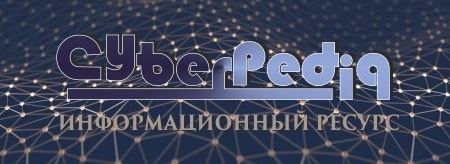
Эмиссия газов от очистных сооружений канализации: В последние годы внимание мирового сообщества сосредоточено на экологических проблемах...
Индивидуальные и групповые автопоилки: для животных. Схемы и конструкции...
Топ:
Генеалогическое древо Султанов Османской империи: Османские правители, вначале, будучи еще бейлербеями Анатолии, женились на дочерях византийских императоров...
Эволюция кровеносной системы позвоночных животных: Биологическая эволюция – необратимый процесс исторического развития живой природы...
Основы обеспечения единства измерений: Обеспечение единства измерений - деятельность метрологических служб, направленная на достижение...
Интересное:
Наиболее распространенные виды рака: Раковая опухоль — это самостоятельное новообразование, которое может возникнуть и от повышенного давления...
Средства для ингаляционного наркоза: Наркоз наступает в результате вдыхания (ингаляции) средств, которое осуществляют или с помощью маски...
Искусственное повышение поверхности территории: Варианты искусственного повышения поверхности территории необходимо выбирать на основе анализа следующих характеристик защищаемой территории...
Дисциплины:
![]() |
![]() |
5.00
из
|
Заказать работу |
|
|
Важным методическим вопросом является принцип подразделения элементов на макро – и микроэлементы. В соответствии с предложенной ранее классификацией /8/, к макроэлементам относят элементы, которые «существенным образом влияют на ход процессов добычи, производства, потребления или эксплуатации предмета, определяя технико-экономические показатели упомянутых стадий техногенных преобразований природных ресурсов». В количественном выражении можно принять, что к макроэлементам относятся те, содержание которых в рассматриваемом продукте (или системе) превышает около 0,1% (масс.). Если содержание элемента составляет менее 0,1% его можно условно отнести к категории микроэлементов.
Микроэлементы, как правило, подразделяются на «микропримесные» – существенным образом влияющие на свойства и количественные характеристики продукта, и «следовые» – содержание которых настолько незначительно, что их присутствие никак не влияет ни на какие из известных в настоящее время потребительских или токсических характеристик продукта (рисунок 16).
Рис. 16. Подразделение химических элементов
Среди микропримесей выделяются легирующие, «бродячие» и композитные элементы. Проблема «бродячих» элементов имеет в современной чёрной металлургии особое значение. Термин «бродячие элементы» пришёл из американского сленга, в последние годы, в специальной литературе чаще употребляется термин «элементы-ваганты» (или «голиарды»). В отечественной металлургической литературе наиболее близким по смыслу является термин «циркулирующие элементы». «Бродячие» элементы не только оказывают отрицательное влияние на качество чугуна (как и большинство микропримесных элементов), но и не могут быть легко удалены из него в процессе последующих металлургических переделов. Поэтому «бродячие» элементы постепенно накапливаются в готовом стальном продукте в процессе круговорота «сталь – металлолом – сталь». Наиболее важными бродячими элементами в настоящее время считаются: медь, хром, никель (обозначаемые специальной аббревиатурой «CCN»), олово, молибден.
|
Применительно к процессам металлургии железа может быть принято следующее подразделение элементов. Элементы основы: железо, углерод, кислород, азот, водород, кальций, кремний, алюминий, магний. Они являются обязательными составляющими любой металлургической системы. К макропримесным элементам обычно относят марганец, серу, цинк, калий и натрий, иногда – титан и свинец (в случае их высокого содержания в металлургических материалах). К микропримесям относятся все остальные химические элементы периодической системы.
Марганец, фосфор и сера представляют собой элементы, которые определяют качественные характеристики готового продукта и, поэтому, контролируются на всем протяжении технологического цикла и включаются во все виды стандартов или сертификатов на изделия из железа. Калий и натрий играют важнейшую роль в процессах формирования металлургических шлаков, а также, совместно с цинком, существенным образом влияют на показатели процессов производства первичного металла (главным образом чугуна) и стойкость огнеупоров доменных печей. В связи с этим, химическому анализу на цинк, калий и натрий, как правило, подвергаются все шихтовые материалы, поступающие на металлургическое предприятие (прежде всего: коксующиеся угли, железорудные материалы, флюсы).
