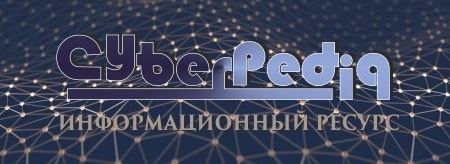
История развития пистолетов-пулеметов: Предпосылкой для возникновения пистолетов-пулеметов послужила давняя тенденция тяготения винтовок...
Архитектура электронного правительства: Единая архитектура – это методологический подход при создании системы управления государства, который строится...
Топ:
Характеристика АТП и сварочно-жестяницкого участка: Транспорт в настоящее время является одной из важнейших отраслей народного хозяйства...
Марксистская теория происхождения государства: По мнению Маркса и Энгельса, в основе развития общества, происходящих в нем изменений лежит...
Эволюция кровеносной системы позвоночных животных: Биологическая эволюция – необратимый процесс исторического развития живой природы...
Интересное:
Аура как энергетическое поле: многослойную ауру человека можно представить себе подобным...
Уполаживание и террасирование склонов: Если глубина оврага более 5 м необходимо устройство берм. Варианты использования оврагов для градостроительных целей...
Мероприятия для защиты от морозного пучения грунтов: Инженерная защита от морозного (криогенного) пучения грунтов необходима для легких малоэтажных зданий и других сооружений...
Дисциплины:
![]() |
![]() |
5.00
из
|
Заказать работу |
|
|
Процесс измельчения. Физико-механические свойства материалов
Измельчением называют процесс разрушения кусков твердого материала при критических внутренних напряжениях, создаваемых в результате какого-либо нагружения и превышающих соответствующий предел прочности.
Напряжения в материале могут создаваться механическим нагружением, температурными воздействиями, ультразвуковыми колебаниями и др. Наибольшее применение в современном производстве имеют механические способы измельчения.
Измельчение делят на дробление и помол, а машины, применяемые для этих целей, называются дробилками и мельницами. В зависимости от размеров частиц продукта различают следующие виды измельчения:
- дробление крупное (dк = 100…350 мм), среднее (dк =40…100 мм),мелкое (dк = 5…40мм),
- помол грубый (dк = 0,1…5 мм), средний (dк = 0,05…0,1 мм), тонкий (dк = 0,001…0,05 мм), сверхтонкий (dк< 0,001 мм).
Основной характеристикой процесса измельчения является степень измельчения, которая определяется соотношением средневзвешенных размеров частиц материала до и после измельчения:
i = d н / d к.
Степень измельчения отражает технологию и определяет параметры измельчителей.
С целью обеспечения эффективности измельчение материала от исходной до конечной крупности осуществляется, как правило, в несколько приемов, с последовательным переходом от крупного дробления к более мелкому и к помолу с постадийным разделением материала по классам. Следовательно, процесс измельчения целесообразно осуществлять последовательно на нескольких измельчителях. Каждыйотдельный измельчитель выполняет часть общего процесса, называемую стадией измельчения.
Число стадий измельчения определяется требуемой степенью измельчения. Например, если в исходном твердом материале содержатся куски размером до 1200 мм, а готовый продукт должен содержать частицы с максимальным размером до 40 мм, то общая степень измельчения i o = 1200 / 40 = 30.
|
Степень измельчения, достигаемая на одной машине, для большинства видов дробильного оборудования не превышает 3…7. Поэтому для обеспечения i = 30 необходимо применить несколько стадий дробления, например: i 1 = 3, i 2 = 3, i 3 = 4. Тогда i 0 = i 1 i 2 i 3 = 3 . т.е. требуется минимум три стадии измельчения.
В то же время следует отметить, что увеличение стадий дробления приводит к повышению капитальных затрат на строительство заводов, переизмельчению материала и к удорожанию эксплуатации завода. Поэтому выбор схемы измельчения следует осуществлять из условия обеспечения минимального числа стадий дробления. Однако, в ряде случаев только применение многостадийных схем (четырех- и пятистадийных) обеспечивает получение готового продукта в необходимом объеме и высокого качества.
Энергозатраты, нагрузки на элементы измельчителей и качество продукта зависят от прочности, хрупкости, твердости, упругости, абразивностии плотности твердых материалов.
Прочность - свойство твердого материала сопротивляться разрушению при возникновении внутренних напряжений, появляющихся в результате какого-либо нагружения. Обычно прочность твердых материалов оценивается пределом прочности при сжатии σc. По величине σc измельчаемые материалы делят на мягкие (σc< 80 МПа), средней прочности (σc = 80...150 МПа), прочные (σc = 150...250 МПа) и очень прочные (σc> 250 МПа).
