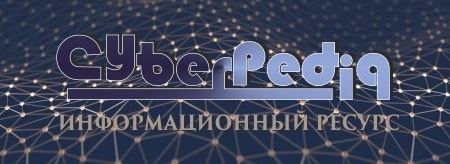
Опора деревянной одностоечной и способы укрепление угловых опор: Опоры ВЛ - конструкции, предназначенные для поддерживания проводов на необходимой высоте над землей, водой...
Типы сооружений для обработки осадков: Септиками называются сооружения, в которых одновременно происходят осветление сточной жидкости...
Топ:
Методика измерений сопротивления растеканию тока анодного заземления: Анодный заземлитель (анод) – проводник, погруженный в электролитическую среду (грунт, раствор электролита) и подключенный к положительному...
Марксистская теория происхождения государства: По мнению Маркса и Энгельса, в основе развития общества, происходящих в нем изменений лежит...
Особенности труда и отдыха в условиях низких температур: К работам при низких температурах на открытом воздухе и в не отапливаемых помещениях допускаются лица не моложе 18 лет, прошедшие...
Интересное:
Как мы говорим и как мы слушаем: общение можно сравнить с огромным зонтиком, под которым скрыто все...
Финансовый рынок и его значение в управлении денежными потоками на современном этапе: любому предприятию для расширения производства и увеличения прибыли нужны...
Что нужно делать при лейкемии: Прежде всего, необходимо выяснить, не страдаете ли вы каким-либо душевным недугом...
Дисциплины:
![]() |
![]() |
5.00
из
|
Заказать работу |
|
|
Назначение технологической оснастки и её особенности в зависимости от серийности производства. Классификация ТО - приспособлений.
Приспособление - это вспомогательное устройство, используемое при механической обработке, сборке и контроле изделий, обеспечивающее нужное взаимное расположение обрабатываемой детали, оборудования и инструмента в процессе обработки, сборки и контроля.
Вспомогательный инструмент – это устройство для базирования и закрепления режущего и иного инструмента.
Классификация технологического оборудования:
1. По целевому назначению:
a. станочные приспособления (токарные, фрезерные, шлифовальные и т.д.);
b. вспомогательный инструмент (патроны, оправки, резцовые державки);
c. сборочные приспособления (для соединений деталей в изделии(для запрессовки, склеивания, спайки, гибки…);
d. испытательная оснастка (для проведения гидравлических, тепловых и прочих испытаний);
e. контрольные приспособления(для определения погрешностей);
f. транспортные (траверсы, тара, ящики)
2. По степени специализации:
1) Универсальные – применяются в единичном и мелкосерийном производстве.
a. стандартные (тиски, патроны, поворотные столы, планшайбы);
b. безналадочные (кулачковые патроны);
c. наладочные (делительные головки, поворотные столы);
d. специальные (для деталей определенного типа, но разных размеров (2 кулачковые патроны с призматическими губками))
2) Переналаживаемые – в мелко и среднесерийном пр-ве (малая жесткость, неоптимальная конструкция).
a. универсально-сборные (УСП)
b. сборно-разборные (СРП)
c. универсально-наладочные приспособления (УНП)
3) Специальные – предназначены для выполнения только одной операции на детали.
|
a. одноместные;
b. многоместные;
c. однопозиционные;
d. многопозиционные;
e. групповые (переналаживаемые)
f. многооперационные (спутники).
Специальные пр. обладают следующими достоинствами:
- точное соответствие детали
- наибольшая точность установки детали;
- наибольшая жёсткость;
- наибольшее быстродействие и качество закрепления
Их недостатки:
- дороги и неуниверсальны;
- занимают много места в цехе;
- увеличивают продолжительность ТПП (технологической подготовки производства)
3. По степени автоматизации и механизации:
1. ручные;
2. механизированные;
3. полуавтоматические;
4. автоматические;
5. с управлением от внешних устройств.
Основные узлы приспособлений.
