss of lubrication, cooling, contamination of oil, abnormal noise, etc), leakages from pump casing, very high noise and vibration levels, or driver (motor or turbine) related problems.
|
The list of pump failure conditions mentioned above is neither exhaustive nor are the conditions mutually exclusive. Often the root causes of failure are the same but the symptoms are different. A little care when first symptoms of a problem appear can save the pumps from permanent failures. Thus the most important task in such situations is to find out whether the pump has failed mechanically or if there is some process deficiency, or both. Many times when the pumps are sent to the workshop, the maintenance people do not find anything wrong on disassembling it. Thus the decision to pull a pump out of service for maintenance / repair should be made after a detailed analysis of the symptoms and root causes of the pump failure. Also, in case of any mechanical failure or physical damage of pump internals, the operating engineer should be able to relate the failure to the process unit's operating problems.
Any operating engineer, who typically has a chemical engineering background and who desires to protect his pumps from frequent failures must develop not only a good understanding of the process but also thorough knowledge of the mechanics of the pump. Effective troubleshooting requires an ability to observe changes in performance over time, and in the event of a failure, the capacity to thoroughly investigate the cause of the failure and take measures to prevent the problem from re-occurring.
The fact of the matter is that there are three types of problems mostly encountered with centrifugal pumps:
· design errors
· poor operation
· poor maintenance practices
The present article is being presented in three parts, covering all aspects of operation, maintenance, and troubleshooting of centrifugal pumps. The article has been written keeping in mind the level and interests of students and the beginners in operation. Any comments or queries are most welcome.
|
|
Механическое удерживание земляных масс: Механическое удерживание земляных масс на склоне обеспечивают контрфорсными сооружениями различных конструкций...
Типы сооружений для обработки осадков: Септиками называются сооружения, в которых одновременно происходят осветление сточной жидкости...
Поперечные профили набережных и береговой полосы: На городских территориях берегоукрепление проектируют с учетом технических и экономических требований, но особое значение придают эстетическим...
История создания датчика движения: Первый прибор для обнаружения движения был изобретен немецким физиком Генрихом Герцем...
© cyberpedia.su 2017-2024 - Не является автором материалов. Исключительное право сохранено за автором текста.
Если вы не хотите, чтобы данный материал был у нас на сайте, перейдите по ссылке: Нарушение авторских прав. Мы поможем в написании вашей работы!