При других видах деформаций прочность твердых материалов существенно ниже. Например, предел прочности известняка, гранита составляет при растяжении 2…5 %, при изгибе 8…10 % и при сдвиге 10…15 % предела прочности при сжатии.
Хрупкость - свойство твердого материала разрушаться без заметных пластических деформаций. Она определяется на специальном копре числом ударов мерного груза. По числу ударов, выдерживаемых образцами, твердые материалы делят на очень хрупкие (до 2), хрупкие (2…5), вязкие (5…10), очень вязкие (более 10).
|
Абразивность - способность перерабатываемого материала изнашивать рабочие органы машины. Ее оценивают в граммах износа эталонных бил, отнесенных к одной тонне измельченного материала.
Машины для дробления материала
Барабанные мельницы
Барабанные мельницы используются при производстве цемента, извести, гипса, керамических изделий и т.п. для измельчения материала до частиц размером менее десятых долей миллиметра. Процесс помола отличается большой энергоёмкостью и стоимостью.
В барабанных мельницах материал измельчается внутри полого вращающегося барабана. При вращении мелющие тела (шары, стержни) и измельчаемый материал (называемые «загрузкой») сначала движутся по круговой траектории вместе с барабаном, а затем падают по параболе. Часть загрузки, расположенная ближе к оси вращения, скатывается вниз по подстилающим слоям. Материал измельчается в результате истирания при относительном перемещении мелющих тел и частиц материала, а также вследствие удара.
В промышленности строительных материалов барабанные мельницы получили наибольшее применение.
Барабанные мельницы классифицируют по:
- режиму работы – периодического и непрерывного действия;
- способу помола – сухого и мокрого помола;
- характеру работы – мельницы, работающие по открытому и замкнутому циклу;
- форме мелющих тел – шаровые, стержневые и самоизмельчения (без мелющих тел);
- способу разгрузки – с механической и пневматической разгрузкой;
- конструкции загрузочного и разгрузочного устройства – с загрузкой и выгрузкой через люк, через полые цапфы и с периферийной разгрузкой;
- конструкции привода – с центральным и периферийным приводом.
Барабанные мельницы различаются между собой следующими признаками: измельчающей средой, т. е. родом применяемых измельчающих тел (шары, стержни, ролики, галька, крупные куски руды); геометрической формой барабана (короткий цилиндр, длинный цилиндр, конус); способом разгрузки материала из барабана (разгрузка периодическая или непрерывная; причем последняя может быть: через диафрагму, а затем через цапфу или непосредственно через цапфу или только через диафрагму; способом измельчения (сухой, мокрый).
|
Рис.2 Классификация барабанных мельниц
Классификация барабанных мельниц приведена в табл.1, которую иллюстрирует рис.2.1; Придерживаясь последовательности, принятой в табл.1 и кратко характеризуя мельницы различного типа, можно отметить следующие их особенности.
Табл.1 Классификация барабанных мельниц.
Тип мельниц | Измельчающие тела | Способ разгрузки готового продукта | Способ измельчения |
1. Шаровая периодического действия (рис. 2.1, а) | Стальные шары | Периодическая разгрузка через люк | Сухой (для лабораторных — сухой и мокрый) |
2. Шаровая с периферической разгрузкой (рис. 2.1, б ) | Стальные шары | Разгрузка через цилиндрическое сито | Сухой и мокрый |
3. Шаровая с центральной разгрузкой (рис. 2.1, в) | Стальные шары | Центральная разгрузка (непосредственно через цапфу) | Сухой и мокрый |
4. Шаровая с решеткой (рис. 2.1, г) | Стальные шары | Разгрузка через решетку, а затем через цапфу | Сухой и мокрый |
5. Шаровая с открытым концом (рис. 2.1, д) | Стальные шары | Через решетку (без цапфы) | Сухой и мокрый |
6. Трубная однокамерная (рис. 2.1, е) | Стальные шары | Центральная разгрузка (через цапфу) | Сухой и мокрый |
7. Трубная многокамерная (рис. 2.1, ж) | Стальные шары | Между камерами — разгрузка через решетку; из последней камеры — центральная разгрузка | Сухой и мокрый |
8. Коническая мельница (рис. 2.1, з) | Стальные шары | Центральнаяразгрузка | Сухой и мокрый |
9. Стержневая с центральной разгрузкой (рис. 2.1, и) | Стальные стержни (длиной, равной длине барабана) | Центральнаяразгрузка | Мокрый |
10. Стержневая с периферической разгрузкой (рис. 2.1, к) | Стальные стержни | Разгрузка через окна в барабане | Сухой |
11. Рудно-галечная бесшаровая (рис. 2.1, л) | Крупные куски измельчаемой руды | Разгрузка через цапфу | Сухой и мокрый |
12. Барабанная роликовая (рис. 2.1, м) | Массивный ролик | Периферическая разгрузка через окна (или центральная сливная) | Мокрый и сухой |
Мельница шаровая предназначена для размалывания (истирания) ТМ; каменного угля, глины, кокса, графита, формовочного песка и может быть использована для измельчения других материалов: шамота, кварца, шифера, известняка и т.д. тонкость помола достигается путём установки сит требуемой густоты
|
Шары стальные мелющие для шаровых мельниц.
