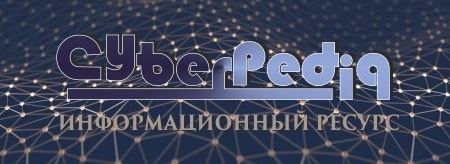
Особенности сооружения опор в сложных условиях: Сооружение ВЛ в районах с суровыми климатическими и тяжелыми геологическими условиями...
Кормораздатчик мобильный электрифицированный: схема и процесс работы устройства...
Топ:
Основы обеспечения единства измерений: Обеспечение единства измерений - деятельность метрологических служб, направленная на достижение...
Когда производится ограждение поезда, остановившегося на перегоне: Во всех случаях немедленно должно быть ограждено место препятствия для движения поездов на смежном пути двухпутного...
Оценка эффективности инструментов коммуникационной политики: Внешние коммуникации - обмен информацией между организацией и её внешней средой...
Интересное:
Средства для ингаляционного наркоза: Наркоз наступает в результате вдыхания (ингаляции) средств, которое осуществляют или с помощью маски...
Берегоукрепление оползневых склонов: На прибрежных склонах основной причиной развития оползневых процессов является подмыв водами рек естественных склонов...
Как мы говорим и как мы слушаем: общение можно сравнить с огромным зонтиком, под которым скрыто все...
Дисциплины:
![]() |
![]() |
5.00
из
|
Заказать работу |
|
|
Постановление Совмина СССР о строительстве Серовского завода ферросплавов (СЗФ) вышло 15 января 1951 г. 23 июня 1958 года было выпущена первая плавка ферросилиция. В декабре 1958 г. завершен ввод в эксплуатацию первой очереди плавильного цеха № 1 в составе шести рудовосстановительных печей мощностью по 10,5 МВ·А, которые тогда выплавляли 45 % и 75 %-ный ферросилиций. В конце 1961 г. состоялся пуск первой печи плавильного цеха № 2 и через год цех работал в составе девяти наклоняющихся печей мощностью по 3,5 МВ·А, производившихся средне- и низкоуглеро-дистый феррохром. С вводом цеха № 2 и переводом печей цеха № 1 на выплавку высокоуглеродистого феррохрома и ферросиликохрома завод стал специализированным предприятием по выплавке хромистых сплавов. Объем продукции постоянно увеличивался и составил около 30 % общего производства феррохрома в стране. Для обеспечения цеха № 2 известью в 1962 г. пущен в эксплуатацию цех обжига известняка в составе трех вращающихся горизонтальных печей.
Серовский завод ферросплавов находится в Свердловской области г. Серов.
Первый руководитель завода – директор В. П. Нахабин.
С 1963 г. развернулось строительство комплекса расширения цеха № 1 в составе трех электропечей с системой мокрой очистки колошникового газа. 1965 г. впервые в СССР освоена выплавка высокоуглеродистого феррохрома в закрытых печах. Начата отгрузка готовой продукции на экспорт. Работа печей характеризовалось высокой стабильностью, лучшими в отрасли технико-экономическими показателями, печной газ использовался в качестве топлива. Применение печного газа при производстве извести сэкономило природный газ и мазут.
Значительный этап в развитии завода – освоении производства низкоуглеродистого феррохрома методом смешение расплавов. Этот способ позволил получить низкоуглеродистый феррохром с очень малым содержанием углерода в больших количествах с более низкой себестоимостью, чем другими способами, а так же пониженным содержанием фосфора и азота. Это стало началом широко-масштабного завоевание внешнего рынка. Феррохром, получаемый методом смещение расплавов, неоднократно экспонировался на международных ярмарках и по качеству не уступал лучшим феррохромам западно-европейского производства. К настоящему времени на половине мощностей плавильного цеха № 2 производится феррохром по внедрении технологии, на заводах в странах СНГ такое производство отсутствует.
|
В 1967 г. введен в эксплуатацию участок переработки самораспадающихся известковых шлаков от производства низко- и среднеуглеродистого феррохрома.
Практически с момента пуска основных цехов на заводе не прекращалась работа по реконструкции и модернизации электропечей. На первом этапе мощность электропечей цеха № 1 было увеличена с 10,5 до 14,5 МВ·А, на втором – с 14,5 до 16,5 в цехе № 2 – с 3,5 до 5 МВ·А, затем с 5 до 7 МВ·А. В настоящее время проектная мощность завода перекрыта более чем в два раза.
