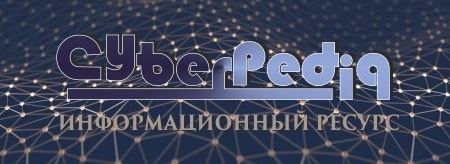
Своеобразие русской архитектуры: Основной материал – дерево – быстрота постройки, но недолговечность и необходимость деления...
История развития хранилищ для нефти: Первые склады нефти появились в XVII веке. Они представляли собой землянные ямы-амбара глубиной 4…5 м...
Топ:
Комплексной системы оценки состояния охраны труда на производственном объекте (КСОТ-П): Цели и задачи Комплексной системы оценки состояния охраны труда и определению факторов рисков по охране труда...
Установка замедленного коксования: Чем выше температура и ниже давление, тем место разрыва углеродной цепи всё больше смещается к её концу и значительно возрастает...
Особенности труда и отдыха в условиях низких температур: К работам при низких температурах на открытом воздухе и в не отапливаемых помещениях допускаются лица не моложе 18 лет, прошедшие...
Интересное:
Распространение рака на другие отдаленные от желудка органы: Характерных симптомов рака желудка не существует. Выраженные симптомы появляются, когда опухоль...
Наиболее распространенные виды рака: Раковая опухоль — это самостоятельное новообразование, которое может возникнуть и от повышенного давления...
Отражение на счетах бухгалтерского учета процесса приобретения: Процесс заготовления представляет систему экономических событий, включающих приобретение организацией у поставщиков сырья...
Дисциплины:
![]() |
![]() |
5.00
из
|
Заказать работу |
|
|
Получение длинномерных изделий с помощью различных видов прокатно-прессово-волочильного производства является достаточно сложным процессом и включает большое количество промежуточных технологических операций, повышающих себестоимость металлопродукции. В последнее время особую актуальность приобрели работы, направленные на создание технологий, в которых разные виды обработки металлов давлением или литье заготовок с последующим их формоизменением объединяются в один цикл. Такие технологии применяют достаточно давно и успешно. Например, по такому принципу работают высокопроизводительные литейно-прокатные агрегаты, используемые для стали, алюминиевых и медных сплавов. Однако эти агрегаты имеют сложную конструкцию, ориентированы на большие объемы производства, пригодны не для всех сплавов, что делает их малоэффективными в условиях быстрого перехода с одного размера профиля на другой при небольших партиях заказов.
В настоящее время при получении профилей небольшого сечения из алюминиевых и медных сплавов наряду с традиционными технологиями, особенно для мини-производств, используются технологии непрерывного прессования конформ, экстроллинг, лайнекс и непрерывного литья, прокатки, прессования кастекс, кастср. Модульное оборудование, предназначенное для таких производств, характеризуется высокой мобильностью, гибкостью перехода от одного вида продукции к другому, а также сравнительно высокой производительностью. Поэтому можно заключить, что совершенствование этих технологий является перспективным направлением развития процессов прокатки, прессования и волочения.
Многообразие появившихся в последнее время новых процессов обработки металлов и сплавов требует их классификации, за основу которой можно взять типовые процессы прокатно-прессово-волочильного производства, поскольку они формируют такие промежуточные и комбинированные процессы, как, например, прокатка - волочение или прессование -волочение. К данным процессам может быть также отнесена обработка металлов и сплавов с применением активных сил трения, основанная на опережающем движении одного тела относительно другого. В них для перехода от тормозящего действия сил трения к активному используют следующие способы:
|
– применяют инструмент, который опережает деформируемое тело в направлении его движения (валки, контейнер);
• вращают инструмент вокруг продольной оси для развития активного трения в поперечной плоскости;
• деформируют металл, заключенный в опережающие податливые оболочки, или создают опережающее действие технологической смазки (гидропрессование).
Стремление использовать активные силы трения для непрерывной деформации металлов привело к разработке новых методов непрерывного прессования. При этом в различных схемах таких процессов (конформ, экстроллинг, лайнекс) используются комбинации операций обработки металлов давлением: прокатки, прессования и волочения.
С точки зрения протекания совмещенных процессов во времени можно выделить дискретные (циклические), полунепрерывные и непрерывные процессы обработки металлов и сплавов.
Следует отметить, что к совмещенным процессам в последнее время прибавились и процессы, в которых операции обработки металлов давлением проводятся одновременно с операциями термообработки. В качестве примера можно привести процесс закалки термически упрочняемых алюминиевых профилей на столе пресса, патентирование и др.
Как было рассмотрено, технологический процесс прокатно-прессово-волочильного производства является многооперационным и состоит из набора простых операций. При этом чем меньше площадь поперечного сечения изделия, тем больше требуется операций. Так, например, для получения алюминиевой проволоки по традиционной технологии необходимо выполнить до 15-20 операций, которые обычно разорваны во времени. Таким образом, в области производства изделий из цветных металлов и сплавов выделяют простые и сложные (интегральные) процессы обработки.
|
Под простыми процессами понимают такие, которые включают один цикл обработки металла в одном очаге деформации (или литья) без смены направления течения металла или приложения нагрузки. Интегральные процессы включают несколько операций в одном очаге деформации либо комбинацию операций со сменой направления перемещения металла. В основу классификации новых процессов прокатно-прессово-волочильного производства может быть положен принцип, по которому новый интегральный процесс должен возникать в результате взаимодействия простых процессов и обладать уже новым комплексом свойств, которые в основном должны исключать недостатки совмещаемых (комбинируемых) операций.
