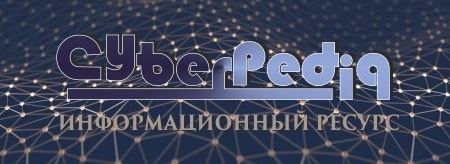
Общие условия выбора системы дренажа: Система дренажа выбирается в зависимости от характера защищаемого...
Наброски и зарисовки растений, плодов, цветов: Освоить конструктивное построение структуры дерева через зарисовки отдельных деревьев, группы деревьев...
Топ:
Организация стока поверхностных вод: Наибольшее количество влаги на земном шаре испаряется с поверхности морей и океанов...
Эволюция кровеносной системы позвоночных животных: Биологическая эволюция – необратимый процесс исторического развития живой природы...
Интересное:
Национальное богатство страны и его составляющие: для оценки элементов национального богатства используются...
Что нужно делать при лейкемии: Прежде всего, необходимо выяснить, не страдаете ли вы каким-либо душевным недугом...
Подходы к решению темы фильма: Существует три основных типа исторического фильма, имеющих между собой много общего...
Дисциплины:
![]() |
![]() |
5.00
из
|
Заказать работу |
|
|
Токарная обработка ступеней вала производится на универсаль-
ных, револьверных, одно- и многошпиндельных (автоматах и полуав- томатах), многорезцовых, токарно-копировальных станках и на стан- ках с ПУ. В условиях крупносерийного и массового производства применяются одно- и многошпиндельные прутковые автоматы для
обработки валов небольшого диаметра и l £1*0 мм. На автоматах
можно выполнить полную обработку вала, кроме наружного обтачи- вания и обработки осевого отверстия с одной стороны, можно осуще- ствить фрезерование лысок и сверление поперечного отверстия (при не вращающемся шпинделе). На дополнительной позиции, после от- резки, можно просверлить отверстие с другой стороны вала. Исполь- зуя специальные приспособления, можно фрезеровать шлицы, про- шивать фасонные отверстия, накатывать клейма и т.д. Обычно на ав- томатах и револьверных станках (серийное производство) обрабаты- вают валы без центровых отверстий с установкой заготовок в патрон.
Многошпиндельные вертикальные и горизонтальные полуавто- маты из-за высокой цены и сложности наладки находят применение только в массовом и крупносерийном производстве.
При обработке ступенчатых валов в крупносерийном и массо- вом производстве часто используют одношпиндельные многорезцо- вые (например, моделей 171*, 1721, 1А720, 1А730, А983 и А984) и гидрокопировальные (например, моделей 1708, 1712, 1713, 1719, 1722, 1Б732 и др.) полуавтоматы.
Точность обработки на вертикальных многошпиндельных полу- автоматах последовательного действия - 8¼9 квалитет, а параллель- ного - 11 квалитет. Использование одношпиндельных многорезцовых полуавтоматов на стадии предварительной обработки обеспечивает точность в пределах *1...1* квалитета, а чистовое течение - 11 квали- тет. Если при этом применяются чистовые «бреющие» резцы, то точ- ность повышается до 8¼9 квалитета, Аналогичную точность обеспе- чивает обработка на гидрокопировальных станках.
|
Точность многорезцовой обработки ниже из-за значительной погрешности наладки инструментов на размер (даже при использова- нии взаимозаменяемых державок), из-за неравномерного изнашива- ния резцов (автоматическую подналадку на размер осуществить не- возможно). Резцы, количество которых стремятся ограничить *0, вступают в работу в разное время, что приводит к большой и неоди- наковой во времени деформации системы. Несмотря на это, многорезцовая обработка эффективнее копировальной при обработке валов,
имеющих большие длину, диаметры и перепады ступеней. На много- резцовых станках обработку ведут, как правило, по методу деления длины, т.е. каждую шейку обрабатывают за один проход. Основное время обработки определяется по наибольшей длине хода лимити- рующего резца. Причем, многорезцовое обтачивание в любом вариан- те осуществления имеет, как правило, преимущества перед однорез- цовым обтачиванием не только в затратах основного (машинного) времени, но и вспомогательного времени. Однако подготовительно- заключительное время и время технического обслуживания на много- резцовых станках выше, чем на гидрокопировальных станках.
