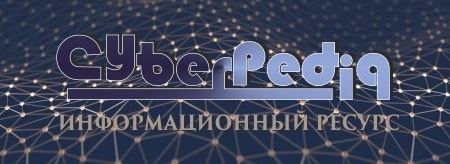
Особенности сооружения опор в сложных условиях: Сооружение ВЛ в районах с суровыми климатическими и тяжелыми геологическими условиями...
Адаптации растений и животных к жизни в горах: Большое значение для жизни организмов в горах имеют степень расчленения, крутизна и экспозиционные различия склонов...
Топ:
Определение места расположения распределительного центра: Фирма реализует продукцию на рынках сбыта и имеет постоянных поставщиков в разных регионах. Увеличение объема продаж...
Устройство и оснащение процедурного кабинета: Решающая роль в обеспечении правильного лечения пациентов отводится процедурной медсестре...
Характеристика АТП и сварочно-жестяницкого участка: Транспорт в настоящее время является одной из важнейших отраслей народного...
Интересное:
Инженерная защита территорий, зданий и сооружений от опасных геологических процессов: Изучение оползневых явлений, оценка устойчивости склонов и проектирование противооползневых сооружений — актуальнейшие задачи, стоящие перед отечественными...
Мероприятия для защиты от морозного пучения грунтов: Инженерная защита от морозного (криогенного) пучения грунтов необходима для легких малоэтажных зданий и других сооружений...
Влияние предпринимательской среды на эффективное функционирование предприятия: Предпринимательская среда – это совокупность внешних и внутренних факторов, оказывающих влияние на функционирование фирмы...
Дисциплины:
![]() |
![]() |
5.00
из
|
Заказать работу |
|
|
ПРЕДИСЛОВИЕ К ПЕРВОМУ ИЗДАНИЮ
Книга предназначена в качестве учебника для студентов-технологов металлургических высших учебных заведении, специализирующихся по кузнечно-штамповочному производству.
В данном труде автор стремился изложить методически материал так, чтобы студент привыкал инженерно мыслить и понимать направление в развитии кузнечно-прессового машиностроения. С этой целью в книге приведены некоторые исторические справки о совершенствовании кузнечно-прессовых машин, разъясняющие, почему то или иное направление в конструировании кузнечно-прессового оборудования не получило развития.
В книге описаны типовые кузнечно-прессовые машины, преимущественно применяемые в Советском Союзе. В ней не рассматриваются не проверенные практикой в СССР виды машин (машины высоких энергий типа «Динапак», гидровинтовой пресс-молот, виброгидропрессы и др.). Наряду с описанием схем основных кузнечно-прессовых машин приведены расчетные материалы, необходимые для понимания работы машины, эффективного ее использования и правильной эксплуатации, Ряд методов расчета публикуется впервые (расчет чеканочного пресса, расчет рычажного амортизатора прижимного ползуна пресса двойного действия, расчет допускаемого усилия на ползуне шестерноэксцентрикового пресса, определение требуемого веса тяги автоматического устройства управления работой фрикционного молота с доской).
Существенные уточнения внесены в расчеты, опубликованные ранее автором данного учебника и другими исследователями (расчет штока молота, к. п. д. кривошипных машин, расчет фрикционного винтового пресса, расчет усилия предварительной затяжки стяжных болтов станин, расчет фрикционной муфты, расчет тормоза, расчет допускаемых усилий на ползуне бульдозеров, горизонтальноковочных машин, горячештамповочных прессов, расчет фундамента с амортизаторами под молоты, расчет фрикционного молота с доской, расчет срезающегося предохранителя во втулке маховика, расчет фрикционного предохранителя и ДР.), Все расчёты построены на системах единиц измерения МКСГ и МКГСС (килограмм, килограмм-сила, метр, секунда и др.).
|
Параллельно введен в действие ГОСТ 9867—61 на единицы измерений в соответствии с Интернациональной системой СИ.
ГОСТ 7664—61 и другие, получившие широкое распространение, должны быть немедленно заменены единицами измерения системы СИ во всем народном хозяйстве. Внедрение в практику расчетов системы СИ будет проводиться постепенно в течение ряда лет, поскольку все измерительные приборы, аппаратура, ГОСТы на кузнечно-прессовые машины, парк кузнечно-прессовых машин, справочные материалы по механическим и физическим свойствам металлов и сплавов и т. п. построены на единицах измерения в соответствии с системами МКГС и МКГСС и др.
