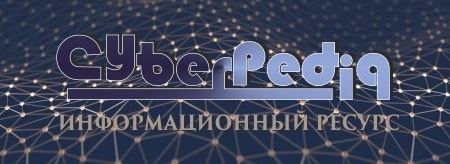
Папиллярные узоры пальцев рук - маркер спортивных способностей: дерматоглифические признаки формируются на 3-5 месяце беременности, не изменяются в течение жизни...
Семя – орган полового размножения и расселения растений: наружи у семян имеется плотный покров – кожура...
Топ:
Техника безопасности при работе на пароконвектомате: К обслуживанию пароконвектомата допускаются лица, прошедшие технический минимум по эксплуатации оборудования...
Марксистская теория происхождения государства: По мнению Маркса и Энгельса, в основе развития общества, происходящих в нем изменений лежит...
Интересное:
Средства для ингаляционного наркоза: Наркоз наступает в результате вдыхания (ингаляции) средств, которое осуществляют или с помощью маски...
Влияние предпринимательской среды на эффективное функционирование предприятия: Предпринимательская среда – это совокупность внешних и внутренних факторов, оказывающих влияние на функционирование фирмы...
Подходы к решению темы фильма: Существует три основных типа исторического фильма, имеющих между собой много общего...
Дисциплины:
![]() |
![]() |
5.00
из
|
Заказать работу |
|
|
Марка стали | 40Х | 35ХГСА | 30ХМ | 15Х2ВМФ |
Диапазон оптимальной Vохл., 0С/с | 2,5 – 3,7 | 2,5 – 6,0 | до 8 | до 20 |
Таким образом, при выборе режимов сварки сталей данной группы:
1. Производят расчет режима по условиям формирования сварного шва.
2. Для принятого режима рассчитывают скорость охлаждения и сравнивают ее с диапазоном оптимальной скорости охлаждения.
3. Если Vохл> Vкр, то производят расчет необходимой температуры подогрева.
Для приближенной оценки необходимости предварительного подогрева или возможности сварки без него на практике часто пользуются подсчетом полного эквивалента углерода Сэквп по выражению:
, (28)где Сэквх – эквивалент углерода, определяемый по выражению (20);
Сэквр - эквивалент углерода, учитывающий влияние толщины свариваемого металла, и определяемый по выражению:
, (29)
где S - толщина свариваемого металла.
Расчет производят по верхним пределам содержания элементов в стали, если Сэкв≥0,45, то предварительный подогрев необходим, а его температура определяется по соотношению:
. (30)
В некоторых случаях, применяя особые технологические приемы, обеспечивающие увеличение времени пребывания металла шва и ОШЗ в субкритическом интервале температур и «автотермообработку» закаленных участков, прилегающих к шву, можно обеспечить отсутствие закалки в ОШЗ либо вовсе без подогрева, либо с невысоким подогревом. Один из таких приемов называется сваркой короткими участками каскадным методом.
Рассмотрим схемы заполнения разделки на проход и каскадным методом (рис. 9, в). Заполнение разделки одинаково, однако ТЦС различны. Особенность термического цикла многослойной сварки указанным способом состоит в том, что теплота второго и последующего слоев не позволяет металлу ОШЗ 1-го слоя охладиться ниже определенной температуры. После сварки 2-го и последующих слоев ОШЗ охлаждается значительно медленнее, чем после сварки одного 1-го слоя (рис. 9, а). При наложении 1-го слоя температура точки 1 резко возрастает, превышая температуру АС3, а затем резко падает. В момент, когда температура в точке 1 понизится до допустимого значения ТВ (ТВ > ТМ), тепловая волна от наложения 2-го слоя осуществит повторный нагрев металла ОШЗ 1-го слоя, но до температуры более низкой, чем при сварке 1-го слоя.
|
При сварке 3-го слоя снова происходит некоторый подогрев, причем по мере выполнения последующих слоев температурные воздействия ослабевают и процесс стремится к установившемуся температурному состоянию. По окончании сварки металл ОШЗ медленно охлаждается.
На рис. 9, б показано изменение температуры в точке 2, находящейся у поверхности листов. При выполнении каждого последующего слоя температура в точке 2 нарастает, при выполнении последнего слоя достигает максимума и после этого начинает снижаться. По прошествии t в (время пребывания металла в интервале температур ТАс3 – ТМ)температура точки 2 снижается до температуры мартенситного превращения и, если за это время не успевает произойти распад аустенита, то образуется мартенситная структура.
