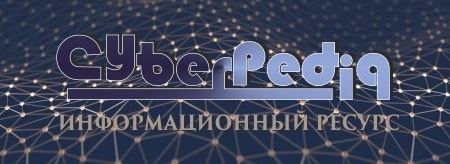
Таксономические единицы (категории) растений: Каждая система классификации состоит из определённых соподчиненных друг другу...
Организация стока поверхностных вод: Наибольшее количество влаги на земном шаре испаряется с поверхности морей и океанов (88‰)...
Топ:
Эволюция кровеносной системы позвоночных животных: Биологическая эволюция – необратимый процесс исторического развития живой природы...
Организация стока поверхностных вод: Наибольшее количество влаги на земном шаре испаряется с поверхности морей и океанов...
Характеристика АТП и сварочно-жестяницкого участка: Транспорт в настоящее время является одной из важнейших отраслей народного хозяйства...
Интересное:
Мероприятия для защиты от морозного пучения грунтов: Инженерная защита от морозного (криогенного) пучения грунтов необходима для легких малоэтажных зданий и других сооружений...
Аура как энергетическое поле: многослойную ауру человека можно представить себе подобным...
Наиболее распространенные виды рака: Раковая опухоль — это самостоятельное новообразование, которое может возникнуть и от повышенного давления...
Дисциплины:
![]() |
![]() |
5.00
из
|
Заказать работу |
|
|
ВВЕДЕНИЕ
Основой современных производственных процессов являются автоматизированные технологические процессы механической обработки и сборки, которые обеспечивают высокую производительность и необходимое качество изготовляемых изделий. И в настоящее время перед промышленностью стоят две основные задачи: крупносерийное производство наделить производство определенной гибкостью, сохранив преимущества полной автоматизации, а мелкосерийное производство необходимо комплексно автоматизировать таким образом, чтобы наряду с гибкостью оно приобрело черты массового производства – непрерывность, ритмичность, высокий темп выпуска изделий, стабильность технологических процессов.
Современное отечественное машиностроение должно развиваться в направлении автоматизации производства с широким использованием ЭВМ и роботов, внедрения гибких технологий, позволяющих быстро и эффективно перестраивать технологические процессы на изготовление новых изделий. Автоматизация проектирования технологии и управления производственными процессами — один из основных путей интенсификации производства, повышения его эффективности и качества продукции.
Характерным признаком современного производства является частая сменяемость изделий. При этом требования к производительности в условиях мелко- и среднесерийного производства значительно возрастают. Противоречия требований мобильности и производительностинаходят разрешение в создании гибких производственных систем (ГПС). Высокая эффективность производства достигается рациональным сочетанием оборудования, организацией транспортных операций и управления ГПС. Растет выпуск станков с ЧПУ и роботов, в особенности с CNC-yправлением.
|
Использование гибких производственных систем и технологическихмодулей позволяет изготовлять детали в любом порядке и варьироватьих выпуск в зависимости от производственной программы, сокращаетзатраты и время на подготовку производства, повышаеткоэффициент использования оборудования, изменяет характер работыперсонала, повышая удельный вес творческого, высококвалифицированного труда.
Наметились три направления, по которым идет решение проблемыповышения эффективности инженерного труда в сфере проектирования:
• рационализация системы проектирования, включая систематизациюсамого процесса проектирования и улучшение организациитруда инженера-проектировщика;
• комплексная автоматизация умственно-формальных, нетворческихфункций инженера-проектировщика в процессе проектирования;
• разработка имитационных моделей для воспроизводства наЭВМ умственной деятельности человека, его способности приниматьрешения в условиях полной и частичной неопределенностипроектных ситуаций, разработки эвристических алгоритмов,позволяющие качественно решать сложные задачипроектирования при введении определенных ограничений.
Тенденцией современного этапа автоматизации проектированияявляется создание комплексных систем автоматизированного проектированияи изготовления, включающих конструирование изделий,технологическое проектирование, подготовку управляющих программдля оборудования с программным управлением, изготовление деталей,сборку узлов и машин, упаковку и транспортирование готовойпродукции.
