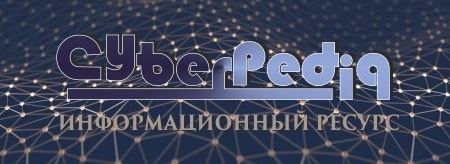
Автоматическое растормаживание колес: Тормозные устройства колес предназначены для уменьшения длины пробега и улучшения маневрирования ВС при...
Индивидуальные очистные сооружения: К классу индивидуальных очистных сооружений относят сооружения, пропускная способность которых...
Топ:
Выпускная квалификационная работа: Основная часть ВКР, как правило, состоит из двух-трех глав, каждая из которых, в свою очередь...
Комплексной системы оценки состояния охраны труда на производственном объекте (КСОТ-П): Цели и задачи Комплексной системы оценки состояния охраны труда и определению факторов рисков по охране труда...
Отражение на счетах бухгалтерского учета процесса приобретения: Процесс заготовления представляет систему экономических событий, включающих приобретение организацией у поставщиков сырья...
Интересное:
Принципы управления денежными потоками: одним из методов контроля за состоянием денежной наличности является...
Распространение рака на другие отдаленные от желудка органы: Характерных симптомов рака желудка не существует. Выраженные симптомы появляются, когда опухоль...
Средства для ингаляционного наркоза: Наркоз наступает в результате вдыхания (ингаляции) средств, которое осуществляют или с помощью маски...
Дисциплины:
![]() |
![]() |
5.00
из
|
Заказать работу |
|
|
Особенности инструментального производства. Технологическая классификация металлорежущих инструментов.
Инструмент рассматривают как объект пр-ва. В зависимости от уровня востребованного инструмента их пр-ва может быть организована как на специализированных инструментальных заводах, так и в инструментальных подразделениях (цехах) машиностроительных предприятий выпускающих другую основную продукцию. Обычно на инструментальных заводах изготавливают стандартизированные инструменты. Технология производства характеризуется рядом особенностей вызываемой специфиой объекта пр-ва.
Особенности и причины:
1. Высокие расходы на заготовку и мех. Обработку. Объясняется это применением трудноизготавливаемых мат-ов.
2. Дифецитность и дороговизна мат-ов, требует применения малоотходных тех.процессов.
3. Необходимость применения дорогостоющих станков и технич.оснастки для получения сложной фассонно- втулочной формы.
4. Необходимость применения высокоточного оборудования для достижения точности режущих инструментов.
Классификация РИ:
1. Круглые стержневые инструменты- имеют рабочую часть в виде круглого стержня и цилиндра или конический хвостовик
2. Насадные(втулочные) инструменты- имеют форму, которую можно вписать в цилиндр длина которой больше диаметра, так же имеют цилиндр или коническое посадочное отверстие.
3. Дисковые инструменты, по конструкции близки к втулочным, так же имеют конические или цилиндрические посадочные отверстия, но длинна меньше диаметра.
4. Плоские инструменты- имеют форму наружней поверхности, которую можно вписать в призму.
Способы крепления вставок из быстрорежущей стали на державки инструментов.
|
1 – группа с тепловыми воздействиями (сваривание,плавка)
2 – группа методов механического крепления
3 – группа методов с химическими воздействиями (склеивание)
Для пластин из быстрорежущей стали чаще всего применяют приваривание, которое выполняют с помощью сварочных порошков. Инструмент помещают в печь и нагревают до температуры 900 градусов. Выдерживают 20-30 минут, затем нагревают до 1200 градусов. С помощью пресса пластина прижимается к державке и выдерживается до полной кристаллизации.
Пайка проводиться обычно в печах или на установках ТВЧ.
При наплавке источниками тепла служат либо газовая горелка, либо электрическая дуга.
Присадочный пруток из быстрорежущей стали оплавляется пламенем горелки или электрической дугой и попадает на нужное место на инструменте.
