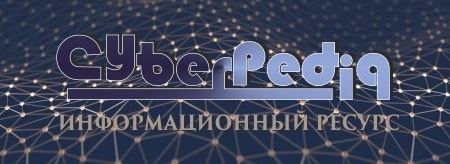
Кормораздатчик мобильный электрифицированный: схема и процесс работы устройства...
Эмиссия газов от очистных сооружений канализации: В последние годы внимание мирового сообщества сосредоточено на экологических проблемах...
Топ:
Генеалогическое древо Султанов Османской империи: Османские правители, вначале, будучи еще бейлербеями Анатолии, женились на дочерях византийских императоров...
Организация стока поверхностных вод: Наибольшее количество влаги на земном шаре испаряется с поверхности морей и океанов...
История развития методов оптимизации: теорема Куна-Таккера, метод Лагранжа, роль выпуклости в оптимизации...
Интересное:
Средства для ингаляционного наркоза: Наркоз наступает в результате вдыхания (ингаляции) средств, которое осуществляют или с помощью маски...
Лечение прогрессирующих форм рака: Одним из наиболее важных достижений экспериментальной химиотерапии опухолей, начатой в 60-х и реализованной в 70-х годах, является...
Искусственное повышение поверхности территории: Варианты искусственного повышения поверхности территории необходимо выбирать на основе анализа следующих характеристик защищаемой территории...
Дисциплины:
![]() |
![]() |
5.00
из
|
Заказать работу |
|
|
Система цилиндр — поршень. Паровой цилиндр ковочных молотов отливают из чугуна, причем толщину стенок принимают с учетом того, что при износе можно будет произвести расточку цилиндра. Больше всего изнашивается средняя часть цилиндра (А на рис. 9). Цилиндр должен выдержать не меньше трех переточек, причем при каждой переточке удаляют 5 мм металла и более на сторону.-
Цилиндры штамповочных молотов отливают из мягкой углеродистой стали 30, внутрь них вставляют чугунные (марки СЧ28-48) втулки. Толщина стенки для стальных цилиндров 0,1 Dц и для малых молотов —0,2 Dц, где Dц — внутренний диаметр цилиндра. Толщина стенки втулки — 0,05 Dц (точнее 0,08-0,03 Dц; чем больше молот, тем меньший берут коэффициент). Минимальная толщина втулки после переточек 12-20 мм, иначе втулка разбивается ударами поршня в процессе работы молота.
Штамповочные молоты имеют диаметры поршня примерно на 15% меньше (работают с большим наполнением пара и меньшим его расширением).
Вследствие неодинакового теплового расширения цилиндра и поршня (цилиндр охлаждается интенсивней, чем окруженный паром поршень), последний вставляют в цилиндр с некоторым зазором (табл. 2).
Таблица 2
Зазоры между цилиндром и поршнем, мм.
Диаметр | Ковочный молот | Штамповочный молот |
До 200 | 0,5 | 0,35 |
200—350 | 0,6 | 0.4 |
350—500 | 0,75 | 0.5 |
500—585 | 1.0 | 0,6 |
585—635 | 1,25 | 0.7 |
635—675 | 1,5 | 0,8 |
675—710 | 1,5 | 0,9 |
Для создания плотности между поршнем и стенками цилиндра на поршень в специальные канавки надевают два — четыре стальных разрезных кольца (рис. 10 и 11), которые пружинят,
обеспечивая необходимую плотность. Срок службы колец в штамповочных молотах составляет 1,5—3 месяца. В ковочных молотах срок службы в 3—4 раза больше.
|
Для создания плотности между поршнем и стенками цилиндра на поршень в специальные канавки надевают два — четыре стальных разрезных кольца (рис. 10 и 11), которые пружинят, обеспечивая необходимую плотность. Срок службы колец в штамповочных молотах составляет 1,5—3 месяца. В ковочных молотах срок службы в 3—4 раза больше.
|
Поршневые кольца имеют два вида замков (рис. 11, а и б), Замок типа, показанного на рис. 11, б, лучше герметизирует, не труднее в изготовлении.
