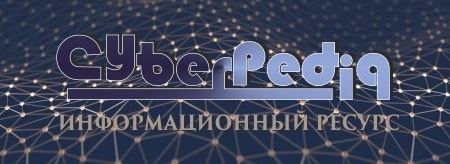
Опора деревянной одностоечной и способы укрепление угловых опор: Опоры ВЛ - конструкции, предназначенные для поддерживания проводов на необходимой высоте над землей, водой...
Общие условия выбора системы дренажа: Система дренажа выбирается в зависимости от характера защищаемого...
Топ:
Установка замедленного коксования: Чем выше температура и ниже давление, тем место разрыва углеродной цепи всё больше смещается к её концу и значительно возрастает...
Методика измерений сопротивления растеканию тока анодного заземления: Анодный заземлитель (анод) – проводник, погруженный в электролитическую среду (грунт, раствор электролита) и подключенный к положительному...
Марксистская теория происхождения государства: По мнению Маркса и Энгельса, в основе развития общества, происходящих в нем изменений лежит...
Интересное:
Лечение прогрессирующих форм рака: Одним из наиболее важных достижений экспериментальной химиотерапии опухолей, начатой в 60-х и реализованной в 70-х годах, является...
Уполаживание и террасирование склонов: Если глубина оврага более 5 м необходимо устройство берм. Варианты использования оврагов для градостроительных целей...
Подходы к решению темы фильма: Существует три основных типа исторического фильма, имеющих между собой много общего...
Дисциплины:
![]() |
![]() |
5.00
из
|
Заказать работу |
|
|
На основании данных о химическом составе металлургических материалов и показателях работы доменных печей исследуемых предприятий были построены характерные балансы микроэлементов доменной плавки. Для оценки возможности конденсации примесных элементов из газовой фазы на поверхность выносимых из печи частиц пыли, введены коэффициенты концентрации элементов в колошниковой пыли (КККП) и доменном шламе (ККДШ):
КККП = % ЭКП/ % ЭШ
ККДШ= % ЭДШ/ % ЭШ
где, % ЭШ – содержание элемента в шихте с учетом всех компонентов, включая кокс,
% ЭКП – содержание элемента в колошниковой пыли,
% ЭДШ – содержание элемента в доменном шламе.
Были выполнены расчеты показателей КККП и ККДШ для элементов основы, макро - и микропримесных элементов. Результаты расчетов показали, что КККП для всех групп элементов изменяется в пределах от 0,5 до 1,5 ед. Из этого можно сделать вывод о том, что конденсация возгонов элементов на поверхности относительно крупных частиц колошниковой пыли не оказывает существенного влияния на изменение их состава. Вместе с тем, для некоторых макро – и микропримесных элементов (таблица 50), было отмечено существенное увеличение значений коэффициента ККДШ - до 3,0…5,0, а в отдельных случаях до 50…60 единиц. Принимая во внимание данные о последних исследованиях образования мелких фракций пыли в доменной печи, в этом случае можно говорить о развитии процессов адсорбции элементов из газовой фазы /308…312/. Таким образом, коэффициент ККДШ можно использовать в качестве индикатора перехода микроэлемента в газовую фазу доменного процесса.
Как уже указывалось выше, поведение микроэлементов в доменном процессе зависит от того, в каком виде (соединении, окружении) они попадают в агрегат. Рассмотрим два основных способа поступления микроэлементов в доменную печь.
|
Первый способ (поток): приход в минеральных соединениях, которые составляют основу железосодержащих компонентов шихты, а также присутствуют в коксе – IА;
Второй способ (поток): приход в составе органических соединений, присутствующих только в коксе, при этом рассматриваемый элемент находится в структуре органических молекул (металлорганика) – IB. Для определения количества микроэлемента в органической части кокса (ОЧК) использовались данные исследований Юдовича, Кетриса и др. /317, 319, 320/.
Введем размерность потоков в граммах элемента на тонну чугуна. Тогда общий приход элемента составит:
I = IА + IB
Обозначим ρ = IА / I – минеральную часть прихода элемента, и η = IB / I – органическую часть прихода.
С учетом того, что каждый микроэлемент в доменном процессе распределяется в три основные среды: жидкий чугун; жидкий шлак; газовую фазу, введем обозначения коэффициентов распределения (перехода) элемента в эти среды:
γ1 – доля перехода в чугун,
γ2 – доля перехода в шлак,
γ3 – доля перехода в газ.
