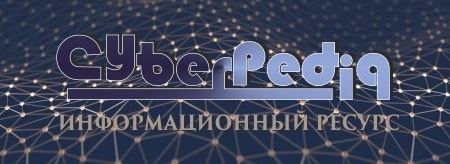
Эмиссия газов от очистных сооружений канализации: В последние годы внимание мирового сообщества сосредоточено на экологических проблемах...
Поперечные профили набережных и береговой полосы: На городских территориях берегоукрепление проектируют с учетом технических и экономических требований, но особое значение придают эстетическим...
Топ:
Выпускная квалификационная работа: Основная часть ВКР, как правило, состоит из двух-трех глав, каждая из которых, в свою очередь...
Организация стока поверхностных вод: Наибольшее количество влаги на земном шаре испаряется с поверхности морей и океанов...
Отражение на счетах бухгалтерского учета процесса приобретения: Процесс заготовления представляет систему экономических событий, включающих приобретение организацией у поставщиков сырья...
Интересное:
Национальное богатство страны и его составляющие: для оценки элементов национального богатства используются...
Лечение прогрессирующих форм рака: Одним из наиболее важных достижений экспериментальной химиотерапии опухолей, начатой в 60-х и реализованной в 70-х годах, является...
Как мы говорим и как мы слушаем: общение можно сравнить с огромным зонтиком, под которым скрыто все...
Дисциплины:
![]() |
![]() |
5.00
из
|
Заказать работу |
|
|
Технология производства машин, станков и механизмов в на-
стоящее время развивается по трем основным направлениям:
1) ускорение производственных процессов на основе внедрения
поточного производства;
2) разработка и внедрение новых высокопроизводительных про- цессов и методов обработки и совершенствование существующих, обеспечивающих высокое качество изделий, их износостойкость и
долговечность на уровне лучших мировых образцов;
3) повышение уровня механизации и автоматизации производ- ственных процессов, в первую очередь связанных с тяжелым, вред- ным и утомительным трудом.
Совершенствование процессов изготовления заготовок в литей- ных цехах должно идти в направлении значительного расширения производства отливок повышенной точности, включая отливки в формы, спрессованные под высоким удельным давлением, по вы- плавляемым моделям, в корковые формы, в кокиль, центробежное ли- тье и литье под давлением, а также с применением быстродействую- щих смесей.
Методы изготовления заготовок в кузнечнопрессовых цехах за- водов должны совершенствоваться путем внедрения безоблойной штамповки, штамповки на кривошипных горячештамповочных прес- сах и горизонтально-ковочных машинах, точной радиальной ковки, резки заготовок на пресс-ножницах, профилирование заготовок на вальцах.
Совершенствование изготовления заготовок, как в литейных це- хах, так и в кузнечнопрессовых неотделимо от значительного повы- шения уровня механизации и автоматизации производственных про- цессов.
Совершенствование процессов сварочного производства долж- но предусматривать расширение применения автоматической и полу- автоматической сварки под слоем флюса и в среде углекислого газа, электрошлаковой, точечной и рельефной сварки, а также сварки тре- нием.
|
Для механизации сварочных работ необходимо применять по- точные линии с устройствами для механизации сборочно-сварочных
работ и вспомогательных операций, а также механизированные сбо-
рочно-сварочные стенды с применением механизированных зажимов.
Совершенствование технологических процессов термической
обработки предусматривает:
- внедрение химико-термической; обработки (азотирование, це- ментация, закалка ТВЧ) непосредственно в технологические потоки изготовления отдельных деталей. (Контроль, приборы).
- внедрение комплексно-механизированных линий для закалки, отпуска, отжига и нормализации с применением манипулятора для за- грузки и выгрузки поддонов с деталями, внедрение закалочных стан- ков для термообработки ТВЧ различных деталей.
Совершенствование механической обработки предусматривает внедрение поточных методов и технологических процессов, повы- шающих точность и долговечность машин.
Внедрение поточных методов, (данные приводятся по станкоза- водам страны), обеспечивает улучшение всех технико-экономических показателей работы любого завода. Темпы роста производительности труда на заводах поточного производства значительно выше среднего темпа роста производительности труда по всем станкозаводам. Себе- стоимость продукции заводов с поточным производством примерно на 30...40% ниже себестоимости продукции всех остальных станкоза- водов.