Одним из путей к успешному внедрению системы CAD/САМ являетсяреализация принципов групповой технологии, основанной наиспользовании оборудования, планировании и организации производствапо принципу технологической общности деталей.
Если выпуск изделий осуществляется с использованием ГПС, тосистема автоматизации проектирования технологических процессовпрежде всего должна обеспечивать их гибкость. Под гибкостью понимаетсявозможность быстрого перехода на новые технологическиепроцессы в связи с изменением факторов, определяющих качество выпускаемыхдеталей (точность, качество поверхностного слоя и др.) ипроизводительность. При изменении конструктивных параметров деталитехнологическая система (технологические системы) должна (должны)количественно и качественно переналаживаться в сжатые срокипри минимальных затратах.
|
Таким образом, тенденцией современного этапа автоматизациипроектирования является создание комплексных систем, включающихконструирование изделий, технологическое проектирование и изготовлениеизделий в ГПС. Спроектированный технологический процессдолжен оперативно реагировать на изменение производственных ситуацийпроцесса изготовления изделий.
Повышение требования конкурентоспособности продукции машиностроениятребует новых производительных систем. Для этого создаютвиртуальные производственные системы (информация о ееструктуре хранится только в памяти ЭВМ) на основе распределенныхпроизводственных систем (отдельные производственные системы,организационно не связанные между собой и имеющие технологическоеоборудование). При этом решаются задачи организации и управления.
Организация виртуальной производственной системы напрямуюсвязана с технологическим содержанием реализуемых проектов. Процессыорганизации виртуальной производственной системы и технологическогопроектирования взаимосвязаны. Имеют место прямые иобратные связи информационных потоков. Создаваемая система управленияфункционирует, как правило, без участия человека.
Требования к металлорежущему оборудованию и производственным процессам, подлежащим автоматизации
Основным требованием к металлорежущему оборудованию, работающему в комплексе с промышленным роботом (ПР), является необходимость его работы в автоматическом или полуавтоматическом режиме.
Для обеспечения совместной работы ПР и металлорежущего оборудования необходимо согласовать работу систем управления роботом и станком.
Станки должны быть оснащены автоматизированными устройствами с регулируемым усилием зажима для закрепления заготовки. Для обработки заготовок несимметричной формы в оборудовании следует предусмотреть возможность останова шпинделя в заданном положении.
|
Компоновка и параметры рабочей зоны металлорежущего оборудования, а также конструкция приспособлений должны обеспечивать беспрепятственный доступ руки робота в зону резания для установки, заготовки и снятия детали. Конструкция станины, компоновка станка и точки крепления станочных приспособлений должны обеспечивать возможность загрузки и разгрузки станка с фронтальной или тыльной стороны (в зависимости от конкретной планировки РТК).
При создании РТК важным является решение проблемы автоматизации удаления стружки. Короткая и дробленая стружка должна удаляться из зоны резания активно (путем выдувания, отсоса или смывания) или пассивно (под действием силы тяжести).
Управление автоматизированными перемещениями пинолей, прижимов, зажимных элементов приспособлений и другой оснастки подобного назначения должно иметь блокировку, допускающую перемещение этих элементов только при исходном положении инструмента и при отсутствии вращения заготовки, поддерживаемой этими элементами.
Автоматические устройства для контроля должны выполнять измерения в процессе обработки и управлять режимом работы основного технологического оборудования. Применение тех или иных методов автоматического контроля должно зависеть от следующих основных факторов: требуемой точности обработки; формы и размеров измеряемых деталей; требуемой производительности и экономичности.
При прямом методе измерения параметров обрабатываемой заготовки наконечник контрольного устройства должен находиться в контакте с поверхностью обрабатываемой заготовки. По достижении заданного размера устройство автоматически должно подавать сигнал об окончании обработки или необходимости изменения режима обработки. Устройства подобного рода применяют при контроле диаметров заготовок на операциях наружного точения и шлифования.