Для увеличения времени пребывания металла ОШЗ при температуре выше точки мартенситного превращения накладывают так называемый «отжигающий валик», границы которого не выходят за пределы металла шва и тем самым не нагревают подверженный закалке металл ОШЗ до температуры выше АС3. Наплавка отжигающего валика увеличивает время пребывания металла ОШЗ в субкритическом интервале температур с t в до t ’ в.
Рис. 9. Термический цикл околошовной зоны при многослойной сварке
короткими участками:
а - первый слой (точка 1); б - последний слой (точка 2);
в - схема каскадной сварки
|
При многослойной сварке короткими участками необходимо определить длину участка, при которой температура ОШЗ до прихода тепловой волны от каждого последующего слоя не успеет понизиться ниже допустимой величины ТВ.
Длина участка, при которой металл в ОШЗ после сварки 1-го слоя охладится до температуры ТВ, определяется по формуле Н.Н. Рыкалина:
(31)
где q – эффективная тепловая мощность дуги;
S - толщина свариваемой детали;
Vсв – скорость сварки;
Т0 – начальная температура изделия;
сρ – объемная теплоемкость;
λ – коэффициент теплопроводности;
Тв – температура, ниже которой в процессе сварки металл ОШЗ не должен охлаждаться (обычно Тв=Тм+(50÷100 0С)).
k г = tг/(tг + tп) – коэффициент горения дуги, т.е. отношение времени горение дуги к полному времени сварки. Практически k г =0,6÷0,8 при РДС и 0,8÷0,9 при сварке в среде СО2.
С учетом отличия расчетной схемы ввода тепла в изделие (быстродвижущийся линейный источник в пластине без теплоотдачи) от действительного процесса поправочным коэффициентом k 3 расчетная формула принимает вид:
, (32)
где k 3 – поправочный коэффициент, определяемый путем сопоставления расчетной температуры охлаждения 1-го слоя с опытной и учитывающий тип сварного соединения: для стыковых соединений k 3 =1,5; тавровых – 0,9, крестовых – 0,8.
Разбивка на отрезки участка шва зависит от принятого числа слоев в каскаде: их должно быть столько, сколько слоев, но не менее четырех.
Для того чтобы при сварке в ОШЗ получить такие структуры, которые обеспечат деформационную способность металла, достаточную для предотвращения образования холодных трещин при охлаждении и вылеживании изделия до проведения соответствующей термообработки, необходимо, чтобы общее время выдержки в субкритическом интервале температур было бы достаточным для полного распада аустенита. Это время определяют по диаграмме изотермического распада аустенита стали данной марки.
Последовательность расчета длительности пребывания ОШЗ в субкритической области температур при данной длине участка.
1. Определяем значение расчетной мощности дуги:
, (33)
где k г - коэффициент горение дуги;
q - эффективная тепловая мощность дуги;
k q – коэффициент приведения мощности дуги, зависящий от типа сварного соединения: для стыкового k q =1,0; для таврового k q =0,67;для крестового k q =0,60.
|
2. Рассчитываем относительную температуру точек, лежащих в ОШЗ:
, (34)
где - длина участка; S – толщина листов;
- коэффициент температуропроводности;
- коэффициент, учитывающий поверхностную теплоотдачу; a - коэффициент теплоотдачи.
3. Находим относительное расчетное расстояние точек ОШЗ от плоскости источника:
, (35)
где Х – действительное расчетное расстояние ОШЗ от плоскости источника (см). При сварке стыковых швов величина Х равна половине ширины разделки по верху, для тавровых, угловых, нахлесточных соединений Х =1/2 катета.
4. Определяем относительную продолжительность действия источника тепла, принимаемую за длительность полной заварки рассматриваемого участка многослойного шва, включая и перерывы:
, (36)
где n – число слоев в каскаде;
tc – время сварки ступени каскада;
Vсв – скорость сварки.