1. Корпуса – предназначены для удерживания в определённом положении остальных узлов приспособления.
2. Установочные элементы – опоры, пластины, призмы, цилиндрические отверстия, оправки, сложные поверхности (резьбовые, шлицевые, конусные и пр.) – те, на которые устанавливается деталь, для придания детали нужного положения в пространстве
3. Зажимные устройства – обеспечивают силовое и геометрическое замыкание при базировании детали в приспособлении
-клиновые, эксцентриковые, резьбовые;
-рычажные (пружины, прихваты);
-упругие (пружины, воздух, жидкость и т.д.)
4. Приводы – устройства, создающие зажимное усилие, вместе с управляющей аппаратурой.
Установочные элементы и их назначение. Условные обозначения опор и установочных устройств по ГОСТ3.1107-81. Материалы применяемые для изготовления опор, твердость и шероховатость их рабочих поверхностей.
Основные опоры – служат для наложения на деталь основных (не более 6) связей.
Конструкции основных опор (установочных пальцев).
При D>16 мм, опоры изготовляют из стали 20,20Х, h=0,8-1,2 (величина цементации), 65-60 HRC
При D≤16 мм, У7А, У8А до 60-65 HRC
Шероховатость поверхности не грубее чем устанавливаемой пов-ти обычно Ra 1,25 0,63 0,32
|
1. Опорные пластины - Применяются для того, чтобы деталь лежала ровно.
1.
2.
Плавающие опоры.
Применяются в тех случаях когда обрабатываемые детали имеют невысокую жёсткость или малую контактную прочность базовой поверхности детали.
Дополнительные опоры.
Устанавливаются в тех местах, где обрабатываемая деталь подвергается чрезмерной деформации под действием сил резания. Каждая дополнительная опора подводится к обрабатываемой детали и закрепляется индивидуально, после того как деталь будет установлена на основные опоры и закреплена основными зажимными устройствами.
Применяется 3 вида дополнительных опор: 1. Самоустанавливающиеся 2. Подводимые (подводятся к поверхности обрабатываемой детали вручную) 3.Регулируемые.
1.
2.
3.
Центра
Люнеты
Также существует различный вид привода
Опорные пластины.
Опорные пластины бывают двух исполнений: плоские и с косыми пазами. Пластины крепятся двумя или тремя винтами к корпусу приспособления или плите. Плоские пластины целесообразно закреплять на вертикальных стенках корпуса, т.к. при горизонтальном их положении в углублениях под головками винтов скапливается мелкая стружка, которую трудно удалить. Пластины с косыми пазами устанавливают на горизонтальных поверхностях корпуса. В этом случае стружка при движении устанавливаемой детали попадает в углубления (косые пазы) и не нарушает контакта при установке.
Применяются для того, чтобы деталь лежала ровно.
1.
2.
Плавающие опоры.
Применяются в тех случаях когда обрабатываемые детали имеют невысокую жёсткость или малую контактную прочность базовой поверхности детали.
Дополнительные опоры.
Устанавливаются в тех местах, где обрабатываемая деталь подвергается чрезмерной деформации под действием сил резания. Каждая дополнительная опора подводится к обрабатываемой детали и закрепляется индивидуально, после того как деталь будет установлена на основные опоры и закреплена основными зажимными устройствами.
Применяется 3 вида дополнительных опор: 1. Самоустанавливающиеся 2. Подводимые (подводятся к поверхности обрабатываемой детали вручную) 3.Регулируемые.
1.
2.
3.
При базировании деталей по торцу и отверстию в зависимости от условий обработки возможны 2 случая:
|
- основной базирующей поверхностью является отверстие;
- основной базирующей поверхностью является торец
Установка детали на оправку
Для обеспечения мин биения оправки эту поверхность обрабатывают после установки оправки на станок (обтачивают, шлифуют)
Определение силы зажима.
Сила зажима находится в результате решения уравнения равновесия обрабатываемой детали под действием всех приложенных к ней сил и моментов.