Таким образом, в ближайшие годы параллельно с системой СИ будут действовать системы единиц измерения МКГС и МКГСС. В связи с этим в книге приведены таблицы для пересчета единиц измерения по ныне распространенным системам в единицы измерения системы СИ.
В работе над рукописью принимали участие следующие рецензенты: специалисты кафедры машин и технологии обработки металлов давлением МВТУ имени Баумана, возглавляемой доктором техн. наук проф. А. И. Зиминым, а также доктор техн. наук проф. И. В, Климов, которые тщательно просмотрели рукопись, сделали ряд замечаний и дали много ценных советов, учтенных автором при доработке рукописи, что, несомненно, повысило ее качество.
ВВЕДЕНИЕ
Кузнечное дело, как его называли раньше, является одним из наиболее древних способов обработки металлов; оно существовало еще задолго до нашей эры. Однако начало использования машин-орудий для ковки относится лишь к XVI в. нашей эры, когда стали применять примитивные рычажные молоты, приводившиеся в действие при помощи водяных колес. Это так называемые хвостовые, лобовые и среднебойные молоты; вес бабы у них не превышал 700 я (70 кг). По мере развития металлургии в машиностроения, особенно судостроения и артиллерии, требовалось все более мощное оборудование. В конце первой половины XIX в. появились паровые молоты, а в середине второй половины XIX в. — гидравлические прессы. Потребность в производстве крупных поковок привела в конце XIX в. к быстрому росту размера молотов, вес падающих частей которых достиг 1,20 Мн. (120 Т). Самый большой молот в России был установлен в 1873 г. на Мотовилихинском орудийном заводе в г. Перми. Вес падающих частей этого молота составлял 0,5 Мн (50 Т). Ныне этот молот снят. В 80-х годах прошлого столетия пятидесятитонный молот был установлен также на Обуховском заводе в Петербурге.
|
По мере улучшения конструкции гидравлических прессов и повышения их быстроходности началось постепенное вытеснение крупных ковочных молотов гидравлическими прессами. В настоящее время уже не устанавливают ковочных молотов с весом падающих частей более 50 кн. (5 Т) и вместе с тем имеются гидравлические ковочные прессы, развивающие усилие 100-М50 Мн (10000-т-15000 Т).
С организацией крупносерийного производства широкое рас-пространение получила штамповка. Для ее осуществления потребовалось создать специальные штамповочные молоты, вес падающих частей которых достиг 300 кн. (30 Т). Для штамповки крупных поковок построены штамповочные гидравлические прессы усилием 300-750 Мн (30000-75000 т с): Создаются проекты штамповочных гидравлических прессов усилием свыше 750 Мн (75000 тс).
Наряду с кузнечными машинами этого типа появляются универсальные и специализированные, главным образом кривошипные машины (горизонтальноковочные, гибочные, просечные, вытяжные, двойного действия, многоползунные ковочные, горячештамповочные отбортовочные, болтогаечные автоматы и т.п.)
В последнее время в технологии кузнечных цехов стали все чаше применять принципы прокатки. Используют раскаточные станы, например, в производстве колец шарикоподшипников, прокатные станы в производстве шариков для подшипников, для получения проката периодического профиля, накатки зубьев шестерен и т. п.
|
В дореволюционной России не было организованного производства кузнечных машин. Все кузнечное оборудование, имевшееся в начале XX в., было иностранного производства, если не считать, что отдельные заводы для своих нужд изготовляли кузнечное машинное оборудование, представлявшее собой копии с иностранных образцов, в ряде случаев несколько улучшенные по сравнению с оригиналом. Следует отметить, что хотя своего национального кузнечного машиностроения в России не существовало, однако теоретическая мысль русских инженеров в анализе работы кузнечных машин была для того времени на сравнительно большой высоте. Русские инженеры (проф. П. М. Мухачев, проф. И. А. Тиме, проф. А. П. Гавриленко, проф. Я. Н. Маркович и др.) разработали элементы расчета молота.