Отнесение того или иного элемента к одной из упомянутых выше групп зависит от конкретных анализируемых условий. Например, хром чаще всего классифицируется как микропримесный элемент, при этом в случае производства товарного литейного чугуна он обычно рассматривается как легирующий, а при производстве передельного (особенно в случае применения в шихте хромсодержащих металлодобавок) – как «бродячий». Хром, никель, ванадий, фосфор могут играть роль макропримесного элемента при производстве хромоникелевого, ванадиевого или фосфористого чугуна или элемента основы – при выплавке в доменной печи соответствующих ферросплавов.
|
Микроэлементы содержатся во всех материалах, используемых на предприятиях черной металлургии: в железных и марганцевых рудах, углях всех видов, флюсах, ферросплавах, огнеупорах, металлоломе, материалах, используемых для нанесения покрытий на изделия из железа и проч.
В металлургических материалах могут присутствовать в количестве от долей до десятков тысяч ppm (г/т материала) химические элементы всех групп и периодов периодической системы за исключением инертных газов и трансурановых элементов. Вовлекаясь в металлургический передел в составе шихтовых материалов и газов и макро- и микроэлементы могут:
1. Переходить в готовые продукты металлургического производства – как собственно в изделия из железа, так и в «попутные» продукты, например, в металлургические шлаки, или материалы, получаемые в процессе коксохимического производства и т.п.
2. Попадать в отходы производства (в основном в золы и шламы тепловых электростанций (ТЭС), а также сталеплавильные шлаки и шламы), которые в настоящее время складируются в золошламонакопителях, отвалах, полигонах и других объектах, предназначенных для депонирования техногенных материалов.
3. Накапливаться в металлургических агрегатах в составе гарнисажа, настылей и других специфических образований.
4. Переходить в шламы газоочисток, окалину и другие материалы с формированием контура циркуляции внутри металлургического цикла при утилизации этих материалов в агломерационном, доменном, конверторном и других процессах.
5. Выноситься в окружающую среду (атмосферу и гидросферу) в виде газов, возгонов, пылей, взвесей, растворов и т.п., не улавливаемых очистными устройствами.
6. Накапливаться в циркуляционных контурах, формирующихся во внутреннем пространстве металлургических агрегатов в результате возгонки элементов при высоких и последующей конденсации при низких температурах.
|
3.3. Методика определения параметров элементопотоков для предприятий черной металлургии. Элементопоток железа.
Разработана «Методика определения параметров элементопотоков для предприятий черной металлургии» /275/.Она зарегистрирована в качестве НОУ-ХАУ в депозитарии МИСиС,реализована в виде математического описания «ПОТОК» и применялась для анализа движения железа и марганца на отечественных предприятиях ОАО «Носта», ОАО ЗСМК, ОАО «Косогорский металлургический завод» и заводе «EKO-Stahl» (Германия).
Методика отличается от аналогов:
1. Реализацией принципа «непрерывности потока железа», выполнение которого обеспечивает «прозрачность» потока основного элемента на всём протяжении производственного цикла;
2. Критериями выбора потоков материалов для анализа движения железа в рамках производственного рециклинга.
Особенности методики. Методика включает в себя основную часть, в которой определяются баланс и параметры движения железа в производственном цикле предприятия, и вспомогательную часть. Во вспомогательную часть входят расчёты, с помощью которых определяются параметры потока вторичных материалов (т.е. параметры рециклинга материалов). Главной особенностью методики является анализ движения (потока) основного элемента – железа, а не металлургических материалов. Поток железа строится «непрерывным». Непрерывность достигается выполнением следующего правила: количество железа, содержащегося во всех материалах, формирующихся «на выходе» из предшествующего передела (цеха или другого подразделения предприятия), равно сумме количеств железа «на входе» в следующий за ним передел и железа всех видов отходов, попутных и вторичных материалов и выбросов всех видов, образовавшихся в предшествующем переделе. Таким образом, обеспечивается «прозрачность» потока основного элемента на всём протяжении производственного цикла.
Исходные данные:
– технические отчёты основных цехов предприятия;
– технологические инструкции;
– другая статистическая информация различных официальных источников;
– информация о балансовых плавках, спеканиях и т.п.;
|
– официальные отчеты геологических, санитарно-гигиенических и прочих служб;
– данные специальной литературы.