Переход в каждую среду происходит из обоих потоков IА и IB и может осуществляться различными путями (по различным каналам). Под путями (каналами) подразумеваются различные механизмы переходов, которых в каждом конкретном случае может быть несколько (больше или меньше в зависимости от свойств элемента и его соединений и характеристик среды, в которую он переходит).
Пусть λi – производительность i – ого канала (механизма перехода), которая показывает, какую долю прихода элемента из минеральной или органической части переводит данный канал в одну из трех металлургических сред. Величина λi зависит от изменения энергии Гиббса ΔG при i – ом переходе:
λi = ,
где ai – коэффициент, учитывающий структурные, геометрические и прочие факторы, характеризующие процесс перехода.
Тогда полный коэффициент перехода данного элемента в каждую из трех металлургических сред складывается из двух слагаемых;
|
,
Первое слагаемое представляет собой суммарную долю элемента при переходе из минеральной части его общего потока, второе – суммарную долю перехода из органической части; индексы k и l обозначают каналы перехода из минеральной и органической частей соответственно.
Для расчета (оценки) производительности каналов необходим набор физико-химических критериев, описывающих конкретные этапы взаимодействия элемента с компонентами доменного процесса. В качестве основных критериев были выбраны: химическое сродство элемента к «активным компонентам» металлургической системы: кислороду, водороду, сере, хлору, а также растворимость в железе. Для каждого активного компонента был определен набор характеристик:
– наличие химических соединений с данным компонентом;
– области температурной и химической устойчивостей химических соединений;
– доли элемента, связанные в каждом из возможных соединений при заданных условиях;
– летучесть соединений (давление насыщенных паров).
Анализ перечисленных характеристик позволяет найти эффективные значения изменений энергий Гиббса ΔGi для процессов перехода исследуемого микроэлемента, поступающего в доменную печь двумя различными способами, в каждую из трех металлургических сред. Для оценки коэффициентов ai в каждом конкретном случае использовались параметры:
– общий приход элемента в доменную печь,
– растворимость элемента в металле и оксидном (шлак) расплаве,
– возможность формирования самостоятельной фазы (свинец, лантаноиды) и контуров циркуляции (литий, рубидий) и некоторые другие факторы.
В таблицах 50, 52…55 и Приложении «Балансы микроэлементов доменной плавки» приведены основные данные, позволяющие подразделить микропримесные элементы доменной плавки в соответствии с их распределением между основными фазами процесса.
Таблица 50. Подразделение микропримесные элементы доменной плавки в соответствии с их распределением между основными фазами процесса.
Группа | Микроэлементы | Характерные параметры | |||||
Присут- ствие в ОЧК | Переход в чугун | Переход в шлак | ККДШ более 3,0 ед. | Наличие невязки баланса | |||
Первая | барий, цирконий | + | - | + | - | - | |
литий, рубидий | + | - | + | - | + | ||
бериллий, иттрий, лантаноиды скандий, | + | - | + | - | + | ||
стронций | + | - | + | + | - | ||
Вторая
| бор, хром | + | + | + | - | - | |
ванадий, мышьяк, фосфор | + | + | + | + | - | ||
Третья | кобальт, медь | + | + | - | - | - | |
галлий, никель | + | + | - | + | - | ||
Четвертая | молибден | - | + | - | - | - | |
олово, сурьма | - | + | - | + | - | ||
свинец | - | + | - | + | + |
Можно выделить четыре группы микроэлементов. В трех группах представлены элементы, попадающие в доменную печь как в составе минеральной составляющей, так и в органической части кокса. Элементы первой группы в целом ведут себя аналогично шлакообразующим (алюминию, кальцию, магнию) и практически полностью переходят в оксидный расплав. Однако при этом для стронция отмечается значительная возгонка и накопление в шламе, а для лантаноидов и бериллия – невязка баланса. Данные по литию и рубидию практически соответствуют их «химическим» аналогам - натрию и калию.