5. По вычисленным значениям θ1, ρ1, b tc по номограммам Н.Н. Рыкалина (рис. 10) находим относительную продолжительность пребывания металла ОШЗ при температуре выше допустимой Тв и вычисляем действительную длительность пребывания металла ОШЗ 1-го слоя в субкритическом интервале температур по формуле:
. (37)
Рис. 10. Номограммы для определения действительного времени пребывания металла ОШЗ в субкритическом интервале температур
а) r 1 = 0; б) r 1 = 0,1; в) r 1 = 0,2;
Определяем продолжительность пребывания ОШЗ в субкритическом интервале температур при сварке последнего слоя по соотношению:
. (38)
Время пребывания металла околошовной зоны выше температуры Тв должно быть больше, чем время изотермического распада аустенита при этой температуре для стали данной марки.
Т
А3
Рис. 11. Диаграмма изотермического распада аустенита (сталь 40Х)
tв – время необходимое для полного распада аустенита в субкритическом интервале температур.
Например, для стали 40Х С – образные кривые представлены на рис. 11. Если действительное время tв1 или tвп будет меньше tв, то произойдет частичная или полная закалка. Для того, чтобы избежать закалки, необходимо уменьшить длину участка или увеличить Т0 – т.е. ввести предварительный подогрев.
|
2.3 Выбор сварочных материалов при сварке закаливающихся сталей и предупреждение образования горячих трещин
Для обеспечения эксплуатационной надежности сварных соединений необходимо, чтобы швы обладали не только заданным уровнем прочности, но и высокой пластичностью. Поэтому при выборе сварочных материалов необходимо стремиться к получению швов такого химического состава, при котором их механические свойства имели бы требуемые значения. Легирование металла шва элементами, входящими в основной металл, всегда повышает его прочностные характеристики, одновременно снижая пластичность.
Это всегда следует учитывать при выборе сварочных материалов для легированных конструкционных сталей. Так, например, при сварке низколегированной стали с временным сопротивлением 500 МПа применение электродов типа Э-50А может привести к значительному повышению временного сопротивления металла шва и существенному снижению пластичности и ударной вязкости. Это происходит ввиду легирования металла элементами, содержащимися в основном металле при проплавлении последнего. Характер изменения этих свойств зависит от доли участия основного металла в формировании металла шва. Поэтому, как правило, следует выбирать такие сварочные материалы, которые содержат легирующих элементов меньше, чем основной металл.
Легирование металла шва за счет основного металла позволит повысить свойства шва до необходимого уровня. Однако следует помнить, что доля участия основного металла в металле шва, а значит, и степень легирования зависят от способа сварки, применяемого режима сварки и других технологических приемов. Поэтому при разработке технологического процесса сварки необходима расчетная проверка ожидаемых механических свойств металла шва для принятых режимов сварки и сварочных материалов (см. гл. 1).
Для обеспечения технологической прочности сварных швов, выполненных низколегированными сварочными материалами, содержание углерода в них не должно превышать 0,15%, так как дальнейшее увеличение содержания углерода резко повышает склонность металла швов к образованию горячих трещин, а также существенно снижает пластичность и особенно ударную вязкость металла шва в эксплуатационных условиях. Необходимых прочностных характеристик металла шва достигают легированием его элементами, которые, повышая прочность, не снижают существенно его деформационную способность и ударную вязкость.
Высокую технологическую прочность и работоспособность можно получить, если содержание легирующих элементов в низколегированном металле шва не превысит (в %): 0,15 С; 0,5 Si; 1.5 Mn; 1,5 Cr; 2,5 Ni; 0,5 V; 1,0 Мо; 0,5 Nb. Комбинируя различные легирующие элементы в указанных пределах, можно получить швы с временным сопротивлением до 600 – 700 МПа в исходном после сварки состоянии и 850 – 1450 МПа после соответствующей термообработки. При сварке низколегированных сталей повышенной прочности не предъявляют требований к идентичности состава металла шва и основного металла; основным критерием выбора служит получение гарантированных механических свойств металла шва, что и предусмотрено действующим ГОСТ 9467-75.
|
При сварке глубокопрокаливающихся высокопрочных сталей необходимо выбрать такие сварочные материалы, которые обеспечат получение швов, обладающих высокой деформационной способностью при минимально возможном количестве водорода в сварочной ванне. Это может быть достигнуто применением низколегированных сварочных электродов, не содержащих в покрытии органических веществ и подвергнутых высокотемпературной прокалке (низководородистые электроды).