На гидрокопировальных станках точность несколько выше, т.к. они позволяют с автоматическим циклом выполнять одно- и много- проходную обработку наружных, внутренних и торцовых поверхно- стей деталей l = *0*¼700 мм и до l = 200* мм (на станку модели 1Б7*2) одним резцом, что снижает деформации и позволяет обтачи- вать валы невысокой жесткости.
На современных станках при одном установе можно вести чер- новую и чистовую обработку с использованием нескольких незави- симых копировальных и подрезных суппортов. На копировальных суппортах могут быть установлены револьверные державки с не- сколькими инструментами. Скорость резания почти в два раза выше, чем на многорезцовых станках. Копировальные станки могут быть оснащены устройствами для активного контроля размеров или адап- тивного управления для автоматической подналадки и смены инстру- мента, для загрузки и разгрузки заготовок, для программирования бесступенчатого изменения частоты вращения шпинделя и т.д.
|
При наладке инструмент устанавливают на одной шейке, а ос- тальные размеры обеспечивает копир, поэтому время наладки мало
(20¼40 мин.)
Наиболее характерные варианты обработки ступенчатых валов
токарных гидрокопировальных полуавтоматов:
- одним копировальным суппортом без использования подрез- ного суппорта в один или несколько проходов обрабатывают одну
сторону вала;
- аналогичная обработка, но с использованием двух копироваль-
ных суппортов;
- любой из первых двух вариантов, но с использованием одного
или двух подрезных суппортов для обработки канавок и торцевых по-
верхностей;
- многопроходная обработка вала с двух сторон при использова- нии двух копировальных суппортов с разным направлением рабочей подачи. Могут быть использованы (в случае необходимости и под- резные суппорты). При реализации этого варианта обработки приме- няют специальные торцовые поводковые патроны.
Современные токарные гидрокопировальные полуавтоматы за- частую производительнее многорезцовых токарных станков, хорошо приспособлены для встраивания в автоматические линии; их целесо- образно применять в серийном производстве при партии деталей бо- лее 10 шт. и в массовом производстве.
В связи с развитием силового шлифования обработку шеек же- стких ступенчатых валов нередко производят на круглошлифоваль- ных станках вместо предварительного многорезцового обтачивания. При заготовке, получаемой методом точной штамповки, снижается припуск на сторону до 2¼2,5 мм. Шлифование производят много- камневым кругом методом поперечной подачи на станках с автомати- ческим циклом.
В серийном и мелкосерийном производствах целесообразно производить обтачивание валов на токарных станках, оборудованных универсальными гидрокопировальными устройствами, например, на станка моделей КСТ-1, ГС-1, МГ*34 и др. Применение копироваль- ных устройств позволяет сократить в 2¼4 раза вспомогательное вре- мя, а штучное в 2¼3 раза по сравнению с обычными токарными станками и становится целесообразным при обработке партии из *¼* заготовок. Точность обработки в пределах 8¼9 квалитетов.
|
При обработке валов в центрах рекомендуется для выдержива- ния линейных размеров от постоянной базы применять плавающие передние центра с упором торца заготовки в упорное кольцо. Для по- вышения точности обработки и жесткости после закрепления детали рекомендуется закреплять и плавающий центр.
При единичном изготовлении валов заготовку получают отрез- кой от проката или свободной ковкой, в зависимости от конфигура- ции и размеров вала, а также от перепада диаметральных размеров ступеней. Токарные операции выполняются последовательной обра- боткой ступеней на обычных токарных станках. При этом зацентров- ку крупных валов производят по разметке, а обработку - с креплением в патроне и установкой другого конца вала в люнете. Для осуще-
ствления такой установки предварительно обрабатывают шейку под люнет, для чего вал устанавливают в патроне с поджимом задним центром.
Чтобы избежать специальной обработки под люнет, иногда для валов диаметром до 200 мм применяют специальные регулируемые муфты, которые закрепляют на необработанных шейках. Эти муфты служат для установки в люнеты. Причем, совмещение осей муфты и вала достигается регулировкой винтами, головки которых должны быть утоплены в тело фланцев муфты.