Элементы второй группы распределяются между металлическим и шлаковым расплавом (в целом аналогично марганцу или кремнию), но для ванадия, мышьяка и фосфора имеет место значимый (ККДШ ~ 3,5 ед.) переход в газовую фазу процесса. Элементы третьей группы практически полностью переходят в чугун. При этом для никеля и галлия отмечается также переход в газовую фазу (ККДШ ~ 3,5 ед.).
Для элементов четвертой группы характерен приход в доменную печь только в составе минеральной составляющей шихты, они распределяются между чугуном и газовой фазой процесса. При этом для олова и свинца отмечаются самые высокие значения ККДШ – от 50 до 60 ед., а для свинца еще имеет место невязка баланса на уровне 20…25 % отн.
Проиллюстрируем использование предложенной расчетной схемы описанием определения коэффициентов перехода микроэлементов в газовую фазу (в возгоны). Выберем элементы, отличающиеся друг от друга химическими свойствами и проявляющие различные типы поведения в доменном процессе (относящиеся к различным группам таблицы 50). В таблице 51 приведены некоторые исходные данные и результаты расчетов. Значения η и φ (доля элемента перешедшего в шлам от его общего прихода в печь) являются усреднением заводских данных, полученных на четырех металлургических предприятиях: ОАО «Северсталь», ОАО «Тулачермет» и ОАО НЛМК (Россия), «ЭКО-Шталь» (Германия).
|
Таблица 51. Параметры перехода микроэлементов в газовую фазу доменного процесса.
Показатель | Микроэлементы | |||||||
Барий | Цирконий | Стронций | Фосфор | Медь | Галлий | Никель | Олово | |
η, масс % | 23 | 7 | 10,2 | 20 | 13 | 8,5 | 4,7 | 0 |
φ, масс % | 1,2 | 1,2 | 4,2 | 4,2 | <3,1 | 3,0 | 3,6 | 33,6 |
γ3, масс % | 3 | ≈0,5 | 6,7 | ~ 15 | > 1,4 | ≈ 2,6 | 4,2 | ≈50 |
Анализ полученных результатов позволяет утверждать, что разработанная методика достаточно точно количественно описывает распределение микроэлементов между основными фазами доменного процесса. Ниже приводится краткое описание поведения в доменной плавке некоторых элементов только на базе анализа балансовых и термодинамических расчетов, а в последующих разделах главы – подробное описание поведения галлия, стронция, мышьяка, свинца и фосфора, полученное по итогам физического моделирования и анализа опубликованных результатов специальных исследований других авторов.
Барий практически не восстанавливается до металла в доменной печи и мало растворим в железе, что сокращает до минимума возможности его перехода в газ из минеральной части (таблица 52). Его возгонка из органической части возможна либо в виде летучих оксидов, либо в соединениях с хлором. Поскольку приход бария в доменную печь намного превышает приход хлора, то переход его в газовую фазу в составе соединений с хлором незначителен. Учет этого и некоторых других критериев позволяет для бария получить долю перехода в газ: γ3Ba = 3%.
Таблица 52. Характерные балансы бария при выплавке передельного чугуна, г/ т чугуна.
Статья баланса | Предприятие | |||
«Северсталь» | НЛМК | «Тулачермет» | EKO-Stahl | |
Приход в доменные печи: | ||||
с железорудной частью | 110 | 130 | 250 | 400 |
с коксом | 90 | 270 | 250 | 110 |
в том числе с ОЧК | 45 | 135 | 125 | 55 |
Приход итого, г/ т чугуна | 200 | 400 | 500 | 510 |
Переходит в ходе доменной плавки | ||||
в чугун | нет | нет | нет | нет |
в шлак | 195 | 390 | 480 | 500 |
в колошниковую пыль | 3 | 6 | 10 | 5 |
в доменный шлам | 2 | 4 | 10 | 5 |
Цирконий (таблица 53) имеет очень стойкие оксиды, которые совершенно не могут восстанавливаться при доменном процессе. Сам цирконий и его соединения почти не газифицируются независимо от того, находятся ли они в минеральной или в органической части. Очень незначительная газификация оксида ZrO2 возможна лишь в окислительной среде при температуре не ниже 22000С, т.е. в фурменной зоне. При этом максимальное количество циркония в газе может составить около γ3Zr ≈ 0,5%.
