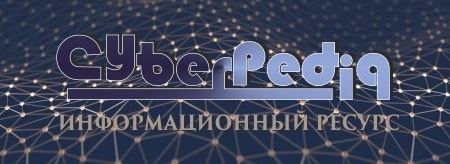
Общие условия выбора системы дренажа: Система дренажа выбирается в зависимости от характера защищаемого...
История развития хранилищ для нефти: Первые склады нефти появились в XVII веке. Они представляли собой землянные ямы-амбара глубиной 4…5 м...
Топ:
Основы обеспечения единства измерений: Обеспечение единства измерений - деятельность метрологических служб, направленная на достижение...
Комплексной системы оценки состояния охраны труда на производственном объекте (КСОТ-П): Цели и задачи Комплексной системы оценки состояния охраны труда и определению факторов рисков по охране труда...
Интересное:
Национальное богатство страны и его составляющие: для оценки элементов национального богатства используются...
Инженерная защита территорий, зданий и сооружений от опасных геологических процессов: Изучение оползневых явлений, оценка устойчивости склонов и проектирование противооползневых сооружений — актуальнейшие задачи, стоящие перед отечественными...
Берегоукрепление оползневых склонов: На прибрежных склонах основной причиной развития оползневых процессов является подмыв водами рек естественных склонов...
Дисциплины:
![]() |
![]() |
5.00
из
|
Заказать работу |
|
|
4.1. Методология комплексных исследований поведения микроэлементов в сложных металлургических системах на примере доменной плавки.
Для построения элементопотока необходимо знать, как конкретный элемент ведет себя в каждом металлургическом переделе. Статистической информации для такого анализа в виду высокой сложности металлургических систем недостаточно. Предлагаемая методология исследования поведения микроэлементов в металлургических системах базируется на комплексном термодинамическом и балансовом способах их анализа /8, 304…308/.
Микроэлементы содержатся во всех шихтовых материалах и дутьевых добавках, применяемых в доменной плавке. Они могут входить в состав материалов природного происхождения и в материалы, подвергнутые техногенным преобразованиям /309…312/. Современная доменная плавка практически полностью проходит на шихте из предварительно термически обработанных материалов, т.е. по существу на материалах техногенного происхождения, заново прошедших стадию минералообразования. При производстве агломерата – основного компонента железорудной части доменной шихты – в рамках производственного рециклинга широко используется мелкодисперсные материалы, обогащённые примесными микроэлементами /313…316/.
Особую специфику имеют микропримеси, входящие в состав кокса и каменных углей. Они присутствуют в упомянутых материалах в двух основных формах. Микроэлементы могут находиться непосредственно в кристаллической структуре, формируемой атомами углерода: в этом случае принято говорить, что они входят в состав «органической» части массы угля или кокса. Атомы примесных микроэлементов при этом называются также «гетероатомами» углеродной кристаллической решётки. Кроме того, микроэлементы могут находиться в частицах, попавших в угольные пласты в процессе их формирования, или в частицах пород, вмещающих угольные пласты, оставшихся в угольном концентрате после обогащения и перешедших впоследствии в металлургический кокс. О таких микроэлементах принято говорить как о входящих в «минеральную» часть угля или кокса. Поведение микропримесей «органической» и «минеральной» частей кокса и угля в доменной плавке, как правило, имеет существенные отличия /317…320/.
|
Доменный процесс представляет собой сложный объект исследований, поскольку формирующаяся в доменной печи металлургическая система включает все виды сред: газовую, жидкую и твердую, и характеризуется сложными закономерностями массообменных процессов в противоточной системе в широком интервале температур (от 50 до 25000С) и давлений (до 5 атм.). В последние годы характер доменного процесса существенно изменился:
- повысилась интенсивность процессов в горне печи (особенно в печах большого объема), что привело к снижению времени контакта чугуна и шлака;
- возросла роль процессов, протекающих непосредственно на поверхности коксовой насадки, в том числе в «тонких пленках» металлических и оксидных расплавов;
- особое значение приобрели процессы в окислительной зоне печи, в связи с постоянным увеличением доли и разнообразия применяемых топливных добавок /321…324/.
По мнению многих специалистов /325…331/, в ближайшие десятилетия неизбежен переход на широкое использование в доменной плавке комплексных руд, пылеугольного топлива, мазута и плотных углей. Именно дополнительное топливное сырье (особенно низкосортные угли и мазуты) отличается повышенным содержанием примесных микроэлементов, таких как свинец, никель, ванадий, титан, медь, молибден.