Одновременно при выполнении сварки необходимо принимать меры для исключения других источников насыщения сварочной ванны водородом (влаги, ржавчины, органических загрязнений на кромках и др.).
Наиболее широко для сварки этих сталей применяют аустенитные сварочные материалы. В большинстве случаев в шве стремятся получить высоколегированную аустенитную хромоникелевую или хромоникелемарганцовистую сталь. Такой металл обладает высокой пластичностью и не претерпевает полиморфных превращений, т. е. сохраняет аустенитную структуру во всем диапазоне температур, вследствие этого растворимость водорода в шве с понижением температуры изменяется незначительно, а проницаемость его мала. Для механизированной сварки и изготовления стержней электродов в ГОСТ 2246 - 70 предусмотрены проволоки марок Св-08Х20Н9Г7Т и Св-08Х21Н10Г6, а в ГОСТ 10052 - 75 электроды типа ЭА-1Г6 и др. Применяются электродные покрытия основного типа, а для механизированной сварки - основные флюсы, например 48-ОФ-6.
Предупреждение склонности металла шва к образованию горячих трещин. Склонность металла шва к образованию горячих трещин определяется низкой деформационной способностью металла шва в температурном интервале хрупкости (ТИХ), что объясняется в основном наличием легкоплавких эвтектик с одной стороны – и величиной и скоростью нарастания растягивающих напряжений в температурном интервале низкой пластичности и прочности – с другой.
Одним из основных факторов, повышающих склонность металла шва к образованию горячих трещин, является повышение содержания углерода сверх допустимого предела, который усиливает отрицательное влияние серы. Известно, что сера образует с железом легкоплавкую эвтектику FeS с Тпл= 980 0С, которая, обволакивая границы зерен, разобщает их. Введение достаточного количества марганца (Mn) приводит к образованию более тугоплавкого соединения MnS с Тпл= 1650 0С т.к. сера обладает большим сродством к марганцу, чем к железу. Известна такая зависимость
|
|
Чтобы не допустить образование горячих трещин в металле шва, необходимо обеспечить концентрацию марганца в шве в 20 ÷ 22 раза больше, чем концентрация серы. Увеличение содержания углерода уменьшает температуру предварительного подогрева и увеличивает склонность к образованию горячих трещин.
Полезное действие марганца заключается также в увеличении количества центров кристаллизации в сварочной ванне. Поэтому для сварки под флюсом предельное содержание углерода в металле шва, при котором еще не появляются горячие трещины ограниченно 0,16 %, а для ручной дуговой – 0,22 %.
У этих сталей содержание углерода повышенное. Даже при сварке низкоуглеродистыми сварочными материалами углерод в достаточном количестве попадает в металл шва из основного металла, особенно при сварке корневого прохода. Поэтому при сварке сталей этой группы необходимо выбирать также режимы, которые обеспечивают минимальную долю участия основного металла в металле шва. Доля участия основного металла зависит как от величины Iсв и Vсв, так и от типа соединения и формы подготовки кромок.
Зависимость γ0 от Vсв имеет следующий характер (рис.13).
![]() | |||
![]() | |||
Первая кривая относится к случаю наплавки на лист; сварки встык
без разделки на больших токах. Вторая кривая то же самое – на малых токах. Третья кривая – сварка в разделку на больших токах. Четвертая кривая – то же самое на малых токах. Увеличение Vсв приводит к увеличению термического к.п.д. дуги. Происходящее при этом снижение площади провара происходит менее интенсивно, чем снижение площади наплавки.
Таким образом, для уменьшения γ0 приходится варить на малых токах и низких скоростях и делать разделку там, где это и не требуется по условиям формирования шва, но иногда и этого недостаточно.
Для предупреждения образования горячих трещин может использоваться предварительный подогрев изделия, т.к. выполнение его отдаляет момент возникновения деформаций растяжения в металле шва. Таким образом, при сварке с подогревом горячие трещины могут не появиться и при большом содержании углерода, что видно из следующей зависимости (рис. 14).
Возникновение горячих трещин кроме того, зависит от формы провара и содержания углерода в металле шва (рис.15).
