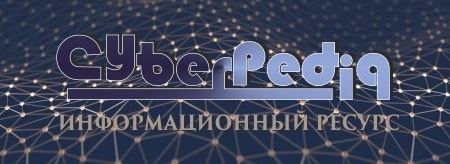
Механическое удерживание земляных масс: Механическое удерживание земляных масс на склоне обеспечивают контрфорсными сооружениями различных конструкций...
Поперечные профили набережных и береговой полосы: На городских территориях берегоукрепление проектируют с учетом технических и экономических требований, но особое значение придают эстетическим...
Топ:
Эволюция кровеносной системы позвоночных животных: Биологическая эволюция – необратимый процесс исторического развития живой природы...
Особенности труда и отдыха в условиях низких температур: К работам при низких температурах на открытом воздухе и в не отапливаемых помещениях допускаются лица не моложе 18 лет, прошедшие...
Отражение на счетах бухгалтерского учета процесса приобретения: Процесс заготовления представляет систему экономических событий, включающих приобретение организацией у поставщиков сырья...
Интересное:
Искусственное повышение поверхности территории: Варианты искусственного повышения поверхности территории необходимо выбирать на основе анализа следующих характеристик защищаемой территории...
Инженерная защита территорий, зданий и сооружений от опасных геологических процессов: Изучение оползневых явлений, оценка устойчивости склонов и проектирование противооползневых сооружений — актуальнейшие задачи, стоящие перед отечественными...
Финансовый рынок и его значение в управлении денежными потоками на современном этапе: любому предприятию для расширения производства и увеличения прибыли нужны...
Дисциплины:
![]() |
![]() |
5.00
из
|
Заказать работу |
|
|
3-1. Органическое стекло — термопластичная пластмасса — широко распространенный и доступный материал. Выпускается прозрачным или окрашенным в мас-.се, хорошо обрабатывается, склеивается (см. п. 4-27), окрашивается (пп. 3-18 — 3-20).
Органическое стекло полируется вручную чистой и „сухой суконкой или же суконкой с зубным порошком. Для получения блестящей, зеркальной поверхности органическое стекло полируют мелкозернистыми составами полировочных смесей. Хорошие результаты дает использование зубной пасты.
При механической полировке нужно использовать полировальный круг из хлопчатобумажной, а не из суконной ткани, так как при сильном прижимании детали к суконному вращающемуся кругу полируемую поверхность можно оплавить. Такой изъян ликвидировать очень трудно, а порой и невозможно.
3-2. Целлулоид широко используют для декоративной отделки шкал, шильдиков, элементов и деталей футляров приборов, усилителей, приемников. Этот материал легко определить по запаху камфары, который становится особенно ощутимым при трении о твердые поверхности. При нагреве до 90 — 100°С целлулоид размягчается и становится пластичным, а при охлаждении снова Затвердевает. Детали из целлулоида прочно склеиваются, нитроклеем (п. 4-25) и хорошо полируются. Но целлулоид огнеопасен и, кроме того, под влиянием солнечных лучей желтеет, поэтому при возможности целлулоид заменяют другим, подобным ему, но негорючим пластиком — триацетатной пленкой. Целлулоид и триацетатные йленки в большинстве случаев выпускают прозрачными. -Рецепты крашения целлулоида приведены в п. 3-17.
3-3. Гетинакс — листовой материал из прессованной бумаги, пропитанной бакелитовым лаком. Для исполь-
|
зования на низких частотах выпускают гетинакс толщиной от 0,2 до 50 мм, на высоких частотах — от 0,4 до 3,8 мм. Последний характеризуется малыми диэлектрическими потерями. Кроме того, выпускается фольгиро-ванный (одно- и двусторонний) гетинакс. Этот материал в домашних условиях пригоден для изготовления не только печатных плат, но и корпусов приборов, небольших экранированных блоков; при этом стенки и перегородки блоков соединяют пайкой.
