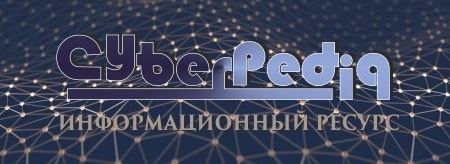
Общие условия выбора системы дренажа: Система дренажа выбирается в зависимости от характера защищаемого...
Адаптации растений и животных к жизни в горах: Большое значение для жизни организмов в горах имеют степень расчленения, крутизна и экспозиционные различия склонов...
Топ:
Проблема типологии научных революций: Глобальные научные революции и типы научной рациональности...
Методика измерений сопротивления растеканию тока анодного заземления: Анодный заземлитель (анод) – проводник, погруженный в электролитическую среду (грунт, раствор электролита) и подключенный к положительному...
Оценка эффективности инструментов коммуникационной политики: Внешние коммуникации - обмен информацией между организацией и её внешней средой...
Интересное:
Инженерная защита территорий, зданий и сооружений от опасных геологических процессов: Изучение оползневых явлений, оценка устойчивости склонов и проектирование противооползневых сооружений — актуальнейшие задачи, стоящие перед отечественными...
Финансовый рынок и его значение в управлении денежными потоками на современном этапе: любому предприятию для расширения производства и увеличения прибыли нужны...
Распространение рака на другие отдаленные от желудка органы: Характерных симптомов рака желудка не существует. Выраженные симптомы появляются, когда опухоль...
Дисциплины:
![]() |
![]() |
5.00
из
|
Заказать работу |
|
|
Цпет окраски | Первый раствор | Второй раствор | Температура раствора, °С | Время выдержки в каждом растворе, мин |
Белый | Азотнокислый барий | Сернокислый натрий | 60 | 30 |
СИНИЙ | Хлорное железо | Железистосинеро-дистый калий | 60 | 20 |
Желтый | Уксусный свинец | Двухромовокис-лый калий | 90 | 10 |
Оранжевый | Азотнокислое серебро | Хромовокислый калий | 75 | 10 |
Коричневый | Медный купорос | Железистосине-родистый калий | 60 | 20 |
1-20. Химическое никелирование предлагаемыми способами позволяет никелировать детали из стали, меди и медных сплавов.
Поверхность детали шлифуют, полируют, а затем обезжиривают. Для обезжиривания стальных деталей применяют водный раствор следующего состава: едкий натр или едкий калий — 20 — 30, сода кальцинированная — 25 — 50, жидкое стекло (силикатный клей) — 5 — 10 г/л. Раствор для обезжиривания меди и медных сплавов: трннатрийфосфат — 100, жидкое стекло — 10 — 20 г/л. Обезжиривание в растворе комнатной температуры длится 40 — 60 мин. При нагревании раствора до 75 — 85°С процесс значительно ускоряется.
Обезжиренную деталь тщательно промывают в проточной воде и переносят в 5 %-ный раствор соляной кислоты на 0,5 — 1 мин для декапирования. Температура раствора должна быть не выше 20 °С. Затем деталь тщательно промывают и сразу переносят в раствор для никелирования (на воздухе деталь быстро покрывается оксидйой пленкой).
Раствор для никелирования приготавливают следующим образом. В литре воды, нагретой до 60°С, растворяют 30 г хлористого никеля и 10 г уксуснокислого натрия. Температуру раствора доводят до 80 °С, добавляют 15 г гипосульфита натрия и погружают в раствор никелируемую деталь. Раствор с деталью подогревают до температуры 90 — 92 °С, которую поддерживают постоянной до конца никелирования. При температуре раствора ниже 90 °С процесс никелирования протекает медленно, а при нагревании выше 95 °С раствор портится.
|
Объем раствора в литрах численно должен быть равен одной трети площади детали, выраженной в квадратных дециметрах.
Скорость наращивания пленки приблизительно 10 мкм/ч.
Другой способ позволяет никелировать медные, латунные и бронзовые детали, обеспечивает плотную блестящую пленку, обладающую хорошими антикоррозийными свойствами. Не требует сложного оборудования и особых затрат на материалы.
Деталь зачищают, полируют. Обезжиривают в растворе, рецепт которого приведен выше. Декапирования при этом можно не производить.
В эмалированную посуду наливают 10 %-ный раствор хлористого цинка («паяльной кислоты») и к нему добавляют сернокислый никель до тех пор, пока раствор не станет густо-зеленого цвета. Полученный раствор нагревают до кипения и опускают в него деталь. В кипящем растворе деталь должна находиться 1 — 2 ч (при этом толщина слоя никеля будет около 10 мкм), затем деталь переносят в меловую воду (10 — 15 г мела на стакан воды) и слегка протирают ветошью. Далее деталь промывают и протирают насухо.
