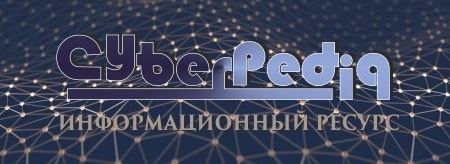
Состав сооружений: решетки и песколовки: Решетки – это первое устройство в схеме очистных сооружений. Они представляют...
Семя – орган полового размножения и расселения растений: наружи у семян имеется плотный покров – кожура...
Топ:
Характеристика АТП и сварочно-жестяницкого участка: Транспорт в настоящее время является одной из важнейших отраслей народного хозяйства...
Выпускная квалификационная работа: Основная часть ВКР, как правило, состоит из двух-трех глав, каждая из которых, в свою очередь...
Интересное:
Принципы управления денежными потоками: одним из методов контроля за состоянием денежной наличности является...
Как мы говорим и как мы слушаем: общение можно сравнить с огромным зонтиком, под которым скрыто все...
Мероприятия для защиты от морозного пучения грунтов: Инженерная защита от морозного (криогенного) пучения грунтов необходима для легких малоэтажных зданий и других сооружений...
Дисциплины:
![]() |
![]() |
5.00
из
|
Заказать работу |
|
|
Автоматизация — одно из направлений научно-технического прогресса, использующее саморегулирующие технические средства и математические методы с целью освобождения человека от участия в процессах получения, преобразования, передачи и использования энергии, материалов, изделий или информации, либо существенного уменьшения степени этого участия или трудоёмкости выполняемых операций.
Автоматизируются:
· производственные процессы;
· проектирование;
· организация, планирование и управление;
· научные исследования;
· обучение;
· бизнес-процессы;
· и другие сферы человеческой деятельности.
Автоматизация позволяет повысить производительность труда, улучшить качество продукции, оптимизировать процессы управления, отстранить человека от производств, опасных для здоровья. Автоматизация, за исключением простейших случаев, требует комплексного, системного подхода к решению задачи. В состав систем автоматизации входят датчики (сенсоры), устройства ввода, управляющие устройства (контроллеры), исполнительные устройства, устройства вывода, компьютеры. Применяемые методы вычислений иногда копируют нервные и мыслительные функции человека. Весь этот комплекс средств обычно называют системами.
Основные виды систем автоматизации:
· автоматизированная система планирования (АСП),
· автоматизированная система научных исследований (АСНИ),
· система автоматизированного проектирования (САПР),
· автоматизированный экспериментальный комплекс (АЭК),
· гибкое автоматизированное производство (ГАП) и автоматизированная система управления технологическим процессом (АСУ ТП),
· автоматизированная система управления эксплуатацией (АСУ) и система автоматического управления (САУ).
|
Основная тенденция развития систем автоматизации идет в направлении создания автоматических систем, которые способны выполнять заданные функции или процедуры без участия человека. Роль человека заключается в подготовке исходных данных, выборе алгоритма (метода решения) и анализе полученных результатов. Также в подобных системах предусматривается постепенно наращиваемая защита от нестандартных событий (аварий) или способы их обхода (с точки зрения науки катастроф это не одно и то же).
Однако, присутствие в решаемых задачах эвристических или сложно программируемых процедур объясняет широкое распространение автоматизированных систем (также, в зависимости от терминологии некоторых исследований, – полуавтоматических систем). Здесь человек участвует в процессе решения, например, управляя им, вводя промежуточные данные. В таких случаях принципиально экономят на защите от редких и сложных нестандартных событий, отводя её роль человеку.
На степень автоматизации влияют вероятность и разнообразность нестандартных событий (аварий), продолжительность времени, отведенного на решение задачи, и её вид — типовая или нет. Так, при срочном поиске решения нестандартной задачи следует полагаться только на самого себя.
Автоматизация производства — это процесс в развитии машинного производства, при котором функции управления и контроля, ранее выполнявшиеся человеком, передаются приборам и автоматическим устройствам. Введение автоматизации на производстве позволяет значительно повысить производительность труда и качество выпускаемой продукции, сократить долю рабочих, занятых в различных сферах производства.
До внедрения средств автоматизации замещение физического труда происходило посредством механизации основных и вспомогательных операций производственного процесса. Интеллектуальный труд долгое время оставался не механизированным (ручным). В настоящее время операции физического и интеллектуального труда, поддающиеся формализации, становятся объектом механизации и автоматизации.
|
Основой автоматизации производства являются технологическиепроцессы (ТП), которые должны обеспечивать высокую производительность,надежность, качество и эффективность изготовленияизделий. С этой точки зрения большое значение приобретают прогрессивныевысокопроизводительные методы обработки и сборки, используемыепри проектировании автоматизированных ТП.