При косвенном методе измерения контролируется перемещение рабочего органа станка. Этот метод применяется, например, при контроле глубины сверления, растачивания и т.д.
|
Транспортные устройства должны обеспечивать накопление заготовок для обеспечения работы РТК в течение определенного времени и транспортирование полуфабриката между последовательно установленными РТК. В некоторых случаях транспортные устройства РТК могут выполнять функции внутрицехового транспорта.
В механическом (механосборочном) цехе выполняют различные транспортно-загрузочные операции: загрузку полуфабрикатов, заготовок, инструмента, приспособлений и изделий для хранения на склад и их выгрузку по требованию; перемещение этих предметов со складов к рабочим местам (сборочным позициям, станкам) и обратно, а также межоперационные перемещения заготовок между станками. Эти операции осуществляют с помощью транспортных систем (ТС).
Автоматическая транспортная система — совокупность взаимосвязанных автоматически действующих средств для транспортирования приведенных выше предметов в системе автоматически работающих машин (станков).
Автоматизированная транспортная система отличается от автоматической тем, что транспортно-загрузочные операции автоматизированы частично. Такие системы используют в поточных АЛ. Комплексная автоматизация транспортно-загрузочных операций позволяет транспортные процессы осуществлять почти непрерывно. Основой для проектирования транспортной системы является схема материальных потоков, цеха и участков, которая должна быть составлена с учетом обеспечения мощности грузопотоков.
Грузовые потоки цеха представляют собой определенную схему движения предметов труда в соответствии с цоследователь-ностью производственного процесса. Грузопотоки классифицируют по следующим признакам в зависимости от массы — миниатюрные (до 0,01 кг), легкие (0,01—0,05 кг), средние (0,5—16 кг), переходной массы (16—125 кг), тяжелые (более 125 кг); в зависимости от способа загрузки — в таре, без тары, навалом, ориентированные, кассетированные в пакетах, на спутниках;в зависимости от формы — тела вращения, корпусные и др.; в зависимости от материала — металлические, неметаллические и т. д.; в зависимости от свойств материала — твердые, хрупкие, пластичные, магнитные.
Рис. 1. Классификация транспортных систем в зависимости от транспортируемых грузов
Расчет интенсивности грузопотоков и определение их оптимальных схем является одной из составляющих частей проекта цеха. Организация оптимальных грузопотоков включает в себя решение таких задач, как сокращение общей длины транспортных путей, пересечений и разветвлений, исключение транспортных петель и возвратных трасс, обеспечение ремонтопригодности транспортных средств.
|
Это приводит к снижению капитальных и эксплуатационных затрат. В общем случае транспортная система состоит из транспортных средств (TCP) доставки грузов и загрузочно-разгрузочных средств, обеспечивающих связь с технологическим оборудованием.
Для перемещения грузов широко применяют ленточные транспортеры (рис. 2).
Рис. 2. Общий вид транспортера
Подающие устройства предназначены для размещения заготовок, выдачи их на позицию захвата роботом в ориентированном положении. Выбор типов транспортных и подающих устройств должен определяться организацией производства и условиями подачи заготовок на РТК.
Выбранный для применения в РТК ПР не всегда в полном объеме удовлетворяет всем предъявляемым к нему требованиям.
Поэтому часто возникает ряд задач по доработке конструкций некоторых узлов робота. В первую очередь это относится к захватному устройству, которое должно соответствовать параметрам конкретных обрабатываемых заготовок. Помимо функций захвата и удержания заготовки, в некоторых случаях захватное устройство должно реализовать установочные перемещения заготовки (например, при досылке заготовки в приспособление станка).
В настоящее время серийно выпускаются РТК типа “станок - робот” на базе станков токарной, сверлильной, фрезерной и шлифовальной групп, а также станков с ЧПУ.
Классификация деталей
Классификацию деталей проводят в целях определения групп технологическиоднородных деталей для их совместной обработки в условияхгруппового производства.
Выполняют ее в два этапа: первичнаяклассификация — кодирование деталей обследуемого производствапо конструктивно-технологическим признакам; вторичная классификация— группирование деталей с одинаковыми или несущественноотличающимися признаками классификации.
