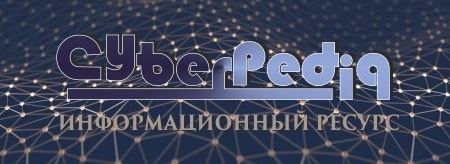
Таксономические единицы (категории) растений: Каждая система классификации состоит из определённых соподчиненных друг другу...
Наброски и зарисовки растений, плодов, цветов: Освоить конструктивное построение структуры дерева через зарисовки отдельных деревьев, группы деревьев...
Топ:
Особенности труда и отдыха в условиях низких температур: К работам при низких температурах на открытом воздухе и в не отапливаемых помещениях допускаются лица не моложе 18 лет, прошедшие...
Характеристика АТП и сварочно-жестяницкого участка: Транспорт в настоящее время является одной из важнейших отраслей народного...
Интересное:
Мероприятия для защиты от морозного пучения грунтов: Инженерная защита от морозного (криогенного) пучения грунтов необходима для легких малоэтажных зданий и других сооружений...
Уполаживание и террасирование склонов: Если глубина оврага более 5 м необходимо устройство берм. Варианты использования оврагов для градостроительных целей...
Принципы управления денежными потоками: одним из методов контроля за состоянием денежной наличности является...
Дисциплины:
![]() |
![]() |
5.00
из
|
Заказать работу |
|
|
В зависимости от назначения и принципа действия в машинах для измельчения могут использоваться различные виды нагрузок: раздавливание (сжатие куска), излом (изгиб), раскалывание (эквивалентно растяжению), истирание и удар (рис. 1.1).
Рис.1Способы механического разрушения материалов, реализуемых в дробилках и мельницах.
Как правило, перечисленные виды силовых нагрузок в процессе измельчения действуют одновременно, например, раздавливание и истирание, удар и истирание и др. Необходимость в различных видах нагрузок, а также в различных по принципу действия конструкциях и размерах машин вызвана многообразием свойств и размеров измельчаемых материалов и различными требованиями к крупности исходного материала и готового продукта. Однако при работе измельчителей в зависимости от их конструкций преобладает тот или иной способ измельчения.
Имеются практические рекомендации по использованию соответствующих видов нагрузок в зависимости от типа измельчаемого материала. Так, дробление прочных и хрупких материалов целесообразно осуществлять раздавливанием и изломом, а прочных и вязких - раздавливанием и истиранием. Крупное дробление мягких и хрупких материалов предпочтительно выполнять раскалыванием, среднее и мелкое - ударом. В промышленности дробление материалов проводят, как правило, сухим способом. Реже применяют мокрое дробление, когда в загрузочные устройства машин разбрызгивают воду для уменьшения пылеобразования.
По способу воздействия на измельчаемый материал различают дробилки, разрушающие материал сжатием (щековые, конусные и валковые дробилки) и ударом (роторные и молотковые дробилки).
В конусных дробилках разрушение материала происходит раздавливанием, изломом и истиранием при обкатывании подвижного конуса внутри неподвижного. При этом происходит периодическое сближение и отход от рабочих поверхностей конусов, в принципе, как в щековых дробилках.
|
В валковых дробилках материал измельчается в сужающемся пространстве между вращающимися навстречу друг другу валками путем раздавливания. При использовании рифленых и зубчатых валков материал измельчается также раскалыванием и изломом.
Машины для измельчения делят на дробилки и мельницы. По конструктивным признакам различают дробилки: щековые, валковые, конусные, ударного действия (роторные и молотковые). Пальцевые измельчители и бегуны занимают промежуточное положение между дробилками и мельницами, так как их можно применять как для мелкого дробления, так и для крупного помола.
Машины для дробления материала
Барабанные мельницы
Барабанные мельницы используются при производстве цемента, извести, гипса, керамических изделий и т.п. для измельчения материала до частиц размером менее десятых долей миллиметра. Процесс помола отличается большой энергоёмкостью и стоимостью.