Научная мысль русских ученых стала быстро развиваться после Октябрьской революции. Теория кузнечных машин-орудий и анализ их рабочего цикла связаны с именами таких советских ученых, как проф. Я. Н. Маркович (теории парового молота и пневматического молота), проф., докт. техн. наук А. И. Зимин (уточненный метод теоретического анализа парового молота, теория фрикционного пресса), докт. техн. наук М. В. Сторожев (теории гидравлических прессов и кривошипных прессов), канд. техн. наук И. И. Гирш и проф. В. И. Залесский (теории кривошипных гибочных машин и горизонтальноковочных машин), проф. Е. П. Унксов (теория пружинного и пневматического молотов), проф. И. В. Климов (теория бесшаботного молота, уточненный метод теплового расчета паровых молотов), канд. техн. наук В. Ф. Щеглов (уточненный метод расчета паровоздушных молотов) и др. Этот краткий перечень имен показывает, что именно нашей стране принадлежит приоритет в разработке теоретического анализа работы основных видов кузнечного оборудования.
Резкое улучшение в организации производства кузнечно-прессовых машин в СССР достигнуто в результате выполнения решений съездов КПСС по развитию народного хозяйства, особенно XXIII съезда. В СССР воспитаны кадры конструкторов и созданы учреждения по исследованию и проектированию кузнечных машин — орудий: Экспериментальный научно-исследовательский институт кузнечного машиностроения (ЭНИКМАШ), центральный научно-исследовательский институт технологии машиностроения (ЦНИИТМАШ), Всесоюзный научно-исследовательский институт металлургического машиностроения (ВНИИМЕТМАШ), Центральное бюро кузнечного машиностроения (ЦБКМ), специальные конструкторские бюро 9 и 10 и конструкторские
|
бюро при специализированных заводах по производству кузнечно-прессовых машин и другие организации, обеспечивающие создание оригинальных советских конструкций.
В результате реализации наших пятилетних планов развития народного хозяйства создана прочная специализированная промышленная база для изготовления кузнечного оборудования. В 1969 г. было изготовлено свыше 40000 единиц кузнечно-прессового оборудования. Отечественные кузнечные машины типизированы. Таким образом, в Советском Союзе создано отечественное кузнечно-прессовое машиностроение и имеются неограниченные возможности для производства различных кузнечных машин, как по типам, так и по мощности.
В настоящее время штамповочное производство достигло такого совершенства, что можно получать поковки, не требующие в дальнейшем обработки на металлорежущих станках, так как точность их размеров выдержана с допуском до 0,05 мм, а чистота и качество поверхности выше, чем после шлифовки. Наряду с этим производительность при изготовлении деталей машин методом штамповки во много раз выше, чем при обработке методом снятия стружки (резанием). По этой причине область применения кузнечно-штамповочных методов производства деталей непрерывно расширяется и в настоящее время этот метод является одним из основных и самым прогрессивным в машиностроении. Парк кузнечных машин непрерывно увеличивается в связи с организацией предприятий с крупносерийным и массовым характером производства.
Количество, темп роста и удельный вес кузнечных машин в общем станочном парке характеризуют индустриальную мощь страны и степень совершенства машиностроения. В наиболее экономически развитых странах кузнечные машины составляют до 1/3 общего станочного парка, в то время как 25—30 лет назад они составляли лишь около 10—15%. Число типоразмеров современных кузнечно-прессовых машин достигает нескольких тысяч наименований. В СССР количество действующих кузнечно-прессовых машин составляет около 400 тыс. единиц.
В связи с большим разнообразием типов кузнечно-прессовых машин — орудий их при изучении необходимо классифицировать на основе общих Принципиальных признаков, к которым относятся:
|
1) кинематические и динамические признаки рабочего хода машины — орудия, т. е. хода, в течение которого деформируется поковка (таким образом, рабочий ход начинается с момента соприкосновения бойка, штампа или пуансона с поковкой и заканчивается в момент остановки рабочего инструмента или изменения направления его движения на обратный ход);
2) характер или род привода;
3) технологические признаки, т. е. для выполнения какой технологии предназначена машина.
По кинематическим и динамическим признакам рабочего хода кузнечные машины — орудия подразделяют на три группы *. К первой — относятся машины, работающие ударом, т. е. за счет кинетической энергии, накопленной в процессе движения рабочими частями машины к моменту начала рабочего хода. Эта энергия к моменту окончания рабочего хода оказывается полностью израсходованной, причем, пока она не будет полностью израсходована, рабочий ход будет продолжаться. Если запасенная энергия оказывается недостаточной для требуемой деформации поковки, то для дальнейшей деформации поковки необходим повторный ход, для того чтобы соответствующие детали машины приобрели известный запас кинетической энергии.