Состав признаков устанавливают с учетом особенностей анализируемогопроизводства. При классификации деталей нужно учитыватьследующие признаки: конструктивные — в соответствии с классификаторомЕСКД; габаритные размеры, массу, материал, вид обработкии заготовки; число операций обработки; точностные и другие показатели,определяемые особенностями объектов исследования.
Группирование деталей по конструктивно-технологическим признаками выбор деталей-представителей выполняют методом сопоставлениязапросов на группирование с перечислением признаковпервичной классификации в такой последовательности: выбор совокупностидеталей на уровне классов, например, тела вращения длямеханообрабатывающего производства; выбор совокупности деталейна уровне подкласса, например, детали типа вала; классификациядеталей по комбинации поверхностей, например, валы с комбинациейгладких цилиндрических поверхностей; группирование погабаритным размерам с выделением областей с максимальной плотностьюраспределения размеров (рис. 3); определение по диаграммеобластей с наибольшим числом наименований деталей.
Одним из факторов, определяющих приоритет автоматизации, является станкоемкость групповой обработки. Итоговые данные удельноговеса станкоемкости обработки рассчитывают для каждой группы деталей. Этот показатель необходим для определения целесообразности и очередности автоматизации.
Рис. 3. Пример диаграммы частоты распределения
При большой номенклатуре деталей и трудностях с выполнением кодирования и группирования допускается анализ выпускаемой продукции по ее основным группам.
В этом случае по каждой группе деталей определяют деталь-представитель, имеющую наибольшее число общих признаков, присущих деталям данной группы. Остальные детали являются модификациями базовой детали.
Полученную в результате классификации деталей информацию формализуют и используют для формирования базы данных (БД) по объектам производства.
Применение информационных технологий позволяет использовать эти БД при выборе технологии, основного и вспомогательного оборудования.
При этом значительное упрощение иудешевление конструирования и производства машин за счет резкогосокращения типажа приспособлений, режущего и мерительного инструментов,инструментальных наладок и использования типовых технологическихмодулей (модульной технологии) возможно на основе унификацииКТЭ деталей машин и точностных параметров.
Основой унификации деталей и элементов являются их классификацияпо конструктивно-технологическим признакам и последующийстатистический анализ точностных и геометрических параметров унифицируемыхдеталей и элементов.
Унификация конструктивныхэлементов деталей и сборочных единиц заключается в системном подходек формированию групп элементов по их геометрическим, точностным,технологическим признакам, выделению ограниченного количестватиповых представителей этих групп на основе статистическогоанализа.
Унификация элементов и их параметров должна сопровождатьсятщательным анализом функционального назначения детали иузла, особенностей их конструкции и эксплуатации, технологическихвозможностей производства, т. е. унификация конструктивно-технологическихэлементов (наружных цилиндрических поверхностей, расточек,канавок, пазов и т. д.) должна проводиться на стадии отработкиконструкций изделий на технологичность.
Промышленные роботы
Промышленные роботы используются в составе:
1. робото-техническихкомплексов (РТК),
2. гибких производственных модулей (ГПМ),
3. роботизированных технологических линий (РТЛ),
4. роботизированных технологических участков (РТУ).
Использование промышленных роботов позволяет исключить брак, сократить издержки, повысить рентабельность выпускаемой продукции. Роботы успешно внедряются производство, заменяя людей, решая множество задач, важнейшая из которых – исключение человеческого фактора.
Роботы способны производить продукцию с высокой степенью повторяемости. Они могут быть укомплектованы различными датчиками движения и системами технического зрения. Качество продукции при использовании роботов не снизится, если работа утомительна и однообразна или выполняется в условиях опасной окружающей среды.
Роботизированные технологии принципиально отличаются от обычных традиционных средств, так как имеют многоцелевое назначение. Они легко перестраиваются на выполнение самых разнообразных операций.
Наиболее часто используются следующие роботизированные решения на базе промышленных роботов, предназначенные для выполнения разного рода специализированных операций:
1. для сварки – дуговой, плазменной, контактной (рис. 5);
2. для обслуживания станков, в том числе токарно-фрезерной группы, машин плазменной, лазерной резки;
3. для позиционирования заготовок;
4. для транспортировки деталей;
5. для нанесения лакокрасочных покрытий.