По твердости шары металлические подразделяются на 4 группы:
1. Нормальной твердости общего назначения;
2. Повышенной твердости общего назначения;
3. Высокой твердости для измельчения руд черных металлов;
4. Особо высокой твердости для измельчения руд цветных металлов, цемента и огнеупоров.
Диаметр стальных помольных шаров варьируется от 15 мм до 120 мм.
Условный диаметр, мм | Номинальный диаметр, мм | Масса одного шара, кг |
15 20 25 30 40 50 60 70 80 90 100 110 120 | 15,0 20,0 25,0 31,5 41,5 52,0 62,0 73,0 83,0 94,0 104,0 114,0 125,0 | 0,014 0,033 0,064 0,128 0,294 0,58 0,98 1,60 2,35 3,41 4,62 6,09 8,03 |
Конусные дробилки
Конусные дробилки используют во всех стадиях дробления при переработке самых разнообразных материалов как по крупности дробимого материала, так и по разнообразию физико-механических свойств. В этих машинах материал разрушается в камере, образованной наружным неподвижным и внутренним подвижным усеченными конусами. По технологическому назначению их делят на дробилки: крупного дробления (ККД), обеспечивающие степень измельчения i = 5... 8; среднего (КСД) и мелкого (КМД) дробления (степень измельчения i до 20... 50). В химической промышленности, в основном, используют дробилки КСД и КМД.
Главным параметром дробилок ККД является ширина приемного отверстия – расстояние между образующими боковых поверхностей конусов в зоне загрузки. Отечественной промышленностью выпускаются дробилки типа ККД с шириной приемного отверстия 500, 900,1200 и 1500 мм. Основным параметром дробилок типов КСД и КМД является диаметр нижнего основания подвижного конуса, который может быть равен 600, 900, 1200, 1750 и 2200 мм.
По конструктивному признаку – способу опирания вала дробящего конуса – различают дробилки с подвешенным валом, опорным пестом и с консольным валом. Последнюю конструкцию используют в машинах КСД и КМД.
Рис. 3 Схема конусных дробилок
В дробилках с подвешенным валом вал 3 дробящего конуса 4 в верхней точке, совпадающей с точкой пересечения осей конусов, подвешен к опоре 5, воспринимающей осевую и радиальную нагрузки. Нижний конец вала размещен в эксцентрике 2, опоры которого также воспринимают радиальную нагрузку дробящего конуса. Вращение эксцентрика осуществляется через коническую зубчатую передачу 1. В дробилке с опорным пестом осевая нагрузка дробящего конуса с пяты вала передается на пест 6 и далее на плунжер гидроцилиндра 7, который уравновешивается давлением жидкости. За счет этого обеспечивается возможность оперативного регулирования ширины b выходной щели.
|
В дробилках с консольным валом дробящий конус имеет более пологую форму. В этих машинах осевая нагрузка воспринимается сферической пятой 8, а радиальная – опорой эксцентрика.
Производительность конусных дробилок (при сопоставимых параметрах) выше, чем у щековых. Это объясняется тем, что в щековых дробилках площадь выходного отверстия при перемещении щеки изменяется, а в конусных она постоянная и изменяется лишь положение подвижного конуса в камере дробления. Перекатывание дробящего конуса также способствует лучшему заполнению камеры дробления и захвату кусков.
Рассмотрим конструкции дробилок на примере конусной дробилки мелкого дробления КМД (рис. 2.3).