Для повторного применения раствор может быть сохранен в течение 6 мес в плотно закупоренной посуде.
Химическое никелирование алюминия почти не отличается от химического никелирования стали, за исклю-чевем того, что декапирование производят погружением детали на 2 — 3 мин в 50 %-ный раствор азотной кислоты.
1-21. Окраска стали (железа). Детали можно покрывать всеми видами лаков и красок. Чтобы покрытия были прочными, металл тщательно зачищают и грунтуют, причем каждому виду красок должен соответствовать определенный тип грунта.
При зачистке детали на длительное время погружают в керосин, затем снимают с них ржавчину и обезжиривают. Ржавчину можно снимать и другими способами (п. 1-4).
|
Грунт обладает повышенной адгезией (способностью сцепляться с поверхностью детали). Таким образом обеспечивается прочность всего покрытия (грунт плюс краска). Грунт кладут на поверхность детали слоем не более 0,2 мм толщиной и после высыхания зачищают наждачной шкуркой до полного выравнивания. В качестве своеобразного грунта можно применять уксусную эссенцию, которой протирают хорошо зачищенную и обезжиренную деталь. На такой «грунт» хорошо ложатся все виды красок, лаков и эмалей.
Окрашивают детали мягкими кистями в два слоя, причем второй слой наносят в направлении, перпендикулярном предыдущему.
Окраску удобно производить с помощью распылителя, приняв меры предосторожности для защиты от засорения свежего покрытия пылью. При этом могут быть использованы нитроэмали, синтетические меламиноал-кидные и алкидные эмали.
Нитроэмали высыхают быстро даже при комнатной температуре, но очень чувствительны к влаге (когда относительная влажность воздуха выше 70 %, пленка краски при высыхании может покрыться белыми пятнами). После высыхания образуется полуглянцевое покрытие, блеск которого может быть усилен до желаемой степени шлифованием и полированием. Процессы полирования и шлифования длительны и трудоемки. Адгезия нитроэмалей к металлу невысокая, поэтому перед окраской необходимо предварительное грунтование. Нитроэмали «обратимы». Это означает, что наносить кистью повторный слой нитроэмали нельзя без риска растворить ранее нанесенный слой.
Синтетические меламиноалкидные эмали образуют прочную глянцевую пленку. При температуре 100 — 130°С (в зависимости от сорта эмали) свеженанесенная пленка высыхает за 30 мин (выше 130°С эмаль нагревать нельзя). При комнатной температуре такая эмаль, к сожалению, вообще не высыхает. Шлифовать высохшую эмаль нельзя. Полируют ее составами, содержащими воск. Адгезия к металлу хорошая, поэтому можно. красить без грунтовки.
Алкидные эмали близки по природе к масляным краскам. По прочности аналогичны синтетическим и так же реагируют на шлифование и полирование. В отличие от синтетических эмалей они высыхают при комнатной температуре за 2 сут (при повышении температуры это время может быть значительно сокращено),
Некоторые эмали выпускаются в аэрозольной упаковке. В баллоны с эмалью закладываются стальные шарики. Их назначение — помочь равномерно перемешать содержащиеся в баллоне эмаль и растворитель. Поэтому перед пользованием необходимо встряхивать баллон до тех пор, пока не послышатся звуки ударов шариков о стенки баллона. Более того, встряхивание надо продолжать после этого еще в течение двух минут и лишь затем приступать к окраске. Из предосторожности струю направляют куда-либо в сторону, а уж потом, убедившись в равномерной подаче эмали, — на окрашиваемую поверхность.
|
В течение всего процесса окрашивания нужно совершать непрерывные равномерные движения рукой с баллоном, держа его на расстоянии 25 — 30 см от окрашиваемой поверхности. Струя краски должна быть перпендикулярной к поверхности. При перерыве в работе необходимо продуть клапан баллона, иначе эмаль в клапане высохнет и он засорится. Для этого баллон надо перевернуть и нажать на пусковую кнопку: как только струя, выходящая из сопла, станет бесцветной, продувание следует прекратить.
1.22. Удаление старых лакокрасочных покрытий с металлических изделий осуществляют с помощью смывок и смывочных паст.
