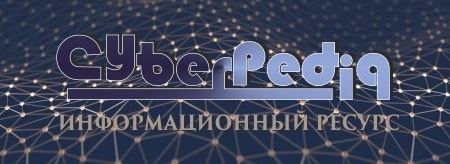
Автоматическое растормаживание колес: Тормозные устройства колес предназначены для уменьшения длины пробега и улучшения маневрирования ВС при...
История создания датчика движения: Первый прибор для обнаружения движения был изобретен немецким физиком Генрихом Герцем...
Топ:
Генеалогическое древо Султанов Османской империи: Османские правители, вначале, будучи еще бейлербеями Анатолии, женились на дочерях византийских императоров...
Оснащения врачебно-сестринской бригады.
Выпускная квалификационная работа: Основная часть ВКР, как правило, состоит из двух-трех глав, каждая из которых, в свою очередь...
Интересное:
Как мы говорим и как мы слушаем: общение можно сравнить с огромным зонтиком, под которым скрыто все...
Берегоукрепление оползневых склонов: На прибрежных склонах основной причиной развития оползневых процессов является подмыв водами рек естественных склонов...
Искусственное повышение поверхности территории: Варианты искусственного повышения поверхности территории необходимо выбирать на основе анализа следующих характеристик защищаемой территории...
Дисциплины:
![]() |
![]() |
5.00
из
|
Заказать работу |
|
|
Одной из традиционных расчетных задач, решаемых с помощью
средств вычислительной техники, является расчет припусков и опе- рационных размеров.
Определение припусков на обработку и допусков имеет важное технико-экономическое значение.
Завышенные припуски - это перерасход материала, увеличение трудоемкости. Однако, заниженные припуски - это ухудшение каче- ства и невозможность достижения требуемой точности и шероховато- сти поверхности. Величина припуска должна быть технически обос- нованной.
Общий припуск - это слой металла, необходимый для выполне- ния всей совокупности переходов от черновой обработки до готовой детали.
in
ZOå *i ,
i1
где Zi - припуск на обработку рассматриваемой поверхности на *-ой опе-
рации.
Существует три метода определения припусков.
Дифференциально-аналитический метод определения припусков яв-
ляется наиболее точным и базируется на анализе производственных по- грешностей, учитывает влияние на величину припуска конфигурации и размеров детали, качества заготовки, погрешностей, возникающих при ме- ханической и термической обработке. Общий вид формулы для определе- ния минимального припуска на обработку на i-ой операции можно пред-
ставить в виде:
Zmin k⋅ Rzi-1Ti-1ri-1ei,
i
где R*(i-1) - высота шероховатости неровностей профиля, мкм; T(i-1) -
глубина дефектного слоя на предшествующей операции (переходе),
мкм;r(i-1) - векторная сумма пространственных отклонений взаимо-
связанных поверхностей обрабатываемой заготовки, получившихся
на предшествующей операции;ei - векторная сумма погрешностей
|
базирования и закрепления; k - коэффициент, учитывающий характер
припуска (для односторонних припусков *=1, для симметричного k=2).
Метод широко применяется при автоматизации решения техно- логических задач, т.к. позволяет наиболее точно определять значения припусков и операционных размеров (снижение отходов металла в стружку на 20...50%).
Исходные данные:
- чертеж детали с техническими требованиями;
- метод получения заготовки;
- точность и качество заготовки;
- установочные базы; - тип приспособления;
- технологический маршрут обработки элементарной поверхно-
сти;
- вид термической обработки.
Алгоритм расчета припусков и операционных размеров с ис-
пользованием дифференциально-аналитического метода включает
следующие этапы:
* Ввод исходной информации.
2 Выбор или назначение технологического маршрута обработ-
ки i-ой элементарной поверхности.
3 Определение составляющих Rz(i-1), T(i-1),r(i-*),ei.
4 Расчет минимального припуска Zmini для i-ой операции.
* Определение допусков для соответствующих квалитетов, их
верхних и нижних отклонений для каждой i-ой операции.
6 Расчет максимальных, общих и номинальных припусков на все операции.
