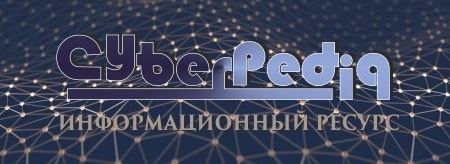
Адаптации растений и животных к жизни в горах: Большое значение для жизни организмов в горах имеют степень расчленения, крутизна и экспозиционные различия склонов...
Археология об основании Рима: Новые раскопки проясняют и такой острый дискуссионный вопрос, как дата самого возникновения Рима...
Топ:
Техника безопасности при работе на пароконвектомате: К обслуживанию пароконвектомата допускаются лица, прошедшие технический минимум по эксплуатации оборудования...
Интересное:
Распространение рака на другие отдаленные от желудка органы: Характерных симптомов рака желудка не существует. Выраженные симптомы появляются, когда опухоль...
Средства для ингаляционного наркоза: Наркоз наступает в результате вдыхания (ингаляции) средств, которое осуществляют или с помощью маски...
Мероприятия для защиты от морозного пучения грунтов: Инженерная защита от морозного (криогенного) пучения грунтов необходима для легких малоэтажных зданий и других сооружений...
Дисциплины:
![]() |
![]() |
5.00
из
|
Заказать работу |
|
|
Работой универсального горизонтально-фрезерного (универсально-фрезерного) станка модели 6Н81
6 - фрезерный станок (номер группы по классификации ЭНИМС)
Н – серия (поколение) станка (Б, К, Н, М, Р, Т)
8 – номер подгруппы (1, 2, 3, 4, 5, 6, 7, 8, 9) по классификации ЭНИМС (8 - горизонтально-фрезерный)
1 – исполнение станка - типоразмер (0, 1, 2, 3, 4) (1 - размер рабочего стола - 250 х 1000)
Станок предназначен для обработки различных деталей сравнительно небольших размеров в условиях индивидуального и мелкосерийного производства. Из числа работ, выполняемых на фрезерных станках и показанных на рис. 1, характерными для универсально-фрезерного являются те, которые производятся насадными фрезами (см. рис. 1,а,г,е,ж,м,о,п).
Достаточно часто выполняются операции отрезания (отрезки) и разрезания (разрезки) заготовок. Отрезание – процесс отделения части материала от целого (бруска, уголка и т.д.) и разрезание – процесс разделения целого (бруска, уголка и т.д.) на равные или неравные части производится тонкими дисковыми фрезами, называемыми отрезными. Возможна обработка вертикальных плоскостей торцовыми фрезами (см. рис. 1,в) и горизонтальных пазов и уступов на вертикальных поверхностях концевыми фрезами.
Общий вид универсально-фрезерного станка представлен на рис. 2. Основные узлы и детали станка на рисунке показаны буквами, а элементы управления – цифрами.
Станок устроен следующим образом. На плите (основании) А закреплена станина Б, внутри которой размещён разделённый привод главного движения. Он состоит из коробки скоростей и перебора со шпиндельным узлом. На вертикальных направляющих станины расположена вертикально подвижная консоль И с коробкой подач. На горизонтальных направляющих консоли установлены поперечно подвижные салазки Ж с поворотной плитой Е, а на направляющих плиты – продольно подвижный стол Д.
|
Для поддержки длинных оправок, на которых закрепляются цилиндрические, дисковые и тому подобные насадные фрезы, станки оснащаются хоботом В с двумя подвесными серьгами (подвесками) Г. Хобот по станине и серьги по хоботу могут быть перемещены и закреплены в нужном положении, зависящем от длины оправки. Если используются торцовые и концевые фрезы, то серьги снимаются, а хобот сдвигается назад (по рис. 2 – влево).
Компоновка станка с консолью удобна тем, что при фрезеровании заготовок с любой высотой уровень зоны обработки не меняется, что обеспечивается при соответствующем установе консоли по вертикали. Однако несущая система станка не является замкнутой, в результате чего её жёсткость снижена. Увеличение жёсткости станка может быть обеспечено связью хобота с консолью двумя поддерживающими стойками К.
