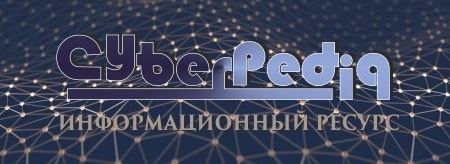
Адаптации растений и животных к жизни в горах: Большое значение для жизни организмов в горах имеют степень расчленения, крутизна и экспозиционные различия склонов...
Наброски и зарисовки растений, плодов, цветов: Освоить конструктивное построение структуры дерева через зарисовки отдельных деревьев, группы деревьев...
Топ:
Эволюция кровеносной системы позвоночных животных: Биологическая эволюция – необратимый процесс исторического развития живой природы...
Отражение на счетах бухгалтерского учета процесса приобретения: Процесс заготовления представляет систему экономических событий, включающих приобретение организацией у поставщиков сырья...
Техника безопасности при работе на пароконвектомате: К обслуживанию пароконвектомата допускаются лица, прошедшие технический минимум по эксплуатации оборудования...
Интересное:
Уполаживание и террасирование склонов: Если глубина оврага более 5 м необходимо устройство берм. Варианты использования оврагов для градостроительных целей...
Берегоукрепление оползневых склонов: На прибрежных склонах основной причиной развития оползневых процессов является подмыв водами рек естественных склонов...
Влияние предпринимательской среды на эффективное функционирование предприятия: Предпринимательская среда – это совокупность внешних и внутренних факторов, оказывающих влияние на функционирование фирмы...
Дисциплины:
![]() |
![]() |
5.00
из
|
Заказать работу |
|
|
V 1/3 Применение вибраций в процессах ОМД
Вибрации при волочении, горячей объёмной и холодной листовой штамповке благодаря уменьшению контактного трения снижают усилия деформирования и приводят к повышению пластичности металла в процессе его обработки. Одновременно улучшаются структура и качество металла изделий.
Вибрационное нагружение снижает напряжение деформирования, увеличивает пластичность металлов; снижает остаточные напряжения, обеспечивает более равномерное распределение деформаций и напряжений, способствует получению более однородной и мелкозернистой структуры. Такое влияние вибрации на технологические и механические свойства металлов объясняется уменьшением как внутренних, так и внешних сил сопротивления деформации, наиболее значительной частью которых является контактное трение. Практически верхний предел ультразвуковых колебаний соответствует частоте тепловых колебаний молекул вещества. Существуют различные типы вибровозбудителей - гидравлические, пневматические, электромагнитные, электромеханические, гидродинамические и магнито-стрикционные. Так, например, электромеханические инерционные вибровозбудители с приводом от асинхронных двигателей основаны на принципе возникновения центробежной силы при вращении неуравновешенной массы (дебаланса).
Они обеспечивают возможность получения больших кинетических моментов и сравнительно высоких частот при устойчивости и надежности работы. В установившемся режиме основная часть мощности привода вибровозбудителя расходуется на преодоление трения. При использовании вибраций одной из основных проблем является устранение шума, основным источником которого служат подшипники, передача, амортизаторы и др.
|
Вибровозбудитель представляет собой массивную стальную блок-плиту, в горизонтальных расточках которой установлены на подшипниках качения вибровалы симметрично относительно оси пресса. Каждый вибровал приводится отдельным асинхронным двигателем через скоростную плоскоременную передачу. Валы вращаются навстречу друг другу.
Жесткость конструкций виброблока обеспечивает синхронизацию вращения валов и строго вертикально направленные колебания. Виброблок ставится на упругие амортизаторы. Суммарная жесткость амортизаторов определяется таким образом, чтобы собственная частота вибрируемой массы была значительно меньше минимальных возбуждаемых частот во избежание появления резонанса и передачи вибрации на фундамент.
Кроме того, амортизаторы должны выдерживать рабочее усилие пресса. В практике применяют пружинные, а также надежные в работе гидравлические закрытые амортизаторы с постоянным объемом жидкости. В качестве рабочей жидкости используется цилиндрическое масло. Ступенчатое регулирование частоты вибратора от 60 до 200 гц осуществляется сменными шкивами, а регулирование амплитуды от 0,06 до 0,5 мм достигается сменой дебалансов.
Назначение гидроформовки
Гидроформовка используется для замены процесса штамповки конструкции из двух частей и их сварки или для создания отдельных сложных контуров и форм. В итоге получаемые детали с облегченным весом и высоким качеством поверхности имеют увеличенную прочность и жесткость. Гидроформовка дает возможность достичь сложной геометрии деталей за счет поддержания упругой жидкой средой.
С помощью гидроформовки можно совершать многие виды операций: свободную гибку, вырезку материала и пробивку отверстий, вытяжку, отбортовку, выдавливание надписей и рисунков, штамповку подсечек.