Кольца в малом количестве изготовляют следующим образом. Пруток изгибают по окружности до соприкосновения концов, отрезают некоторую часть от одного конца и изготовляют замок так, чтобы зазор (см. рис. 11) при свободном состоянии кольца составлял 0,1 Dц, где Dц—диаметр цилиндра. После пригонки замков кольцо сжимают, запаивают, а затем обтачивают по наружной поверхности до необходимого диаметра. Затем его распаивают и надевают на поршень.
Если расход поршневых колец значителен, то можно применять специальные приспособления, позволяющие отковать из стали марки 30 обечайки на несколько колец. После отжига или нормализации обечайку можно обточить на требуемые размеры по диаметру, затем произвести накатку во внутренней поверхности в специальном приспособлении. Затем обечайку можно разделить на отдельные кольца. Далее пропиливают и пригоняют замки. Вследствие полученного наклепа по внутренней поверхности от накатки кольцо будет пружинить.
Зазор между канавкой поршня и внутренним диаметром кольца в рабочем состоянии должен быть равен зазору между поршнем и цилиндром (см. табл. 2). Зазор в канавке необходим для того, чтобы обеспечить возможность сжатия кольца при посадке поршня в цилиндр и чтобы кольцо могло полностью войти в канавку при боковом нажиме поршня на стенку цилиндра. Зазор в канавке по высоте кольца составляет —0,15 мм.
Профиль поперечного сечения поршневого кольца показан на рис. 10. Высота кольца а=5-6,5 мм для молотов до 15 кн (1,5 Г), а=9,5-10 мм для молотов свыше 15 кн. Ширина кольца с=9,5-7-10 мм для молотов до 15 кн, с= 12— 19 мм для молотов до 60 кн. Применяют кольца и других размеров. Для удобства заправки кольца в канавку со стороны внутренней поверхности кольца снимают фаски по 1 мм с каждой стороны.
|
Система поршень — шток.
Шток молота изготовляют ковкой из легированной или углеродистой стали и подвергают термической обработке на сорбитовую структуру (желательно, чтобы предел прочности был не менее 800—900 Мн/м2, удлинение — около 18%). Лучшую стойкость показывают штоки, изготовленные из стали марок 40ХНМ и ОХН1М.
Срок службы штока у штамповочных молотов составляет 1,5-2 месяца, а у ковочных — несколько лет. Для увеличения стойкости штока целесообразно подвергать его поверхностной закалке и нагартовке: нижнюю часть штока на 1/з его длины — обычной закалке, а остальную часть оставлять в отожженном
виде. Срок службы обработанного таким образом штока возрастает. Для исключения поперечных рисок, создающих концентрацию напряжений, следует шлифовать шток не вкруговую, а в продольном направлении и потом обязательно полировать. Шток во всех случаях изготовляют отдельно от поршня и бабы, за исключением небольших ковочных молотов.
Типы соединения штока с поршнем. На рис. 12, а, 6 и в приведены устаревшие конструкции соединения штоков с поршнем у ковочных молотов. В момент удара контактные опорные поверхности штока и поршня (рис. 12, а) сминаются. Вследствие этого образуются зазоры, которые по мере работы молота увеличиваются. В результате происходит ослабление соединений и срыв гайки.
Для увеличения опорных поверхностей применяли конусную посадку (рис. 12, б). Угол конусности больше угла трения и составляет 1:9, Этот способ соединения неудобен тем, что при ударе молота поршень наползает на шток, увеличивая зазор под гайкой. При обратном ходе подвижных частей молота происходит удар поршня о гайку» а затем и срыв последней.
Для устранения возможности появления зазора под гайкой использовали соединение штока с поршнем, состоящее из разрезного и сжимающего кольца (рис. 12, в). Сжимающее кольцо надевают на разрезное в горячем состоянии.
В штамповочных молотах применяют более простое крепление штока с поршнем (рис. 12, г). Подобное соединение штока и поршня используют и в современных ковочных молотах.
|
Угол наклона конуса на сторону изготовляют меньше угла трения — около 1град 47' (конусность 1:16). Поршень насаживают на шток в горячем состоянии. В верхней части поршня имеется фаска, а у штока — кольцевой выступ, который расклепывают, предварительно нагрев его. Получается достаточно прочное соединение. Поршень, разогретый до 400—450° С, насаживают строго перпендикулярно по отношению к оси штока. Для расклепки верхней части головки штока ее разогревают обычно ацетиленовым пламенем. Следует заметить, что головку штока можно и не расклепывать, так как при горячей посадке сила трения достаточна, чтобы удержать поршень на штоке, а сама операция расклепки связана с риском ослабления посадочного натяга.