Таблица 1-2
Составы смывок и паст для удаления эмалей и лаков на основе нитроцеллюлозы, глифталевых и нитроглифталевых смол, %
Компонент |
Составы | ||||||
I |
III | IV | V | VI | VII | |||
Ацетон | 30 | 47 | 25 | 14 | 40 | 60 | |
Этиловый спирт | 10 | 6 | — | — | — | — | — |
Этилацетат | 30 | 19 | — | 1 | — | — | — |
Метиловый спирт | — | — | 30 | 82 | — | 44 | — |
Скипидар | — | 7 | — | — | — | — | — |
Бензин | 30 | 8 | — | — | — | — | — |
Бензол | — | — | 20 | — | — | 5.0 | 30 |
Лигроин | — | — | — | — | 40 | ||
Ксилол | — | — | 7 | __ | — | — | — |
Четыреххлористый углерод Парафин | — | 2 | 15 3 | 2 | 20 | 6 | 10 |
Воск | — | — | 1 | ||||
Нафталин | — | 11 | — | — | — | — |
В табл. 1-2 приведены составы некоторых смывок и паст. Смывку или пасту наносят на покрытие, подлежащее удалению. Через некоторое время лакокрасочное покрытие размягчается и его можно легко удалить. Наличие парафина (воска) делает состав более густым или даже пастообразным. Работать с пастообразным составом удобнее, чем со смывкой, которую приходится наносить на обрабатываемую поверхность несколько раз.
|
Удаление масляных красок и лаковых покрытий с металлических поверхностей производят теми же составами, что и для снятия их с деревянных поверхностей (см. п. 2-18),
Наете ли Вы?
1-23. Если зенковать ручной дрелью отверстие под потайную головку винта в вязком листовом металле (медь, алюминий, мягкий дюралюминий) толщиной меньше трети диаметра сверла и при этом закрепить деталь струбцинами на пластине из текстолита или твердого дерева, то коническое углубление получится более аккуратным.
1-24. При нарезании резьбы в мягких металлах (например, в алюминии) следует ограничиться нарезкой резьбы только первым метчиком. В таком отверстии, винт удерживается прочнее.
1-25. Резьбу после обрезания винта или шпильки будет легко восстановить, если предварительно навинтить на них плашку или гайку. Отрезав или откусив кусачками лишнее, конец резьбовой детали опиливают напильником, а затем свинчивают плашку (гайку) — резьба восстанавливается.
1-26. Чтобы резьба, нарезанная метчиком в глухом отверстии, была чистой, отверстие следует предварительно заполнить расплавленным парафином и резьбу нарезать, когда он затвердеет.
1-27. Вымыть посуду, в которой находился керосин, можно известковым молоком: в очищаемый сосуд всыпают немного гашеной извести и, часто взбалтывая, наполняют доверху водой. Через несколько часов содержимое выливают, прополаскивают водой и повторяют все еще раз. Чистка будет быстрее, если в посуду при взбалтывании добавлять крупный песок.
1-28. Если после работы с керосином, растворителями, краской руки имеют специфический запах, то лучший способ избавиться от него — вымыть руки водой с горчицей.
1-29. Мелкие шайбы и втулки удобнее рассверливать, аккуратно зажав их в патроне дрели; сверло в этом случае зажимают в тисках. В остальном процесс сверления не отличается от обычного. Этот способ уменьшает вероятность порчи детали.
1-30. В насечках напильника не будут застревать частицы обрабатываемого металла, если напильник предварительно натереть мелом или древесным углем или смочить спиртом.
1-31. Просверливаемые в тонком металлическом листе отверстия получатся чище, если, зажимая лист в тисках, подложить под него деревянный брусок.
1-32. Никелированные поверхности различных предметов можно чистить пеплом от сигарет, насыпан его на влажную тряпочку.
1-33. Изделия из меди и латуни сохраняют свой блеск, если их тщательно натереть воском.
1-34. Металлические детали отделки не потеряют блеска, если их покрыть цапонлаком или бесцветным лаком для ногтей.
1-35. Бронзовые детали можно чистить сырым картофелем или жесткой волосяной щеткой, смоченной горячим уксусом. После этого деталь необходимо протереть мягкой тканью.
|
1-36. Освежить поверхность небольших изделий из меди можно, прокипятив их в течение 30 мин в растворе кальцинированной соды (40 г/л).
1-37. Шасси, изготовленное из алюминия или его сплавов, можно сделать слегка матовым, если обработать в 5 %-ном растворе едкого натра в течение 5 мин. Предварительно шасси тщательно зачищают мелкой шкуркой и промывают в мыльной воде.
1-38. Освежить алюминиевые шасси, панели и экраны можно, промыв их жесткой волосяной щеткой в теплом водном растворе хозяйственного мыла.
1-39. Насечки у напильников бывают одинарные и перекрестные (двойные). Для обработки твердых металлов более пригодна перекрестная насечка, для мягких — одинарная.
1-40. Если деревянные ручки у слесарного инструмента слегка обжечь на огне (до потемнения), то можно предотвратить появление мозолей или водяных пузырей на руках во время обработки металлов (или, по крайней мере, замедлить их образование).