ψпр
Рис. 15. Влияние геометрии сварного шва и содержания углерода на возникновение горячих трещин
Это объясняется условием кристаллизации: при малых значениях ψпр, т.е. узких и глубоких швах, растущие дендриты оттесняют ликват в центр шва, где он и скапливается. При оптимальных значениях ψпр – нормальных чашеобразных швах - ликват вытесняется на поверхность. При больших значениях ψпр – широких швах – дендриты растут почти параллельно и ликват застревает между их осями.
Основные методы сварки
Ручная дуговая сварка покрытыми электродами. Конструктивные элементы подготовки кромок для ручной дуговой сварки штучными электродами такие же, как и для сварки углеродистых сталей, т. е. в соответствии с рекомендациями ГОСТ 5264-80. Для сварки низколегированных сталей повышенной прочности выбирают электроды типов Э-50А, Э-70, Э-85 и др. по ГОСТ 9467-75.
Температуру предварительного подогрева при сварке низколегированных сталей с повышенным содержанием углерода назначают в соответствии с результатами расчета, выполненного по методике, изложенной в 2.2 данной главы. Расчетную скорость охлаждения при температуре наименьшей устойчивости аустенита принимают для стали данной марки в зависимости от характера термообработки до и после сварки и требований к свойствам сварного соединения.
Если сталь перед сваркой подвергают термообработке на высокую прочность (нормализации или закалке с отпуском), а после сварки - отпуску для снятия напряжений и выравнивания механических свойств сварного соединения с целью обеспечения его равнопрочности с основным металлом, то критерием расчетного определения температуры предварительного подогрева будет скорость охлаждения V д, при которой имеет место частичная закалка околошовной зоны, но гарантируется отсутствие трещин в процессе сварки и до проведения последующей термообработки.
Если сталь перед сваркой подвергают термообработке, но после сварки отпуск невозможен из-за крупных размеров конструкции, то сталь данной марки можно использовать для изготовления такой конструкции только в том случае, если не предъявляется жестких требований к равнопрочности сварного соединения и основного металла в условиях статического нагружения. Для обеспечения свойств сварного соединения, гарантирующих требуемую его работоспособность, критерием необходимой температуры подогрева будет диапазон скоростей охлаждения, обеспечивающий необходимый уровень механических свойств в околошовной зоне.
Аустенитными электродами обычно сваривают без предварительного подогрева, но при этом регламентируется время с момента окончания сварки до проведения термообработки изделия. Если сваривают низколегированные стали с невысоким содержанием углерода (0,12 - 0,17%), то последующую термообработку проводят в исключительно редких случаях. Разделку заполняют каскадом или горкой, причем длину участков рассчитывают согласно указаниям, изложенным в 2.2 данной главы. Температура охлаждения зоны термического влияния в процессе сварки допускается не ниже Тв = 150 - 200 °С.
Механизированная сварка под флюсом. Конструктивные элементы подготовки кромок под автоматическую и механизированную сварку под флюсом выполняют такими же, как и при сварке углеродистых и низколегированных незакаливающихся конструкционных сталей, т. е. в соответствии с рекомендациями ГОСТ 8713-79. Однако в диапазоне толщин, для которого допускается сварка без разделки и со скосом кромок, последней следует отдать предпочтение. Наряду с затруднениями, связанными с образованием холодных трещин в околошовной зоне и получением металла шва и других зон сварного соединения со свойствами, обеспечивающими высокую работоспособность сварных соединений, при механизированной сварке под флюсом швы имеют повышенную склонность к образованию горячих трещин. Это связано с тем, что при данном способе сварки доля основного металла в металле шва достаточно велика (см. 2.3).
При использовании для сварки низкоуглеродистых проволок в полной мере можно реализовать преимущество сварки под флюсом: получать швы с глубоким проплавлением, используя при однопроходной сварке стыковых соединений без разделки кромок повышенный сварочный ток и скорость сварки. Необходимый состав металла шва будет обеспечиваться повышением доли основного металла в шве, которую при выборе режима сварки во избежание перелегирования шва следует проверять расчетом.
Сварочные материалы (электродную проволоку и флюс) выбирают в зависимости от состава и назначения свариваемой стали. Для низколегированных сталей повышенной прочности (например 40Х, ЗОХГС, ЗОХНМ, ЗОХМА и им подобным) в зависимости от требований, предъявляемых к сварным соединениям, используют низкоуглеродистую проволоку Св-08А и легированные проволоки, например Св-10ГН, Св-08ГСМТ, Св-18ХГС и др.