При разработке ТП автоматизированного производства (АП) рассматриваюткомплексно все его элементы: загрузку-выгрузку изделий,их базирование и закрепление, обработку, контроль, межоперационноетранспортирование и складирование и др. Поэтому для оценкивозможности и эффективности автоматизации важно правильно классифицироватьТП.
Характерной особенностью ТП обработки и сборки является строгаяориентация деталей и инструмента относительно друг друга в рабочемпроцессе — первый класс процессов. Другие виды обработки(термообработка, сушка, окраска и пр.), которые не требуют строгойориентации детали, относят ко второму классу процессов.
Кроме того, ТП по непрерывности подразделяют на дискретные инепрерывные. Дискретные процессы характеризуются прерывистостьюи строгой последовательностью рабочих и холостых движений,непрерывные — не прерываясь, изменяются плавно, без скачков (например,бесцентровое шлифование, протягивание). Это разделениеносит условный характер, так как большинство процессов сочетаетдискретность с непрерывностью.
Для обеспечения высокой производительности и надежности проводятдифференциацию ТП, т.е. делят его на упрощенные технологическиепереходы (позиции). По мере возможности для уменьшениядлины транспортных путей и числа операций, а также в силу техническойцелесообразности осуществляют концентрацию переходов ипозиций на едином оборудовании в одну операцию. Эффективностьэтих мероприятий устанавливается технико-экономическими расчетами,обязательно сопровождающими проектирование ТП автоматизированногопроизводства.
Разработка технологических процессов АП характеризуется следующимиособенностями:
• автоматизированные ТП включают не только разнородныеоперации механической обработки, но и обработку давлением,термообработку, сборку, контроль, упаковку, а также транспортно-складские и другие операции;
|
• требования к гибкости и автоматизации производственныхпроцессов диктуют необходимость комплексной и детальнойпроработки технологии, тщательного анализа объектов производства,проработки маршрутной и операционной технологии,обеспечения надежности и гибкости процесса изготовленияизделий с заданным качеством. Степень подробноститехнологических решений должна быть доведена до уровняподготовки управляющих программ для оборудования;
• при широкой номенклатуре изделий технологические решениямноговариантны;
• возрастает степень интеграции работ, выполняемых различнымитехнологическими подразделениями.
Насущные требования по совершенствованию и сокращению сроковтехнологической подготовки производства вызвали необходимостьв принципиально новом подходе к проектированию ТП с использованиемметодов систем автоматизированного проектирования (САПР).
Повышению эффективности автоматизированной разработки ТП вомногом способствует рациональное сочетание типовых и индивидуальныхтехнологических решений на всех стадиях проектирования, атакже высокий уровень стандартизации и унификации изделий, оборудованияи самих технологических процессов, позволяющих создаватьи использовать соответствующие базы данных на основе информационныхтехнологий.
Внедрение гибкой технологии (технологии переналаживаемогопроизводства) с широким использованием компьютерной техники ипереналаживаемых средств автоматизации позволяет быстро и эффективноперестраивать ТП на изготовление новых изделий. Последнеевесьма актуально в условиях мелкосерийного и серийного производства,преобладающего в машиностроении.
Требования к металлорежущему оборудованию и производственным процессам, подлежащим автоматизации
Основным требованием к металлорежущему оборудованию, работающему в комплексе с промышленным роботом (ПР), является необходимость его работы в автоматическом или полуавтоматическом режиме.
|
Для обеспечения совместной работы ПР и металлорежущего оборудования необходимо согласовать работу систем управления роботом и станком.
Станки должны быть оснащены автоматизированными устройствами с регулируемым усилием зажима для закрепления заготовки. Для обработки заготовок несимметричной формы в оборудовании следует предусмотреть возможность останова шпинделя в заданном положении.
Компоновка и параметры рабочей зоны металлорежущего оборудования, а также конструкция приспособлений должны обеспечивать беспрепятственный доступ руки робота в зону резания для установки, заготовки и снятия детали. Конструкция станины, компоновка станка и точки крепления станочных приспособлений должны обеспечивать возможность загрузки и разгрузки станка с фронтальной или тыльной стороны (в зависимости от конкретной планировки РТК).
При создании РТК важным является решение проблемы автоматизации удаления стружки. Короткая и дробленая стружка должна удаляться из зоны резания активно (путем выдувания, отсоса или смывания) или пассивно (под действием силы тяжести).
Управление автоматизированными перемещениями пинолей, прижимов, зажимных элементов приспособлений и другой оснастки подобного назначения должно иметь блокировку, допускающую перемещение этих элементов только при исходном положении инструмента и при отсутствии вращения заготовки, поддерживаемой этими элементами.
Автоматические устройства для контроля должны выполнять измерения в процессе обработки и управлять режимом работы основного технологического оборудования. Применение тех или иных методов автоматического контроля должно зависеть от следующих основных факторов: требуемой точности обработки; формы и размеров измеряемых деталей; требуемой производительности и экономичности.
