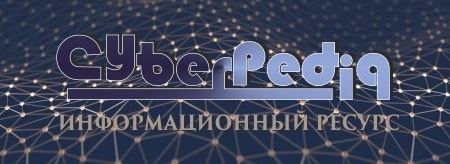
Автоматическое растормаживание колес: Тормозные устройства колес предназначены для уменьшения длины пробега и улучшения маневрирования ВС при...
Индивидуальные и групповые автопоилки: для животных. Схемы и конструкции...
Топ:
Основы обеспечения единства измерений: Обеспечение единства измерений - деятельность метрологических служб, направленная на достижение...
Марксистская теория происхождения государства: По мнению Маркса и Энгельса, в основе развития общества, происходящих в нем изменений лежит...
Интересное:
Средства для ингаляционного наркоза: Наркоз наступает в результате вдыхания (ингаляции) средств, которое осуществляют или с помощью маски...
Влияние предпринимательской среды на эффективное функционирование предприятия: Предпринимательская среда – это совокупность внешних и внутренних факторов, оказывающих влияние на функционирование фирмы...
Берегоукрепление оползневых склонов: На прибрежных склонах основной причиной развития оползневых процессов является подмыв водами рек естественных склонов...
Дисциплины:
![]() |
![]() |
5.00
из
|
Заказать работу |
|
|
В настоящее время в практике ферросплавного производства нашли наибольшее применение следующие способы разливки: на разливочных машинах различного типа; в стационарные поддоны и изложницы; послойно в напольные изложницы или в канаву методом «плавка на плавку».
Наиболее перспективной считается разливка ферросплавов на ленточных конвейерных машинах. Они применяются для разливки ферросилиция, силикомарганца, углеродистого ферромарганца и иногда углеродистого феррохрома. При этом значительно повышается механизация и производительность труда, улучшаются его условия в разливочном пролете, поскольку сплавы разливают не с помощью крана, а на специальных гидравлических кантователях, которые помещены в герметизированные камеры. Существенным недостатком машины конвейерного типа является переменная высота падения сплава при разливке, что вызывает сильное его разбрызгивание. Потери металла при разливке достигают 3 %, к тому же товарный вид получаемых слитков значительно ухудшается из-за опрыскивания мульд известковым молоком.
Для разливки высококремнистых сплавов, модификаторов и лигатур, а также сплавов, содержащих легкоокисляющиеся элементы, применяют карусельные машины конвейерно-тележечного типа (рисунок 3.6). По сравнению с конвейерной эта машина обеспечивает уменьшение потерь металла при разливке, улучшение качества и товарного вида слитков. Машина представляет собой замкнутую цепь тележек, размещенных на рельсовом пути. На тележках находятся поддоны–изложницы, обеспечивающие получение тонких слитков.
Для извлечения слитков изложницы либо переворачиваются, либо слитки выталкиваются специальным толкателем в короб, установленный под изложницей. Разливка в стационарные поддоны и чугунные изложницы представляет собой устаревший и малопроизводительный способ разливки ферросплавов, оставшийся в основном в цехах с рафинировочными печами и металлотермических цехах. Этот способ связан с повышенной загруженностью разливоч-ных кранов, высокой теплонапряженностью в цехе и необходимостью увеличения его площади для размещения стационарных изложниц. Однако, сплавы склонные к сегрегации (ферросилиций с содержанием >75 % Si), целесообразно разливать в массивные поддоны толщиной слитка до 80 мм. или в кристаллизаторы.
|
1 – ковш с кантователем; 2 – изложница; 3 – приемный бункер
Рисунок 3.6 – Карусельная разливочная машина.