Для этого необходимо знать:
- величины, направления и точки приложения сил резания и крутящих моментов резания;
- величины сил инерции, возникающих при обработке (вращении детали при токарной обработке), точку приложения и направление силы зажима.
Поскольку на надежность закрепления детали влияет много факторов, связанных с состоянием инструмента, с материалом детали, способом закрепления и тд, то силы и момент резания при расчете сил зажима корректируются коэф надежности закрепления-К
W=PK; K=K0 K1 K2... K5
Типовые случаи расчета сил зажима:
1. Направление действия сил зажима с силами резания. Wmin = Р
2. Сила резания и сила зажима приложены в разных направлениях. W = (2…2.5) P
3. Сила зажима перпендикулярна силе резания.
f1 и f2 – коэффициенты трения, k – коэффициент запаса
k × P = f1 × W + f2 × W
W = kp / (f1 + f2)
При f1 = f2 = 0,1 (сталь о сталь) W = 5 × k × P
4. Закрепление в трёхкулачковом патроне. Действие двух силовых факторов – крутящего момента и осевой силы. В данном случае сила зажима – сила, действующая со стороны одного кулачка на деталь. От осевого смещения деталь удерживают силы трения, как и от поворота.
М: ;
X: ;
5. Обработка отверстия на сверлильном станке.
k × M = W × f × R
W = k × M / f × R
6. Сверление нескольких отверстий с помощью многошпиндельной сверлильной головки, наиболее часто это используется при обработке корпусных деталей, деталей типа фланцев.
Особенности конструкции и эксплуатации винтовых и клиновых зажимов. Примеры их использования в приспособлениях. Величина усилия зажатия, создаваемая данными механизмами.
|
Винтовые механизмы.
Применяют в приспособлениях с ручным закреплением заготовок, в приспособлениях механизированного типа, а также в автоматических приспособлениях. Они просты, компактны и надежны в работе.
Винтовые зажимы – самые используемые. К их особенностям следует отнести: большие зажимные усилия при малых исходных; универсальность – для закрепления самых разнообразных деталей; самоторможение – исходное усилие действует только в момент закрепления. К недостаткам следует отнести малую производительность, износ. Применяются в основном в единичном и мелкосерийном производстве. Коэффициент запаса К должен быть больше 2,5.
На показан пример закрепления винтовым зажимом:
Пути повышения производительности:
1. Быстросменные шайбы
2. Применение специальный винтовых гаек
3. Применение откидных шайб
Номинальный диаметр винта в мм определяется из соотношения:
где С= 1,4 коэффициент для метрической резьбы;
Q – сила закрепления заготовки, Н;
s - допустимое напряжение растяжения (сжатия) (для винтов из стали 45 - s = 80 – 100 МПа).
Диаметр округляется до ближайшего большего значения. В приспособлениях применяют резьбы от М8 до М42.
Расчётные формулы:
здесь: rср- средний радиус резьбы (по ГОСТ)
α – угол подъёма резьбы
L – длина рукоятки
f – коэффициент трения
b - угол профиля
j=6…16°
Тогда исходное усилие зажима:
для приближённых вычислений можно использовать формулу:
На рисунке показан пример зажима детали гайкой.
Расчётные формулы:
В этом случае доля крутящего момента, развиваемого гаечным ключом, идущая на создание зажима, будет меньше из-за существования трения на поверхности гайки.
для приближённых вычислений можно использовать формулу (для резьб М8-М48):
Клиновые механизмы.
Тело под действием силы Q перемещается по плоскости. Возникает нормальная реакция N и сила трения F, отклоняющая реакцию опоры от нормального направления на угол j. Этот угол называется углом трения. Из рис. видно, что:
Коэффициент трения скольжения f равен:
.
В силовых механизмах клин может работать с трением на двух поверхностях (наклонной поверхности и основании клина) или с трением только по наклонной поверхности (например, в цанговых патронах). На рис.___ показана схема действующих на зажатый односкосый клин с трением по двум поверхностям.