![]() | ![]() | ![]() |
а) | б) | в) |
Рис. 5. Промышленные роботы
а) робот дуговой сварки; б) робот контактной сварки; в) робот общего назначения
Применение промышленных роботов позволило эффективнее выполнять непосильные человеку по трудоемкости и точности работы: загрузку/разгрузку, укладку, сортировку, ориентацию деталей; перемещение заготовок от одного робота к другому, а готовых изделий - на склад; точечную сварку и сварку швов; сборку механических и электронных деталей; прокладывание кабеля; разрезание заготовок по сложному контуру. Пример автоматизированного участка сборочной линии показан на рис. 6.
Рис.6.Роботизированная сборочная линия
На рис.7 показаны примеры расположения промышленных роботов в составе РТК.
Промышленный робот может быть самостоятельной единицей или конструктивно объединенным с основным технологическим оборудованием.
На рис. 7, а показан промышленный робот 4, встроенный в металлорежущий станок с системой управления 3.
Тактовый стол 5 подает заготовку на фиксированную позицию. Промышленный робот снимает заготовку и устанавливает ее в рабочую зону станка 2.
После обработки готовая деталь снимается и устанавливается роботом в ту же позицию тактового стола. Затем система управления 1 промышленного робота подает сигнал для перемещения тактового стола на один шаг: готовая деталь перемещается на другую позицию, а на ее место поступает новая заготовка.
Рис. 7. Расположение промышленных роботов в РТК с одним станком: а - встроенный в станок, б - портальный, в - установленный рядом со станком, г - встроенный в ГПМ
На рис. 7,б показан портальный промышленный робот 4, установленный над станком 2 с системой управления 3. Накопитель заготовок 6 размещается рядом со станком. Для загрузки - разгрузки заготовокслужит каретка, перемещающаяся по порталу.
На рис. 7,в показан промышленный робот 4 для установки и снятия инструментов и готовых изделий, установленный рядом со станком 2 и работающий в цилиндрической системе координат. Загрузка заготовок происходит с использованием тактового стола 5 и промышленного робота 4 в станок 2. Станок и промышленный робот имеют свои системы управления соответственно 3 и 1.
На рис. 7,г показано применение промышленного робота в ГПМ для обработки корпусных деталей. Модуль состоит из стеллажа 7 для накопления заготовок 8 и обработанных деталей и станка 2, работающего без участия рабочего. Промышленный робот 4 служит для установки заготовки со стеллажа в рабочую зону станка и обработанной детали из рабочей зоны в стеллаж 7.
В РТК может совсем отсутствовать технологическое оборудование, тогда основную операцию выполняет непосредственно промышленный робот.
На рис. 8 показан технологический промышленный робот 1 для сверления и фасонного фрезерования деталей самолетов, образующий РТК.
Рис. 8. Технологический промышленный робот
Сбоку от робота установлен инструментальный магазин с набором различных сверл и фрез в оправках (на рис.4.14 не показан). Обрабатываемая панель 2 устанавливается оператором на одну из граней поворотного приспособления 3.
В это время с другой стороны приспособления с помощью робота производится обработка второй панели. После окончания операции приспособление поворачивается специальным механизмом 4 с гидравлическим приводом и робот осуществляет обработку следующей детали.
Чтобы добиться необходимой точности обработки, на обрабатываемую панель устанавливается "кондуктор", который определяет положение отверстий. В состав РТК входят гидростанция 5 и система управления 6. РТК значительно дешевле, чем установка пятикоординатного многоцелевого станка.
Если оборудование, расположенное в РТК, образует технологический поток, то такой комплекс принято называть роботизированной технологической линией (РТЛ).
На рис.9 показана многостаночная РТЛ, построенная на базе портальных промышленных роботов и предназначенная для обработки валов электродвигателей.
Рис. 9. Многостаночная РТЛ на базе портальных промышленных роботов
Штучные заготовки, имеющие обработанные торцы и центровые отверстия, подаются по конвейеру 1, откуда они снимаются портальным промышленным роботом 3, имеющим двухзахватное устройство для обслуживания токарных станков 2 и 4.