Блок-схема расчета приведена на рис. 17, а структура взаимосвязей между отдельными элементами математического описания – на рис. 18.
Общее количество элементов схемы зависит от структуры конкретного предприятия и составляет, как правило, 20…25 ед. (основных производственных подразделений металлургического комбината), количество потоков материалов достигает 130. Полный перечень металлургических материалов, которые учитывались при проведении расчетов (а также входили в блок-схему математического описания «ПОТОК») приведен в Приложении «Металлургические материалы, учитываемые в блок-схеме математического описания «ПОТОК».
Рис. 17. Блок-схема расчета математического описания «ПОТОК».
Рис. 18. Структура взаимосвязи между отдельными элементами математического описания. Потери железа на стадии транспортировки материалов Xk – Yl учитывались в составе Xkпот.
Расчёты выполняются в следующей последовательности:
– составление балансов железа для отдельных цехов (производств);
– построение схем движения железа с материалами производственного рециклинга (потоки G1…G4);
– построение схем движения (потоков) железа для основных групп металлургических переделов (потоки Xk, Yl, Zm);
– построение общей схемы движения железа во всём производственном цикле предприятия;
– составление макробаланса железа для предприятия в целом;
– составление макробалансов легирующих и примесных микроэлементов.
При анализе параметров производственного рециклинга на металлургическом предприятии полного цикла выделяются четыре основных потока материалов:
1. отсевы агломерата, окатышей и кокса, а также колошниковая пыль, поступающие из доменного цеха в агломерационное производство (G1);
2. окалина и сварочный шлак (G2);
3. стальной и чугунный лом, включающий: обрезь, брак, «недоливки», литники, лом валков, стружку образующиеся при работе МНЛЗ прокатных, сталеплавильных и литейных цехов (G3);
4. скрап чугунный и стальной всех видов (G4).
Условием сведения балансов железа, как для отдельных объектов схемы, так и для основных переделов (аглодоменного, сталеплавильного, прокатного) в целом является выполнение соотношения (рис. 18):
Таким образом, точность расчетов составляет 1 кг железа на тонну железа готовой продукции. В итоге балансы железа, макро- и микроэлементов предоставляют исчерпывающую информацию об общей степени их извлечения из всех металлургических материалов, поступивших на предприятие, в готовую продукцию и распространении в составе выбросов всех видов во все природные среды. Кроме того, они служат основой для определения мощности техногенных месторождений, формирующихся в регионах черной металлургии. Наиболее характерные параметры макробалансов железа интегрированных предприятий России, ЕС и Японии при производстве сортового и толстолистового проката приведены в таблицах 39, 40, 41.
|
Таблица 39. Макробаланс железа для производственного цикла ЗСМК
Статьи баланса | Период | |||
2000 | 2001 | 2002 | 2003 | |
Поступило в производственный цикл, всего | 5359582 | 5487383 | 5531245 | 4906400 |
металлолом «со стороны», % от общего прихода железа | 21,5 | 20,9 | 20,5 | 19,0 |
отложенный производственный рециклинг: шламы со «шламового поля»% от общего прихода железа | 0 | 0,8 | 0,9 | 1,0 |
Степень извлечения железа в готовую продукцию, % от прихода железа «со стороны» и шламов | 88,8 | 88,4 | 89,2 | 90,4 |
Железо рециклинга, кг/т железа готовой продукции | 175 | 182 | 187 | 189 |
в том числе: обрезь | 74 | 74 | 73 | 72 |
…….. мелкодисперсные материалы | 81 | 86 | 89 | 90 |
Таблица 40. Макробаланс железа для производственного цикла ОАО «Носта».
Статьи баланса | Период | |||
2004 | 2002 | 2001 | 2003 | |
Поступило в производственный цикл, всего | 309078 | 266271 | 236579 | 248108 |
в т. ч. металлолом «со стороны» | 99388 | 87071 | 78781 | 83116 |
% от прихода железа | 32,1 | 32,7 | 33,3 | 33,5 |
Перешло в готовую продукцию | 264259 | 225798 | 201565 | 244617 |
Степень извлечения железа в готовую продукцию, % от общего прихода железа | 85,5 | 84,8 | 85,2 | 86,1 |
Железо рециклинга, всего | 99398 | 104112 | 92975 | 95626 |
кг/т железа готовой продукции | 376 | 391 | 393 | 385 |
в т.ч. обрезь | 231 | 235 | 239 | 239 |
Таблица 41. Некоторые параметры макробалансов железа интегрированных предприятий России, ЕС и Японии при производстве сортового и толстолистового проката.