Таблица 53. Характерные балансы циркония при выплавке передельного чугуна, г/т чугуна.
|
Статья баланса | Предприятие | |||
«Северсталь» | НЛМК | «Тулачермет» | EKO-Stahl | |
Приход в доменные печи: | ||||
с железорудной частью | 95 | 15 | 50 | 75 |
с коксом | 30 | 30 | 120 | 6 |
в том числе с ОЧК | 5 | 5 | 20 | 1 |
Приход итого, г/ т чугуна | 125 | 45 | 170 | 81 |
Переходит в ходе доменной плавки | ||||
в чугун | нет | нет | нет | нет |
в шлак | 122 | 43 | 165 | 80 |
в колошниковую пыль | 2 | 1 | 3 | 0,5 |
в доменный шлам | 1 | 1 | 2 | 0,5 |
Стронций, также как барий, почти не восстанавливается до металла, устойчивые соли стронция и другие его соединения из рудной части шихты легко переходят в шлак. Возгоняться из минеральной части может только гидрооксид при температурах выше 10000С. Кроме того, в газ могут переходить атомы стронция из органической части кокса. Общая доля стронция в газе составляет γ3Sr= 6,7%.
Галлий при температурах 950 – 11000С газифицируется в виде оксида или сульфида из органической части кокса. Термодинамический анализ показывает, что в летучие соединения может переходить до 30% галлия из органической части. Это значит, что γ3Ga ≈ 2,6%. Кроме того, небольшое количество галлия может попасть в газ из минеральной части в виде хлорида, это количество зависит от состава шихты и содержания в ней хлора и серы. Остальной галлий при восстановлении в твердом состоянии растворяется в железе и переходит в чугун.
Медь (таблица 54)должна переходить в газовую фазу из органической части кокса в виде летучих сульфидов и гидридов. Кроме того, в газ может переходить часть меди из минеральной части шихты также в соединениях с серой. Эта часть может сильно варьироваться в зависимости от состава шихты. Остальная часть меди при температурах свыше 13000С восстанавливается и, имея хорошую растворимость в железе, может переходить в чугун. Общее содержание меди в газовой фазе должно быть не менее γ3Cu > 1,4%. Возможно, что низкое содержание меди в шламе объясняется формированием в доменной печи контура циркуляции сульфидов меди (например, аналогично сульфидам свинца). В итоге, основная часть газообразного сульфида меди поглощается шлаковой фазой процесса, и практически вся медь переходит в чугун.
Таблица 54. Характерные балансы меди при выплавке передельного чугуна, г/ т чугуна.
Статья баланса | Предприятие | |||
«Северсталь» | НЛМК | «Тулачермет» | EKO-Stahl | |
Приход в доменные печи: | ||||
с железорудной частью | 5 | 25 | 40 | 60 |
с коксом | 10 | 20 | 5 | 5 |
в том числе с ОЧК | 4 | 8 | 2 | 2 |
Приход итого, г/ т чугуна | 15 | 45 | 45 | 65 |
Переходит в ходе доменной плавки | ||||
в чугун | 15 | 45 | 45 | 65 |
в шлак | нет | нет | нет | нет |
в колошниковую пыль | менее 1 | менее 1 | менее 1 | менее 1 |
в доменный шлам | менее 1 | менее 1 | менее 1 | менее 1 |
Никель (таблица 55) легко восстанавливается в условиях доменного процесса и, кроме того, почти полностью растворим в железе, что позволяет всей его доле, содержащейся в минеральной части почти полностью перейти в чугун. Переход никеля в газ опять-таки возможен только из органической части кокса. Этот переход может быть растянут от температуры 13000С, когда появляется газообразный гидрид никеля и газифицируются атомы чистого никеля из коксовой органики, до 16000С. Суммарная доля никеля, переходящая в газовую фазу составляет γ3Ni= 4,2%.
Таблица 55. Характерные балансы никеля при выплавке передельного чугуна, г/ т чугуна.