Чтобы участки РТЛ могли работать несинхронно, встроен промежуточный накопитель 5, который используется также для создания П-образной компоновки. Двухзахватный портальный промышленный робот 6 обслуживает один многоцелевой станок 7, который служит для снятия лысок, обработки шпоночных пазов, сверления отверстий и других операций. Обрабатываемые детали поступают в накопитель 8, откуда двухзахватным промышленным роботом 14 последовательно передаются на круглошлифовальные станки 9 и 10. Готовые детали укладываются на отводящий конвейер 13. Управление линией комбинированное. Централизованное управление всей РТЛ производится от ЭВМ 11 и пультов управления 12 систем ЧПУ у отдельных станков.
Роботизированный технологический участок (РТУ). Следующим по сложности роботизированным комплексом является роботизированный технологический участок. Он характеризуется выполнением нескольких основных технологических операций, которые объединены конструктивно (оборудованием) и (или) организационно (управлением). Эти операции могут быть одинаковыми или различными, но не связанными технологическим потоком в определенную последовательность.
Простейший роботизированный технологический участок РТУ может включать несколько единиц технологического оборудования, обслуживаемых одним промышленным роботом (неподвижным с размещением оборудования вокруг промышленного робота или подвижным, перемещающимся вдоль оборудования). Другие РТУ имеют несколько промышленных роботов, которые последовательно выполняют основную технологическую операцию, например сборку одного изделия.
На рис. показан РТУ из токарных станков с ЧПУ, обслуживаемый подвижным промышленным роботом, с общим управлением от ЭВМ, автоматизированным складом и единой транспортной системой.
На складе 1 хранятся как заготовки, так и изделия (типа валов). Станки 5 с пультами 4 ЧПУ расположены в два ряда, а между ними по рельсам перемещается (с четким позиционированием) промышленный робот 7. По периметру участка четырехугольником расположены роликовые конвейеры 2, связывающие участок с автоматизированным складом и позицией 8 контроля.
Рис. 10. Участок станков с ЧПУ, обслуживаемый подвижным промышленным роботом, с общим управлением от внешней ЭВМ, автоматизированным складом и единой транспортной системой
За ней расположен отводящий конвейер для выдачи обработанных изделий. За задними бабками станков перпендикулярно линии центров и внешнему общему конвейеру проходят конвейеры-накопители 3, которые выводят изделия и заготовки на позиции обслуживания промышленным роботом. Стружка отводится специальным конвейером в бункер 6. По команде ЭВМ 9 заготовки выдаются со склада, автоматически передаются конвейером на каждый станок, устанавливаются роботом на станки, снимаются им и передаются на внешний конвейер, направляющий их на станцию контроля и затем на склад готовой продукции.
Следующий по сложности роботизированный участок включает несколько единиц технологического оборудования и обслуживающих их одинаковых промышленных роботов. Дальнейшим усложнением РТУ является совместная работа промышленных роботов различных типов.
РТК может представлять собой цех, состоящий, например, из нескольких РТУ, автоматизированных складов и связывающих их транспортных промышленных роботов. Пределом развития роботизированного производства является комплексно роботизированный завод.
Создание РТК связано со значительными единовременными затратами. По мере усложнения РТК и повышения уровня автоматизации эти затраты увеличиваются. Экономическая эффективность от создания РТК определяется из сравнения затрат и достигаемых результатов, которые выступают в виде составляющих социально-экономического эффекта роботизации. Этот эффект проявляется в трех сферах: разработка и изготовление, производственное использование и применение продукции.
Типовые компоновки РТК
Станочные системы различных видов, включающие одну и более единиц технологического оборудования при наличии в их составе промышленных роботов, принято называть роботизированными комплексами. Роботизированный комплекс состоит из оборудования, в пределах которого изделия перемещаются поштучно. Началом (входом) комплекса и его окончанием (выходом) являются накопители различного рода.