Важными особенностями рудной и топливной базы предприятий чёрной металлургии России в настоящее время являются:
|
· выраженный акцент на широкое использование материалов из собственных отвалов и накопителей (мощность которых, по некоторым оценкам, превышает 100 млн. т), что позволит в течение ближайших 30-50 лет работать с долей «собственного», часто загрязнённого примесями, железа до 10 % от общего количества поступающего на комбинат полного цикла;
· ориентация предприятий Южного Урала и Западной Сибири, в связи с высокими затратами на транспортировку железорудных материалов, на разработку запасов собственных месторождений сложного генезиса с высоким содержанием микропримесей /332…335/;
· высокий расход в доменном производстве кокса, при производстве которого часто используются концентраты коксующихся углей с повышенным содержанием микропримесей.
По сути производимые в настоящее время в России чугуны являются «микролегированными» (см. Приложение «Содержание элементов - микропримесей в металлургических материалах») и содержат от 20 до 28 примесных элементов общим количеством от 0,55 до 1,6 кг/т чугуна. Тем не менее, представления о поведении в доменной плавке примесных микроэлементов по-прежнему базируются на данных 30-40-летней давности.
При разработке новой методики анализа поведения микропримесей в доменной плавке исходили из следующих соображений. Поскольку относительные количества микропримесей незначительны, их поведение определяющим образом зависит от способа и места попадания в реакционное пространство металлургического агрегата. Если элемент распределен равномерно и достаточное время находится в реакционной зоне, то должно устанавливаться его равновесное распределение между всеми фазами. Однако примеси попадают в доменную печь компактно в отдельных составляющих сырьевых материалов. Например, многие редкие и цветные металлы концентрируются в органической части кокса, галогены входят в состав железорудных минералов и дутьевых добавок. При таком комплексном попадании в печь примеси «чувствуют» только локальное реакционное окружение, которое зависит от той составляющей, в которой они находятся.
Попадающие в доменную печь микроэлементы распределяются между жидкими продуктами плавки (чугуном и шлаком), доменным газом и пылью (колошниковой пылью и шламом). Кроме того, они переходят в состав некоторых особых образований, формирующихся в печи в процессе ее эксплуатации: гарнисажа, настылей, отложений на загрузочных устройствах, выделений некоторых металлов (например, свинца, титана, лантаноидов) на футеровке горна и лещади и т.п. Также микроэлементы могут формировать контуры циркуляции во внутреннем пространстве печи в результате возгонки при высоких и последующей конденсации на поверхности твердых шихтовых материалов при низких температурах. Микроэлементы, попадающие в шламы газоочистных сооружений, могут накапливаться в цикле «доменная печь → шлам → агломерация → доменная печь».
|
Разработанная методика для изучения поведения микропримесей в доменной плавке включает экспериментальную, исследовательскую и расчетную теоретическую части. Экспериментальная часть базируется на сведении баланса по каждому исследуемому элементу, а теоретическая – на термодинамических расчетах равновесия для сложных химических систем. В результате сопоставления экспериментальных данных и результатов моделирования выполняется оценка распределения элемента между чугуном, шлаком и газовой фазой доменного процесса.
Для исследования поведения микроэлементов в условиях доменной плавки были использованы следующие методики и выполнены эксперименты:
– отбор проб металлургических материалов доменного производства,
– выполнение тонкого химического анализа металлургических материалов
– изготовление, обжиг и восстановление содержащих микроэлементы железорудных окатышей и брикетов;
– выплавка чугуна, содержащего микроэлементы;
– изготовление шлифов;
– исследование минералогической структуры шлифов материалов, содержащих микроэлементы.
– термодинамическое моделирование поведения микроэлементов в сложных металлургических системах, характерных для доменного процесса;
Исследования по физическому моделированию поведения микроэлементов в металлургических системах были выполнены в лабораториях: МИСиС, Института металлургии имени Байкова, ГИРЕДМЕТ.