Крепление штока, с бабой. Для ковочных молотов старых конструкций применяют несколько типов крепления штока с бабой (рис. 13,а,б и в).
I тип. Шток (см. рис. 13, а) на конце имеет обратный конус с шаровой пятой. При помощи двух разрезных полуколец 2, затягиваемых двумя клиньями /, шток прижимается к опорной подушке 3. Недостатки этого типа соединения состоят в том, что в момент удара изнашивается шаровая опорная поверхность. Как только образуется (вследствие смятия) зазор между подушкой и опорной поверхностью штока, необходимо подтянуть клинья или, не хватает хода затяжки клиньев, поставить прокладки под сферическую опору.
II тип. Конец штока заточен в виде обратного конуса (рис. 13, б) я на бабе имеется соответствующая выточка большего размера. Конец штока вводят сверху в выточку, затем в зазор между штоком и бабой закладывают разрезную втулку; все это затягивают с помощью клиньев. Такое крепление более надежно в отношении срыва бабы. Клин 4 при ударе затягивает основной клин и не дает возможности образоваться зазору у опорной поверхности штока.
III тип. Были попытки создать шарнирное крепление (рис. 13, в) для уменьшения напряжения в штоке. Однако никакого преимущества этот вид крепления на практике не показал.
IV т и п. У штамповочных, а также у современных ковочных молотов шток к бабе крепят посредством трения (рис. 13, г). Угол наклона образующей конуса меньше угла трения — около 1°11' (конусность 1:25). Посадку производят в холодном состоянии. Заключается она в том, что шток забивают в бабу верхним паром и затем 1—3 раза ударяют по подложенной деревянной доске. При последующих ударах молота продолжается дальнейшее продвижение штока в бабу до тех пор, пока не наступит силовое равновесие. Например, по опытам В. Ф. Лошкарева, у молота весом падающих частей 16 кн (1600 кГ) за 60 ударов шток внедрился в бабу на 21 мм, после чего при дальнейших ударах продвижение его практически прекратилось. После длительной работы молота невозможно разъединить шток и бабу, так как при ударах частицы бабы и штока взаимно внедряются настолько, что создают механически не разъединимую систему (поверхность конуса как бы «изъедена оспой»). Чтобы обеспечить выбивание штока из бабы, необходимо между ними ставить медные (латунные) прокладки толщиной 1—2 мм.
|
В современной конструкции крепления штока к бабе (рис. 13, д) имеется цилиндрическая по внешней поверхности и разрезанная по образующей стальная втулка (толщина стенки 10— 20 мм), вставляемая в цилиндрическое гнездо бабы. Твердость материала втулки должна быть ниже твердости бабы. Внутренняя поверхность втулки выполнена конусной. В нее вставляют шток с латунной прокладкой. Конусную поверхность втулки цементируют на твердость, несколько меньшую, чем твердость конуса штока.
Запрессованная часть конуса штока испытывает сжимающие напряжения в поперечном направлении. Наибольший сжимающим напряжениям подвержена нижняя часть запрессованного конуса. При ударе шток в незажатой части получает деформацию уширения в горизонтальном направлении вследствие продольного сжатия. У запрессованной части конуса, наоборот, в результате дополнительного упругого внедрения в гнездо бабы возрастает деформация сжатия в горизонтальном направлении. В сечении штока, переходном от сжатия к уширению, возникают напряжения сдвига одного слоя относительно другого.
|
|
|
Биохимия спиртового брожения: Основу технологии получения пива составляет спиртовое брожение, - при котором сахар превращается...
Археология об основании Рима: Новые раскопки проясняют и такой острый дискуссионный вопрос, как дата самого возникновения Рима...
Эмиссия газов от очистных сооружений канализации: В последние годы внимание мирового сообщества сосредоточено на экологических проблемах...
Таксономические единицы (категории) растений: Каждая система классификации состоит из определённых соподчиненных друг другу...
© cyberpedia.su 2017-2024 - Не является автором материалов. Исключительное право сохранено за автором текста.
Если вы не хотите, чтобы данный материал был у нас на сайте, перейдите по ссылке: Нарушение авторских прав. Мы поможем в написании вашей работы!