Структура роботизированного комплекса может быть различной в зависимости от состава технологического оборудования, вспомогательных устройств, промышленных роботов.
В состав роботизированного комплекса, в котором промышленные роботы выполняют транспортные функции, входят соответствующее технологическое оборудование, различного рода накопители и сами промышленные роботы. Промышленные роботы могут работать совместно с отдельным оборудованием (прессами, установками для сварки и т.д.). В этом случае такие операции, как сварка, окраска, сборка, могут выполняться непосредственно на позиции входа - выхода заготовки, на специальной позиции или на транспортном конвейере, имеющем тактовое перемещение.
Рис. 14. РТК для механической обработки заготовок типа «вал»
Роботизированные комплексы различаютсяпо характеру производства, в котором они применяются. Для вновь создаваемых производств с новой технологией разрабатывается заново все основное оборудование, а для действующего производства, автоматизируемого на базе серийных промышленных роботов, изменение основного оборудования минимально.
По виду обработки роботизированные комплексы делят на РТК для обработки резанием, холодной штамповки, ковки, литья, прессования пластмасс, термической обработки, сварки, сборки, контроля, испытания и т.д.
Роботизированные комплексы производятся по типу основного технологического оборудования (полуавтоматы, автоматы с цикловым управлением, станки с ЧПУ и т.д.), типу применяемых роботов (числу манипуляторов, подвижности в пределах комплекса, типу управления) и числу единиц обслуживаемого оборудования.
Роботизированный технологический комплекс характеризуется двумя показателями:
- объемом партий продукции, которые могут выпускаться без переналадки комплекса,
- номенклатурой – перечнем выпускаемых видов продукции.
Компоновка РТК в зависимости от размещения технологического оборудования и промышленных роботов может быть:
1. линейной,
2. круговой,
3. линейно-круговой.
4. управление РТК подразделяется на:
5. централизованное,
6. децентрализованное,
7. комбинированное.
Централизованное управление может осуществляться от ЭВМ или от специального устройства, а децентрализованное - от местных устройств управления, которые связаны между собой для взаимной координации. Простейшим вариантом такой координации является увязка по времени начала и конца отдельных операций (включая выдачу команд и блокировок).
Комбинированное управление предполагает наряду с централизованным управлением наличие местных устройств.
Все эти варианты управления РТК могут быть программными и адаптивными как в отношении основного технологического оборудования, так и роботов.
По степени участия человека РТК могут быть двух видов:
- в первом человек выполняет некоторые технологические операции (основные или вспомогательные),
- во втором человек участвует в управлении комплексом.
В первом случае РТК будет не автоматическим, а автоматизированным.
Анализ последствий отказов
Для работающей технологической системы наиболее опасны внезапные отказы, т. е. отказы функционирования. Они непредсказуемы и могут привести к тяжелейшим последствиям:
1. отказ по точности обработки (когда Аф>Адоп) приводит к браку;
2. отказ функционирования, т. е. внезапный отказ станка, отдельного узла или детали. При этом могут возникать опасные ситуации:
3. поломка режущего инструмента (авария и брак);
4. поломка элементов механической части (узла, механизма, отдельной детали), что требует поиска и устранения неисправностей, а иногда и ремонта;
5. неисправности в системе управления, которые трудно обнаружить сразу (сгорела плата, элемент, нет контакта и пр.).
Экономический ущерб из-за отказов проявляется в следующем: работа с ухудшенными параметрами; повышенные простои и трудозатраты на восстановление работоспособности; снижение производительности и эффективности.
Для повышения надежности автоматизированных систем применяют специальные методы, хотя это требует дополнительных затрат.
Повышение информативности
Стабильность процесса обработки определяется уровнем надежности элементов РТК. Повысить надежность можно за счет повышения информативности о состоянии отдельных элементов РТК (и точности выполнения заданных функций), используя специальные технические средства информации—датчики.
Применяют датчики внутренней и внешней информации. Датчики внутренней информации используют для контроля за параметрами, обусловливающими надежность функционирования оборудования (станков с ЧПУ, роботов), — контроль температуры, давления, силы, вибраций и др.