Основной организационной формой серийного, мелкосерийного и единичного производства является создание предметно-замкнутых участков для обработки технологически подобных деталей. Эта фор- ма организации позволяет применить методы поточного производства при изготовлении средних и мелких серий деталей путем внедрения групповых методов обработки, специализированного оборудования, налаженных станков, групповой оснастки.
|
Для длительного сохранения точности сельхозмашин, станков, машин необходимо провести комплекс мероприятий, включающих отработку конструкции на технологичность, ужесточение техниче- ских условий; повышение качества металла, применяемого для дета- лей; изменение технологии изготовления деталей и сборки сборочных единиц, а также ряд организационных мероприятий. Для этого необ-
ходимо:
- повышение величины контакта поверхностей, находящихся под нагрузкой до 65...75% и более, путем повышения точности обра-
ботки и снижения шероховатости поверхности до 0,63...0,16;
- повышение твердости рабочих поверхностей для чугунных де-
талей до НВ 450...5*0;
- сокращение влияния внутренних напряжений в деталях путем применения различного вида старения в процессе обработки, соответ- ствующих режимов резания, регламентирования усилий зажима дета-
лей, ограничения величин нагрева деталей в процессе резания;
- применение новых технологических схем обработки ответст- венных деталей, в частности, применение двух- и трехкратной обра- ботки деталей с введением термической обработки между этими эта-
пами;
- применение высокоточных станков для окончательной обра- ботки основных поверхностей ответственных деталей, оснащенных инструментами из твердых сплавов, шлифовальными кругами, при-
способлениями с тарированными зажимами;
- применение измерительных средств с разрешающей способно-
стью 0,3...0,5 мкм;
- применение специальных средств для транспортировки и хра- нения, исключающих деформацию и повреждение деталей.
Для повышения точности обработки, прежде всего, необходимо увеличить удельный вес станков для финишной обработки за счет уменьшения удельного веса станков для черновой и получистовой обработки.
Очевидно, что в связи с увеличением применения высокоточных станков на финишных операциях, наряду с повышением точности производства решается задача, повышения производительности труда станочников путем применения следующего высокопроизводительно-
го оборудования:
- многошпиндельных продольно-фрезерных станков (в том
числе для тонкого фрезерования);
- станков с программным управлением, агрегатно-расточных
станков для черновой и получистовой расточки корпусных деталей;
- многошпиндельных алмазно-расточных станков для чистовой
|
расточки корпусных и других деталей;
- расточных станков с автоматической сменой инструмента с
ПУ;
- сверлильных станков с ПУ;
- шлифовальных станков для силового и чистового шлифова-
ния;
- фрезерных станков с программным управлением;
- токарных многошпиндельных автоматов и полуавтоматов;
- станков для непрерывного протягивания.
При механической обработке необходимо реализовать следую-
щие решения:
1. Применение прогрессивных видов заготовок с максималь- ным приближением к размерам готовой детали.
2. Внедрение новых технологических схем обработки с приме- нением комплекта оборудования, обеспечивающего полную обработ- ку деталей в механических цехах без каких-либо доделочных и при- гоночных операций в процессе сборки.
3. Расширение применения многопредметных, легкоперенала- живаемых поточных линий с укомплектованием их оборудованием для комплексной обработки деталей по всем операциям.
4. Насыщение переменно-поточных линий многопозиционной и многоместной легкопереналаживаемой групповой оснасткой с гид- равлическим или пневматическим зажимом деталей. Широкое приме- нение в мелкосерийном производстве групповых переналаживаемых приспособлений, УСП, УСПК, УСПШ.
5. Применение специального (преимущественно агрегатиро- ванного), специализированного и модернизированного универсально- го металлорежущего оборудования, автоматов и полуавтоматов, а также расширение применения прецизионного оборудования на фи- нишных операциях.
*. Более широкое применение методов групповой обработки, в первую очередь, на деталях подлежащих обработке на станках авто- матно-револьверной группы, а также на деталях общего назначения: шестернях, шкивах, фланцах и т.д.
7. Введение раздельной обработки в трех зонах: черновой, по- лучистовой и окончательной с промежуточной термообработкой де- талей.
8. Более широкое применение процессов шлифования для фи- нишной обработки шлицевых валов, кулачковых муфт, нарезки резь- бы на шпинделях, подготовки базовых центров под финишную опе- рацию круглого наружного шлифования.