В барабанных мельницах материал измельчается внутри полого вращающегося барабана. При вращении мелющие тела (шары, стержни) и измельчаемый материал (называемые «загрузкой») сначала движутся по круговой траектории вместе с барабаном, а затем падают по параболе. Часть загрузки, расположенная ближе к оси вращения, скатывается вниз по подстилающим слоям. Материал измельчается в результате истирания при относительном перемещении мелющих тел и частиц материала, а также вследствие удара.
В промышленности строительных материалов барабанные мельницы получили наибольшее применение.
Барабанные мельницы классифицируют по:
- режиму работы – периодического и непрерывного действия;
- способу помола – сухого и мокрого помола;
- характеру работы – мельницы, работающие по открытому и замкнутому циклу;
|
- форме мелющих тел – шаровые, стержневые и самоизмельчения (без мелющих тел);
- способу разгрузки – с механической и пневматической разгрузкой;
- конструкции загрузочного и разгрузочного устройства – с загрузкой и выгрузкой через люк, через полые цапфы и с периферийной разгрузкой;
- конструкции привода – с центральным и периферийным приводом.
Барабанные мельницы различаются между собой следующими признаками: измельчающей средой, т. е. родом применяемых измельчающих тел (шары, стержни, ролики, галька, крупные куски руды); геометрической формой барабана (короткий цилиндр, длинный цилиндр, конус); способом разгрузки материала из барабана (разгрузка периодическая или непрерывная; причем последняя может быть: через диафрагму, а затем через цапфу или непосредственно через цапфу или только через диафрагму; способом измельчения (сухой, мокрый).
Рис.2 Классификация барабанных мельниц
Классификация барабанных мельниц приведена в табл.1, которую иллюстрирует рис.2.1; Придерживаясь последовательности, принятой в табл.1 и кратко характеризуя мельницы различного типа, можно отметить следующие их особенности.
Табл.1 Классификация барабанных мельниц.
Тип мельниц | Измельчающие тела | Способ разгрузки готового продукта | Способ измельчения |
1. Шаровая периодического действия (рис. 2.1, а) | Стальные шары | Периодическая разгрузка через люк | Сухой (для лабораторных — сухой и мокрый) |
2. Шаровая с периферической разгрузкой (рис. 2.1, б ) | Стальные шары | Разгрузка через цилиндрическое сито | Сухой и мокрый |
3. Шаровая с центральной разгрузкой (рис. 2.1, в) | Стальные шары | Центральная разгрузка (непосредственно через цапфу) | Сухой и мокрый |
4. Шаровая с решеткой (рис. 2.1, г) | Стальные шары | Разгрузка через решетку, а затем через цапфу | Сухой и мокрый |
5. Шаровая с открытым концом (рис. 2.1, д) | Стальные шары | Через решетку (без цапфы) | Сухой и мокрый |
6. Трубная однокамерная (рис. 2.1, е) | Стальные шары | Центральная разгрузка (через цапфу) | Сухой и мокрый |
7. Трубная многокамерная (рис. 2.1, ж) | Стальные шары | Между камерами — разгрузка через решетку; из последней камеры — центральная разгрузка | Сухой и мокрый |
8. Коническая мельница (рис. 2.1, з) | Стальные шары | Центральнаяразгрузка | Сухой и мокрый |
9. Стержневая с центральной разгрузкой (рис. 2.1, и) | Стальные стержни (длиной, равной длине барабана) | Центральнаяразгрузка | Мокрый |
10. Стержневая с периферической разгрузкой (рис. 2.1, к) | Стальные стержни | Разгрузка через окна в барабане | Сухой |
11. Рудно-галечная бесшаровая (рис. 2.1, л) | Крупные куски измельчаемой руды | Разгрузка через цапфу | Сухой и мокрый |
12. Барабанная роликовая (рис. 2.1, м) | Массивный ролик | Периферическая разгрузка через окна (или центральная сливная) | Мокрый и сухой |
|
Мельница шаровая предназначена для размалывания (истирания) ТМ; каменного угля, глины, кокса, графита, формовочного песка и может быть использована для измельчения других материалов: шамота, кварца, шифера, известняка и т.д. тонкость помола достигается путём установки сит требуемой густоты
Шары стальные мелющие для шаровых мельниц.
