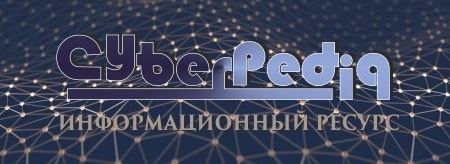
Состав сооружений: решетки и песколовки: Решетки – это первое устройство в схеме очистных сооружений. Они представляют...
Двойное оплодотворение у цветковых растений: Оплодотворение - это процесс слияния мужской и женской половых клеток с образованием зиготы...
Топ:
Генеалогическое древо Султанов Османской империи: Османские правители, вначале, будучи еще бейлербеями Анатолии, женились на дочерях византийских императоров...
Теоретическая значимость работы: Описание теоретической значимости (ценности) результатов исследования должно присутствовать во введении...
Интересное:
Мероприятия для защиты от морозного пучения грунтов: Инженерная защита от морозного (криогенного) пучения грунтов необходима для легких малоэтажных зданий и других сооружений...
Что нужно делать при лейкемии: Прежде всего, необходимо выяснить, не страдаете ли вы каким-либо душевным недугом...
Средства для ингаляционного наркоза: Наркоз наступает в результате вдыхания (ингаляции) средств, которое осуществляют или с помощью маски...
Дисциплины:
![]() |
![]() |
5.00
из
|
Заказать работу |
|
|
С торжественного пуска в июле 1931 г. Челябинского ферросплавного завода начался отчет эпохи советской ферросплавной промышленности. К этому времени коллектив предприятия освоил производство углеродистого феррохрома и приступил к выплавке ферросилиция. В последующие десять лет готовой объем продукции возрос с 3 до 70 тыс. и включал всю существующую в тот период номенклатуру феррохрома, ферросилиция, кремния кристалличес-кого, ферровольфрама и ферромолибдена. В годы Великой Отечественной войны в результате ввода дополнительных мощностей, реконструкции агрегатов и благодаря самоотверженному труду рабочих удалось вдвое увеличить выпуск ферросплавов.
В послевоенные годы по генеральному плану реконструкции и развития завода были введены в действия специализированные цехи: в 1954 г. по производству – ферровольфрама, в 1955 г. по производству – ферромолибдена. В начале 60-х годов после включения состав завода электродного отделения предприятия было преобразовано в Челябинский металлургический комбинат (ЧЭМК). В 1961 г. вступил в строй специализированный цех по выплавке низкоуглеродистого феррохрома, а через три года по производству ферросилиция. В 1978 г. в цехе № 8 началось освоение технологии выплавки низкоуглеродистого феррохрома методом смешивания рудно–известкового расплава с ферросиликохромом. Наивысшим уровень готового выпуска ферросплавов – 700 тыс. тонн был достигнут в 1988 г. К середине 90-х годов в результате снижения общего уровня промышленного производства и распада СССР производства ферросплавов сократилось до 400 тыс.
За 75-летнию историю комбинат были решены многие задачи по разработке и освоению принципиально новых технологий выплавке ферросплавов и расширению их номенклатуры. В частности, был создан не имеющий аналогов способ получения ферровольфрама вычерпыванием сплава, освоен уникальный обжиг молибденового концентрата в вертикальных многоподовых печах, внедрены водная грануляция ферросплавов и вращение ванн ферросилициевых печей. Впервые в стране был построен цех обжига известняка во вращающихся печах с использованием извести для производства высших марок для углеродистого феррохрома. Комбинат первым освоил углеродотермическую и силикотермическую технологии производства всей номенклатуры силикокальция и подавляющего большинства лигатур на его основе.
|
В начале 90-х годов значительно снизился спрос на лигатуры и модификаторы, что объясняется переориентированием большинства металлургических заводов на выпуск дешевых рядовых сталей. В частности, только Кузнецкий металлургический комбинат к концу 80-х годов потреблял в год более 1000 тонн силикокальция с ванадием для производства рельсов высшей категории, а Нижнетагильский металлургический комбинат – почти 2000 тонн кальцийтитан-алюминиевой лигатуры. В последние два года спрос на ряд лигатур возрос. В связи с этим на комбинате активно осваивается программа производства малотоннажных ферросплавов: комплексных модификаторов с магнием и кальцием, лигатур на основе ферросилиция и силикокальция с барием, алюминием и титаном в различных композициях. Большие технические мероприятия проводятся для обеспечения выпуска фракционированных ферросплавов, модификаторов и лигатур практически любого класса крупности. Комбинат готов к производству специальных сплавов на основе хрома, проводится подготовка к выплавке ферросилико-алюминия с использованием высокозольных углей.