3-4. Декоративный пластик представляет собой гетинакс с односторонним (как правило) декоративным покрытием. Покрытие лицевой стороны листа может имитировать текстуру древесины ценных пород или иметь различный декоративный рисунок. Выпускаются также листы с однотонной лицевой стороной различных цветов и оттенков. Применение пластиков в любительских конструкциях позволяет придать хороший внешний вид лицевым панелям, футлярам приборов и др. При этом следует иметь в виду, что пластик с односторонним покрытием имеет свойство коробиться из-за различия механических напряжений, возникающих в основе пластика и в его покрытии. Под воздействием изменяющихся температуры и влажности окружающей среды изменяется и характер деформации, что особенно заметно у деталей, имеющих большие площади. Поэтому лицевые панели, дверки целесообразно склеивать из двух листов пластика, выкраивая их из симметрично деформированных листов, причем лучше — выпуклостью в сторону декоративного покрытия, чтобы отрывающие нагрузки на клеевое соединение действовали бы в центре листов, а не на их краях.
Если на пластике светлых тонов при изготовлении лицевых панелей делать гравировку, снимая декоративный слой до темной основы, надписи получаются достаточно контрастными без дополнительного подкрашивания.
3-5. Текстолит — прессованная хлопчатобумажная ткань, пропитанная бакелитовым лаком. Текстолит выпускается в виде листов толщиной от 0,5 до 50 мм и стержней диаметром от 8 до 60 мм. Из листового текстолита изготовляют различные монтажные планки и платы, элементы креплений и т. п. Из стержней вытачивают крепежные стойки, втулки, ролики, ручки для инструмента и другие детали.
|
3-6. Стеклотекстолит изготавливается на основе стеклоткани и обладает повышенной механической прочностью, особенно на изгиб. Выпускается в виде листов толщиной от 0,5 до 2,5 мм. Наибольшее применение находит фольгированный стеклотекстолит (одно- и двусторонний). Используется так же, как и гетинакс. При необходимости лист стеклотекстолита можно расслоить (п. 3-22).
3-7. Разметка листового материала. Разметку целесообразно проводить вначале на отдельном листе бумаги (лучше с миллиметровой сеткой) в масштабе 1:1. На лисг наносят все контурные линии будущей детали, отмечают отверстия и другие элементы. Чертеж крепят на заготовке и кернером переносят на материал нужные точки, которые затем высверливают. Этот метод разметки сохраняет гладкую поверхность заготовки, без царапин и лишних прочерчиваний.
Для «кернения» отверстий на термопластичных ма-териалах, особенно на органическом стекле, лучше пользоваться специальной насадкой на жало паяльника или специальным сменным жалом-(см. рис. 9-5). Лунки получаются ровными, органическое стекло не растрескивается. Глубина лунок зависит от длительности прикосновения насадки к детали, температуры насадки и определяется опытным путем. Для отверстий диаметром 1 — 10 мм угол заточки насадки должен быть 30 — 45°, а для отверстий диаметром 15 — 25 мм — до 100 — 120°.
При изготовлении круглых деталей разметку делают с помощью разметочного циркуля. Чтобы ножка циркуля не оставляла в центре окружности след, ее следует устанавливать в центрик, воткнутый в стиральную резинку. Этим способом можно размечать детали более сложной формы, если элементами ее являются дуги окружностей.
3-8. Резка листового материала возможна различными инструментами в зависимости от конкретных условий, конфигурации детали, марки материала и др.
Наиболее удобны для резки листового материала специальные резаки, изготовленные из старых ножовочных полотен (см. п. 5-13).
Резак ведут по краю плотно прижатой линейки, причем неоднократно. После того как резак углубится на 0,2 — 0,3 мм, линейку можно убрать. Сделав надрез на треть толщины листа, ножовкой надпиливают лист на краях, переворачивают заготовку и повторяют операцию на обратной стороне. После этого, положив лист на стол так,-чтобы линия отреза совпала с краем стола, разламывают лист. Торец обрабатывают плоским напильником. Резак, конструкция которого описана в п. 5-14, позволяет вырезать круглые отверстия больших диаметров.
|
Детали сложной конфигурации приходится вырезать лрбзиком, используя ножовочное полотно для металла.