РАБОТА С ДРЕВЕСИНОЙ
2-1. Выбор породы древесины обусловливается назначением изделия, его формой и внешним видом. Древесина имеет слоисто-волокнистую структуру, и свойства ее во многом определяются плоскостью среза. Выделяют три основных среза: поперечный или торцевой (поперек волокон), радиальный — по оси ствола и тангенциальный — в плоскости вдоль ствола, отстоящей от оси на любом расстоянии. Следует иметь в виду, что бруски и доски радиального среза менее подвержены короблению. Ниже приведены характеристики основных пород древесины, наиболее широко используемых в любительской практике.
Сосна — самая распространенная порода древесины. Ее достоинства — легкость и достаточно высокая прочность, недостатки — сучковатость, смолистость и трудность декоративной отделки. Применяют сосну для изделий, идущих под оклейку шпоном ценных пород (пп. 2-8, 2-10), под отдельку текстурованной бумагой (п. 2-12) и для деталей, не требующих отделки (например, дно, внутренние связующие и вспомогательные бруски корпусов, футляров).
Ель по прочности и стойкости уступает сосне. Ее достоинство — равномерный белый, долго сохраняющийся цвет древесины. Ель обладает меньшей смолистостью, поэтому лучше, чем сосна, поддается склеиванию и отделке. Изготовленные из ели звукоотражательные доски акустических систем имеют более высокие показатели, чем изготовленные из сосны.
Береза однородна по строению, прочна и очень хорошо отделывается. Благодаря белому цвету она легко окрашивается даже в самые нежные тона, ее отделывают под орех, красное и черное дерево. Недостаток березы — деформация под влиянием переменной влажности воздуха.
Ольха очень хорошо поддается обработке и отделке. Ее структура однородна, мягка, хорошо отделывается под орех, красное дерево, мореный клен.
Бук — вязкая и довольно твердая порода древесины, но дает значительную усушку и сильно коробится. Буковый шпон имеет красивую текстуру, легко отделывается и широко применяется для фанерования изделий из сосны и ели.
Дуб — твердая и прочная порода древесины. Применяется для изготовления наиболее ответственных деталей, несущих значительные механические нагрузки. Красивый рисунок и цвет позволяют использовать дуб для лицевых панелей. Особенно ценится мореный дуб, имеющий темную окраску. Для получения гладкой поверхности необходима тщательная обработка — покрытие по-розаполнительными составами (п. 2-9) с последующей полировкой, однако основной обработкой деталей из дуба считают восковую полировку — вощение (п. 2-14) и лакирование (п. 2-15).
2-2. Сушка древесины заключается в испарении влаги с ее поверхности и перемещении влаги из толщи к поверхности. Первый процесс протекает быстрее второго, особенно при сушке заготовок большого сечения. Атмосферная сушка древесины (на открытом воздухе) продолжается многие месяцы. Применение сушильных камер и форсированных режимов значительно ускоряет сушку, но и в этом случае доски толщиной 50 мм и влажностью 60 % сушатся до влажности 12 % не менее 5 сут. При форсированных режимах сушки в древесине возникают внутренние напряжения, поэтому в промышленных условиях процесс сушки ускоряют, но только так, чтобы эти напряжения не превысили предела прочности материала, а растрескивание и коробление находились бы в границах допустимого.
На открытом воздухе древесину можно высушивать до влажности 20 — 25 % в зависимости от времени года и погоды. Однако изделия из древесины, которые будут использоваться или храниться в жилых помещениях, должны иметь влажность 10 — 12 %. Следовательно, изготовление изделий из древесины нужно начинать после досушивания, и лучше всего в обрезанных по контуру заготовках с запасом материала на усушку. Такие заготовки занимают меньше места и быстрее высыхают. При этом нельзя класть их у отопительных или нагревательных приборов. Лучшим местом для сушки заготовок в квартире являются антресоли. Производя разметку заготовок, следует помнить, что усушка древесины вдоль волокон составляет около 0,1 %, в радиальном направлении — 3 — 5 %, в тангенциальном — 6 — 10 %.
2-3. Выбор поделочного материала для любительских работ достаточно разнообразен. В распоряжении мастера могут быть доски и бруски из различных пород древесины, фанера и древесностружечная плита, паркетная дощечка. Последняя пригодна, например, для изготовления декоративных элементов конструкций и ответственных узлов и деталей, несущих механические нагрузки. Даже тарная дощечка в умелых руках мастера может обрести новую жизнь.
Породу древесины выбирают в зависимости от предназначения и вида будущего изделия, приемлемых способов обработки и отделки. Выбирая поделочный материал, нужно учитывать не только его механические свойства, но и его цвет, тон. Правда, способы обработки и отделки позволяют изменить цвет и тон древесины имитацией (п. 2-10) или отбеливанием (п. 2-11). Доски лучше выбирать хорошо просушенные, выдержанные и радиального среза, потому что они меньше подвержены короблению.
