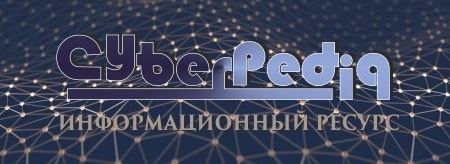
Историки об Елизавете Петровне: Елизавета попала между двумя встречными культурными течениями, воспитывалась среди новых европейских веяний и преданий...
Адаптации растений и животных к жизни в горах: Большое значение для жизни организмов в горах имеют степень расчленения, крутизна и экспозиционные различия склонов...
Топ:
Особенности труда и отдыха в условиях низких температур: К работам при низких температурах на открытом воздухе и в не отапливаемых помещениях допускаются лица не моложе 18 лет, прошедшие...
Устройство и оснащение процедурного кабинета: Решающая роль в обеспечении правильного лечения пациентов отводится процедурной медсестре...
Характеристика АТП и сварочно-жестяницкого участка: Транспорт в настоящее время является одной из важнейших отраслей народного...
Интересное:
Мероприятия для защиты от морозного пучения грунтов: Инженерная защита от морозного (криогенного) пучения грунтов необходима для легких малоэтажных зданий и других сооружений...
Подходы к решению темы фильма: Существует три основных типа исторического фильма, имеющих между собой много общего...
Национальное богатство страны и его составляющие: для оценки элементов национального богатства используются...
Дисциплины:
![]() |
![]() |
5.00
из
|
Заказать работу |
Содержание книги
Поиск на нашем сайте
|
|
Закон эксцентриситета (закон Рэлея)
Отражает распределение величин, характеризующихся их абсолютными значениями (т. е. без учета знака). К этим величинам относятся: эксцентриситет, биение, разностенность, отклонение от параллельности, отклонение от перпендикулярности.
Например, описывая формирование эксцентриситета втулки при двухмерном гауссовском распределении двух случайных величин х и у с параметрами хср = уср = rср = 0;
Рис. 45.4. Схема для определения параметров эксцентриситета
Рис. 45.5. Графическое изображение закона Рэлея
Закон распределения Рэлея однопараметрический (рис. 45.4):
Интегральный закон распределения эксцентриситета имеет следующий вид (рис. 45.5):
;
;
;
;
.
Закон распределения модуля разности
Рис. 45.6. Примеры отклонений расположения формы:
а - конусообразность; б - овальность
Отклонение расположения и формы определяется абсолютными значениями разности двух значений (овальность, конусообразность) (рис. 45.6).
Если две случайные величины х1 и х2 имеют нормальное распределение с параметрами , и
и
то модуль разности
этих величин r = |х, — х2 | имеет распределение, которое называется распределением модуля разности (рис. 45.7):
,
.
Рис. 45.7. Графическое изображение закона модуля разности
Производим в последнем уравнении замену:
СТРУКТУРА ПОЛЯ РАССЕЯНИЯ
Каждому виду обработки свойственна величина рассеяния, характеризуемая полем рассеяния W (рис. 48.1). Однако внутри данного вида обработки значение W изменяется и зависит от точности и жесткости станка.
Особое место занимает точность изготовления деталей, которая определяет близость к номинальному значению. Количественной мерой точности служит погрешность. Повышение точности, уменьшение погрешности приводит к увеличению надежности машин, уменьшает размеры припусков на обработку и способствует экономии материала.
|
Погрешности обработки подразделяют на пять видов:
• погрешность размеров;
• отклонение расположения поверхностей;
Рис. 48.1. Схема для определения структуры • отклонение формы;
поля рассеяния • волнистость поверхности;
• шероховатость.
Систематические составляющие (а0) погрешности остаются постоянными или закономерно изменяются. Например, отклонение размера блока концевых мер при измерении, изменение уровня настройки станка при износе инструмента и т.п.
Систематическая составляющая выражается математическим ожиданием М(х) = а0 = const или функцией М(х) = a(t), если изменяется в зависимости от случайного аргумента (например, времени /).