Показатель | Предприятия РФ | Предприятия ЕС и Японии |
Степень извлечения железа, % масс. | 90…92 | 92…93 |
Доля вторичных ресурсов (амортизационного лома) в приходе железа, % масс. | 18…22 | 25…27 |
Количество железа производственного рециклинга, кг/т железа проката | 170…200 | 130…150 |
Приведенные данные наглядно демонстрируют, что при близких значениях общей степени извлечения железа в готовую продукцию аналогичного качества, отечественные предприятия существенно уступают передовым мировым показателям использования вторичных ресурсов и производственного рециклинга. Анализ характерных макробалансов железа интегрированных предприятий черной металлургии России позволяет сделать следующие выводы:
1. Показатель «степень извлечения железа в готовую продукцию» с позиции принципов «социальной ответственности производителя» концепции «3R» не может служить исчерпывающей характеристикой эффективности применяемых технологий, поскольку в отечественных условиях он, как правило, достигается за счет высокой доли использования природных ресурсов и, соответственно, низком уровне переработки вторичных ресурсов.
2. Увеличение количества перерабатываемых вторичных ресурсов (амортизационного лома) в отечественных условиях обычно сопровождается увеличением количества материалов производственного рециклинга и связанных с их переработкой вторичных выбросов.
3. Для корректной оценки соответствия отечественных предприятий принципам «социальной ответственности производителя» концепции «3R» они должны обладать системой учета металлургических материалов, обеспечивающей «прозрачность» движения железа во всем производственном цикле предприятия. В частности, из технических отчетов подразделений предприятий следует исключить позиции «угар», «улет» и т.п., должна быть введена единая унифицированная система учета вторичных материалов, обеспечивающая погрешность балансов железа не более 1 кг/т анализируемого материала (т.е. не более 0,1 %).
4. Разработанные в последние годы концепции развития отечественных интегрированных предприятий черной металлургии не ориентированы на преимущественное использование вторичных ресурсов, т.е. не являются ресурсосберегающими /268…274/.
Для оценки соответствия металлургической технологии принципам «социальной ответственности производителя» концепции «3R» и требованиям ВАТ (BREF) предлагается ввести критерий: «Степень извлечения железа на интегрированном предприятии черной металлургии в Обществе рециклинга», μFe, % масс:
где μFe – степень извлечения железа, масс доля, % от прихода железа в производственный цикл в составе природных и вторичных ресурсов и материалов, депонированных на территории предприятия (материалов «отложенного» рециклинга),
Feприр. – количество железа, поступившее в производственный цикл непосредственно из природной среды, кг/т Fe готовой продукции,
Feвтор. – количество железа, поступившее в производственный цикл в составе вторичных ресурсов, кг/т Fe готовой продукции,
Feдеп. - количество железа, поступившее в производственный цикл в составе материалов «отложенного» рециклинга (+) или размещенное на территории предприятия в составе «отложенных» отходов (-), кг/т Fe готовой продукции,
Feвыб. – количество железа, безвозвратно потерянное в составе выбросов, кг/т Fe готовой продукции,
Feпр.рец. – количество железа, циркулирующее в производственном цикле предприятия в рамках производственного рециклинга, кг/т Fe готовой продукции,
φ – коэффициент безвозвратных потерь железа в составе вторичных выбросов, возникающих в процессах производственного рециклинга, доли ед.,
Fe∑ - общее количество железа, поступившее в производственный цикл в составе природных и вторичных ресурсов (в том числе материалов, депонированных на территории предприятия - материалов «отложенного» рециклинга).
В зависимости от структуры выпускаемой продукции для отечественных условий должны быть научно обоснованы максимально допустимые значения Feприр., Feвыб., Feпр.рец. и минимальный уровень Feвтор. Ключевым параметром является уровень использования вторичных ресурсов амортизационного лома /97, 99, 100, 112, 113, 276…278/. Поэтому грамотный прогноз количества его образования и структуры становится существенным определяющим фактором в формирующейся системе государственного регулирования потребления вторичных ресурсов железа. Подобный прогноз, как показывают результаты последних исследований /58, 100, 103, 112, 277, 278/, не может опираться на привычные параметры «норма сбора лома» и «средний срок эксплуатации стальных изделий». Он должен строиться исходя из современной методологии исследований, которую активно разрабатывают в передовых индустриально развитых странах.