Исследования поведения микроэлементов в доменном процессе проводились на базе Металлургических предприятий: ОАО “Северсталь”, АК “Тулачермет”, ОАО “НЛМК”, ОАО «НТМК», ОАО «Косогорский металлургическоий завод», «ЕКО-Шталь» (Германия), «Кардемир» (Турция), «Хадисолб» (Египет).
|
Отбор проб шихтовых материалов: железорудных концентратов, агломерата, известняка, окатышей, кокса, чугуна, шлака, шламов и пылей был осуществлен в соответствии с действующими на время проведения исследований стандартами: ГОСТ 16598-80, ГОСТ 15054-80, ГОСТ 23083-78, ГОСТ 7565-81 и ГОСТ 2789-73.
Полный химический состав металлургических материалов определялся в лабораториях кафедры Сертификации и аналитического контроля МИСиС и Масс-спектрометрии и хроматографии ГИРЕДМЕТ («MS&GC Lab. GIREDMET Testing Analytical Center»).
Использовались следующие аналитические методы анализа:
- искровая масс-спектрометрия (ИМС): на масс-спектрометре с двойной фокусировкой JMS-01-BM2 (JEOL, Япония) с регистрацией спектров на фотопластинах Ilford-Q и применением микроденситометра MDM6 (Joyce Loebl, Великобритания) и мини ЭВМ NOVA 4 (США);
- рентгено - флуоресцентная энерго - дисперсионная спектрометрия (РФЭС) с применением PHILIPS PW9500;
- атомно-эмиссионная спектрометрия (АЭС) с применением Jobin Yvou JY38;
- атомно-абсорбционная спектрофотомерия (ААС) по оригинальной методике MS&GC Lab.;
- специальные количественные методы определения содержания отдельных химических элементов в конкретных твердых материалах.
По каждому из исследованных материалов было параллельно проанализировано по 4 усредненных пробы. Результаты анализов, отличавшиеся от среднего значения по всем четырем испытаниям более чем на 10 % (отн.), в дальнейшем не учитывались. При расчете содержаний микропримесей использовалось математическое обеспечение, разработанное в MS и GS (случайная погрешность результатов анализа характеризуется величиной относительного стандартного отклонения 0,15 – 0,30 % массовых долей). Для последующего количественного определения содержания в пробах обнаруженных микропримесей применялись специальные физико-химические методы анализа. Тонкий количественный химический анализ выполнен в лаборатории химического анализа кафедры СиАК МИСиС. Использованные в работе методы тонкого химического анализа отвечают передовым мировым технологиям исследований и гарантируют необходимую точность выполнения измерений /308/.
Результаты выполненных исследований приведены в Приложении «Содержание элементов - микропримесей в металлургических материалах».
Методика лабораторных исследований. Изготовление и высокотемпературная вакуумная обработка чугуна, содержащего примесные микроэлементы (галлий, мышьяк, свинец). Получение чугуна, содержащего микроэлементы, проводилось в вакуумно-индукционных печах «ТК-30-1750. 1Ф» и “LEYBOLD-HERAUSES” (Германия).
|
Нагрев печи «ТК-30-1750. 1Ф» производился в две стадии: с 20 до 100 0С в течение 1 часа, со 100 до 1500 0С в течение 3,5 часа, выдержка при температуре 1500 0С осуществлялась в течение 1 часа. В графитовый тигель помещали гранулы (массой до 3г), содержащие микроэлементы (как правило, в виде металлов), и обернутые фольгой из Al2O3 (массой до 2г). Затем опускали тигель в печь и выдерживали 15-18 минут при температуре 1500 0С, до расплавления содержимого тигля, затем производили помешивание расплава. После этого, вынимали тигель из печи и охлаждали на воздухе при комнатной температуре. Извлекали чугун, содержащий микроэлементы из тигля.
Вакуумно-индукционная печь фирмы “LEYBOLD-HERAUSES” (Германия) имела следующие основные параметры. Размеры печи: длина – 3780 мм., ширина – 1790 мм., высота – 3620 мм., при объеме рабочей камеры 0,8 м3. Диапазон изменения температуры: 0 – 1800 оС. Расход электроэнергии: 600 – 800 кВт/ч*т. Рабочий частотный диапазон 0 – 10 кГц. Максимальная сила тока - 11 кА. Продолжительность плавки при массе шихты 15 кг. - 30 мин. Печь была оборудована дозатором, позволявшим многократно подгружать в печь шихту и специальные добавки, и двумя насосами: форнасосом производительностью 460 л/мин и диффузионным насосом производительностью 380 л/мин.