Базовым называют такой процесс, при котором во время приложения нагрузки внешнее распределение силы и ее направление на поверхности очага пластической деформации (или при кристаллизации) не изменяется. Основными базовыми процессами для прокатно-прессово-волочильного производства являются литье, прокатка, прессование, волочение и термообработка. Комбинированным процессом обработки (рис. 11.1) называют комбинацию двух и более базовых процессов, при которых происходит суммарное (интегральное) наложение нагрузок в одном очаге деформации, иногда и со сменой направления течения металла. В качестве примера комбинированного процесса можно привести, например, прокатку-волочение, когда прокатка ведется с натяжением конца полосы. При этом в зависимости от величины натяжения прокатка-волочение (рис. 11.1, а) может превращаться в волочение-прокатку (рис. 11.1,6), когда удельный вес процесса вытягивания превалирует над процессом обжатия в валках.
Совмещенный процесс является более сложным и характеризуется разделением базовых процессов во времени или пространстве. Такими типовыми процессами считаются литье и прокатка (рис. 11.1, в) или литье и прессование, когда заготовку получают с помощью кристаллизатора, а затем прокатывают на непрерывном стане или подвергают непрерывному экструдированию. В данном случае процессы обработки металла выстраиваются последовательно и только после окончания одного из них начинается следующий. В качестве примера можно привести совмещенный процесс литья, прокатки, фрезеровки и отжига ленты. Считают, что именно с применением этих процессов можно добиться радикального повышения экономичности производства и качества продукции.
|
В настоящее время наблюдается тенденция к созданию совмещснно-комбинированных процессов, когда на каждом последовательном этапе обработки может применяться комбинированный процесс. Примером реализации такого процесса может быть техническое решение, при котором на одной установке осуществляются одновременно операции литья-кристаллизации, прокатки-прессования, охлаждения и смотки готовых пресс-изделий в бухту (рис. 11.1, 6) с калибровкой готового изделия на заданный диаметр.
Интегральные схемы все более усложняются, становясь многофункциональными и непрерывными, а на сочетания традиционных видов обработки металлов могут накладываться такие виды обработки, как магнитноимпульсная, вибрационная, термомеханическая и др.
За основу классификации интегральных видов прокатно-прессово-волочильного производства можно принять предложенную авторами работы (рис. 11.2).
в
Рис. 11.1. Схемы процессов обработки цветных металлов: а, б - комбинированных; в, г- совмещенных; д - совмещенно-комбинированных
Следует отмстить, что в данной схеме приведены как виды обработки, которые уже находят практическое применение, так и наиболее перспективные. При этом схема может быть расширена и усовершенствована при появлении новых разновидностей процессов.
Для реализации многих вариантов комбинированных процессов обработки чаще всего используется прокатка, основным преимуществом которой является возможность создания с помощью вращающихся валков непрерывного процесса деформации. Кроме того, силы трения, препятствующие протеканию процесса во многих операциях обработки металлов и требующие дополнительных энергетических затрат, при прокатке становятся активными и способствуют деформации. Однако традиционная продольная прокатка не позволяет получить большие единичные степени деформации за один цикл обработки. Вместе с тем известно, что максимальные степени деформации могут быть достигнуты применением прямого прессования, но тогда процесс становится циклическим, и около двух третей усилия будет затрачиваться на преодоление сил контактного трения по инструменту. Отсюда возникает интерес к соединению положительных свойств каждого процесса: непрерывности и активных сил трения при прокатке и возможности деформировать металл с большими степенями деформации - при прессовании.
|
Для операций волочения помимо значительных потерь на трение характерны малые степени деформации за проход, что так же, как и при прокатке, ведет к многооперационности.
В настоящее время разработки ученых мира направлены на создание комбинированных способов обработки металлов давлением, в которых бы по возможности совмещались положительные качества каждого из входящих в комбинацию процессов.
|
|
Двойное оплодотворение у цветковых растений: Оплодотворение - это процесс слияния мужской и женской половых клеток с образованием зиготы...
Биохимия спиртового брожения: Основу технологии получения пива составляет спиртовое брожение, - при котором сахар превращается...
Семя – орган полового размножения и расселения растений: наружи у семян имеется плотный покров – кожура...
Состав сооружений: решетки и песколовки: Решетки – это первое устройство в схеме очистных сооружений. Они представляют...
© cyberpedia.su 2017-2024 - Не является автором материалов. Исключительное право сохранено за автором текста.
Если вы не хотите, чтобы данный материал был у нас на сайте, перейдите по ссылке: Нарушение авторских прав. Мы поможем в написании вашей работы!