К машинам первой труппы относятся все типы молотов и винтовые прессы. Изменение скорости за рабочий ход этих машин можно представить графически, откладывая по оси ординат скорость V, а по оси абсцисс — путь Н или время (кривая АВ рабочего хода,
Рис. 1. Изменение скорости рабочего хода у машин: а — первой группы: б — второй группы; в — третьей группы
*Проф. А. И. Зимин, предложивший классификацию кузнечных машин по кинематическим и динамическим признакам рабочего хода, делит эти машины на четыре группы. Мы полагаем, что рабочий ход (ход деформации) у четвертой группы имеет такой же характер, как у машин третьей группы: скорость изменяется от максимального значения до нуля по жесткой кривой.
|
рис 1, а). Скорость v0 бойка (штампа) в начале деформации поковки имеет всегда большее значение, чем на всем остальном рабочем ходе и по желанию может регулироваться в широких пределах до максимальной величины, которую может развить данная машина. Кривая АВ1, для первой группы машин может принимать различную кривизну в зависимости от сопротивления металла деформации. Другими словами, скорость в процессе рабочего хода (процесс деформации металла) может затухать быстрее или медленнее (кривая АВг) в зависимости от сопротивления металла, причем и величина рабочего хода, и время на его совершение будут соответственно различными. Продолжительность рабочего хода (продолжительность процесса деформации) исчисляется тысячными и десятитысячными долями секунды (молоты) и в некоторых случаях (винтовые прессы) доходит до секунды.
Ко второй группе относятся машины, работающие только за счет энергии, непрерывно подводимой к ее подвижным частям (гидравлические прессы). Рабочий ход этих машин может быть прерван в любой момент путем прекращения подачи энергии, что характерно для машин данной группы. Кривая изменения скорости рабочего хода АСВ (рис. 1, б) не является жесткой и может принимать различную кривизну в зависимости от сопротивления металла деформации. Рабочий ход, как правило, начинается после того, как инструмент (боек, штамп и т. п.) наложен на поковку, и, таким образом, скорость в процессе работы изменяется от нуля, достигает максимума и опять падает до нуля. Продолжительность рабочего хода у машин второй группы исчисляется секундами и на тяжелых машинах доходит до десятков секунд. Рабочий ход иногда начинают с некоторой начальной скоростью* vн, далее она достигает v-макс и падает до нуля. В эту группу машин входят все гидравлические прессы.
К третьей группе относятся машины, у которых скорость за время рабочего хода изменяется по жесткой кривой**, зависящей от кинематической особенности данной машины (рис I, в). У таких машин энергия предварительно запасается (применяется маховик), но не расходуется полностью. К этой группе относятся все кривошипные и ротационные машины. Продолжительность рабочего хода у них составляет десятые доля секунды.
В зависимости от характера привода каждая из указанных групп машин делится на подгруппы, а последние разделяются по технологическому назначению (рис. 2).
* Соприкосновение рабочего инструмента с поковкой в этом случае происходит со скоростью Vв. С этой скоростью совершается удар подвижных частей машины (пресса) о поковку. Удар передается на стол пресса и через его опоры — на фундамент, что может привести к износу (смятию) опор и поломке стола машины. Такая работа на прессе неправильна.
** В данном случае не принимают во внимание перепад числа оборотов и упругую деформацию машины.
ОБЩИЕ СВЕДЕНИЯ
Паровоздушные молоты (рис. 3) работают на паре или на сжатом воздухе. При этом применяется давление от 0,4— 1,2 Мн/м2 (4 до 12 ати). Ввиду того, что процесс расширения и сжатия пара и воздуха происходит по разным законам, при переводе молота с пара на воздух в большинстве случаев необходимо соответственно регулировать паровоздухораспределительные органы *.
Паровоздушные молоты бывают простого и двойного действия. Паровоздушным молотом простого действия называют молот, у которого пар (воздух) действует снизу на поршень и служит только для подъема падающих частей. Падающие части такого молота (см. рис. 3) перемещаются вниз под действием силы тяжести. Накопленная энергия к моменту удара составляет:
, (1)
где m — масса падающих частей (кГ*сек2)/м (кг);
voп — скорость бойка в момент соприкосновения с поковкой, для молота простого действия, м/сек. Для повышения энергии удара, как это видно из формулы (1), выгодно увеличивать voп. Поэтому было предложено в момент падения подвижных частей ускорять их движение путем впуска пара сверху поршня. Таким образом, была получена схема паровоздушного молота двойного действия: при подъеме пар впускается в цилиндр под поршень и выпускается сверху поршня, при падении — наоборот.