Элементопоток марганца.
Рассчитаны характерные балансы марганца для интегрированных предприятий черной металлургии передовых индустриальных стран и России. При составлении балансов использованы данные источников /198…203, 104…109, 264, 265, 279…281/, а также Международного института черной металлургии (IISI), Национального консультативного совета по материаловедению (NMAB) и Бюро технической оценки проектов при Конгрессе США (OTA). В качестве основных исходных допущений были приняты следующие:
· производительность комбината составляет 5 млн. т. стального проката в год;
· сырьевая база представлена рудами Курской магнитной аномалии и углями Кузнецкого бассейна;
· расходные коэффициенты сырьевых материалов (железорудных концентратов, окатышей, коксующихся углей, металлолома, флюсов и т. п.), продуктов металлургических переделов и вторичных материалов (оборотного лома, шлаков, шламов и проч.) соответствуют условиям работы предприятий Европейской части России.
Вариант №1 соответствует технологической схеме с использованием конверторного производства и выплавкой рядовых углеродистых сталей, а вариант №2 – до сих пор применяемой в нашей стране схеме производства марганцовистых сталей в мартеновских печах (таблица 42).
Таблица 42. Баланс марганца при производстве проката на интегрированных предприятиях черной металлургии, кг/т проката:
Статья баланса | Передовые страны ЕС и США |
Россия | ||||
1980 | 1990 | 2000 | 2005 | ЗСМК | «Носта» | |
Приход | ||||||
Железорудные материалы, флюсы, коксующиеся угли | 4,38 | 4,02 | 3,22 | 3,12 | 3,61 | 2,89 |
Марганцевые руды | 0,64 | 0,86 | 0,43 | 0,32 | 1,70 | - |
Металлолом "со стороны" | 1,69 | 1,89 | 2,31 | 2,42 | 0,71 | 1,12 |
Ферросплавы | 5,40 | 4,35 | 4,17 | 4,01 | 4,60 | 12,27 |
Приход «со стороны», итого | 12,11 | 11,15 | 10,13 | 9,87 | 10,62 | 16,28 |
Конверторный шлак | 1,41 | 1,91 | 2,95 | 3,12 | 1,85 | - |
Приход, итого: | 13,52 | 13,06 | 13,08 | 12,99 | 12,47 | 16,28 |
Расход | ||||||
Стальной прокат | 6,26 | 6,01 | 6,44 | 6,52 | 4,35 | 8,92 |
Доменный шлак, корольки, шлам, пыль | 1,26 | 1,29 | 0,95 | 0,85 | 1,80 | 0,90 |
Сталеплавильные шлаки, корольки, шлам, пыль | 5,80 | 5,60 | 5,55 | 5,50 | 6,05 | 6,25 |
Не уловленная пыль | 0,20 | 0,16 | 0,14 | 0,12 | 0,27 | 0,21 |
Доля марганца, перешедшего в прокат, % от прихода "со стороны" | 51,7 | 53,9 | 63,6 | 66,1 | 41,0 | 54,8 |
Доля марганца конверторного шлака, подвергаемого производственному рециклингу, % | 24,3 | 34,1 | 53,2 | 56,7 | 30,6 | - |
Расход марганца природных ресурсов на производство готовой продукции, кг/кг Mn проката | 1,66 | 1,54 | 1,21 | 1,14 | 2,70 | 1,70 |
Вариант № 1 – на основе данных ОАО ЗСМК, 2005 год
Вариант № 2 – на основе данных ОАО «Носта», 2005 год
На передовых зарубежных предприятиях четко прослеживается тенденция существенного увеличения поступления марганца в производственный цикл в рамках глобального (с металлоломом) и производственного (в частности с конверторным шлаком) рециклинга. За двадцать пять (с 1980 по 2005 год) лет это позволило добиться повышения степени перехода марганца в готовую продукцию из материалов, поступающих на предприятие со стороны почти на 12% (с 51,7% до 63,6%). Для отечественных предприятий данный показатель до сих пор составляет немногим более 40% и существенно уступает схеме с использованием мартеновских печей. Расход марганца природных ресурсов (руд, флюсов, углей и ферросплавов) на производство готовой продукции (кг/кг Mn проката) на предприятиях ведущих индустриальных стран понизился с 1,66 до 1,14. В России он до сих пор находится на уровне 2,7.