Здесь: N – нормальная сила на наклонной плоскости;
F – сила трения на наклонной плоскости;
W1 – нормальная реакция основания;
F1 – сила трения на основании клина.
Конструктивно клиновые механизмы выполняются:
1) с односкосым клином без роликов и с роликами. Они применяются в качестве усилителей пневмо- и гидроприводов.
|
2) многоклиновые самоцентрирующие механизмы, которые используются в конструкциях патронов и оправок.
Определение силы зажима W.
а) для механизма с трением на обеих поверхностях клина сила зажима W будет зависеть от известной силы привода Q:
б) для механизма с трением только на наклонной плоскости, когда :
в) для клина с двумя роликами. В этом случае трение скольжение заменяется тренем качения:
г) для клина с роликами только по наклонной плоскости:
Пневматические приводы
Применяются в массовом и крупносерийном производствах. Реже используются в мелко и среднесерийном. Для работы в пневмоприводах используют сжатый воздух Р = 4 – 6 кГ/см2 (0,4 – 0,6 МПа). Он должен быть очищен от влаги, механических примесей и кислот.
Преимущества пневмоприводов: простота конструкции и эксплуатации, большой диапазон развиваемых усилий, высокое быстродействие (Vвозд = 180м/с), дешевизна, экологическая чистота.
К недостаткам можно отнести: неплавное действие; т.к. давление сжатого воздуха невелико, то габариты пневмоцилиндра могут быть большими (диаметр поршня 2…320мм); малое давление воздуха в магистрали; при давлении р > 0,6 МПа наблюдается конденсация и замерзание влаги в магистралях (для устранения применять величину давления не больше 0,4 МПа); необходимость тщательной обработки внутренней поверхности пневмоцилиндра (у Перевозщикова: H7/h7; Польский – H9/f9; Ra не грубее 0,4); необходимость смазки пневмоаппаратуры (распыление масла в потоке воздуха специальными масленками); невысокий КПД (0,8)
Состоят пневмоприводы из пневмодвигателя, пневматической аппаратуры и пневмосети, представляющей собой трубы, рукава, каналы и соединения.
Пример пневмоцилиндра одностороннего действия
1-кран, 2-корпус, 3-поршень, 4-пружина, 5-шток
Для нормальной работы пневмоцилиндров требуется герметичность и изоляция друг от друга его полостей. Для этого применяются уплотнения., которые соединяют между собой поршень и цилиндр, шток и крышку и неподвижные соединения (крышка и цилиндр).
Основные требования к уплотнениям:
1) Герметичность при всех рабочих режимах;
2) Высокая износостойкость и минимальные потери на трение (в пределах 150 000 ходов поршня).
3) Надежность работы при высоких и низких температурах и способность не разрушаться в результате химического взаимодействия с уплотняемой средой.
4) Удобство монтажа, демонтажа и отсутствие необходимости подтяжки и регулировки при эксплуатации.
5) Экономичность.
В современных конструкциях пневмодвигателей применяются 2 типа уплотнений:
1. Манжеты V-образного сечения из маслостойкой резины для уплотнения поршней и штоков.
2. Кольца Круглого сечения из маслостойкой резины по ГОСТ 9833-73 для уплотнения поршней, штоков и неподвижных соединений.
При сборке манжеты устанавливаются с натягом, т.е. D1 - наружный диаметр манжеты больше Dц – наружного диаметра цилиндра. При поступлении в цилиндр рабочей среды (сжатого воздуха или масла) она как клин распирает лепестки манжеты и автоматически уплотняет сопряжение движущихся частей.
Кольца круглого сечения также уплотняются автоматически. Они закладываются в прямоугольные канавки, высота которых меньше диаметра d сечения кольца, а ширина b – больше, что необходимо для нормальной работы кольца.