Органическое стекло можно разрезать обыкновенной ниткой № 00. Нитку натягивают в станке для ножовочного полотна или в лобзике. Резку производят так же, как и ножовкой. Этим способом можно выполнять фигурную резку органического стекла с большой точностью. Для фигурной резки можно также воспользоваться отрезком нихромовой или никелиновой проволоки диаметром 0,2 — 0,3 мм, натянутым на изоляторах в станке для ножовочного полотна или в лобзике и подключенным к электрической сети через низковольтный трансформатор и регулируемый автотрансформатор. Температуру проволоки надо подобрать опытным путем, изменяя приложенное к ней напряжение.
Рис. 3-1. Сверло из ролика стеклореза
1 — твердосплавное колесико; 2 — осьзаклепка; 3 — стержень или трубка
3-9. Резка стекла производится алмазом или стеклорезом. Эта операция проста и не требует особых пояснений. Если под рукой не окажется нужного инструмента, можно, воспользоваться кварцевой пластиной от неисправного резонатора, обломком корундового камня (от бруска или круга) или даже обломком напильника. Но иногда возникает необходимость вырезать из стекла деталь непрямолинёйной конфигурации. Для этого на стекло наносят рисунок нужной формы или подкладывают рисунок на бумаге под стекло, но в обоих случаях так, чтобы одна сторона этого рисунка находилась на краю заготовки. Стекло надпиливают трехгранным личным напильником или алмазным надфилем. Затем раскаленным жалом прибора для выжигания (при полном накале) медленно, начиная от надпила, обводят нарисованный контур. Под раскаленным жалом будет непрерывно образовываться трещина, заметная невооруженным глазом. Далее лишнее стекло небольшими участками обламывают с помощью плоскогубцев (лучше, погрузив стекло в воду). Края можно зашлифовать абразивным бруском. Теперь нужно снять образовавшиеся остаточные механические напряжения в стекле кипячением в воде не менее часа. В противном случае могут образоваться трещины.
|
Вместо прибора для выжигания можно использовать специально приготовленные угольные палочки. Древесный березовый уголь толкут в мелкий порошок и замешивают на густом и теплом клейстере (см. пп. 4-20, 4-21), а еще лучше на гуммиарабике (см. п. 4-19). Из полученной тестообразной массы катают тонкие палочки. Высушенные палочки готовы к применению. Угольную палочку поджигают, раздувают, прикладывают к краю стекла и ведут ее за образующейся трещиной по контуру рисунка.
3-10. Сверление стекла всегда производят через кондуктор (металлическую накладку толщиной 4 — 5 мм с отверстием, равным диаметру сверла), плотно прижатый к стеклу. Стекло должно лежать на твердой и ровной поверхности. Сверлят ручной дрелью одним из ниже приведенных способов при несильном нажатии, уменьшая его при выходе сверла. 1-й способ. Сверление производят обычным сверлом. Чтобы закалить сверло, которым собираются работать, кончик сверла накаляют добела, затем быстрыми движениями вдавливают его в сургуч до тех пор, пока сургуч не перестанет плавиться. Место сверления необходимо непрерывно смачивать следующим составом (в массовых частях): камфара — 8, скипидар — 12, эфир — 3.
2-й способ. Сверлят плоским сверлом, заточенным лопаточкой, вращая сверло попеременно то в одну, то в другую сторону. В качестве эмульсии в этом случае используют силикатный клей (жидкое стекло). Эмульсию меняют, как только она помутнеет.
3-й способ. Сверлом может быть подходящая по диаметру медная трубка, слегка расширенная на конце кернером или другим подходящим инструментом. На место сверления наносят несколько капель силикатного клея с наждачным порошком (лучше корундовым). При сверлении смесь периодически обновляют.