В мелкосерийном производстве применяются также токарные гидрокопировальные полуавтоматы, токарные станки обычного типа и с программным управлением (станки токарные моделей 16К20Ф3, 1А*1*Ф3, 1М63Ф3*, гидрокопировальные - 1Б732Ф3, 1712Ф3, 1*13Ф3 и др.), оснащенных или двумя суппортами с поворотными резцедержателями или револьверной головкой и суппортом. В зави- симости от выбранной схемы возможна последовательная, парал- лельная и параллельно-последовательная обработка. Обработку дета- лей на таких станках ведут по заранее составленной программе. Пе- реналадку на обработку другой детали можно осуществить быстро и достаточно просто. Эти станки позволяют вести обработку деталей в несколько проходов и в случае необходимости с изменением частоты вращения шпинделя. Наибольший эффект достигается при обработке сложных деталей с криволинейным профилем. В этом случае меньше время обработки в 1,5¼2 раза по сравнению с обработкой на универ- сальных станках, повышается качество деталей, уменьшается вероят- ность получения бракованных деталей. С целью повышения точности обработки вводится предискажение траектории движения режущего инструмента.
|
При использовании станков с ПУ требуется более высокая ква- лификация наладчиков и более низкая квалификация станочников, чем на обычных станках. Однако применение таких станков связано с увеличением трудоемкости проектирования операции, необходимо- стью применения точного режущего и вспомогательного инструмен- та, увеличением затрат на эксплуатацию оборудования. Поэтому не- обходимо определять экономическую целесообразность использова- ния станков с ПУ.
*.2.8 Обработка шпоночных пазов и шлицевых поверхностей
На валах
Обработка шпоночных канавок
Шпоночные канавки на валах и вообще в охватываемых деталях
изготовляются для призматических и сегментных шпонок.
Шпоночные канавки для призматических шпонок могут быть закрытыми с двух сторон (глухие), закрытыми с одной стороны и сквозными.
Шпоночные канавки изготовляются различными способами в зависимости от конфигурации канавки и вала, применяемого инстру- мента; они выполняются на горизонтально-фрезерных или на верти- кально-фрезерных станках общего назначения или специальных.
Сквозные и закрытые с одной стороны шпоночные канавки из- готовляются фрезерованием дисковыми фрезами (рис. 8.8, а). Фрезе- рование канавки производится за один-два прохода. Этот способ наи- более производителен и обеспечивает достаточную точность ширины канавки.
Основное время при фрезеровании дисковой фрезой шпоночной канавки - сквозной и крытые канавки с закруглениями на концах не могут выполняться этим способом; они изготовляются концевыми фрезами с продольной подачей за один или несколько проходов (рис. 8.8, б).
Фрезерование концевой фрезой за один проход производится та- ким образом, что сначала фреза при вертикальной подаче проходит на полную глубину канавки, а потом включается продольная подача, с которой шпоночная канавка фрезеруется на полную длину. При этом способе требуется мощный станок, прочное крепление фрезы и обиль- ное охлаждение. Вследствие того что фреза работает в основном своей периферической частью, диаметр которой после заточки несколько
уменьшается, в зависимости от числа переточек фреза дает неточный
|
размер канавки по ширине.
Применение этого способа ограничивает конфигурация канавок: закрытые канавки с закруглениями на концах не могут выполняться этим способом; они изготовляются концевыми фрезами с продольной подачей за один или несколько проходов (рис. 8.* б).
Фрезерование концевой фрезой за один проход производится таким образом, что сначала фреза при вертикальной подаче проходит на полную глубину канавки, а потом включается продольная подача, с которой шпоночная канавка фрезеруется на полную длину. При этом способе требуется мощный станок, прочное крепление фрезы и обильное охлаждение. Вследствие того что фреза работает в основ- ном своей периферической частью, диаметр которой после заточки несколько уменьшается, в зависимости от числа переточек фреза дает неточный размер канавки по ширине.
Для получения по ширине точных канавок применяются специ-
альные шпоночно-фрезерные станки с «маятниковой подачей», рабо- тающие концевыми двухспиральными фрезами с лобовыми режущи- ми кромками. При этом способе фреза врезается на 0,*¼0,3 мм и фре- зерует канавку на всю длину, затем опять врезается на ту же глубину, как и в предыдущем случае, и фрезерует канавку опять на всю длину, но в другом направлении (рис. 8.8 в). Отсюда и происходит определе- ние метода - «маятниковая подача».
Этот метод является наиболее рациональным для изготовления шпоночных канавок в серийном и массовом производствах, так как дает вполне точную канавку, обеспечивающую взаимозаменяемость в шпоночном соединении. Кроме того, поскольку фреза работает лобо- вой частью, она будет долговечнее, так как изнашивается не перифе- рийная часть ее, а лобовая. Недостатком этого способа является зна- чительно большая затрата времени на изготовление канавки по срав- нению с фрезерованием за один проход и тем более с фрезерованием дисковой фрезой. Отсюда вытекает следующее: 1) метод маятниковой подачи надо применять при изготовлении канавок, требующих взаи- мозаменяемости; 2) фрезеровать канавки в один проход нужно в тех случаях, когда допускается пригонка шпонок по канавкам.