Статья баланса | Предприятие | |||
«Северсталь» | НЛМК | «Тулачермет» | EKO-Stahl | |
Приход в доменные печи: | ||||
с железорудной частью | 45 | 65 | 50 | 150 |
с коксом | 20 | 15 | 15 | 20 |
в том числе с ОЧК | 5 | 3 | 3 | 5 |
Приход итого, г/ т чугуна | 65 | 80 | 65 | 170 |
Переходит в ходе доменной плавки | ||||
в чугун | 60 | 75 | 60 | 165 |
в шлак | нет | нет | нет | нет |
в колошниковую пыль | 1 | 1 | 1 | 1 |
в доменный шлам | 4 | 4 | 4 | 4 |
ККДШ | ~3,5 | ~3,5 | ~3,5 | ~3,5 |
Олово (таблица 56), которое практически не присутствует в органической части кокса, вместе с тем легко возгоняется из минеральной части уже при температурах выше 9000С в виде хлорида, оксида, сульфида и в виде паров металлических атомов. При температуре выше 1200 – 13000С восстановленное олово может растворяться в твердом восстановленном железе, а также захватываться каплями металлического расплава и переходить в чугун. Таким образом, в газ попадает та часть олова, которая успела газифицироваться до этих температур: γ3Sn ≈ 50%.
Таблица 56. Характерные балансы олова при выплавке передельного чугуна, г/ т чугуна.
Статья баланса | Предприятие | |||
«Северсталь» | НЛМК | «Тулачермет» | EKO-Stahl | |
Приход в доменные печи: | ||||
с железорудной частью | 35 | 15 | 15 | 20 |
с коксом | нет | нет | нет | нет |
Приход итого, г/ т чугуна | 35 | 15 | 15 | 20 |
Переходит в ходе доменной плавки | ||||
в чугун | 20 | 10 | 10 | 15 |
в шлак | нет | нет | нет | нет |
в колошниковую пыль | менее 1 | менее 1 | менее 1 | менее 1 |
в доменный шлам | 15 | 5 | 5 | 5 |
ККДШ | 40,0 | 30,0 | 30,0 | 50,0 |
Галлий.
В последние годы резко возрос интерес к исследованиям поведения в доменной плавке микроэлементов, попадающих в печи в составе техногенных материалов. Технологии их рециклинга активно внедряются в передовых индустриальных странах в рамках реализации «Инициативы 3R». Типичным примером такого микроэлемента является галлий, который широко используется при производстве полупроводниковых интерметаллических соединений, применяющихся в электронике, электротехнике и производстве лазерных фотодиодов. Отметим, что галлий входит и в состав природных сырьевых материалов доменной плавки. Он присутствует практически во всех коксующихся углях и железных рудах /282, 283, 336…340/.
Исследования по определению содержания галлия в металлургических материалах отечественных (ОАО «Северсталь», ОАО НЛМК, ОАО «Тулачермет», ОАО НТМК) и зарубежных предприятий (EKO-Stahl, Германия) были выполнены в МИСиС и ГНЦ «Гиредмет». Установлено, что в ходе плавки галлий переходит в чугун и концентрируется в доменном шламе. Причем содержание галлия в шламе достигает 200…300 г/т шлама, что в 3 – 5 раз превосходит его содержание в доменной шихте. Таким образом, поведение в доменной плавке галлия принципиально отличается от его химического аналога – алюминия, который полностью переходит в шлак. Характерные балансы галлия для некоторых исследованных предприятий приведены в таблице 57.
Таблица 57. Характерные балансы галлия при выплавке передельного чугуна, г/ т чугуна.
Статьи баланса | Предприятие | ||
«Северсталь» | «Тулачермет» | «EKO-Stahl» | |
Приход в доменные печи: | |||
с железорудной частью | 140 | 90 | 30 |
с коксом | 15 | 15 | 10 |
Приход итого, | 155 | 105 | 40 |
Переходит в ходе доменной плавки | |||
в чугун | 150 | 100 | 35 |
в шлак | нет | нет | нет |
в доменный шлам | 5 | 5 | 5 |
Исследование железо – галлий – алюминиевых (ЖГА) брикетов и окатышей. ЖГА брикеты и окатыши массой от 18 до 24 грамм, были подвергнуты сначала окислительной (при температуре 1200о С), а затем восстановительной обработке (при температуре 800о С). Приложение «Лабораторные образцы, содержащие галлий». Характерной особенностью окисленных образцов является наличие ярко выраженной (видимой даже при небольшом увеличении) зональной структуры, связанной с миграцией галлия. Зональная структура, получаемая в окисленных образцах, представлена на рис. 20.
Рисунок 20. Железо – галлий - алюминиевый окисленный брикет (отражённый свет, увеличение ×50).