Для высокотемпературной обработки чугуна использовалась вакуумно-индукционная печь мощностью 10 кВт. Внутренний объем печи – 30 литров, диаметр тиглей 20 мм. Кусочки чугуна помещались в тигель, который подвергали нагреву до температуры не менее 1850 оС. Затем включали вакуумные насосы для достижения вакуума глубиной 1´ 10-1 мм. рт. ст. Под вакуумом расплавленный чугун выдерживался не менее 30 минут. Затем печь выключали, и расплав охлаждался до комнатной температуры вместе с печью.
Изготовление, обжиг, восстановление и оптические исследования металлургических материалов, содержащих микроэлементы. Получение металлургических материалов, содержащих микроэлементы, осуществлялось в лаборатории кафедры ЭРЧМ (РТП) МИСиС двумя методами: брикетированием с помощью холодного прессования и изготовлением окатышей. Прессование осуществлялось ручным гидравлическим прессом в стальной пресс-форме. Давление составляло около 250 кгс/см3. Полученные брикеты выдерживали сбрасывание с высоты 1,5 м на стальную плиту, при этом наблюдалось образование лишь незначительных поверхностных сколов. Изготовление окатышей проводилось вручную. Полученную шихту тщательно перемешали, добавляя воду, а затем изготовили сырые окатыши. Полученные сырые окатыши высушили в сушильном шкафу при температуре 150 оС в течение 15 минут.
Для проведения опытов по обжигу и восстановлению окатышей и брикетов, содержащих микроэлементы, использовались лабораторные печи, размещенные в лаборатории кафедры ЭРЧМ (РТП) МИСиС. В качестве восстановительного реагента применялся водород. Работа по изучению шлифов исследуемых материалов проводилась на микроскопах марки МИН-9.
Термодинамические расчеты с использованием пакета программ «ИВТАНТЕРМО». Анализ технологических режимов металлургических процессов в настоящее время в значительной степени сдерживается отсутствием данных об условиях формирования жидких продуктов и газовой фазы процесса. В специальной литературе, в частности, отсутствует описание методик расчета поведения в металлургических процессах многих примесных элементов в различных температурных и окислительно-восстановительных условиях. В связи с этим, актуален анализ поведения элементов и их соединений с точки зрения термодинамики. Это обусловлено принципиальным характером получаемых выводов: если синтез некоторого химического соединения при заданных расчетных условиях невозможен исходя из законов термодинамики, то это означает безусловный «запрет» на его образование в реальных условиях. В то же время термодинамическая возможность того или иного процесса еще не означает его обязательной реализации: процесс «разрешенный» законами термодинамики может быть невозможен по кинетическим причинам из-за ничтожно малых скоростей протекания. Поэтому получаемые в результате термодинамического расчета концентрации веществ рассматриваются как максимально возможные значения.
Таким образом, с учетом кинетических ограничений безусловный характер имеют лишь выводы о термодинамической невозможности тех или иных процессов. Именно это и представляет наиболее важную задачу экологической экспертизы любого технологического процесса по предполагаемым вредным выбросам. Применительно к анализу формирования вредных выбросов определяющее значение имеют как раз «запретительные» выводы термодинамического моделирования, поскольку результатом подобного теоретического анализа является нахождение условий, когда вредные вещества образуются в минимальном количестве или не образуются вовсе.
Результаты термодинамических расчетов /305/, выполненных с использованием автоматизированного комплекса ИВТАНТЕРМО для соединений серы и азота, показали хорошую сходимость с фактически материалом, содержащим данные по выбросам в атмосферу для различных технологий и производств. По мнению авторов «термодинамический способ расчета является единственно возможным, например, для прогнозирования химического состава столь сложной многокомпонентной системы как доменный процесс». При этом кинетические ограничения, влияющие на результаты анализа, могут быть частично сняты разумным выбором исходного состава и условий протекания реакций, а также ограничением числа входящих в систему элементов и химических соединений, базирующимся на основе опытных данных о составе чугуна, шлаков, выбросов и газовой фазы процесса. Исследования показали, что для изучения поведения любых микроэлементов в доменной печи целесообразна следующая общая схема расчетов: постепенный переход от изучения простых систем к расчету более сложных.
Исходя из изложенного выше, для термодинамического моделирования поведения микропримесей в условиях доменного процесса использовался автоматизированный комплекс ИВТАНТЕРМО для Windows /306/. В состав комплекса входят:
– база данных, которая на сегодняшний день содержит сведения о свойствах около 2600 веществ, образованных из 96 химических элементов,
– автономные программы, реализующие следующие функции: работа с базой данных, расчет состава и параметров равновесного состояния многокомпонентных гетерогенных термодинамических систем.