2-4. Сверление отверстий я деталях из древесины производят специальными сверлами: поперечное сверление — центровыми, так называемыми пёрками, а продольное — спиральными. Сверло закрепляют в коловороте или дрели с малым числом оборотов. Чтобы выход отверстия большого диаметра при сверлении был чистым (без сколов), лучше вначале сделать сквозное отверстие сверлом в два-три раза меньшего диаметра, затем, просверлив деталь сверлом нужного диаметра до половины, перевернуть ее и продолжать сверление, но уже с другой стороны. Можно сверлить и в один заход, но в этом случае, чтобы избежать сколов древесины на выходе сверла из сквозного отверстия, деталь необходимо плотно прижать к вспомогательной дощечке, лучше струбцинами. Древесина вспомогательной дощечки должна быть более плотной.
Отверстия диаметром более 25 мм удобно высверливать, пользуясь циркульным кондуктором, с последующим фрезерованием краев (см. пп. 5-12, 5-31).
2-5. Склеивание деталей — наиболее распространенный способ соединения деталей из древесины. Для этого пригодны многие клеи. Однако предпочтение отдают столярному клею, клею ПВА и казеиновому (см. пп. 4-1, 4-10, 4-14). Казеиновый клей особенно предпочтителен, когда склеивание деталей ведется с запрессовкой.
Главными требованиями к клеевым соединениям деталей являются прочность, а часто и незаметность соединения. Последнее особенно важно, когда отделка завершается прозрачным покрытием (пп. 2-9, 2-13 — 2-15). При окрашивании древесины клеевой шов должен принимать одинаковый с древесиной цвет. Обычно красители для древесины растворяют в воде, поэтому и клей в этом случае должен быть водным.
Незаметность и прочность соединения достигаются только в случае, если склеиваемые плоскости деталей плотно пригнаны одна к другой. Ровные плоскости или прямолинейные кромки прифуговывают. Когда плоскости нельзя прифуговать, поступают следующим образом. Выравнивают одну из плоскостей и покрывают сухой краской или штрихуют мягким карандашом. Затем накладывают ее на вторую плоскость, прижимают к ней и легким трением притирают плоскости; краска отмечает выпуклые места, которые срезают стамеской, снимают циклей или другими инструментами. Неоднократной обработкой добиваются, чтобы окрашенные пятна равно- мерно расположились по всей плоскости склеивания. После этого краситель снимают мягкой резинкой или легким циклеванием.
Соединение на клею часто дополняют столярным соединением — на шипах или на шурупах.
В тех случаях, когда невозможно обеспечить минимальный зазор между склеиваемыми поверхностями, целесообразно использовать клеевые пасты (см. п. 4-32).
2-6. Столярные соединения деталей (вязки) весьма разнообразны по исполнению. Детали из древесины могут быть соединены между собой при помощи шипов, шурупов или гвоздей. Эти вязки чаще всего не исключают соединения на клею, а дополняют его.
Шипом называют ту часть детали, которая входит в соответствующее отверстие, сделанное в другой, сочленяемой с ней детали. Соединение двух деталей (например, брусков) может быть концевым, когда оба бруска соединяются своими концами, или серединным (тавровым), когда конец одного бруска соединяется со средней частью другого. Шип может составлять одно целое с деталью или быть вставным, может проходить через деталь насквозь или кончаться в ее теле.
Вязки при помощи шипов разнообразны. На рис. 2-1 показаны распространенные типы столярных соединений.
Накладкой вполдерева — наиболее простое соединение, но недостаточно прочное и требует дополнительных креплений нагелями, гвоздями или шурупами. Для выполнения накладки срезают 1/2 толщины бруска.
Рис. 2-1. Угловые вязки брусков: а — накладкой вполдерева; б — прямым сквозным одинарным шипом; в — прямым двойным шипом; г — шипом «ласточкин хвост»; д — прямым глухим шипом; е — вставными шипами-шкантами; ж — «на ус» примыканием; з — «на ус» со вставным шипом; и — «на ус» внакладку; к — «на ус» со вставными шкантами; л — «на ус» сквозным шипом; м — «на ус» потайным шипом
Сквозным прямым одинарным шипом — очень распространено. Толщина шипа — 1/3 толщины бруска.
Сквозным прямым двойным шипом — несколько прочнее, чем соединение одинарным шипом. Толщина шипа составляет 1/5 толщины бруска.
Рис. 2-2. Тавровые вязки брусков: а — вполдерева; б — вполдерева «лапой»; в — трапециевидной накладкой; г — глухим сковороднем; д — прямым одинарным шипом; е — круглыми вставными шипами (нагелями)
«Ласточкиным хвостом» — чаще применяется там, где соединение работает на разрыв. Узкая часть шипа равна 1/3, а широкая — 3/5 т,олщины бруска.