* Это относится к ковочным молотам, у которых расширение пара (воздуха) происходит на сравнительно большом пути движения подвижных частей.
У штамповочных молотов в процессе подъема подвижных частей период расширения незначительный и регулировку распределительных органов при переводе с одного вида энергии на другой можно не производить.
У молотов двойного действия при падении падающих частей с такой же высоты, что и у молотов простого действия, скорость vo в момент удара
,
где
коэффициент 1,8, а не 2, принят в связи с учетом сопротивления трения, в основном в сальниках штока, при падении подвижных частей молота
, (2)
где Н — высота падения, м.
Отсюда энергию удара молотов двойного действия можно было бы определить по формуле
, (3)
но с введением молотов двойного действия оказалось возможным уменьшить высоту молота за счет уменьшения хода, а следовательно, и строительную высоту цеха. Поэтому вследствие меньшей величины хода (примерно на 20%) у молотов двойного действия по сравнению с молотом простого действия Ао=1,8Аоп.
Скорость подвижных частей в момент удара у молота простого действия V оп =4,5—6,5 м/сек; скорость молота двойного действия V о =6,5—9 м/сек. Вследствие меньшего хода и большей скорости падения количество ударов в минуту у молотов двойного действия больше, чем у молотов простого действия.
Следует отметить, что результат при ковке будет различным в зависимости от того, за счет чего получена энергия удара (за счет массы или скорости). При одинаковом значении энергии удара Ао большая масса подвижных частей молота проковывает металл на большую глубину. Это объясняется различным временем действия удара.
ОТ КОВОЧНЫХ
Энергия, приобретаемая массой, воспринимающей удар, соответствует уравнению (20). У штамповочных молотов коэффициент восстановления к больше, чем у ковочных (более жесткий удар). Для того чтобы энергия, передаваемая грунту и вызывающая сотрясения, значительно не увеличилась, масса шабота у штамповочных молотов принимается большей, чем у ковочных. У штамповочных молотов шабот в 20—30 раз тяжелее падающих частей. В СССР штамповочные молоты изготовляются -в соответствии с ГОСТ 7024—54 весом падающих частей от 0,0063— 0,16 Мн (от 0,63 до 16 Г). Кроме того, в индивидуальном порядке изготовляют штамповочные молоты 0,25 Мн (25 Т) и более.
К штамповочным молотам предъявляются следующие требования: недопустимость перекоса оси шабота по отношению к оси падающих частей молота и недопустимость сдвига верхнего штампа относительно нижнего. Первое требование удовлетворяется путем установки стоек молота на шаботе (рис, 46). Вследствие этого штамповочный молот по внешнему виду резко отличается от ковочного, у которого должно иметься в рабочем пространстве больше места для манипуляции с заготовкой и накладным инструментом. Стойки молота связаны с шаботом посредством болтов с пружинами, смягчающими сотрясения верхней части молота (цилиндр, парораспределительные органы и т. п.) и уменьшающими напряжение в болтах.
Второе требование выполняется развитием базы направления бабы, а сами направляющие делаются регулируемыми посредством продольных (см. рис. 46) или поперечных (рис. 47, а) клиньев. Первый тип предпочтителен, так как требует меньше времени для регулировки.
Количество выступов у W-образных направляющих (рис.47, б) может быть от двух до восьми. Зазор между направляющими и бабой должен обеспечивать необходимую точность штамповки и возможность некоторого расширения бабы вследствие ее нагрева в процессе работы. Поэтому по мере нагрева зазор в направляющих уменьшается, что необходимо учитывать при регулировании направляющих.
Направляющие следует регулировать так, чтобы баба не сдвигалась вбок от осевой линии цилиндра, так как иначе произойдет изгиб штока, работающего у штамповочных молотов и без того
с большими напряжениями. Деформация поковок по высоте, особенно при последних ударах процесса штамповки, весьма незначительна. Энергия удара расходуется при этом на малом пу-
ти, отчего развивается большое ускорение торможения падающей системы. Поэтому штоки штамповочных молотов по сравнению
со штоками ковочных работают значительно меньший период период времени (см. гл. I)
§ 15. КРЕПЛЕНИЕ СТОЕК НА ШАБОТЕ
Существует два основных типа крепления стоек молота с ша
ботом.