Основные материалы для гидроформовки
Материалом трубных заготовок для гидроформовки могут быть любые металлы и сплавы, которые обладают достаточной пластичностью. Распространено использование горячекатаных и холоднотянутых труб, труб из коррозионностойких и жаропрочных легированных, а также углеродистых марок стали. Из цветных металлов чаще всего применяют латунь, медь, алюминий и др. Также используют и сварные трубы. Гидроформовка делает возможным изготовление деталей из биметаллических труб и получение биметаллические деталей из составных труб.
|
V 1/1 Технологии кузнечно-штамповочного производства с использованием эффекта сверхпластичности
Сверхпластическая формовка
Одним из прогрессивных направлений в обработке металлов давлением является использование в различных технологиях эффекта сверхпластичности. По классическому определению сверхпластичность - это способность металлических тел квазиравномерно удлиняться с высокой скоростной чувствительностью напряжения течения.
Для перевода металлов в состояние свсрхпластичности необходимы следующие условия:
• ультрамелкозернистая (УМЗ) структура заготовки, характерный диапазон размера зерна: от ~0,5 до ~10 мкм;
• температура деформации выше ~ 0,5 Тпл, К;
• скорость деформации от ~105 до ~101 с”1.
При этих условиях металлические материалы способны иметь следующие показатели деформации: высокое относительное удлинение (порядка 102–103 %), низкое сопротивление деформации (порядка 100–101 МПа) и высокий показатель m (более 0,2-0,3)- Другими словами, создав в металлической заготовке определенную структуру и деформируя ее при высокой температуре с низкой скоростью, можно значительно повысить ее пластичность (в десятки и сотни раз) и снизить сопротивление деформации (в 5-7 раз).
Установлено, что главным условием перевода сплавов в состояние сверхпластичности является создание в заготовках структуры с ультрамелким зерном. Для исследований применяют следующие направления:
• разработка и использование сверхпластичных сплавов, в которых мелкозернистая структура получается за счет регулирования их химического и фазового состава;
• разработка технологии получения УМЗ структуры в существующих промышленных сплавах.
Эти направления дополняют друг друга, но второй путь перспективнее, поскольку подбор материалов для деталей машин и конструкций производят исходя из требований к их эксплуатационным характеристикам, а не из возможности реализации для них новых прогрессивных технологий, в том числе и эффекта сверхпластичности. Поэтому второй путь обеспечивает более быстрое внедрение использования свсрхпластичности в промышленности.
|
Для измельчения зерна применяют специальные технологии, основанные на варьировании условий кристаллизации, а также термомеханическую обработку. В настоящее время разработаны технологии для измельчения зерна в листовых полуфабрикатах сплавов ряда цветных металлов, таких как алюминиевые, медные, никелевые и др. Эффективно измельчается зерно в титановых сплавах, которые еще называют «природно сверхпластичными», так как ультрамелкое зерно в них формируется при традиционной технологии обработки давлением, например, при горячей прокатке.
Схемы термомеханической обработки позволяют измельчать зерно в тонких листах или тонких прутках. В последнем случае вместо прокатки используют экструзию или способы, основанные на высоких сдвиговых деформациях, таких как равноканальное угловое прессование. Однако получать ультрамелкозернистую структуру этими методами в крупногабаритных полуфабрикатах не удается.
Использование эффекта сверхпластичности в обработке давлением создало новые возможности для изготовления сложных листовых деталей на основе использования методов формовки, неприменимых для обычных металлов и сплавов. Перспективным способом следует считать сверхпластическую формовку (СПФ), называемую также газокомпрессионной штамповкой или газостатической формовкой.
Малые напряжения течения, характеризующие деформацию СП материалов, способствуют тому, что более предпочтительным средством для их деформирования оказывается давление газа (обычно 0,1-2,2 МПа), а не штампы, приводимые в движение гидравлически или механически. Таким образом, процессы СПФ существенно отличаются от процессов, используемых для обычных металлов и сплавов, и имеют больше общего со способами, применяемыми для штамповки термопластов.
За время освоения процесса СПФ накоплен большой опыт, позволивший сформулировать принципы разработки технологии и анализа техникоэкономической эффективности процесса. Безусловно, что использование режимов сверхпластичности наиболее перспективно для обработки малопластичных и труднодеформируемых сплавов, условно разбиваемых на две группы.
|
К первой группе относят сплавы с температурой сверхпластического состояния 200-500°С (сплавы цинка, алюминия, магния). Для формовки в пределах этого температурного интервала можно использовать простые штампы и оборудование, аналогичные применяемым для формовки термопластов. Из этих сплавов можно получать сложные цельноформованные изделия. Во вторую группу входят сплавы с температурой сверхпластичности 800-1100°С (стали, сплавы титана, никеля и др.). Это, как правило, жаропрочные труднодеформируемые сплавы, плохо обрабатываемые традиционными методами листовой штамповки. Перевод в состояние сверхпластичности таких сплавов повышает допустимые технологические деформации, снижает деформирующие усилия, что по сравнению с традиционной листовой штамповкой уменьшает продолжительность производственного цикла и энергозатраты на него. Однако в этом случае требуется более дорогостоящая штамповая оснастка, чем для сплавов первой группы.