Датчики внешней информации бывают контактные (тактильные, силомоментные, проскальзывания) и бесконтактные (расстояния, обнаружения, системы технического зрения).
Тактильные датчики позволяют: определить момент соприкосновения схвата с деталью; получить информацию о силе и давлении при захвате детали схватом; регистрировать «проскальзывание» детали в схвате; определить наличие детали в накопителе; определить исходное положение схвата.
Повысить работу роботов, не допустить отказов и аварий можно за счет оснащения РТК датчиками внешней информации (рис. 22). Если усилие зажима детали схватом недостаточное, то происходит экстренный останов робота и опасная ситуация ликвидируется.
Рис. 22. Алгоритм функционирования робота с датчиками внешней информации и АСУ ТП
Вопросы для самоподготовки:
1. Какие существуют состояния объекта в области надежности?
2. Назовите особенности отказов и охарактеризуйте их физическую природу?
3. Какие показатели оценки надежности существуют?
4. Чем обосновывается связь надежности и производительностью?
5. В чем выражается специфика формирования показателей надежности и их связь с производительностью?
6. Существует ли зависимость показателей надежности и производительности от времени эксплуатации станков?
7. На чем основывается принятие решений на начальных стадиях проектирования?
8. В чем заключаются принципы избыточности и резервирования?
9. Как реализуется принцип повышения информативности?
Для станков с ЧПУ
Управляющая программа (УП)—совокупность команд на языке программирования,соответствующая алгоритму функционирования станкапри обработке заготовок.
Технологический процесс изготовления деталей на станках с ЧПУсвязан с получением, обработкой, передачей, хранением и управлениемогромными информационными потоками. При этом важную роль играетчеловек (разработка ТП, работа в режиме диалога с ЭВМ, подготовкаи отладка УП, активное участие в организации и управлении процессомобработки).
Поэтому с позиции кибернетики комплекс системпроектирования ТП (САПР), подготовки УП (система автоматическогопрограммирования—САП) и управления процессом обработки (СЧГГУ)можно рассматривать как человеко-машинную систему, где человек используетуникальные возможности электронной техники (рис.23).
1. возможность комплексной автоматизации всего процесса изготовлениядеталей за счет широких технологических возможностейавтоматического программно-управляемого оборудования;
2. возможность автоматизации процесса проектирования ТП иподготовки УП с использованием САПР и САП (см. рис. 17).
3. возможность обеспечить автоматическое управление станками.
Рис. 23. Обобщенная структура и связь САПР, САП и СЧПУ приизготовлении деталей в условиях ГАП
При разработке ТП и подготовке УП большой объем информацииперерабатывается в определенной последовательности:
1. Разработка маршрутной технологии — определение состава ипоследовательности операций.
2. Разработка операционной технологии с расчетом режимов резания.
3. Расчет траектории движения режущих инструментов — расчеткоординат опорных точек.
4. Формирование команд и функций, кодирование информации.
5. Запись УП на программоноситель.
6. Проверка и отладка УП (внесение коррекции).
Программирование ТП изготовления деталей на станках с ЧПУ —качественно новый этап, когда выполняется часть работы (этапы 3-6),
Действия рабочего при обработке заготовок на обычном станке(после этапов 1-2) выполняются на станке с ЧПУ в автоматическомрежиме по УП. Под обработкой п
|
|
Семя – орган полового размножения и расселения растений: наружи у семян имеется плотный покров – кожура...
Опора деревянной одностоечной и способы укрепление угловых опор: Опоры ВЛ - конструкции, предназначенные для поддерживания проводов на необходимой высоте над землей, водой...
Архитектура электронного правительства: Единая архитектура – это методологический подход при создании системы управления государства, который строится...
Двойное оплодотворение у цветковых растений: Оплодотворение - это процесс слияния мужской и женской половых клеток с образованием зиготы...
© cyberpedia.su 2017-2024 - Не является автором материалов. Исключительное право сохранено за автором текста.
Если вы не хотите, чтобы данный материал был у нас на сайте, перейдите по ссылке: Нарушение авторских прав. Мы поможем в написании вашей работы!