9. Широкое применение высокопроизводительного и стойкого твердосплавного и алмазного инструмента для черновых, обдирочных и финишных отделочных операций.
|
10. Внедрение прерывистого шлифования, исключающего на- грев и деформацию обрабатываемой детали.
Для повышения эффективности механического производства
важное значение имеет освоение станков с программным управлени- ем.
Технология сборки должна совершенствоваться следующим пу-
тем:
- применением поточных методов сборки для крупносерийного производства с применением конвейеров на общей и узловой сборках и специализированных рабочих мест - для групповой сборки мелких
сборочных единиц; - применения групповых методов сборки в условиях мелкосе-
рийного производства; повышения уровня механизации сборочных работ за счет большего применения ручного механизированного ин- струмента, механизированных сборочных стендов, приспособлений с механизированными зажимами, применения холодильных и нагрева- тельных установок при сборке соединений с натягом.
20-22 Методы достижения точности замыкающего звена размерной цепи
Обеспечение точности создаваемой машины сводится к дости-
жению требуемой точности замыкающих звеньев размерных цепей, заложенных в ее конструкцию, и размерных цепей, возникающих в процессе изготовления машины. Задача обеспечения требуемой точ- ности замыкающего звена в зависимости от предъявляемых к нему требований, типа и условий производства может быть решена эконо- мично одним из пяти методов: полной, неполной, групповой взаимоза- меняемости, пригонки или регулирования.
Метод полной взаимозаменяемости предусматривает сборку машин без какой-либо дополнительной обработки деталей с установ- кой и заменой любой детали без пригонки. При сборке по этому ме- тоду требуется более высокая точность изготовления деталей, специ- альное оборудование и оснастка.
Простейшим примером использования данного метода является достижение требуемой точности зазора при соединении электроламп и патронов, в которые они ввертываются при эксплуатации.
Преимуществами метода полной взаимозаменяемости являют-
ся:
- наибольшая простота достижения требуемой точности замы- кающего звена, так как построение размерной цепи сводится к про-
стому соединению всех составляющих ее звеньев;
- простота нормирования процессов во времени;
- возможность широкого использования основных преимуществ
кооперирования различных цехов и отдельных заводов для изготов-
ления деталей или сборочных единиц машин;
- возможность выполнения технологических процессов сборки рабочими, не обладающими высокой квалификацией, поскольку про- цесс сводится к простому соединению деталей.
|
Решение о применении сборки с полной взаимозаменяемостью должно базироваться на анализе работы механизмов и на технико- экономических расчетах. При этом основными факторами, ограничи- вающими использование этого метода сборки, являются требования применения точных методов обработки большого количества деталей,
сложных и точных приспособлений и контрольно-измерительных
приборов, что нерентабельно при небольшом объеме производства. Использование метода полной взаимозаменяемости целесообразно в массовом и крупносерийном производствах, в этом случае капиталь- ные затраты на оснащение производства окупаются большим количе- ством изготовляемых машин.
Границы применения метода полной взаимозаменяемости опре- деляют экономикой производства. В этом легко убедится, если рас- смотреть график (рис.2.5.), показывающий зависимость величины возможного брака в партии деталей в зависимости от установленной величины допуска на один из размеров детали.
Рассматривая кривую 1, можно видеть, что по мере уменьшения величины допуска количество выходящих за пределы поля допуска деталей увеличивается. Вначале этот процесс идет медленно (участок а-б), затем темп роста брака увеличивается (участок б-в), наконец при малых величинах допусков брак возрастает настолько резко (участок в-г), что обработка деталей становится неэкономичной и возможно появление сплошного брака.
В таких случаях для достижения высокой точности необходимо перейти на новый технологический процесс (кривая 2), а следова- тельно, большей частью и на новый вид оборудования. Однако изме- нение технологического процесса и особенно переход на новый вид оборудования, дающего более высокую точность, обычно связаны с
увеличением затрат и, следовательно, себестоимости изготовления детали (изделия).
Относительная себестоимость возрастает с уменьшением допус- ка по гиперболической кривой, т.к. новое дополнительное оборудова- ние обычно более дорогое и зачастую менее производительное.
Использование метода полной взаимозаменяемости является экономичным в условиях достижения высокой точности при помощи малозвенных размерных цепей. При этом решающее значение имеет также и количество изделий, подлежащих изготовлению. С увеличе- нием количества изделий возрастают возможности экономичного ис- пользования более дорогого, но и более производительного и точного оборудования, инструмента и другой технологической оснастки. Если величина допуска в производственных условиях, соответствующих этапу развития техники, оказывается не экономичной, то от использо- вания метода полной взаимозаменяемости приходится отказываться и переходить на другие методы.