При прямом методе измерения параметров обрабатываемой заготовки наконечник контрольного устройства должен находиться в контакте с поверхностью обрабатываемой заготовки. По достижении заданного размера устройство автоматически должно подавать сигнал об окончании обработки или необходимости изменения режима обработки. Устройства подобного рода применяют при контроле диаметров заготовок на операциях наружного точения и шлифования.
При косвенном методе измерения контролируется перемещение рабочего органа станка. Этот метод применяется, например, при контроле глубины сверления, растачивания и т.д.
Транспортные устройства должны обеспечивать накопление заготовок для обеспечения работы РТК в течение определенного времени и транспортирование полуфабриката между последовательно установленными РТК. В некоторых случаях транспортные устройства РТК могут выполнять функции внутрицехового транспорта.
|
В механическом (механосборочном) цехе выполняют различные транспортно-загрузочные операции: загрузку полуфабрикатов, заготовок, инструмента, приспособлений и изделий для хранения на склад и их выгрузку по требованию; перемещение этих предметов со складов к рабочим местам (сборочным позициям, станкам) и обратно, а также межоперационные перемещения заготовок между станками. Эти операции осуществляют с помощью транспортных систем (ТС).
Автоматическая транспортная система — совокупность взаимосвязанных автоматически действующих средств для транспортирования приведенных выше предметов в системе автоматически работающих машин (станков).
Автоматизированная транспортная система отличается от автоматической тем, что транспортно-загрузочные операции автоматизированы частично. Такие системы используют в поточных АЛ. Комплексная автоматизация транспортно-загрузочных операций позволяет транспортные процессы осуществлять почти непрерывно. Основой для проектирования транспортной системы является схема материальных потоков, цеха и участков, которая должна быть составлена с учетом обеспечения мощности грузопотоков.
Грузовые потоки цеха представляют собой определенную схему движения предметов труда в соответствии с цоследователь-ностью производственного процесса. Грузопотоки классифицируют по следующим признакам в зависимости от массы — миниатюрные (до 0,01 кг), легкие (0,01—0,05 кг), средние (0,5—16 кг), переходной массы (16—125 кг), тяжелые (более 125 кг); в зависимости от способа загрузки — в таре, без тары, навалом, ориентированные, кассетированные в пакетах, на спутниках;в зависимости от формы — тела вращения, корпусные и др.; в зависимости от материала — металлические, неметаллические и т. д.; в зависимости от свойств материала — твердые, хрупкие, пластичные, магнитные.
Рис. 1. Классификация транспортных систем в зависимости от транспортируемых грузов
Расчет интенсивности грузопотоков и определение их оптимальных схем является одной из составляющих частей проекта цеха. Организация оптимальных грузопотоков включает в себя решение таких задач, как сокращение общей длины транспортных путей, пересечений и разветвлений, исключение транспортных петель и возвратных трасс, обеспечение ремонтопригодности транспортных средств.
Это приводит к снижению капитальных и эксплуатационных затрат. В общем случае транспортная система состоит из транспортных средств (TCP) доставки грузов и загрузочно-разгрузочных средств, обеспечивающих связь с технологическим оборудованием.
Для перемещения грузов широко применяют ленточные транспортеры (рис. 2).
Рис. 2. Общий вид транспортера
Подающие устройства предназначены для размещения заготовок, выдачи их на позицию захвата роботом в ориентированном положении. Выбор типов транспортных и подающих устройств должен определяться организацией производства и условиями подачи заготовок на РТК.
Выбранный для применения в РТК ПР не всегда в полном объеме удовлетворяет всем предъявляемым к нему требованиям.
Поэтому часто возникает ряд задач по доработке конструкций некоторых узлов робота. В первую очередь это относится к захватному устройству, которое должно соответствовать параметрам конкретных обрабатываемых заготовок. Помимо функций захвата и удержания заготовки, в некоторых случаях захватное устройство должно реализовать установочные перемещения заготовки (например, при досылке заготовки в приспособление станка).
В настоящее время серийно выпускаются РТК типа “станок - робот” на базе станков токарной, сверлильной, фрезерной и шлифовальной групп, а также станков с ЧПУ.
|
|
Семя – орган полового размножения и расселения растений: наружи у семян имеется плотный покров – кожура...
Общие условия выбора системы дренажа: Система дренажа выбирается в зависимости от характера защищаемого...
Архитектура электронного правительства: Единая архитектура – это методологический подход при создании системы управления государства, который строится...
Автоматическое растормаживание колес: Тормозные устройства колес предназначены для уменьшения длины пробега и улучшения маневрирования ВС при...
© cyberpedia.su 2017-2024 - Не является автором материалов. Исключительное право сохранено за автором текста.
Если вы не хотите, чтобы данный материал был у нас на сайте, перейдите по ссылке: Нарушение авторских прав. Мы поможем в написании вашей работы!