4-й способ. При необходимости просверлить отверстие диаметром 6,5 мм в качестве сверла можно использо-вать твердосплавное колесико от стеклореза, закрепив его на оси-заклепке в прорези стержня или трубочки диаметром 4 — 5 мм (рис. 3-1). Место сверления смачивают водой. Сверление отверстия этим способом в стекле тол-щиной 6 мм занимает 4 — 6 мин.
3-11. Сверление пластиков. При сверлении отверстий в пластиках, особенно в гетинаксе и декоративном слои-стом пластике, материал с обратной стороны часто скалывается. Чтобы этого не случилось, вначале следует сверлить отверстия сверлом, диаметр которого примерно вдвое меньше необходимого. Затем сверлом (диаметр которого на 0,5 — 1,0 мм больше диаметра требующегося отверстия), заточенным под углом 60 — 90°, производят зенкование полученных отверстий с обеих сторон и, наконец, рассверливают их сверлом необходимого диаметра. Такой способ сверления отверстий в пластиках полностью устраняет опасность сколов и трещин и дает возможность получить очень точные, чистые отверстия, не требующие никакой дополнительной обработки.
|
Рис. 3-2. Пресс-машина
1 — винт; 2 — перекладина; 3 — латунная труба, 4 — слюда; 5 — поршень; 6 — спираль от электроплитки; 7 — литник; 8 — основание; 9 — фильера
3-12. Нарезание резьбы в пластмассах можно осуществить и самодельным метчиком. Для этого берут стальную шпильку или болт с требуемой резьбой и опиливают конец (2 — 5 мм) на конус, Головку болта отрезают и трехгранным напильником или с помощью бормашины (см. п. 5-24) и шлифовального круга соответствующего профиля пропиливают 3-4 режущие кромки до длине болта.
Хвостовик изготовленного метчика можно заточить под вороток или, прорезав в нем шлиц шириной 2 — 4 мм, вставить металлический пруток и припаять.
Вполне удовлетворительные результаты, особенно для резьбы М4 и менее, можно получить, не пропиливая режущие кромки, а спилив резьбу винта или шпильки с двух сторон. Чтобы нарезаемая резьба была более чистой, по резьбе изготовленного метчика нужно «пройти» соответствующей плашкой или гайкой. Шпильку, болт или винт берут с нарезной, а не с накатной резьбой,
3-13. Изгибание листового термопластичного материала (органическое стекло, полистирол, винипласт и др.) можно осуществлять, только прогрев материал, причем хороший изгиб правильной формы получается лишь при равномерном прогреве материала с обеих сторон на ширину 5 — 15 мм — в зависимости от толщины листа.
Для разогревания на лист пластика с обеих сторон вдоль линии изгиба накладывают полосу нужной ширины из тонкой алюминиевой фольги и прижимают. Концы полосы подключают к накальной обмотке какого-либо трансформатора, сетевая обмотка которого подключена через лабораторный автотрансформатор, и подбирают необходимое напряжение. Не следует допускать перегрева, так как при этом прозрачность или цвет материала по линии сгиба могут заметно измениться. Как только материал прогреется, фольгу снимают, лист изгибают на требуемый угол и выдерживают заготовку до полного оеты&ания.
3-14. Литье из термопластичных материалов. Сырьем для.литья служит вторичное сырье из полиамидов (старые капроновые чулки, ветошь из капрона, нейлона, силона, дедерона, дакрона, рыболовные жилки и др.), акрилаты (акрил-пластмассы, органическое стекло), полистирол. При использовании в качестве сырья чулок из капрона необходимо срезать швы, носок и пятку, так как они часто делаются с добавлением другого материала.
Сырье тщательно обезжиривают в 10 %-ном содовом растворе при температуре 50 — 60 °С в течение 1 ч, затем промывают в теплой воде, сушат, измельчают (твердый материал измельчают до частиц размером менее 5 мм) и загружают в пресс-машину.