В последние годы все более широкое распространение получает послойная разливка методом «плавка на плавку» (рисунок 3.7). За рубежом этот способ применяется при разливке марганцевых сплавов. Сплав разливают из ковша послойно в широкие канавы, расположенные вне цеха вдоль стены разливочного пролета. Послойная разливка позволяет резко снизить загруженность кранов разливочного пролета, тепловыделения в цехе, уменьшить размеры здания цеха. В этом случае разливочный пролет используют только для транспортировки сплава и шлака из цеха. Учитывая, что мощность ферросплавных печей постоянно растет, представляется рациональным вынести разливку сплава из плавильного корпуса.
При разливке ферросплавов важное значение имеет способ отделения металла от шлака. За рубежом имеются печи с раздельным выпуском сплава и шлака через две летки. В случае печей с одной леткой продукты плавки выпускают из печи в ковш с переливом шлака через верх ковша или через шлакоотделительное устройство (скиммер).
1 – тележка приводная с ковшом; 2 – чаша железобетонная; 3 – аспирационная установка
Рисунок 3.7 – Установка для напольной разливки ферросилиция
|
При выпуске в ковш с переливом легче регулировать параметры струи жидкого металла, металл получается чище и плотнее. Однако в этом случае необходимы достаточная площадь для разливочного участка, мостовые краны большой грузоподъемности, ковшовые тележки, что связано со значительными капиталовложениями.
При использовании скиммера, который может быть стационарным или передвижным, отпадает необходимость в кранах большой грузоподъемности, дополнительные площади нужны только для размещения скиммера и довольно длинных желобов; металл за скиммером может быть направлен непосредственно в изложницы разливочной машины. Однако при этом возможно загрязнение шлаком и образование в выпускных желобах избыточного количества скрапа, идущего в отвал. Следует отметить, что в случае разливки сплава по желобам из печи через скиммер в разливочный пролет упрощается компоновочное решение цеха, появляется возможность сократить ширину здания.
Практика показывает, что выпуск через ковш обязателен, если сплав в дальнейшем идет на рафинирование или его для разливки следует удалить от печи на некоторое расстояние. За рубежом выпуск через ковш применяют для кремнистых сплавов, а через скиммер – для сплавов марганца. Вопрос о том, какой способ выпуска сплавов, через ковш или через скиммер, предпочтительнее, решается отдельно в каждом конкретном случае.
Рисунок 3.8 – Схема фракционирования ферросплавов на отечественном ДСК
Разделка ферросплавов с целью получения требуемого размера кусков включает такие операции, как дробление и рассев (рисунок 3.8 и 3.9). Выбор типа дробилки зависит от прочности ферросплава. За рубежом изготавливают только фракционированные ферросплавы, т.е. сортированные на куски различной крупности. Производство фракционированных ферросплавов предусмотрено и отечественными стандартами. Использование сплавов определенного гранулометри-ческого состава в сталеплавильном производстве способствует быстрому усвоению легирующих элементов жидкой сталью, уменьшению теплопотерь металла в ковше.
Рисунок 3.9 – Схема фракционирования ферросплавов на ДСК фирмы KUE–KEN
Ферросплавы поставляют в кусковом (более 10 мм.), зернистом (10-2 мм.) и порошкообразном (2-0 мм.) виде. Порошки получают как измельчением сплава в дробилках, так и распылением его в жидком состоянии паром или инертным газом (грануляция). Развитие грануляции связано с увеличением спроса на ферросплавы небольшой крупности, которые могут непрерывно загружаться в сталеплавильные агрегаты.
|
|
Кормораздатчик мобильный электрифицированный: схема и процесс работы устройства...
Семя – орган полового размножения и расселения растений: наружи у семян имеется плотный покров – кожура...
Архитектура электронного правительства: Единая архитектура – это методологический подход при создании системы управления государства, который строится...
Биохимия спиртового брожения: Основу технологии получения пива составляет спиртовое брожение, - при котором сахар превращается...
© cyberpedia.su 2017-2024 - Не является автором материалов. Исключительное право сохранено за автором текста.
Если вы не хотите, чтобы данный материал был у нас на сайте, перейдите по ссылке: Нарушение авторских прав. Мы поможем в написании вашей работы!