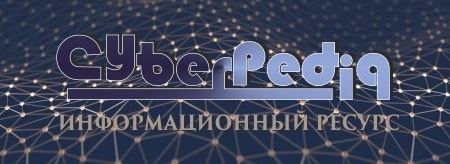
Таксономические единицы (категории) растений: Каждая система классификации состоит из определённых соподчиненных друг другу...
Особенности сооружения опор в сложных условиях: Сооружение ВЛ в районах с суровыми климатическими и тяжелыми геологическими условиями...
Топ:
Техника безопасности при работе на пароконвектомате: К обслуживанию пароконвектомата допускаются лица, прошедшие технический минимум по эксплуатации оборудования...
Характеристика АТП и сварочно-жестяницкого участка: Транспорт в настоящее время является одной из важнейших отраслей народного...
Установка замедленного коксования: Чем выше температура и ниже давление, тем место разрыва углеродной цепи всё больше смещается к её концу и значительно возрастает...
Интересное:
Средства для ингаляционного наркоза: Наркоз наступает в результате вдыхания (ингаляции) средств, которое осуществляют или с помощью маски...
Финансовый рынок и его значение в управлении денежными потоками на современном этапе: любому предприятию для расширения производства и увеличения прибыли нужны...
Влияние предпринимательской среды на эффективное функционирование предприятия: Предпринимательская среда – это совокупность внешних и внутренних факторов, оказывающих влияние на функционирование фирмы...
Дисциплины:
![]() |
![]() |
5.00
из
|
Заказать работу |
|
|
I-1 Pump Safety Tips
Maintenance personnel should be aware of potential hazards to reduce the risk of accidents
Safety Apparel
Couplings Guards:
Flanged Connections:
Operation:
Maintenance Safety:
Trouble shooting Centrifugal Pumps
Predictive and Preventative
I-11 Predictive and Preventative Maintenance Program
This overview of Predictive and Preventative Maintenance (PPM) is intended to assist the pump users who are starting a PPM program or have an interest in the continuous improvement of their current programs.
There are four areas that should be incorporated in a PPM program. Individually each one will provide information that gives an indication of the condition of the pump; collectively they will provide a complete picture as to the actual condition of the pump.
PUMP PERFORMANCE MONITORING
There are six parameters that should be monitored to understand how a pump is performing. They are Suction pressure (Ps), discharge pressure (Pd), flow (Q), pump speed (Nr), pumpage properties, and power. Power is easiest measured with a clip on amp meter but some facilities have continuous monitoring systems that can be utilized. In any event, the intent is to determine the BHP of the pump. When using a clip on amp meter the degree of accuracy is limited. It should not be used to determine the efficiency of the pump. Clip on amp meters are best used for trouble shooting where the engineer is trying to determine the operating point of the pump.
The most basic method of determining the TDH of the pump is by utilizing suction and discharge gauges to determine PS and Pd. The installation of the taps for the gauges is very important. Ideally, they should be located normal to the pipe wall and on the horizontal centerline of the pipe. They should also be in a straight section of pipe. Avoid locating the taps in elbows or reducers because the readings will not indicate the true static pressure due to the velocity head component. Avoid locating taps in the top or bottom of the pipe because the gauges can become air bound or clogged with solids.
|
Flow measurements can be difficult to obtain but every effort should be made to do so, especially when trouble shooting. In some new installations permanent flow meters are installed which make the lob easier. When this is the case, make sure the flow meters are working properly and have been calibrated on a regular schedule. When flow meters are not installed, pitot tubes can be used. Pitot tubes provide a very accurate measure of flow, but this in an obtrusive device and provisions must be made to insert the tube into the piping. The other method of determining flow is with either a doppler or transitime device. Again, provisions must be made on the piping for these instruments, but these are non-obtrusive devices and are easier to use than the pitot tube. Caution must be exercised because each device must be calibrated, and independent testing has shown these devices are sensitive to the pumpage and are not 100% accurate.
An accurate power measurement reading can also be difficult to obtain. Clip on tap meters are the most common tool available to the Field Engineer who is trouble shooting a pump problem. In most cases this has proven to be accurate. However, as previously mentioned, this tool must be used and applied properly. Clip on tap meters are not accurate enough to determine the actual efficiency of a pump. If accurate horsepower readings are necessary, a torque shaft must be installed but is not very practical in an actual field installation and lends itself to use in a laboratory environment much better. In some critical installations where the user has provided a permanent power monitor, these have varying degrees of accuracy and they must be understood up front.
Finally, the properties of the pumpage must be known to accurately determine the actual pump performance. Pumpage temperature (TP), viscosity, and specific gravity (S.G.), must be known.
When all of the above parameters are known, it becomes a simple matter of calculating the pump performance. There are instances when it proves to be a very difficult if not an impossible task to determine all of the above parameters in the field, therefore, the Field Engineer must rely on his or her ability to understand where a compromise must be made to get the lob done. The basic document the Field Engineer must have is the pump performance curve. With this it can be determined where the pump is performing in some cases without all of the information.
|
|
Опора деревянной одностоечной и способы укрепление угловых опор: Опоры ВЛ - конструкции, предназначенные для поддерживания проводов на необходимой высоте над землей, водой...
Особенности сооружения опор в сложных условиях: Сооружение ВЛ в районах с суровыми климатическими и тяжелыми геологическими условиями...
Эмиссия газов от очистных сооружений канализации: В последние годы внимание мирового сообщества сосредоточено на экологических проблемах...
Общие условия выбора системы дренажа: Система дренажа выбирается в зависимости от характера защищаемого...
© cyberpedia.su 2017-2024 - Не является автором материалов. Исключительное право сохранено за автором текста.
Если вы не хотите, чтобы данный материал был у нас на сайте, перейдите по ссылке: Нарушение авторских прав. Мы поможем в написании вашей работы!