Конструкция пресс-машины показана на рис. 3-2. Пресс-машина изготовлена из отрезка латунной трубы с припаянным снизу дном. В верхней части трубы в специальных прорезях помещена перекладина, в средней части которой имеется отверстие с резьбой М10 илиМ12, куда ввертывается изогнутая в виде буквы «Г» шпилька (можно использовать винт от струбцины). При помощи этой шпильки или винта в трубе перемещается поршень, который и выдавливает размягченный материал через литник в подготовленную для отливки форму.
Сырье размягчается при температуре 80 — 200 °С. Для нагрева внутреннего объема пресс-машины на образующую цилиндра наматывают, а под его основание укладывают на слой слюды выпрямленную спираль от бытовой электроплитки. Поверх спирали наносят пасту, приготовленную из крошки слюды или асбеста и силикатного клея. Можно также использовать пасту, приготовленную по рецепту, приведенному в п. 4-33. Затем цилиндр обматывают асбестовым шнуром и устанавливают на деревянное основание, подложив под него лист асбеста. Чтобы регулировать температуру нагрева, спираль включают в электросеть через лабораторный автотрансформатор.
Для получения различных декоративных окантовок необходимо -изготовить фильеры нужной конфигурации. Фильера навинчивается на литник. При выдавливании масса приобретает профиль отверстия фильеры. По выходе из фильеры массу нужно охлаждать в холодной воде. Этим способом можно получать различные изоля-, ционные прокладки и окантовки из полихлорвинила. Температура размягчения полихлорвинила 80 — 100°С.
3-15. Литье из зубопротезных пластмасс. Зубопротезные пластмассы акриловой группы (например, прота-крил) являются прекрасным материалом для изготовления ручек и клавишей, подшипников скольжения, элементов декоративного оформления и многих других деталей.
Протакрил — самотвердеющая пластмасса на основе акриловых полимеров (типа порошок — жидкость). Эта пластмасса устойчива к истиранию (не уступает капрону) и обладает высокой адгезией. Из нее получаются хорошие подшипники скольжения для миниатюрных механических устройств (моторы, редукторы и др.), не требующие смазки, работающие долго без заметного износа. Электрические характеристики этого материала (без наполнителя) несколько выше, чем у органического стекла.
Литьевые формы для получения деталей из этой пластмассы можно изготавливать из жести, дерева, папье-маше (п. 3-16, 5-й рецепт), глины, пластилина, гипса и других материалов. Из гипса можно изготавливать Достаточно износостойкие формы для неоднократного использования; при этом процесс изготовления отличается малой трудоемкостью.
Гипс предварительно просеивают, размешивают в холодной воде до образования сметанообразной массы. Подходящую по размерам коробку наполовину заливают гипсом. В жидкий гипс вдавливают наполовину модель, предварительно смазав ее густым мыльным, раствором, чтобы потом ее можно было извлечь, не разрушив формы. После застывания этой половины формы в ней по краям, не задевая контура модели, высверливают 2 — 3 неглубоких отверстия, которые будут направляющими для другой половины формы. Затем замешивают, вторую порцию гипса и заливают в коробку. Предварительно первую половину формы, в том числе и направляющие отверстия, смазывают густым мыльным раствором и сушат. Когда гипс застынет, половины формы осторожно разъединяют и извлекают модель.
После этого обе половины формы тщательно покрывают антиадгезирующим веществом: смазывают силиконовым маслом или натирают графитовым порошком. Несколько худшие результаты дает обыкновенное подсолнечное масло. Приготовленную пластмассу по приведенной в п. 4-24 технологии заливают в первую и вторую половины формы.и обе половины складывают так, чтобы совпали углубления первой половины формы и высту-пы второй. Форму плотно стягивают струбциной или заматывают тонким проводом и помещают в посуду с холодной водой. Воду медленно подогревают и доводят до кипения.