C пособы крепления твердосплавных пластин на державки инструментов
1) закрепление пластин напайкой непосредственно на корпус или державку инструмента,
2) закрепление пластин напайкой на специальных вставках или ножах, закрепляемых механически в корпусе или в державке инструмента,
3) закрепление пластин в державках или в корпусе механическим способом,
4) закрепление многогранных неперетачиваемых пластин в державках или в корпусе механическим способом.
Первый и второй способы крепления обеспечивают прочное и надежное соединение режущих частей инструмента с корпусом. Конструкция подобных инструментов отличается простотой и универсальностью. Однако в процессе напайки возникают температурные напряжения в твердосплавных пластинах, приводящие к появлению трещин и уменьшению ресурса работы таких инструментов. Поэтому в последние годы стали широко применять третий и четвертый способы крепления твердосплавных пластин, что значительно усложняет конструкцию инструментов. Во многих случаях, особенно в массовом и крупносерийном производствах, использование неперетачиваемых пластин оказывается более целесообразным по ряду причин. Основной причиной является высокая экономичность использования твердого сплава, так как на одной пластине располагаются три, четыре, шесть и более режущих кромок, которые можно использовать последовательно без каких-либо существенных дополнительных затрат.
|
Подготовка технологических баз инструментов
1. Подготовка баз у стержневого инструмента.
Для стержневого инструмента характерным является использование искусственных технологических баз в виде центровых отверстий, или наружных конусов по краям заготовки.
Базирование по наружным конусам применяется при малом диаметре инструмента (< 8 мм.), а также когда конструкция центровых отверстий не предусмотрена.
Заготовки базируются в обратных центрах, в дальнейшем конические фаски удаляются.
Использование в качестве баз центровых отверстий позволяет выдержать принцип единства баз на большинстве операций последующей обработке и обеспечения точных поверхностей.
Перед зацентровкой, обязательно обрабатывают торцы заготовки. В единичном и мелкосерийном производстве, обработка выполняется на горизонтально-фрезерных станках. Обработка выполняется с переустановкой.
В серийном, крупносерийном и массовом производстве, обработка торцов и зацентровка выполняется на фрезерно-центровальных или центровально-подрезных станках (заготовки до 50 мм.)
В процессе обработки заготовка неподвижна, предпочтительна ее установка в центрирующее приспособление со сходящимися призмами. Это обеспечивает концентричность центровых отверстий и наружных цилиндров, что гарантирует равномерное распределение припуска при последующей обработке.
На фрезерно-центровальных станках в 1-ой позиции фрезеруются оба торца, во 2-ой выполняется их зацентровка.
На центровально-подрезных станках выполняется двухсторонняя обработка с центровочной головкой, состоящая из центровочного сверла и резца для обработки торца установленные в одном корпусе.
В обоих случаях обеспечивается высокая точность центровых отверстий, что влияет на точность последующей обработки.
2. Подготовка баз у втулочных, дисковых и призматических инструментов.
В качестве чистовых технологических баз у втулочных и дисковых инструментов используется цилиндрическое или коническое центрально отверстие и прилегающий торец или наружный цилиндр и торец. Базирование при последующей обработке по отверстию предпочтительно, т.к. позволяет использовать при обработке простые и высокоточные инструменты, жесткие и разжимные оправки.
|
Подготовка баз в единичном и мелкосерийном производстве выполняется на универсальных токарных станках. В серийном производстве на станках с ЧПУ, на серийном и массовом на одно- и многошпиндельных станках автоматов.
У призматического инструмента в качестве баз используются взаимно перпендикулярные поверхности, установка выполняется в координатный угол.
Подготовка баз в единичном и мелкосерийном производстве выполняется на вертикально- и горизонтально-фрезерных станках, в крупносерийном и массовом производстве с использованием местных инструментов или на протяжных станках.
ОБРАБОТКА ЛАПОК И КВАДРАТОВ
Обработка чаще всего выполняется на горизонтально-фрезерных станках набором из 2-хдисковых фрез установленных на одной оправке.
