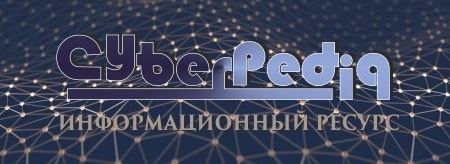
История развития хранилищ для нефти: Первые склады нефти появились в XVII веке. Они представляли собой землянные ямы-амбара глубиной 4…5 м...
Двойное оплодотворение у цветковых растений: Оплодотворение - это процесс слияния мужской и женской половых клеток с образованием зиготы...
Топ:
Оснащения врачебно-сестринской бригады.
Методика измерений сопротивления растеканию тока анодного заземления: Анодный заземлитель (анод) – проводник, погруженный в электролитическую среду (грунт, раствор электролита) и подключенный к положительному...
Выпускная квалификационная работа: Основная часть ВКР, как правило, состоит из двух-трех глав, каждая из которых, в свою очередь...
Интересное:
Финансовый рынок и его значение в управлении денежными потоками на современном этапе: любому предприятию для расширения производства и увеличения прибыли нужны...
Распространение рака на другие отдаленные от желудка органы: Характерных симптомов рака желудка не существует. Выраженные симптомы появляются, когда опухоль...
Уполаживание и террасирование склонов: Если глубина оврага более 5 м необходимо устройство берм. Варианты использования оврагов для градостроительных целей...
Дисциплины:
![]() |
![]() |
5.00
из
|
Заказать работу |
|
|
Ручная дуговая сварка низколегированных сталей выполняется в основном электродами с фтористо-кальциевым покрытием типа Э-42А, Э-50А, обеспечивающими более высокую технологическую прочность и повышенные пластические свойства по сравнению с электродами других типов. Для сварки сталей с пониженным содержанием углерода (например 09Г2) в ряде случаев используют электроды с рутиловым покрытием, например АНО-1. Наиболее широко применяют электроды марок УОНИИ 13/45А, СМ-11, АНО-8 (тип Э-42А) и УОНИИ 13/55, ДСК-50, АНО-7 (тип Э-50А), обеспечивающие прочность и пластичность металла шва на уровне свойств основного металла.
Высокая прочность металла шва при сварке электродами типа Э-42А достигается за счет перехода легирующих элементов в шов из основного металла и повышенной скорости охлаждения металла шва. Для сварки кольцевых швов трубопроводов, работающих при температурах до – 70 0С, например из стали 10Г2, находят применение электроды марки ВСН-3 с фтористо-кальциевым покрытием.
Требования к конструктивным элементам и геометрическим размерам сварных швов регламентируются ГОСТ 5264-80 и ГОСТ 15535-75.
Механизированная сварка под флюсом в большинстве случаев выполняется с применением тех же сварочных материалов, что и при сварке низкоуглеродистых сталей: плавленные флюсы АН-348А, ОСЦ-45 (однодуговая сварка), АН-60 (многодуговая сварка), а также сварочные проволоки Св-08ГА, Св-10Г2. Для сварки микролегированных сталей, например 15Г2АФ, в ряде случаев применяют низкокремнистый флюс АН-22 в сочетании с проволоками Св-08ХМ и Св-10НМА. Однако при этом швы менее стойки против кристаллизационных трещин, вследствие чего сварку следует выполнять с предварительным подогревом.
|
Металл швов, сваренных под флюсом, благодаря значительной доли участия основного металла и достаточному содержанию легирующих элементов обладает более высокой стойкостью против коррозии в морской воде, чем металл швов, сваренных покрытыми электродами обычного состава.
Требования к конструктивным элементам и геометрическим размерам сварных швов регламентируются ГОСТ 8713-79 и ГОСТ 15534-75.
Механизированная сварка в защитных газах выполняется в основном в полуавтоматическом режиме. Технология сварки низколегированных сталей в углекислом газе практически ничем не отличается от технологии сварки низкоуглеродистой стали. На практике применяют те же сварочные материалы, что и для сварки низкоуглеродистой стали. Так, стали 15ХСНД, 14ХГС, 10ХСНД сваривают сварочной проволокой Св-08Г2С. При однослойной сварке и сварке не более чем в два-три слоя можно применять проволоку Св-12ГС.
Механизированную сварку в СО2 выполняют также порошковыми проволоками ПП-АН4 и ПП-АН-8, при этом швы равнопрочны основному металлу и имеют повышенные пластические характеристики.
Для повышения коррозионной стойкости сварных соединений в морской воде применяют сварочную проволоку Св-08ХГ2С, обеспечивающую дополнительное легирование металла шва хромом.
Требования к конструктивным элементам и геометрическим размерам сварных швов регламентируются ГОСТ 14771-76 и ГОСТ 23518-79.
Электрошлаковая сварка низколегированных сталей эффективна при сварке проката большой толщины, как правило, более 30 – 40 мм. Равнопрочность сварных соединений обеспечивается при использовании сварочных проволок Св-10Г2 или Св-08ГС в сочетании с флюсами АН-8 или ФЦ-7.