Термическую обработку деталей из протакрила таким методом проводят в течение 1,5 — 2 ч, причем делать это лучше через 1--2 сут., т.е. когда полностью закончится предварительная полимеризация в глубинных слоях пластмассы.
По окончании термической обработки форму охлаждают, вскрывают и извлекают из нее изготовленную деталь. Если требуется, деталь дополнительно обрабатывают. Для повышения долговечности форм в гипс добавляют измельченный асбест.
При изготовлении партии деталей необходимо применять металлическую форму. Модель в этом случае изготавливают из алюминия или дюралюминия. Первую половину формы отливают из свинца или гарта (гарт — типографский сплав). Вторую половину формы изготавливают из сплава свинца и легкоплавкого зубопротезного сплава (или легкоплавкого припоя) в соотношении 1:1.
Если необходимо сделать дубликаты какой-либо пластмассовой детали, то сначала по оригиналу изготавливают гипсовую форму и отливают свинцовый дубликат детали. По полученному дубликату детали изготавливают форму, первую половину которой отливают из сплава свинца и легкоплавкого припоя, вторую — из одного легкоплавкого припоя.
3-16. Самодельные «пластмассы» применяют при изготовлении разнообразных деталей, не несущих больших нагрузок (стойки, кронштейны, обоймы), деталей оформления аппаратуры (футляры, ящики, наличники, обрамления), ручек различного инструмента, а также для заливки отверстий в абразивных кругах и т.д. Приготовление этих пластмасс несложно. Ниже приведен ряд рецептов.
1-й рецепт. Самодельные «текстолиты» изготовляют на тканевой основе, пропитываемой клеем. Можно применять столярный или казеиновый клей, но обязательно с добавлением антисептирующего вещества (см. пп. 4-10, 4-14). Вместо клея можно использовать загустевший нитролак или нитрокраску. Можно воспользоваться эпоксидным клеем.
Из самодельных текстолитов можно изготавливать корпуса для приборов, различные кожухи, задние стенки и другие детали. Для небольших деталей используют хлопчатобумажный или шелковый трикотаж. Годятся старые, но чистые майки, рубашки и т. п. Для крупногабаритных конструкций лучше применять мешковину.
Ткань натягивают на форму, изготовленную из мягкой древесины и покрытую тонким слоем парафина, приготовленным, как для вощения древесины (см. п. 2-14), закрепляют и смазывают клеем, затем натягивают следующий слой ткани — и так несколько раз. Столярный клей лучше использовать в горячем состоянии. Закреплять ткань удобно затяжными сапожными гвоздями, так как их легче извлекать при креплении следующего слоя. Излишки материала на закруглениях формы срезают так, чтобы ткань на линиях разреза можно было сшить встык, причем излишки материала вырезают таким об-разом, чтобы стыки второго слоя не совпадали со швами первого слоя..Второй слой натягивают и крепят гвоздями, удаляя гвозди, крепившие первый слой. Так укладывают 4 — 8 слоев и сушат в течение 8 — 10 суток.
Далее заготовку, не снимая с модели, шпаклюют смесью горячего столярного клея с мелом или с тальком и окончательно сушат. Можно применить и другую шпаклевку, выпускаемую для работ по дереву или приготовленную по одному из рецептов, приведенных в табл. 4-1. Слой шпаклевки должен быть не более 0,2 — 0,3 мм, т. е. чтобы только скрыть все неровности и структуру материала. Полное высыхание наступает через 20 — 25 сут, после чего уже нет опасности коробления заготовки. Высохшую заготовку зашкуривают, обрезают кромку и снимают с модели. Снимать заготовку нужно осторожно, применяя как рычаг широкую стамеску. Хорошо перед снятием заготовки оторвать ее от модели, пропуская между моделью и заготовкой металлическую измерительную линейку. Снятую с модели заготовку грунтуют и окрашивают с внутренней и наружной стороны. Для окончательной отделки лучше применять нитролаки или нитрокраски с соответствующими грунтами, так как они быстро сохнут и деталь не успевает покоробиться. После окраски деталь полируют до зеркального блеска.