Для исследований были выделены три зоны, обозначенные 1, 2, 3. Установлено наличие оксидного раствора, включающего Al2O3, Ga2O3, Fe2O3. Причем, содержание в растворе Al2O3 в различных зонах меняется незначительно, а содержание Ga2O3 постепенно убывает от места первоначального расположения частицы галлия, который был введен в систему в виде металла. Данные рентгеноспектрального анализа, иллюстрирующие изменение состава ЖГА окисленного брикета, вызванное миграцией галлия, приведены в таблицах 58. Их анализ позволяет предположить развитие изоморфного взаимного замещения галлия и железа в железо – галлий - алюминиевом оксидном растворе при практически неизменной массовой доле Al2O3.
Таблица 58. Изменение состава железо – галлий - алюминиевого окисленного брикета
Компонент | Содержание, массовая доля, % | ||
1 | 2 | 3 | |
Al2O3 | 25,2 | 24,7 | 25,0 |
Ga2O3 | 72,7 | 53,6 | 20,8 |
Fe2O3 | 2,1 | 21,7 | 54,2 |
Исследования восстановленного ЖГА брикета, микроструктура которого представлена на рисунке 21, позволили установить характерное изменение состава оксидной фазы (область 1) в направлении восстановленного железа (светлые участки в области 2). Направление замеров обозначено векторами 1 – 2- 3- 4 и 5 – 6 -7 – 8. Результаты приведены в таблицах 59 и 60.
Рис. 21. Железо – галлий - алюминиевый восстановленный брикет. Микрострктура х500
Таблица 59. Изменение состава оксидной фазы в направлении восстановленного железа.
Содержание компонента в исследуемой системе, массовая доля, % | |||
Номер точки | Al2O3 | Fe2O3 | Gа2O3 |
1 | 29,6 | 16,9 | 53,3 |
2 | 29,6 | 36,8 | 32,9 |
3 | 26,2 | 36,8 | 36,9 |
4 | 25,0 | 33,7 | 40,2 |
5 | 27,4 | 15,4 | 54,4 |
6 | 38,5 | 39,7 | 21,5 |
7 | 32,3 | 37,7 | 29,8 |
8 | 25,8 | 32,8 | 41,7 |
Из данных таблицы 60 следует, что с момента появления металлической фазы начинается активная диффузия галлия в восстановленное железо. Концентрация галлия по отношению к железу в восстановленном образце на расстоянии 40 – 50 мкм от границы локализации галлия в виде Ga2O3 возрастает примерно в два раза.
Таблица 60. Изменение концентрации Ga в системе Ga-Fe по результатам рентгеноспектрального анализа, массовая доля, %
Образец | Номера замера | ||||
1 | 2 | 3 | 4 | ||
Восстановленный окатыш | Участок замера | Участок, обогащенный галлием | граница раздела Ga2O-Fe2O3 | 50 мкм от границы | 200 мкм от границы |
Содержание галлия | 39,8 | 10,4 | 5,0 | 3,6 | |
Восстановленный брикет | Участок замера | участок, обогащенный галлием | граница раздела Ga2O-Fe2O3 | 50 мкм от границы | 200 мкм от границы |
Содержание галлия | 48,5 | 9,6 | 5,8 | 4,2 |
Полученные данные позволяют оценить эффективный коэффициент диффузии галлия в оксидной системе в направлении восстановленного железа. Для оценки использовали корреляцию между размерами диффузионной зоны (диффузионной длиной Ld) и коэффициентом диффузии:
L = 2 √Dt,
где t – время, с,
D – коэффициент диффузии, м2/с.
В соответствии с данными таблицы 60 можно принять, что Ld = 100 мкм (10-4м), время опыта t = 30 мин (2∙103с). Таким образом, D = 10-12 м2/с.
Для сравнения рассчитаем коэффициент самодиффузии железа:
,
где E = 280 кДж/моль,
D0 = 0,0118 м2/с,
T = 1200 °C.
Полученное значение D = 10-12 м2/с позволяет утверждать, что при анализируемых условиях величина эффективного коэффициента диффузии галлия примерно одного порядка с коэффициентом диффузии железа. Таким образом, высокая подвижность галлия в оксидных системах Fe-Ga-Al-O обеспечивает возможность в течение короткого времени формирования структуры, близкой к равновесной.