Сквозные шпоночные канавки валов можно обрабатывать на строгальных станках. Канавки на длинных валах, например на ходо- вом вале токарного станка, строгают на продольно-строгальном стан- ке. Канавки на коротких валах строгают на поперечно-строгальном
станке - преимущественно в индивидуальном и мелкосерийном про-
изводстве.
Шпоночные канавки под сегментные шпонки изготовляются
фрезерованием с помощью концевых дисковых фрез (рис. 8.8 г).
Шпоночные канавки в отверстиях втулок зубчатых колес, шки- вов и других деталей, надевающихся на вал со шпонкой, обрабатыва- ются в единичном и мелкосерийном производствах на долбежных стан- ках, в крупносерийном и массовом - на протяжных станках. На рис. 8.* показано протягивание шпоночной канавки в заготовке зубчатого колеса на горизонтально-протяжном станке.
Заготовка насаживается на направляющий палец *, внутри кото- рого имеется паз для направления протяжки 2. Когда канавка протя- гивается за 2 - 3 прохода, то под протяжку помещают подкладку 3.
Обработка шлицевых поверхностей
В шлицевых соединениях сопряженные детали центрируются
тремя способами:
1) центрированием втулки (или зубчатого колеса) по наружному
диаметру шлицевых выступов вала;
2) центрированием втулки (или зубчатого колеса) по внутреннему
диаметру шлицев вала (т. е. по дну впадин);
3) центрированием втулки (или зубчатого колеса) по боковым сто- ронам шлицев.
Форма шлицев бывает прямоугольная, эвольвентная и треуголь- ная.
Шлицевые соединения широко применяются в машиностроении (станкостроении, автомобиле- и тракторостроении и других отраслях) для неподвижных и подвижных посадок.
Технологический процесс изготовления шлицев валов зависит от того, какой принят способ центрирования вала и втулки. Наиболее ггочным является способ центрирования по внутреннему диаметру шлицев вала; он применяется, например, в станкостроительной и реже в автомобильной промышленности. Центрирование по наружному диа- метру шлицевых выступов вала встречается довольно часто, этот спо- соб применяется в тракторостроении, в автомобилестроении, а также в станкостроении и др. Центрирование по боковым сторонам шлицев применяют сравнительно редко. В автомобильной промышленности этот способ применяется для передачи больших крутящих моментов при наименьшем боковом зазоре.
Шлицы на валах и других деталях изготовляются различными способами, к числу которых относятся: фрезерование с последующим шлифованием, накатывание (шлиценакатывание), протягивание, стро- гание (шлицестрогание).
Наиболее распространенным способом изготовления шлицев является фрезерование. Применение остальных способов имеет еще мало опыта; они весьма производительны, дают высокий технико-
экономический эффект и, таким образом, являются прогрессивными.
Применение их целесообразно в крупносерийном и массовом произ- водствах.
Фрезерование шлицев
Шлицы валов небольших диаметров (до 100 мм) обычно фрезе-
руют за один проход, больших диаметров за два прохода. Черновое фрезерование шлицев, в особенности больших диаметров, иногда производится фрезами на горизонтально-фрезерных станках, имею- щих делительные механизмы lп - величина перебега; lп = 2¼5 мм; i - число шлицев; h - высота
шлица, фрезеруемого в данном проходе, в мм; Dф - диаметр фрезы в мм; * м np = * z zn - продольная минутная подача; sz - подача на зуб фре-
зы в мм; z - число зубьев фрезы; п - число оборотов фрезы в минуту.
Фрезеровать шлицы можно способом, изображенным на рис. 8.10 б, позволяющим применять более дешевые фрезы, чем дисковые.
Более производительным способом является одновременное фрезерование двух шлицевых канавок двумя дисковыми фрезами специального профиля (рис. 8.10 в).
Чистовое фрезерование шлицев дисковыми фрезами произво- дится только в случае отсутствия специального станка или инстру- мента, так как оно не дает достаточной точности по шагу и ширине шлицев.