2-й рецепт. Самодельные «пластики» из полос бумаги можно применять для изготовления корпусов, крышек футляров, задних стенок сложного профиля, сферических корпусов громкоговорителей. Для малогабаритных конструкций можно использовать полосы газетной бума-ги, для крупногабаритных — тонкие обои.
Модель покрывают тонким слоем парафина и накладывают на нее первый слой размоченных в горячей воде полосок бумаги. Затем полоски бумаги,для следующего слоя намазывают клеем. Можно использовать различные клеи (см. пп. 4-10 — 4-21), однако предпочтение.следует отдать стол-ярному или казеиновому клею с обязательным добавлением антисептиков.
Бумаге, намазанной клеем, дают время как следует пропитаться им. Если бумага впитала клей, ее промазывают еще раз и наклеивают полоски каждый раз перпендикулярно к направлению предыдущего слоя. Наклеив таким образом 4 — 5 слоев, делают промежуточную сушку в течение суток. Процесс повторяют несколько раз до получения необходимой толщины. Высушенную заготовку обрабатывают далее так же, как рекомендовано в 1-м рецепте,
3-й рецепт. Тщательно перемешивают 65 массовых частей мелких древесных опилок и 35 магнезита. Смесь заливают 0,1 %-ным раствором хлористого магния и размешивают до тестообразного состояния. Основной способ получения заготовок из данной «пластмассы» — литье в формы и изложницы. Застывая, «пластмасса» приобретает достаточно высокую прочность и при этом хорошо обрабатывается: ее легко пилить, сверлить и обтачивать. Применяют ее обычно для изготовления стоек, кронштейнов, для заливки отверстий в абразивных кругах и т. д.
4-й рецепт. Перемешивают мелкие древесные опилки и тальк молотый в массовом соотношении 5: 2, заливают приготовленным столярным клеем (консистенции сметаны) и размешивают до тестообразного состояния. Желательно ввести в смесь 0,3 — 0,5 массовых частей алюминиевых или алюмокалиевых квасцов, которые предупреждают появление плесени и тем самым сохраняют прочность «пластмассы:». Чтобы пластмасса была более пластичной, в нее необходимо ввести 0,5 массовой части натуральной о„лифы.
Можно заменить столярный клей казеиновым, в состав которого необходимо ввести антисептирующее вещество (см. п. 4-14).
Эта «пластмасса» менее прочна, чем «пластмасса», приготовленная по 3-му рецепту. Из нее можно изготавливать детали, не подвергающиеся большим механическим нагрузкам: наличники, обрамления, различные декоративные украшения и др. При желании «пластмассу» можно окрасить, добавив в ее состав анилиновый краситель нужного цвета.
После просушки изготовленную деталь шпаклюют, зашкуривают и окрашивают, причем шпаклевку лучше приготовлять на основе того клея, который применялся для изготовления самой «пластмассы».
Более прочной и быстровысыхающей получается «пластмасса», если вместо клея использовать сгущенный нитролак или нитрокраску. Детали из этой «пластмассы» также изготовляют литьем.
5-й рецепт. Для приготовления папье-маше из бумажной массы измельчают газетную бумагу, заваривают ее крутым кипятком и выдерживают в горячей воде 1 — 2 сут. Когда образуется взвесь тонкой консистенции, воду отцеживают и массу сушат. Высушенная масса легко превращается в порошок, который и служит основой папъе-маше. Порошок (10 массовых частей) перемешивают с тонкопросеянным мелом или тальком (3) и заливают клейстером, приготовленным из сухого столярного клея J2) и пшеничной муки (3). Для антисептирования в клейстер необходимо добавить 0,2 массовой части алюминиевых или алюмокалиевых квасцов. Массу можно окрашивать анилиновыми красителями.