При электрошлаковой сварке из-за длительного пребывания при температуре более 1000 – 1100 0С в околошовном участке ЗТВ образуются крупные зерна аустенита, распад которых в условиях замедленного охлаждения сопровождается возникновением видманштеттовой структуры с пониженной ударной вязкостью по сравнению с основным металлом. Для повышения ударной вязкости сварные соединения подвергаются последующей или сопутствующей высокотемпературной обработке – нормализации, после которой осуществляют высокий отпуск для снятия сварочных напряжений, если толщина проката превышает 36 мм.
|
При выполнении нормализации температура печи при посадке сварных изделий, аппаратов или их узлов должна быть не более 250 – 300 0С, и скорость нагрева не должна превышать 100 – 150 0С/ч. Охлаждение – на спокойном воздухе.
При проведении последующего отпуска температура печи при посадке и скорость нагрева сварных изделий такие же, как и при нормализации. Температура при выгрузке – не более 300 0С.
Температура нагрева при нормализации сварных изделий составляет 910 – 920 0С, а при высоком отпуске 650 ± 10 0С. Время выдержки при нормализации 1 – 1,5 мин на 1 мм толщины проката. При высоком отпуске время выдержки выбирается из расчета 2 – 3 мин на 1 мм толщины проката. После охлаждения на спокойном воздухе структура металла шва и ЗТВ – ферритно-перлитная. Структура сварных соединений характеризуется высокой степенью дисперсности.
С целью повышения эффективности применения электрошлаковой технологии за счет исключения необходимости применения последующей высокотемпературной обработки сварных соединений возможно применение технологических способов регулирования структуры и свойств, рассмотренных в п.1.1.
Требования к конструктивным элементам и геометрическим размерам сварных швов регламентируются ГОСТ 1564-79.
Глава 2. Технология сварки машиностроительных низколегированных сталей (с повышенным содержанием углерода)
Особенности свариваемости
Рассматриваемая группа сталей (40Х, 30ХГСА, 25Н3 и др.) относится к закаливающимся сталям, в сварных соединениях которых под действием термического цикла сварки (ТЦС) могут образовываться хрупкие и малопластичные зоны в участках, где металл нагревался до температур выше точки Ас3. Распад аустенита при охлаждении в условиях сварочного термического цикла начинается при более низких температурах и в некоторых случаях полностью не заканчивается даже при остывании до 20 0С. При этом в структуре металла наряду с мартенситом остается нестабильный остаточный аустенит (в зависимости от уровня легирования).
|
Стали, склонные к резкой закалке, имеющие в результате ТЦС структуру мартенсита и остаточного аустенита при повышенной концентрации водорода и воздействии внутренних напряжений чувствительны к образованию холодных трещин (ХТ). Наиболее часто ХТ образуются в швах и ОШЗ среднеуглеродистых и легированных сталей перлитного и мартенситного классов, свариваемых проволокой, состав которой близок к составу основного металла. Холодные трещины возникают как в интервале температур образования мартенсита (250 0С и ниже), так и после полного остывания сварного соединения, спустя некоторое, иногда значительное время после сварки (1- 2 суток). Чем ниже температура распада аустенита, грубее структура мартенсита, выше уровень внутренних сварочных и структурных напряжений, тем вероятнее образование ХТ. С увеличением толщины свариваемого металла возможность образования холодных трещин возрастает.
Элементы, снижающие температуру g ® М превращения, усиливают склонность металла к образованию холодных трещин. В указанных сталях температура мартенситного превращения снижается при повышении содержания марганца, никеля, хрома, молибдена и др. О свариваемости стали применительно к ее чувствительности к закаливаемости судят по эквиваленту углерода, определяемого по соотношению (20).
Стали с Сэкв > 0,45 склонны к образованию холодных трещин при сварке. Однако этот критерий не является основанием для неприменения стали в сварной конструкции. При одном и том же показателе Сэкв стали с большим содержанием углерода имеют более высокую чувствительность к ХТ, чем сложнолегированные стали с меньшим содержанием углерода. Образование холодных трещин спустя некоторое время после полного остывания сварного соединения является наиболее неприятным, так как качество изделия теряется после его контроля. Замедленное разрушение связано с фиксированием нестабильного остаточного аустенита в структуре мартенсита при быстром остывании участков сварных соединений, нагревающихся выше точки Ас3. Остаточный аустенит с течением времени распадается при Т = 20 0С. Интенсивность этого процесса усиливается при охлаждении ниже 0 0С.
|
|
Историки об Елизавете Петровне: Елизавета попала между двумя встречными культурными течениями, воспитывалась среди новых европейских веяний и преданий...
Семя – орган полового размножения и расселения растений: наружи у семян имеется плотный покров – кожура...
Таксономические единицы (категории) растений: Каждая система классификации состоит из определённых соподчиненных друг другу...
Типы оградительных сооружений в морском порту: По расположению оградительных сооружений в плане различают волноломы, обе оконечности...
© cyberpedia.su 2017-2024 - Не является автором материалов. Исключительное право сохранено за автором текста.
Если вы не хотите, чтобы данный материал был у нас на сайте, перейдите по ссылке: Нарушение авторских прав. Мы поможем в написании вашей работы!