Сущность метода неполной (частичной) взаимозаменяемости заключается в том, что требуемая точность замыкающего звена раз- мерной цепи достигается с некоторым, заранее обусловленным рис- ком путем включения в нее составляющих звеньев без выбора, подбо- ра или изменения их значений.
Преднамеренный риск выхода значений замыкающего звена за пределы допуска, определяемого условиями задачи, обычно незначи- телен. Однако этот риск позволяет расширить допуски составляющих звеньев в сравнении с их значениями, установленными при достиже- нии точности замыкающего звена методом полной взаимозаменяемо- сти. Эта возможность создается малой вероятностью возникновения крайних отклонений составляющих звеньев и попаданий таких откло- нений в одно изделие. Таким образом, метод основан на учете веро- ятностей отклонений размеров, составляющих размерную цепь.
Отличие рассматриваемого метода от предыдущего заключается в установлении больших по величине допусков на составляющие зве- нья, что делает изготовление деталей более экономичным. При этом идут на риск получения небольшого процента случаев выхода по- грешности замыкающего эвена размерной цепи за пределы установ- ленного допуска. В основе рассматриваемого метода лежит одно из известных положений теории вероятностей, по которому возможные сочетания крайних значений погрешностей всех составляющих размерную цепь звеньев встречаются несравненно реже, чем средних
значений, вследствие чего возможный процент изделий, имеющих выход погрешностей замыкающего звена за пределы требуемого до- пуска, обычно крайне мал.
Дополнительные затраты труда и средств на исправление не- большого количества изделий, вышедших за пределы допуска, в по- давляющем большинстве случаев малы, по сравнению с экономией труда и средств, получаемой за счет изготовления составляющих звеньев с большими величинами допусков.
Преимущества данного метода по сравнению с предыдущим возрастают по мере повышения требований к точности замыкающего звена и увеличения количества звеньев в размерной цепи.
Сущность метода групповой взаимозаменяемости (селектив- ной сборки), заключается в том, что требуемая точность исходного (замыкающего) звена достигается путем включения в размерную цепь составляющих звеньев, принадлежащих к одной из групп, на которые они предварительно разбиты.
Добавочные расходы, связанные с необходимостью измерения всех деталей точным измерительным инструментом вручную или ав- томатически с *opтировкой, хранением и доставкой деталей отдель- ными группами на сборку, должны окупаться за счет экономии, полу- чаемой от обработки деталей по широким, экономически достижи- мым допускам.
Обычно данный метод используется для достижения более вы- сокой точности замыкающих звеньев малозвенных размерных цепей в шарикоподшипниковой промышленности, в соединениях поршней и пальцев авиационных и автомобильных двигателей и т.д.
Сущность метода пригонки заключается в том, что требуемая точность замыкающего звена достигается в результате изменения ве- личины одного из заранее намеченных составляющих звеньев (ком- пенсатора) путем снятия с него необходимого слоя металла.
При этом на все составляющие звенья размерной цепи устанав- ливаются экономичные в данных производственных условиях допус- ки, что и является основным преимуществом этого метода.
Существенным недостатком метода является необходимость до- полнительных работ, связанных с пригонкой компенсаторов по «мес- ту», причем в подавляющем большинстве случаев эти работы выпол- няются вручную и требуют высокой квалификации рабочего.
Данный метод применим при изготовлении единичных изделий,
у которых при большом количестве звеньев в размерных цепях требу- ется обеспечить высокую точность замыкающего звена.
Сущность метода регулировки заключается в том, что требуе- мая точность замыкающего звена достигается путем изменения вели- чины заранее забранного компенсирующего звена 6eз снятия с него слоя материала.
Метод регулировки может осуществляться двумя путями:
- изменением положения одной из деталей (метод подвижных
компенсаторов);
- введением в размерную цепь специальной детали требуемого размера (метод неподвижного компенсатора, в том числе и метод шайб).
Метод регулировки имеет следующие преимущества:
- возможность достижения любой степени требуемой точности
замыкающего звена при экономичных допусках на все составляющие
звенья;
- отсутствие пригоночных работ;
- возможность периодически, а в ряде случаев - непрерывно и
автоматически сохранять требуемую точность замыкающего звена.