По твердости шары металлические подразделяются на 4 группы:
1. Нормальной твердости общего назначения;
2. Повышенной твердости общего назначения;
3. Высокой твердости для измельчения руд черных металлов;
4. Особо высокой твердости для измельчения руд цветных металлов, цемента и огнеупоров.
Диаметр стальных помольных шаров варьируется от 15 мм до 120 мм.
Условный диаметр, мм | Номинальный диаметр, мм | Масса одного шара, кг |
15 20 25 30 40 50 60 70 80 90 100 110 120 | 15,0 20,0 25,0 31,5 41,5 52,0 62,0 73,0 83,0 94,0 104,0 114,0 125,0 | 0,014 0,033 0,064 0,128 0,294 0,58 0,98 1,60 2,35 3,41 4,62 6,09 8,03 |
Конусные дробилки
Конусные дробилки используют во всех стадиях дробления при переработке самых разнообразных материалов как по крупности дробимого материала, так и по разнообразию физико-механических свойств. В этих машинах материал разрушается в камере, образованной наружным неподвижным и внутренним подвижным усеченными конусами. По технологическому назначению их делят на дробилки: крупного дробления (ККД), обеспечивающие степень измельчения i = 5... 8; среднего (КСД) и мелкого (КМД) дробления (степень измельчения i до 20... 50). В химической промышленности, в основном, используют дробилки КСД и КМД.
Главным параметром дробилок ККД является ширина приемного отверстия – расстояние между образующими боковых поверхностей конусов в зоне загрузки. Отечественной промышленностью выпускаются дробилки типа ККД с шириной приемного отверстия 500, 900,1200 и 1500 мм. Основным параметром дробилок типов КСД и КМД является диаметр нижнего основания подвижного конуса, который может быть равен 600, 900, 1200, 1750 и 2200 мм.
|
По конструктивному признаку – способу опирания вала дробящего конуса – различают дробилки с подвешенным валом, опорным пестом и с консольным валом. Последнюю конструкцию используют в машинах КСД и КМД.
Рис. 3 Схема конусных дробилок
В дробилках с подвешенным валом вал 3 дробящего конуса 4 в верхней точке, совпадающей с точкой пересечения осей конусов, подвешен к опоре 5, воспринимающей осевую и радиальную нагрузки. Нижний конец вала размещен в эксцентрике 2, опоры которого также воспринимают радиальную нагрузку дробящего конуса. Вращение эксцентрика осуществляется через коническую зубчатую передачу 1. В дробилке с опорным пестом осевая нагрузка дробящего конуса с пяты вала передается на пест 6 и далее на плунжер гидроцилиндра 7, который уравновешивается давлением жидкости. За счет этого обеспечивается возможность оперативного регулирования ширины b выходной щели.
В дробилках с консольным валом дробящий конус имеет более пологую форму. В этих машинах осевая нагрузка воспринимается сферической пятой 8, а радиальная – опорой эксцентрика.
Производительность конусных дробилок (при сопоставимых параметрах) выше, чем у щековых. Это объясняется тем, что в щековых дробилках площадь выходного отверстия при перемещении щеки изменяется, а в конусных она постоянная и изменяется лишь положение подвижного конуса в камере дробления. Перекатывание дробящего конуса также способствует лучшему заполнению камеры дробления и захвату кусков.
Рассмотрим конструкции дробилок на примере конусной дробилки мелкого дробления КМД (рис. 2.3).