Рис.4 Дробилка КМД с консольным валом
Дробилка состоит из станины 4 с опорным кольцом 6 и предохранительными пружинами 5, эксцентрика 1, установленного в центральном стакане станины на четырехдисковомподпятнике 2. Через конические зубчатые колеса эксцентрик связан с приводным валом 16, расположенным в горизонтальном патрубке станины 4. С коническим отверстием эксцентрика 1 сопряжен конический хвостовик вала 13 дробящего конуса, опирающегося на сферический подпятник опорной чаши 3. Рабочая камера дробилки образуется наружной поверхностью дробящего конуса, футерованного броней 15 из высокомарганцовистой стали, и внутренней поверхностью неподвижной брони 14 регулирующего кольца, сопрягающегося упорной резьбой с опорным кольцом 6. Для обеспечения правильной работы резьбы под нагрузкой осевой люфт в резьбе выбирается при подтягивании регулирующего кольца колонками 12 с клиньями. Клинья опираются на кожух 7, установленный на опорном кольце 6. В верхней части дробилки имеется герметичное загрузочное устройство 9, установленное на четырех стойках 11 и станине 4. Исходный материал поступает в приемную коробку 10 загрузочного устройства и через патрубок ссыпается на распределительную плиту 8 дробящего конуса.
При вращении эксцентрика дробящему конусу сообщается гирационное движение. Благодаря качанию распределительной плиты,
обеспечивается равномерная по окружности загрузка рабочего пространства. В результате при сближении конусов материал дробится, а при их расхождении выгружается.
Характерной особенностью дробилок КСД и КМД является наличие в камере дробления параллельной зоны, т.е. участка, на котором зазор между образующими конусов постоянен. Тем самым обеспечивается получение однородного продукта, близкого по размерам к зазору.
Валковые дробилки
Для среднего и мелкого дробления материалов высокой и средней прочности, а также для измельчения пластичных и хрупких материалов применяются валковые дробилки. В этих машинах процесс измельчения осуществляется непрерывно при затягивании кусков материала в суживающееся пространство между параллельно расположенными и вращающимися навстречу друг другу валками.
Валковые дробилки бывают одно-, двух-, трех- и четырех валковые.
В зависимости от вида поверхности валков различают дробилки с гладкими, рифлеными и зубчатыми валками. Дробилки с гладкими и рифлеными валками обычно применяют для дробления материалов средней прочности; дробилки с зубчатыми валками – материалов малой прочности. Размер кусков продукта зависит как от размера выходной щели между валками, так и от типа поверхности рабочих органов.
Основными недостатками валковых дробилок являются: 1) интенсивное и неравномерное изнашивание рабочих поверхностей валков при измельчении прочных и абразивных материалов; 2) сравнительно невысокая удельная производительность.
Широкое применение валковых дробилок объясняется тем, что они наиболее приспособлены для переработки очень распространенных материалов, склонных к налипанию или содержащих липкие включения. Во время работы дробилок налипший на поверхность валков материал срезается очистными скребками.
Валковые дробилки характеризуются диаметром D и длиной L валков, при этом L/D = 0,4...1,0. Изготовляют двухвалковые дробилки ДГ с гладкими валками для среднего и мелкого, сухого и мокрого дробления материалов с пределом прочности при сжатии до 350 МПа;двухвалковые дробилки ДР с рифлеными валками для дробления материалов с пределом прочности при сжатии до 250 МПа; двухвалковые дробилки ДГР с гладкими и рифлеными валками; четырех валковые дробилки Д4Г с гладкими валками для мелкого дробления кокса. Наиболее распространена двухвалковая дробилка.
Рис.4 Двухвалковая дробилка
Машина с гладкими или рифлеными валками (рис. 2.4) состоит из станины 1 - рамной конструкции. Валок 8 - установлен на подшипниках, размещенных в разъемных корпусах 9. Корпуса 5 подшипников другого валка установлены в направляющих 4 и могут перемещаться по ним вдоль станины. Регулирование ширины выпускной щели (зазора между валками) осуществляется с помощью набора прокладок 10, которые устанавливаются между корпусами неподвижных и подвижных подшипников. Подвижный валок прижимается к неподвижному системой верхних 6 и нижних тяг с пакетом пружин 3.Предварительное натяжение пружин, создаваемое гайками 2, обеспечивает суммарное усилие на валок, обеспечивающее дробление материала. При попадании в машину недробимых предметов пружины сжимаются, валки расходятся и пропускают их. Для предотвращения пыления дробящие валки закрыты кожухом с приемной воронкой 7.