I тип (рис. 48). Недостаток соединения заключается в том, что опорная поверхность соприкосновения стойки с шаботом мала, вследствие чего с течением времени она сминается.
|
II тип (см. рис. 46). Стойки молота устанавливают на шабот, выверяют клиньями и закрепляют болтами. Эта конструкция в отношении износа соприкасающихся опорных поверхностей стойки и шабота значительно лучше предыдущей. Стойки молота в ранних конструкциях были стянуты внизу и в верхней части болтами с распорными трубами (рис. 49), отчего стойки можно одновременно перемещать (например, при установке штампов) по шаботу вдоль фронта, чем, однако, редко пользуются. Кроме того, болты с распорными трубами затрудняют работу штамповщика, стесняя ему подход к рабочей зоне. Поэтому в более современных конструкциях (см. рис. 46) отказались от применения взаимной стяжки стоек болтами I распорными трубами. Болты с пружинами, притягивающие стойки к шаботу, устанавливают с наклоном, что предотвращает возможность сближения стоек (перемещения их вдоль фронта) в момент удара молота. Перемещение стоек по шаботу поперек фронта
|
$ 17. ПАРОРАСПРЕДЕЛЕНИЕ У ШТАМПОВОЧНЫХ МОЛОТОВ
|
Парораспределительными органами штамповщик управляет от педали, шарнирно закрепленной на шаботе (рис. 51) и имеющей ограниченный ход. Штамповка в чистовом ручье завершается за небольшое число ударов (обычно от одного до 'пяти). Следовательно, для завершения процесса штамповки за минимальное число ударов желательно, чтобы первый удар был максимальной энергии, Поэтому у штамповочных молотов вместо держания бабы на весу имеется цикл ее качания. При ненажатой педали автоматически регулируется впуск и выпуск пара посредством золотника, передвигаемого с помощью кинематической связи с саблей, скользящей по скосу бабы. Каналы в дросселе при этом значительно перекрыты, и проходящий через него пар мнется.
При цикле качания баба все время передвигается вверх и вниз на верхнем участке общего хода, причем, когда поршень подходит к верхнему положению, то сверху него, на участке В 'Нт (рис. 52, а) происходит сжатие пара, а на участке у'Нт — впуск свежего пара. При этом снизу поршня на участке В Нт пар расширяется, а на участке "(1—-у— -В)Н m происходит его выпуск *,
Вследствие этого баба, дойдя до верхнего положения, остановится и сразу начнет опускаться. При спускании саблеобразный рычаг передвигает золотник вниз, отчего после прохождения участка (1—у— В)Нm прекратится выпуск нижнего пара, а в конце участка y 'Нт произойдет отсечка впуска верхнего пара. Стало быть, на участке В Нт будет происходить сжатие нижнего пара, а на участке В 'Нт — расширение верхнего пара. Затем начнется впуск снизу и выпуск сверху поршня. При построении предполагаемых индикаторных диаграмм кривые расширения верхнего и сжатия нижнего пара продолжаются за участки отсечки пара (см. рис. 52,а).
* Парораспределение можно наладить так, чтобы выпуска нижнего пара не происходило, т.е. 1-y-B=0, но при этом требуется следить за своевременным выпуском из цилиндра конденсата при продолжительном цикле качания.
Баба в процессе опускания, не дойдя примерно одной трети полного хода 1/3 Н m) до нижнего положения, затормозится и начнёт опять подниматься и т. д. Так будет осуществляться цикл качания. Для совершения удара необходимо нажать педаль. При этом золотник передвинется вверх и откроет окна для впуска верхнего и выпуска нижнего пара, а дроссель откроется полностью, отчего мятие пара при прохождении через дроссель будет минимальным (СМ. рис. 52. а ).
Момент нажатия педали для совершения удара должен совпасть с моментом подхода бабы к верхнему положению, когда сверху поршня уже имеется паровая подушка. Таким образом, в этот момент сверху поршня будет находиться пар под давление в снизу — выпуск. Вследствие этого первый удар будет обладать большей энергией, чем если бы имело место держание на весу, при котором переключение золотника на положение, соответствующее удару, происходит в момент, когда снизу поршня имеется давление, более высокое, чем сверху.
Если после удара оставить педаль нажатой, то баба останется в крайнем нижнем положении, так как золотник передвинется саблей на такой уровень, при котором пар из полости снизу поршня будет еще выпускаться (или произойдет отсечка выпуска), а сверху поршня будет продолжаться впуск свежего пара (или произойдет отсечка впуска). Получится так называемый прилипающий, или единичный удар. Для подъема бабы необходимо отпустить педаль. При этом золотник опустится. Начнется подача нижнего пара и выпуск верхнего в соответствии с рассмотренным ранее первым ходом вверх при цикле качания бабы. Дроссель при этом окажется открытым только частично.