Важно отметить, что низкий уровень использования вторичных материалов заставляет применять в производстве марганцевые руды, расход которых на предприятиях черной металлургии России почти в 4 раза превосходит передовые зарубежные показатели. При этом не используются возможности повышения прихода марганца с металлоломом и конверторным шлаком. На последнем материале следует остановиться особо. По объему образования на металлургических заводах конвертерные шлаки занимают второе место после доменных. Поэтому до сих пор актуальными остаются проблемы снижения выхода шлака и его максимального использования в собственном производстве и других отраслях индустрии.
Технологический маршрут, который позволил бы минимизировать объем образующегося шлака и связанные с ним затраты и, вместе с тем, обеспечил бы высокую производительность зависит от многих факторов. На его выбор оказывают влияние наличие и качество сырья, состав оборудования завода, маркетинговая стратегия и сортамент продукции, а также экономические факторы, действующие по отдельности и совместно. Например, металлургические предприятия США, как правило, предпочитают не применять предварительную обработку чугуна, так как стремятся к высокой доле лома в завалке конвертеров, когда требуется высокое содержание кремния в жидком чугуне, заливаемом в конвертер.
Основными отраслями индустрии, в которых применяются конверторные шлаки, являются автодорожная и строительная промышленность. Однако использование конверторного шлака зависит от конкретной ситуации на отдельном заводе. Например, в Китае основное внимание уделяется производству цемента. Завод фирмы POSCO в Корее больше внимания уделяет использованию шлака для частичной или полной замены флюса в доменных печах и на агломерационных фабриках.
В Японии активное применение конвертерного шлака началось в 1980-х годах, когда около 40% всего образующегося шлака использовали для подъема грунта. Однако в дальнейшем неуклонно увеличивалось потребление конверторного шлака в качестве вторичного сырья.
Богатый опыт переработки металлургических шлаков имеют страны Евросоюза. Наиболее показательно отношение к этой проблеме в Германии, где уже в 1949 г. было организовано специальное научно-техническое общество - РЕПЗ - для всестороннего исследования свойств металлургических шлаков с целью их максимального использования в промышленности и сельском хозяйстве. В 1995 г. было принято решение об исключении металлургических шлаков из Европейского каталога отходов и Европейских правил обращения отходов в Европейском сообществе. В 2000 г РЕПЗ стал ядром общеевропейской ассоциации шлаков ЕВРОШЛАК, которая была основана Европейской конференцией по шлакам в Дюссельдорфе.
В настоящее время в странах ЕС конверторные шлаки применяются в трех основных направлениях: для вторичной переплавки в доменных печах, в качестве оснований дорог и составляющих асфальтобетонных покрытий, а также для рекультивации почв. При этом наиболее перспективным признается вариант использования шлака в рамках производственного рециклинга, и активно исследуются возможности его вдувания в доменные печи с целью улучшения условий шлакообразования.
3.5. Элементопоток галлия в металлургическом цикле интегрированного предприятия (на примере ОАО «НТМК»).
О повышенном содержании галлия в железных рудах известно давно /282/, в СССР в 60-80-е годы XX века проводили специальные геолого-оценочные работы по установлению содержания галлия в железных рудах. Повышенная концентрация галлия характерна для титаномагнетитовых руд Качканарского ГОК, который является главным источником железорудного сырья для ОАО «НТМК» и ОАО «Чусовской металлургический завод». Исследования титаномагнетитовых руд Качканарского месторождения проводились в 1990-х годах специалистами ГИРЕДМЕТ /283/.
В работе /283/ отмечается, что анализы руд, концентратов и других металлургических материалов на содержание галлия выполнены по специально разработанной методике количественного спектрального анализа с предварительной селективной возгонкой из камерных электродов. «Метод отличается очень высокой чувствительностью и точностью — нижний предел определения галлия 0,0001 % (1 г/т или 1 ррm). Точность определения для содержаний 0,0001-0,001 % —10 % (отн.), для содержаний от 0,001 % и выше — 7 % (отн.)». Результаты анализов приведены в Приложении «Содержание галлия в металлургических материалах Качканарского ГОК и ОАО «НТМК» по данным ГИРЕДМЕТ».