В настоящее время ЧЭМК продолжает ориентироваться на производства широкой номенклатуры сплавов и удовлетворения требований к качеству продукции, как отечественных потребителей, так и зарубежных партнеров.
|
С 1996 г. комбинат осваивает производство марганцевых сплавов, ранее не выпускающихся в России. Большая работа ведется с казахстанскими поставщиками руды, часть руды закупается в Австралии. После решения вопроса обеспечения сырьем комбинат планирует приступить к выплавке средне- и низкоуглеродистого малофосфористого ферромарганца. Наличие производственных мощностей рафинировочных печей позволило отработать и осуществить технологию комплексной переработки отходов и шлаков производства ферросиликомарганца. В настоящее время отвальные шлаки содержат до 4 % MnO, благодаря чему удалось повысить степень извлечения марганца по комбинату до 84 %. Ввод в эксплуатацию рукавных фильтров с комплексом переработки уловленной пыли поможет решить большинство экологических вопросов и улучшить технико-экономические показатели. Освоение производства ферросиликомарганца и высокоуглеродистого ферромарганца, имеющих пониженное содержание фосфора (менее 1%), позволило предприятию занять свою нишу на рынке марганцевых ферросплавов и успешно конкурировать с украинскими и казахстанскими производителями.
Начиная с 1994 г. ЧЭМК продолжает увеличивать выпуск ферросплавов, составивших в 2000 г. 520 тыс. тонн. Общий объем продукции за 75 лет составил около 23 млн. тонн ферросплавов, модификаторов и лигатур, в том числе 3700 ферросиликохрома; 540 силикокальция; 470 ферромолибдена; 440 ферровольфрама; 230 сплавов марганца; 45 модификаторов и лигатур, в с Mg, Al, V, Ti, Ni, РЗМ; 18 кристаллического кремния; 3 ферротитана.
Освоение новых сплавов позволило комбинату, с одной стороны, более гибко реагировать на запросы рынка, с другой – сохранить высокий уровень производства в условиях нестабильной работы смежных предприятий.
Ритмичное обеспечение сырьем и энергоносителями – основа успешного развития предприятия. Длительное время источником главного для комбината виды сырья были хромитовые руды Казахстана. Уникальное запасы Казахстана, высокое качество, отлаженные в системе плановой экономики хозяйственные связи не стимулировали геологических исследований по изысканию новых месторождений в других регионах страны. С разрывом этих связей хромитовые руды перешли в категорию остродефицитного сырья, и комбинат был вынужден изыскивать их альтернативные источники. Перспективы дальнейшего увеличения объема продукции и повышения ее рентабельности оказались непосредственно связанными с развитием местной сырьевой базы. В настоящее время в Челябинской области известно более сотни мелких проявлений хромитов, часть из них отрабатывалась с дореволюционного периода вплоть до 40-х годов, в 11 рудоносных массивах сосредоточенно более 125 месторождений. Общие прогнозные ресурсы хромовых руд на территории области превышают 190 млн. тонн, а ожидаемый выход в промышленную категорию С1 составляет 38 млн. тонн. Создание в 1995 г. на ЧЭМК отдела сырьевых ресурсов, впоследствии реорганизованного в производственно-сырьевое управление, позволило комбинату организовать работу по промышленному освоению запасов хромитовых и марганцевых руд Челябинской области.омышленную категорию С1 составляет 38 млн. рии облости превышают 190 млн.редоточенно более 125 месторождений.нными с развитии Возобновление в 1995 г. геологических работ обеспечило ежегодную добычу 60-70 тыс. местных хромитовых руд, что соответствует примерно четверти общей потребности ЧЭМК в хромитовых рудах.
|
Изменение сырьевой базы, сопровождающейся резким ухудшением качества руд, привело к переориентации производства на переработку бедного хроморудного сырья и освоению технологии выплавке марганцевых ферросплавов. Низкое содержание оксида хрома (15-25 %), специфика минералогического состава руд, увеличение 2,5-3 раза отношение фосфора к хрому потребовали серьезного изменения технологии и решения сложных организационных задач. Инженерный корпус комбината успешно справился с этим, и сейчас предприятие готово к использованию низкокачественному труднообогатимых хромовых руд. Начиная с 1996 г. на ЧЭМК переработано 325 тыс. тонн хромовых руд Уральского региона содержащих около 50 тыс. тонн хрома, что позволило сохранить уровень производства феррохрома. Эти меры в значительной степени способствовали ослаблению зависимости комбината от зарубежных поставщиков и стабилизировали экономическую ситуацию на горно-металлургических предприятиях области.
|
Наряду с освоением новых видов сырья и продукции на комбинате продолжают совершенствовать технологию получения традиционных сплавов – ферросилиция и феррохрома. Использование щепы, окатышей, брикетированных материалов, новых видов углеродистых восстановителей позволило в последние годы не только повысить технико-экономические показатели производства, но и в ряде случаев улучшить качество выпускаемой продукции.
На ЧЭМК эффективно функционирует корпоративная информационная система, включающая систему управление производством (АСУП) на уровне предприятия и система управления технологическими процессами на уровне цехов и отдельных агрегатов (АСУТП). Основной функционирования информационной системы является современная высокоскоростная вычислительная сеть, объединившая компьютеры основных цехов, лабораторий и отделов заводоуправления в единое информационное производство. Это позволяет отслеживать и прогнозировать движение материальных и финансовых ресурсов, качество сырья и продукции, вести документооборот от стадии отгрузки сырья на комбинат до сдачи готовой продукции потребителю. В системе АСУТП ферросплавных печей решаются задачи управления электрическим режимом и перепуском электродов в реальном времени оптимизируют распределение тепла в ванне печи, улучшает энергетический КПД установки, повышает производительность печи, уменьшает удельный расход электроэнергии. Автоматическое управление дозировкой обеспечивает оптимальное соотношение компонентов шихты, равномерную загрузку агрегата, расчет параметров для систем управления электрическим режимом. Разрабатывая и внедрения производство эти и многие другие наукоемкие направления, комбинат активно сотрудничает с научно-исследовательскими институтами и высшими учебными заведениями.