Для ручного управления станком – переключения частот вращения шпинделя и подач, включения рабочих перемещений стола, салазок и консоли, выполнения ручных перемещений этих узлов – на станке имеются следующие элементы:
1 – рукоятка переключения групповых передач коробки скоростей;
2 – рукоятка переключения перебора шпинделя;
3 – маховик ручного продольного перемещения стола;
4 – рукоятка включения продольной подачи;
5 – рукоятка включения поперечной подачи;
6 – рукоятка включения вертикальной подачи;
7 – рукоятка ручного вертикального перемещения консоли с кареткой и столом;
8 – маховик ручного поперечного перемещения каретки со столом;
9, 10 – рукоятки переключения групповых передач коробки подач.
![]() |
Универсального токарно-винторезного станка модели 1К62
1 — токарный станок. К – поколение агрегата. 6 — токарно-винторезная подгруппа. 2 — высота над станиной (22 сантиметра).
Обтачивание конических поверхностей при смещении задней бабки
|
Таким способом обрабатывают длинные наружные конические поверхности с небольшим углом уклона.
Обтачивание конических поверхностей небольшой длины
Резцом с широкой режущей кромкой (широким резцом)
Этим способом обрабатывают короткие конические поверхности (длиной до 25 мм). Ширина режущей кромки резца должна быть больше образующей конуса на 3-4 мм.
Обтачивание конических поверхностей
Работающих по методу обката
На зубодолбёжных станках нарезают (рис. 1) цилиндрические колёса наружного и внутреннего зацепления с прямыми и винтовыми зубьями, колёса с буртами, блоки зубчатых колёс, зубчатые секторы, а также шлицевые валики, зубчатые рейки, храповики и т.д. Нарезание колёс с внутренними зубьями, а также зубчатых венцов на многовенцовых блоках и заготовках с буртами возможно практически только на зубодолбёжных станках.
![]() |
По расположению шпинделя зубодолбёжные станки подразделяются на вертикальные и горизонтальные. Наибольшее применение в промышленности имеют вертикальные зубодолбёжные станки.
Нарезание шестерён на большинстве моделей зубодолбёжных станков осуществляется методом обката, на некоторых моделях – методом копирования.
На станках, действующих по методу обката (обкатки), в процессе зубодолбления воспроизводится зацепление двух цилиндрических зубчатых колёс (рис. 2). Т.е. обработка зубьев происходит при вращении двух сцепленных колёс – их взаимном обкате. Одно из этих колёс имеет зубья, оснащённые режущими кромками, и является режущим инструментом – зуборезным долбяком, а другое, не имеющее зубьев, является заготовкой нарезаемого колёса. Ясно, что долбяк и заготовка должны приводиться во вращение так, как вращались бы, будучи в зацеплении, два зубчатых колёса. Для этого заготовку и долбяк соединяют жёсткой кинематической цепью со сменными колёсами для настройки на получение изделия с требуемым числом зубьев. Таким образом, при строго согласованном вращении долбяка и заготовки осуществляется деление и, одновременно, обкат и круговая подача.
|
При долблении зубьев колёс с наружным зацеплением направление вращения долбяка противоположно направлению вращения заготовки, а при долблении колёс с внутренним зацеплением направление их вращения совпадает. Поэтому в кинематическую цепь, связывающую движение долбяка и заготовки, включают реверсивное устройство.
Назначение станка
Зубофрезерный станок модели 5К32 предназначен для обработки зубьев цилиндрических прямозубых и косозубых колёс, а также червячных колёс с радиальной и тангенциальной подачами червячными фрезами. Нарезание цилиндрических зубчатых колёс производится встречным и попутным фрезерованием как с продольной (обычной), так и диагональной подачами.
Основной применяемый режущий инструмент – червячные модульные фрезы.
Компоновка и работа станка
На горизонтальных направляющих станины А (рис.1) установлены салазки Е с круглым столом Д. В центральном коническом отверстии стола устанавливается оправка с заготовкой. Верхний конец оправки поддерживается кронштейном Ж, установленным на направляющих стойки, закрепленной справа на салазках стола.