Прямым.глухим одинарным (или двойным) шипом — применяют там, где необходимо скрыть торцевые стороны шипов на лицевой стороне изделия.
Двумя вставными шипами-шкантами — достаточно прочное, но требует хорошей приторцовки брусков и точного сверления или долбления гнезд.
«На ус» примыканием — недостаточно прочное и требует очень тщательной приторцовки брусков с дополнительным креплением «косынкой». «Косынку» ставят на клей, иногда укрепляют гвоздями или шурупами.
«На ус» со вставным шипом — может иметь один или несколько шипов на клею. Толщина шипа зависит от толщины брусков. В миниатюрных конструкциях шип может быть выполнен из шпона.
«На ус» внакладку — не отличается высокой прочностью. Толщина накладки — 1/2 толщины бруска.
«На ус» со вставными, шкантами — требует точной приторцовки брусков и точного сверления или долбления гнезд.
«На ус» сквозным или потайным шипом — прочнее, но также требует точной приторцовки поверхностей. Шипы делают толщиной от 1/3 до 1/5 толщины брусков.
Основные виды тавровых вязок представлены на рис. 2-2. Для прочности шипы этих вязок можно дополнительно скреплять нагелями.
Если части соединения с усилием входят одна в другую, то их сбивают, нанося удары молотком или киянкой. Чтобы не смять древесину, подкладывают предохранительный брусок или доску.
Стенки корпуса (футляра) можно соединять с помощью брусков, помещая их во внутреннюю полост угла. Чаще этот способ применяют для соединения фанерных стенок. Брусок прямоугольного или треугольного сечения приклеивают к стенкам и при необходимости крепят шурупами или гвоздями, часто — гвоздями без шляпок.
В любительской практике иногда можно обходиться клеевым соединением, усиливая его шурупами. Чтобы фанера на краях при ввертывании шурупов не скалывалась, следует предварительно просверлить в ней отверстия по диаметру шурупов и зенковать, если шуруп с потайной головкой. В бруске сверлят отверстия на половину глубины ввертывания шурупа сверлом соответствующего диаметра.
2-7. Соединение деталей из древесностружечной плиты (ДСП) вызывает определенные трудности. Поскольку этот материал на кромках легко крошится, столярные шиповые соединения здесь непригодны, и для обеспечения прочного соединения приходится использовать дополнительные детали из древесины или металла.
Рис. 2-3. Соединение деталей из древесно-стружечной плиты
Один из способов соединения деталей из древесностружечной плиты, удобный, например, при изготовлении ящиков акустических систем, позволяющий получить прочное и герметичное неразборное соединение деталей, основан на применении шурупов и эпоксидного клея.
-В торец одной из соединяемых деталей ввинчивают Шурупы на расстоянии 30 — 50 мм один от другого. Под шурупы заранее просверливают отверстия диаметром, на 1 — 1,5 мм меньшим диаметра шурупа. Резьбу шурупов перед завинчиванием смазывают эпоксидным клеем.
- Во второй детали в соответствующих местах сверлят -отверстия такого диаметра и глубины, чтобы головки шурупов первой детали легко входили в них. Теперь остается заполнить эпоксидным клеем отверстия во второй детали, обильно промазать этим же клеем соединяемые поверхности, сложить (как показано на рис. 2-3) и сжать детали, обеспечив прямой угол между ними. Излишки клея нужно удалить и выдержать узел в течение суток при комнатной температуре.
- Этим способом удобно изготовлять ящики из полированной древесностружечной плиты, а также из толстой фанеры или досок, поскольку он проще шипового и не нарушает декоративной целостности материала в месте соединения.
2-8. Фанерование — оклеивание изделия или деталей и узлов изделия из древесины шпоном — строганой фанерой, изготовленной из древесины ценных пород.
Все вырывы, выбоины, отщипы и вмятины на фанеруемой поверхности должны быть заделаны вставками с помощью клея. Самые мелкие из этих дефектов можно зашпаклевать клеевой шпаклевкой (см. табл. 4-1 и п. 4-12). После заделки поверхность необходимо выровнять и зашкурить. Во избежание образования трещин в шпоне после оклейки необходимо еще в процессе подготовки изделия все шиповые соединения и торцевые поверхности заделать при помощи планок, наклеек или «косынок», укрывающих места соединений и торцы. Для больших фанеруемых площадей выбирают шпон с крупным рисунком, для малых — с мелким. Раскрой шпона производят по бумажной выкройке острозаточенным сапожным ножом с помощью металлической линейки. Раскроенные куски шпона шлифуют с внутренней стороны крупнозернистой шкуркой и шпаклюют клеевой шпаклевкой в местах, имеющих трещины. Подготовленный шпон после выравнивания кромок, которые должны сходиться в местах стыков, складывают по размерам фанеруемой детали кромка к кромке и склеивают бумажной лентой шириной 20 — 25 мм. Чтобы кромки шпона стягивались, бумагу перед наклейкой пропитывают водой, а наклеивая, тщательно разглаживают.