Флюс выбирают в зависимости от марки электродной проволоки. При использовании низкоуглеродистой проволоки или низколегированной, не содержащей достаточного количества элементов раскислителей, сварку выполняют под кислыми высоко-или среднемарганцовистыми флюсами (в зависимости от состава свариваемой стали). При использовании низколегированных проволок, содержащих элементы-раскислители в достаточном количестве, лучшие результаты (по механическим свойствам металла шва) обеспечивает применение низкокремнистых, низкомарганцовистых флюсов, например АН-15, АН-24, АН-20.
Температуру предварительного подогрева при сварке низколегированных сталей с повышенным содержанием углерода рассчитывают по методике, изложенной в п. 2.2 данной главы, причем расчетную скорость охлаждения в зависимости от характера термообработки до и после сварки и требований к свойствам сварных соединений выбирают на тех же основаниях, что и при ручной дуговой сварке.
Сварка в среде защитных газов. Сварка в среде защитных газов находит широкое применение при изготовлении тонколистовых конструкций из низколегированных (с повышенным содержанием углерода) сталей и конструкций из металла средней и большой толщины. Конструктивные элементы подготовки кромок под сварку в среде защитных газов следует выполнять в соответствии с требованиями ГОСТ 14771-76.
В зависимости от разновидности метода сварки в защитных газах подготовка кромок должна быть различной. Так как при сварке в защитных инертных газах расплавленный металл изолирован от атмосферного воздуха, то в сварочной ванне могут протекать металлургические процессы, связанные с наличием в нем растворенных газов и легирующих элементов, внесенных из основного или дополнительного металла. При использовании смесей инертных с активными газами возникают металлургические взаимодействия между элементами, содержащимися в расплавленном металле, и активными примесями в инертном газе.
Если в сварочной ванне содержится некоторое количество кислорода, то при высоких концентрациях углерода будет протекать реакция окисления его. Если концентрация углерода в сварочной ванне в период кристаллизации будет достаточно высокой, то при отсутствии или недостатке других раскислителей реакция образования СО будет продолжаться, что может вызвать порообразование. Возникновению пор способствует также и водород, содержание которого при малой степени окисленности ванны может быть достаточно высоким.
Для подавления реакции окисления углерода в период кристаллизации металла шва в сварочной ванне должно содержаться достаточное количество раскислителей, например кремния или марганца. Наряду с этим устранение пор при отсутствии раскислителей при сварке с защитой аргоном может быть достигнуто некоторым повышением степени окисленности ванны за счет добавки к аргону кислорода (до 5%) или углекислого газа (до 25%) в смеси с кислородом (до 5%). При этом интенсифицируется окисление углерода в зоне высоких температур (в головной части сварочной ванны), усиливается его выгорание, вследствие чего концентрация углерода и содержание кислорода в сварочной ванне к моменту начала кристаллизации уменьшаются и тем самым прекращается образование СО.
Интенсивное окисление углерода вызывает энергичное кипение сварочной ванны в головной ее части, за счет которого пузырьки окиси углерода, интенсивно выделяясь из ванны, захватывают и уносят выделяющийся из раствора водород, как бы очищая ванну. При сварке низколегированных закаливающихся сталей в инертных газах и их смесях с активными можно использовать любую из тридцати марок легированной проволоки, предусмотренных ГОСТ 2246-70; ту или иную марку необходимо выбирать в зависимости от состава и свойств свариваемых сталей и от требуемого состава металла шва.
При сварке в углекислом газе - активном окислителе металла ванны - в составе проволоки обязательно, кроме других легирующих элементов, должны присутствовать раскислители - кремний и марганец (а иногда и титан). Поэтому для сварки в углекислом газе можно использовать только те проволоки, в составе которых содержатся эти элементы, т. е. в маркировке обозначены «Г» и «С», например Св-08Г2С, Св-08ГСМТ, Св-08ХГСМА, Св-08ХГСМФА и др. в зависимости от состава свариваемой стали и требований к механическим свойствам металла шва.