Кольца устанавливаются в канавку с натягом, обеспечивающим предварительное уплотнение. С поступлением в цилиндр рабочей среды кольцо перемещается к стенке канавки (в направлении потока воздуха или масла) и деформируясь принимает D-образную форму. Степень уплотнения возрастает с увеличением давления рабочей среды.
В двигателях двухстороннего действия на поршне требуется две V-образные манжеты, а кольцо круглого сечения – одно, т.к. последнее обеспечивает уплотнение в обе стороны.
При уплотнении Vобразными манжетами требуются: посадка в сопряжении поршня с цилиндром: или
, шероховатость обработки зеркала цилиндра Ra = 0.32 – 0.63 мкм, смазка умеренная.
При уплотнении кольцами требуется посадка или
, зеркало цилиндра следует обрабатывать по Ra = 0.16 – 0.08 мкм, смазка обильная.
Электромеханический привод
Преимущества
-самоторможение, т.е. можно отключить после закрепления детали
-простота подключения и управления
-не загрязняет рабочее пространство
-высокий КПД
-легко передать энергию на вращающееся устройство.
Недостатки: малая распространенность привода обусловлена:
-быстрым износом
-малым развиваемым усилием
-сложностью устройства
-необходимостью ограничения зажимного усилия и длины рабочего хода
-наличием разгонной муфты
Магнитный привод
Выпускается в двух исполнениях – в виде магнитных плит и магнитных (в лекциях планшайб) патронов. По способу создания магнитного поля различают:
- электромагнитные;
- магнитные (с постоянным магнитом).
Преимущества:
- отсутствие движущихся частей;
- долговечность;
- развивает достаточно высокие усилия зажима, порядка 35…50 Н/см2
Электромагнитные устройства создают большие усилия, чем устройства с постоянными магнитами, но при отключении питания закрепленные детали раскрепляются. Устройства с постоянными магнитами этого недостатка лишены, но для включения/выключения необходим дополнительный привод (механический, пневматический). Применяются, в основном, на плоскошлифовальном оборудовании.
Вакуумный привод
W=F(Pатм-Рост)
Рат=0,1МПа
Применяются для закрепления деталей, которые могут быть повреждены от действия сосредоточенных усилий. Вакуумные насосы чувствительны к нечистому воздуху.
Передаточные механизмы.
Передаточные механизмы нужны для:
-увеличения усилия
-изменения перемещения
-увеличения силы зажима
-изменения направления силы
Винторычажный зажим
Примеры других передаточных механизмов в Горошкине стр. 191-211
Призматические механизмы.
Действуют от винта с правой и левой резьбой. Упор служит для регулирования положения ползуна на винте.
Деталь закрепляется тремя плунжерами, расположенными через 120°, которые перемещаются в пазах ползушки. кольцевая пружина круглого сечения прижимает плунжеры к пазам. Для коротких деталей используют один ряд плунжеров, для длинных – 2 ряда.
2. Плунжерные
Цанговые (см вопрос 9)
Мембранные.
Используются для точной центровки и закрепления деталей типа втулок и колец.
Бывают: - специальные;
- переналаживаемые.
Они состоят из круглой привернутой к планшайбе станка пластины (мембраны) 1 с симметрично расположенными выступами-кулачками 2 (6 – 12 шт.). Внутри шпинделя проходит шток 3 пневмоцилиндра. Включая пневматическое устройство прогибают пластину и тем самым раздвигают кулачки. При отходе штока назад пластина, стремясь вернуться в исходное положение, сжимает своими кулачками заготовку 4. Материал мембраны – стали 65Г, 30ХГС или У7А, закаленные до твердости HRC 40…45. Точность центрирования 0,003 – 0,005 мм.
Кулачковые патроны.
А. Двухкулачковые.
Используются для закрепления несимметричных заготовок или фасонных деталей и обычно являются самоцентрирущими. Могут быть с ручным (ключевым) или механизированным приводом. Пневматические патроны бывают двух видов:
1) реечные;
2) клинорычажные.
Б. Трехкулачковые.