Величина этой составляющей определяется широтой рассеяния, которую принято измерять числом укладывающихся в ней средних квадратических отклонений ;
представляет собой среднее взвешенное по вероятностям значение случайной величины. Следуют напомнить, что «взвешивание» значений случайной величины означает умножение каждого значения на его «вес», т.е. на
, с последующим делением суммы произведений на сумму «весов»:
На рис. 48.1 представлена структура поля рассеяния погрешности обработки валов на токарном станке. К систематическим составляющим поля рассеяния относят:
1) среднее начальное значение систематической погрешности а0;
2) величину изменения систематической составляющей в рассматриваемом интервале
времени tn и tk. Здесь = 0,56 мкм/мин - скорость изменения мгновенного центра
рассеяния; Т = tk-tn= 42 — 8 = 34 - межналадочный период при изготовлении или диапазон изменения при измерении.
Случайная составляющая определяется средними квадратическими отклонениями:
|
• начальных погрешностей от их среднего значения;
• мгновенного рассеяния , т.е. рассеяния единичных значений параметра относительно изменяющегося по закону
от их мгновенных центров в пределах Т =
.
РАСЧЕТ РАЗМЕРНЫХ ЦЕПЕЙ
ПРИМЕР РАСЧЕТА НА МАКСИМУМ И МИНИМУМ
Для детали методом расчета на максимум и минимум (рис. 52.1) определить:
1) номинальный размер замыкающего звена А0;
2) величину его допуска ТА0;
3) верхнее предельное отклонение (ESA0) и нижнее предельное отклонение (ЕIА0);
4) координату середины допуска (ЕСА0).
1. =60 + 20-40-35 = 5 мм.
2. =0,16+ 0,3+ 0,13 + 0,16=0,75 мм.
3. =
=(0,0 + 0,13) - (0,0 + 0,0) = +0,13 мм.
=
=(-0,30 + 0) - (0,16 + 0,16) = -0,62 мм.
Предельные отклонения А4 звена
4. = 0,13 - 0,375 = -0,245 мм;
-0,62 + 0,375 = -0,245 мм.
НА МАКСИМУМ И МИНИМУМ
КЛАССИФИКАЦИЯ БАЗ
ПРИНЦИП СОВМЕЩЕНИЯ (ЕДИНСТВА) БАЗ
При назначении технологических баз для точной обработки заготовки в качестве технологических баз следует принимать поверхности, которые одновременно являются конструкторскими и измерительными базами детали, а также используются в качестве баз при сборке изделий.
При совмещении технологических, конструкторских и измерительных баз обработка заготовки осуществляется по размерам, проставленным в рабочем чертеже, с использованием всего поля допуска на размер, предусмотренного конструктором.
Если технологическая база не совпадает с конструкторской или измерительной базами, технолог вынужден производить замену размеров, проставленных в рабочих чертежах от конструкторских и измерительных баз, более удобными для обработки технологическими размерами, простав-
ленными непосредственно от технологических баз. При этом происходит удлинение соответствующих размерных цепей заготовки, и поля допусков на исходные размеры, проставленные от конструкторских баз, распределяются между вновь введенными промежуточными размерами, связывающими технологические базы с конструкторскими базами и с обрабатываемыми поверхностями. Это приводит к ужесточению допусков на размеры, выдерживаемые при обработке заготовок, к удорожанию процесса обработки и понижению его производительности.
При обработке паза на глубину 10 H I4 (рис. 56.1, а) для упрощения конструкции приспособления удобно установить заготовку на нижнюю поверхность В (рис. 56.1, г). Так как дно паза С связано размером 10+0,36 с верхней плоскостью А, эта плоскость является для паза конструкторской и измерительной базами. В данном случае технологическая база - поверхность В не совпадает с конструкторской и измерительной базами и не связана с ними ни размером, ни условием правильного взаимного расположения.
|
Рис. 56.1. Фрезерование паза от опорной технологической базы В, не совпадающей с конструкторской (а-г)
Поскольку при работе на настроенном станке расстояние от оси фрезы до плоскости стола сохраняется неизменным (к = const), а следовательно, постоянен и размер с, отсутствующий на чертеже, то размер глубины паза а = 10+0’36 мм не может быть выдержан, так как на его колебание непосредственно влияет погрешность размера мм, выдерживаемого на предыдущей операции (рис. 56.1, б). Очевидно, что на операционном эскизе фрезерования паза в таком случае следует поставить технологический размер с, точность которого не зависит от предыдущей операции, а конструкторский размер а = 10+0’36 мм целесообразно с эскиза снять.