Рис.4 Дробилка КМД с консольным валом
Дробилка состоит из станины 4 с опорным кольцом 6 и предохранительными пружинами 5, эксцентрика 1, установленного в центральном стакане станины на четырехдисковомподпятнике 2. Через конические зубчатые колеса эксцентрик связан с приводным валом 16, расположенным в горизонтальном патрубке станины 4. С коническим отверстием эксцентрика 1 сопряжен конический хвостовик вала 13 дробящего конуса, опирающегося на сферический подпятник опорной чаши 3. Рабочая камера дробилки образуется наружной поверхностью дробящего конуса, футерованного броней 15 из высокомарганцовистой стали, и внутренней поверхностью неподвижной брони 14 регулирующего кольца, сопрягающегося упорной резьбой с опорным кольцом 6. Для обеспечения правильной работы резьбы под нагрузкой осевой люфт в резьбе выбирается при подтягивании регулирующего кольца колонками 12 с клиньями. Клинья опираются на кожух 7, установленный на опорном кольце 6. В верхней части дробилки имеется герметичное загрузочное устройство 9, установленное на четырех стойках 11 и станине 4. Исходный материал поступает в приемную коробку 10 загрузочного устройства и через патрубок ссыпается на распределительную плиту 8 дробящего конуса.
|
При вращении эксцентрика дробящему конусу сообщается гирационное движение. Благодаря качанию распределительной плиты,
обеспечивается равномерная по окружности загрузка рабочего пространства. В результате при сближении конусов материал дробится, а при их расхождении выгружается.
Характерной особенностью дробилок КСД и КМД является наличие в камере дробления параллельной зоны, т.е. участка, на котором зазор между образующими конусов постоянен. Тем самым обеспечивается получение однородного продукта, близкого по размерам к зазору.
Валковые дробилки
Для среднего и мелкого дробления материалов высокой и средней прочности, а также для измельчения пластичных и хрупких материалов применяются валковые дробилки. В этих машинах процесс измельчения осуществляется непрерывно при затягивании кусков материала в суживающееся пространство между параллельно расположенными и вращающимися навстречу друг другу валками.
Валковые дробилки бывают одно-, двух-, трех- и четырех валковые.
В зависимости от вида поверхности валков различают дробилки с гладкими, рифлеными и зубчатыми валками. Дробилки с гладкими и рифлеными валками обычно применяют для дробления материалов средней прочности; дробилки с зубчатыми валками – материалов малой прочности. Размер кусков продукта зависит как от размера выходной щели между валками, так и от типа поверхности рабочих органов.
Основными недостатками валковых дробилок являются: 1) интенсивное и неравномерное изнашивание рабочих поверхностей валков при измельчении прочных и абразивных материалов; 2) сравнительно невысокая удельная производительность.
Широкое применение валковых дробилок объясняется тем, что они наиболее приспособлены для переработки очень распространенных материалов, склонных к налипанию или содержащих липкие включения. Во время работы дробилок налипший на поверхность валков материал срезается очистными скребками.
Валковые дробилки характеризуются диаметром D и длиной L валков, при этом L/D = 0,4...1,0. Изготовляют двухвалковые дробилки ДГ с гладкими валками для среднего и мелкого, сухого и мокрого дробления материалов с пределом прочности при сжатии до 350 МПа;двухвалковые дробилки ДР с рифлеными валками для дробления материалов с пределом прочности при сжатии до 250 МПа; двухвалковые дробилки ДГР с гладкими и рифлеными валками; четырех валковые дробилки Д4Г с гладкими валками для мелкого дробления кокса. Наиболее распространена двухвалковая дробилка.
Рис.4 Двухвалковая дробилка
Машина с гладкими или рифлеными валками (рис. 2.4) состоит из станины 1 - рамной конструкции. Валок 8 - установлен на подшипниках, размещенных в разъемных корпусах 9. Корпуса 5 подшипников другого валка установлены в направляющих 4 и могут перемещаться по ним вдоль станины. Регулирование ширины выпускной щели (зазора между валками) осуществляется с помощью набора прокладок 10, которые устанавливаются между корпусами неподвижных и подвижных подшипников. Подвижный валок прижимается к неподвижному системой верхних 6 и нижних тяг с пакетом пружин 3.Предварительное натяжение пружин, создаваемое гайками 2, обеспечивает суммарное усилие на валок, обеспечивающее дробление материала. При попадании в машину недробимых предметов пружины сжимаются, валки расходятся и пропускают их. Для предотвращения пыления дробящие валки закрыты кожухом с приемной воронкой 7.