Величина энергии удара зависит от хода педали при нажатии
последнюю. При большем ходе нажатия педали дроссель от-
кроется на большую величину, а золотник поднимется выше.
Следовательно, впуск пара сверху поршня и выпуск снизу него
производиться на большем пути в процессе падения бабы.
Кроме того, вследствие меньшего мятия в дросселе, пар, поступающий в цилиндр, будет иметь большее давление. Отсюда и
энергия удара получится большей.
И штамповке высоких поковок величина недохода бабы до нижнего положения при цикле качания Н н=1/3Нт иногда окапается недостаточной для безопасной установки заготовки в ручей. В этом случае необходимо наладить парораспределитель-устройство не на цикл качания, а на держание подвижных частей молота на весу. Для этого начальное положение золотника устанавливается ниже с таким расчетом, чтобы при крайнем верхнем положении подвижных частей молота не было впуска верхнего и выпуска нижнего пара, так как последний должен удерживать систему подвижных частей от падения. При такой наладке (рис. 52, б) период впуска нижнего пара и выпуска верх-
него пара получается большим, чем при цикле качания. В результате к Моменту, когда система подвижных частей молота поднимется на величину Нт, она будет еще обладать известным запасом кинетической энергии, и движение вверх будет продолжаться. При этом поршень упрется в стержень предохранителя в верхней крышке цилиндра и остаток накопленной энергии подвижных частей молота будет расходоваться на преодоление всех сопротивлений, в том числе на сжатие пружин или воздуха (пара) предохранителя.
Таким образом, при подъеме подвижные части молота пройдут дополнительный путь &Нт (см. рис. 52, б — наладка на «держание на весу»). После того как накопленная энергия при подъеме полностью израсходуется, система остановится и силой сжатых пружин или воздуха (пара) предохранителя будет отодвинута вниз на величину & Нт, н а которую был поднят стержень предохранителя в процессе предшествовавшего подъема (т. е. баба остановится и будет удерживаться на высоте Нт).
Если сравнительно длительное время держать подвижные части на весу, то вследствие конденсации пара система медленно начнет опускаться. Как только в процессе этого опускания баба передвинется до уровня, при котором автоматически передвинутый золотник начнет открывать нижние окна на впуск свежего пара, давление под поршнем возрастает, и подвижные части молота быстро поднимутся. При нажатии на педаль для совершения единичного удара впуск верхнего и выпуск нижнего пара будет происходить не на всем пути Нт (см. рис. 52, б — педаль нажата, наладка на «держание на весу»), так как золотник расположен ниже, чем при наладке на цикл качания. Отсюда следует, что первый единичный удар обладает меньшей энергией, чем в рассмотренном ранее случае. Последующие удары вследствие большего хода падения подвижных частей (Нт+&Нт) и ускоряющего действия предохранителя, воздействующего на поршень, имеют большую энергию, чем первый удар. При построении ожидаемых индикаторных диаграмм точка [ a 1] — начало заметного мятия пара, точка a1 — исходная для построения кривой расширения и соответствующие точки [аII] и аII для верхнего пара нахо-дятся так, как было описано ранее (см. гл. И, § 13).
Часто оказывается, что при наладке на «держание на весу» удар в предохранитель получается чрезмерно сильным. Тогда следует изменить размеры полок золотника, увеличив их в нижнюю сторону, так, как показано на (рис. 52, а (наладка на цикл качания), линией наложенной проекции.
С помощью так называемого контролера 1 (см. рис. 51) можно изменять путем перемещения рукоятки начальное положение дросселя, пропускающего к золотнику пар с большей или мен шей степенью мятия, чем следует пользоваться для установления требуемой величины давления пара в зависимости от наличного давления в паропроводе.