Заготовка устанавливается коническим хвостовиком в призму. Для повышения производительности приспособления могут быть многоместными.
Фрезерование квадратов у разверток и метчиков также выполняется набором из 2-х фрез. Заготовку устанавливают в цангу делительного приспособления, что позволяет выполнить поворот на 90 градусов после фрезерования 2-х сторон.
В серийном производстве лапы и квадраты могут обрабатываться на фрезерных станках с ЧПУ.
ЗАТЫЛОВАНИЕ ФРЕЗ РЕЗЦАМИ
Цель этой технологической операции заключается в образовании на зубьях инструментов задней поверхности заданной формы, обеспечивающей при переточках по передней поверхности два условия: постоянство профиля зуба и постоянство величины заднего угла в радиальном сечении.
Величина затылования:
где Dеи – наружный диаметр затылуемого инструмента;
zи – число зубьев затылуемого инструмента;
αВ – задний угол при вершине.
Рис. Схема движения резца 2 и изделия 1 при затыловании от т. a до т. b
Затылование осуществляется токарным резцом на токарно-затыловочных станках мод. 1810, 1Е811, 1812, 1813, а также на специальных станках для затылования дисковых фрез КТ-152, червячных и дисковых фрез КТ-150 и КТ-151.
|
Главный принцип затыловочных станков – возвратно-поступательное перемещение резца, связанное кинематически с равномерным вращением заготовки. Возвратно-поступательное движение инструмента по отношению к оси центров станков может быть трех видов: радиальное, косое и осевое.
Рис. Схема затылования зуба:
ABC – путь резца при затыловании;
AB – длина рабочего хода, состоит из ширины зуба, входа и выхода инструмента;
BC – обратный ход.
Гитару деления настраивают так, чтобы 1 обороту заготовки соответствовало число оборотов кулачка, равное zи.
1 об.загот. >zи об. кул.
За 1 оборот кулачка резец должен осуществить затылование 1 зуба и отвод резца, т. е.
1 об.загот. >Sпоп. инс.
2 движение (Sраб. и Sотв.) осуществляется кулачком, вращение которого связанно с вращением шпинделя станка при помощи делительной головки. Форма кулачка состоит из рабочей части, выполненной по архимедовой спирали, и нерабочей, выполненной в виде плавной кривой или прямой.
Величина центрального угла (300-330)° зависит от соотношения ширины зуба и впадины.
Фасонные фрезы затыловывают фасонными резцами.
Для фасонных фрез при радиальном затыловании задний угол αN в сечении, перпендикулярном режущей кромке в любой точке профиля М:
ЗАТОЧКА ТОКАРНЫХ РЕЗЦОВ.
В процессе резания конструкционных материалов происходит износ рабочих поверхностей резца. Износ по передней поверхности сопровождается, образованием впадины или лунки, задних поверхностей -образованием площадок или фасок, но которых величина заднего угла равна нулю.
Износ рабочих поверхностей резца появляется в начальный момент процесса резания и, постоянно вырастая, продолжается в течении всего процесса резания.
По величине износа резцов определяют толщину слоя инструментального материала, снимаемого при заточке резца, количество переточек и общий срок службы резца.
Измеряем углы при помощи универсального угломера. Измеряем величину износа при помощи лупы Бринелля или электронного микроскопа и рассчитываем толщину снимаемого слоя по задней и передней поверхности, количество переточек, ширину снимаемого слоя и общую стойкость резца.
Заточка токарных резцов осуществляется на универсальных заточных станках, на стол которого устанавливаются трехповоротные тиски. Для заточки резцов с твердосплавными пластинами используют алмазные круги, при заточке которыми не требуется последующая доводка. При заточке резца по передней поверхности трехповоротные тиски настраивают таким образом что бы задняя поверхность была параллельно заточному кругу, а при заточке по передней поверхности настраивают так что бы передняя поверхность была параллельна заточному кругу. При заточке резца заточник должен выполнять следующие действия: после каждого двойного хода стола, вращающийся круг подается на глубину резания t.
|
Заточка метчиков.