Бегуны
Для мелкого дробления (конечный размер частиц 3...8 мм) и грубого помола (0,2...0,5 мм) извести, глины и других материалов применяются бегуны. Кроме того, бегуны могут также обеспечить растирание, гомогенизацию, уплотнение и обезвоздушивание материала.
В бегунах массивные катки, перекатываясь по слою материала, находящемуся на поддоне, измельчают его раздавливанием и истиранием. Это происходит вследствие того, что широкие катки, перемещаясь по окружности небольшого радиуса, непрерывно разворачиваются относительно поддона и их внешняя сторона скользит юзом, а внутренняя буксует.
В бегунах может осуществляться как сухой, так и мокрый помол материалов. Главным параметром бегунов является диаметр D и ширинаb катков. Для мокрого помола выпускают бегуны с размерами D × b от 1200×300 до 1800× 550 мм с катками массой, соответственно 2...7 т. Для сухого помола изготавливают бегуны с D ×b от 600× 200 до 1800× 450мм.Бегуны изготавливают с неподвижным поддоном, по которому перекатываются катки, и с вращающимся поддоном.
Рис.5 Схема бегунов
Рабочими органами бегунов являются массивные катки 1 и 2 (рис.5), перемещающиеся в чаше с измельчаемым материалом. Увеличение скорости и частоты приложения разрушающих нагрузок интенсифицирует процесс помола материала благодаря усталостным явлениям. Бегуныхарактеризуются пониженными, по сравнению с барабанными мельницами,энергозатратами, меньшим износом рабочих органов и компактностью.
Рис.6 Бегуны с вращающимися валками
Бегуны мокрого помола (влажностью более 15 %) с вращающимися катками (рис. 6) имеют нижнее расположение привода. При вращении вертикального вала 1 катки 5, установленные на подшипниках на водилах 6, перекатываются по поддону 4 и одновременно вращаются вокруг собственных осей. Коленчатые водила, шарнирно закрепленные в цапфе 7,позволяют каткам подниматься или опускаться в зависимости от толщины слоя материала и преодолеватьнедробимые предметы. Катки устанавливают на разных радиусах от центра поддона, чтобы они перекрывали большую площадь. Поддон укладывают плитами, имеющими овальные отверстия размером от 6×30 до 12×40 мм. Измельченный материал продавливается сквозь отверстия в поддоне и попадает на вращающуюся тарелку 8, с которой сбрасывается скребком 3 в разгрузочный лоток 2. К валу 1 прикреплены поводки со скребками 9, которые очищают борта и поверхность чаши от налипшего материала и равномерно направляют его под катки.
Применяют также верхний привод катков, бегуны с вращающейся чашей,
бегуны с пружинным, гидравлическим или пневматическим прижимом катков. Использование последних позволяет снизить металлоемкость машины. Частота вращения вертикального вала бегунов 0,3...0,9 об/с, удельный расход энергии 0,7...4,0 кВт⋅ч/т.
Абразивное изнашивание
Изнашивание - это процесс постепенного изменения размеров деталей в результате трения во время эксплуатации. При этом обычно изменяется форма и состояние рабочих поверхностей.
Износом называется результат изнашивания.
Тепловой износ проявляется на рабочих поверхностях кулачков распределительных валов, торцов толкателей, цилиндров двигателей, зубьев шестерен и на шейках коленчатых валов двигателей.
Абразивный износ характерен наличием микропластических деформаций и срезанием метила деталей твердыми абразивными частицами (пыли, нагара, продуктов изнашивания, твердых структурных составляющих металле детали), находящимися между поверхностями трения. Интенсивность абразивного износа зависит от механических свойств материала деталей, режущих свойств абразивных частиц, удельного давления и скорости скольжения пря трении.
Абразивное изнашивание – это разрушение поверхности детали в результате его взаимодействия с твердыми частицами (абразивом). Абразивным материалом называют материал естественного или искусственного происхождения, зерна которого имеют достаточную твердость и обладают способностью резания (царапания).
Такими частицами могут быть микровыступы, твердые частицы грунта, металлическая стружка, песок, оксидная пленка, нагар, продукты износа и т.д., попавшие в зону силового контакта сопряженных поверхностей. Твердые частицы могут находиться как в закрепленном состоянии (неподвижно закрепленные твердые зерна), так и в свободном.