Фанерование производят в помещении с температурой воздуха 25 — 30 °С. Поверхность фанеруемой детали и внутреннюю сторону шпона смазывают столярным клеем, а спустя 8 — 10 мин шпон накладывают на фанеруемую поверхность и притирают куском гладкого бруска и плоским столярным молотком. Хорошо притирать шпон утюгом, нагретым до 60 °С. Притирать следует вдоль линий текстуры шпона от середины площади к краям. Появляющиеся пузыри надо сразу же устранять, для чего шпон в дефектном месте смачивают водой, надрезают и вводят клей под него при помощи пипетки или шприца, а затем это место заглаживают утюгом. Сколы и вырывы устраняют путем вставки заплат, подобранных по цвету и рисунку текстуры. Вмятины увлажняют и проглаживают горячим утюгом до получения ровной поверхности. После полутора-, двухчасовой сушки при температуре 25 — 30 °С бумажные полрски, которыми были соединены куски шпона, следует удалить.
2-9. Подготовка поверхности под прозрачную отделку сводится к шлифованию, снятию ворса, грунтованию для заполнения пор, чтобы получить ровную и чистую поверхность, уменьшить впитывание лака и предотвратить выход пузырьков воздуха под лаковую поверхность.
Шлифуют прямолинейные участки поверхности изделия с помощью шкурки, обернутой вокруг деревянного бруска, криволинейные участки — шкуркой, в которую завернута мягкая резина нужной формы, а узкие отверстия или закругленные фаски — шкуркой, навернутой на круглую деревянную палочку. Мелкие детали и малодоступные места изделия шлифуют шкуркой, сложенной в несколько слоев и свернутой в плотную трубку. Движение шкурки должно быть направлено вдоль волокон, в противном случае на шлифуемой поверхности остаются глубокие царапины, которые трудно ликвидировать. Шлифование ведут последовательно, уменьшая зернистость шкурки.
После шлифования на поверхности древесины появляются почти незаметные волоски (ворс), в основном прилегающие к поверхности. Если смочить поверхность древесины водой, ворс поднимается, а после просушивания хорошо снимается мелкозернистой шкуркой. Для достижения особо чистой поверхности снятие ворса с увлажнением водой или водным красителем повторяют. После этого в поверхность изделия втирают порозапол-нители или грунтуют ее для заполнения мелких пор древесины. В качестве порозаполнителя может быть использован воск, растворенный в скипидаре (п. 2-14), или специальные порозаполнители, выпускаемые промышленностью, например КФ-1, КФ-2, КФ-3, жидкий воск (в аэрозольной упаковке) и др. К грунтам предъявляется -ряд специфических требований: грунт не должен скрывать структуру древесины, должен хорошо заполнять поры, быстро сохнуть, обладать водостойкостью и разбавляться растворителем. Простейший грунт может быть приготовлен по следующему рецепту (в массовых частях): олифа натуральная — 35 — 55, скипидар — 7 — 10, сиккатив — 5 — 7, молотый мел с красителем нужного тона — 40 — 50 для крупнопористых пород и 15 — 20 для мелкопористых.
Грунтование можно также осуществлять древесной пудрой (очень мелкими опилками), замешанной на жидком столярном клее с добавлением красителя под цвет изделия. Вместо столярного клея можно использовать другие разжиженные клеи, например БФ-2 со спиртом или ПВА с водой, а в качестве наполнителя — мел или тальк с нужным красителем. При пользовании клеевым грунтом ворс можно не снимать, так как он пристает и присыхает к поверхности древесины. :
После высыхания грунта или порозаполнителя обрабатываемую поверхность окончательно шлифуют.
2-10. Имитация ценных пород древесины обычно осуществляется пропитыванием поверхности древесины водным или спиртовым растворами специальных морилок, водными растворами анилиновых красителей или специальными химическими составами, рецептуры которых приведены в табл. 2-1. Для обработки древесины «под красное дерево» можно также воспользоваться смесью черной и красной туши (необходимую пропорцию следует подобрать опытным путем). Имитацию ореховой древесины можно получить при обработке древесины спиртовым раствором йода (2 %-ным).
Отделке «под красное дерево» хорошо поддаются ольха, вяз, ясень, бук, кедр; береза, вишня и груша, «под черное дерево» — береза, дуб, клен, граб, яблоня, слива -и вишня, «под орех» — ольха, береза, липа и бук.