Наиболее распространены клиновые (ГОСТ16886-71) и рычажно-клиновые (ГОСТ 16862-71) патроны с механизированным приводом. В крупносерийном производстве используются рычажные патроны с пневмоприводом.
В мелкосерийном, единичном и серийном производстве применяются патроны с ручным (ключевым) приводом спирально реечные с плоской архимедовой спиралью и конической зубчатой передачей к спиральному диску.
Рычажные зажимы.
Отодвигаемый зажим.
2) Самоустанавливающиеся опоры. Представляют собой постоянную опору, разложенную на 2 или 3 точки. Нагрузка, приходящаяся на каждую точку, суммируется в центре, давая здесь равнодействующую, воспринимаемую корпусом приспособления.
Примером конструкции самоустанавливающейся опоры является опора по ГОСТ 13159-67.
Головка плунжера 1 при освобожденном винте 3 под действием пружины выступает несколько над тремя основными опорами при установке детали. Она силой своего веса опускает плунжер и устанавливается на основные опоры. После закрепления детали плунжер стопорится винтом 3, превращаясь в основную опору. Сила пружины должна быть такой, чтобы установленная на три основные опоры, но не закрепленная деталь не приподнималась плунжерами. Угол скоса a должен быть самотормозящим (6 - 10°), т.к. в противном случае при стопорении он может подниматься вверх и приподнимать деталь с основных опор.
Перед установкой каждой новой детали плунжер необходимо освобождать, иначе деталь может либо не коснуться основных опор, либо головки плунжера. Гайка 4 служит для предотвращения от попадания стружки.
3)Вспомогательные опоры то же бывают самоустанавливающиеся.
4)Дополнительные опоры выполняют то же самоустанавливающимися. При установке заготовки опоры индивидуально самоустанавливаются к поверхности заготовки, а затем стопорятся, превращаясь на время выполнения данной операции в жесткие опоры.
Условные обозначения:
Делительные устройства. Их назначение и конструктивные особенности в зависимости от назначения. Схемы делительных устройств. Материалы основных деталей делительных устройств, их твёрдость, точность изготовления рабочих поверхностей.
Предназначены для поворота на заданный угол, обрабатываемой детали, закрепленной в приспособлении.
В каждом делительном устройстве есть 2 характерные части:
- делительный диск;
- фиксатор.
Бывают универсальные и специальные.
По конструктивным схемам делятся на осевые и радиальные.
Эти устройства являются наиболее ответственными в делительных приспособлениях, от них зависит точность деления при позиционной обработке.
Фиксаторы представляют собой стержни различной формы, которые монтируются на неподвижной части приспособления – корпусе. Перед началом обработки стержень заводится в одно из отверстий в подвижной (поворотной) части и жестко фиксирует ее относительно корпуса.
Управление фиксатором осуществляется вручную или автоматически.
Фиксаторы выполняются с цилиндрической, конической и призматической частью. Фиксаторы и базовые поверхности делительных приспособлений обрабатываются по 5…6 квалитету. Материал фиксаторов и втулок: стали с высокой износостойкостью 60HRC. Диски диаметром до 150 мм изготавливают цельные из сталей У8А, У10А (закалка, шлифовка). Диски диаметром более 150 мм изготавливают из конструкционных сталей.
Радиальная схема.
Свойства:
- малые осевые габариты, но большие радиальные;
- повышенная точность деления;
- низкая технологичность, технологически сложнее осевой схемы.
Осевая схема.
Свойства:
- малые радиальные и большие осевые габариты;
- точность деления меньше, чем радиальной схемы;
- высокая технологичность;
Требования к точности по ГОСТ 22129:
1) допуск перпендикулярности оси фиксатора к рабочей поверхности диска 0,01 мм;
2) допуск скрещивания оси фиксатора и оси вращения диска 0,01 мм;
3) допуск соосности центрирующего и базового отверстия 0,01 мм.