Абразивному изнашиванию подвержены большое количество деталей машин, работающих в абразивной среде (ходовая часть гусеничных тракторов и дорожно-строительных машин, рабочие органы сельскохозяйственных машин и металлорежущих станков, узлы бурильного оборудования нефтяной и газовой промышленности и т.д.).
Поверхность детали может быть разрушена как в результате одноактного воздействия абразива, так и многоактного процесса деформирования поверхности абразивными частицам.
а) скольжение детали по монолитному образцу;
б) качение детали по абразиву;
в) соударение с частицами абразива;
г) соударение детали с монолитным абразивом;
д) влияние потока абразивных частиц на поверхность детали;
е) скольжение детали в массе абразивных частиц;
ж) взаимодействие сопряженных деталей в контакте с абразивными частицами.
На процесс абразивного изнашивания влияют различные факторы: природа абразивных частиц, их форма и размер, агрессивность среды, свойство изнашиваемых поверхностей, ударное взаимодействие, температура и т.п.
Рис.11 Абразивный износ вала
Экспериментально установлено, что если размер частиц не превышает 5 мкм, то они, имея большую развитую поверхность, абсорбируют на себе продукты окисления масла, что может снизить интенсивность изнашивания детали. Многие исследования показывают, что частицы с размерами менее 5 мкм уменьшают износ частицы, размером более 5 мкм – увеличивают износ.
Соотношение твердости материала Нм и абразива На оказывает влияние на процесс абразивного изнашивания.
При выполнении условия Кт=Нм/На<0,5, (4.4) возможно прямое разрушение материала.
При Кт больше 0,7 происходит многоцикловое разрушение. Стойкость абразивному изнашиванию также зависит от состава и структуры поверхностных слоев.
Мел
Мел — осадочная горная порода белого цвета, мягкая и рассыпчатая, нерастворимая в воде, органического (зоогенного) происхождения. Показатель преломления 1,55.
Основу химического состава мела составляет карбонат кальция с небольшим количеством карбоната магния, но обычно присутствует и некарбонатная часть, в основном оксиды металлов. В меле обычно находится незначительная примесь мельчайших зёрен кварца и микроскопические псевдоморфозы кальцита по ископаемым морским организмам (радиолярии и др.) Нередко встречаются крупные окаменелости мелового периода: белемниты, аммониты и др.
Применение мела и его аналоги.
Мел — необходимый компонент мелованной бумаги, используемой в полиграфии для печати качественных иллюстрированных изданий. Молотый мел широко применяется в качестве дешёвого материала (пигмента) для побелки, окраски заборов, стен, бордюров, для защиты стволов деревьев от солнечных ожогов.
Мел широко применяют в лакокрасочной промышленности в качестве наполнителя. Мел не применяют в качестве пигмента в красках (белый пигмент - это как правило соединения титана, магния, цинка) по причине характерной структуры частиц мела, но применяют в резиновой, бумажной, в сахарной промышленности — для очистки свекловичного сока, для производства вяжущих веществ (известь, портландцемент), в стекольной промышленности, для производства спичек. В этих случаях обычно используют т. н. Мел осаждённый, полученный химическим путём из кальцийсодержащих минералов. Мел нашел широкое применение в качестве дисперсного наполнителя для полимерных композиций (полипропилена и полиэтилена) Мел используется для письма на больших досках для общего обозрения (например, в школах) (формованный школьный мелок на 40 % состоит из мела (карбонат кальция) и на 60 % из гипса (сульфат кальция). Следует отметить, что при рентгеновских исследованиях желудочно-кишечного тракта применяют вещество, которое иногда ошибочно принимают за мел. На самом деле это взвесь также нерастворимого в воде сульфата бария.
Гипс
Гипс — минерал из класса сульфатов, по составу гидрат сульфата кальция (CaSO4·2H2O).
Волокнистая разновидность гипса называется селенитом, а зернистая — алебастром.
Блеск стеклянный или шелковистый (у волокнистых разновидностей), спайность весьма совершенная в одном направлении (расщепляется на тонкие пластинки). Цвет белый, серый, иногда красноватый, при наличии примесей имеет серую, желтоватую, розоватую, бурую окраску. Волокнистые разности дают занозистый излом. Черта белая. Сингония моноклинная. Плотность — 2,3 г/см³, твёрдость по шкале Мооса — 2. Текстура — массивная.
Волокнистый гипс (селенит) используют для недорогих ювелирных изделий. Из алебастра издревле вытачивали крупные ювелирные изделия — предметы интерьера (вазы, столешницы, чернильницы и т. д.).