Наиболее высокое содержание галлия (45…52 г/т) характерно для титаномагнетитовых сырьевых материалов Качканарского ГОКа. В чугуне содержание галлия повышается почти в 1,5 раза и достигает 65…80 г/г. «Высокогаллиеносными» продуктами передела железорудного сырья в условиях ОАО «НТМК» являются пыли сталеплавильного производства и возгоны вакуумной обработки чугуна и стали, содержащие до 200 г/т галлия. Теоретические исследования по термодинамике и кинетике процесса возгонки галлия, выполненные в ГИРЕДМЕТ, свидетельствуют о том, что при вакуумной обработке чугуна галлий переходит в газовую фазу в виде GaS.
Для количественной оценки движения галлия в качестве микропримесного элемента была построена схема его элементопотока в металлургическом цикле ОАО «НТМК» (рисунок 19, таблиц 43).
Рисунок 19. Схема элементопотока галлия при производстве ванадиевого чугуна в ОАО «НТМК», г/т чугуна
Таблица 43. Содержание галлия в металлургических материалах, г/т
Материал | По данным ГНЦ «Гиредмет» | По данным МИСиС | ||
материала | чугуна | материала | чугуна | |
Железная руда | 17,2 | 105,5 | 23,9 | 146,5 |
Пыль (ж.р.) | 17,6 | 0,9 | 23,5 | 1,2 |
Концентрат | 81,7 | 85,0 | 121,1 | 126,0 |
Пыль (концентрат) | 3,8 | 19,1 | 3,8 | 19,3 |
Хвосты | 80,8 | 2,1 | 119,2 | 3,1 |
Агломерат | 51,1 | 35,8 | 78,3 | 54,8 |
Окатыши | 45,7 | 47,1 | 66,1 | 68,1 |
Кокс | 5,8 | 2,6 | 5,8 | 2,6 |
Пыль колошниковая | 100,0 | 2,2 | 200,0 | 4,4 |
Шлак | 1,1 | 0,4 | 1,1 | 0,4 |
Пыль н.у(ДП). | 102,4 | 5,6 | 199,3 | 10,9 |
Чугун | - | 77,3 | - | 112,0 |
Ванадийсодержащие титаномагнетиты Качканарского месторождения, являющегося железорудной базой комбината, содержат 45…52 г галлия /т руды. С ними в производственный цикл предприятия поступает 105,5…146,5 г галлия / т чугуна. В чугун переходит 77,3…112,0 г галлия. Таким образом, сквозной коэффициент извлечения галлия составляет порядка 75 %.
Большая часть потерь галлия (около 15 % от его прихода с рудой) происходит в процессе обогащения руды. Прочие потери (с пылью и доменным шлаком) незначительны. Баланс галлия для условий НТМК представлен в таблице 44.
Таблица 44. Баланс галлия, г/т чугуна
Поступает в производство | Получается в процессе производства | ||||
По данным «Гиредмет» | По данным МИСиС | По данным «Гиредмет» | По данным МИСиС | ||
Железная руда | 105,5 | 146,5 | Пыль | 25,7 | 31,4 |
Кокс | 2,6 | 2,6 | Хвосты | 2,1 | 3,1 |
Шлак | 1,1 | 1,1 | |||
Чугун | 77,3 | 112,0 | |||
Итого | 108,1 | 149,1 | Итого | 108,1 | 149,1 |
С колошниковой пылью циркулирует: 2,2 г/т чуг. (ГИРЕДМЕТ), 4,4 г/т чуг. (МИСиС
3.6. Баланс углерода и методология оценки энергоэффективности производства черных металлов и выбросов СО2.
Проблема энергосбережения в развитии современной цивилизации имеет две важнейшие особенности: с одной стороны, принятая мировым сообществом концепция «устойчивого развития» требует динамичного роста производства энергии; с другой стороны, именно энергетические агрегаты и установки по-прежнему являются основными производителями выбросов всех видов. В связи с этим главными приоритетами в развитии производства и потребления энергии в рамках Ресурсо-экологической концепции являются:
– Снижение последствий производства, передачи и потребления энергии для окружающей среды;
– Оптимизация структуры потребления природных энергоресурсов;
– Увеличение доли потребления вторичных энергоресурсов (ВЭР);
– Снижение энергоёмкости оборудования за счет совершенствования технологии производства.