Допуск размера с определяется из той же размерной цепи, в которой исходным размером является конструкторский размер а = 10+0’36, так как весь расчет производится на основании предпосылки, что размер а должен быть автоматически получен в пределах заданного конструктором допуска при выполнении составляющих размеров цепи b и с в пределах установленных для них допусков:
откуда
;
.
Подставляя соответствующие значения, получаем .
Так как допуск - величина существенно положительная и отрицательной быть не может, полученное уравнение не может быть решено без увеличения уменьшаемого или без уменьшения вычитаемого. Допуск размера задан конструктором и не может быть увеличен, поэтому единственным способом решения поставленной задачи является уменьшение вычитаемого, т.е. ужесточение допуска на размер
. Уменьшение
следует произвести таким образом, чтобы на размер
и на технологический размер с были установлены технологически выполнимые допуски. Так как с технологической точки зрения сложность выполнения размеров
и
одинакова (оба размера лежат в одном интервале размеров и получаются на горизонтально-фрезерном станке от опорной технологической базы), допуск размера
ужесточается до величины
- 0,18 мм, равной половине допуска исходного размера
. В этом случае на технологический размер с можно назначить допуск, близкий установленному допуску размера
|
Окончательно размер назначается с допуском, равным ближайшему стандартному с сохранением установленного чертежом минусового отклонения поля допуска от номинала, т.е
.
Тогда расчетный допуск технологического размера
Тс = 0,36 — 0,16 — 0,20 мм.
Предельные значения технологического размера с определяются из той же размерной цепи на рис. 56.1, в, т.е. а = - с:
;
мм;
;
мм.
Расчетная величина размера - Окончательно принимается ближайшее стандартное значение этого размера
соответствующее значению
.
Проверочный расчет на максимум и минимум: ;
показывает, что предельные значения исходного конструкторского размера а находятся в границах предельных размеров, установленных чертежом, и пересчет размеров сделан правильно.
В случаях, когда стандартный размер, ближайший к расчетному технологическому размеру с, значительно отличается по величине своего поля допуска от расчетного, окончательно может быть принят расчетный размер с.
На основании проведенного расчета в операционных эскизах заготовки вместо чертежных размеров и
должны быть проставлены новые размеры:
и
Таким образом, в связи с несовпадением технологической и конструкторской (измерительной) баз рабочему фактически приходится выдерживать заметно более жесткие допуски по сравнению с допусками, установленными конструктором. В рассмотренном случае вместо допусков по H 14, установленных чертежом, должны быть выдержаны допуски по h 11 и b 1 1.
Если столь значительное повышение требуемой точности обработки приведет к чрезмерному снижению производительности и возрастанию себестоимости продукции, то может оказаться целесообразным использовать специальное приспособление, позволяющее осуществить фрезерование паза непосредственно от конструкторской базы А.
ПРИНЦИП ПОСТОЯНСТВА БАЗ
Принцип заключается в том, что при разработке технологического процесса необходимо стремиться к использованию одной и той же технологической базы (не считая смены черновой базы), поскольку смена технологических баз увеличивает погрешность взаимного расположения поверхностей.
Пример. Требуется обеспечить совмещение оси четырех малых отверстий с осью центрального отверстия в пределах .Расточка центрального отверстия предусматривается на
|
Рис. 57.1. Применение принципа постоянства баз при расточке и сверлении
токарном станке, а сверление четырех малых отверстий в кондукторе (рис. 57.1). При использовании плоскостей A и В допуск не выполняется.
;
.
При использовании обеих операций от неизменной базы колебание величины укладывается в допуск .