В «сыром» виде используется как удобрение и в целлюлозно-бумажной промышленности, в химической для получения красок, эмали, глазури. Обожжённый гипс применяют для отливок и слепков (барельефы, карнизы и т. д.), как вяжущий материал в строительном деле, в медицине.
Желтоватые и более плотные разновидности гипса являются хорошим поделочным материалом.
Сегодня минерал «гипс» — это в основном сырье для производства α-гипса и β-гипса. β-гипс (CaSO4·0,5H2O) — порошкообразный вяжущий материал, получаемый путём термической обработки природного двухводного гипса CaSO4·2H2O при температуре 150—180 градусов в аппаратах, сообщающихся с атмосферой. Продукт измельчения гипса β-модификации в тонкий порошок называется строительным гипсом или алебастром, при более тонком помоле получают формовочный гипс или, при использовании сырья повышенной чистоты, медицинский гипс.
При низкотемпературной (95-100 °C) тепловой обработке в герметически закрытых аппаратах образуется гипс α-модификации, продукт измельчения которого называется высокопрочным гипсом.
В смеси с водой α и β-гипс твердеет, превращаясь снова в двуводный гипс, с выделением тепла и незначительным увеличением объема (приблизительно на 1 %), однако такой вторичный гипсовый камень имеет уже равномерную мелкокристаллическую структуру, цвет различных оттенков белого (в зависимости от сырья), непрозрачный и микропористый. Эти свойства гипса находят применение в различных сферах деятельности человека.
По ГОСТ 125-79 в зависимости от сроков схватывания различаются виды гипса:
· быстротвердеющий — начало схватывания не ранее 2 мин., конец — не позднее 15 мин.;
· нормальнотвердеющий — начало схватывания не ранее 6 мин., конец — не позднее 30 мин.;
· медленнотвердеющий — начало схватывания не ранее 20 мин., конец — не нормируется.
Алебастр
Алеба́стр - название двух различных минералов: гипса (диаквасульфата кальция) и кальцита (карбонат кальция).
Эти два вида значительно отличаются друг от друга по относительной твёрдости. Гипс настолько мягок, что может быть поцарапан ногтём (твёрдость по шкале Мооса равна 2), в то время как кальцит достаточно твёрд (твёрдость по шкале Мооса равна 3), однако может быть легко поцарапан ножом. Кроме того, кальцитовый алебастр, будучи карбонатом, бурно реагирует с соляной кислотой, в то время как гипсовый алебастр в этом случае остаётся инертным.
Сегодня гипсовый камень (алебастр), это в основном сырье для производства гипса — порошкообразного вяжущего материала, получаемого путём термической обработки природного двухводного гипса CaSO4*2H2O при температуре 150—180 °C в аппаратах, сообщающихся с атмосферой, до превращения его в полуводный гипс CaSO4*0,5H2O — гипс β-модификации. Продукт измельчения гипса β-модификации в тонкий порошок до или после обработки называется строительным гипсом или алебастром, при более тонком помоле получают формовочный гипс или, при использовании сырья повышенной чистоты, медицинский гипс.
При низкотемпературной (95-100 °C) тепловой обработке в герметически закрытых аппаратах образуется гипс α-модификации, продукт измельчения которого называется высокопрочным гипсом.
В смеси с водой гипсовый порошок быстро твердеет (20…60 мин.), превращаясь снова в двуводный гипс, с выделением тепла и незначительным увеличением объёма, однако такой вторичный гипсовый камень имеет уже равномерную мелкокристаллическую структуру, цвет различных оттенков белого (в зависимости от сырья), непрозрачный и микропористый. Эти свойства гипса находят применение в различных сферах деятельности человека.
Современный строительный гипс — это порошок белого, желтоватого, розоватого или светло-серого цвета, со значительной примесью крупной фракции (песка), поступающий в розницу обычно в бумажных мешках весом до 40 кг. Применяется в строительстве как воздушное вяжущее вещество для оштукатуривания стен и потолков в зданиях с относительной влажностью не более 60 %, как основа для изготовления специальных строительных смесей (шпаклевок, штукатурок), в производстве гипсовых перегородочных панелей, листов сухой штукатурки, гипсокартона, вентиляционных коробов, арболита, гипсоволокнистых и гипсостружечных плит. При смешивании с водой строительный гипс быстро затвердевает, снова превращаясь в гипсовый камень, что используется в нетребовательных к прочности материала строительных, скульптурных и архитектурных работах, а также и в медицине, куда он нередко приходит в мешках с надписью «Медицинский». В отличие от высокопрочных гипсов, имеет укороченные сроки схватывания из-за большого содержания крупнозернистой фракции, выступающей как катализатор и повышенную адгезию к поверхностям, что ценно в строительстве, однако и меньшую прочность (обычно Г-5…Г-7]) и большую пористость. Из всех гипсов это самый низкосортный и дешёвый материал.