Метчики затачиваются по передней и задней поверхности как в процессе изготовления, так и в процессе затачивания.
По передней поверхности обработка выполняется на специальных заточных станках 3687, 86, а также на универсально-заточных и круглошлифовальных станках с использованием специального приспособления.
Затачивание по передней поверхности выполняется при изготовлении метчиков и при восстановлении их режущих свойств в процессе эксплуатации. Обработка выполняется на универсально заточных станках при установки метчика в центрах чашечным или тарельчатым шлифовальным кругом. При этом радиус при вершине круга заправляют таким образом, чтобы обеспечить плавное сопряжение передней поверхности и дна стружечной канавки.
ЗАТОЧКА КРУГЛЫХ ПРОТЯЖЕК
В условиях крупносерийного производства используют спец. заточные станки.
Протяжки затачивают за 3 операции;
1) Заточка по передней поверхности
2) Шлифование спинки зуба
3) Заточка по задней поверхности
При эксплуатации износ зубьев протяжек происходит как по задней, так и по передней поверхти.
Призаточки ширина затачиваемого слоя равна: ∆=hз+0.05мм≈0,15-0,3мм.
Толщина удаляемого слоя протяжки за весь её период работы до 1,5 мм.
Заточку передней поверхности протяжки необходимо выполнять конической поверхностью тарельчатого круга, при этом перемещая, образовывающийся конус круга должнасовподать по направлению с подачей. Для обеспечения требуемого переднего угла кривизна конической поверхности круга должна быть меньше кривизны передней поверхности зуба протяжки. Это достигается подбором соответствующего диаметра круга и угла его установки относительно оси протяжки.
Рис - Заточка протяжек по задней поверхности торцем чашечного круга…
Особенности инструментального производства. Технологическая классификация металлорежущих инструментов.
Инструмент рассматривают как объект пр-ва. В зависимости от уровня востребованного инструмента их пр-ва может быть организована как на специализированных инструментальных заводах, так и в инструментальных подразделениях (цехах) машиностроительных предприятий выпускающих другую основную продукцию. Обычно на инструментальных заводах изготавливают стандартизированные инструменты. Технология производства характеризуется рядом особенностей вызываемой специфиой объекта пр-ва.
Особенности и причины:
1. Высокие расходы на заготовку и мех. Обработку. Объясняется это применением трудноизготавливаемых мат-ов.
2. Дифецитность и дороговизна мат-ов, требует применения малоотходных тех.процессов.
3. Необходимость применения дорогостоющих станков и технич.оснастки для получения сложной фассонно- втулочной формы.
4. Необходимость применения высокоточного оборудования для достижения точности режущих инструментов.
Классификация РИ:
1. Круглые стержневые инструменты- имеют рабочую часть в виде круглого стержня и цилиндра или конический хвостовик
2. Насадные(втулочные) инструменты- имеют форму, которую можно вписать в цилиндр длина которой больше диаметра, так же имеют цилиндр или коническое посадочное отверстие.
3. Дисковые инструменты, по конструкции близки к втулочным, так же имеют конические или цилиндрические посадочные отверстия, но длинна меньше диаметра.
4. Плоские инструменты- имеют форму наружней поверхности, которую можно вписать в призму.
|
|
Кормораздатчик мобильный электрифицированный: схема и процесс работы устройства...
Общие условия выбора системы дренажа: Система дренажа выбирается в зависимости от характера защищаемого...
Своеобразие русской архитектуры: Основной материал – дерево – быстрота постройки, но недолговечность и необходимость деления...
Типы оградительных сооружений в морском порту: По расположению оградительных сооружений в плане различают волноломы, обе оконечности...
© cyberpedia.su 2017-2024 - Не является автором материалов. Исключительное право сохранено за автором текста.
Если вы не хотите, чтобы данный материал был у нас на сайте, перейдите по ссылке: Нарушение авторских прав. Мы поможем в написании вашей работы!