Обычно выделяют следующие преимущества СПФ перед традиционными процессами листовой штамповки металлов:
• возможность получения деталей сложной формы за одну формообразующую операцию, в отличие от традиционных технологий производства тех же деталей многопереходной штамповкой или другими способами;
• относительно низкая стоимость оснастки, так как обычно требуется только один основной инструмент вместо точно сопряженных пуансона и матрицы или многопозиционных штампов;
• низкие капитальные затраты на производственное оборудование благодаря тому, что деформирующие усилия относительно малы.
Если первые два преимущества очевидны, то капитальные затраты на производственное оборудование имеют тенденцию к повышению за счет необходимости тщательного контроля за процессами формовки, а также сопутствующего влияния относительно малой производительности формующих машин на себестоимость единицы продукции, так как цикл формовки обычно составляет минуты, а не секунды. В случае СПФ титановых сплавов конструкция оснастки усложняется в связи с повышением температуры формовки и склонности титановых сплавов к окислению. Таким образом, баланс затрат на процессы СПФ склоняется в пользу партий относительно малых размеров, когда низкие издержки на оснастку уравновешивают соответствующую стоимость относительно длительного цикла формовки.
|
Для реализации СПФ применительно к листовым заготовкам используют следующие приемы. Заготовку, жестко зажатую по фланцу, нагревают до температуры сверхпластичности и в изотермических условиях подвергают воздействию избыточного газового давления, обеспечиваемого подачей сжатого газа или вакуумированием внутренней полости матрицы. Характерными особенностями процесса являются статический характер приложения нагрузки и формоизменение исключительно за счет утонения свободной части заготовки, находящейся под давлением газовой среды без перемещения фланца. Неподвижность фланца, обеспечиваемая прижатой кромкой, создает соответствующее напряженное состояние, переменное вдоль контура листа.
Для СПФ различают макро- и микроформовку. Макроформовкой называют образование геометрической формы изделия, а микроформовкой -получение рельефной поверхности на его дне или стенках по аналогии с тиснением или чеканкой.
Некоторые изделия из листа соответствующей конфигурации могут быть получены СПФ без оснастки или с оформлением инструментом только характерных зон окончательной формы. Так, используя свободную выдувку сваренных по краю титановых заготовок, фирма British Aerospace изготавливает трубопроводы и баки
Такой процесс является очень привлекательным из-за своей простоты, однако номенклатура подобных изделий ограничена.
Процесс СПФ с использованием штамповой оснастки позволяет получать полые изделия из плоской или предварительно профилированной листовой или трубчатой заготовки за счет воздействия на лист небольшого газостатического давления, обеспечивающего при температуре сверхпластичности воспроизведение гравюры штампа. СПФ можно получать изделия сложных форм за один - два перехода без промежуточных отжигов на более простых по сравнению с прессами установках при сравнительно дешевой оснастке и с минимальными потерями металла.
Различают два основных вида формовки: негативную и позитивную. Оба термина заимствованы из технологии формовки изделий из листовых термопластов, где негативной называют схему формовки газовым или эластичным пуансоном изделия, наружная поверхность которого воспроизводит внутреннюю поверхность матрицы (копирование по матрице), а позитивной - схему натягивания заготовки газовой или эластичной матрицей на пуансон (копирование по пуансону).
При негативной формовке возникает разнотолщинность деформированного листа с минимальной толщиной материала в полюсе. Разнотолщинность с увеличением глубины выпуклости возрастает.
При позитивной формовке для предварительного растяжения зон, прилегающих к фланцу при негативной формовке, используют вспомогательный инструмент (пуансон-толкатель), движущийся в осевом направлении. При этом деформация затормаживается в местах контакта листа с толкателем и сосредоточивается в участках заготовки, находящихся между толкателем и зажатым фланцем. После этого подают давление, и заготовка обтягивает пуансон.
Реверсивную формовку используют для уменьшения разнотолщинности материала, присущей негативной формовке, при сохранении простоты этого процесса.
При реверсивной формовке лист сначала формуют в противоположном от матрицы направлении. Деформирование листа ведут до высоты, которая превышает глубину матрицы. Затем давление подают с другой стороны листа таким образом, чтобы произошло заполнение полости матрицы и деталь приобрела нужную форму. Цель этого способа - увеличение толщины в углах формы матрицы за счет большего утонения в полюсе.
|
|
История развития хранилищ для нефти: Первые склады нефти появились в XVII веке. Они представляли собой землянные ямы-амбара глубиной 4…5 м...
Состав сооружений: решетки и песколовки: Решетки – это первое устройство в схеме очистных сооружений. Они представляют...
Папиллярные узоры пальцев рук - маркер спортивных способностей: дерматоглифические признаки формируются на 3-5 месяце беременности, не изменяются в течение жизни...
Таксономические единицы (категории) растений: Каждая система классификации состоит из определённых соподчиненных друг другу...
© cyberpedia.su 2017-2024 - Не является автором материалов. Исключительное право сохранено за автором текста.
Если вы не хотите, чтобы данный материал был у нас на сайте, перейдите по ссылке: Нарушение авторских прав. Мы поможем в написании вашей работы!