Комплекс ИВТАНТЕРМО осуществляет расчет количества молей и мольных долей компонентов многоэлементной и многофазной системы в равновесном состоянии при заданных параметрах: температуре, давлении и элементном составе. Расчёт в системе “ИВТАНТЕРМО” может производиться для 400 одновременно сосуществующих веществ, результаты могут быть представлены в виде графических диаграмм, на которых даны концентрации имеющихся в равновесии веществ в зависимости от температуры, давления или концентрации любого исходного компонента системы. Алгоритм расчета основан на минимизации энергии Гиббса (G) системы. Метод сводится к определению конечного вещественного состава, отвечающего минимума энергии Гиббса:
G = Gini,
где G – энергия Гиббса i- компонента системы (i = 1, 2,…k);
ni – число молей i- компонента;
R – универсальная газовая постоянная (R=8,31 Дж/моль·К);
Т – температура.
Если в системе присутствует m видов атомов (химических элементов), то для каждого вида количество грамм-атомов в одном моле газовой атмосферы определяется по уравнению:
где nij - количество атомов j-ro элемента (j; = 1,...,k) в i-м газовом веществе.
Фактически уравнение выражает закон сохранения вещества для каждого вида атомов. Учтем еще одно условие, сокращающее число неизвестных в данной модели. Оно заключается в законе Дальтона:
Данное уравнение эквивалентно условию ∑Xi = 1. Теперь, если найти минимум энергии Гиббса при описанных условиях, это позволит определить искомые концентрации веществ в равновесной газовой смеси - Xi. Для практического осуществления решения используют метод неопределенных коэффициентов Лагранжа. Составляется вспомогательная функция Лагранжа L (где λj и λx - неопределенные коэффициенты):
Минимум функции L совпадает с минимумом G. Для его нахождения L дифференцируется по всем неизвестным – xi, λj и λx и результаты приравниваются к нулю.
Для проведения термодинамических расчетов задаются исходные параметры: химические составы исследуемых веществ с концентрациями элементов, присутствующих в их составе и температурный интервал с интересующим шагом. Исследовался интервал температур от 100 до 2500 °С.
Для получения сведений о процессах, протекающих в доменной печи в конкретных условиях, рассматривались различные температурные зоны, границы которых определялись в зависимости от поставленной задачи исследования. «Низкотемпературная» зона соответствовала верхней части доменной печи с максимальной температурой - 1300 °С, «промежуточная» зона - условиям нижней части печи с температурами от 1300 до 1600 °С. «Высокотемпературная» зона, или зона «фурменного очага» имела температуры от 1600 до 2500 °С.
В пределах температурных зон равновесные составы рассчитывались в зависимости от соотношения «кислород - углерод» (О/С), которое варьировалось в пределах от 0,1 до 10. Для получения развернутой картины происходящих процессов расчеты проводили с постепенным усложнением системы, последовательно добавляя к первоначально упрощенным вариантам дополнительные элементы и вещества. Так, например, исходная система для расчета распределения стронция по фазам первоначально включала следующие элементы: Fe, Ca, O, C, Si, Sr. Затем постепенно она была усложнена за счет учета серы, водорода, азота и т.д. При этом учитывалась возможность образования растворов в расплавах металла и шлака. Давление в исследуемых системах варьировалось от 2,5 атм. (на колошнике печи) до 4 атм. (в фурменной зоне).
|
|
Историки об Елизавете Петровне: Елизавета попала между двумя встречными культурными течениями, воспитывалась среди новых европейских веяний и преданий...
Наброски и зарисовки растений, плодов, цветов: Освоить конструктивное построение структуры дерева через зарисовки отдельных деревьев, группы деревьев...
Археология об основании Рима: Новые раскопки проясняют и такой острый дискуссионный вопрос, как дата самого возникновения Рима...
Типы сооружений для обработки осадков: Септиками называются сооружения, в которых одновременно происходят осветление сточной жидкости...
© cyberpedia.su 2017-2024 - Не является автором материалов. Исключительное право сохранено за автором текста.
Если вы не хотите, чтобы данный материал был у нас на сайте, перейдите по ссылке: Нарушение авторских прав. Мы поможем в написании вашей работы!