Слева на станине закреплена суппортная стойка Б, на вертикальных направляющих которой установлена каретка Г с фрезерным суппортом В, несущим шпиндель с фрезой. Благодаря наличию поворотного круга суппорт В может поворачиваться для установки оси фрезы на необходимый угол относительно заготовки.
В станке имеется гидропривод. Он размещен в станине и предназначен для нагружения винтовой пары подачи фрезерного суппорта (при попутном фрезеровании), перемещения кронштейна Ж по стойке салазок стола, привода транспортера стружки и для смазки станка.
Станок работает по методу обкатки, то есть вращается червячная фреза и согласованно с ней вращается нарезаемое колёсо. За один оборот однозаходной фрезы нарезаемое колёсо поворачивается на 1/Z оборота, где Z – число нарезаемых зубьев. Таким образом, фреза и изделие воспроизводят движение элементов червячной передачи.
При нарезании зубьев цилиндрических колёс, кроме этих движений, фрезе сообщается перемещение параллельно оси заготовки, а при нарезании зубьев червячных колёс заготовка движется на фрезу в радиальном направлении.
|
Станок является полуавтоматом.
Цилиндрические колёса можно нарезать как в автоматическом, так и простом циклах.
Автоматический цикл:
1) ускоренный подвод стола;
2) радиальная подача до жесткого упора (врезание);
3) вертикальная (продольная) подача суппорта;
4) ускоренный отвод стола в исходное положение;
5) ускоренный отвод суппорта в исходное положение;
6) выключение станка.
Простой цикл:
1) вертикальная подача;
2) останов подачи и выключение электродвигателя рабочих ходов.
Ускоренный отвод стола и суппорта в исходное положение осуществляется в наладочном режиме, то есть последовательным нажатием на соответствующие кнопки.
Червячные колёса нарезаются по следующему циклу:
1) ускоренный подвод стола;
2) радиальная подача;
3) останов подачи.
По окончании доработки всех зубьев рабочий нажимает кнопку "стоп", выключая двигатель рабочего хода.
Нажатием на кнопку "вправо" производятся ускоренный отвод стола от фрезы и автоматический останов в исходном положении.
Кинематика станка
При фрезеровании прямозубых и косозубых колёс с продольной подачей и червячных колёс с радиальной подачей сочетаются определённым образом следующие движения:
- главное движение – вращение фрезы;
- движение обката или деления – вращение заготовки, согласованное с вращением фрезы;
- продольная подача – вертикальное перемещение суппорта с фрезой;
- дополнительное вращение заготовки для образования винтового зуба;
- радиальная подача – горизонтальное перемещение стола с заготовкой;
- ускоренные перемещения суппорта и стола.
Рис. 2. Схема расположения поперечных суппортов
Для смены позиции инструмента револьверная головка периодически поворачивается на 1/6 часть оборота. Верхний суппорт используют, как правило, для отрезки детали. Работа суппортов может частично совмещаться по времени как одного с другим, так и с какими-либо холостыми ходами.
Основное направление вращения шпинделя – левое, т.е. точение резцами (см. рис. 2) и обработка отверстий леворежущими центровыми инструментами производится при вращении прутка в левом направлении.
Для нарезания правой резьбы (наружной – плашкой, внутренней – метчиком) производится переключение шпинделя на правое вращение. После нарезания резьбы шпиндель снова реверсируется, и при его левом вращении происходит свинчивание плашки или вывинчивание метчика и продолжаются обработки резцами.
При одной и той же настройке привода вращения шпинделя частота правого вращения значительно ниже частоты левого, поскольку нарезание должно производиться с невысокими скоростями резания.
|
Цикл работы автомата начинается с подачи и зажима прутка, а заканчивается отводом верхнего суппорта после отрезки готовой детали.
КИНЕМАТИКА АВТОМАТА
Кинематическая схема станка (см. рис. 1) включает привод вращения шпинделя с прутком, приводы вращения вспомогательного и распределительного валов, приводы механизмов холостых ходов. Вращение прутка является главным движением резания, перемещения суппортов с режущими инструментами, обеспечиваемые от кулачков распредвала, – подачей.