В структурах ЖГА окисленных и восстановленных брикетов и окатышей обнаружено присутствие металлической фазы, характерный вид которой представлен на рисунках 22 и 23. Рентгеноспектральное исследование обнаруженной фазы показало, что она представляет собой железо-галлиевый твердый раствор. Содержание компонентов в растворе составило: Ga – около 31 % (масс. доли), Fe – около 69 % (масс. доли). Из чего следует, что атомное соотношение компонентов составляет:
Ga / Fe = 31,03/69,08 = (31,03/69,72)/(69,08/55,87) = 0,445/1,237 = 1/2,78 ≈ 1/3,
где 69,72 – атомная масса Ga, % (ат.);
55,87 – атомная масса Fe, % (ат.).
Это позволяет предположить, что исследуемая фаза представлена интерметаллидом, состав которого соответствует формуле Fe3Ga.
Рисунок 22. Железо – галлий - алюминиевый окисленный брикет. Микроструктура х500
Рисунок 23. Зерна интерметаллида в структуре железо – галлий - алюминиевого восстановленного брикета. Микрострктура х200
Экспериментальные исследования распределения галлия между чугуном и доменным шлаком. Распределение галлия между чугуном и доменным шлаком изучалось на специальной лабораторной установке Фрайбергской Горной академии (Германия). Ее основным элементом являлась горизонтальная индукционная печь с частотой тока 400 кГц и максимальной мощностью 15 кВт.Были проведены две серии экспериментов, отличающиеся тем, что в первом случае галлий в исследуемую систему вводили в составе чугуна, а во втором - в составе шлака в виде оксида Gа2О3. Кроме того, исследовалось влияние на процесс основности шлака, химический состав которого представлен в таблице 61 /341/.
Таблица 61. Химический состав шлаков, использованных в опытах по изучению распределения галлия, массовая доля, %
Тип шлака | SiO2 | CaO | MgO | Al2O3 | Основность, (СаО + MgО)/(SiO2 + Al2O3) |
Основной | 40,9 | 36,4 | 11,4 | 6,7 | 1,00 |
Кислый | 46,9 | 32,7 | 10,4 | 6,0 | 0,81 |
Чугун содержащий галлий получали в результате сплавления предельного чугуна и металлического галлия в графитовом тигле при продувке печи газом, состоящим из90 % (объём,) азота и 10 % (объём.) водорода с выдержкой при 1400 °С в течение -10 минут. После охлаждения печи в тигель добавляли шлак и повторяли операцию нагрева до 1400 °С при сохранении режима продувки газом упомянутого состава. Время выдержки составляло 30 минут. Охлаждение печи происходило со скоростью 250 °С/мин.
Содержащий галлий шлак был изготовлен следующим образом. Металлический галлий растворяли в азотной кислоте, после чего к полученному раствору добавляли NH4OH и, в результате процесса осаждения, выделяли конденсат гидрооксида галлия Gа(ОН)3. После фильтрации влажная масса обжигалась при температуре 700 °С в течение 30 минут с получением оксида галлия Ga2Оз, который добавляли в доменный шлак. Предельный чугун и содержащий галлий шлак подвергались обработке в вышеописанном режиме. Содержание галлия определяли с помощью масс-спектрометрического анализа. Результаты экспериментов приведены в таблице 62.
Таким образом, установлено, что независимо от способа ввода в систему «чугун - шлак» (в составе металлической или оксидной фазы), галлий практически полностью (с массовой долей, % - 98…99,5) переходит в металл, а изменение основности шлака в интервале 0,8…1,0 (по (СаО + MgО)/(SiO2 + Al2O3) не оказывает существенного влияния на распределение галлия между металлическим и оксидным расплавами.
Таблица 62. Распределение галлия между чугуном и шлаком.