Более точное фрезерование шлицев производится методом об- катки при помощи шлицевой червячной фрезы (рис. 8.10 г). Фреза помимо вращательного движения имеет продольное перемещение вдоль оси нарезаемого вала. Этот способ является наиболее точным и наиболее производительным.
При центрировании втулки (или зубчатого колеса) по внутрен- нему диаметру шлицев вала как червячная, так и дисковая фреза должна иметь «усики», вырезающие канавки в основания шлица, что- бы не было заедания во внутренних углах; эти канавки необходимы также при шлифовании по боковым сторонам и внутреннему диамет- ру.
Шлифование шлицев
При центрировании шлицевых валов по наружному диаметру
шлифуют только наружную цилиндрическую поверхность вала на обычных кругло-шлифовальных станках; шлифование впадины (т.е. по внутреннему диаметру шлицев вала) и боковых сторон шлицев не при- меняется.
При центрировании шлицевых валов по внутреннему диаметру шлицев фрезерование последних дает точность обработки по внут- реннему диаметру до *,05¼0,06 мм, что не всегда является достаточ- ным для точной посадки.
Если шлицевые валы после чернового фрезерования прошли термическую обработку в виде улучшения или закалки, то после этого они не могут быть профрезерованы начисто; необходимо шлифовать по поверхностям впадины (т.е. по внутреннему диаметру) и боковых сторон шлицев. Наиболее производителен способ шлифования фа- сонным кругом (рис. 8.11 а), но при таком способе шлифовальный круг изнашивается неравномерно ввиду неодинаковой толщины сни- маемого слоя у боковых сторон и впадины вала, поэтому требуется частая правка круга. Несмотря на это, данный способ широко распро- странен в машиностроении.
Шлифовать шлицы можно в две отдельные операции (рис. 8.11 б); в первой шлифуют только впадины (по внутреннему диаметру), а во второй - боковые стороны шлицев. Для уменьшения износа шли- фовального круга после каждого хода стола вал поворачивается и, та- ким образом, шлифовальный круг обрабатывает впадины постепенно одну за другой. Обычно вал поворачивается автоматически после каждого двойного хода стола станка. Но такой способ шлифования ме-
нее производителен, чем первый.
Для объединения двух операций шлифования в одну применя- ются станки, на которых шлицы шлифуют одновременно тремя кру- гами; один шлифует впадину, а два других - боковые поверхности шлицев (рис. *.11 в).
На рис. *.12 дана схема правки тремя алмазаминому на каждый шлиц расположены радиально в сегментах 4 массив-
ного корпуса 1 накатной головки (рис. 8.13). При передвижении голов- ки по детали 3 свободно вращающиеся ролики 2, вдавливаясь в по- верхность вала, образуют на ней шлицы соответствующей профилю ролика формы. Все шлицы накатываются одновременно, без враще- ния детали.
На специальных станках для накатывания шлицев (рис. 8.14) на- катная головка 1 размещается на салазках, для которых направляю- щими служат валы 2 и 5, соединяющие две массивные стойки. Салаз- ки перемещаются приводом от гидроцилиндра, расположенного в зад- ней стойке. В передней стойке находится гидравлический зажимной патрон 4, в котором закрепляется обрабатываемая деталь 3. Каждый ролик независимо регулируется на требуемую высоту. Головка как са- мостоятельный узел снимается со станка, не нарушая расположения роликов. На смену роликов затрачивается 5¼10 мин, на наладку стан- ка - около *0 мин.
На таких станках наибольшее число накатываемых шлицев до- ходит до 18, наименьшее составляет 6¼8 (на валах диаметром 16 мм). Продольная подача до 15 мм/сек. Получаемая точность шлицев по шагу 0,04 мм, непрямолинейность не превышает 0,04 мм на *00 мм длины.
Основное время при накатывании шлицев определяется по фор-
муле
* o L l [ мин ], (8.8)
Sм
где L - длина накатываемых шлицев в мм; * - величина перебега роли-
ка в мм; Sм - минутная подача при накатывании в мм.
Процесс накатывания весьма производителен, так как все шлицы
накатываются одновременно, при малой затрате времени, с достаточно высокой точностью.
Протягивание и строгание шлицев
Одним из методов изготовления шлицев на поверхности валов или
подобных деталей является протягивание их на горизонтально-
протяжных станках с применением специального приспособления.
Для протягивания сквозных шлицев применяется специальная протяжка с ножами, профиль режущей части которых соответствует форме шлица. Каждый шлиц протягивается поочередно с помощью де- лительного устройства.