Как видно из изложенного, у штамповочных молотов получило распространение полуавтоматическое парораспределение. Отсечка пара происходит автоматически, совершение удара и подъем после него подвижных частей молота осуществляются посредством управления педалью. Отсюда следует, что у штамповочных молотов имеет место качественное (при помощи дросселя) и количественное (при помощи золотника) регулирование пара.
|
Одно время у штамповочных молотов ("Чемберсбург", США) пытались применять вместо цилиндрических плоские золотники (рис. 53). Предполагалось, что плоский золотник будет иметь следующие преимущества: не потребует уплотнительных колец; утечка пара через зазоры будет несколько меньше; появится возможность компенсировать износ за счет поджатия плиты (щеки) посредством клиньев. Однако оказалось, что штамповочные молоты, оборудованные плоским золотником, преимуществ не имеют, но изготовление и ремонт таких золотников сложнее, чем цилиндрических. Поэтому плоские золотники распространения не получили.
ОБЩИЕ СВЕДЕНИЯ
Пневматическим молотом называется молот, работающий за счет разрежения и сжатия воздуха, находящегося между компрессорным и рабочим поршнями. Давление в цилиндре во время работы молота изменяется примерно от 0,06 до 0,3 Мн/мг (0,6—3 ата). Работу пневматического молота регулируют количеством подаваемого воздуха от компрессора в рабочий цилиндр. Органы распределения находятся между цилиндрами компрессора и молота. Частота ударов включенного в работу молота соответствует числу оборотов вала- компрессора. Коэффициент полезного действия пневматических молотов несколько выше, чем у паровых.
Коэффициент полезного действия самого молота, считая от мощности, потребляемой электродвигателем, составляет =35%. При отличном состоянии молота этот коэффициент может быть доведен до 65 и даже до 70%. В наиболее благоприятных условиях электроэнергия, подводимая к электродвигателю молота, составляет 21% от энергии топлива, израсходованного в котельной. Таким образом, общий экономический к. п. д. всей установки, считая от энергии топлива, составляет 7%, а в лучшем случае— около 14%.
Несмотря на сравнительно высокий экономический к. п. д., пневматические молоты с падающими частями весом свыше 10 кн (1 T) не нашли широкого применения из-за сложности конструкции и частого выхода из строя, хотя имеются отдельные установки пневматических молотов с весом падающих частей до 30 кн (З Т).
Пневматические молоты предназначены для ковки. Их целесообразно устанавливать в тех случаях, когда требуются ковочные молоты с весом падающих частей не более 10 кн (1 Г), а также когда нет паровоздушной установки и нерентабельно ее строить ввиду небольшого числа устанавливаемых ковочных молотов. В большинстве случаев пневматические молоты используют для ковки резцов и для ремонтных целей в промышленности и сельском хозяйстве. Они бывают простого и двойного действия.
ОБЩИЕ СВЕДЕНИЯ
Как было указано ранее (см. гл. I, § 1) при деформации со скоростями 18 м}сек и более происходит интенсивное местное течение поверхностных слоев металла. Вследствие кратковременного воздействия удара тепло, выделившееся в местах сдвига при деформации металла, не успевает отводиться, отчего резко проявляется местный тепловой эффект, и сопротивление металла деформации в этих зонах падает. Этот эффект используется для штамповки тонко оребренных поковок или готовых деталей в высокоскоростных молотах, развивающих скорость к моменту удара 18 м/сек и более.
Отсюда следует, что высокоскоростные молоты предназначены для штамповки поковок с тонкими ребрами. Как правило, штамповку на них завершают за один удар. В качестве энергоносителя в высокоскоростных молотах используется энергия сжатого газа (азота). Строятся они по двум принципиальным схемам: по типу молота, у которого система, воспринимающая удар, имеет эластичную опору в виде амортизаторов, и до типу бесшаботных молотов со встречным ударом.
|
ПРЕДИСЛОВИЕ К ПЕРВОМУ ИЗДАНИЮ
Книга предназначена в качестве учебника для студентов-технологов металлургических высших учебных заведении, специализирующихся по
|
|
Историки об Елизавете Петровне: Елизавета попала между двумя встречными культурными течениями, воспитывалась среди новых европейских веяний и преданий...
Археология об основании Рима: Новые раскопки проясняют и такой острый дискуссионный вопрос, как дата самого возникновения Рима...
Семя – орган полового размножения и расселения растений: наружи у семян имеется плотный покров – кожура...
Типы оградительных сооружений в морском порту: По расположению оградительных сооружений в плане различают волноломы, обе оконечности...
© cyberpedia.su 2017-2024 - Не является автором материалов. Исключительное право сохранено за автором текста.
Если вы не хотите, чтобы данный материал был у нас на сайте, перейдите по ссылке: Нарушение авторских прав. Мы поможем в написании вашей работы!