При выполнении обеих операций от неизменной базы (от плоскости А), колебания величины смещений осей уменьшится, так как оно определяется из более короткой технологической размерной цепи.
Примечания.
8. Допускается несколько одноименных опор обозначать количеством их справа.
9. Допускаются отклонения от размеров графических обозначений, указанных на схеме.
ОБОЗНАЧЕНИЯ ОПОР, ЗАЖИМОВ
Виды технологичности
Виды технологичности определяются признаками, характеризующими область се проявления. По области проявления различают: производственную и эксплуатационную технологичность.
Производственная технологичность проявляется в сокращении средств и времени на конструкторскую и технологическую подготовку производства, процессы изготовления, в том числе контроля и испытаний.
Эксплуатационная технологичность конструкции изделий проявляется в сокращении времени и средств на техническое обслуживание и ремонт изделия.
Увеличением технологичности конструкции можно увеличить выпуск продукции при тех же средствах производства, трудоемкость сократить на 15—20 % и более, себестоимость их изготовления на 5-10 %. Недооценка технологичности конструкции часто приводит к необходимости корректирования рабочих чертежей после их составления, удлинению сроков подготовки и дополнительным издержкам производства.
Понятие технологичности конструкций распространяется не только на область производства, но и на область их эксплуатации. Конструкция машин должна быть удобной для обслуживания и ремонтопригодной, так как затраты на все виды ремонта часто превышают затраты на изготовление
новых изделий (стоимость изделия). Повышение ремонтопригодности изделия обеспечивается легкостью и удобством разборки и сборки, осуществлением принципа узловой смены и узлового ремонта элементов изделия, а также возможностью восстановления наиболее сложных деталей.
При конструировании машин необходимо предусматривать возможность использования технологических методов, обеспечивающих повышение надежности.
В настоящее время работа по улучшению технологичности конструкции изделия ведется в различных отраслях машиностроения. На основе обобщения и систематизации накапливаемых данных для конструкторов многими организациями создаются соответствующие нормативы, справочные и руководящие технические материалы.
Отработка конструкции изделия на технологичность осуществляется на всех стадиях разработки конструкторской документации, начиная с эскизного проекта до разработки рабочей документации для изготовления и испытания установочных серий и серийного или массового производства.
Исполнителями отработки конструкции на технологичность являются разработчики конструкторской и технологической документации, обеспечивающие технологичность конструкции изделия при его проектировании и осуществляющие как технологический контроль, так и подготовку и внесение изменений по ГОСТ 2.503-68 в конструкторскую документацию.
При отработке технологичности конструкции на стадии эскизного проекта производят:
1) выбор наиболее простой принципиальной схемы;
2) установление (по возможности) базовой конструкции, которая должна быть положена в основу проектируемого изделия;
3) унификацию сборочных единиц и основных деталей для проектируемого и находящегося в производстве изделия;
4) разбивку изделия на самостоятельные сборочные единицы;
5) обеспечение технологичности оригинальных деталей;
6) выбор рациональных заготовок для оригинальных деталей.
На стадии технического проекта определяются конструкция изделия и его сборочных единиц, а также конструктивная форма всех деталей. На этой стадии решаются основные вопросы технологичности заготовок, механической обработки и сборки:
• выбор наиболее простой конструкции сборочных единиц и деталей;
• выбор баз сборки;
• определение и расчет важнейших размерных цепей;
• обеспечение требований технологичности сборки (разбивка конструкции на самостоятельные замкнутые сборочные единицы);
• обеспечение технических требований механической обработки;
• обеспечение выполнения технологических требований, предъявляемых к форме и основным размерам заготовок.