При протягивании несквозных шлицев используется блочная протяжка, в которой режущие зубья имеют независимое взаимное пе- ремещение в радиальном направлении.
В корпусе 1 блока устанавливаются по скользящей посадке но- жи 2 прямоугольного сечения. Форма режущей части ножа соответст- вует профилю шлица. Каждый нож имеет независимое перемещение вдоль паза блока. Поджимная планка 3 регулирует зазор, необходи- мый для скольжения ножей в блоке. Ползуны 6 соединяются с ножа- ми тягой 7; оси роликов 5 закреплены в ползунах 6; пружины 4 при помощи тяги 7 прижимают ролики к копирной линейке. В конце ра- бочего хода каждого ножа копир отводит ролик и выводит нож из об- рабатываемой детали. Ножи затачиваются в специальном приспособ- лении комплектно.
Процесс изготовления шлицев на валах (или других деталях) строганием (шлицестрогание) аналогичен процессу долбления зубьев зубчатых колес методом копирования с помощью многорезцовой го- ловки. В этом случае все шлицы также обрабатываются одновремен- но набором профильных резцов, число которых равно числу впадин обрабатываемого шлицевого вала. Обрабатываемая деталь, располо- женная вертикально, движется возвратно-поступательно; при каждом ходе вверх она входит внутрь неподвижной резцовой головки, в ради- альных пазах которой размещены резцы. Все резцы одновременно на- резают шлицы, получая радиальную подачу на двойной ход обраба- тываемой детали. При обратном ходе детали (вниз) резцы в головке отходят в радиальном направлении, чтобы избежать трения задних поверхностей резцов об обрабатываемую поверхность.
Процесс шлицестрогания весьма производителен и может быть
применен в крупносерийном и массовом производстве при очень большом выпуске одинаковых деталей, так как для каждого числа шлицев должен быть изготовлен комплект специальных резцов. Наи- более выгодно применять его для обработки шлицев с припуском под шлифование.
Изготовляются шлицестрогальные станки- полуавтоматы модели МА-4В, которые могут быть использованы как отдельно работающие станки или, что особенно эффективно, встро- енными в автоматическую линию.
Работа станочника на таких станках сводится лишь к установке и съему обрабатываемой детали. Все остальные движения, в том чис- ле отвод стружки из зоны резания, включение и выключение охлаж- дения, закрытие и открытие ограждения, автоматизированы.
Главное движение, движения подачи и отвода резцов осуществ- ляются гидравлическим приводом. Зажатие заготовки в центрах про- изводится гидроцилиндром. Для установки и съема резцовой головки станки имеют подъемное устройство.
На станках указанной модели можно обрабатывать валы со сквозными и глухими шлицами диаметром от 25 до 60 мм при длине
прорезаемой впадины от *0 до 370 мм и наибольшей глубине 3,5 мм.
Расстояние между центрами станка *45 мм; скорость рабочего хода 2* м/мин, обратного 28 м/мин, диапазон бесступенчатых подач 0,03¼0,** мм/дв. ход; номинальная тяговая сила станков 294*0 Н; мощность электродвигателя главного привода 14 квт, число оборотов в минуту 1000.
Весьма производительным методом обработки шлицев является одновременное долбление всех впадин шлицев специальной много- резцовой головкой.
Обработка шлицевых отверстий
Обработка шлицевых поверхностей в отверстиях втулок, зубча-
тых колес и других деталей производится обычно протягиванием. Сначала отверстие и иногда торец обрабатываются предварительно, потом отверстие протягивается круглой протяжкой и затем шлицевой протяжкой - обычной или прогрессивной.
Шлицевые отверстия диаметром до *0 мм протягиваются обыч- но одной комбинированной протяжкой.
Если втулка или зубчатое колесо подвергается термической об- работке, то после этого на внутришлифовальном станке шлифуется
цилиндрическая поверхность отверстия, которая сопрягается с дном
впадины шлицев вала (при центрировании по внутреннему диаметру шлицев вала).
Протягивание винтовых шлицев отверстий (рис. 8.16) отличает- ся от протягивания обычных отверстий тем, что в процессе работы движение режущих кромок зубьев протяжки должно осуществляться по винтовой линии, что достигается сочетанием поступательного и вращательного движений двумя способами. Первый способ - оба движения сообщаются протяжке при неподвижной детали.
Второй способ - поступательное движение сообщается протяж- ке, а вращательное - детали.