В разные периоды на заводе были проведены широко-масштабные работы по механизации и автоматизации технологи-ческих производственных процессов. Так, механизированы нагрузка шихты в электропечи, электродной массы в кожуха самоспекающихся электродов; закрытие леток печей, чистка разливочных ковшей; механизирован и автоматизирован процесс грануляции сплавов, повышена его безопасность, организована производства фракционирования феррохрома в крупных масштабах; внедрены в производство новые схемы автоматизации дозирования шихты, перепуска электродов, управления электрическим режимом печей. Занятость ручным трудом в настоящее время составляет в целом по заводу менее 20 %.
Заводскими исследователями совместно с учеными научно-исследовательских институтов выполнен значительный комплекс работ по использованию новых видов углеродистых восстановителей, оптимизации параметров электропечей. В разные годы были следованны и внедрены в производства нетрадиционные виды углеродистых восстановителей: полукокс из углей Черемховского месторождения, полукокс из углей Кузбасса, тощие и жирные угли, отходы графитизации электродов и пр.
|
Переход к рыночной экономики поставил завод, как и все функционирующие предприятия черной металлургии, в крайне сложные условия. Сырьевая база завода в Республике Казахстан, и к 1996 г. поставки кусковой хромовой руды, без которой невозможно производство высокоуглеродистого феррохрома прекратились. В связи с этим была разработана технология выплавки высоко-углеродистого феррохрома с использованием кусковой руды Сарановского месторождения, находящегося в Пермской области. Однако эти руды с небольшим содержанием оксида хрома (36-38 %) после обогащения и отношением хрома к железу 1,9-2,1 отличаются высоким содержанием фосфора и ни в коей мере не могут компенсировать отсутствие кусковых казахстанских руд. Использование их привело к резкому снижению качественных и технико-экономических показателей при выплавке феррохрома и невозможности конкурировать с казахстанскими производителей феррохрома. В результате были освоены кусковые хромитовые руды дальнего зарубежья для производства высокоуглеродистого ферро-хрома и мелкие классы руд для выплавки низкоуглеродистого и среднеуглеродистого феррохрома.
В последнее время с целью снижения влияния негативных факторов осуществлен ряд технических мероприятий: построен и эксплуатируется участок по переработке текущих шлаков высокоуглеродистого феррохрома и шлаков со шлакоотвала; оптимизируется состав восстановительных смесей для снижения содержания фосфора в феррохроме и улучшения техника- экономических показателей; модернизируются печные трансформа-торы в направлении улучшения электрических параметров с целью увеличения производительности электропечей. В производство внедрена технология внепечной дефосфорации ферросиликохрома; расширен сортамент производства в результате внедрения выплавки силикомарганца из марганцевой руды Казахстана; освоена выплавка ферросилиция марок ФС 45 и ФС 65 и фракционирования феррохрома в полном объеме; построен гараж-размораживатель; дорогостоящий и дефицитный термоантрацит заменен на антрацит, выполнена реконструкция электрокальцинаторов при производстве электродной массы для самообжигающихся электродов; исследовано возможность марганцевых руд российских месторождений для выплавки силикомарганца с пониженным содержанием фосфора.
|
Для дальнейшего улучшения экономических показателей производства ферросплавов коллектив работает по следующим направлениям; повышения эффективности переработки шлаков и шлакоотвала с получением высококачественного металлоконцентрата, увеличения извлечения металла из шлаков, а также доведения объема переработки шлака до 500 тыс. т. в год; совершенствование подготовки шихты для выплавки высоко-, низко- и среднеуглеро-дистого феррохрома; расширение сырьевой базы производства силикомарганца с вовлечением в производство марганцевых руд российских месторождений; совершенствования электрических и технологических режимов выплавки ферросплавов; повышение единичной мощности рудовосстановительных электропечей; строительство за тремя печами газоочистных сооружений мощностью 500 тыс. м3 / час и другие мероприятия.
Основные проблемы завода связаны с отсутствием в России сырьевой базы для производства хромистых и марганцевых сплавов и высокой стоимостью электроэнергии. Решения их лежит в плоскости освоения российских месторождений хромистых и марганцевых руд, строительство мощностей по их обогащению, жесткое регулирование и минимизации стоимости электроэнергии.
|
|
Типы сооружений для обработки осадков: Септиками называются сооружения, в которых одновременно происходят осветление сточной жидкости...
Археология об основании Рима: Новые раскопки проясняют и такой острый дискуссионный вопрос, как дата самого возникновения Рима...
История развития хранилищ для нефти: Первые склады нефти появились в XVII веке. Они представляли собой землянные ямы-амбара глубиной 4…5 м...
Состав сооружений: решетки и песколовки: Решетки – это первое устройство в схеме очистных сооружений. Они представляют...
© cyberpedia.su 2017-2024 - Не является автором материалов. Исключительное право сохранено за автором текста.
Если вы не хотите, чтобы данный материал был у нас на сайте, перейдите по ссылке: Нарушение авторских прав. Мы поможем в написании вашей работы!