На стадии разработки рабочей документации проводят доработку по всем вопросам технологичности конструкции каждой детали и всего изделия в целом, особое внимание обращается:
• на выбор технологических баз деталей (в соответствии с конструктивными базами и базами сборки);
• проверку правильности простановки размеров и назначения оптимальных допусков на основе размерного анализа и удовлетворения конструктивных и производственно-технологических требований;
• выбор наиболее дешевых и недефицитных материалов;
• ограничение номенклатуры применяемых профилей материалов;
• проверку соблюдения всех требований, предъявляемых к оформлению элементов конструкции заготовок (толщина стенок, радиусы переходов, уклоны, линии разъема и т. п.);
• проверку соблюдения требований, предъявляемых к технологичности элементов конструкции при механической обработке (доступность обработки, возможность входа и выхода инструментов, наличие надежных поверхностей для крепления деталей при механической обработке и т. д.);
• максимальную унификацию элементов конструкции (диаметров, резьб, шлицевых соединений, модулей и т. д.).
При изготовлении опытных образцов (опытной партии) конкретизируются условия обеспечения требований технологичности, в том числе использование типовых технологических процессов и средств технологического оснащения с учетом вида и масштаба производства.
При подготовке к выпуску установочной серии проверяется технологичность заготовок и оригинальных деталей с учетом применения минимально необходимого количества оснастки для их изготовления; при этом в чертежи должны быть внесены необходимые исправления ошибок, выявленных при испытании опытного образца.
При подготовке к серийному или массовому производству окончательно проверяется технологичность конструкции в соответствии с разрабатываемым рабочим технологическим процессом.
При тщательной отработке чертежей на предыдущих этапах исправления ошибок, выявленных при составлении рабочей документации, будут относительно невелики и коснутся главным образом простановки размеров.
Общие требования к технологичности конструкции деталей
1. Конфигурация детали должна представлять собой сочетание простых геометрических форм, обусловливающих применение высокопроизводительных технологических процессов и предусматривать удобную, надежную базу для установки заготовки в процессе ее обработки.
2. Заданные точность и шероховатость поверхности детали должны быть обоснованы ее служебным назначением. Необоснованно завышенные требования к точности и шероховатости вынуждают вводить дополнительные операции, удлиняют цикл обработки, увеличивают трудоемкость процесса обработки, повышают себестоимость.
3. Стандартизация и унификация деталей и их элементов уменьшает трудоемкость и себестоимость их изготовления в связи с увеличением серийности выпуска и унификацией станочных наладок (унификация - сокращение числа объектов одинакового функционального назначения).
Требования технологичности определяются методами обработки заготовок, применяемыми приемами обработки, оснасткой, а также типом производства.
Требования к технологичности классифицируются по видам технологических операций:
•заготовительных;
• механической обработки;
•термической и химико-термической обработки, а также методов упрочняющей обработки;
•сборочных операций.
Технологичность конструкции изделия - понятие относительное. Для одной и той же машины она будет разной для различных типов производства. Изделие технологичное в единичном производстве может быть малотехнологичным в поточном и совершенно нетехнологичным в поточноавтоматизированном производстве.
Технологичность конструкции одного и того же изделия будет разной для заводов с различными производственными возможностями. Если в единичном производстве используют станки с ПУ или другое переналаживаемое оборудование, то характеристика технологичности конструкций выпускаемых изделий может измениться по сравнению с условиями единичного производства, оснащенного универсальным оборудованием без ПУ. Развитие техники и технологии изменяет уровень технологичности конструкции. Ранее нетехнологичные конструкции могут стать технологичными при новых методах обработки.
Технологичность конструкции изделия - понятие комплексное. Она рассматривается во взаимной связи и с учетом условий выполнения заготовительных процессов, процессов механической обработки, сборки и контроля. Отработанная на технологичность конструкция заготовки не должна усложнять последующую механическую обработку. В то же время отработку на технологичность в конструкции детали следует производить не только в целях упрощения механической обработки, но и с учетом выполнения заготовительных процессов и сборки, стремясь получить минимальную себестоимость и трудоемкость изготовления машины в целом.
Общие требования заготовительных операций
Отверстия
1. Во избежание поломки сверл поверхности на входе и выходе инструмента должны быть перпендикулярны оси отверстия (рис. 60.5).
2. Необходимо предусматривать сквозные отверстия, так как их обработка значительно легче обработки глухих отверстий.