7 Расчет минимальных и максимальных размеров обрабатывае- мых поверхностей по всем операциям.
Автоматизация расчета припусков этим методом затруднена ис- пользованием большого объема справочно-нормативной информации в зависимости от конкретных условий обработки.
Нормативный метод определения припусков (опытно- статистический) является основным методом назначения припусков при неавтоматизированном проектировании. В его основе лежит ис-
пользование нормативных таблиц. Припуск устанавливается на осно-
вании опытных данных о фактических припусках, при которых про- изводилась обработка аналогичных заготовок. Большой объем норма- тивных таблиц сдерживает применение этого метода в САПР ТП.
Интегрально-аналитический метод определения припусков ос-
|
нован на использовании эмпирических уравнений следующего типа:
Z*in a b⋅ Dm *⋅ *n,
i
где коэффициент a представляет собой часть припуска, которую не-
обходимо снять, чтобы удалить дефектный слой T(i-1) и микронеров-
ности Rz(i-1).
Сумма b⋅ Dm *⋅ Ln соответствует части припуска, которая
вводится для компенсации неравномерности, обусловленной про-
странственными отклонениями отдельных участков обрабатываемой
поверхности и зависящей от габаритных размеров заготовки D и *.
Коэффициенты a, b, c и показатели степени m и n определялись путем обработки данных справочно-нормативных таблиц операцион- ных припусков с использованием метода наименьших квадратов.
Этот подход позволил установить эмпирические зависимости
типа Zmin=*(D, L) для определения минимальных операционных при-
пусков для различных поверхностей и методов обработки.
Вычисление припусков (рис. 7.14) начинается с последней К-ой операции. Определяется минимальный диаметр детали после выпол-
нения К-ой операции Dmin (оператор 3), затем определяется припуск
Zmin * для i-ой операции по зависимостям типа Zmin=f(D, L) (оператор
5). Расчет величины допускаdi производится по специальной про-
грамме (оператор *). После определения Dmax (оператор 7) проверяет-
ся количество рассчитанных операций, и если *>*, то происходит пе-
реход к (i-1)-ой операции, и цикл повторяется. В конце на печать вы-
водятся значения Zmin, Dmax, Dmin,di для всех операций маршрута.
В зависимости от заданной точности и шероховатости поверх- ности детали определяется конечная стадия STM*X (оператор 3), а в зависимости от вида заготовки и ее точности - начальная стадия S*MI* (оператор 5) процесса обработки. После этого формируется
множество N возможных маршрутов <M*, M2,..., M*>. Далее произ-
водится их последовательный анализ и расчет. Для этого на монитор
выводится Mi маршрут обработки рассматриваемой поверхности
(оператор 9). Если предлагаемый маршрут принимается, то произво-
дится расчет операционных припусков и размеров (оператор 11) по специальной подпрограмме. Результаты проектирования выводятся на монитор, и после их анализа принимается решение о выборе опти- мального варианта
В тех случаях, когда проектировщик отвергает предлагаемый i- ый вариант маршрута обработки (операторы 10 и13), на экран дис- плея выдается (i+1)-ый вариант, для которого аналогично произво- дится анализ и расчет операционных припусков и размеров. После выбора оптимального варианта результат проектирования выводится на печать в виде технологической карты.
|
|
Эмиссия газов от очистных сооружений канализации: В последние годы внимание мирового сообщества сосредоточено на экологических проблемах...
Особенности сооружения опор в сложных условиях: Сооружение ВЛ в районах с суровыми климатическими и тяжелыми геологическими условиями...
Семя – орган полового размножения и расселения растений: наружи у семян имеется плотный покров – кожура...
Опора деревянной одностоечной и способы укрепление угловых опор: Опоры ВЛ - конструкции, предназначенные для поддерживания проводов на необходимой высоте над землей, водой...
© cyberpedia.su 2017-2024 - Не является автором материалов. Исключительное право сохранено за автором текста.
Если вы не хотите, чтобы данный материал был у нас на сайте, перейдите по ссылке: Нарушение авторских прав. Мы поможем в написании вашей работы!