Практическая часть
Эксперимент №1
Во время написания дипломной работы, были проведены несколько исследовательских опытов с применением гипса и мела, которые были проделаны в лаборатории университета.
Целью первого эксперимента была проверка материала на свойство гигроскопичности.
Гигроскопичность - это свойство материалов поглощать (сорбировать) влагу из окружающего влажного воздуха. Количество влаги, поглощенной (при установившемся гидротермическом равновесии) весовой единицей материала, зависит от относительной влажности и температуры окружающей воздушной среды, а также от природы материала (химического. состава, физической. структуры, гидрофильности).
Особенности гигроскопичности отдельных строит, материалов выражаются изотермами сорбции — кривыми зависимости количества поглощенной влаги от относительной влажности воздуха при определенной темп-ре. Процессы сорбции у плотных строит, материалов протекают очень медленно; для завершения поглощения влаги до равновесного состояния требуется несколько. месяцев. Поэтому исследованиями, проводимыми на сравнительно больших образцах, помещаемых на ограниченный срок во влажную воздушную среду, нельзя установить максимальное количество поглощенной влаги - предел гигроскопичности.
Для проведения эксперимента, материал мы поместили в восемь небольших ёмкостей, в каждую из которых было помещено от 20 до 50 граммов сырья. Каждый образец был пронумерован и отмечен (по виду сырья, по весу и дате начала проведения эксперимента). Затем образцы были распределены на две равные группы по 4 ёмкости.Все ёмкости, которые мы использовали для проведения эксперимента были изготовлены из одинакового материала и имели одинаковую массу - 1.8г.
№ | условие | см3 | t0 = 22; 15.00 | Слой (мм.) | t1 = 23; 9.10 | Ʈг= 23; 16.30 | 24; 07.30 | 29; 10.30 | ||
M1' | M0;M'-1,8 | M'1 | M1 |
|
|
| ||||
1 | подвал | 20 | 25 |
| 14,4 | 25,1 | M'- M'1= | 25,1 | 25,3 | 25,4 |
2 | 29 | 29 |
| 18,3 | 29,1 | 29,2 | 29,3 | 29,5 | ||
3 | 40 | 35,9 |
| 25,9 | 36,1 | 36,1 | 36,2 | 36,5 | ||
4 | 50 | 46,3 |
| 35,8 | 46,5 | 46,5 | 46,6 | 47 | ||
5 | батарея | 20 | 19,4 |
| 14,4 | 19,3 |
| 19,2 | 19,3 | 19,3 |
6 | 30 | 27,5 |
| 19,8 | 27,4 | 27,4 | 27,4 | 27,4 | ||
7 | 40 | 38,2 |
| 25,1 | 38 | 38 | 38,1 | 38 | ||
8 | 50 | 47,4 |
| 35,2 | 47,3 | 47,3 | 47,3 | 47,2 |
Таблица. Гигроскопичность.
В первый день эксперимента (t0-22; 15.00) 22 числа в 15.00 дня, на подготовительном этапе, были проведены исходные замеры материала помещенного в емкости.
Для условий повышенной влажности (подвал):
1) масса – 25г, объем - 20см3, слой материала – 14.4мм.
2) масса – 29г, объе
|
|
Автоматическое растормаживание колес: Тормозные устройства колес предназначены для уменьшения длины пробега и улучшения маневрирования ВС при...
Эмиссия газов от очистных сооружений канализации: В последние годы внимание мирового сообщества сосредоточено на экологических проблемах...
История развития пистолетов-пулеметов: Предпосылкой для возникновения пистолетов-пулеметов послужила давняя тенденция тяготения винтовок...
Организация стока поверхностных вод: Наибольшее количество влаги на земном шаре испаряется с поверхности морей и океанов (88‰)...
© cyberpedia.su 2017-2024 - Не является автором материалов. Исключительное право сохранено за автором текста.
Если вы не хотите, чтобы данный материал был у нас на сайте, перейдите по ссылке: Нарушение авторских прав. Мы поможем в написании вашей работы!