3. Конструкция глухих отверстий должна быть увязана с конструкцией применяемого осевого инструмента, например зенкера (рис. 60.6, а) или развертки (рис. 60.6, б).
4. Ось отверстия должна располагаться от вертикальной стенки детали не ближе определенного расстояния:
,
а для отверстий под соединительные болты:
,
где D - диаметр отверстия; - диаметр описанной окружности гайки; R - радиус переходной поверхности к поверхности фланца (рис. 60.7).
5. Расстояние между отверстиями необходимо назначать с учетом возможности применения многошпиндельных сверлильных головок; унифицировать расположение и размеры отверстий во фланцах в целях применения многошпиндельных головок.
6. Количество отверстий во фланцах выбирать таким, чтобы можно было сверлить их многошпиндельной головкой.
7. Для одновременной обработки нескольких отверстий, расположенных на одной оси, рекомендуется последовательно уменьшать размеры отверстий на величину, превышающую припуск на обработку предшествующего отверстия (ступенчатое расположение отверстий).
8. При сверлении отверстий в пазах назначать их диаметр меньше ширины пазов на 0,5 — 1,0 мм.
9. У дна точных глухих отверстий предусматривать канавку для выхода инструмента (рис. 60.8).
Рис. 60.7. Требования к технологичности
расположения оси отверстий относительно вертикальной стенки заготовки
Рис. 60.8. Требования к технологичности конструкции глухих отверстий
10. Избегать отверстий с непараллельными осями (рис. 60.9), а также глухих отверстий, пересекающихся с внутренними полостями (рис. 60.10), предпочтительнее делать сквозное отверстие с заглушкой.
a в
Рис. 60.9. Требования к технологичности расположения осей отверстий:
а - нетехнологично; б - технологично
Рис. 60.10. Требования к технологичности пересекающихся отверстий:
а - нетехнологично; б - технологично
а б
Рис. 60.11. Требования к технологичности цекуемых торцов отверстий:
а - нетехнологично; б - технологично
Рис. 60.12. Требования к технологичности канавок в отверстиях
П.Цекование торцов отверстий лучше делать точением или фрезерованием (рис. 60.11).
12. Избегать растачивания канавок в отверстиях, обрабатываемых на сверлильных и агрегатных станках, так как это усложняет обработку (рис. 60.12)
Резьбы
Рис. 60.13. Требования к технологичности заходной фаски на нарезаемом отверстии
1. Рекомендуется на нарезаемом отверстии применять заходную фаску (рис. 60.13).
2. Резьба должна быть нормализована не только для данной машины, но и для всего завода или данной отрасли промышленности
3. Следует избегать применения резьб малого диаметра ( 6 мм) в круглых деталях ввиду частой поломки метчиков при механическом нарезании таких резьб.
4. При нарезании резьбы на концах валиков надо предусматривать сбег резьбы.
5. Конструкция отверстия с резьбой должна давать возможность работать резьбовым инструментом на проход (рис. 60.14).
а б в г
Рис. 60.14. Требования к технологичности резьб в отверстии: а, в - нетехнологично; б, г - технологично
Плоскости
1. Конфигурация обрабатываемых плоскостей в плане должна обеспечивать равномерный и безударный съем стружки.
2. Размеры плоскости (ширину) необходимо увязывать с нормальным рядом диаметров торцов или длин цилиндрических фрез.
Puc. 60.15. Требования к технологичности конструкции плоских поверхностей при обработке
плоскости на проход (а-г)
3. Необходима предварительная обработка плоскостей на проход (рис. 60.15, а).
4. В случае, когда не предусмотрен выход для режущего инструмента, переходная часть обрабатываемых плоскостей должна соответствовать размерам и виду поверхностей режущего инструмента (рис. 60.15, б).
5. Плоскости бобышек и площадок на деталях следует располагать на одном уровне (рис. 60.15, в). При этом необходимо избегать обработки закрытых площадок (внутри корпусных деталей).
6. Обрабатываемые плоскости желательно располагать выше примыкающих элементов (ребер, выступов), это облегчает обработку на проход (рис. 60.15, г).