Способы повышения точности делительных устройств:
1)Повышение точности изготовления отдельных элементов делительного устройства, особенно делительного диска
2)Увеличение диаметра делительного диска
3)Замена цилиндрического фиксатора коническим
4)Уменьшение диаметра фиксатора
5)Фиксаторы не должны воспринимать внешних усилий, следовательно после совершения деления поворотная часть должна быть зафиксирована.
Элементы для ориентации и установки приспособления на столе металлорежу-щего станка. Особенности их конструкции в зависимости от назначения (показать на эскизах). Материалы, применяемые для изготовления рассматриваемых элементов, их твёрдость, точность изготовления.
Конфигурации и размеры основной базы корпуса обусловлены необходимостью обеспечить возможно большую устойчивость приспособления на станке и установку его на станок без выверки. Для установки приспособления на станок без выверки конфигурация и размеры основной базы корпуса должны быть выполнены в соответствии с посадочными местами станков.
На фрезерных станках установка приспособлений осуществляется с помощью шпонок, которые устанавливаются в Т-образный паз.
Шпонки лишают приспособление 5 степеней свободы. Они изготавливаются из сталей У7А, У8А. Установочные поверхности шпонки изготавливаются по 7 квалитету.
На сверлильных станках и станках с ЧПУ приспособления устанавливаются на пальцы или штифты.
Вспомогательный инструмент и его назначение. Виды вспомогательного инструмента в зависимости от типа станка и их конструктивные особенности. Пример конструкции вспомогательного инструмента для любого типа станка.
Вспомогательный инструмент – устройство для базирования и закрепления режущего и иного инструмента.
Требования к вспомогательному инструменту:
1. простота конструкции и дешевизна,
2. высокая прочность, жесткость, надежность закрепления,
3. высокая точность настройки инструмента на заданный размер,
4. возможность компенсации износа инструмента,
5. отсутствие вибраций и их гашение,
6. универсальность.
Основные виды вспомогательного инструмента:
1. резцедержатели для призматических и круглых резцов (токарные, токарно-револьвер-ные станки),
2. борштанги для расточных и токарных станков,
3. оправки для крепления насадного инструмента (фрезерные станки),
4. патроны для закрепления концевого, осевого инструмента (плавающие патроны для крепления развёрток, метчиков; патроны для крепления фрез, развёрток)
5. Переходные втулки для закрепления инструмента в конических расточках шпинделя и в патронах. Бывают цилиндрические, конические разрезные.
6. Регулируемые расточные резцовые державки.
7. Резцовые головки для обработки плоских поверхностей.
Для грубой и предварительной настройки режущего инструмента на заданный размер в конструкции вспомогательного инструмента предусматривают направляющие.
Для тонкой настройки и компенсации износа целесообразно применять упруго-деформи-руемый вспомогательный инструмент.
Контрольные приспособления и их назначение. Требования, предъявляемые к КП. Методика расчёта на точность КП. Пример схемы к расчёту на точность КП контроля биения шейки вала, установленного в центрах и составляющие погрешности приспособления.
Контрольные приспособления применяют для проверки заготовок деталей и узлов машин в тех случаях, когда эта проверка не может быть произведена с помощью универсального измерительного инструмента и калибров с достаточной точностью, либо совсем не возможна в условиях поточного автоматизированного производства.
Требования предъявляемые к КП:
Корпуса выполняются с большей точностью, но испытывают меньшие нагрузки. Для снижения износа установочные поверхности выполняют очень высокой твёрдости, нередко из твёрдых сплавов, или выполняют в виде роликов (заменяют трение скольжения трением качения).
Для контрольных приспособлений погрешности измерения не должны превышать 8% от поля допуска для контроля ответственных изделий, 15-20% для менее ответственных и 30% поля допуска для неответственных изделий.
К элементам контрольного приспособления относятся: корпусные, установочные, зажимные, измерительные, вспомогательные устройства.
При проектировании контрольных приспособлений следует стремиться к совмещению измерительных и установочных баз. Погрешность базирования не должна превышать 10-15% поля допуска на проверяемый размер для неответственной продукции.