работой универсального горизонтально-фрезерного (универсально-фрезерного) станка модели 6Н81
6 - фрезерный станок (номер группы по классификации ЭНИМС)
Н – серия (поколение) станка (Б, К, Н, М, Р, Т)
8 – номер подгруппы (1, 2, 3, 4, 5, 6, 7, 8, 9) по классификации ЭНИМС (8 - горизонтально-фрезерный)
1 – исполнение станка - типоразмер (0, 1, 2, 3, 4) (1 - размер рабочего стола - 250 х 1000)
Станок предназначен для обработки различных деталей сравнительно небольших размеров в условиях индивидуального и мелкосерийного производства. Из числа работ, выполняемых на фрезерных станках и показанных на рис. 1, характерными для универсально-фрезерного являются те, которые производятся насадными фрезами (см. рис. 1,а,г,е,ж,м,о,п).
Достаточно часто выполняются операции отрезания (отрезки) и разрезания (разрезки) заготовок. Отрезание – процесс отделения части материала от целого (бруска, уголка и т.д.) и разрезание – процесс разделения целого (бруска, уголка и т.д.) на равные или неравные части производится тонкими дисковыми фрезами, называемыми отрезными. Возможна обработка вертикальных плоскостей торцовыми фрезами (см. рис. 1,в) и горизонтальных пазов и уступов на вертикальных поверхностях концевыми фрезами.
Общий вид универсально-фрезерного станка представлен на рис. 2. Основные узлы и детали станка на рисунке показаны буквами, а элементы управления – цифрами.
Станок устроен следующим образом. На плите (основании) А закреплена станина Б, внутри которой размещён разделённый привод главного движения. Он состоит из коробки скоростей и перебора со шпиндельным узлом. На вертикальных направляющих станины расположена вертикально подвижная консоль И с коробкой подач. На горизонтальных направляющих консоли установлены поперечно подвижные салазки Ж с поворотной плитой Е, а на направляющих плиты – продольно подвижный стол Д.
Для поддержки длинных оправок, на которых закрепляются цилиндрические, дисковые и тому подобные насадные фрезы, станки оснащаются хоботом В с двумя подвесными серьгами (подвесками) Г. Хобот по станине и серьги по хоботу могут быть перемещены и закреплены в нужном положении, зависящем от длины оправки. Если используются торцовые и концевые фрезы, то серьги снимаются, а хобот сдвигается назад (по рис. 2 – влево).
Компоновка станка с консолью удобна тем, что при фрезеровании заготовок с любой высотой уровень зоны обработки не меняется, что обеспечивается при соответствующем установе консоли по вертикали. Однако несущая система станка не является замкнутой, в результате чего её жёсткость снижена. Увеличение жёсткости станка может быть обеспечено связью хобота с консолью двумя поддерживающими стойками К.
Для ручного управления станком – переключения частот вращения шпинделя и подач, включения рабочих перемещений стола, салазок и консоли, выполнения ручных перемещений этих узлов – на станке имеются следующие элементы:
1 – рукоятка переключения групповых передач коробки скоростей;
2 – рукоятка переключения перебора шпинделя;
3 – маховик ручного продольного перемещения стола;
4 – рукоятка включения продольной подачи;
5 – рукоятка включения поперечной подачи;
6 – рукоятка включения вертикальной подачи;
7 – рукоятка ручного вертикального перемещения консоли с кареткой и столом;
8 – маховик ручного поперечного перемещения каретки со столом;
9, 10 – рукоятки переключения групповых передач коробки подач.
![]() |
|
|
История развития пистолетов-пулеметов: Предпосылкой для возникновения пистолетов-пулеметов послужила давняя тенденция тяготения винтовок...
Состав сооружений: решетки и песколовки: Решетки – это первое устройство в схеме очистных сооружений. Они представляют...
Общие условия выбора системы дренажа: Система дренажа выбирается в зависимости от характера защищаемого...
Организация стока поверхностных вод: Наибольшее количество влаги на земном шаре испаряется с поверхности морей и океанов (88‰)...
© cyberpedia.su 2017-2024 - Не является автором материалов. Исключительное право сохранено за автором текста.
Если вы не хотите, чтобы данный материал был у нас на сайте, перейдите по ссылке: Нарушение авторских прав. Мы поможем в написании вашей работы!