Отсутствие толстой шлаковой корки на поверхности шва позволяет выполнять механизированную сварку в защитных газах короткими и средней длины участками (каскадом, горной), сократить до минимума перерыв между наложением слоев многослойного шва, а также выполнять автоматическую двух- или многодуговую сварку дугами, горящими в различных плавильных пространствах таким образом, чтобы тепловое воздействие от выполнения последующего слоя на околошовную зону предыдущего происходило при необходимой температуре. Все это позволяет регулировать термический цикл наилучшим образом, добиваясь наиболее благоприятных структур в околошовной зоне.
Электрошлаковая сварка. Применение электрошлаковой сварки низколегированных сталей с повышенным содержанием углерода наиболее рационально для соединения толстолистовых конструкций. Основные типы и конструктивные элементы сварных соединений и швов, выполняемых электрошлаковой сваркой, должны соответствовать требованиям ГОСТ 15164-80, который регламентирует основные типы соединений, выполняемых всеми разновидностями электрошлаковой сварки.
Для электрошлаковой сварки низколегированных сталей повышенной прочности применяют флюсы марок АН-8, АН-22 и др. При выборе электродной проволоки для электрошлаковой сварки следует исходить из требований к составу металла шва. Флюс практически мало влияет на состав металла шва вследствие малого его количества. Поэтому только в случае необходимости легирования шва элементами, обладающими большим сродством к кислороду (например титаном, алюминием), следует применять флюсы на основе фторидов или системы CaF2-CaO-Al2O3.
Электродные проволоки при сварке проволочными электродами и плавящимся мундштуком в зависимости от состава свариваемой стали и требований, предъявляемых к шву, выбирают из числа групп легированных или высоколегированных проволок по ГОСТ 2246-70, например Св-08ХГ2С, Св-08ГСМТ, Св-18ХМА, Св-10Х5М и др. Пластины при сварке плавящимся мундштуком и пластинчатыми электродами изготовляют из аналогичных сталей.
Высокие значения погонной энергии при электрошлаковой сварке позволяют в ряде случаев выполнять ее без предварительного подогрева, даже при сварке низколегированных сталей с повышенным содержанием углерод». Однако при неблагоприятных условиях и при электрошлаковой сварке могут возникать горячие трещины в шве и горячие и холодные трещины типа отколов в околошовной зоне. Трещины-отколы возникают преимущественно в начале шва и на участках возобновления процесса из-за случайных перерывов. Для предупреждения горячих трещин в шве необходимо выполнять сварку на режимах, обеспечивающих получение относительно неглубокой и широкой металлической ванны. При этом столбчатые кристаллиты по мере приближения их к оси изгибаются кверху, вследствие чего отсутствует резко выраженная встреча кристаллитов. Наоборот, при сварке на режимах, при которых образуется узкая и глубокая сварочная ванна, столбчатые кристаллиты, растущие от противоположных кромок, почти не изменяют своего направления, и при их встрече образуется резко выраженная плоскость слабины. Для предупреждения трещин в околошовной зоне при сварке жестко закрепленных элементов необходимо применять предварительный подогрев до температуры 150—200 0С.
Низкие скорости охлаждения околошовной зоны при электрошлаковой сварке приводят к длительному пребыванию ее в области высоких температур, вызывающих рост зерна и охрупчивание металла. Поэтому после электрошлаковой сварки низколегированных сталей с повышенным содержанием углерода необходима высокотемпературная термообработка сваренных изделий для восстановления механических свойств до необходимого уровня. Время с момента окончания сварки до проведения термообработки должно быть регламентировано.
|
|
Археология об основании Рима: Новые раскопки проясняют и такой острый дискуссионный вопрос, как дата самого возникновения Рима...
История создания датчика движения: Первый прибор для обнаружения движения был изобретен немецким физиком Генрихом Герцем...
История развития хранилищ для нефти: Первые склады нефти появились в XVII веке. Они представляли собой землянные ямы-амбара глубиной 4…5 м...
Своеобразие русской архитектуры: Основной материал – дерево – быстрота постройки, но недолговечность и необходимость деления...
© cyberpedia.su 2017-2024 - Не является автором материалов. Исключительное право сохранено за автором текста.
Если вы не хотите, чтобы данный материал был у нас на сайте, перейдите по ссылке: Нарушение авторских прав. Мы поможем в написании вашей работы!