Данный метод эффективен при решении задач достижения вы- сокой точности замыкающего звена в многозвенных размерных це- пях, а также в таких размерных цепях, где имеются звенья, изменяю- щиеся по величине вследствие износа, колебаний температуры и т.д.
Недостатком метода регулировки является увеличение в некото- рых случаях количества деталей в машине.
Расчет прямой и обратной задачи методом полной взаимозаме-
няемости
При решении размерной цепи приходится иметь дело с двумя
видами задач:
1) Прямая - когда при известных величинах допуска и коор-
динаты его середины для замыкающего звена размерной цепи требу- ется определить величины допусков и координат их середин всех со- ставляющих звеньев размерной цепи.
2) Обратная задача - когда при известных величинах допус-
ков и координат их середин всех составляющих звеньев размерной цепи требуется определить допуск и координату его середины для за- мыкающего звена.
Если обратная задача имеет математически однозначное реше-
ние, то прямая задача имеет математически неоднозначное решение, т.к. уравнений для расчета, всегда меньше, чем неизвестных величин. Поэтому решение прямой задачи может быть однозначным только при совместном решении уравнения с другими техноэкономическими закономерностями.
Рассмотрим методики решения этих двух задач.
Обратная задача. Для ее решения Ивановым В.В. предложена
следующая методика. Построив схему размерной цепи, подсчитывают допуск замыкающего звена, для чего допуски увеличивающих и уменьшающих звеньев сводят в расчетную таблицу (+,-) руководству- ясь следующими правилами записи: для увеличивающих звеньев верхняя граница допуска записывается в колонку «+», а нижняя - в колонку «-», а для уменьшающих звеньев наоборот - нижняя граница допуска - в колонку «+», а верхняя - в колонку «-».
Причем, если при занесении в таблицу (+,-) значения верхних и нижних границ допусков увеличивающих звеньев берутся с теми же знаками, что и на чертеже, то для уменьшающих звеньев знак меняет- ся на обратный.
Затем производится алгебраическое суммирование величин по колонкам и в результате получаем для замыкающего звена верхнюю границу допуска (в колонке +) и нижнюю (в колонке -), причем уже со знаком границ допусков.
то есть, получен тот же результат, что и методом Иванова.
При решении прямой задачи, когда по замыкающему звену оп- ределяются составляющие звенья, на практике используются три спо-
соба распределения допусков:
1) Равномерное распределение допуска Т ∆ между составляю-
щими звеньями - способ равных допусков или принцип равных влия- ний, т.е. полагается, что все звенья в равной степени влияют на обра- зование погрешности замыкающего звена, и, следовательно, величи- ны их допусков могут быть равны. При этом условии средняя величи-
на допуска Тср определяется из формулы
Т ср Т ∆
* -1
где m - количество звеньев в размерной цепи.
Если эта средняя величина допуска оказывается экономически приемлемой в производственных условиях, то ее корректируют, учи- тывая трудности и экономику получения требуемой точности для ка- ждого из составляющих звеньев размерной цепи.
2) Способ назначения допусков на составляющие звенья, соот- ветствующие одному и тому же квалитету точности обработки - способ равной точности, т.е. в его основу положен принцип одинаковой
сложности изготовления всех размеров звеньев.
Сложность изготовления звеньев зависит от их номинальных размеров. Так при механической обработке проще получить размер
40-0,** , чем размер 400-0,05. Это видно из таблиц допусков. Поэтому в
основу построения таблиц допусков и посадок положена единица до-
пусков (ЕД), которая выражается следующей формулой
ЕД 0,53 d
где d - средний размер в мм той группы размеров, в которую входит
данный номинальный размер.
|
|
Кормораздатчик мобильный электрифицированный: схема и процесс работы устройства...
Состав сооружений: решетки и песколовки: Решетки – это первое устройство в схеме очистных сооружений. Они представляют...
Таксономические единицы (категории) растений: Каждая система классификации состоит из определённых соподчиненных друг другу...
Типы сооружений для обработки осадков: Септиками называются сооружения, в которых одновременно происходят осветление сточной жидкости...
© cyberpedia.su 2017-2024 - Не является автором материалов. Исключительное право сохранено за автором текста.
Если вы не хотите, чтобы данный материал был у нас на сайте, перейдите по ссылке: Нарушение авторских прав. Мы поможем в написании вашей работы!