Переработка и утилизация отходов производства по-прежнему остается главнейшей задачей. Построенный в начале 30-х годов на далекой окраине небольшого города, комбинат оказался в центре мегаполиса, что выдвинуло проблемы защиты окружающей среды на первый план. Многие экологические вопросы давно и успешно решены, но некоторые, и весьма существенные, остались и требуют своего решения.
С 1967 г. на комбинате работает цех сепарации самораспадаю-щихся шлаков, в котором ежегодно извлекается и возвращается в производства до 15 тыс. тонн феррохрома. До распада СССР ежегодно реализовалось 340-360 тыс. тонн шлакового порошка в качестве мелиоранта для известкования кислых почв и около 100 тыс. тонн в литейное производство для быстротвердеющих стержневых смесей, часть шлака использовалось в строительной индустрии и стекольной промышленности. С разрушением хозяйственной системы и ликвидации централизованных фондов «Союзсельхозхимии» мелиорация кислых почв практически прекратилась. Спад производства и рост железнодорожных тарифов свели на нет потребление шлака литейщиками. Активная работа ведется по реализации шлака в строительной индустрии и дорожном строительстве, и некоторые сдвиги наметились, но наиболее перспективным и, главное, востребованным направлениям является рекультивация многочисленных техногенных выработок. С 1993 г. на комбинате работает цех по переработки неразлагающихся шлаков. Твердые шлаки текущего производства, а также материал шлакового отвала перерабатывается на строительный щебень с извлечением из него металла. Ежегодно цех производит и реализует около 90 тыс. тонн строительного щебня и песка, извлекается и возвращается в производства до 1,5 тыс. тонн хрома, т. е. около 5 % выпуска. Введенный в эксплуатацию в 2000 г. участок по изготовлению асфальтобетонных смесей позволил вовлечь в переработку шлаки текущего производства и обеспечить не только собственные, но и частично городские потребности в высококачественном асфальте.
|
Особое место в экологических проблемах комбината занимает Переработка шлакового отвала, занимающего 37 га, на которой находится около 18 млн. тонн материала. К решению этой сложнейшей проблеме привлекались многие организации, например южноафриканская фирма «Бэтман». Опытно промышленная эксплуатация отсадочной машины позволила проанализировать состав отвала и наметить пути его комплексной переработки. В ближайший план комбината строительство участка по переработке отвала с извлечением металла и превращением залежей отвала в экологический чистый материал, пригодный для рекультивации и дорожного строительства.
Практика эксплуатация цеха по очистке оборотной воды от систем мокрых газоочисток закрытых печей показало реальную возможность исключение попадание загрязненных стоков в реку Миасс. Оборот технической воды составляет более 97 %. По заключению «Уралэнергочермета», комбинат имеет один из лучших на металлургических предприятиях Уральской зоны показателей водного хозяйства. Ежегодно при работе 11 закрытых печей образуется около 30 тыс. тонн шлама. Основной проблемой его остается утилизация, определенные направления, в частности использования шлама в цементной промышленности уже проработаны, но доводка оборудования и организация широкомасштабной реализации требуют времени.
На комбинате особое внимание уделяется охране воздушного бассейна. Все плавильные и обжиговые печи оборудованы газоочистными сооружениями, над повышением эффективности которых ведется постоянная работа. В 2000 г. Введены в эксплуатацию рукавные фильтры в цехе № 5. В связи с организацией выплавки марганцевых сплавов строятся рукавные фильтры печами цеха №7. Совсем недавно, впервые в России, в цехах электродного производства внедрен католический дожиг смолистых веществ, образующихся в результате обжига электродов. Это позволило значительно сократить выбросы внедренных веществ в атмосферу города.
|
|
История развития пистолетов-пулеметов: Предпосылкой для возникновения пистолетов-пулеметов послужила давняя тенденция тяготения винтовок...
История развития хранилищ для нефти: Первые склады нефти появились в XVII веке. Они представляли собой землянные ямы-амбара глубиной 4…5 м...
Особенности сооружения опор в сложных условиях: Сооружение ВЛ в районах с суровыми климатическими и тяжелыми геологическими условиями...
Своеобразие русской архитектуры: Основной материал – дерево – быстрота постройки, но недолговечность и необходимость деления...
© cyberpedia.su 2017-2024 - Не является автором материалов. Исключительное право сохранено за автором текста.
Если вы не хотите, чтобы данный материал был у нас на сайте, перейдите по ссылке: Нарушение авторских прав. Мы поможем в написании вашей работы!