Бегуны
Для мелкого дробления (конечный размер частиц 3...8 мм) и грубого помола (0,2...0,5 мм) извести, глины и других материалов применяются бегуны. Кроме того, бегуны могут также обеспечить растирание, гомогенизацию, уплотнение и обезвоздушивание материала.
В бегунах массивные катки, перекатываясь по слою материала, находящемуся на поддоне, измельчают его раздавливанием и истиранием. Это происходит вследствие того, что широкие катки, перемещаясь по окружности небольшого радиуса, непрерывно разворачиваются относительно поддона и их внешняя сторона скользит юзом, а внутренняя буксует.
В бегунах может осуществляться как сухой, так и мокрый помол материалов. Главным параметром бегунов является диаметр D и ширинаb катков. Для мокрого помола выпускают бегуны с размерами D × b от 1200×300 до 1800× 550 мм с катками массой, соответственно 2...7 т. Для сухого помола изготавливают бегуны с D ×b от 600× 200 до 1800× 450мм.Бегуны изготавливают с неподвижным поддоном, по которому перекатываются катки, и с вращающимся поддоном.
Рис.5 Схема бегунов
Рабочими органами бегунов являются массивные катки 1 и 2 (рис.5), перемещающиеся в чаше с измельчаемым материалом. Увеличение скорости и частоты приложения разрушающих нагрузок интенсифицирует процесс помола материала благодаря усталостным явлениям. Бегуныхарактеризуются пониженными, по сравнению с барабанными мельницами,энергозатратами, меньшим износом рабочих органов и компактностью.
Рис.6 Бегуны с вращающимися валками
Бегуны мокрого помола (влажностью более 15 %) с вращающимися катками (рис. 6) имеют нижнее расположение привода. При вращении вертикального вала 1 катки 5, установленные на подшипниках на водилах 6, перекатываются по поддону 4 и одновременно вращаются вокруг собственных осей. Коленчатые водила, шарнирно закрепленные в цапфе 7,позволяют каткам подниматься или опускаться в зависимости от толщины слоя материала и преодолеватьнедробимые предметы. Катки устанавливают на разных радиусах от центра поддона, чтобы они перекрывали большую площадь. Поддон укладывают плитами, имеющими овальные отверстия размером от 6×30 до 12×40 мм. Измельченный материал продавливается сквозь отверстия в поддоне и попадает на вращающуюся тарелку 8, с которой сбрасывается скребком 3 в разгрузочный лоток 2. К валу 1 прикреплены поводки со скребками 9, которые очищают борта и поверхность чаши от налипшего материала и равномерно направляют его под катки.
Применяют также верхний привод катков, бегуны с вращающейся чашей,
бегуны с пружинным, гидравлическим или пневматическим прижимом катков. Использование последних позволяет снизить металлоемкость машины. Частота вращения вертикального вала бегунов 0,3...0,9 об/с, удельный расход энергии 0,7...4,0 кВт⋅ч/т.
|
|
Организация стока поверхностных вод: Наибольшее количество влаги на земном шаре испаряется с поверхности морей и океанов (88‰)...
Автоматическое растормаживание колес: Тормозные устройства колес предназначены для уменьшения длины пробега и улучшения маневрирования ВС при...
Общие условия выбора системы дренажа: Система дренажа выбирается в зависимости от характера защищаемого...
Таксономические единицы (категории) растений: Каждая система классификации состоит из определённых соподчиненных друг другу...
© cyberpedia.su 2017-2024 - Не является автором материалов. Исключительное право сохранено за автором текста.
Если вы не хотите, чтобы данный материал был у нас на сайте, перейдите по ссылке: Нарушение авторских прав. Мы поможем в написании вашей работы!