Вращательное движение протяжки можно получить или непо- средственно путем самовращения ее силами резания, или принуди- тельно специальным механизмом.
Самовращение протяжки применяется при небольших углах на- клона на винтовой линии шлицев (до 1*°) и невысоких требованиях к точности шага.
Как указано выше, принудительное вращение может быть сооб- щено или протяжке, или детали. Механизмы для вращения протяжки являются конструктивно более простыми, чем механизмы для враще- ния детали.
При небольших отверстиях вращение протяжки осуществляется двумя пальцами 2 (рис. 8.*6 а), входящими в канавки протяжки 4. Пальцы размещаются во втулке 3, которая закреплена в опорном кольце * приспособления. Протяжка 4 соединяется со шпинделем станка патроном 5. При отверстиях больших размеров (d> 15 мм) вращение протяжки происходит благодаря выступам в отверстии спе- циальной гайки 2 (рис. 8.16 б), которые входят в направляющие пазы протяжки *. Гайка 2 закреплена в опорном кольце 1 приспособления. Протяжка 3 соединяется патроном 4 со шпинделем станка.
На рис. 8.1* в показана схема протягивания винтовых шлицев с помощью копирной линейки. В суппорте станка устанавливают рейку 2, сцепляемую с зубчатым колесом *. Одним концом рейка 2 через ролик прижимается к копирной линейке 1, закрепленной на станине
под углом а, определяемым по формуле
* g ap D,
T
где * - диаметр начальной окружности колеса 3, Т - шаг протягивае-
мых винтовых шлицев.
Изменяя угол установки копирной линейки, можно протягивать
винтовые шлицы с различными значениями шага Т.
При продольном перемещении протяжки 4 она одновременно будет вращаться с зубчатым колесом 3 от передвигающейся рейки 2. Простой способ протягивания внутренних винтовых шлицев основан на свободном вращении заготовки 1 (рис. 8.16 г) от самой протяжки 2 с винтовыми зубьями при ее поступательном движении. Свободное вращение заготовки от протяжки обеспечивается шариковой опорой 3.
Контроль шлицевых валов и отверстий
В шлицевых валах проверяются следующие элементы:
1) наружный или внутренний диаметр в зависимости от посадки
детали (втулки, зубчатого колеса и др.) - по наружному или внутрен- нему диаметру шлицевого вала. Наружный диаметр проверяется обыкновенной предельной скобой; внутренний диаметр можно изме- рять микрометром, специальной скобой и индикаторной скобой. У индикаторной скобы шпилька А (рис. 8.*7 а) устанавливается по на- ружному диаметру, что дает возможность быстрее измерять диаметр впадины. Нулевое положение индикатора устанавливается по измери- тельным плиткам или по эталону. Отклонение стрелки определяет действительный размер.
2) Толщина шлицев (выступов) проверяется предельными ско- бами (рис. 8.*7 б).
3) Шлицевой вал на биение по внутреннему диаметру проверя- ется индикатором; проверяются также конусность и спиральность, для чего индикатор перемещается параллельно оси, а вал предвари- тельна устанавливается горизонтально (рис. 8.1* в).
4) Расположение шлицев по окружности проверяется специаль- ным шлицевым кольцом (рис. 8.17 г).
*) Профиль поверхности впадины шлицевых валов (по внутрен-
нему диаметру) проверяется при помощи специальных шаблонов.
Универсальный прибор с делительной головкой позволяет про- верить все элементы шлицевых валов: шаг, расположение шлицев по окружности и др.
Контроль шлицевых отверстий обычно производится шлицевой пробкой.
|
|
История развития хранилищ для нефти: Первые склады нефти появились в XVII веке. Они представляли собой землянные ямы-амбара глубиной 4…5 м...
Историки об Елизавете Петровне: Елизавета попала между двумя встречными культурными течениями, воспитывалась среди новых европейских веяний и преданий...
Адаптации растений и животных к жизни в горах: Большое значение для жизни организмов в горах имеют степень расчленения, крутизна и экспозиционные различия склонов...
Биохимия спиртового брожения: Основу технологии получения пива составляет спиртовое брожение, - при котором сахар превращается...
© cyberpedia.su 2017-2024 - Не является автором материалов. Исключительное право сохранено за автором текста.
Если вы не хотите, чтобы данный материал был у нас на сайте, перейдите по ссылке: Нарушение авторских прав. Мы поможем в написании вашей работы!