Способ ввода галлия в систему | Тип шлака | Содержание галлия по окончании опыта, г/т | |
в чугуне | в шлаке | ||
В составе чугуна | основной | 0,74..5,59 | 0,014…0,022 |
кислый | 0,88…5,15 | 0,013…0,020 | |
В составе шлака | основной | 0,58…1,43 | 0,017…0,022 |
кислый | 1,94 | 0,018 |
Исследования чугуна содержащего галлий. Для приготовления чугуна содержащего галлий был использован передельный чугун производства ОАО «Северсталь». К образцам чугуна, масса которых составляла 300 грамм, добавлялись завернутые в алюминиевую фольгу кусочки металлического галлия массой 6 грамм. Рентгеноспектральный анализ шлифов показал практически равномерное распределение галлия в объеме металла: соответственно 2,6 % по отношению к железу на краях образца и 2,8% - в центре.В связи с тем, что значительная часть отходов содержащих галлий, представлена арсенидом галлия, интересным для анализа представляется сплав чугуна с мышьяком и галлием. К мышьяковистому чугуну (As- 11 % (масс.)) добавляли галлий – 11 % (масс.), для того чтобы добиться равного состава по галлию и мышьяку. Для структуры сплава характерно присутствие эвтектики (серый цвет), обогащенной галлием и мышьяком и содержащей интерметаллид сложного состава.
Для определения влияния галлия на механические свойства чугуна были проведены опыты по измерению твёрдости чугуна по Роквелу (ГОСТ 9013-59) в зависимости от содержания в нём галлия. Образцы для опытов изготавливались следующим образом: в высверленную полость помещался легирующий металл и засыпался чугунной стружкой. Образец помещался в графитовый тигель индукционной печи. В печи создавался вакуум, после чего она заполнялась аргоном до атмосферного давления.. После выдержки в течение пяти минут при температуре 1550…1580 °С металл сливался в графитовую изложницу (охлаждение тигля вместе с печью и металлом приводит к прилипанию металла к тиглю). После охлаждения металл извлекался из изложницы, и измерялась твердость образцов, результаты измерений представлены в таблице 63.
Как видно из ее данных галлий оказывает существенное влияние на твёрдость чугуна. По-видимому, оно связано с образованием твёрдого раствора галлия в железе, который при увеличении содержания галлия образует самостоятельную фазу, в результате чего твёрдость чугуна падает.
Таблица 63. Изменение твердости чугуна в зависимости от содержания галлия, HRC
Содержание галлия, массовая доля, % | Твердость |
0,01 | 3…5 |
0,1 | 50…52 |
0,5 | 40…42 |
2,0 | 10…12 |
Термодинамическое моделирование. При проведении термодинамического анализа учитывали следующие обстоятельства /8, 44, 342, 343/:
В результате можно утверждать, что полное восстановление галлия из Ga2O3 в раствор на основе железа возможно уже при температурах около 800 ºС, т.е. восстановление галлия в раствор практически происходит начиная с температуры восстановления самого железа, при этом газообразный оксид Ga2O не образуется. Термодинамическая предпочтительность восстановления элемента в раствор с железом вполне очевидна, особенно с учетом малой концентрации галлия, поскольку его химический потенциал в сильно разбавленном растворе значительно ниже, чем в самостоятельной фазе. Это обусловливает большую стабильность состояния галлия, как примеси раствора на основе железа и объясняет обнаруженный экспериментально практически полный переход элемента в чугун. Согласно проведенным термодинамическим расчетам при концентрациях галлия около 100 г/т чугуна в интервале температур 800 – 1800 ºС практически весь галлий должен быть связан в растворе железа.
При более высоких температурах в восстановительных условиях (при избытке углерода) становится заметным переход галлия в газовую фазу в виде паров металла. Этот процесс возможен в фурменной зоне доменной печи для гетероатомов галлия органической части кокса. Пары галлия, увлекаемые газовым потоком, частично выносятся в верхние горизонты печи, где неизбежно окисляются CO2 в газовой фазе сначала до Ga2O,
|
|
Архитектура электронного правительства: Единая архитектура – это методологический подход при создании системы управления государства, который строится...
Общие условия выбора системы дренажа: Система дренажа выбирается в зависимости от характера защищаемого...
Двойное оплодотворение у цветковых растений: Оплодотворение - это процесс слияния мужской и женской половых клеток с образованием зиготы...
История развития пистолетов-пулеметов: Предпосылкой для возникновения пистолетов-пулеметов послужила давняя тенденция тяготения винтовок...
© cyberpedia.su 2017-2024 - Не является автором материалов. Исключительное право сохранено за автором текста.
Если вы не хотите, чтобы данный материал был у нас на сайте, перейдите по ссылке: Нарушение авторских прав. Мы поможем в написании вашей работы!