Таблица 2-1 Водные растворы для имитации древесины ценных пород
Состав | Концентрация, г/л | Имитация | Технология |
1. Двухромово-кислый калий 2. Марганцево-кислый калий | 25 25 | «Под орех» | Второй раствор наносить спустя 10 мин после нанесения первого |
1. Медный купорос 2. Желтая кровяная соль | 10 — 50 100 | «Под красное дерево» | Второй раствор наносить после высыхания первого |
1. Хлористый анилин 2. Хлористая медь 3. Двухромово-кислый калий | 50 50 25 | «Под черное дерево» | Сначала нанести смесь двух первых растворов, а через 10 мин — трети раствор |
Растворы наносятся на тщательно отшлифованную (п. 2-9) поверхность тампоном из сложенной в несколько рядов марли, грубой кистью, пульверизатором; можно погружать детали в раствор. Чтобы состав ложился равномерным слоем, поверхность изделия следует предварительно увлажнить. Если спустя 15 — 20 мин после первого покрытия не получился цвет желаемой тональности, обработку следует повторить несколько раз, но при этом стараться не переувлажнить древесину, чтобы не вызвать ее коробление и растрескивание.
Цвет и тон красителя лучше проверить сначала на бумаге, а окончательно — на кусочке древесины той же породы, подготовленном аналогичным образом. Сырая, обработанная составом древесина дает почти правильное представление о яркости цвета и тона под лаком. Высохший мазок, покрытый лаком, соответствует окончательному цвету и тону будущего покрытия.
Краска лучше закрепляется на древесине, если в раствор добавить немного (до 3 %) столярного клея. При обработке древесины хвойных пород рекомендуется предварительно очистить ее от натеков смолы, а затем промыть составом, растворяющим смолу: 10 %-ным раствором едкого натра, бензином, скипидаром, спиртом или 10 %-ным раствором поваренной соли.
Имитация древесины ценных пород может быть осуществлена и при отделке металлических футляров фанерным шпоном. Ниже приводится один из технологических приемов такой отделки. Ровный, без изъянов лист органического стекла толщиной около 3 мм и другими размерами, на 30 — 50 мм~ большими, чем у самой большой стенки футляра, тщательно отмывают от пыли и грязи, сушат, смазывают одну из сторон вазелином и протирают насухо. При этом вазелин остается в микропорах стекла. Затем лист кладут на ровную горизонтальную поверхность смазанной стороной вверх и выливают на него некоторое количество приготовленного эпоксидного клея. Клей аккуратно распределяют по стеклу слоем в 1 — 1,5 мм и накладывают на него вырезанный с некоторым припуском лист шпона (лицевой стороной вниз). Все пузырьки воздуха из клеевого слоя тщательно удаляют, выдавливая их к краям. Пузырьки легко обнаружить, просматривая пакет со стороны стекла. Затем шпон покрывают тонким слоем эпоксидного клея и сверху накладывают футляр — одной из его сторон. Футляр перед этой операцией должен быть тщательно очищен от пыли и обезжирен. Через 6 — 7 ч органическое стекло снимают. Для этого лист стекла с одного края осторожно отгибают, и он постепенно отходит от слоя затвердевшего клея. Поверхность получается ровной, с зеркальным блеском. Натеки клея по краям спиливают напильником сразу же, не дав ему окончательно отвердеть (через несколько суток он станет хрупким и будет скалываться при обработке). После этого обрабатывают следующую сторону футляра.
2-11. Отбеливание древесины осуществляют для снижения интенсивности цвета, удаления пятен и т. п. Известен ряд отбеливающих веществ (главным образом для тканей), удаляющих пятна с белья. Однако.эти вещества на древесину плохо действуют. Хороший отбеливающий раствор можно приготовить
|
|
История развития пистолетов-пулеметов: Предпосылкой для возникновения пистолетов-пулеметов послужила давняя тенденция тяготения винтовок...
Папиллярные узоры пальцев рук - маркер спортивных способностей: дерматоглифические признаки формируются на 3-5 месяце беременности, не изменяются в течение жизни...
Автоматическое растормаживание колес: Тормозные устройства колес предназначены для уменьшения длины пробега и улучшения маневрирования ВС при...
История развития хранилищ для нефти: Первые склады нефти появились в XVII веке. Они представляли собой землянные ямы-амбара глубиной 4…5 м...
© cyberpedia.su 2017-2024 - Не является автором материалов. Исключительное право сохранено за автором текста.
Если вы не хотите, чтобы данный материал был у нас на сайте, перейдите по ссылке: Нарушение авторских прав. Мы поможем в написании вашей работы!