Фасонные поверхности
а б
1. Радиусы вогнутых и выгнутых поверхностей увязывают с размерами нормальных фрез.
2. Конструкция вогнутой сферической поверхности должна предусматривать сквозное или глухое отверстие, чтобы при ее обработке не было нулевых скоростей резания (рис. 60.16).
Рис. 60.16. Требования к технологичности конструкции вогнутой сферической формы: а - сквозное отверстие; б - глухое отверстие
Пазы и гнезда
1. Пазы должны по возможности допускать обработку на проход.
2. Предпочтительны пазы, обрабатываемые дисковыми, а не концевыми фрезами (рис. 60.17).
Рис. 60.17. Требования к технологичности формы пазов:
а - нетехнологично; б – технологично
Рис. 60.18. Требования к технологичности радиусов закруглений у гнезд выемок
3. Глубину и ширину пазов выбирают в соответствии с размерами нормальных пазовых фрез.
4. Радиусы закруглений у гнезд выемок должны быть одинаковыми по всему контуру обрабатываемой поверхности и соответствовать размерам нормальных пазовых фрез (рис. 60.18). Приведенные правила и рекомендации носят общий характер. Для деталей, обрабатываемых на станках с ПУ, агрегатных станках, автоматических линиях существуют дополнительные рекомендации.
Корпусные детали
1. Корпусные детали должны иметь хорошо развитые опорные технологические базы, обеспечивающие надежное жесткое крепление детали в процессе механической обработки с расположением этих баз в одной плоскости.
2. При наличии соосных отверстий на нескольких осях целесообразно предусматривать убывание диаметров отверстий в одном направлении на всех осях. Отверстие в детали (рис. 60.19) можно обрабатывать только с поворотом детали, сначала обрабатывают отверстия, расположенные на одной оси, после поворота - отверстия, расположенные на другой оси. Поворот детали увеличивает погрешность в относительном расположении отверстия. В технологичной конструкции этот недостаток устранен.
а 6
Рис. 60.19. Требования к технологичности к конструкций соосных отверстий:
а - нетехнологично; б - технологично
3. Внутренние торцевые поверхности должны быть легко доступны для обработки (рис. 60.20). Внутренний торец 1 обрабатывается через отверстие 2 зенкером, насаживаемым на оправку, что при небольшом отверстии 2 менее производительно. С увеличением диаметра отверстия указанный торец можно обрабатывать на предварительно настроенном станке с высокой производительностью.
Рис. 60.20. Требования к технологичности конструкции внутренних торцовых поверхностей:
а-нетехнологично; б—технологично
Общие требования термической и химико-термической обработки
Качественная оценка
Характеризует технологичность конструкции обобщенно, на основании опыта исполнителя и допускается на всех стадиях проектирования.
При качественной оценке технологичности конструкции:
1) обращают внимание на обрабатываемость, стоимость и дефицитность материалов детали;
2) определяют возможность применения легкого, но более прочного материала или улучшения физико-механических свойств имеющегося;
3) предусматривают максимальное количество поверхностей без последующей обработки;
4) учитывают, что конструкция детали должна предусматривать применение высокопроизводительного инструмента и оборудования;
5) анализируют простановку размеров на чертеже детали (связь между конструкторскими, технологическими и измерительными базами и возможность их совмещения). Обращают вним
|
|
Архитектура электронного правительства: Единая архитектура – это методологический подход при создании системы управления государства, который строится...
Индивидуальные и групповые автопоилки: для животных. Схемы и конструкции...
Таксономические единицы (категории) растений: Каждая система классификации состоит из определённых соподчиненных друг другу...
Индивидуальные очистные сооружения: К классу индивидуальных очистных сооружений относят сооружения, пропускная способность которых...
© cyberpedia.su 2017-2024 - Не является автором материалов. Исключительное право сохранено за автором текста.
Если вы не хотите, чтобы данный материал был у нас на сайте, перейдите по ссылке: Нарушение авторских прав. Мы поможем в написании вашей работы!