Для повышения производительности контроля применяются многомерные контрольные приспособления, в которых производится одновременно проверка нескольких размеров.
Для использования многомерных приспособлений необходимо:
1) простановка проверяемых размеров от одной измерительной базы;
2) совмещение этой базы с удобной установочной базой детали;
3) возможность пересчёта допусков на проверяемые размеры с учётом специфики многомерного контроля.
Зажимные устройства в контрольных приспособлениях предупреждают смещение детали относительно измерительного устройства, обеспечивают плотный контакт установочных баз с опорами приспособления. Зажимные устройства должны развивать небольшие, но стабильные усилия, должны быть быстродействующими.
Вся методика расчёта КП на точность сводится к определению приведённой погрешности приспособления по формуле:
где, - погрешность взаимного расположения элементов контрольного приспособления (поверхностей, линий);
- коэффициент отклонения распределения данной погрешности от нормального распределения;
-коэффициент влияния данной составляющей на суммарную погрешность (передаточное отношение).
На рисунке пример схемы к расчёту на точность КП контроля биения шейки вала, установленного в центрах и составляющие погрешности приспособления.
-погрешность индикатора;
-погрешность центровых отверстий;
-погрешность зазора.
Узлы контрольных приспособлений. Требования к ним. Особенности конструиро-вания.
1. Корпуса
2. Установочные элементы
3. Зажимные элементы
4. Измерительные элементы
5. Вспомогательные элементы
Корпуса выполняются с большой точностью, но испытывают меньшие нагрузки, для уменьшения износа рабочей установочной поверхности выполняются очень высокой твердости, или применяют ролики для замены трения скольжения на трение качения.
Следует стремиться к совпадению измерительных и установочных баз. Материал корпуса должен обладать высокой жёсткостью, временной стабильностью формы.
Опоры должны обладать высокой износостойкостью.
Зажимные устройства в контрольных приспособлениях предупреждают смещение деталь относительно измерительных устройств, обеспечивают плотный контакт установочных баз детали с опорой приспособления. Зажимные устр-ва контр. приспособлений должны развивать небольшие, но стабильные усилия, должны быть быстродействующими.
Измерит. устр-ва контр. приспособлений делятся на
1. предельные (бесшкальные)
2. отсчетные (шкальные)
3. работающие по принципу нормальных калибров.
Предельные устройства не дают численных значений измеряемых величин, но позволяют поделить изделия на 3 группы (годные и 2 вида брака). В качестве таких устройств применяются выдвижные скобы, щупы, пробки, которые часто устанавливают на корпусе контрольного приспособления, а проверяемую деталь передвигают от одного устройства к другому.
Электроконтактные датчики применяются в сочетании с устройствами сортировки или индикации (точность порядка 1 мкм).
Приспособления с отсчетными изм. устр-ми применяются при обычном и статистическом контроле (индикаторы, измерительные головки, миниметры, микрокаторы, оптикаторы, пневматические микрометры).
Пневматические микрометры позволяют производить измерения с точностью 0,5…0,2 мкм. Т.к. у них отсутствует прямой контакт с деталью, они очень долговечны.
В качестве устр-в работающих по принципу
|
|
Адаптации растений и животных к жизни в горах: Большое значение для жизни организмов в горах имеют степень расчленения, крутизна и экспозиционные различия склонов...
Двойное оплодотворение у цветковых растений: Оплодотворение - это процесс слияния мужской и женской половых клеток с образованием зиготы...
Кормораздатчик мобильный электрифицированный: схема и процесс работы устройства...
Типы оградительных сооружений в морском порту: По расположению оградительных сооружений в плане различают волноломы, обе оконечности...
© cyberpedia.su 2017-2024 - Не является автором материалов. Исключительное право сохранено за автором текста.
Если вы не хотите, чтобы данный материал был у нас на сайте, перейдите по ссылке: Нарушение авторских прав. Мы поможем в написании вашей работы!