Черная металлургия является одной из наиболее энергопотребляющих отраслей промышленности. При этом ей присущи характерные особенности:
1. Основу топливного баланса металлургических предприятий составляют коксующиеся угли – дефицитное высококачественное сырье, весьма специфичное по химическому составу.
2. Используемое в металлургических процессах топливо, как правило, выполняет множественные функции: оно не только является источником энергии, но также играет роль восстановителя и «поставщика» элементов - микропримесей.
3. В черной металлургии, как ни в какой другой отрасли индустрии, высока доля ВЭР, представленных газами – наиболее технологичным видом энергоресурсов.
Наглядно вышеупомянутые обстоятельства и вытекающие из них проблемы подхода к оценке эффективности затрат энергии можно представить в виде таблицы 45.
Вплоть до настоящего времени энергоэффективность производства металлов часто оценивается показателем энергоёмкости вырабатываемой продукции, выраженной в единицах условного топлива (1 т.у.т. = 7000 ккал). При этом затраты всех видов энергии в виде топлива, электрической и тепловой энергии на всех стадиях производства суммируются и из полученной величины вычитается энергия, произведенная энергетическим хозяйством предприятия в виде электроэнергии, пара, горячей воды, сжатого воздуха и т.п. Вычисленный таким образом параметр имеет следующие недостатки: во-первых, он никаким образом не связан с последствиями функционирования предприятия для окружающей среды и, во-вторых, не дает информации об уровне использования вторичных энергоресурсов, а лишь показывает абсолютную величину энергии, вырабатываемой при их утилизации.
Предлагаемая методика оценки энергоэффективности производства металла базируется на составлении балансов основных энергетических элементов: углерода и водорода, а также электроэнергии. Центральное место при этом занимает баланс углерода, который составляется для всего производственного цикла получения металла от добычи сырья и источников энергии до обращения с производственными и отложенными отходами /8, 137…142/.
Таблица 45. Методические проблемы оценки эффективности энергосбережения в черной металлургии.
Особенности энергопотребления в черной металлургии | Факторы, требующие учета и специальной методической проработки | Проблемы отраслевого уровня | Проблемы регионального и глобального масштаба |
Высокая энергоемкость металлургических агрегатов | Балансы углерода, водорода и электроэнергии | Уменьшение энергоемкости Оптимизация использования различных видов топлив | Распределение электроэнергии |
Специфичность основного источника энергии (кокса) | Микропримесный состав коксующихся углей | Комплексная переработка металлургических углей | Развитие производства попутной продукции |
Множественность функций металлургических топлив | Металлургические свойства топлива. Взаимозависимости между показателями потребления энергии, восстановительных процессов и интенсивность плавки | Минимизация расхода топлива без потери устойчивости процесса | Снижение выбросов «парниковых газов» |
Высокая доля ВЭР | Параметры энергетической ценности и технологичности ВЭР. Эффективность газоочистных сооружений | Увеличение доли ВЭР в тепловом и энергетическом балансах предприятий | Уменьшение производства ЗШО с последующей ликвидацией ЗШН |
Анализ энергоэффективности работы предприятий черной металлургии на основе балансов углерода позволяет:
– сопоставить долю различных видов энергии, используемых при производстве чугуна и стали,
– получить информацию о наиболее масштабных и токсичных выбросах в окружающую среду, например: золошлаковых отходов (ЗШО) и шламов различных процессов на поверхность земли, оксида и диоксида углерода и углеводородов – в атмосферу.
Баланс углерода строится в разме
|
|
Опора деревянной одностоечной и способы укрепление угловых опор: Опоры ВЛ - конструкции, предназначенные для поддерживания проводов на необходимой высоте над землей, водой...
Архитектура электронного правительства: Единая архитектура – это методологический подход при создании системы управления государства, который строится...
Индивидуальные и групповые автопоилки: для животных. Схемы и конструкции...
Адаптации растений и животных к жизни в горах: Большое значение для жизни организмов в горах имеют степень расчленения, крутизна и экспозиционные различия склонов...
© cyberpedia.su 2017-2024 - Не является автором материалов. Исключительное право сохранено за автором текста.
Если вы не хотите, чтобы данный материал был у нас на сайте, перейдите по ссылке: Нарушение авторских прав. Мы поможем в написании вашей работы!