Приготовленную массу наносят на модель, предварительно покрытую парафином. Можно отливать детали в формы или изложницы.
После полного высыхания деталь обрабатывают шкуркой, так чтобы не было неровностей, грунтуют и окрашивают.
6-й рецепт. «Пластмассу» с лучшими, чем у папье-маше, механическими свойствами можно получить, используя следующие компоненты (в массовых частях): сухую бумажную массу — 5; клей столярный (сухой) — 28; тонкопросеянный мёл — 60; глицерин — 2,5; спирт этиловый — 3,5; охру сухую — 1,0. Сухую бумажную.массу заливают теплым раствором столярного клея, добавляют при постоянном помешивании мел, глицерин, спирт и охру. После тщательного перемешивания полученная масса не должна прилипать к рукам. Дальнейший процесс аналогичен приготовлению и обработке «пластмассы» по 4-му или 5-му рецепту.
7-й рецепт. «Пластмасса» с хорошими изоляционными свойствами может быть приготовлена из 60 массовых частей творога и 40 — негашеной извести. Свежий творог заворачивают в чистую тряпочку и кладут на несколько часов под пресс, чтобы хорошо отжать. Отжатый творог растирают в порошок и высыпают в глубокий стеклянный сосуд, в другом сосуде растирают в тонкий порошок известь и высыпают ее небольшими порциями в творог, перетирая массу деревянной палочкой. Вступая в реакцию с известъю, творог образует казеиновую массу — густой «сироп», который быстро затвердевает. «Сироп» разливают по формам. Формы должны быть смазаны вазелином или маслом. Казеиновая «пластмасса» обладает большей прочностью, если она затвердевает под прессом.
Надо учитывать, что при плохом качестве негашеной -извести застывание массы происходит медленно и сопровождается обильным выделением влаги, излишки кото-рой нужно удалять. В этом случае следует уточнить со--- отношение компонентов опытным путем.
3-17. Окрашивание целлулоида и триацетатной пленки можно производить путем кипячения их в течение нескольких часов в воде, содержащей органический краситель типа анилинового для материи. Однако такой способ трудоемок и не всегда дает желаемый оттенок окраски. Одним из способов поверхностного крашения этих материалов является обработка их в горячем растворе уксусной кислоты, содержащем краситель. Если используют фотопленку, то ее предварительно обрабатывают веществами, разлагающими желатин, например горячим раствором щелочи. Отмывку эмульсии можно ускорить, очищая пленку щеткой. Количество красителей, вносимых в раствор, и ориентировочное время крашения приведены в табл. 3-1. Краситель заливают небольшим количеством кипяченой горячей воды и размешивают до получения однородной массы (пасты). Затем добавляют в пасту остальное количество горячей воды и 50 мл уксусной кислоты (95 %-ной). Вместо кислоты можно взять 60 мл уксусной эссенции и 940 мл воды или 550 мл столового уксуса (9 %-ного) и 450 мл воды. Раствор фильтруют через несколько слоев марли, сливают в эмалированную кастрюлю и закрывают ее крышкой.
Таблица 3-1
|
|
Поперечные профили набережных и береговой полосы: На городских территориях берегоукрепление проектируют с учетом технических и экономических требований, но особое значение придают эстетическим...
История развития хранилищ для нефти: Первые склады нефти появились в XVII веке. Они представляли собой землянные ямы-амбара глубиной 4…5 м...
Состав сооружений: решетки и песколовки: Решетки – это первое устройство в схеме очистных сооружений. Они представляют...
Кормораздатчик мобильный электрифицированный: схема и процесс работы устройства...
© cyberpedia.su 2017-2024 - Не является автором материалов. Исключительное право сохранено за автором текста.
Если вы не хотите, чтобы данный материал был у нас на сайте, перейдите по ссылке: Нарушение авторских прав. Мы поможем в написании вашей работы!